La maquinaria heredada se puede extraer de datos para operaciones modernas
Hace tan solo dos años, cuando Brad Klippstein de Okuma America quiso extraer algunos datos operativos de una máquina herramienta heredada, tuvo que conectar docenas de cables al gabinete de control y agregar un PLC. Una vez que terminó, los datos fluyeron de la máquina herramienta al PLC y luego a un concentrador o servidor donde se almacenan.
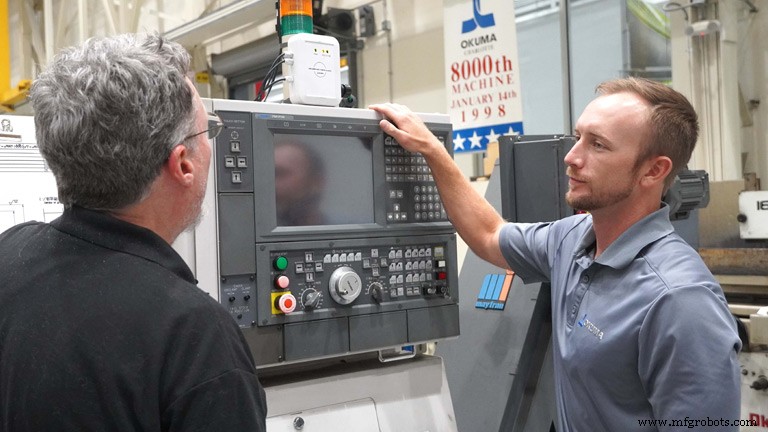
“Tenemos cosas como Ethernet y Wi-Fi y toda esta tecnología que podemos usar hoy en día”, dijo Klippstein, supervisor especialista en productos. “Pero los equipos de hace más de 30 años no tenían esa capacidad, por lo que tenía que conectar físicamente un dispositivo al gabinete de control para extraer todos esos datos. Ahora ni siquiera tenemos que tener una conexión fuerte [con máquinas nuevas]. Puedes hacer cosas de forma inalámbrica. Esa es la transición en los últimos 30 o 40 años”.
Parte del trabajo de Klippstein es ayudar a los clientes a dar pasos discretos hacia el mundo conectado, digitalizado y basado en datos de la Industria 4.0, para máquinas herramienta nuevas y heredadas.
Estos beneficios pueden incluir:
- Monitorización de máquinas-herramienta en tiempo real, en fábrica o desde una ubicación remota
- Mayor productividad y calidad
- Informes sin prejuicios
- Justificación de la adquisición
- Mantenimiento predictivo
- Atraer y retener a los mejores talentos entusiasmados con la perspectiva de aprender cosas nuevas y estar a la vanguardia de los procesos modernos.
Ya sea que se transmitan a través de cables o por aire, los datos recopilados de los dispositivos de fábrica pueden ayudar al propietario de una tienda a tomar decisiones comerciales más inteligentes.
Con el análisis de los datos a mano, los trabajadores tendrán una mayor visibilidad de las operaciones de la planta, lo que puede ayudarlos a resolver problemas, mejorar los procesos y aumentar la productividad.
Con un avance reciente, es posible que el dueño de la tienda ya no necesite a alguien como Klippstein para sus máquinas herramienta heredadas.
En 2019, Okuma presentó NET BOX suite-C Quick como una alternativa de menor costo a una solución diseñada para recopilar datos de máquinas más antiguas. El NET BOX CQ, para abreviar, se conecta directamente a una torre de señales y luego a un concentrador o dispositivo que se usa para recibir señales.
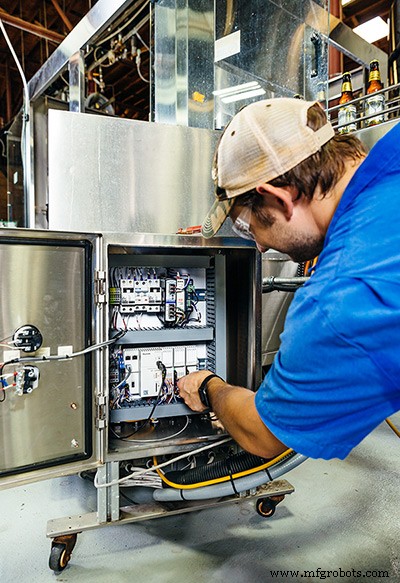
NET BOX CQ utiliza tres sensores ópticos, uno para las luces verde, amarilla y roja de la torre, y convierte la información que recopilan a un formato que puede leer un sistema informático. Para estandarizar los datos recopilados por cualquiera de sus programas, Okuma utiliza MT Connect, un protocolo de comunicaciones de código abierto y de uso común.
"Es fácil de instalar y no necesita un técnico de Okuma para hacerlo", dijo Klippstein sobre NET BOX CQ.
Para empezar, la capacidad de ver si una máquina está funcionando es una excelente métrica para realizar un seguimiento porque el propietario de un taller generalmente quiere impulsar cada pieza del equipo a la máxima producción. Quiere que la efectividad general de su equipo (OEE) esté en el rango de 65 a 85 por ciento porque una máquina solo genera dinero cuando está funcionando.
“Entonces, con solo obtener esa información (verde, amarillo, rojo), puedo rastrear y generar tendencias a lo largo del tiempo y al menos ver cuándo se han producido interrupciones y por cuánto tiempo”, dijo Klippstein. “Y luego daría el siguiente paso y diría:‘¿Por qué ocurrió esto y por qué continúa ocurriendo todos los días a las 2:30?’ Entonces, ahora puedo poner las cosas en tendencia. Al menos eso me da un paso en la dirección correcta”.
Christopher Rezny, gerente regional central del proveedor de automatización de fábricas Fastems, dijo que si bien MT Connect y el software de Okuma son muy buenos vehículos para la recopilación de datos, la cantidad limitada de datos disponibles de una máquina heredada no es su única desventaja en comparación con las máquinas modernas.
“Las interfaces de máquinas heredadas más antiguas con otro software interno que se está utilizando, digamos un sistema ERP como ejemplo, también son muy limitadas o inexistentes”, dijo. "También puede haber problemas relacionados con los mecanismos de retroalimentación de estas máquinas más antiguas en relación con los protocolos de seguridad para el usuario".
Los trabajadores de planta deben estar preparados para el cambio
A pesar de las limitaciones descritas por Rezny, hay muchos datos y máquinas para que empresas como Okuma y Excellerant Manufacturing puedan trabajar.
“La mayoría de los talleres tienen equipos heredados”, dijo John Carpenter, presidente de Excellerant Manufacturing. “La mayoría de la gente acude a nosotros debido a nuestra historia con equipos heredados, conociendo esos gabinetes por dentro y por fuera, porque literalmente hemos conectado decenas de miles de máquinas CNC a lo largo de los años y hemos acumulado lo que yo llamaría secretos comerciales sobre cuál es la mejor manera de conectar este equipo heredado”.
El primer objetivo cuando se llama a un nuevo cliente es entender qué es lo que él o ella quiere. ¿Esa persona solo está tratando de traer datos de la fábrica para que todos estén al tanto de lo que está pasando?
“Se trata de qué problema estás tratando de resolver”, dijo Carpenter. “Y luego vamos a darte lo básico para empezar. La mayoría de las fábricas no han apreciado completamente los datos que están allí. Están gateando ahora mismo. Entraré en las tiendas y sentiré lástima por ellos porque ni siquiera han llegado a la etapa de rastreo”.
Carpenter recordó a un cliente en el que la gerencia quería transparencia básica:datos de lo que sucedía en el taller. Y los trabajadores de la planta se resistían a recopilar los datos por temor a que el Gran Hermano los observara.
Carpenter dejó el problema en manos de la gerencia del taller. Pero reconoció que los trabajadores no tenían elección. Sabía que los líderes de las tiendas buscaban datos para medir la producción y mejorar los procesos, no como una táctica de Gran Hermano. Desafortunadamente, la gerencia no había preparado a sus empleados para la mudanza.
“Abre tantos ojos en tantos niveles, pero su gente tiene que estar preparada para el cambio”, dijo.
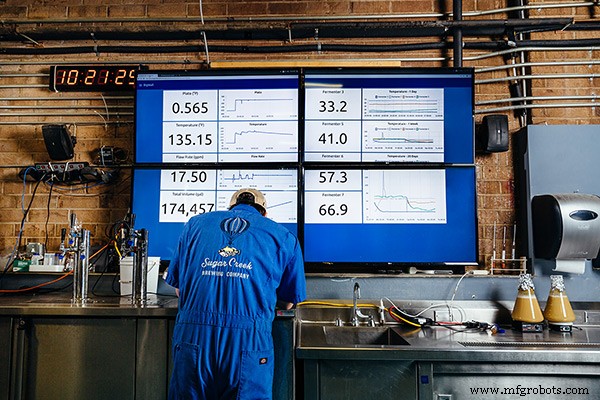
Una vez que se está rastreando lo básico, ¿estamos recortando? Si estamos recortando, ¿está al 100 por ciento? Y si no es así, ¿estamos en un modo de producción reducido? Y los datos se introducen en la plataforma de comunicaciones y datos de la máquina en tiempo real de Excellerant, es posible agregar una miríada de sensores y transductores para obtener más datos.
Se pueden incorporar sensores para medir temperatura, vibración, presión, flujo, concentración y más.
“Tienes que determinar qué es importante”, dijo Carpenter. “Podemos recopilar todo tipo de datos desde un punto en un taller. Hay una gran cantidad de datos cuando ingresa al análisis de vibraciones y roturas de herramientas. La lista sigue y sigue.”
Siempre hay una manera de recopilar más datos, pero a veces se vuelve prohibitivo, dijo. El propietario de la tienda debe determinar cuánto quiere gastar en un sensor para llevar sus datos al siguiente nivel.
"Normalmente, cuando envuelves esto en algún tipo de proyecto OEE, es un retorno de la inversión rápido", dijo Carpenter.
Conoce las preguntas que debes hacer
“Obviamente, este es un problema de toda la industria, pero las preguntas que recibimos generalmente se dividen en dos categorías”, dijo Cory Weber, arquitecto senior de IoT industrial en Bosch Rexroth. “Es:¿Cómo puedo aumentar la calidad de mi producción usando IoT o usando IIoT? O es:¿Cómo puedo aumentar mi eficiencia?
“La otra pregunta que surge es:¿Cómo disminuyo mis costos de producción?”
Además de ayudar a responder estas preguntas relacionadas con la producción, Weber estima que el 90 por ciento de los clientes desean visualización en tiempo real y monitoreo de máquinas herramienta, en el sitio y de forma remota.
"Es el primer paso, ¿verdad?" él dijo. "¿Qué está haciendo mi [línea automatizada o máquina-herramienta]?"
La solución de Bosch Rexroth para exprimir los datos de las máquinas heredadas es una puerta de enlace de IoT llamada PR-21, que es una pequeña computadora de placa única que está reforzada para entornos industriales. También tiene una plataforma IIoT, ctrlX CORE, para extraer y procesar datos y moverlos al almacenamiento en un servidor local o en la nube.
Una de las aplicaciones más comunes que Weber ha visto para usar los datos recopilados es el mantenimiento preventivo.
Los ajustes inteligentes basados en datos en un programa de mantenimiento son una forma de mantener las máquinas herramienta funcionando mientras se reducen los costos de producción al reducir los desechos.
"Sé que incluso en nuestras propias instalaciones hemos hecho cosas como cambiar a horas de uso en lugar de mantenimiento programado [calendario]", dijo Weber.
Por ejemplo, Bosch Rexroth tiene un área de prueba hidráulica donde los trabajadores solían cambiar el fluido cada dos semanas. Después de poner un monitoreo continuo en la máquina, pudieron revisar el programa de reemplazo de fluidos a uno basado en el tiempo de uso frente al tiempo calendario.
“Cuando habla de 50 a 60 galones de fluido hidráulico o más, eso puede resultar costoso”, dijo.
Otros tipos de fluidos tienen parámetros establecidos que deben cumplirse para su uso óptimo, ya sea en función de la concentración, la exposición al calor u otros factores.
“Si puede realizar pruebas con regularidad, puede cambiar su mantenimiento según sea necesario y puede ahorrar mucho dinero y proteger su calidad”, dijo Weber. "Es un punto de venta atractivo y una fruta relativamente madura".
Weber adquirió conocimientos de dominio para la fabricación mientras crecía:su padre es dueño de una pequeña empresa de fabricación. Sin embargo, su educación es en tecnología de la información. Tanto el conocimiento del dominio de fabricación como la inteligencia de datos son necesarios para beneficiarse de la implementación de la Industria 4.0, dijo.
“Se necesita a alguien que entienda el proceso real”, dijo. “Y alguien que entiende el proceso puede ver los datos y decir:'Esto no se parece a lo que se supone que debe ser'”.
Una vez que los datos están disponibles, las posibilidades son infinitas, dependiendo de cuánto desee procesarlos el usuario.
Si el dueño de una tienda tiene la suerte de tener a alguien con experiencia real en ciencia de datos, incluso puede aventurarse en la inteligencia artificial.
"Se trata de recopilar suficientes datos para que sean valiosos y luego, y no puedo enfatizar esto lo suficiente, saber qué preguntas quieres hacer sobre los datos", dijo.
Los consejos relacionados con los datos de Weber, por supuesto, se aplican tanto a las máquinas nuevas como a las heredadas. La minería de datos para operaciones inteligentes se aplica a ambos.
Sistema de control de automatización
- Los gemelos digitales pueden ser la ventaja inteligente para IoT en el sector de fabricación - Parte 2
- Cómo recopilar datos de sistemas heredados para mejorar las operaciones
- Soldadura robótica:¿Puede encontrar el ROI para operaciones de producción de lotes pequeños?
- ABB pone a prueba una solución de automatización para centros de datos
- Arch Systems se asocia con Flex para la transformación de datos de fabricación
- Actualizaciones de hogares inteligentes para la vida moderna
- Equipo heredado e IIoT:¿Puedes enseñarle nuevos trucos a un perro viejo?
- Cómo los fabricantes pueden usar Analytics para una mejor experiencia del cliente
- La automatización industrial da paso a la automatización de la información
- Tres formas en que la IA mejora las operaciones de fabricación
- Recursos humanos efectivos para el entorno de fabricación moderno:¿cuál es el secreto?