¿Qué es la planificación de procesos? Pasos de planificación de procesos, tipos, ventajas
En este artículo aprenderá sobre Qué es la planificación de procesos ? ¿Cuáles son los requisitos para este proceso, ¿Cuáles son los pasos de planificación del proceso? , tipos , ventajas , desventajas y la secuencia de actividades incluidas. Comencemos con la Definición .
¿Qué es la planificación de procesos?
Planificación de procesos es el procedimiento utilizado para desarrollar una lista detallada de las operaciones de fabricación requeridas para la producción de una parte o un producto. Es el vínculo entre el diseño del producto y la fabricación del producto.
La planificación de procesos establece una secuencia eficiente de operaciones, selecciona el equipo y las herramientas adecuadas y especifica sus operaciones de tal manera que el producto cumpla con todos los requisitos estipulados en la especificación. Al mismo tiempo, el proceso se realizará con el mínimo coste y la máxima productividad.
Básicamente, hay dos formas en que se pueden generar planes de proceso. Están :
REQUISITOS PARA LA PLANIFICACIÓN DE PROCESOS
Un plan de proceso razonablemente bueno debe satisfacer los siguientes requisitos:
Después de comprender los requisitos básicos, lo siguiente son diferentes pasos en la planificación del proceso .
Proceso Pasos de planificación
El propósito de la planificación de procesos es determinar y describir el mejor proceso necesario para producir una pieza. Para lograr estos objetivos, se pueden seguir los siguientes pasos de planificación del proceso:
Vale la pena mencionar que la planificación de procesos es una dinámica para simplificar el procesamiento teniendo en cuenta los cambios tecnológicos del proceso, y los planificadores están obligados a analizar el procedimiento de producción en la fabricación.
Algunos de los pasos mencionados anteriormente en la planificación de procesos que requieren una explicación más detallada se describen a continuación con mayor detalle.
Especificaciones de fabricación: El documento principal en el que se enumeran las especificaciones de fabricación es el dibujo de detalle. El dibujo especifica:
Por último, las especificaciones deben coordinarse con el proceso de mecanizado y la inspección en la mayor medida posible. Si es necesario, se pueden hacer pequeños cambios o modificaciones para que la planificación sea exitosa.
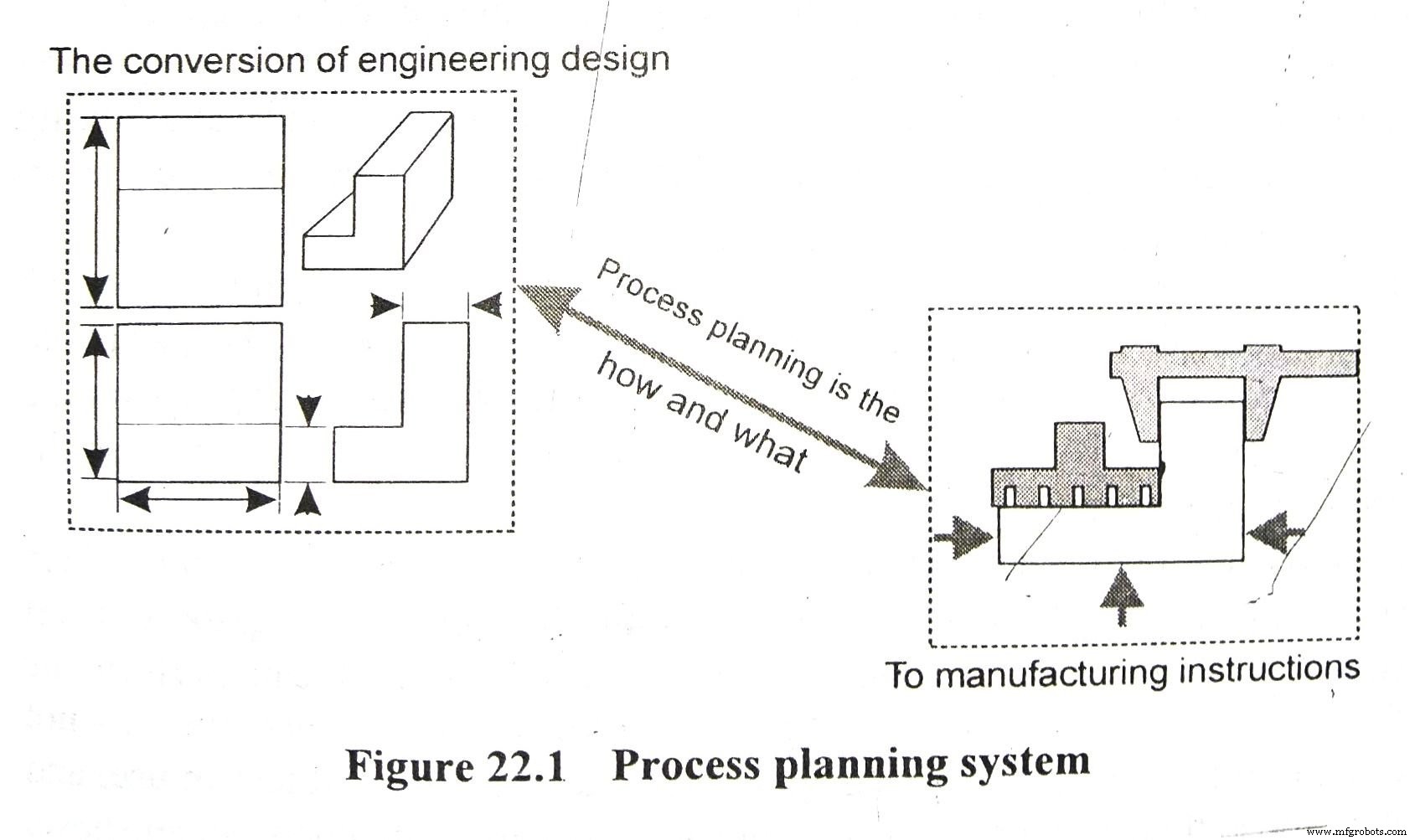
Determinación del espacio en blanco: La planificación del proceso en realidad comienza con la selección de espacios en blanco. El tamaño de la pieza en bruto y las especificaciones de la pieza acabada están interrelacionados y determinan el esquema general de las operaciones de mecanizado y acabado.
La precisión de la pieza bruta, que depende de su método de fabricación, y las especificaciones de la pieza acabada de la máquina determinan el esquema general del proceso de mecanizado y sus subdivisiones en operaciones de desbaste, semiacabado y acabado.
Selección de máquinas herramienta : El siguiente paso de la planificación del proceso es la selección de máquinas herramienta, que está determinada en gran medida por la elección del método o proceso de mecanizado de una pieza. En otras palabras, los principios que rigen los procesos de mecanizado deberían ser la base de la selección de máquinas herramienta. Aunque es difícil formular una regla definitiva para seleccionar la máquina herramienta para cualquier tipo de mecanizado, se deben considerar los siguientes factores al seleccionar una máquina herramienta para una operación en particular:
Gráficos de disponibilidad : La tabla de disponibilidad es una lista de máquinas herramienta organizadas según sus clases (es decir, una lista clasificada), por ejemplo, tornos de motor, tornos de torreta, automáticas y similares, con su identificación y número de modelo, ubicación, estado general, herramientas disponibles, velocidades de corte. y avances, etc. No obstante, en el caso de máquinas herramienta nuevas, las velocidades de corte y los avances se obtienen del catálogo disponible con las mismas. Esta tabla de disponibilidad es necesaria para seleccionar máquinas herramienta para un nuevo producto en una planta existente.
Gráficos de carga de la máquina muestra qué máquina permanece inactiva y cuál está cargada. En consecuencia, el planificador del proceso seleccionará la máquina herramienta particular que se puede utilizar para realizar la operación de mecanizado. El planificador de procesos no se preocupa tanto por el gráfico de carga de la máquina como el planificador de producción.
Gráficos de capacidad : El gráfico de capacidad se puede definir como un gráfico que muestra la capacidad de una máquina herramienta para realizar el trabajo. El gráfico de capacidad muestra cuánto de su capacidad nominal una máquina herramienta puede realizar su función satisfactoriamente. Una máquina herramienta, como cualquier otra máquina, no se mantienen en las mismas condiciones en que se compraron debido al desgaste por el uso, y pierden su precisión a la larga. El gráfico de capacidad que muestra el estado actual de la máquina es una guía para el planificador de procesos a la hora de elegir las máquinas adecuadas.
PLANIFICACIÓN DE LA SECUENCIA DE OPERACIONES
Determinar la mejor secuencia de operaciones es uno de los pasos importantes en el proceso de planificación y en la realización de un producto diseñado para la producción. Tanto el costo del producto como la calidad del producto están estrechamente relacionados con la secuencia de operaciones. Una secuencia diferente de operaciones realizadas dará como resultado diferentes tiempos operativos, diferentes tiempos de transporte al centro de trabajo, diferentes herramientas en vista de diferentes superficies de ubicación y sujeción.
Si se establece una nueva planta para un producto, el planificador de procesos tiene mucha más libertad para determinar la secuencia de operaciones que mejor se adapte al propósito. En el caso de una planta existente, la secuencia de operación para un nuevo producto se determinará sobre la base del equipo disponible y la condición de carga del equipo. En este último caso, se debe proporcionar al planificador del proceso la siguiente información:
- Lista de máquinas disponibles.
- Lista de herramientas de uso general disponibles.
- Capacidad del equipo.
- Tablas de carga de la máquina.
- Datos estándar.
Sin embargo, en cualquier caso, existen ciertos principios fundamentales que deben seguirse al planificar la secuencia operativa óptima. . Estos son:
Las grandes fuerzas de corte y sujeción que pueden estar asociadas con un corte pesado afectan la precisión de las superficies acabadas de otra parte de la misma pieza de trabajo y requieren máquinas destinadas a operaciones de desbaste. Además, los cortes pesados que involucran acabados bastos o ásperos suelen ser más rápidos con trabajadores menos costosos que los acabados finos.
La secuencia de operaciones no es rígida. Varía de un producto a otro e incluso en un mismo producto. Siempre hay margen para la mejora y debe revisarse continuamente para desarrollar mejores métodos, aumentar la productividad y reducir los costos.
Proceso Hoja de planificación
La hoja de planificación del proceso es un registro detallado donde se enumeran en forma tabular toda la información relacionada con las diferentes operaciones necesarias para fabricar una pieza. Esto también se conoce como hoja de análisis. , hoja de instrucciones , hoja de operaciones o hoja de diseño de procesos . Un ejemplo de una hoja de proceso se da en la Tabla 22.1.
La descripción de las operaciones y sus elementos indicados en la hoja de proceso debe brindar información extremadamente concisa pero completa sobre lo que se debe hacer y por qué. Los datos deben indicar claramente cómo y con qué se va a realizar el trabajo y, si es posible, el gasto de tiempo que requerirá.
La forma de dichas láminas puede variar según las diferentes condiciones de producción. El carácter de una hoja de proceso dependerá principalmente de la escala de producción y el grado de importancia del producto que se fabrica. Además, se utilizan diferentes tipos de láminas en conceptos de fabricación que ya están en funcionamiento y en organizaciones que diseñan nuevas plantas.
Sin embargo, en la mayoría de los casos, la siguiente información se incluye en las hojas de proceso:
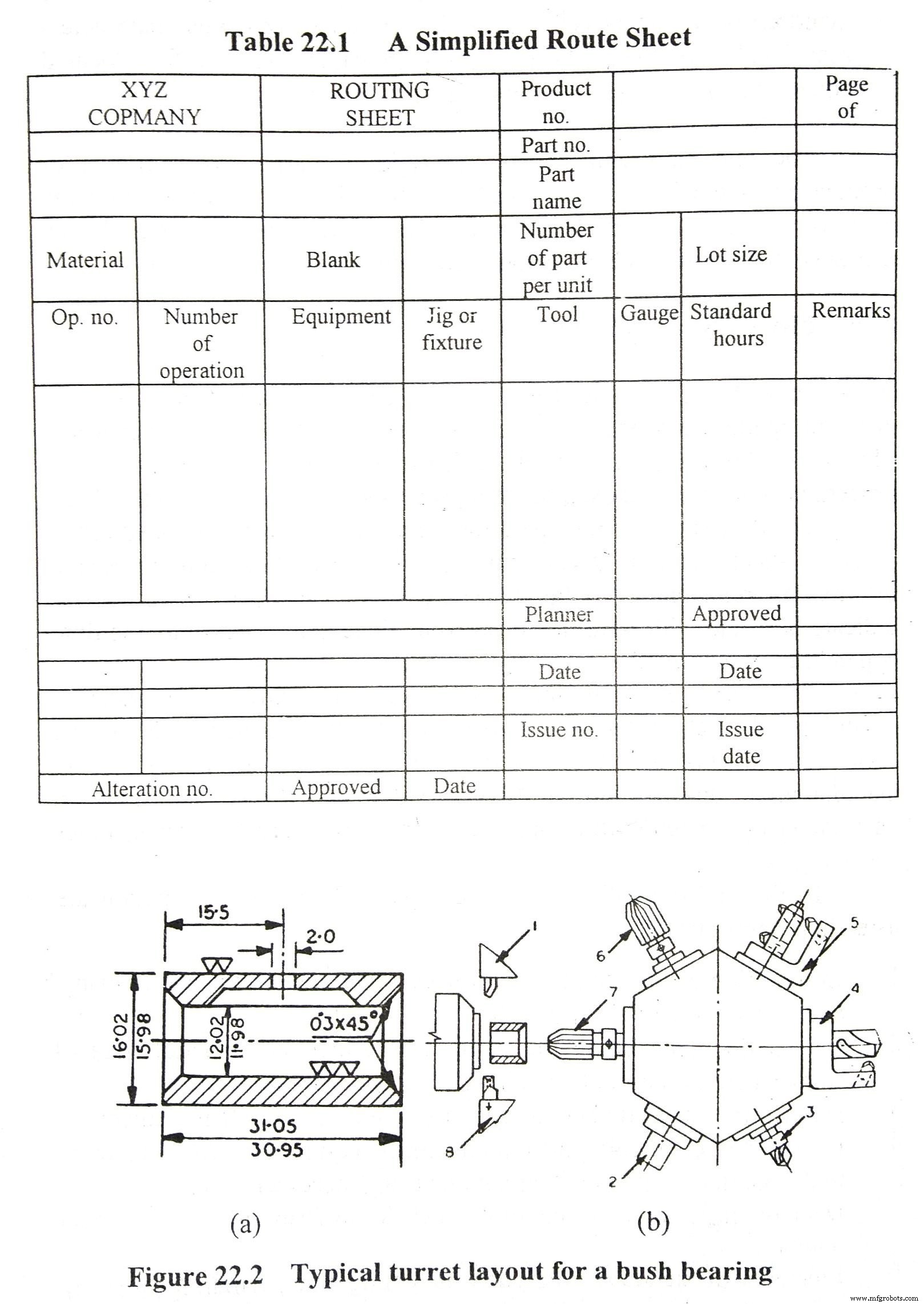
En la planificación de procesos de fabricación para operaciones de mecanizado, con frecuencia se dibujan bocetos de operación para varias operaciones, como se muestra en la fig. 22.2. Las superficies que se van a mecanizar dando la tolerancia deseada.
Un ejemplo de secuencia de operación
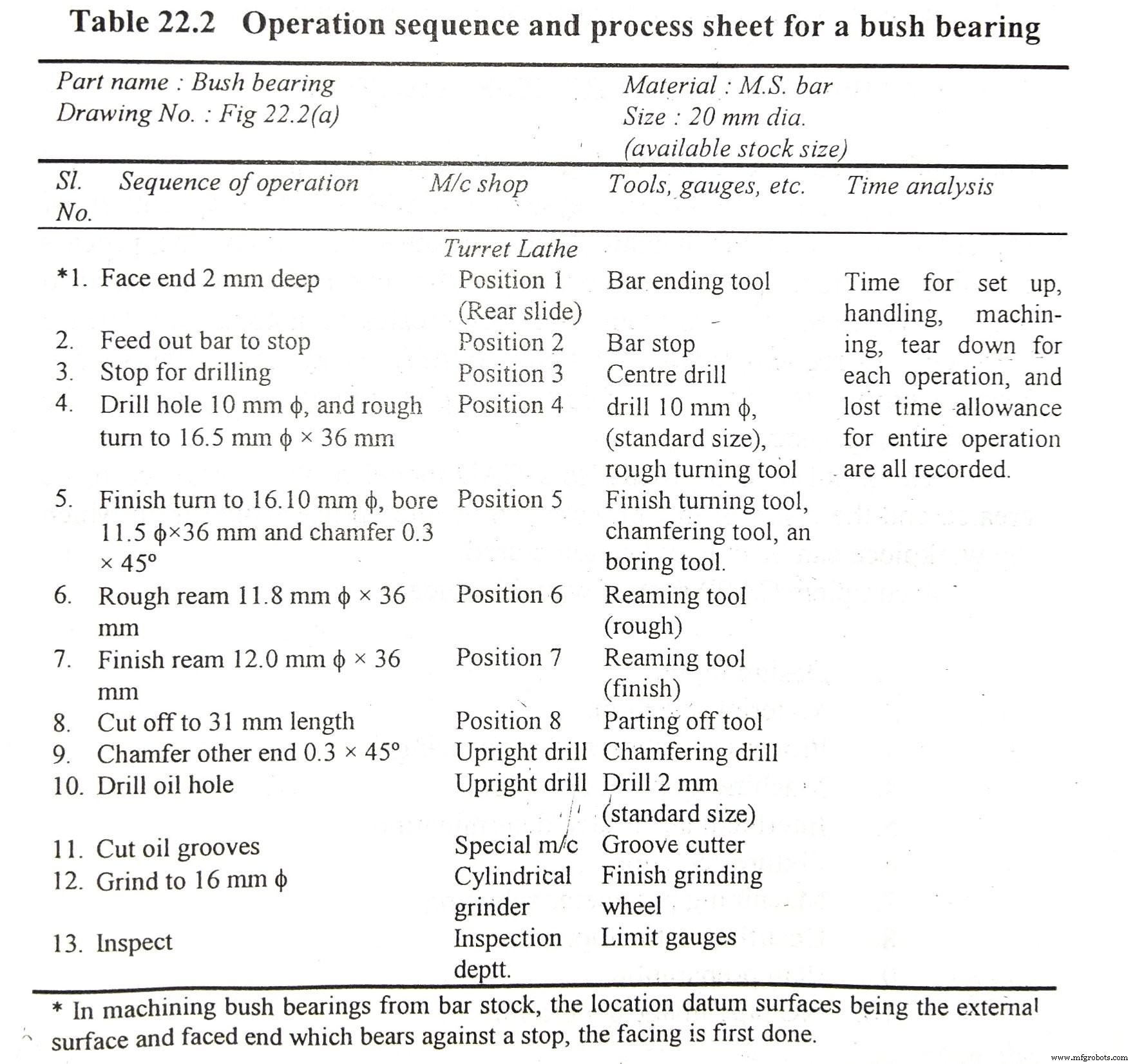
Desventajas de la planificación manual de procesos
La planificación manual de procesos (MPP) tiene muchas desventajas. Ellos son:
- Los MPP son en gran parte subjetivos.
- La calidad del plan de procesos está directamente relacionada con la habilidad y experiencia del planificador.
- La incorporación de cambios en los procesos es extremadamente difícil.
- Los cambios tecnológicos o los cambios en el tamaño de los lotes requieren el cambio en el plan de proceso. Los MPP tardan en responder.
- Es difícil verificar si el plan de proceso es coherente y está optimizado. Cuando no está optimizado, especificará requisitos excesivos de herramientas y materiales.
- Es tedioso buscar manualmente los planes de proceso de piezas similares entre la gran cantidad de documentación de la empresa.
Planificación de procesos asistida por computadora
Planificación de procesos asistida por computadora (CAPP) se ha convertido en el enlace más crítico para los sistemas CAD/CAM integrados. CAPP es la aplicación de computadoras para ayudar al planificador de procesos humanos a ejecutar la función de planificación de procesos. CAPP no también reduce el tiempo y el esfuerzo necesarios para preparar planes de proceso consistentes, sino que solo crea una interfaz automatizada entre diseño asistido por computadora (CAD) y fabricación asistida por ordenador (CAM) para conseguir una integración completa dentro del sistema de fabricación.
La entrada de este proceso es un modelo CAD de la pieza de trabajo que se creará y el resultado de este proceso es un plan de proceso detallado a partir del cual se puede crear/fabricar la pieza de trabajo.
Un sistema CAPP completo incluiría:
Dos enfoques básicos para la planificación de procesos automatizados son:
1 Método variante
Método variante: La planificación de procesos variantes explora las similitudes entre los componentes (piezas) y busca en una base de datos para recuperar el plan de proceso estándar para la familia de piezas a la que pertenece el componente. El plano se recupera y se modifica para crear un plano adecuado para la nueva pieza.
En el enfoque variante, el plan de proceso se genera en dos etapas operativas. Están :
Preparatoria Etapa
En la etapa preparatoria los componentes existentes se codifican, clasifican y agrupan en familias de piezas. La clasificación y codificación ofrece una forma relativamente fácil de identificar la similitud entre las partes. A partir de entonces, se pueden formar familias de piezas agrupando piezas similares.
Se establecen varios esquemas de codificación. MICLASS, DCLASS, OPITZ, CODE son algunos de los esquemas de clasificación. Una vez formadas las familias parciales, a cada familia se le asigna un plan estándar. Un plan estándar consta de un conjunto de procesos de mecanizado, que representa el conjunto común de procesos para fabricar las piezas.
Producción Etapa
En la etapa de producción el componente entrante se codifica según su característica geométrica o los requisitos de procesamiento. El mismo esquema de codificación utilizado en la etapa preparatoria también se utiliza aquí. El código resultante se utiliza como base para asignar la pieza a una familia de piezas.
Si el sistema de codificación se utiliza de manera eficiente, la pieza debe ser similar a las otras piezas pertenecientes a su familia. Se puede obtener un plan de proceso para la nueva pieza modificando el plan estándar (de la familia de piezas a la que pertenece la nueva pieza) recuperado de la base de datos.
2 Método generativo
Método generativo: La planificación generativa de procesos asistida por computadora (GCAPP) sintetiza la información de fabricación para crear un plan de proceso para un nuevo componente (parte). Las lógicas de decisión y los métodos de optimización están codificados en el propio sistema, lo que da como resultado una interacción humana mínima o nula en la planificación del proceso.
Un sistema generativo produce un plan de proceso completo a partir del dibujo de ingeniería o un archivo CAD.
Las tres áreas de un sistema GCAPP son:
En GCAPP, las especificaciones de diseño se ingresan en el sistema. La lógica de decisión reconoce el material en stock y las características de mecanizado de la pieza. Además, determina las secuencias óptimas de operaciones junto con los tipos y ubicaciones de accesorios óptimos.
Desventajas de la planificación generativa de procesos asistida por computadora
En los sistemas GCAPP se observan las siguientes desventajas.
Hasta ahora aprendió sobre los pasos de planificación de procesos, definición, tipos, secuencias de actividades, ventajas y desventajas de los diferentes tipos de planificación de procesos. Comparta este artículo con sus amigos y dé su opinión en los comentarios a continuación.
Tecnología Industrial
- ¿Qué son las técnicas de prueba? Tipos, ventajas y desventajas
- ¿Qué es una máquina virtual? Tipos y ventajas
- Qué es el diseño de sistemas integrados:pasos en el proceso de diseño
- ¿Qué es Formar? Tipos de proceso de formación [Notas y PDF]
- ¿Qué es el brochado? - Proceso, trabajo y tipos
- ¿Qué es la forja? Definición, proceso y tipos
- ¿Qué es la carburación? Definición, tipos y proceso
- ¿Qué es la fundición de metales? Definición, tipos y procesos
- ¿Cuáles son los pasos principales del proceso de mecanizado?
- ¿Cuáles son los 4 tipos de procesos de fabricación?
- ¿Cuáles son los pasos involucrados en el proceso de ensamblaje de PCB?