Replanteamiento de los sistemas de control para plataformas de múltiples pocillos
Los requisitos de datos y control impulsan la necesidad de una arquitectura de control escalable y modular.
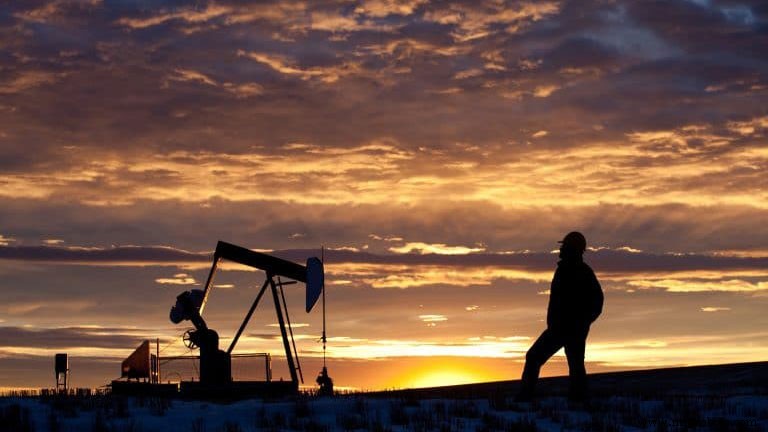
Los avances en la perforación han estimulado la evolución de las operaciones de petróleo y gas desde campos simples de plataforma de un solo pozo hasta plataformas de múltiples pozos más complejas.
Hoy en día, muchos productores utilizan técnicas de fracking y perforación lateral para colocar 10 o más pozos en una plataforma. Algunos operadores incluso están impulsando sus operaciones hasta 52 pozos en una sola plataforma.
Estos avances no solo han aumentado las recuperaciones de producción de los pozos, sino que también han creado oportunidades de producción completamente nuevas en áreas no convencionales. También han permitido a los productores de petróleo y gas reducir su huella operativa.
Sin embargo, a pesar de todos los beneficios de las plataformas de múltiples pozos, su gran aumento en tamaño y alcance ha creado un nuevo desafío. La mayor densidad de múltiples pozos en una sola plataforma aumenta el equipo requerido en el sitio y da como resultado requisitos de control y datos mucho mayores.
Las arquitecturas de control tradicionales que se han utilizado durante décadas están siendo llevadas al límite y es posible que ya no sean sostenibles. En cambio, se necesitan sistemas de control más avanzados para manejar las arquitecturas escalables requeridas por las plataformas de pozos modernas.
Como resultado, tanto los operadores como los fabricantes de equipos que los respaldan ahora deben modificar, si no cambiar radicalmente, el enfoque de sus sistemas de control para estas plataformas de pozos múltiples.
Evolución de la tecnología RTU
Los productores upstream de petróleo y gas han confiado en la tecnología de unidad terminal remota (RTU) para el control del sitio del pozo durante décadas. Inicialmente, el costo de implementar las RTU y los desafíos para programarlas limitaban los dispositivos a una simple adquisición y control de datos.
Sin embargo, con el tiempo, las RTU incorporaron más funciones, incluidas E/S, comunicaciones y programación IEC-61131. Estas capacidades permitieron a los operadores de petróleo y gas monitorear más puntos de datos, registrar el historial y las alarmas, y agregar cálculos más complejos a las RTU. Los constructores de equipos y las empresas de ingeniería también comenzaron a desarrollar aplicaciones especiales para controles de levantamiento artificial en boca de pozo con controladores de microprocesador patentados.
Eventualmente, prácticamente todos los fabricantes de elevadores artificiales habían desarrollado su propia RTU para controlar y optimizar sus respectivas soluciones. Las empresas de ingeniería también desarrollaron sus propios métodos con aplicaciones RTU ligeramente diferentes, mientras que los fabricantes de instrumentación introdujeron nuevos instrumentos para medir casi cualquier punto de proceso requerido.
Sin embargo, recientemente, los mayores requisitos asociados con las operaciones de plataforma de múltiples pozos han comenzado a superar las capacidades de la tecnología RTU.
Dispositivos llevados al límite
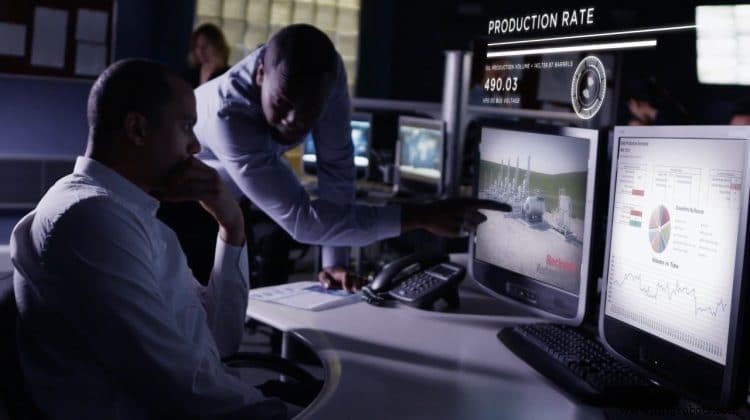
Cada pozo en una plataforma de múltiples pozos requiere un levantamiento artificial, medición de flujo, control de equipos y medición de nivel. Esto crea más E/S y demanda de control de lo que puede manejar una sola RTU. Como resultado, los productores de petróleo y gas se ven obligados a comprar RTU adicionales y distribuir la aplicación y el control del sitio en varias unidades.
Los productores de petróleo y gas han implementado con éxito múltiples controladores RTU en una plataforma de pozo, pero se encuentran con algunos problemas comunes con estas arquitecturas. Algunos de estos problemas incluyen:
- Gestión de cambios de múltiples configuraciones o programas en cada plataforma de pozo.
- Gestión de la comunicación de las numerosas RTU en el sitio (p. ej., comunicaciones entre pares).
- Comunicaciones SCADA con hardware de múltiples proveedores.
- Ejecución poco confiable de programas personalizados en las RTU.
La máxima demanda de dispositivos RTU surge cuando se necesita un control de almohadilla de múltiples pozos mucho más grande. Esto puede incluir una operación con 10 o incluso varias docenas de pozos en una sola plataforma de pozos. La mayor densidad de pozos en una plataforma también aumenta el equipo requerido en el sitio. Por ejemplo, muchas de estas almohadillas para pozos tienen su propio separador.
También resulta más económico instalar compresores de tubería, unidades de recuperación de vapor (VRU) y torres de VRU debido a la alta tasa de gas natural producido en la plataforma. Las unidades de transferencia de custodia automática (LACT) de arrendamiento, la transferencia de agua y las máquinas de inyección de productos químicos también se ven comúnmente en estas plataformas de pozos.
Además, muchos productores de petróleo y gas están invirtiendo en edificios eléctricos conocidos como E-houses. Estos edificios albergan la distribución de energía de los servicios públicos principales, los centros de control de motores (MCC), los conmutadores de red y las fuentes de alimentación ininterrumpida (UPS), y a menudo están controlados ambientalmente.
Todos estos aumentos, en equipos, instrumentación de campo y aplicaciones, solo agravan los problemas comunes con las arquitecturas RTU.
También crean nuevos desafíos de servicio y soporte. El uso de múltiples RTU ha llevado a múltiples configuraciones de aplicaciones y programas para mantenerlas. También obligó a los operadores de petróleo y gas a trabajar con múltiples proveedores.
Además, tener varios dispositivos de múltiples proveedores también requiere que los trabajadores tengan más capacitación y experiencia para brindarles soporte. Si bien algunos productores cuentan con suficiente personal capacitado para manejar el mantenimiento de los sistemas de control de pozos, muchos no lo tienen. Estos productores deben confiar en el soporte del fabricante o en el soporte de ingeniería por contrato para mantener sus sistemas de control.
Transición a sistemas de control escalables y modulares
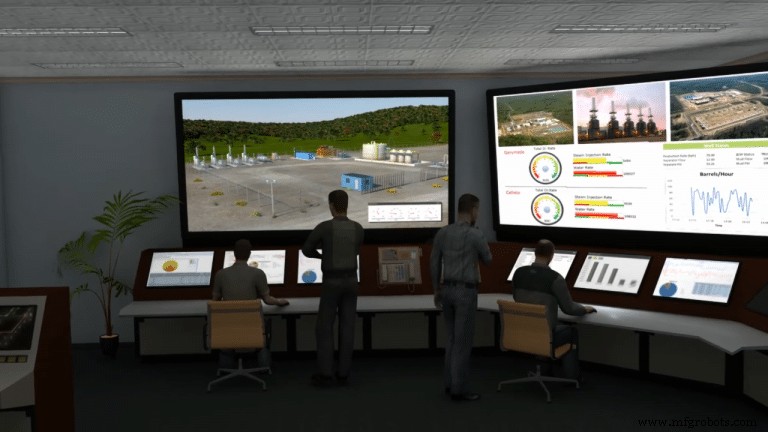
Las RTU han cumplido su función durante décadas en el manejo de requisitos de control simples, interacción simple entre dispositivos de campo y comunicaciones simples. Pero ya no son suficientes en los entornos operativos más complejos de la actualidad.
Muchos productores de petróleo y gas que han experimentado problemas comunes de RTU han encontrado una solución alternativa viable en forma de un controlador lógico programable (PLC) modular y escalable. La tecnología PLC se ha perfeccionado durante años en entornos de control de procesos industriales que son tan resistentes como la producción de petróleo y gas aguas arriba.
Los PLC ofrecen una serie de ventajas en comparación con las RTU:
- Modularidad: Algunas RTU admiten hardware modular. Pero equilibrar los requisitos del módulo con los requisitos de aplicación y control en una RTU es mucho más difícil que en un PLC. Además, los módulos de terceros para RTU normalmente no están disponibles porque las RTU no son arquitecturas abiertas, mientras que los PLC sí lo son.
Hay disponible una amplia variedad de módulos para PLC que permiten monitorear y controlar una amplia variedad de instrumentos de campo. El soporte de comunicación para muchos tipos de redes diferentes también se admite a través de la configuración modular. - Escalabilidad: Esto es importante cuando se considera cómo se ensambla una almohadilla de múltiples pocillos. A menudo, se instalará un solo pozo en un sitio de múltiples pozos, y no será hasta meses o incluso años después que se conectarán pozos y equipos adicionales.
En estos casos, los fabricantes de equipos desean ser capaz de construir patines de equipos fuera del sitio y luego simplemente enchufarlos y configurarlos en la plataforma del pozo. Quieren reducir la necesidad de abrir zanjas, tirar de cables, terminar cables, instalar paneles e instrumentos en el campo para ayudar a reducir costos. En este caso, se requiere escalabilidad tanto en la programación como en el hardware, y eso es exactamente lo que ofrece la tecnología PLC. - Facilidad de programación: Históricamente, los PLC fueron vistos como un lienzo en blanco para la automatización y el control. Solo las empresas de ingeniería o los programadores experimentados sabían cómo empezar desde cero y desarrollar el control requerido en un PLC.
Sin embargo, los PLC modernos tienen bibliotecas de código predesarrollado y documentado que se pueden agregar rápidamente en casi Moda de arrastrar y soltar. Algunos proveedores de PLC también tienen bibliotecas de petróleo y gas aguas arriba desarrolladas previamente que se pueden configurar en el sitio. Los productores de petróleo y gas solo necesitan habilitar y configurar los datos necesarios de la HMI para iniciar un PLC o agregar hardware de patín a un sistema existente.
Esto puede eliminar la necesidad de alguien como un pozo técnico con experiencia especializada para conocer el entorno de programación y escribir código nuevo al agregar hardware.
Además, los cambios de configuración y programa se pueden realizar en línea en un PLC sin cerrar el proceso. Las RTU tradicionalmente no pueden aceptar dichos cambios sin desconectarse y descargarse. Este es un diferenciador fundamental en un entorno moderno de plataforma de múltiples pozos porque apagar el sistema de control da como resultado una pérdida de producción. - Funcionalidad de E/S remotas: Las RTU tradicionalmente no tienen funcionalidad de E/S remotas nativas, pero los PLC sí. Esto puede reducir los costos de instalación. Además, cuando se agregan patines de equipos a un sitio, pueden venir con E/S e instrumentos premontados y cableados. La puesta en marcha de estos patines es tan simple como conectar un cable Ethernet a un conmutador y configurar las E/S en el controlador.
Mejora de la gestión del ciclo de vida
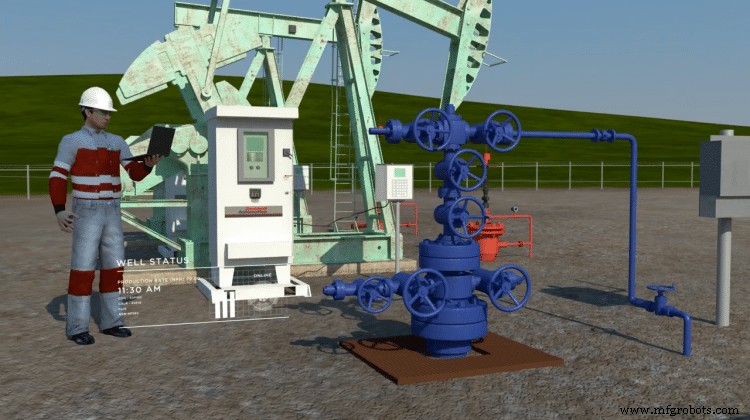
La gestión del ciclo de vida de las plataformas de pozos puede ser un gran dolor de cabeza para los equipos de operaciones. Los pozos pueden pasar por muchos estados de flujo diferentes, incluido el flujo natural, la bomba sumergible electrónica (ESP) o la bomba de cavidad progresiva (PCP) y la bomba de varilla de bombeo. Y el tipo de flujo y el ciclo de vida pueden variar según el pozo.
A menudo se utilizan múltiples RTU solo para controlar los diversos ciclos de vida del pozo. Cambiar la RTU significa cambiar los controladores de comunicación al sistema SCADA porque la RTU física en el pozo es hardware de un nuevo proveedor. Y configurar la RTU para controlar la aplicación y configurar ese hardware en el sistema suele ser un proceso laborioso.
Una plataforma de pozos basada en PLC puede proporcionar un alivio significativo en esta área, brindando beneficios de eficiencia y optimización que los operadores nunca pensaron que fueran posibles.
Mediante el uso de las arquitecturas de hardware de E/S modulares y escalables que ofrece un PLC, los operadores pueden instalar módulos de E/S justo donde se encuentra la instrumentación y enviar esos datos al PLC. E independientemente del enfoque de diseño de E/S que use un productor de petróleo o gas, el hardware en el sistema de control permanecerá constante, las comunicaciones con el sistema SCADA usarán los mismos controladores y el sistema permanecerá en línea y en control de todas las aplicaciones como se realizan actualizaciones. Mientras tanto, solo queda un programa de PLC para mantener.
También está la cuestión del soporte de aplicaciones del proveedor. Como ya se mencionó, muchos proveedores crean sus propias aplicaciones para una variedad de necesidades de producción upstream, y cada proveedor generalmente usa un tipo diferente de RTU. Como resultado, los proveedores generalmente solo admiten algunas aplicaciones específicas, no todas.
El soporte de proveedores de PLC en diseños de almohadillas de múltiples pozos está creciendo diariamente. Esto incluye soporte para aplicaciones de control de equipos, levantamiento artificial y medición de flujo. La automatización de equipos se maneja fácilmente a través de entornos de programación enriquecidos y una amplia variedad de módulos de comunicación y E/S. La medición de flujo también es compatible con la medición de flujo compatible con AGA y API, el soporte de calibración y los informes de transferencia de custodia a los sistemas SCADA. Las aplicaciones de levantamiento artificial, aunque no son tan frecuentes en los PLC, también se están desarrollando rápidamente para admitir todo tipo de levantamientos artificiales.
Por último, muchos productores de petróleo y gas han expresado su frustración porque las aplicaciones RTU son una "caja negra". Esto significa que el sistema está diseñado con entradas específicas destinadas a controlar solo salidas específicas.
Un enfoque de caja negra impide la flexibilidad, ya que no permite que los productores de petróleo y gas cambien la forma en que funciona el sistema. Como resultado, necesitan cambiar de proveedor para satisfacer sus necesidades o simplemente vivir con la tecnología que tienen, sabiendo que no está funcionando con la eficiencia que necesitan.
Un sistema basado en PLC, por otro lado, se puede modificar en el campo con herramientas industriales comunes (IEC-61131), brindando una flexibilidad mucho mayor.
Adoptar la nueva normalidad
El PLC ha sido visto durante mucho tiempo como una solución más adecuada para las instalaciones de fabricación que para el control de plataformas de pozos. Pero las plataformas de pozos modernas de hoy en día son, en esencia, pequeñas fábricas. Tienen edificios con control ambiental, energía de servicios públicos o generadores, y requisitos de datos y control mucho mayores.
Esto los convierte en una opción ideal para un PLC. Un sistema de control de plataforma de múltiples pozos que utiliza las capacidades modulares y escalables de un PLC puede reducir los costos y los tiempos de instalación, mejorar el tiempo de actividad de la producción y facilitar la administración del ciclo de vida.
Zack Munk es gerente de desarrollo de negocios upstream de petróleo y gas en tierra para Rockwell Automation.
Sistema de control de automatización
- Construyendo sistemas de fabricación flexibles para Industrie 4.0
- ASM Assembly Systems utiliza el robot Sawyer de Rethink Robotics para las comprobaciones de control de calidad
- Consideraciones para los paneles de control AFD
- Ventajas de las tecnologías integradas para el diseño modular
- Soluciones simples para sistemas de automatización antiguos
- Las empresas establecen plazos para los sistemas inteligentes
- Los 10 principales flujos de trabajo para fabricantes
- Sistemas locales frente a globales para el control de la producción
- Ventajas de usar VIA en pads
- Marposs anuncia el sistema de control modular BLÚ LT para máquinas herramienta
- ¿Qué son los sistemas de control hidráulico?