Proceso Planificación Estimación Y Costeo
En este artículo, aprenderá sobre la estimación y el costeo de la planificación de procesos y varios términos asociados para una comprensión clara.
Process Planning Estimating and Costing
EVALUACIÓN DE COSTOS
El diseño de un proceso no está completo hasta que se tiene una buena idea del costo requerido para fabricar el producto. Generalmente, el diseño de menor costo tendrá éxito en un mercado libre. Por lo tanto, es vital comprender los elementos que componen el costo.
Elementos de los costos: Las constituciones de un producto o elementos de costo se pueden agrupar en términos generales en (1) costos recurrentes o costos de fabricación o costos operativos y (2) costos no recurrentes. Pueden volver a clasificarse como costes directos , costes indirectos mientras que los costos de capital vienen bajo costos no recurrentes. Los costos recurrentes incluyen todos los costos directos e indirectos, mientras que los costos de capital se incluyen en los costos no requeridos.
Directo Costos
Costos directos son los costes de aquellos factores que pueden atribuirse directamente a la fabricación de un producto específico. Estos incluyen costos de material y mano de obra. Coste de materiales es el costo de ese material que entra en el producto terminado e incluye todos los desechos que se han eliminado del stock original. Coste laboral varía de máquina a máquina y generalmente se calcula multiplicando el tiempo requerido para una operación por la tasa de mano de obra. Así, se debe estimar el tiempo de montaje y realización de una operación para conocer su coste de mano de obra.
Indirecto costos
Costos indirectos son los costos de aquellos factores que solo pueden atribuirse indirectamente a la fabricación de un producto específico. A veces se denominan gastos generales. o sobre los costos . Los costos generales se calculan comúnmente multiplicando el tiempo de operación por una tasa de gastos generales. Tal tasa se obtiene dividiendo los costos indirectos totales aplicables a una unidad de fabricación durante un período de tiempo (por ejemplo, un mes o una semana) por el número total de horas de mano de obra directa en el mismo período.
Capital costos
Costos de capital son costos de una sola vez o costos no recurrentes que incluyen instalaciones depreciables como plantas, equipos y herramientas de construcción o fabricación, y costos de capital no depreciados, como terrenos. Los costos de capital se determinan distribuyendo los principales costos de máquinas y herramientas por hora o entre la pieza producida.
El coste total de un producto es el costo directo de fabricación del producto más cualquier costo indirecto atribuido a la fabricación del producto.
Para que el ingeniero de procesos utilice los datos de costos como una herramienta para ayudar a analizar el problema de fabricación, los costos pueden ser más convenientemente agrupados en costos fijos y costos variables.
Fixed costs include preparation costs such as of tooling setting up, etc., and also the interest and depreciation costs which are independent of the quantity of the product manufactured.
Variable costs are those costs which vary as the quantity of product made varies. This includes the direct labour and material costs, and also that part of the indirect costs which will vary as production varies. The total cost of a product can also be seen to be fixed cost plus variable cost.
Cost Structure
Cost structure : The elements of cost can be combined to give the following types of cost:
Prime cost =Direct material + Direct labour + direct expenses.
Factory cost =Prime cost + Factory expenses.
Manufacturing cost =Factory cost + Administrative expenses.
Total cost =Manufacturing cost + Selling and distributing expenses.
STANDARD COSTS
In cost accounting actual or recorded costs or standard or predetermined costs are used. The nomenclature actual cost is misleading. Usually average labour rates are used rather then the actual ones and arbitrary allocations are made for use of capital equipment and for general and administrative costs. Also actual costs are compiled long after the job in completed. This approach is chiefly aimed at financial accountability than cost control.
Standard costs are based on the proposition that there is certain amount of material in a part and a given amount of labour goes into the part’s manufacture. In a given period of time costs tend to vary around some average cost per unit or per hour. Through the use of standard costs, guesswork is reduced and a standard that measures performance is established. Each part and assembly has a standard cost card on which is recorded the standard material, labour, and overhead costs, and the total cost.
The system of standard costs consists of two parts :(1) a base standard and (2) a current standard. The base standard is determined infrequently, e.g., once a year, and the current standard represents the later cost. The difference between the two is the cost variance.
ESTIMATING LABOUR COSTS
All direct and in direct costs excluding labour costs are determined by the accounts department of the plant. Process planners are mostly concerned with labour costs which are directly related to the process of manufacturing. However, the total time required by workers to perform an operation may be divided into following classes :
The time to perform an operation also includes time for personal needs, time to change and re-sharpen tools, etc. which are taken to be about 20 per cent of the sum of all other times. Besides, there are inspection or checking times which vary from instrument to instrument.
Each operation on a particular type of machine tool is divided into a number of small elements. These elements can be standardized, measured and then recorded. This is mostly done under Time and Motion study . Standard data is also available for various times. Machining times are calculated with the help of formulae for each machining operation which takes into account the feeds, speeds, depth of cut and tool travel plus tool approach.
Machine time : All machining times can be calculated with the basic formula
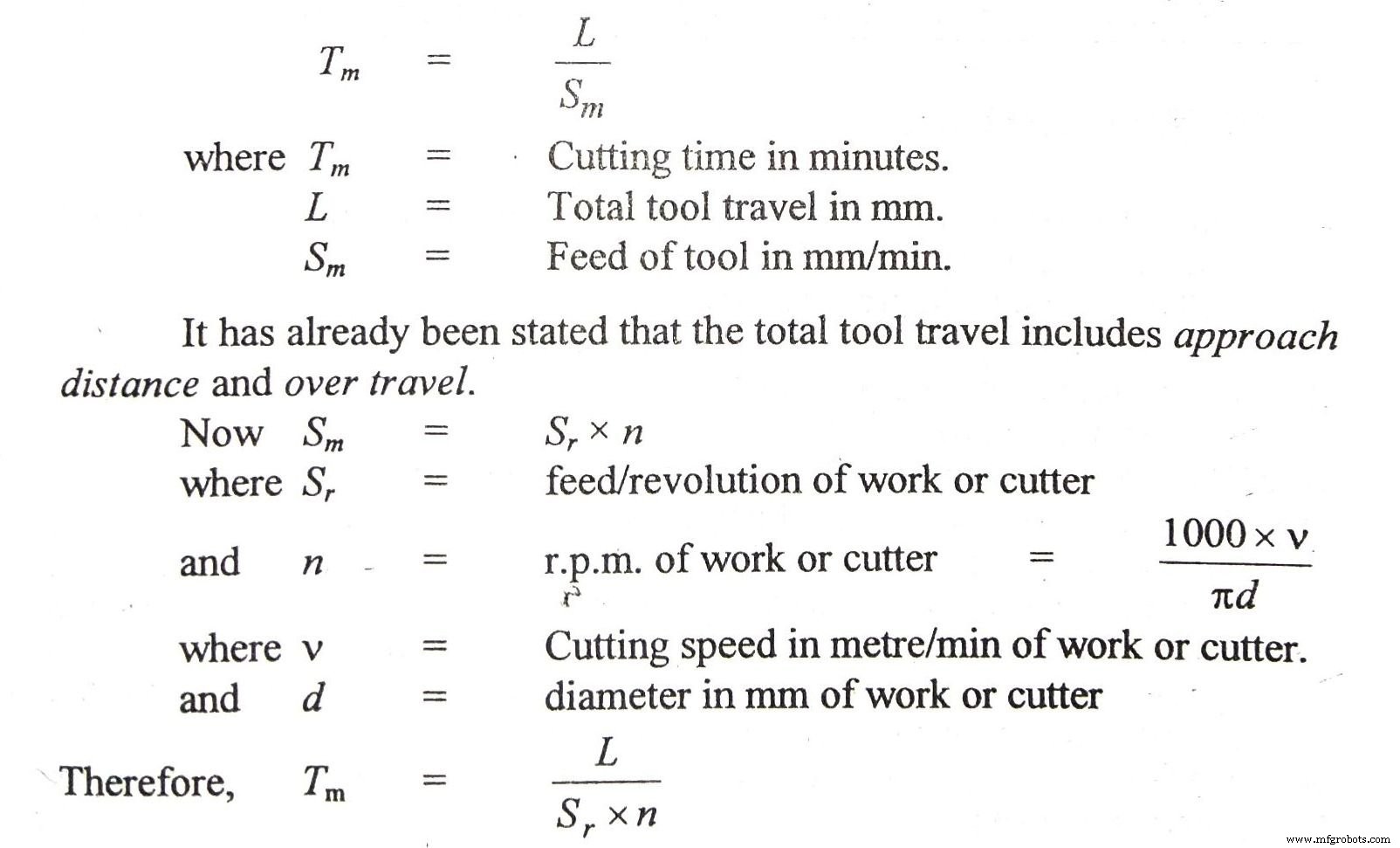
Calculation of machining time for each operation and their feed, speed and depth of cut have been given in each chapter or they may be available in hand books.
Methods of Costing
The method used to develop cost evaluation fall into three categories:methods engineering , cost by analogy , and statistical analysis of historical data .
In the methods engineering approach, that is usually followed, the separate elements of work are identified in great detail and summed into the total cost per part. A typical, but simplified example, is the production of a simple fitting from a steel forging.
Tecnología Industrial
- ¿Qué es el fresado?- Definición, proceso y operaciones
- ¿Qué es la perforación? Definición, proceso y consejos
- ¿Qué es la pulvimetalurgia? Definición y proceso
- ¿Qué es el brochado? - Proceso, trabajo y tipos
- ¿Qué es el mecanizado químico? - Trabajo y proceso
- ¿Qué es el mecanizado ultrasónico? - Trabajo y proceso
- ¿Qué es la soldadura por gas? - Partes, proceso y aplicación
- ¿Qué es el bruñido? - Definición, proceso y herramientas
- ¿Qué es la forja? Definición, proceso y tipos
- ¿Qué es la soldadura robótica? - Proceso y aplicación
- ¿Qué es la soldadura fuerte de plata? - Proceso, varilla y usos