El acoplamiento automatizado reduce drásticamente el tiempo de inactividad de la celda de soldadura robótica
No hay mejor manera de resolver un problema que eliminándolo por completo. Al menos así es como KTH Parts Industries Inc. (St. Paris, OH) consideró su decisión de automatizar un proceso de cambio de equipo manual para sus celdas de soldadura robótica.
KTH seleccionó acopladores de servicios públicos GA2 de ATI Industrial Automation (Apex, NC) para lograr la hazaña. Específicamente, el nuevo acoplamiento automático de los servicios públicos de aire y electricidad a las celdas eliminó aproximadamente 65 horas por año de tiempo de inactividad por línea, redujo el costo total de las operaciones y aumentó la utilización y la productividad del equipo.
KTH Parts Industries, un proveedor automotriz mundial de nivel 1 para partes estructurales de la parte inferior de la carrocería, tiene más de 1100 asociados de ingeniería y fabricación involucrados en las muchas fases de la fabricación de partes automotrices, incluido el desarrollo de productos, el análisis de productos, la conformabilidad del producto, la creación de prototipos, el estampado de producción, la formación, soldadura robótica, montaje y envío de piezas.
Una de las competencias principales de KTH es el diseño y la implementación de líneas de soldadura flexibles para componentes de carrocerías de automóviles. Sus líneas de soldadura utilizan accesorios complejos, o plantillas, para mantener los componentes en su lugar mientras un robot los suelda. Cada modelo de automóvil requiere una plantilla diferente, lo que conduce a muchos cambios de equipo en la planta.
Para aumentar la flexibilidad y optimizar el espacio de producción limitado, KTH creó una celda de trabajo de doble cara con una plataforma giratoria. El objetivo de este diseño era mantener el robot activo y reducir el tiempo de configuración. Las piezas se cargan en la plantilla en un lado de la plataforma giratoria mientras el robot suelda las piezas en el otro.
Antes de la instalación de los acopladores de utilidad GA2 de ATI, KTH confiaba en el trabajo manual para conectar y desconectar los cables y cargar las plantillas en los platos giratorios. Multiplique esto por uno o dos cambios por línea por turno, y tendrá una asombrosa cantidad de interacción hombre-máquina en el proceso.
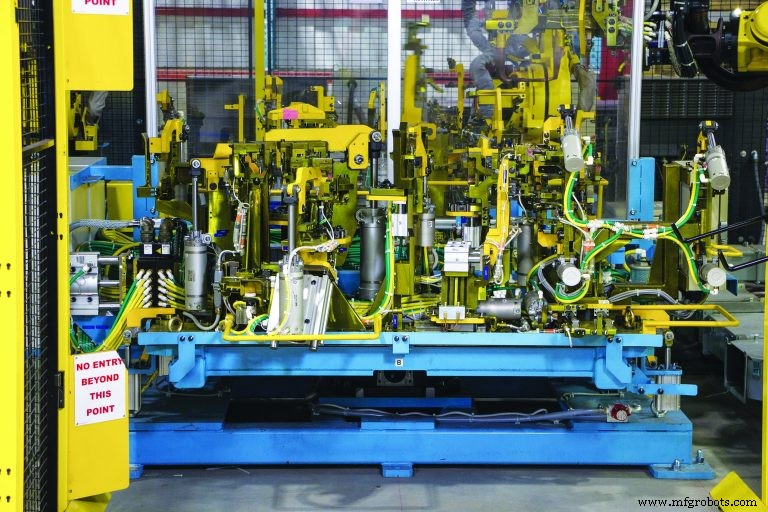
Dave Reed, un líder de proyecto en el departamento de soldadura de KTH, tenía esta opinión sobre el proceso anterior:“Antes de que comenzáramos a usar los acopladores de servicios públicos de ATI, teníamos una línea de aire y un colector, y necesitábamos conectarlos con amarres. En el lado eléctrico, tuvimos que unir las desconexiones de 40 pines girándolas manualmente. Este proceso se repitió muchas veces para cada cambio de plantilla”.
Según KTH, las demandas de trabajo físico del antiguo proceso eran muy altas y, por supuesto, cada vez que un asociado ingresaba a la celda de trabajo, existía un riesgo inherente. En estas condiciones, la alta frecuencia de fallas en los cables no fue una sorpresa. Acoplar y desacoplar los cables con fuerza y torsión inconsistentes generaba un desgaste excesivo. La desalineación de los conectores condujo a pines dañados. Sin un espacio de almacenamiento dedicado para los cables que no se usaban, se dejaban en el piso o encima de otros equipos en la celda.
“Tuvimos líneas de aire cortadas y con fugas, conectores dañados”, dijo Reed. "Se llamó a mantenimiento para tratar de evaluar el problema, pero la mayoría de las veces, era solo una clavija doblada en un conector que nos costaba horas de tiempo de inactividad, aproximadamente 65 horas al año por línea".
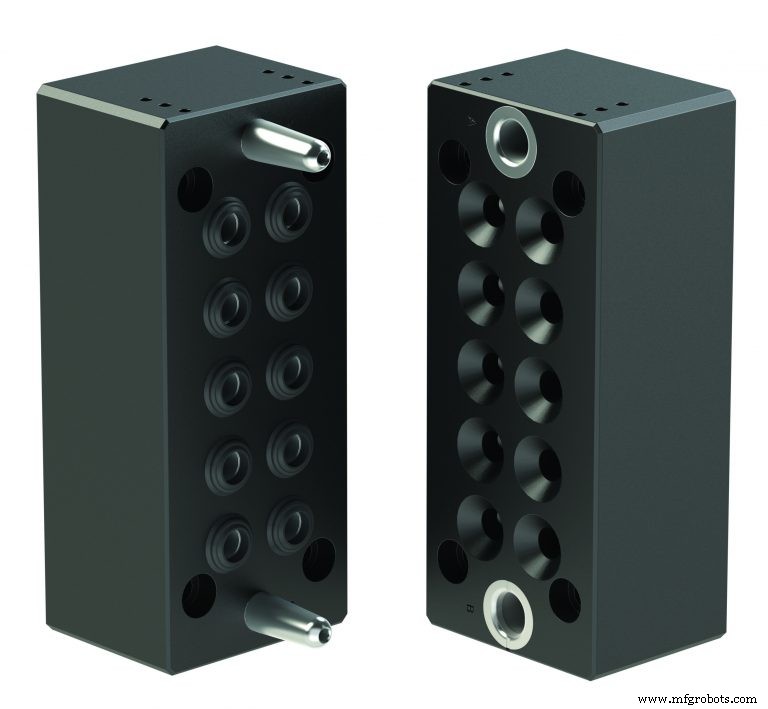
Además de la interacción humana excesiva y las fallas de los equipos, el proceso anterior era una pesadilla para el grupo de soporte de equipos. El líder de la sección del grupo, Jonah Strapp, señaló:“Después de los cambios, tendrías que jugar con algo en la celda para que vuelva a funcionar. El tiempo de inactividad significa pérdida de dinero. Cuando eso ocurre, hay bastante presión para que las líneas funcionen”.
KTH estaba excepcionalmente motivado para mejorar el cambio de plantilla de soldadura para permitir un flujo de operaciones más fluido, aumentar la seguridad de los empleados y reducir los casos de falla del equipo. Matt Myers, ingeniero de personal del grupo de proyectos de ingeniería de KTH, explicó:“Durante nuestro día de operación normal, tratamos de exprimir la mayor cantidad posible de producción de la línea. Cada vez que hacemos un cambio, estamos perdiendo tiempo de producción, lo que se traduce en una gran negativa financiera en nuestros libros. Todo lo que podamos hacer para reducir la cantidad de tiempo de inactividad es increíblemente crítico”.
Ese es exactamente el punto en el que la adopción de los acopladores de servicios públicos de ATI presentó una solución eficiente para ahorrar tiempo. Los acopladores utilitarios de ATI se adaptan bien al cambio de línea de soldadura de KTH. Proporcionan energía, señal y neumática. Los acopladores de servicios públicos de ATI tienen conformidad rotacional incorporada para proporcionar un acoplamiento repetible en un paquete duradero. Dado que el diseño es modular, los acopladores de utilidades funcionan con la extensa familia de módulos de utilidades de cambiador de herramientas de ATI.
Juntos, los acopladores y módulos de servicios también dan servicio a una variedad de protocolos de red, explicó Myers de KTH. “Cuando se trata del diseño de nuevos productos, puedo confiar en el equipo de ingeniería de ATI para diseñar rápidamente un producto eléctrico o neumático que se adapte a nuestras necesidades, o hacer referencia a uno de los miles de productos [disponibles] en su sitio web”. Para este sistema en particular en KTH, ATI configuró un acoplador de servicios públicos y un módulo eléctrico de E/S discreto de 32 pines que se integró fácilmente en las líneas existentes.
“Cuando comenzamos a probar el acoplador de servicios públicos, fue evidente de inmediato que iba a marcar una gran diferencia. Los nuevos acopladores son muy fiables y manos libres. No tenemos que meternos con ellos. Funcionan siempre”, dijo Strapp.
Cuando se le preguntó cómo KTH eligió a ATI como su proveedor, Myers respondió:"Basándonos en nuestra relación de servicio al cliente anterior, los tiempos de entrega rápidos y nuestro gerente de cuenta local, fue una decisión fácil optar por ATI". KTH es un usuario desde hace mucho tiempo de los productos de cambiador de herramientas robótico de ATI, por lo que la transición al acoplamiento automático con los acopladores de servicios públicos de ATI funcionó bien.
Dave Reed confirmó el rendimiento del acoplador de utilidad ATI GA2:"Cambié probablemente cientos de estas plantillas en el último año, y nunca tuve un problema con el sistema ATI. Configuras la plantilla allí, presionas el botón , se presiona, se aprieta, todas las clavijas están acopladas, no tiene tolerancia con las clavijas dobladas o las líneas de aire rotas. Es prácticamente un producto impecable. Hace la vida mucho más fácil".
Sistema de control de automatización
- Mejore el rendimiento con soldadura automatizada
- 4 formas de mejorar el rendimiento de la soldadura robótica
- Cómo la soldadura robótica está cambiando la fabricación pesada
- Soldadura robótica:prevención de causas comunes de tiempo de inactividad no programado
- Mantenimiento de soldadura robótica:aumento del ROI y reducción del tiempo de inactividad
- Producción automatizada de acoplamientos para perforadoras de petróleo
- Células robóticas que permiten el cuidado automatizado de piezas
- Las celdas estandarizadas FastArc facilitan el ingreso a la soldadura robótica
- Las celdas de soldadura robótica de servicio pesado pueden ser un excelente primer paso
- Soldadora por resistencia automatizada:una evolución
- Introducción a la soldadora por resistencia automatizada