Ya no es la fundición de tu abuelo
Las fundiciones continúan evolucionando mediante la adopción de tecnología innovadora y seguridad en el lugar de trabajo
Una fundición es una planta industrial donde el metal se funde y se moldea en formas específicas vertiéndolo en un molde. El proceso en sí tiene siglos de antigüedad. En la actualidad, aproximadamente el 90 % de todos los productos manufacturados dependen de la fundición de metales para sus componentes, siendo los automóviles y camiones el mercado más importante. El aluminio, el hierro y el acero son las aleaciones más comunes que se procesan en las fundiciones.

Historia de las fundiciones
Durante generaciones, la humanidad ha encontrado formas innovadoras de utilizar las materias primas que se encuentran en la naturaleza:trabajar con metales ha sido parte de la civilización desde la antigüedad. Los arqueólogos han descubierto una amplia gama de artefactos, desde objetos de culto hasta herramientas y armas de guerra. De hecho, las épocas de la historia humana han recibido el nombre de los avances en la tecnología del metal:la Edad del Cobre, la Edad del Bronce y la Edad del Hierro. El molde más antiguo conocido encontrado por los historiadores es un hacha de cobre, que fue descubierta enterrada con una momia de aproximadamente 3300 a.C.
La fundición y el horno se originaron en Mesopotamia y regiones de Irak y Siria. Fundición de arcilla y pozos de fuego calientes trabajados para derretir y dar forma al cobre, el oro y la plata. Estas fundiciones primitivas fundieron cobre y fueron capaces de crear formas más complejas, pero no fue hasta que se introdujo el estaño que el trabajo del metal hizo un avance significativo. La adición de estaño redujo la temperatura a la que los dos metales se fundieron y formaron el bronce, la primera aleación.
A lo largo de siglos y generaciones sucesivos, se desarrollaron y perdieron diversas técnicas de fundición y trabajo del metal, a medida que surgían diferentes civilizaciones para dominar el panorama cultural y tecnológico. Es en la edad media donde se documentan por primera vez los procesos de fundición del metal en las fundiciones. Vannoccio Biringuccio (1480-1539) es conocido como el "padre de la industria de la fundición", ya que se convirtió en el autor del primer manual sobre fundiciones, a partir del cual se desarrolló aún más la tecnología.
La primera fundición oficial se conocía como "Canon Shop", que se construyó en Moscú en 1479. La industria de fundición de metales de los siglos XIV y XV en Europa se hizo conocida por la producción de campanas, cánones y balas de cañón de bronce y hierro.
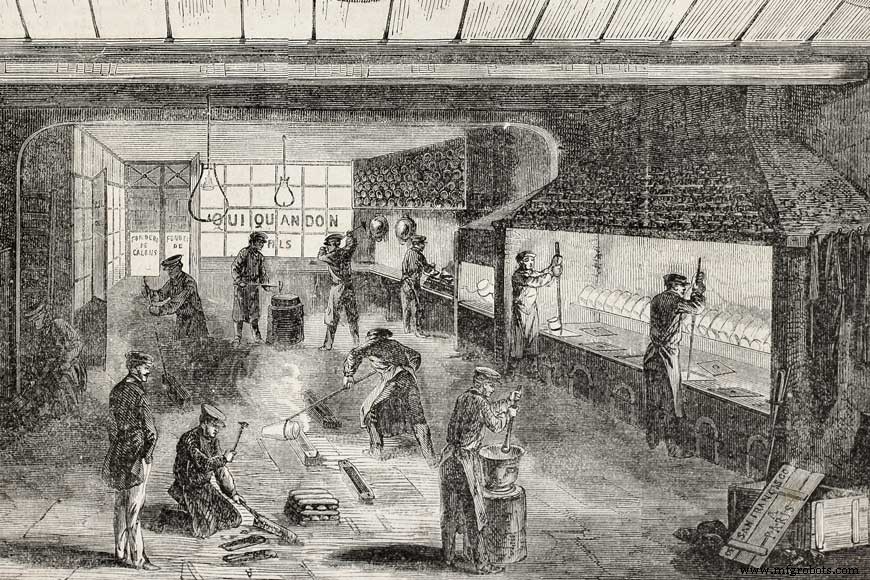
En América del Norte, la industria de fundición de metales creció en apoyo del progreso de los colonos en todo el Nuevo Mundo. Se necesitaban herramientas, herraduras y vías férreas más avanzadas y resistentes para satisfacer la demanda de los pueblos y ciudades en desarrollo.
Saugus Iron Works fue la primera fundición en los EE. UU. y fue encargada en 1642 por los fabricantes de acero europeos. Establecido en Lynn, Massachusetts, se hizo conocido como el lugar de nacimiento de la industria estadounidense del hierro y el acero.
Desarrollos en tecnología de fundición
Los procesos de fundición se desarrollan continuamente para mejorar la calidad de los productos y la eficiencia de la producción, y aprovechar las nuevas tecnologías. Los avances en el desarrollo han permitido avances significativos en la fundición de metales en momentos clave de la historia de la industria.
Desarrollos de hornos
La migración del carbón al coque como combustible para las fundiciones fue iniciada por Abraham Darby. Su innovación en 1709 condujo a una mejora significativa en la eficiencia y el costo, y permitió la construcción de hornos mucho más grandes de lo que antes era posible.
Horno de cúpula
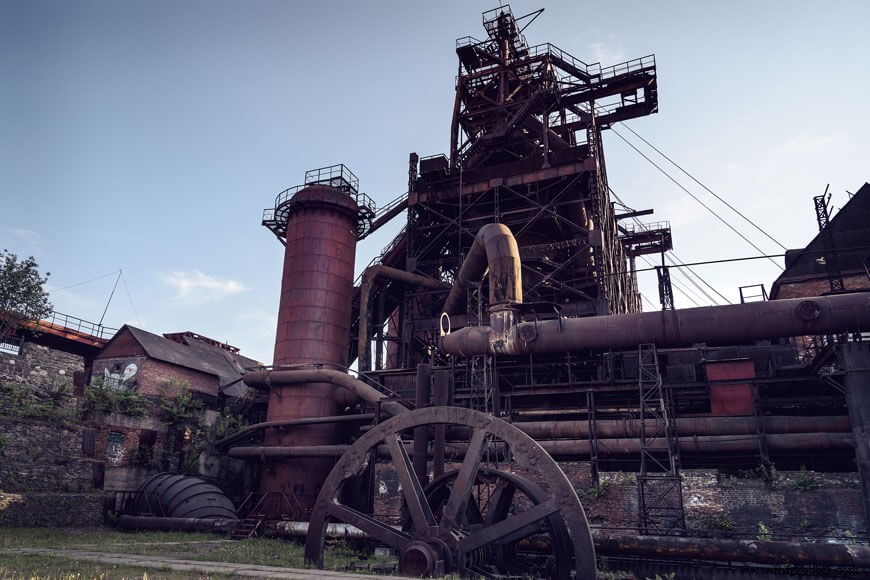
El horno de cúpula fue desarrollado en 1720 por el francés René-Antoine Ferchault de Réaumur. La estructura en forma de cúpula tiene una abertura para suministrar la carga y puertas con bisagras en la base para vaciar el horno después de apagarlo. Un lecho de coque soporta la carga de fundente de metal fundido, coque y piedra caliza por encima de las toberas (aberturas por donde se suministra aire). Aunque el horno de cúpula una vez dominó el panorama de la fundición, ahora ha sido reemplazado en gran medida por hornos de arco eléctrico y de inducción eléctrica más eficientes.
Proceso del crisol
En la Inglaterra del siglo XVIII, Benjamin Huntsman fue el empresario detrás del desarrollo del proceso de crisol. Este fue el primer proceso en el que el acero podía fundirse por completo para producir un producto uniforme después de la fundición.
Horno de arco eléctrico
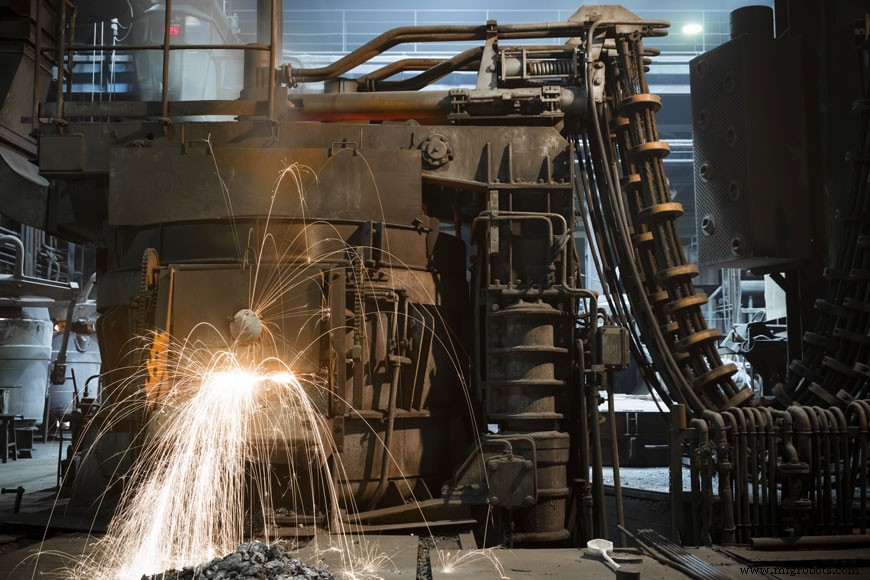
La introducción del suministro comercial de electricidad contribuyó a la invención de los hornos de arco eléctrico. Los electrodos de grafito crean el arco eléctrico y suministran corriente como fuente de energía para fundir el hierro. El primer horno de arco eléctrico fue creado en 1900 por Paul Héroult de Francia. En 1907, se estableció una planta comercial en los Estados Unidos. Estos hornos son más económicos a tasas de producción más bajas y pueden funcionar de forma intermitente, lo que brinda más flexibilidad a las fundiciones de metales.
Horno de inducción eléctrico
Los hornos eléctricos de inducción utilizan una corriente alterna de alta potencia que fluye a través de una bobina para inducir corrientes de Foucault en el metal, generando así calor, y actualmente se encuentran más comúnmente en las fundiciones de producción.
Desarrollos de fundición
En la antigüedad, la fundición de metales se hacía en moldes de arcilla. Uno de los grandes reyes asirios, Senacheribb, afirma haber perfeccionado la técnica de fundición de bronce y cobre en moldes de arcilla. Con el paso del tiempo, los avances tecnológicos transformaron el proceso de fundición, desde la fundición en arena hasta la tecnología electromagnética.
Fundición en arena
Vannochio Birringucio, el fundidor de finales del siglo XV y principios del XVI, escribió un libro sobre todas las formas de fundición y trabajos relacionados. El libro describe el uso de fundiciones en arena, la próxima fase importante de la tecnología de fundición. Inicialmente, la arena se mezclaba con arcilla como agente aglutinante para que el molde mantuviera su forma durante el vaciado, pero con el tiempo se han desarrollado nuevos tipos de arena y agentes aglutinantes.
La arena verde es uno de los materiales más comunes en uso hoy en día. Históricamente, la arena verde consistía en arena de sílice, arcilla de bentonita, agua y carbón marino. Sin embargo, el carbón marino ya no se usa comúnmente en la actualidad y ha sido reemplazado por otros materiales. Si bien la fundición en arena verde sigue siendo de uso común, los procesos "sin horneado", de fraguado químico o de fraguado en frío se están volviendo predominantes en las fundiciones actuales.
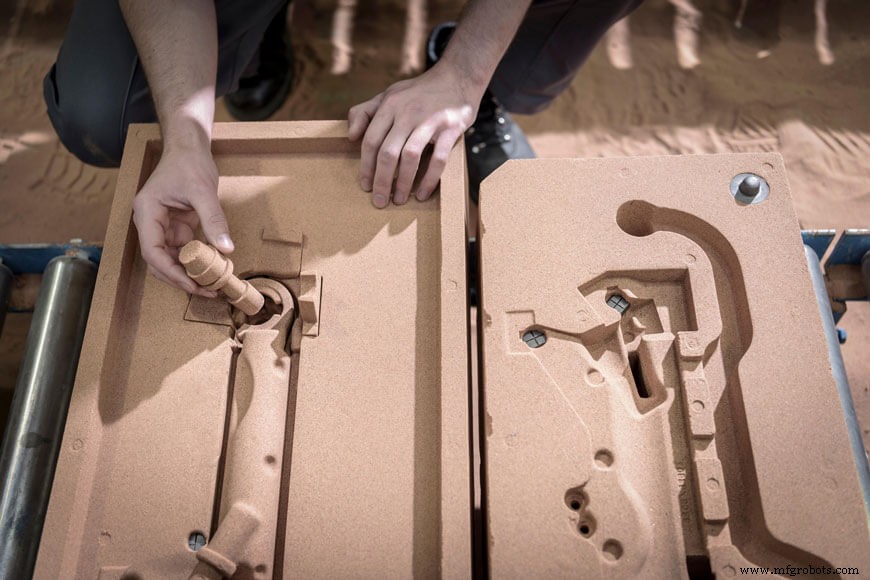
Fundición a presión
La fundición a presión y el moldeo por inversión son técnicas modernas que utilizan materiales recientemente disponibles para mejorar la calidad del acabado de la fundición y el costo de producción. La fundición a presión se caracteriza por forzar el metal fundido a alta presión en una cavidad de molde. Se utiliza una máquina de cámara caliente o fría según el tipo de metal que se va a fundir. Las fundiciones a presión son conocidas por proporcionar un buen acabado superficial y consistencia dimensional.
Colada continua
Quizás el avance más significativo en el proceso de fundición ha sido la introducción de la máquina de colada continua. El metal fundido se vierte en un molde y se retira lentamente para crear longitudes continuas de metal solidificado. La principal ventaja de este método de fundición de acero al carbono es la eliminación de algunos de los pasos de procesamiento posteriores. Estos productos semielaborados se pueden transformar más fácilmente en productos terminados mediante el laminado.
Moldes permanentes
En el siglo XXI, los procesos de fundición dieron otro paso adelante con la introducción de la tecnología electromagnética. Una bobina de inducción se envuelve alrededor de un molde enfriado por agua con campos electromagnéticos que generan corriente alterna.
Estos campos electromagnéticos pasan a través del metal que se está enfriando y provocan la formación de corrientes de Foucault en el metal fundido, lo que da como resultado dos resultados positivos:
- El contacto entre el metal de enfriamiento y la superficie del molde es "suave", lo que brinda una mejor calidad de acabado. En la fundición estándar enfriada con agua, se forma una piel gruesa de microestructura gruesa debido al contacto "duro" con el molde. Esta piel se elimina antes del laminado, lo que genera un desperdicio significativo de producto y un aumento de los costos.
- La homogeneidad del metal mejora considerablemente con una reducción de las segregaciones en los límites de grano.
Promociones de calidad
Sir Henry Bessemer fue el innovador detrás de nuevas técnicas para eliminar el carbono y el exceso de oxígeno del acero fundido que culminó con la invención del convertidor. Bessemer descubrió que soplar oxígeno a través del metal fundido provocaba una reacción con el carbono y el silicio del material, lo que eliminaba las impurezas pero también calentaba el material para facilitar el vertido.
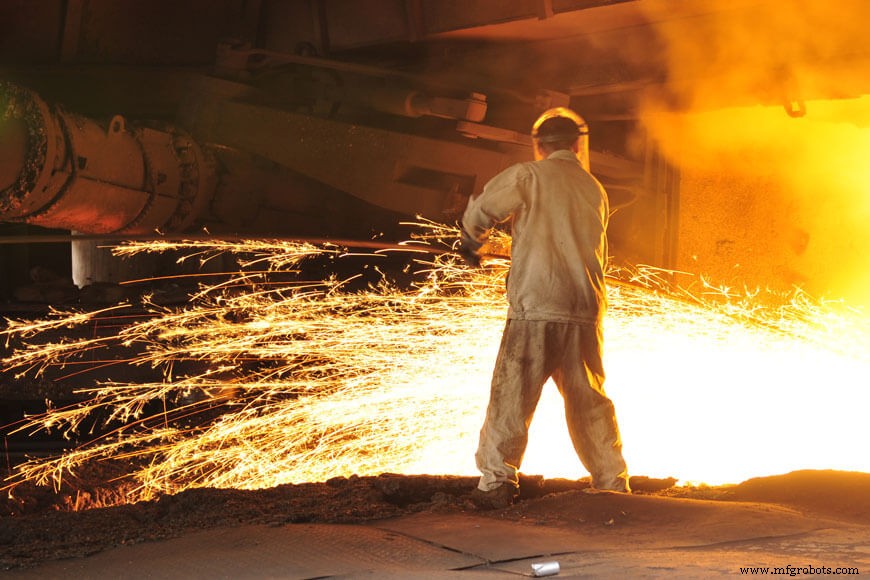
Los convertidores ahora se utilizan para grados finos de control de calidad al establecer proporciones precisas de contenido de carbono y agregar aleaciones y otros aditivos para las propiedades específicas requeridas del producto. En un horno de arco eléctrico, se puede inyectar oxígeno en el baño para “quemar” el carbono y muchos otros elementos e impurezas. Esto hace que el baño inicial sea lo más limpio posible y permite que la fundición alee la masa fundida al contenido perfecto. En la fusión por inducción, la fundición solo puede comenzar con un baño que se crea a partir de la alimentación o la chatarra fundida; el contenido químico de la chatarra debe coincidir con la química del baño que la fundición usa inicialmente.
Desarrollos en medición y control
Junto con los avances en los métodos de producción, ha habido avances en los métodos de prueba de laboratorio del metal fundido mientras la fabricación aún está en proceso. Las muestras pueden extraerse de convertidores y analizarse mediante espectrómetros o análisis de fluorescencia de rayos X. Esta retroalimentación en tiempo real de la composición química crea una oportunidad para que los fabricantes realicen ajustes antes del vertido, ahorrando tiempo y recursos valiosos debido a la repetición del trabajo.
Aunque un operador experimentado puede detectar defectos superficiales y fallas potenciales en el producto fundido a simple vista, la mejora en los métodos de prueba no destructivos ha brindado a los clientes más seguridad en la integridad del producto:
- El colorante penetrante y el polvo fluorescente se pueden suspender en aceite penetrante y aplicar a la superficie de la fundición terminada. Las grietas y los defectos de la superficie son inmediatamente visibles al aplicar el revelador o en presencia de luz ultravioleta.
- La inspección radiográfica es el método más efectivo para identificar orificios internos, grietas o inclusiones. El yeso se expone a la radiación de un tubo de rayos X y la imagen creada en la película radiográfica indica cambios en la densidad del yeso. La ventaja de este método es que la radiografía sirve como registro permanente, que puede acompañar al producto a lo largo de su ciclo de vida para el control de calidad y seguridad.
- La inspección de líquidos penetrantes (LPI) puede encontrar pequeñas grietas, poros u otras imperfecciones superficiales en fundiciones ferrosas y no ferrosas que son difíciles de ver a simple vista. LPI utiliza una solución de aceite de tinte de color en la superficie de la fundición que encuentra su camino hacia los defectos de la superficie. Una vez que se aplica un revelador especial, los defectos se vuelven claramente visibles.
- La inspección de partículas magnéticas (MPI) ayuda a identificar la ubicación de discontinuidades superficiales en metales ferrosos. También puede indicar defectos en el subsuelo si la fuerza de magnetización es suficiente para producir un campo de fuga en la superficie. En esta prueba, se induce un flujo magnético en material ferromagnético. Cualquier discontinuidad abrupta en su camino da como resultado un campo de fuga de flujo local. Si las partículas finamente divididas de material ferromagnético se acercan, ofrecen un camino de baja renuencia al campo de fuga y toman una posición que delinea aproximadamente sus límites efectivos. La fundición a inspeccionar se magnetiza y su superficie se espolvorea con el polvo magnético. Una corriente de aire a baja velocidad sopla el exceso de polvo, dejando que el defecto quede delineado por las partículas de polvo restantes. El polvo se puede aplicar mientras fluye la corriente de magnetización (método continuo) o después de que la corriente está apagada (método residual). Puede aplicarse seco o suspendido, en un destilado ligero de petróleo similar al queroseno.
Inspección de partículas magnéticas
La inspección de partículas magnéticas (MPI) es un tipo de prueba no destructiva que utiliza flujo magnético para determinar cualquier defecto superficial. Observe cómo un trabajador realiza pruebas no destructivas en una soldadura de petróleo y gas.
- La prueba ultrasónica (UT) identifica los defectos internos a través del sonido mediante el empleo de energía acústica de alta frecuencia que se transmite a una pieza fundida. UT permite la investigación del área de la sección transversal de una fundición y, por lo tanto, se considera un método de inspección volumétrica. La energía acústica de alta frecuencia viaja a través de la fundición hasta que golpea la superficie opuesta, interfaz o defecto. La interfaz o defecto refleja porciones de la energía que se recogen en una unidad receptora y se muestran para que el analista las vea. El patrón de desviación de energía puede indicar la ubicación y el tamaño de un defecto interno, así como el espesor de la pared y el número de nódulos de hierro dúctil. UT requiere conocimiento y experiencia para una interpretación precisa de los resultados, lo que aumenta el costo de la inspección.
Novedades en seguridad
Trabajar en una fundición es una ocupación peligrosa. Existen numerosos peligros químicos, mecánicos y de temperatura que deben controlarse para eliminar posibles daños a los trabajadores.
Una de las áreas clave que ha mejorado la seguridad de los trabajadores es la mecanización de la industria.
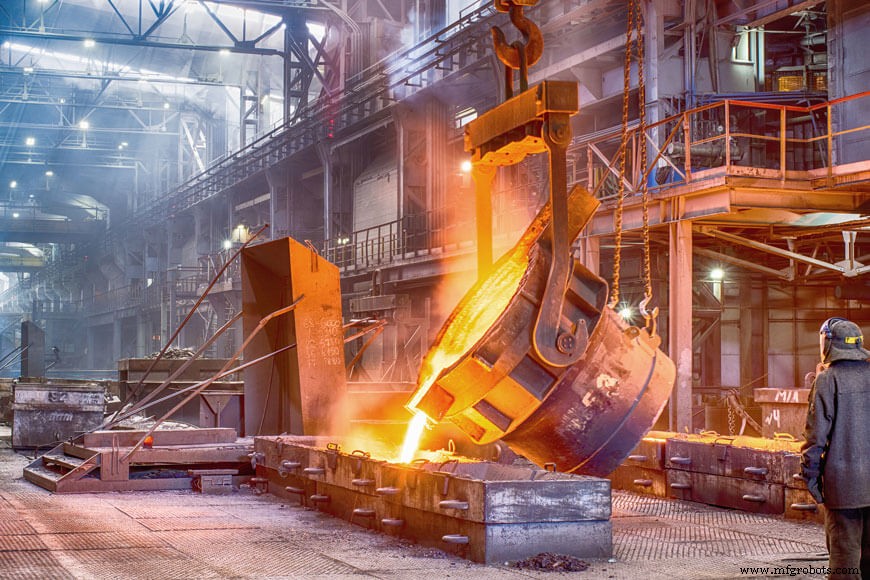
Anteriormente, los cucharones se manipulaban, recogían y movían por el sitio de fundición. Luego se introdujeron los cucharones con engranajes, que permitieron que un operador operara y controlara el cucharón a distancia en lugar de estar parado al lado del recipiente de metal fundido. Se introdujeron grúas para levantar los cucharones a la posición de vertido, pero el ruido del entorno de producción y las limitaciones de la línea de visión todavía significaban que los conductores de grúas eran vulnerables a causar incidentes. Las grúas de proceso son el último desarrollo en el que los cucharones se desplazan sobre pistas preestablecidas con elevadores, lo que elimina la posibilidad de que un operador se interponga en el camino del cucharón en movimiento en condiciones normales de funcionamiento.
El futuro de las fundiciones
Tendencias tecnológicas futuras
La eficiencia es la motivación predominante que impulsa los avances tecnológicos en las fundiciones. Hay un fuerte enfoque en la reducción del consumo de energía debido a un énfasis en la fabricación sostenible, así como la reducción de costos asociada. Una mano de obra más pequeña en las fundiciones también reducirá el potencial de lesiones y optimizará la producción.
Las mejoras en la automatización y un movimiento hacia las simulaciones por computadora, como el software de simulación de solidificación, reducirán la dependencia de la industria de la fundición de la mano de obra y mejorarán la precisión y la eficiencia. La simulación de procesos asistida por computadora ofrece modelos de procesos que ahora están lo suficientemente maduros. Esto permite a los ingenieros de fundición usar el mundo virtual en preparación para el mundo real, minimizando así el número de iteraciones de prueba.
La máquina de medición por coordenadas (CMM) está brindando un nuevo nivel de medición de precisión al taller en la industria del mecanizado. La inspección de orificios, ranuras, piezas soldadas y deformaciones se puede realizar rápidamente, lo que reduce significativamente el tiempo del ciclo. Los datos escaneados luego se combinan con resultados táctiles en informes gráficos para una fácil interpretación. El CMM es una fuerza impulsora para aumentar la productividad y proporcionar información práctica.
Tendencias futuras del mercado
El mercado de la fundición ha estado dominado durante la última década por la consolidación en grandes conglomerados. Las economías de escala son un factor clave de esta tendencia y es probable que continúen en el futuro previsible. Las operaciones más pequeñas y menos eficientes seguirán cerrando debido a la competitividad del mercado.
Futuras tendencias medioambientales y de seguridad
El reciclaje de metales es una de las historias de éxito del desarrollo sostenible, pero sigue existiendo la necesidad de desarrollar el uso sostenible de otros productos involucrados en el proceso de fundición de metales. Se seguirán identificando y explorando nuevas formas de utilizar la escoria y las arenas de molde usadas para mantenerse al día con los constantes avances normativos contra la eliminación de residuos.
Los rápidos avances en tecnología robótica han abierto puertas de oportunidad para reducir la exposición de los humanos a situaciones peligrosas. Los innovadores en tecnología robótica para entornos industriales están desarrollando celdas de trabajo robóticas que están completamente automatizadas y no requieren intervención humana en el lugar de trabajo.
Las fundiciones y su continua evolución
La fundición de metales ha sido parte de la sociedad humana desde la antigüedad, y su uso y avances aumentan día a día.
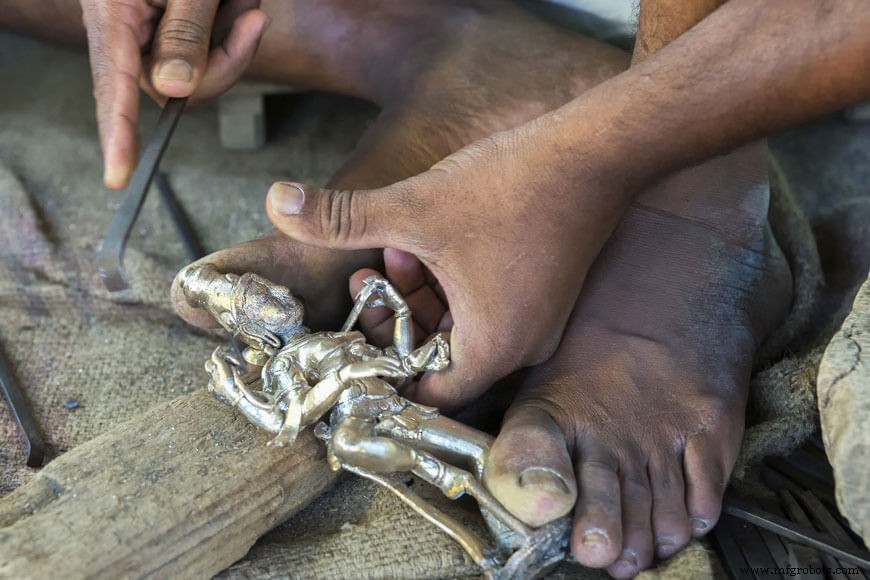
Hoy en día, los productos de fundición de metal afectan nuestras vidas de muchas maneras. Las piezas de automóviles, los utensilios de cocina, las herramientas y muchos otros productos de uso diario son el resultado de los procesos de fabricación de las fundiciones.
Durante siglos, la tecnología ha hecho grandes avances para mejorar la consistencia y el control de calidad de los productos de metal fundido, al tiempo que mejora la seguridad laboral de los trabajadores y reduce los costos a través de una mayor eficiencia. Un estudio de la historia de las fundiciones revela destacados empresarios, ingenieros, innovadores y solucionadores de problemas que han desempeñado un papel en el desarrollo de esta industria.
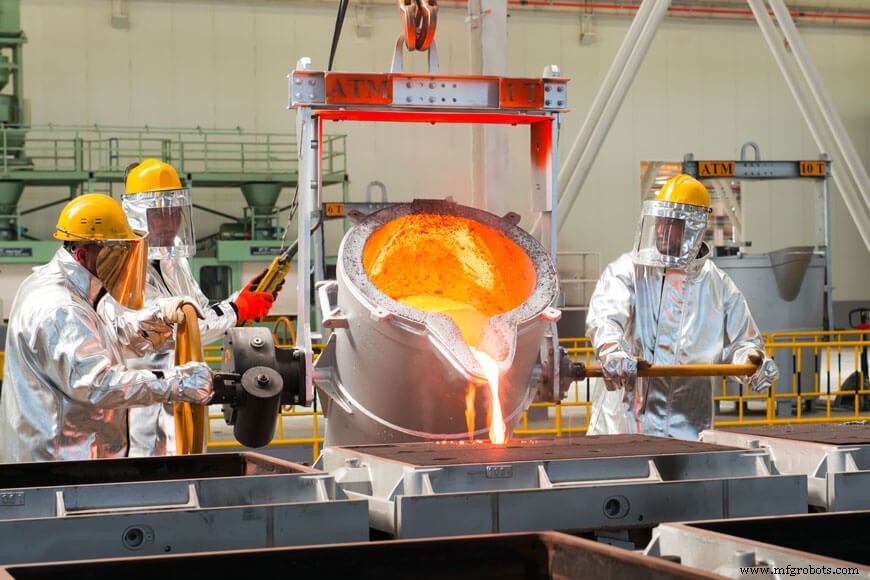
Las presiones económicas del mercado global continúan creando un ambiente que recompensa la innovación, la consistencia y la eficiencia. Las próximas décadas seguramente producirán nuevas tecnologías emocionantes, como el uso de big data y robótica, y nuevos modelos comerciales a través de fusiones y actualizaciones. Las tendencias globales hacia la fabricación sostenible seguirán impulsando mejoras ambientales y de seguridad en la industria, lo que beneficiará a los trabajadores y las comunidades por igual.
Referencias
- Fundiciones metálicas industriales. “Historia de la fundición de metales”
- El diccionario gratuito. “Industria de la fundición”
- Fundición Waupaca. “Historia de la fundición de metales”
- Servicio de Parques Nacionales de EE. UU. “Sitio histórico nacional Saugus Iron Works”
- Enciclopedia Británica. “Horno de cúpula”
- La Fundación Estadounidense de Estudios Siríacos. “El contexto de la invención en el mundo antiguo”
- El instituto del hierro y el acero de Japón. “Tecnología siderúrgica durante los últimos 100 años”
- Sociedad Americana de Fundición. “Castings en nuestro mundo”
- Tecnologías del metal. “Historia de las fundiciones de metal”
- AMAG. “La tecnología EMC aumenta la calidad y la rentabilidad”
- T.P. Fundición. "Industria de la fundición:breve historia y definición"
Proceso de manufactura
- Guillotina
- Silicio
- Bisagras para sus gabinetes de chapa metálica
- 5 maneras de mejorar sus piezas de chapa
- 5 formas de hacer que sus piezas metálicas sean resistentes a la corrosión
- Su guía para el corte del proceso de fabricación de metales
- 5 preguntas importantes para hacerle a su proveedor de metal
- Cómo prevenir la corrosión en su equipo de metal
- Cómo utilizar su máquina perforadora para taladrar metal
- ¿Qué es una Fundición?
- ¿Cuándo se inventó el torno para trabajar metales?