Cómo simplificar la arquitectura de control de los robots de coordenadas cartesianas
Por Barry Weller, director de producto de Mitsubishi Electric
Para seguir siendo competitivos, generalmente se acepta que las industrias deben adoptar estrategias de fabricación ajustada para mejorar la eficiencia del proceso.
Una acción clave puede ser reducir el número de piezas, es decir, el número de componentes de un conjunto o sistema. Esto es particularmente desafiante cuando se trata de aplicaciones de movimiento de coordenadas cartesianas (lineales) de alta precisión.
En estos casos, los fabricantes de máquinas a menudo necesitaban utilizar tanto PLC como controladores numéricos informáticos (CNC) para gestionar completamente el movimiento dentro de la máquina, hasta ahora.
Los robots de coordenadas cartesianas se utilizan ampliamente para automatizar funciones de máquinas, como el corte mecánico, láser o por plasma, y entregan rápidamente artículos de alta calidad que son uniformes y se pueden personalizar en gran medida.
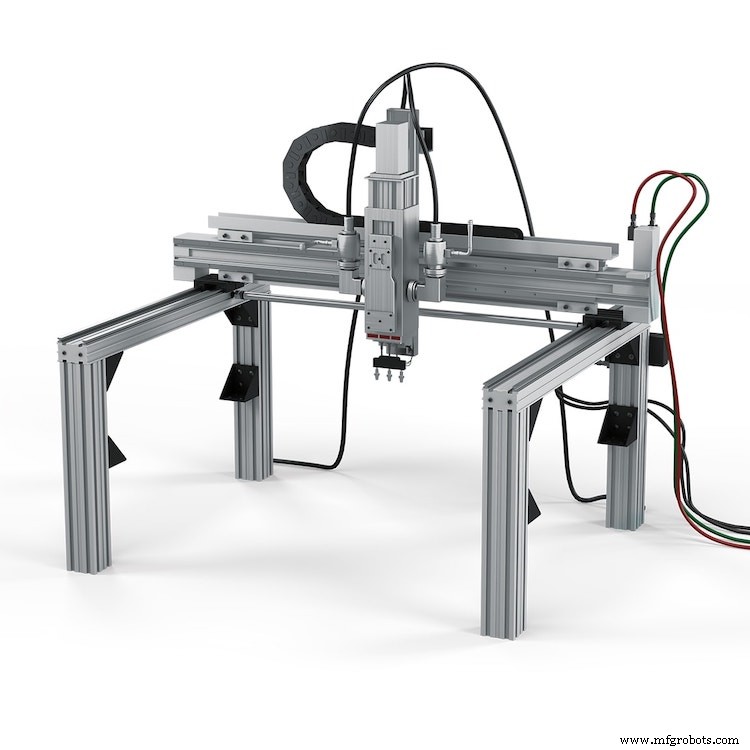
Si bien un robot de coordenadas cartesianas y una máquina CNC (control numérico por computadora) no son necesariamente lo mismo, el movimiento de ambos generalmente se controla mediante un sistema CNC.
La razón de esto radica en la simplicidad de programar trayectorias de control de movimiento con controladores numéricos computarizados y su lenguaje G-Code.
Este lenguaje de programación es distinto porque instruye a las máquinas sobre dónde y cómo moverse en función de imágenes y archivos de diseño/fabricación asistidos por computadora (CAD/CAM).
G-code lee archivos CAD/CAM para los productos finales previstos y los convierte en trayectorias y direcciones para servoaccionamientos CNC dentro del robot de coordenadas cartesianas.
Como resultado, los movimientos altamente exactos, precisos y reproducibles pueden crear incluso las formas y contornos 2D más complicados e inusuales.
Si bien las soluciones CNC funcionan bien como controladores de robots, no pueden monitorear ni guiar otros componentes, como válvulas solenoides, abrazaderas y mangueras de aire; para hacerlo, la unidad necesita un PLC.
En teoría, esto podría manejar el control estricto de la herramienta y la retroalimentación para todas las diferentes partes de automatización, eliminando la necesidad de sistemas CNC.
Sin embargo, escribir código de control de movimiento para robots de coordenadas cartesianas con cualquiera de los cinco lenguajes de PLC sería todo un desafío. En consecuencia, los fabricantes de máquinas y los usuarios deben usar estos dos sistemas de control diferentes para una máquina.
Sin embargo, esta solución está lejos de ser ideal:el hardware adicional solo aumentará el costo total de propiedad de la máquina y también puede afectar el tiempo de construcción/puesta en marcha.
De hecho, dos unidades de control separadas deben compartir información de tiempo crítico, lo que aumenta los tiempos de ciclo potenciales y aumenta la probabilidad de fluctuaciones en la comunicación que podrían desincronizar los procesos basados en PLC y CNC en la misma máquina.
Un enfoque holístico de la programación, el control y la retroalimentación del movimiento
Para abordar estos problemas, los fabricantes de componentes y sistemas de automatización de fábricas están comenzando a invertir en tecnologías de control de movimiento que cruzan los límites entre los PLC y los sistemas CNC para crear controladores de máquinas integrados que combinan funciones clave de ambas soluciones.
Un buen ejemplo es el controlador de movimiento MELSEC iQ-R de Mitsubishi Electric y su biblioteca complementaria G-Code. Al elegir esta solución, los fabricantes de máquinas pueden usar servos de uso general y PLC de la serie MELSEC iQ-R para implementar capacidades CNC, si es necesario, instalando la biblioteca G-Code.
Esto permite la programación de perfiles y trayectorias de corte complejas de alta precisión en código G sin necesidad de controladores numéricos informáticos.
Más precisamente, la función adicional ayuda al sistema a seguir las instrucciones de programación específicas del PLC, como Motion SFC (gráficos de funciones secuenciales), así como a generar y leer automáticamente perfiles de movimiento desde archivos CAD/CAM.
Los programas G-Code, disponibles en formato de texto, se pueden editar fácilmente en las HMI de Mitsubishi Electric o con cualquier editor genérico.
Al eliminar la necesidad de hardware de componentes de PLC y CNC por separado, el sistema MELSEC iQ-R puede sincronizar los diferentes procesos dentro de una máquina y reducir los tiempos de ciclo.
Además, la posibilidad de usar una única solución para varias aplicaciones, incluido el mecanizado CNC y cambiar fácilmente entre ellas, permite a los fabricantes de máquinas usarla para controlar una línea de producción completa.
Como resultado, las empresas pueden beneficiarse de un sistema altamente flexible, rápido y rentable que realmente agiliza sus procesos industriales al mismo tiempo que ofrece calidad y consistencia.
Sistema de control de automatización
- Cómo reducir el costo de retrabajo en la fabricación
- Cómo garantizar el mejor rendimiento de la máquina de estado Qt
- Cómo elegir la máquina CNC adecuada
- El software de B&R aprovecha mejor el potencial de los robots
- Cómo los robots de software pueden ayudarlo a tomar el control de la 'nueva normalidad'
- La máquina de marketing:cómo la tecnología puede impulsar el éxito de los fabricantes
- Cómo la robótica colaborativa está estimulando la innovación en el sector manufacturero
- Cómo elegir la máquina estuchadora adecuada
- Cómo elegir la máquina de corte por chorro de agua adecuada
- ¿Qué tan brillante es el futuro de la automatización?
- ¿Cómo se controla la velocidad de un motor hidráulico?