Reinicio de la pared trasera:todo en uno, remolque para pegar a la pieza CFRP
Al comienzo del avance actual de los compuestos de fibra de carbono en las aplicaciones automotrices, el fabricante BMW Group (Múnich, Alemania) parecía diferenciarse. Trabajo inicial para acelerar el moldeo por transferencia de resina (RTM) para la producción de su M El techo del modelo deportivo llevó al establecimiento de una cadena de suministro completa para piezas de plástico reforzado con fibra de carbono (CFRP) en su i3 y i8 vehículos y luego a celdas de trabajo de fabricación y ensamblaje completamente nuevas para la carrocería en blanco (BIW) con núcleo de carbono multimaterial en su Serie 7 .
BMW apuesta por el i3 en 2009 con gran fanfarria, pero ese mismo año, Audi AG (Ingolstadt, Alemania) estableció un centro técnico dedicado a los plásticos reforzados con fibra. En 2011, Audi anunció una asociación con Voith Composites (Garching, Alemania) para desarrollar y producir piezas de CFRP en grandes cantidades. Al año siguiente, publicitó el desarrollo de un pilar B de acero reforzado con CFRP, fabricado con moldeo por transferencia de resina (RTM), y su asociación con SOGEFI (Guyancourt, Francia) para comercializar resortes de suspensión helicoidales compuestos. En 2012, Audi también se desempeñó como socio fundador del grupo de vanguardia MAI Carbon, que incluía a BMW, Voith Composites, SGL Group (Wiesbaden, Alemania) y otros.
En particular, la propia narrativa de Audi sobre el desarrollo de CFRP comienza con su R8 de primera generación. deportivo, lanzado en 2006. Presentaba cubiertas de compartimento para la capota convertible, así como laterales fabricados por moldeo por transferencia de resina (RTM). La compañía avanzó desde exteriores estéticos y estructuras más pequeñas hasta el Sistema Modular Sportscar (MSS) en el Audi R8 e-tron . Aunque la estructura principal de ese superdeportivo eléctrico constaba de vigas de aluminio extruido unidas por piezas de fundición de aluminio, todos los paneles y rellenos eran de CFRP, incluido un inserto de maletero con estructuras de choque corrugadas que permitían que el módulo trasero absorbiera cinco veces más energía que el marco de metal. .
La columna vertebral del MSS es su pared trasera , que evolucionó de un concepto inicial en 2011 al módulo que se produce actualmente para el R8 no eléctrico por SGL Technologies (anteriormente BENTELER-SGL, Ort im Innkreis, Austria; consulte “Visita a la planta:BENTELER SGL”). Pero Audi ya estaba planeando su siguiente paso:iterar la pared trasera para usarla en su A8 de mayor volumen. sedán de lujo, con Voith Composites como socio de fabricación.
Voith Composites es una filial de 10 años de la multinacional Voith GmbH &Co. KGaA, establecida en 1867. La empresa matriz ahora cuenta con 19.000 empleados, tiene ingresos anuales de 4.200 millones de euros (5.200 millones de dólares estadounidenses) y proporciona equipos y tecnologías de fabricación a través de cuatro divisiones:Voith Digital Solutions, Voith Hydro, Voith Paper y Voith Turbo. Voith Composites evolucionó desde la producción de rollos de CFRP utilizados en la fabricación de papel hasta la fabricación de ejes de transmisión / ejes cardán y laminados planos de CFRP automotriz e industrial.
En 2011, Voith Composites comenzó a trabajar en una cadena de procesos CFRP altamente automatizada, con el objetivo de producir el A8 pared posterior. En su núcleo estaba el aplicador móvil Voith (VRA), que, en una sola línea, esparce estopa de fibra de carbono de 35K de Zoltek (St. Louis, MO, EE. UU.) En cinta unidireccional (UD) ligada, que luego se corta y se apila en Forme un espacio en blanco a medida. La VRA fue reconocida con un premio a la innovación JEC en 2017. También estableció una base sólida para las operaciones posteriores de preformado y moldeado. Los máximos honores de la categoría de automóviles fueron capturados nuevamente para Voith Composites y Audi en JEC World 2018 por la línea de producción digital 4.0 completa basada en VRA utilizada para fabricar el Audi A8 módulo de pared trasera. Trabajando con el proveedor de resinas Dow Automotive (Auburn Hills, MI, EE. UU.) Y Zoltek, estos socios no solo desarrollaron los materiales, el proceso y los sistemas integrados de inspección en línea necesarios para fabricar piezas de CFRP de alto rendimiento a tasas de alto volumen, sino que también crearon el conjunto de herramientas de simulación y diseño asistido por computadora (CAD / CAM) esenciales que ya se están aplicando para desarrollar piezas futuras.
Evolución del diseño impulsada por la eficiencia
"Comenzamos a trabajar con Audi desde el principio", dice el Dr. Jaromir Ufer, director de desarrollo comercial de Voith Composites. La primera prioridad fue desarrollar el nuevo A8 diseño de la pared trasera, que indicaría cómo se debe fabricar la pieza.
“Cuando comenzamos la ingeniería para esta producción, no pudimos encontrar productos [de software] listos para usar que tuvieran todo lo que necesitábamos”, explica Ufer. "Así que reunimos herramientas de diseño como ABAQUS, pero construimos nuestras propias tarjetas de materiales y desarrollamos nuestros propios métodos de simulación". Audi ya había identificado la reducción del peso BIW y el aumento de la rigidez a la torsión como objetivos clave para el R8 diseño de la pared trasera (ver “Pared del asiento del Audi R8:un preludio de la producción”). Para el A8 módulo, se presentó un diseño integral para reducir el MSS multicomponente ensamblado a un solo panel de CFRP con forma con una pequeña cantidad de accesorios adheridos y remachados. Este diseño impulsó el desarrollo de un laminado altamente anisotrópico con trayectorias de carga localizadas, que permite que la pieza terminada proporcione el 33% de la rigidez torsional de la celda de transmisión al 50% del peso frente a un conjunto de tres a cinco piezas de aluminio soldadas.
“La preforma compuesta para el Audi A8 El panel de la pared trasera varía desde una base de 6 capas hasta 19 capas donde se agrega refuerzo local, por ejemplo, donde hay recortes o cargas puntuales, como los accesorios del sistema de retención infantil ”, explica Ufer (Fig 2).
Aplicador itinerante Voith
Ufer señala que el desarrollo de este diseño y el VRA procedieron en conjunto. “Solo teniendo la libertad de diseño que ofrece el VRA fue el rendimiento del nuevo A8 pared trasera posible ". También fue importante el hecho de que el proveedor de fibra Zoltek asumió un compromiso de precio de 7 años con el programa.
El proceso del VRA comienza con una fileta de fibra de carbono PX 35 de Zoltek. Se introducen varias bobinas de estopa de 50K en cada línea VRA y se extienden para producir cintas de 50 mm de ancho. A continuación, se aplica un aglutinante a base de epoxi que luego reaccionará con la resina de matriz epoxi de curado rápido Dow VORAFORCE durante el moldeo por transferencia de resina (RTM) de la pieza compuesta. Se aplica una pequeña cantidad de calor infrarrojo (IR) para derretir el aglutinante lo suficiente como para mantener la cinta unida a través de los pasos posteriores de consolidación, corte y apilado (Paso 1).
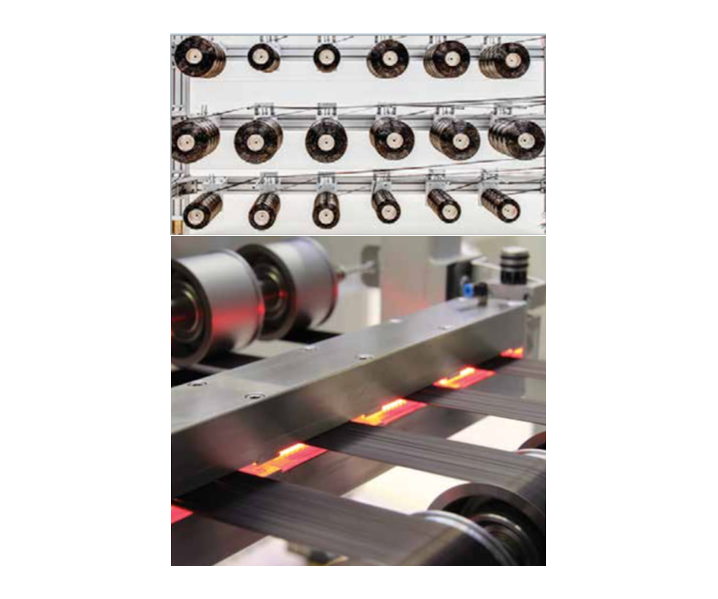
Paso 1: La estopa de fibra de carbono Zoltek 50K se introduce en el aplicador móvil Voith (VRA), donde primero se extiende, luego se recubre con un aglutinante a base de epoxi y luego se calienta por infrarrojos para derretir parcialmente el aglutinante.
“Este es un proceso continuo que está completamente automatizado”, dice Ufer. “Si por alguna razón es necesario detener la línea, el equipo reacciona automáticamente. Por ejemplo, el calentador de infrarrojos se apaga y se retrae inmediatamente para evitar dañar la cinta por sobrecalentamiento. Hay cientos de detalles de este tipo en el equipo y el control digital permite esta tecnología ".
Paso 2: Luego, la cinta de arrastre extendido se consolida a medida que avanza a través de múltiples rodillos bajo tensión.
Después de la aplicación del aglutinante, se logra la consolidación de la cinta a medida que pasa a través de múltiples rodillos bajo tensión (Paso 2). Ufer explica que esto también incorpora un búfer para la línea. "Tenemos una unidad que interrumpe el flujo de tracción continuo de la fibra, proporcionando una transición al formato de pulso del mecanismo de corte y colocación de cinta". Este mecanismo de pórtico corta las cintas en longitudes personalizadas y las coloca en ángulos especificados de 0 a 360 ° en una mesa giratoria (paso 3). Cada pila a medida, que comprende de 6 a 19 capas de cinta, tiene un grosor de 1,5 a 3,7 mm, respectivamente.
Paso 3: Luego, el VRA corta la cinta y coloca hasta cuatro piezas a la vez en una mesa giratoria, adaptando tanto la longitud de la cinta como el ángulo de orientación dentro de la pila de laminado (por ejemplo, 45 ° / 90 ° / 30 °).
Voith ha instalado cuatro líneas VRA (ver foto de apertura), y aunque cada una aplica hasta cuatro cintas de 50 mm de ancho a la vez, señala Ufer, “las líneas tienen un enfoque modular, por lo que podrían aplicar 10 o más cintas a la vez. hora. Depende del tamaño de la pieza y la tasa de producción ".
La automatización incluye la inspección de calidad. Los escaneos de cintas y preformas se comparan con un algoritmo de rechazo. “El escaneo del 100% de la cinta por parte de VRA garantiza la distribución correcta de la fibra para toda la línea de producción”, explica Ufer. "También utilizamos termografía y sensores láser para comprobar las preformas en las áreas designadas". Luego, el VRA puede reaccionar ante cualquier problema que detecte. "Si una cinta no es correcta", señala, "la VRA cortará la longitud deficiente y producirá otra para reemplazarla". Se coloca un código QR en la preforma terminada para su trazabilidad. (Se prefieren los códigos QR a las etiquetas de identificación por radiofrecuencia (RFID) porque, según se informa, resisten mejor el proceso de inyección de resina).
Conformado, moldeado y montaje
La pila 2D sale del VRA y se transporta a la sección de conformado, moldeado y ensamblaje de la línea de producción. La primera prensa en la que se coloca, suministrada por el especialista en automatización de compuestos FILL (Gurten, Austria), utiliza calor y presión para dar forma a la pila de cintas 2D en una preforma 3D (Paso 4). Ufer explica que debido a que la preforma varía en grosor y forma, la prensa puede adaptar la presión aplicada a medida que estampa-forma regiones separadas de la preforma sujeta en la herramienta de formación. ALPEX Technologies (Mils bei Hall, Austria) fabricó los moldes RTM de acero combinado, basándose en un diseño proporcionado por Voith Composites. “Desarrollamos el proceso de prensado y herramientas de forma virtual”, dice Ufer. “Aunque no se requirió un bucle de prueba real, validamos y verificamos los modelos de simulación en otras formas y piezas antes de mecanizar el A8 herramientas de producción de pared trasera. Esta simulación del proceso de moldeo funcionó directamente en la producción real y ayudó a acelerar la optimización ”.
Paso 4 :La pila de cinta se transporta a una prensa, donde se le da la forma final de la pieza 3D.
La prensa se mantiene durante unos segundos para reaccionar el aglutinante en polvo y establecer la forma, lo que da como resultado una preforma estable que puede resistir el lavado de fibras durante la inyección de resina. “Las partículas de aglutinante también funcionan para mantener las fibras separadas para mejorar el flujo de resina durante la RTM”, señala Ufer. "Esto es útil porque no hay costuras en la preforma para ayudar en el flujo de resina, por lo que estas partículas de aglutinante actúan como microcanales de flujo".
A continuación, la preforma moldeada se transfiere mediante un robot a una celda CNC de EiMa Maschinenbau GmbH (Frickenhausen, Alemania), donde un cuchillo ultrasónico recorta el contorno final exterior. Luego se coloca robóticamente en una prensa RTM (paso 5) suministrada por ENGEL (Schwertberg, Austria). Todos los robots de la línea son suministrados por KUKA Robotics (Augsburg, Alemania).
Paso 5: La preforma moldeada se coloca en una prensa de 350 kN y se moldea con ultra-RTM.
El proceso RTM utilizado para moldear el A8 La pared trasera es la misma desarrollada en el Audi Lightweight Center para el R8 anterior. pared trasera, conocida como ultra-RTM. Permite el moldeo de piezas grandes mediante inyección rápida pero a baja presión. En comparación con los 140 bares típicos de HP-RTM, la presión de inyección de resina en el molde durante el ultra-RTM del Audi A8 la pared trasera es <15 bar, incluso menos que la del R8 . Como resultado, en lugar de 2.500 kN de fuerza de prensado, solo se requieren 350 kN. Por lo tanto, se puede usar una prensa más pequeña y menos costosa para producir piezas de alta calidad y alto volumen de fibra.
La resina epoxi VORAFORCE 5300, un sistema de tres componentes que incluye desmoldeante, cura en 90-120 segundos a 120 ° C y tiene una viscosidad de procesamiento de 20 cps. Para el A8 En la pared posterior, se inyecta una granalla de resina de 1,3 kg en la preforma, seguida de un curado de 120 segundos.
La pieza curada se desmolda robóticamente y se carga en una celda de fresado CNC cerrada para el mecanizado de cortes. A continuación, la parte fresada se coloca en una lavadora automática para limpiar el polvo de CFRP residual.
La pared trasera lavada se transfiere a una celda de montaje equipada con dos robots. El primer robot coloca la pieza moldeada en una máquina remachadora automática, que documenta la fuerza aplicada durante la instalación del remache. Esto es parte de la inteligencia de fabricación integrada en el proceso general y se agrega al registro de procesamiento digital de cada pieza (es decir, hilo digital). Luego, la pieza se mueve al área de unión y un segundo robot prepara las áreas para la unión, utilizando una toallita con solvente automatizada. Luego, el mismo robot aplica el adhesivo estructural de poliuretano de dos componentes Dow BETAFORCE 9050M de curado rápido (paso 6), que es compatible con el epoxi de tres componentes. A continuación, la pieza se coloca en un horno para un breve ciclo de curado del adhesivo.
Paso 6: El adhesivo de poliuretano BETAFORCE se aplica de forma robótica para los accesorios adheridos y luego se cura en un ciclo de horno corto.
Esta línea de producción mantiene un tiempo de ciclo de 5 minutos para la pieza terminada y la demanda actual de piezas se puede satisfacer en uno o dos turnos de 8 horas. Periódicamente se utiliza un dispositivo de escaneo láser 3D para comprobar la forma y las medidas 3D de la pieza. Las piezas terminadas se preparan para su envío al Audi A8 línea de montaje final en Neckersalm, Alemania, a unas 3 horas por carretera (paso 7).
Paso 7: Luego, la pieza terminada se prepara para su envío a la línea de ensamblaje final del Audi A8.
Colocación directa de fibra =flexibilidad futura
Con toda la inversión que se ha realizado, es sorprendente saber que Voith Composites no tenía asegurado este negocio, pero de hecho la empresa completó el desarrollo y luego participó en un proceso de licitación competitivo para ganar producción. “Pudimos cumplir con el costo de pieza objetivo definido por Audi, así como con los requisitos de calidad y rendimiento de la pieza”, dice Ufer. Esto no fue poca cosa, considerando que bastantes empresas compitieron por el programa.
Voith Composites ha patentado varias partes de su proceso. “El VRA ha demostrado la industrialización mediante la colocación directa de fibras [DFP] de cintas, lo que reduce los desechos y el material utilizado a través de una capa altamente optimizada”, dice Ufer. También utiliza los materiales más rentables:fibra de arrastre pesado sin tratar y aglutinante en polvo. Su proceso de segunda generación reemplaza el aglutinante en polvo con la aplicación directa de resina, eliminando más pasos del proceso. Sin embargo, la empresa ha desarrollado otros procesos de DFP, incluidos Voith Longfiber Preformer y Voith Prepreg Winding.
"Estamos estableciendo nuevos estándares para las piezas de fibra de carbono para la producción en serie automotriz de gran volumen", dice el director general de Voith Composites, Dr. Lars Herbeck. “La fábrica inteligente que hemos establecido lleva la producción automatizada de componentes CFRP a un nuevo nivel de eficiencia y flexibilidad, que incluye casi cualquier forma y tamaños de lotes individuales”. Esto es, de hecho, hacia donde se dirige la industria.
Resina
- Por qué el material PEEK está en la cima de su clase
- Plástico reforzado con fibra de carbono (CFRP)
- K 2019:Los materiales importan en la Messe
- Arkema lanza el programa "Start-Up Connect"
- Polykemi invierte en su propia planta de compuestos de EE. UU.
- Polykemi tendrá producción de compuestos en tres continentes
- Cinta unidireccional termoplástica de fibra de carbono basada en PPS
- Desafíos del bobinado de cinta asistido por láser de compuestos termoplásticos
- Obra maestra con uso intensivo de compuestos:Corvette 2020, Parte 2
- La fibra de carbono de remolque dividido aumenta el rendimiento de SMC
- El módulo CFRP ahorra peso en el diseño de cohetes