Tipos de procesos de moldeo:descripción completa [con imágenes]
En este artículo, hablaremos sobre el proceso de moldeo, los tipos de procesos de moldeo clasificados según varios términos, como moldeo en arena seca, moldeo en arena verde, moldeo en banco, etc.
Proceso de moldeo de uso común pueden clasificarse según diferentes formas. En términos generales, pueden clasificarse como:
- Moldeado a mano , y
- Moldeo a máquina .
En piezas y lotes pequeños, los moldes de arena se fabrican a mano; Las máquinas de moldeo se emplean en la producción en masa y de lotes grandes.
Tipos de procesos de moldeo
Los procesos de moldeo a menudo se clasifican según:
(A) El tipo de material del que está hecho el molde o
(1) moldes de arena verde,
(2) moldes de arena seca,
(3) mohos secados a la piel,
(4) Moldes de marga.
(B) Los métodos utilizados para hacer el molde.
(1) moldura de banco,
(2) moldura de piso,
(3) moldura de fosa,
(4) moldura de barrido, y
(5) Placa de moldeo.
Proceso de Moldeo a base de Arena Utilizada
1. Moldura Arena Verde
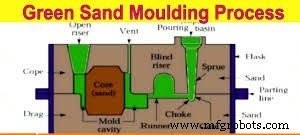
Molduras de arena verde es un método versátil, rápido y económico para crear moldes para fundiciones ferrosas y no ferrosas de alta calidad. La arena verde se compone de arena de sílice, agua, bentonita y otros aditivos, como polvo de carbón para aplicaciones de hierro.
Los moldes de arena verde se preparan con arenas de moldeo naturales o con mezclas de arena de sílice, arcilla de unión y agua. Estos materiales se mezclan completamente en proporciones que darán las propiedades deseadas para la clase de trabajo que se realiza.
2. Molde de Arena Seca
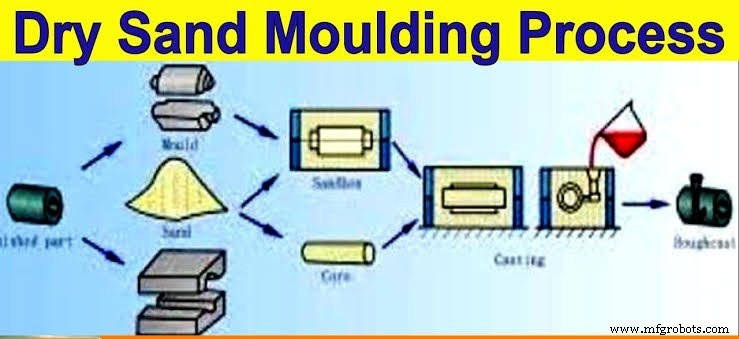
El proceso de moldeo involucrado en la fabricación de moldes de arena seca son similares a los empleados en el moldeo con arena verde, excepto que se usa una mezcla de arena diferente y todas las partes del molde se secan en un horno antes de volver a ensamblarlas para la fundición.
El molde de arena verde depende de la humedad y del aglutinante de arcilla natural en la arena para conservar su forma. Pero la arena utilizada para los moldes de arena seca depende del material aglutinante agregado, como harina, resina, melaza o arcilla. Los materiales se mezclan completamente y se templan con agua de arcilla fina. La cantidad de aglomerante está determinado por el tamaño de la fundición se está haciendo.
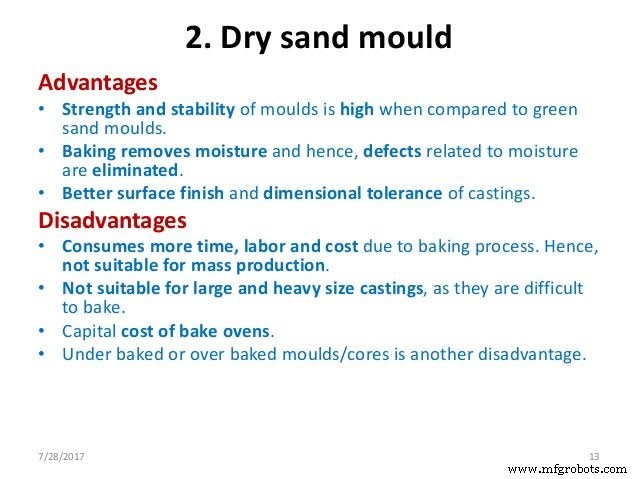
3. Moldeado secado a piel
El proceso de moldeo con secado superficial es un proceso que seca la humedad de la capa superficial de la arena apisonada hasta una profundidad de unos 25 mm o más mediante el uso de sopletes de gas o calentadores. Tiene las ventajas del moldeado con arena verde y arena seca hasta cierto punto. Dado que el tiempo requerido para el secado es menor que en el caso de la arena seca, el método es menos costoso. El secado de piel está especialmente adaptado a moldes muy grandes, o a trabajos que requieren detalles precisos.
4. Molde Marga
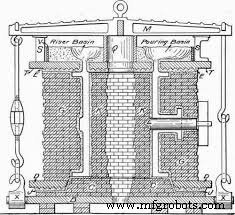
Marga es arcilla y arena mezcladas con agua para formar una fina mezcla plástica de la que se hacen moldes. La arena franca también contiene arcilla refractaria o ganisters. La marga debe ser lo suficientemente adhesiva para que pueda adherirse a las superficies verticales. Los mohos francos siempre requieren una provisión especial para asegurar una ventilación adecuada. El objeto es abrir los poros en la masa densamente unida, por lo demás compacta, por medios artificiales. Así, diversos tipos de materia orgánica como la paja picada y, en particular, el estiércol de caballo , se mezcla con la arena. Una mezcla típica de arena franco se da a continuación:
Este se aplica como yeso a la estructura rugosa del molde generalmente hecho de ladrillo y la forma exacta se da mediante un barrido giratorio alrededor de un husillo central como se muestra en la figura. Se utilizan placas y barras de hierro fundido para reforzar el enladrillado que retiene el material de moldura. Los moldes de marga también se pueden preparar mediante el uso de un patrón de esqueleto hecho de madera. Las superficies de las margas se ennegrecen y se secan antes de ensamblarlas.
Los moldes de marga se emplean principalmente en la fabricación de piezas fundidas grandes para las que sería demasiado costoso utilizar patrones completos y equipo de mufla ordinario. Objetos como cilindros grandes, marmitas de fondo redondo, bandejas de productos químicos, engranajes grandes y otras piezas de máquinas se producen en moldes de marga.
Tipos de procesos de moldeo en función de los métodos utilizados
1. Moldura de banco y piso
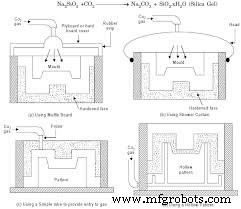
Moldura de banco se aplica principalmente a moldes lo suficientemente pequeños para ser hechos en un banco de trabajo de una altura conveniente para el moldeador.
Las fundiciones muy pesadas o las fundiciones de una profundidad o área considerables pueden moldearse en la arena del piso de la fundición de la misma manera que el moldeo en arena verde o en arena seca. En tales casos, el propio suelo actúa como arrastre, y se puede cubrir con una capa o se puede abrir el molde.
2. Moldura de foso
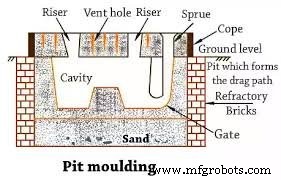
Moldura de foso Proceso :Los moldes de trabajos grandes se preparan generalmente en un pozo excavado en el piso de fundición que facilita el levantamiento del patrón y la fundición del molde fácilmente. Dado que un pozo que funciona como un arrastre no se puede volcar, la arena debajo del patrón se puede apisonar con lechos. El patrón puede suspenderse en la ubicación correcta a medida que se apisona la arena debajo de él. En otros casos, si la superficie inferior de un patrón es plana, el patrón se puede colocar sobre una superficie plana nivelada apisonada para ello.
En el fondo del pozo se coloca un lecho de coque, se cubre con paja y luego con una capa de arena, que se apisona y nivela. El lecho de coque está conectado con la atmósfera mediante tubos de ventilación verticales en las esquinas del pozo para proporcionar una salida a los gases generados. Si el piso está ligeramente húmedo, las superficies internas del pozo se revisten con papel alquitranado, ladrillos o tablones de madera. Generalmente, se requiere una caja para completar el proceso de moldeo. En él se cortan corredores, cuencas de vertido, comederos.
3. Moldura de barrido
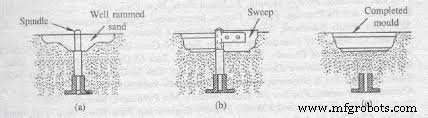
molduras de barrido se emplean para moldear piezas cuya forma es la de una superficie de revolución. En el proceso preliminar, una base 1 y un eje 2 están bien colocados en el piso de fundición. La arena se rellena y apisona hasta que la excavación tiene aproximadamente la forma y el tamaño del molde requerido. Esto se ilustra en la Figura a.
A continuación, se coloca un soporte de barrido 5 en la zona del husillo, el barrido 6 se fija mediante pernos y tuercas. La superficie del molde es producida por el perfil del barrido a medida que gira alrededor del husillo como se muestra en la Figura (b). Después de barrer, se retira el husillo y se parchea el centro del molde. Luego se corta la puerta y el molde está listo para verter. Esto se muestra en la Fig. (c).
4. Moldeado de placas
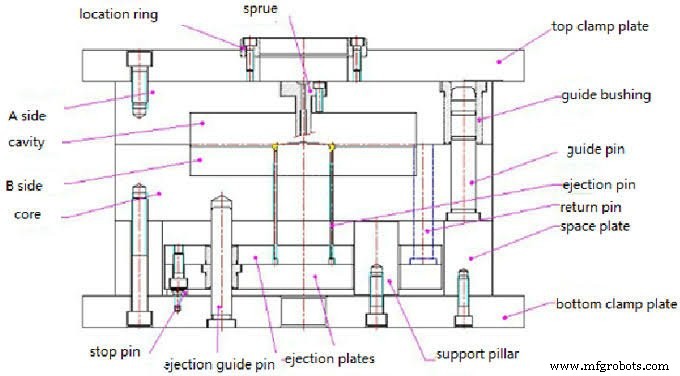
Moldeo de placas Proceso :En este proceso de partición montada, el patrón se divide por la mitad a lo largo de la partición y por la mitad en placas con lados paralelos de la misma forma que la figura. El uso de placas ofrece las siguientes ventajas :
- Los patrones se pueden manejar fácilmente y rápidamente
- La tarea de hacer la unión entre las dos partes del molde se alivia ya que la placa proporciona su propia unión cuando se apisona la mufla.
- El patrón se puede dibujar rápidamente , ya que la placa se superpone al lateral de la caja y los pasadores que la sujetan actúan como guías durante la operación de dibujo.
Algunos procesos de moldeo especiales
En los últimos años, procesos de moldeo especiales se han desarrollado para ahorrar tiempo y dinero, producir moldes y machos de mejor calidad y aumentar la productividad con menos esfuerzo y habilidad. Generalmente, estos procesos no requieren en todos los casos el secado o horneado de moldes o machos, y se produce una rápida acción de endurecimiento debido a reacciones químicas en ellos. El uso de los siguientes procesos de moldeo especiales se ha incrementado considerablemente en los últimos años.
1. Moldeado de dióxido de carbono
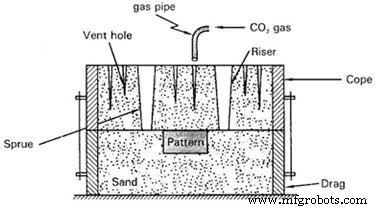
Moldeado de dióxido de carbono Proceso: El proceso es básicamente un proceso de endurecimiento para moldes y machos. El principio de trabajar del proceso de CO2 se basa en el hecho de que si gas CO2 es atravesado una mezcla de arena que contiene silicato de sodio (vaso de agua), la arena se une inmediatamente de forma extremadamente fuerte a medida que el silicato de sodio se convierte en un gel rígido. Este gel es el encargado de dar la fuerza necesaria al molde.
2. Moldeo de ferrosilicio
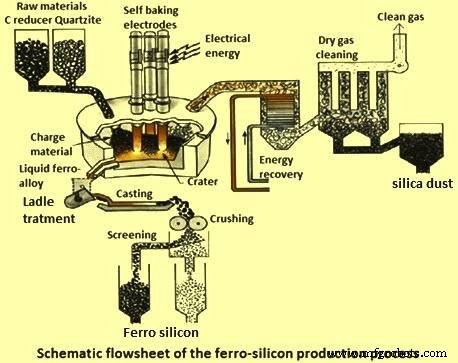
Moldeado de ferrosilicio :Este proceso de moldeado se basa en el principio eso si silicato de sodio y ferrosilicio en polvo son mixtos en la proporción de 2,25 :1 en peso, se produce la acción espumante y la temperatura se eleva por reacción exotérmica entre ellos. A temperatura ambiente, esta reacción se lleva a cabo lentamente, pero una vez que se aumenta la temperatura, la reacción se acelera. Finalmente, la arena de sílice forma una masa dura y esponjosa. No es necesario hornear el molde o el núcleo como en el proceso de CO2.
Normalmente, para fundiciones ferrosas arena limpia y seca de malla 65 , mientras que para fundición no ferrosa , arena de malla 100 es adecuado. Los moldes deben recubrirse con un lavado adecuado antes de cerrarlos.
3. Moldeado de silicato dicálcico
Moldeado de silicato dicálcico :Este proceso de moldeado se basa en el principio eso si alrededor de 2-3 por ciento de silicato dicálcico , conocido por ser un agente endurecedor muy efectivo, y 5 por ciento de silicato de sodio son mixtos con arena junto con productos químicos espumantes adecuados, aumenta la fluidez de la masa de arena. Como resultado, la mezcla de arena puede fluir fácilmente en el molde y no hay necesidad de apisonar como se requiere en el proceso de moldeo convencional. Finalmente, la arena forma una masa dura que tiene suficiente colapsabilidad
La principal ventaja de este proceso de moldeo es el gran ahorro en mano de obra y equipos de moldeo ya que no se necesita secado ni respaldo. Por otro lado, se producen piezas fundidas de alta calidad y sin defectos. Esto encuentra una amplia aplicación en fundiciones medianas y pesadas, tanto en fundiciones de hierro gris como de acero.
4. Moldeo Cemento-Arena
Moldeo Cemento-Arena :El cemento Portland se puede utilizar como material aglutinante para unir los granos de arena. Se encuentra que se logra una buena combinación de resistencia, permeabilidad y fluidez usando cemento junto con silicato de sodio. La lechada de cemento fluida también se puede producir utilizando productos químicos espumantes en la mezcla de arena. El apisonamiento de arena se reduce así considerablemente. Sin embargo, se puede desarrollar una buena unión en la arena con la adición de un 2 por ciento de cemento, un 4-5 por ciento de silicato de sodio y un 1 por ciento de brea o melaza.
Estos moldes producen una superficie lisa y precisa, pero la principal desventaja de los moldes de arena aglomerados con cemento es que son difíciles de sacar del matraz.
5. Moldeo de concha
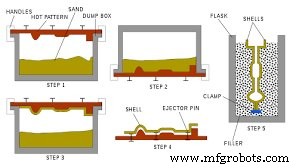
Moldeo de carcasa :Por el nombre de su inventor, el moldeo en cáscara también se conoce como proceso de croning o proceso C . Esta es una variante de la técnica de arena unida con resina para fundición de acero, hierro o aleaciones no ferrosas.
El molde se forma a partir de una mezcla de arena fina (malla 100-150) y un aglutinante de resina termoendurecible que se coloca contra un patrón de metal calentado, preferiblemente de hierro fundido gris. Cuando la mezcla se calienta de esta manera, la resina se cura, haciendo que los granos de arena se adhieran entre sí formando una capa resistente que se ajusta exactamente a las dimensiones y la forma del patrón y constituye la mitad de un molde.
Una vez que la cubierta se ha curado y se ha desprendido del modelo, se colocan los núcleos necesarios, las dos mitades del molde se unen, se colocan en un matraz y se agrega material de respaldo; entonces el molde está listo para verter.
6. Moldeo en Caja Fría y Caliente
El proceso de caja caliente , particularmente adaptado en la fabricación de machos, utiliza básicamente los mismos materiales que los utilizados en el moldeo de cáscaras, pero aquí la resina se aplica para recubrir los granos de arena. Luego, la mezcla de resina y arena se sopla sobre el patrón de metal o la caja de núcleos y se calienta a aproximadamente 200° a 300°C. y se le permitió formar una masa sólida en lugar de permitir la formación de una capa.
Las máquinas especiales de caja caliente ahora están disponibles donde la mezcla de arena se sopla sobre el patrón calentado, la arena soplada se cura y el molde o el núcleo luego se quitan del patrón o caja del núcleo.
Se logra una mayor precisión de las dimensiones y tasas de producción más altas que en el caso del moldeo en cáscara. Este es un proceso de moldeo y fabricación de machos esencialmente para la producción mecanizada de pequeñas piezas de fundición requeridas en grandes cantidades.
El proceso de caja fría consiste en mezclar arena fina seca ya sea resina de poliisocianato carpeta y resina fenólica alquídica , soplando la mezcla en una caja central sellada e inyectando un vapor de trietilamina de catalizador transportado por el aire a través de la caja central. El grupo hidroxilo de la resina fenólica líquida se combina con el grupo isocianato para formar una resina de uretano rígida. Los dos componentes del aglomerante se utilizan normalmente en una proporción de 1:1 con un 1 a 2 por ciento en peso de la mezcla de resina añadida a la arena. a
El proceso tiene la ventaja de que no se requiere calentar el patrón y el curado se lleva a cabo en solo 20-30 segundos. Por lo tanto, es un proceso de fabricación de machos simple y de alta producción, y extremadamente adecuado para piezas fundidas de pequeño tamaño requeridas en grandes cantidades.
7. Moldeo por inversión
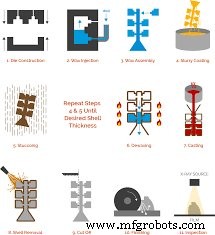
Moldeado de inversión :Este proceso de fabricación de piezas fundidas a menudo se conoce como “proceso a la cera perdida ” y “proceso de fundición de precisión ”. La fundición se puede realizar con tolerancias muy estrechas en este proceso y no requiere un mecanizado posterior.
Consta principalmente de dos etapas que se muestran en la figura. Primero, se hace un patrón maestro de madera o metal alrededor del cual se forma un molde. No consiste en arena para moldes sino en gelatina o una aleación de bajo punto de fusión que se vierte sobre el patrón maestro. Este molde maestro consta de las dos secciones habituales y se puede abrir. Se usa para hacer el “patrón perdido “.
8. Moldura de yeso
Moldura de yeso :En este método se prepara el molde en yeso o yeso de París. En la práctica, el yeso de París se mezcla con talco, amianto, fibras, harina de sílice y una cantidad controlada de agua para formar una suspensión. Esta suspensión de yeso se vierte sobre el patrón metálico confinado en un matraz.
El molde se hace vibrar y la suspensión se deja fraguar. El patrón se retira después de aproximadamente 30 minutos cuando se completa el fraguado y el molde se seca y se recubre calentándolo lentamente a aproximadamente 200°C en un horno transportador. Los insertos y los núcleos se colocan, se adaptan y se arrastran mediante pasadores guía. Luego se vierte el metal fundido en el molde. Finalmente, la fundición se enfría en el molde, se sacude y se destruye el molde. Luego se recortan las compuertas, bebederos y rebabas de las piezas fundidas.
9. Moldeado de cerámica
En moldeado de cerámica proceso, una suspensión espesa, que consta de agregados cerámicos especialmente desarrollados y un aglutinante químico líquido (éster de silicio a base de alcohol) se purifica sobre el patrón de metal dividido y cerrado reutilizable que generalmente se monta en una placa de fósforos. La lechada llena todas las cavidades y huecos por sí misma y no se requiere apisonar ni vibrar el molde. El patrón se retira después de que se establece en unos 3 a 5 minutos. A continuación, la masa cerámica se retira del matraz, se trata con un endurecedor para promover la estabilización química y se calienta a unos 980 °C en un horno para eliminar el aglomerante líquido. El molde está entonces listo para verter el metal fundido.
10. Moldeo por succión
Moldeo por succión Proceso: En este método, se crea un vacío extrayendo aire del espacio del molde. Posteriormente se aspira arena de moldeo y se rellena la cavidad. A partir de entonces, la arena se puede apisonar en el patrón. El proceso se utiliza para la fundición de hierro, acero y aluminio.
Intentamos cubrir todo el punto importante relacionado con el proceso de moldeo y sus tipos y clasificaciones. Espero que hayas disfrutado este artículo. Proporcione sus comentarios en el comentario a continuación.
Tecnología Industrial
- MTBF:una descripción completa
- 5 tipos diferentes de centros de datos [con ejemplos]
- Arena de moldeo:tipos y constituyentes | Casting | Metalurgia
- Propiedades de la arena de moldeo | Materiales | Casting | Metalurgia
- ¿Qué es la arena de moldeo? - Tipos y propiedades
- Tipos de arena utilizados en el proceso de moldeo
- Pistón - Resumen completo
- Tipos de medidores:descripción completa [con imágenes]
- Definición, proceso y tipos de máquinas de fresado
- Proceso de fabricación Significado y tipos
- Tipos de equipos de fundición en arena