Automatización para todos
La automatización alguna vez fue solo para las grandes fábricas, pero ahora los talleres pequeños también pueden beneficiarse
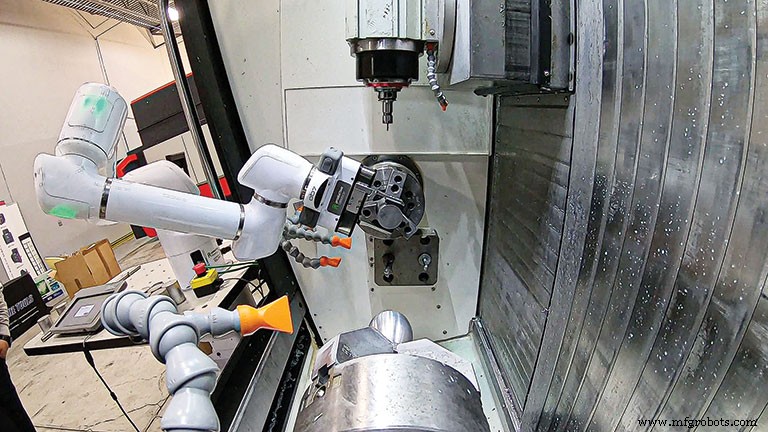
La automatización de los talleres de trabajo se está acelerando, impulsada por la influencia combinada de la Industria 4.0, la continua escasez de mano de obra de fabricación calificada y la pandemia de COVID.
La disponibilidad de opciones robóticas y de transporte de materiales más personalizadas que nunca está ayudando a los fabricantes más pequeños a producir más mientras mueve a los operadores a tareas de mayor valor agregado. La creciente demanda de equipo de protección personal (PPE), junto con la necesidad de proteger a los trabajadores, también ha aumentado los esfuerzos de automatización de las tiendas.
Courtney Ortner, directora de marketing de Absolute Machine Tools, con sede en Lorain, Ohio, resumió claramente los beneficios de la automatización, claramente amplificados durante la pandemia:“Con el uso de cobots (robots colaborativos), tienes un compañero de trabajo y no No tienes que preocuparte por el distanciamiento social. Además, muchas tiendas están perdiendo trabajadores debido a la cuarentena, por lo que esto permite que una tienda continúe funcionando incluso con la pérdida de personal. Y no podemos olvidar que las capacidades de fabricación sin luces son más comunes debido al uso de la automatización; incluso con un cobot, puede configurar un trabajo un viernes por la noche y el lunes por la mañana está listo, lo que a menudo le permite adelantarse a su ciclo de producción”.
Marcha de los Cobots
Los robots suelen ser lo primero en lo que la gente piensa cuando el tema se centra en la fabricación automatizada. Su variante segura para los humanos, los cobots, continúan mejorando en facilidad de configuración, flexibilidad y carga útil.
Desde su introducción hace 15 años, las unidades de Universal Robots (UR), Boston, se han convertido en un pilar en los talleres, particularmente en entornos de bajo volumen y alta combinación. Con una versión de carga útil de 16 kg (UR16) presentada en 2019, UR continúa ampliando los límites de dónde los robots pueden encajar en un flujo de trabajo de producción.
2020 ha sido un año especialmente ocupado, señaló Joe Campbell, jefe de marketing de UR para América del Norte. Han surgido dos temas:la reorganización impulsada por la pandemia y la adopción de nuevos modelos de producción.
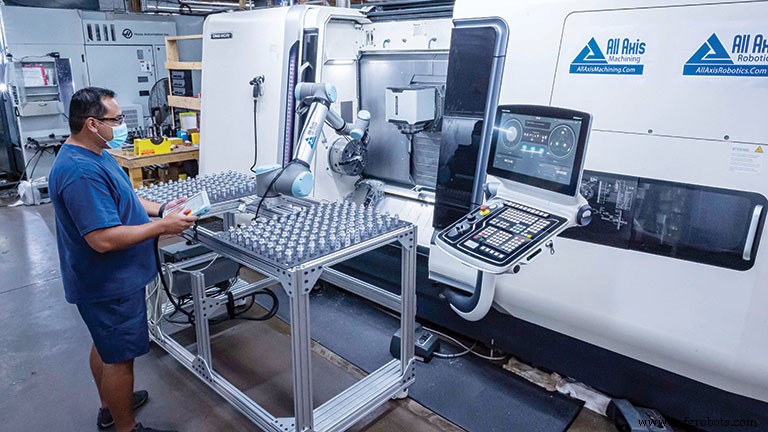
Las pequeñas tiendas en particular, presionadas para usar de manera eficiente cada centímetro de espacio limitado, están implementando cobots para mantener a los trabajadores socialmente distanciados, señaló. "Si tiene un grupo de tres herramientas, coloca uno o dos cobots para darles a los operadores un respiro".
Además, las tiendas se están dando cuenta de cómo los cobots pueden mejorar los resultados. "Los talleres están tomando una mirada diferente" al horario de solo los días de semana "y encuentran que el equipo de fabricación está abierto a una mayor flexibilidad". Un cliente de UR creó un turno de fin de semana y descubrió que muchos miembros del equipo aceptaron la nueva oportunidad. En otros casos, los talleres que anteriormente contaban con un operador calificado que realizaba la configuración y la carga de la máquina agregaron cobots para la función de carga mientras el operador supervisa varias máquinas.
Las unidades UR ahorran horas de taller en tiempo de configuración. Se pueden configurar para funcionar en un piso, pared o techo a través de la pantalla táctil; otros robots a menudo se construyen especialmente para una orientación particular. Los tiempos de ciclo también se reducen, particularmente porque los cobots UR se pueden configurar con una pinza doble para descargar simultáneamente una pieza terminada e insertar una nueva pieza en bruto.
Para la flexibilidad de UR es fundamental la capacidad de combinar sus cobots con una variedad de equipos y software de terceros. Se accede a estos a través del programa UR+, “una especie de tienda de aplicaciones” para UR, dijo Campbell. Se publican interfaces mecánicas, eléctricas y de software para robots UR, y terceros desarrollan productos para cumplir con esas especificaciones. “Más importante aún, nos los envían para que los probemos y validemos. Si decimos que una pinza es plug-and-play, lo es porque la probamos”.
En el ecosistema de UR de 288 periféricos se incluyen cargadores de piezas, sistemas de visión, sensores, opciones de montaje, cubiertas de robots y aplicaciones. Por ejemplo, Beacon by Hirebotics permite a los operadores monitorear cobots a través de la nube. "Puede ver las estadísticas de producción y hacer ajustes sobre la marcha", dijo Campbell.
En marzo, el programa UR+ se amplió para incluir kits de aplicaciones que combinan componentes como pinzas con software "para resolver un problema de aplicación particular". Un kit, de Robotiq, cuenta con una lijadora orbital, hardware de montaje, mangueras de aspiración y software que permite a los usuarios programar un protocolo de lijado para un producto como muebles o gabinetes. “Puede programar contornos complejos en minutos, no en días”, dijo Campbell. Mientras tanto, el kit ActiNav de UR es un kit de carga de máquina flexible que permite a los usuarios tomar piezas de un contenedor y cargarlas en varias máquinas con una orientación precisa. “Puede introducir una pieza nueva en el sistema en menos de una hora”.
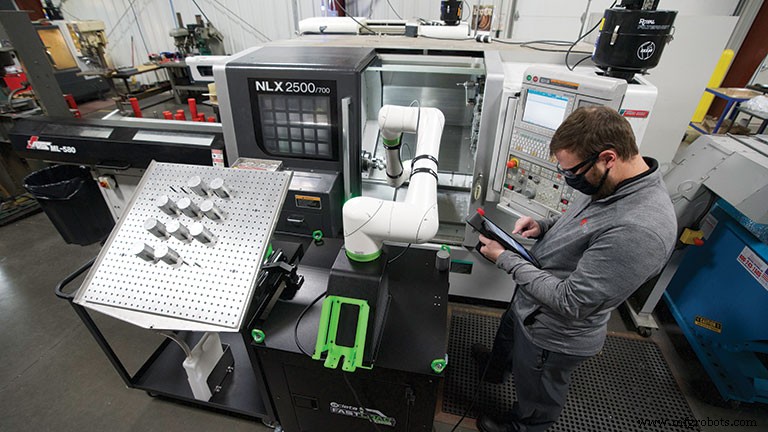
Otra de las claves para que los comercios adopten la automatización es la opción de la formación virtual. UR superó recientemente un hito de capacitación en línea de más de 100 000 operadores a través de UR Academy, que presenta módulos de capacitación gratuitos sobre programación e implementación de cobots de UR.
“Si tiene que enviar a sus tres maquinistas principales fuera del sitio durante la mayor parte de una semana para que se capaciten, su producción es aplastada”, dijo Campbell. Las tiendas pequeñas "realmente se sienten atraídas por la capacidad de realizar el 90 por ciento de su capacitación en línea".
Carga rápida para el futuro
Además de las presiones de automatización de la pandemia, la reubicación de la producción en EE. UU. es otro impulsor importante de robots y equipos de carga para talleres.
“Los fabricantes y talleres que han sido históricamente lentos en adoptar la robótica están comenzando a adoptar la robótica más que nunca”, dijo Jake Corning, gerente de producto e ingeniero mecánico de Acieta LLC, Waukesha, Wis. el interés y los pedidos han aumentado desde que comenzó la pandemia. Ven el beneficio que ofrece la robótica para mantener sus máquinas en funcionamiento y la fabricación de piezas incluso en tiempos de distanciamiento social, empleados enfermos y/o cierres que están afectando las capacidades de producción”.
Además, con la interrupción de la cadena de suministro global, “también ven que la pandemia va a traer una gran cantidad de operaciones de regreso a los Estados Unidos. Se enfrentarán a una escasez de mano de obra aún más significativa que antes de la pandemia si no adoptan la automatización. En última instancia, a pesar de la tragedia que la pandemia ha causado en nuestro país, los fabricantes de EE. UU. ya están adoptando con más comodidad la tecnología robótica y están viendo los beneficios que mejorarán su competitividad, mejorarán la satisfacción laboral y la lealtad de los trabajadores, y entregarán al consumidor estadounidense una mayor competitividad. precios.”
Acieta ofrece una gama de soluciones particularmente adecuadas para rutinas de bajo volumen y mezcla alta, explicó Corning.
“Los sistemas FastLOAD CX1000 y CR2000 están destinados a ser fáciles de usar para los usuarios de robots primerizos”, dijo. “Nuestra interfaz de pantalla táctil para el CR2000 hace que sea muy fácil hacer funcionar el robot con diferentes tamaños de piezas. El operador solo necesita ingresar los parámetros de la pieza y el sistema ajusta automáticamente el programa para ejecutar las piezas nuevas. Las pinzas robóticas y la fijación de piezas son flexibles para una amplia variedad de tamaños de piezas, de modo que muchas piezas diferentes pueden funcionar en el mismo sistema”.
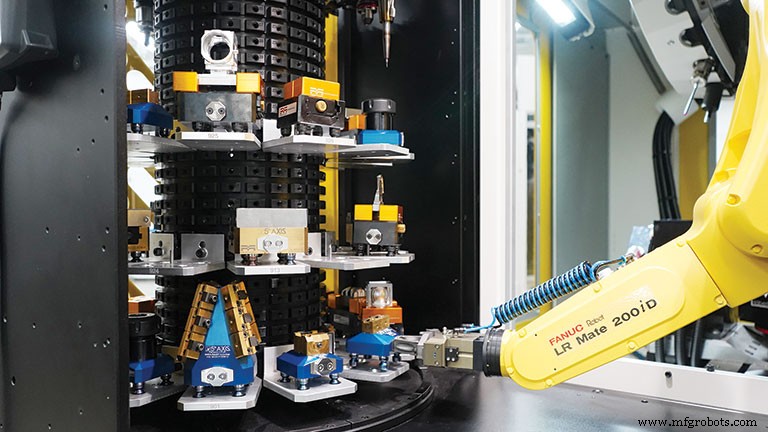
Los cambios en el CR2000 se pueden realizar en minutos, y los sistemas CX1000, CR2000 y DR2000 están diseñados para que el robot pueda seguir funcionando mientras el operador carga o descarga piezas. "Esto permite que las máquinas trabajen sin parar durante los descansos, los almuerzos e incluso fuera de los turnos, siempre que haya suficientes piezas entrantes".
Montada sobre ruedas, la CX1000 es fácil de maniobrar en el taller. También está disponible con múltiples opciones de carro de fijación de cambio rápido y utiliza el robot CRX-10iA/L de FANUC, “que tiene una interfaz de pantalla táctil muy fácil de usar con íconos de programación de arrastrar y soltar”, dijo Corning. “Cuando sus desafíos son más complejos o de mayor escala, nuestras soluciones personalizadas también pueden diseñarse para tiradas de piezas de bajo volumen y mezcla alta mediante el uso de tecnologías como la visión, los cambiadores de herramientas al final del brazo y las fijaciones flexibles”.
Las celdas de mantenimiento de máquinas que acompañan a Acieta han demostrado ser populares, señaló Corning. “Son sistemas de robot estándar diseñados para trabajar con una amplia variedad de piezas. Dado que son productos estándar prediseñados, son mucho menos costosos que un sistema personalizado tradicional y se pueden entregar en tan solo una semana. Los tres sistemas pueden atender varias máquinas herramienta al mismo tiempo. Además, nuestros sistemas CX1000 y CR2000 utilizan robots colaborativos, que ayudan a maximizar el uso del espacio en el piso porque no requieren cercas de seguridad”.
Para los talleres que automatizan por primera vez, un gran punto de partida es el CX1000 colaborativo, dijo Corning. Al liberar a los trabajadores de tareas repetitivas, la automatización les permite “aprender a programar o realizar el mantenimiento de un sistema robótico. Un operador que anteriormente atendía una máquina ahora puede administrar sistemas robóticos en varias máquinas”.
Resolviendo Problemas Esenciales
Con su profundo conocimiento de las necesidades únicas de los talleres de mecanizado y trabajo, Methods Machine Tools Inc., Sudbury, Mass., ayuda a los fabricantes a automatizar con miras a generar más negocios mientras crea una fuerza laboral más capacitada.
“Necesitamos más buenos maquinistas”, afirmó John Lucier, gerente de automatización de Métodos de FANUC. “Eso es con lo que nos ayudan los robots. Los robots ayudan a los talleres a conseguir más puestos de trabajo para que puedan poner a trabajar a más maquinistas”. Un maquinista bien capacitado no está cargando y descargando máquinas, "las está configurando, seleccionando herramientas y escribiendo programas".
Al igual que otros proveedores, Methods ha visto un aumento en la automatización relacionada con la pandemia, dijo, particularmente para producir piezas de ventiladores.
Antes de la pandemia, Lucier recordó haber visitado muchas tiendas de bajo volumen que buscaban la automatización por primera vez. Las operaciones de volumen medio que cambian las celdas dos o tres veces por semana para producir aproximadamente 5000 piezas se están volviendo comunes, y Methods proporciona la línea Job Shop Cell Pro basada en cintas transportadoras para esos entornos. Los divisores de carril ajustables permiten un cambio rápido entre piezas pequeñas y grandes. Otra opción popular es una serie de cajones con una placa de acero o aluminio con orificios para 20 a 40 piezas.
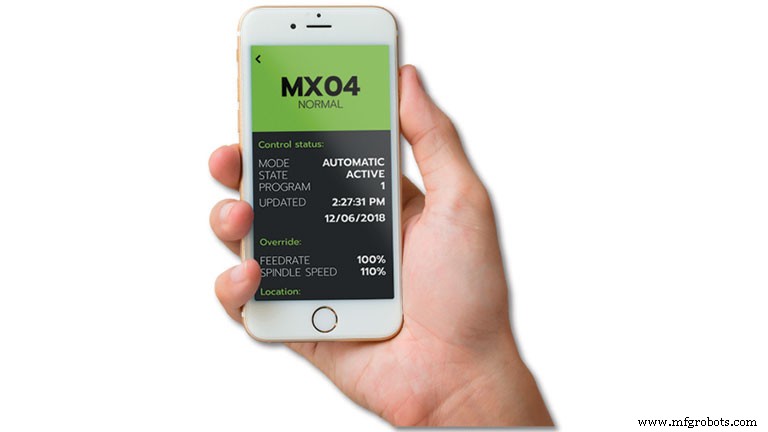
La sujeción de piezas es otra consideración importante, agregó Lucier; Las prensas automatizadas son una solución relativamente simple. “No tiene que ser complejo, con cilindros giratorios y cosas por el estilo. Podría ser algo así como un buen portabrocas o un tornillo de banco con sistema neumático o hidráulico para abrir y cerrar, y usted está haciendo sus propias mordazas, no muy diferente de lo que hacen muchos talleres con tiradas de unas 50 piezas.
Para piezas de menor volumen, incluso tamaños de lote de uno, Methods ofrece los sistemas de carrusel de almacenamiento rotativo robótico Plus-K y Plus-K 60. “No estamos haciendo que el robot sea específico para cada pieza; el robot está configurado para introducir y sacar piezas de sujeción genéricas de la máquina, ya sea un pequeño tornillo de banco o una tarima. El robot está configurado para agarrar una característica común en la parte delantera de la sujeción”. Las piezas se cargan en un tornillo de banco manual y el robot está preprogramado para actuar como un sistema de carga de tarimas; no es necesaria la programación del usuario final. Este sistema también mejora la oferta de herramientas estándar en RoboDrill, pasando de 21 a 161 herramientas opcionales.
Con soluciones como estas, los talleres de trabajo suelen ver el retorno de la inversión en menos de 12 a 18 meses. “Nuestro objetivo es convencerlo de que lo opere en dos o tres turnos:tomar una celda robótica, llenar el sistema de alimentación con piezas e irse a casa a las 5:00 p. m., y obtener de dos a seis horas de tiempo de ejecución. Si puedo conseguir un sistema automatizado que maneje el 80 por ciento del trabajo que planeas hacer, lo estamos haciendo bastante bien”.
Las soluciones de Informating Methods son una conexión de larga data con los talleres y el conocimiento de cómo funcionan, señaló Lucier, él mismo un maquinista de oficio. Por ejemplo, suele recordar a los talleres que pueden mecanizar sus propias pinzas de acero o aluminio. Y ajustar los programas suministrados previamente en los robots puede ser más fácil que la programación CNC. El grupo de integración de automatización de la empresa es muy consciente de los problemas relacionados con las máquinas herramienta, desde el refrigerante y las virutas hasta la rotación de herramientas, la vida útil de las herramientas, el desbarbado y más.
“Si va a poner robots en máquinas herramienta, quiere un integrador de robots que haga eso”, concluyó Lucier. "Los beneficios de los robots no deberían ser difíciles de justificar".

Evaluar la necesidad, agregar velocidad
Comprender las necesidades de automatización de un taller comienza con una evaluación exhaustiva del volumen requerido para aumentar la productividad.
Cuando un cliente nos contrata, dijo Ortner de Absolute, “hacemos un diseño del sistema, decidimos las mejores prácticas para automatizar (sistemas transportadores, robots, manejo de materias primas, manejo de piezas terminadas) y luego lo diseñamos en CAD para garantizar que todas las piezas encajen en su piso. plan, todo mientras trabaja dentro de su presupuesto.”
Además de ofrecer una variedad de equipos de automatización estándar, desde cobots hasta manejo de piezas y monitoreo, Absolute "ofrece un paquete llave en mano", dijo Ortner. "Obtenemos lo que creemos que es la mejor solución y trabajamos con esos proveedores para garantizar el éxito".
La experiencia de Absolute en la obtención del equipo adecuado claramente vale la pena, señaló. “Un cliente que usa un cobot OB7 obtiene un 20 % más de eficiencia y mucho menos desechos en un turno. Pueden reducir los tiempos de entrega en dos semanas en esta ejecución en particular, lo que abre la máquina o celda para trabajo adicional para un ROI más alto. Además, debido a que no tienen que realizar tareas repetitivas con tanta frecuencia, hay menos reclamos de compensación laboral para la empresa, y los trabajadores tampoco se reportan enfermos con tanta frecuencia, ahorrando [al taller] mucho dinero”.
Como han descubierto otros talleres, la mayor disponibilidad de operadores para otras tareas a menudo significa que “tienen más tiempo para contribuir a los procesos generales, como los controles de calidad. Están más involucrados en la gestión de procesos en lugar de simplemente presionar botones y están menos aburridos y fatigados”.
Obtener esos beneficios puede ser sorprendentemente rentable, agregó Ortner. “Nuestra línea de cobots de Productive Robotics comienza en $34,900 para el paquete CNC básico. Puede pasar del paquete CNC básico y actualizar a una celda completamente integrada utilizando varios cobots, transportadores, métodos de medición en proceso y presentación de piezas”.
Supervisión para obtener más resultados
Para ayudar a los talleres a mantener los trabajos a tiempo y ejecutar más proyectos desatendidos, Mitsubishi Electric Automation Inc., Vernon Hills, Illinois, ofrece su Integrated Machine Analytics (IMA) basado en MTConnect para el monitoreo de máquinas. La aplicación IMA Mobile ofrece una entrada fácil de instalar para el monitoreo de máquinas.
Con IMA, los talleres "pueden comprender mejor la producción, lo que ayuda a programar con precisión los trabajos para aprovechar al máximo sus máquinas disponibles y las horas de trabajo, así como a ofertar con mayor precisión por más trabajos", dijo Robert Brodecki, gerente de productos de servicios móviles de IMA. para Mitsubishi Electric Automatización.
El único hardware requerido es el cableado Ethernet y un concentrador/conmutador si se conectan varias máquinas, y la configuración de una máquina demora entre 5 y 10 minutos, explicó. “Con el punto de bajo costo, los usuarios pueden ver el ROI en cuestión de días, especialmente si están ejecutando una producción desatendida o sin luces y han perdido tiempo de producción debido a una falla en la máquina y no se enteran hasta más tarde. Con las notificaciones de IMA Mobile, sabrá dentro de 10 a 15 segundos si una máquina ha dejado de cortar, sin importar dónde se encuentre”.
El monitoreo de la máquina mejora significativamente el rendimiento, agregó. “Solo observando el estado de ejecución, muchos talleres de trabajos suelen tener máquinas que ejecutan trabajos entre el 25 y el 40 por ciento de su tiempo disponible. A través de un simple monitoreo del estado actual a través de IMA Mobile, pueden moverlo rápidamente al 50 por ciento o más al poder atender de inmediato cualquier máquina que haya detenido la producción por cualquier motivo. Estos también son datos reales directamente de la máquina; elimina el juego de adivinanzas de cuánto tiempo la máquina estuvo cortando, inactiva o apagada”. Las horas de máquina disponibles se amplían al ejecutar más turnos con menos trabajadores, o desatendidos, sin pérdida de producción debido a una parada inesperada.
Con IMA Mobile, los operadores pueden pasar a tareas de valor agregado "sabiendo que la aplicación les notificará cuando el trabajo finalice o sea interrumpido por algo que requiera atención".
Con un costo de entrada relativamente bajo, señaló Brodecki, IMA permite a los usuarios “comprender su producción y realizar mejoras, así como iniciar proyectos de mecanizado desatendidos más simples mientras se aseguran de que sus máquinas continúan funcionando. Dado que todo se basa en el estándar MTConnect, si un usuario decide pasar a un sistema de monitoreo personalizable y más profundo, no necesita pagar para que sus máquinas se vuelvan a conectar; simplemente apuntan el nuevo software a los agentes de MTConnect y se puede acceder rápidamente a los datos de la máquina”.
Esa facilidad de entrada ha sido particularmente importante para la automatización en tiempos de COVID, concluyó. “Tiene sentido, ya que las empresas buscan automatizar más, pero es difícil saber exactamente dónde y cómo sin datos de producción precisos para identificar las áreas a automatizar. Al comienzo de la pandemia, muchas empresas con las que hablábamos todavía estaban indecisas sobre el monitoreo de máquinas. A medida que avanzaba la pandemia y las empresas se dieron cuenta de que ya no podrían evitar las soluciones de automatización y trabajo remoto, trasladaron estos proyectos a la parte superior de la lista".
Sistema de control de automatización
- Automatización:Nuevas pinzas para Cobots
- Automatización:Pinza de vacío fuerte para cobots
- Automatización:Nuevos accesorios para Cobots
- Automatización:Cuchilla de desbarbado compatible para robots
- Automatización:destornillador Plug-and-Play para Cobots
- Automatización:lo que significa para el futuro de los negocios
- ABB pone a prueba una solución de automatización para centros de datos
- Un manual para implementar la automatización inteligente hoy
- Qué significa la hiperautomatización para los usuarios de RPA
- Schneider Electric aboga por la automatización industrial universal
- Automatización universal:¿una necesidad para la Gran Bretaña posterior al Brexit?