¿Cuál es el verdadero significado detrás de la mantenibilidad
La capacidad de mantenimiento es un término que a menudo se usa cuando se habla de mantenimiento y confiabilidad. Pero, ¿sabe realmente lo que significa ser de fácil mantenimiento y cómo debería usarse el término?
Si no, lo tenemos cubierto. Desplácese hacia abajo para saber qué es mantenibilidad, se puede medir y cómo el diseño de activos impacta la variable de mantenibilidad.
¿Qué es la capacidad de mantenimiento?
La capacidad de mantenimiento es uno de los conceptos clave para los fabricantes de equipos, operadores y administradores de activos. En su forma más simple, mantenibilidad significa "facilidad de mantenimiento".
Una manera fácil de definir la capacidad de mantenimiento es a través de un evento de pinchazo de un neumático de automóvil. No es una coincidencia que se puedan instalar llantas de repuesto en todas las ubicaciones de llantas y que los fabricantes de automóviles proporcionen pernos en cada llanta que se pueden apretar y aflojar con el mismo tamaño de llave.
Los profesionales de la gestión de activos, responsables del buen funcionamiento de maquinaria complicada y crítica en todo tipo de industrias y sectores de servicios, se enfrentan a una situación similar cada vez que un activo está inactivo por mantenimiento no planificado o programado.
El objetivo es poner el equipo en funcionamiento lo más rápido posible, con el menor costo posible de mantenimiento. Más fácil de realizar reparaciones y mantenimiento en un activo, mayor es su capacidad de mantenimiento .
Mantenibilidad y su relación con confiabilidad y mantenimiento
Los conceptos de confiabilidad, disponibilidad y mantenibilidad están estrechamente relacionados, y juntos equipan a los administradores de activos con las herramientas para evaluar el desempeño de cualquier programa de administración de activos.
El concepto de RAM:confiabilidad, disponibilidad y capacidad de mantenimiento
El acrónimo RAM combina los tres términos técnicos para significar un marco en el que los activos se diseñan y operan utilizando las mejores prácticas para minimizar el tiempo de inactividad y los costos del ciclo de vida.
Ese marco mencionado anteriormente se utiliza para realizar análisis de RAM cuando:
- La confiabilidad es la probabilidad de que un activo realice su función deseada en condiciones predeterminadas durante un período de tiempo determinado. La confiabilidad define la frecuencia de fallas y determina los patrones de tiempo de actividad. A menudo se mide a través del tiempo medio entre fallas (MTBF).
- La capacidad de mantenimiento describe qué tan pronto se puede reparar la unidad / sistema, lo que determina los patrones de tiempo de inactividad. Puede cuantificarse utilizando el tiempo medio de reparación (MTTR). Cuanto menor sea el MTTR, mayor será la capacidad de mantenimiento del activo.
- La disponibilidad representa el porcentaje de tiempo de actividad durante un período de tiempo específico. Está determinado por la confiabilidad y la facilidad de mantenimiento. Dado que considera el tiempo de funcionamiento del sistema y el tiempo de inactividad, tanto el MTBF como el MTTR son parte de su cálculo.
En general, los estudios de RAM se utilizan como herramienta para evaluar las capacidades de un sistema de producción. Por lo tanto, cualquier instalación que dependa de activos físicos puede utilizarla para optimizar el rendimiento operativo.
¿Podemos realizar un seguimiento y medir la capacidad de mantenimiento?
Una métrica importante para medir la capacidad de mantenimiento es el costo gastado en mantener un activo. El costo de mantenimiento como porcentaje del valor del activo de reemplazo (RAV) generalmente se monitorea para garantizar que los costos estén dentro de los rangos obtenidos de la referencia de la industria. Un menor costo de mantenimiento gastado en un activo implica una mayor capacidad de mantenimiento.
De las discusiones anteriores, es evidente que alta capacidad de mantenimiento se indica por MTTR bajo y bajos costos de mantenimiento .
Para garantizar que un activo tenga los niveles deseados de mantenibilidad, es necesario un análisis exhaustivo de mantenibilidad para la fase de diseño del equipo. Implica consideraciones como:
- utilizando materiales y componentes fácilmente disponibles
- utilizando conexiones estándar y atornilladas
- habilitar la identificación de fallas
- asegurando la facilidad de montaje y desmontaje
- etc.
Estas consideraciones se analizan en detalle en la siguiente sección.
Diseño para la facilidad de mantenimiento
Existen varios estándares, mejores prácticas y requisitos de mantenibilidad que se pueden seguir para garantizar que un activo sea altamente mantenible. La mayoría de estas pautas se pueden agrupar en general en las siguientes seis categorías.
1) Estandarización
En lugar de utilizar varios tipos diferentes de piezas y componentes, se recomienda minimizar la variedad entre las piezas para minimizar los requisitos de inventario, herramientas y capacitación.
Una implementación común de esta regla es el uso de conexiones USB estándar en dispositivos electrónicos. Se puede usar un puerto USB para conectar (o cargar) una variedad de accesorios de computadora diferentes sin ningún compromiso en la funcionalidad.
La práctica de la estandarización se emplea comúnmente en el espacio industrial para minimizar los tipos y tamaños de pernos y sujetadores dentro de cualquier conjunto de activos. Esto tiene beneficios obvios como se discutió anteriormente en el artículo.
En la práctica, los diseñadores pueden lograr este objetivo aumentando el número de pernos y tornillos, siempre que sea posible, para obtener resistencia adicional, en lugar de aumentar el diámetro y el tamaño del sujetador.
2) Modularización
La modularización se refiere al diseño de máquinas complicadas a partir de bloques de construcción más pequeños (módulos o subconjuntos) para que cada bloque se pueda mantener de forma independiente entre sí. Esto mejora la capacidad de mantenimiento de las siguientes formas:
- Al facilitar desmontaje y montaje sencillos de las máquinas, mejorando así la accesibilidad a la pieza que requiere mantenimiento o sustitución.
- A menudo es más rentable reemplazar el subensamblaje en lugar de reparar la pieza dañada. El conjunto dañado se puede reparar posteriormente y utilizar como repuesto. Estas prácticas reducen significativamente el MTTR para cualquier activo.
- Actualizaciones a nivel del sistema generalmente son posibles actualizando uno o más subconjuntos en lugar de cambiar todo el equipo.
Una licuadora simple es un buen ejemplo de modularidad. La base que alberga el motor impulsor está diseñada para separarse de los frascos, que son fácilmente extraíbles y reemplazables si las cuchillas se dañan (o si está más interesado en moler especias que en batidos).
Todos los dispositivos electrónicos que nos rodean, desde computadoras portátiles hasta teléfonos inteligentes, emplean principios de modularización que permiten un mantenimiento rápido al reemplazar pantallas rotas, discos duros quemados, etc.
En las industrias de energía, los rotores de turbina están diseñados de tal manera que las palas de la turbina se ensamblan sobre ruedas de turbina, que a su vez se montan en el eje del rotor. Esto permite reemplazar fácilmente las palas dañadas y, en ocasiones, mejorar el rotor de la turbina mediante la instalación de diseños de palas más eficientes.
3) Intercambiabilidad
El uso de componentes genéricos comúnmente disponibles en lugar de piezas de ajuste personalizado permite al usuario final utilizar repuestos alternativos del mercado si los repuestos originales no están disponibles o tienen plazos de entrega más largos. En esencia, es una optimización fácilmente alcanzable de las actividades de mantenimiento.
Un ejemplo común es el uso de tamaños de cojinetes estándar en bombas y otra maquinaria. La mayoría de los fabricantes de rodamientos más populares fabrican rodamientos con tamaños estándar. Si un rodamiento SKF está dañado y no hay un reemplazo disponible localmente, generalmente es posible buscar un rodamiento similar en el catálogo de FAG y utilizar ese en su lugar.
4) Anuncio de avería
Siempre que un activo no esté realizando su función deseada, esta condición defectuosa del activo debe ser obvia para el operador en tiempo real, de modo que la tarea de mantenimiento requerida se pueda planificar y emprender antes de que ocurra una falla catastrófica.
Por ejemplo, el indicador de temperatura en un automóvil informará al conductor sobre los primeros signos de sobrecalentamiento del motor para que se puedan tomar medidas correctivas a tiempo.
La maquinaria complicada en industrias pesadas (procesos químicos, energía, manufactura, etc.) tiene instalados sistemas elaborados de monitoreo. Estos sistemas incluyen sensores de temperatura, sensores de presión, dispositivos de monitoreo de vibraciones y otros equipos de monitoreo de condición que se utilizan como parte de CBM y / o mantenimiento predictivo.
Cualquier desviación de los límites establecidos genera alarmas para el operador, quien puede tomar las medidas necesarias y notificar al personal relevante. Pueden usar esa información para la asignación de los recursos necesarios y para programar el trabajo de mantenimiento, generalmente a través de un sistema de gestión de mantenimiento computarizado (CMMS).
5) Aislamiento de fallas
Siempre que un activo se avería o funciona mal, el primer paso es diagnosticar la causa raíz del problema. Si la causa raíz no es obvia, se dedica mucho esfuerzo (y por lo tanto tiempo y costo) a la inspección y el diagnóstico del componente defectuoso.
Esta pérdida de tiempo y recursos se puede evitar fácilmente incorporando características de diseño que limitan la influencia de los factores humanos, hacen que el problema sea obvio y, en consecuencia, simplifican el mantenimiento correctivo necesario.
Por ejemplo, la mayoría de los electrodomésticos electrónicos (como lavadoras y lavavajillas) muestran un código de error para problemas que ocurren comúnmente y / o modos de falla.
Código de error E1 le dirá que el tubo de descarga de la lavadora está bloqueado. Puede resolver el problema reajustando la tubería y eliminando la fuente del bloqueo. ¿Qué sucede cuando se muestra un código de "error desconocido"? Se debe invertir una cantidad significativa de tiempo y dinero en contratar a un técnico que pueda solucionar y reparar el problema.
En la sección anterior se mencionó que los sistemas de monitoreo se instalan en la maquinaria para la detección de fallas. Si bien una señal de vibración alta puede decirle al operador que algo anda mal con la máquina, un análisis detallado de la señal de vibración puede permitirle a un ingeniero de diagnóstico de vibraciones capacitado identificar exactamente la pieza o componente que necesita mantenimiento (o reemplazo).
En ausencia de un sistema de monitoreo de este tipo, se debe adoptar una estrategia de prueba y prueba costosa y que requiere mucho tiempo, lo que reduce la capacidad de mantenimiento del activo en el proceso.
6) Identificación y etiquetado
Los activos, equipos, conjuntos y subconjuntos deben ser identificables entre sí para facilitar la comunicación y el mantenimiento de registros. Los operadores de activos logran esto asignando etiquetas únicas y significativas a los activos y componentes.
Por ejemplo, a los intercambiadores de calor se les asigna una etiqueta alfanumérica que comienza con la letra "E" seguida de guiones y números. De manera similar, a las bombas se les pueden asignar etiquetas en la secuencia de "P-XXX", etc. El fabricante proporciona números de pieza específicos a los componentes dentro del equipo para que se puedan realizar consultas con respecto a las piezas específicas sin ninguna confusión.
Los profesionales de la gestión de activos utilizan este elaborado sistema de identificación para mejorar la mantenibilidad de diversas formas.
La asignación de números de pieza únicos asegura que las piezas correctas estén dispuestas para un trabajo de mantenimiento, evitando tiempos de inactividad innecesarios. Los registros históricos específicos del equipo y las instrucciones de mantenimiento pueden estar fácilmente disponibles (generalmente a través de un CMMS) utilizando el sistema de etiquetado del equipo que ayuda al personal de mantenimiento a identificar el activo correcto durante las actividades en el campo.
Otras formas de mejorar la capacidad de mantenimiento
La compra de activos que sean fáciles de mantener es un factor importante a considerar durante el proceso de adquisición. Después de todo, usted no puede opinar sobre cómo se diseña el equipo.
Pero hay aspectos de mantenibilidad sobre los que sí tienes cierto control. Hay varias pequeñas mejoras que puede realizar para simplificar el trabajo de mantenimiento en activos complejos. Deberías:
- Proporcionar acceso rápido a listas de verificación de mantenimiento preventivo , dibujos, registros y procedimientos. La forma más sencilla de hacerlo es almacenarlos en una base de datos CMMS. Los técnicos y mecánicos pueden simplemente abrir su aplicación de mantenimiento móvil y obtener el recurso requerido.
- Mejorar las habilidades de los trabajadores y operadores de mantenimiento. Incluso una tarea sencilla puede resultar difícil para manos inexpertas. El departamento de mantenimiento debe garantizar una formación de mantenimiento adecuada, especialmente si se ponen en marcha nuevos requisitos.
- Estandarice el equipo y el inventario de MRO. La organización debe tratar de utilizar los mismos tipos de equipos y herramientas (cuando sea posible y apropiado) para minimizar la necesidad de capacitación adicional y uso indebido.
- Estandarice el trabajo de rutina. Una forma de reducir los costos de operación y mantenimiento es aumentando la productividad de los empleados y reduciendo el número de errores humanos. Junto con los programas de formación, la estandarización de los procedimientos operativos es la forma de hacerlo.
- Céntrese en el mantenimiento proactivo. Un mantenimiento más proactivo conduce a menos averías importantes, que requieren una cantidad significativamente mayor de recursos y habilidades para abordar.
Reducir el mantenimiento reactivo en un 73,2%
Ver los resultados que disfruta Red Hawk con Limble
Lea nuestroCaso de estudio
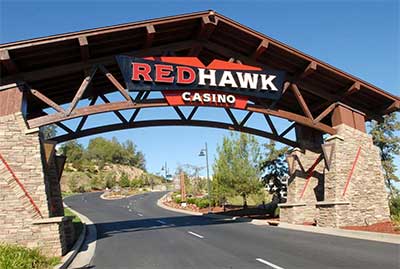
Estos pequeños cambios pueden marcar una gran diferencia a largo plazo.
Conclusiones clave
El objetivo principal de cualquier profesional de mantenimiento es garantizar que el equipo realice la función deseada con una interrupción mínima.
La clave para lograr este objetivo es seguir las mejores prácticas con respecto a la confiabilidad y mantenibilidad de los activos. La capacidad de mantenimiento, o "facilidad de mantenimiento", se puede monitorear a través de métricas como el tiempo medio de reparación (MTTR) y el costo de mantenimiento por valor de activo de reemplazo.
Los activos se pueden diseñar para lograr un mayor nivel de mantenibilidad garantizando el uso de componentes y ensamblajes estandarizados, empleando diseños modulares o por bloques, permitiendo técnicas simples de detección de fallas y utilizando sistemas de identificación y etiquetado.
Para colmo, los gerentes de planta y de mantenimiento deben considerar la implementación del software CMMS para simplificar la ejecución del trabajo de mantenimiento y mejorar indirectamente la capacidad de mantenimiento de sus instalaciones.
Mantenimiento y reparación de equipos
- ¿Qué es el cambio de plataforma en la nube?
- ¿Qué hay detrás del cambio a los agentes de voz personalizados?
- ¿Qué está llevando a la IA al límite?
- ¿Qué es la transformada de Fourier?
- ¡¿Qué hago con los datos ?!
- El futuro de la gestión de activos
- ¿Qué es la mantenibilidad garantizada?
- ¿Qué es la economía circular?
- Motor de CC frente a motor de CA:¿cuál es la diferencia?
- ¿Qué es GASB 35?
- ¿Qué es GASB 34?