HP-RTM para la producción en serie de aeroestructuras de CFRP rentables
Cuando el moldeo por transferencia de resina (RTM) comenzó a hacer la transición a RTM de alta presión (HP-RTM) hace aproximadamente una década, fue elogiado principalmente para aplicaciones automotrices, reduciendo los tiempos de ciclo de piezas compuestas de horas a menos de 2 minutos. Se ha dicho menos sobre la aplicación de esta tecnología a las piezas aeroespaciales. La industria aeronáutica tiene una larga historia con el RTM convencional, incluido su uso para producir miles de aspas de ventilador de plástico reforzado con fibra de carbono (CFRP) y cajas de contención para motores de aviones comerciales. Airbus incluso ha creado un prototipo de un flap multispar compuesto de una sola pieza de 7 metros de largo para el Airbus A320 utilizando RTM. Pero, ¿es posible hacer la transición de esta experiencia con procesos de horas de duración a un moldeado totalmente automatizado de piezas compuestas de aviones en minutos? Varios actores clave dicen que es posible.
El RTM tradicional, al que aquí se hace referencia como LP-RTM para mayor claridad, normalmente utiliza presiones de inyección de 10 a 20 bares. HP-RTM, por otro lado, utiliza presiones de inyección de 30-120 bares.
“Comenzamos a trabajar con el procesamiento aeroespacial RTM hace 10 años a través de un proyecto financiado con fondos europeos para fabricar marcos de fuselaje”, dice Bernhard Rittenschober, director de investigación y desarrollo de Alpex Technologies (Mils, Austria), un proveedor de sistemas de herramientas innovadores para compuestos en serie. producción de piezas. "En ese momento, las predicciones eran que muchas partes del [Airbus] A350 se harían con RTM, pero esto no se materializó". Sin embargo, Alpex siguió trabajando en la tecnología y, como proveedor de las industrias automotriz y aeroespacial, comenzó a analizar cómo se podrían fusionar los procesos utilizados en estas dos industrias. “La idea era utilizar la resina epoxi [Hexcel] RTM6 calificada en la industria aeroespacial, pero con las mejores prácticas de herramientas automotrices y un sistema de inyección automatizado para un menor tiempo de ciclo”, explica Rittenschober.
El resultado fue un programa de investigación de 2013-2015 llamado TAKE OFF, financiado por el gobierno austriaco, en el que Alpex participó con sus socios Airbus Helicopters (instalaciones de Donauworth, Alemania), el proveedor de equipos KraussMaffei (Múnich, Alemania), el especialista en pruebas aeroespaciales y compuestos avanzados. (AAC, Wiener Neustadt, Austria) y el proveedor de resinas Hexcel (Stamford, Connecticut, EE. UU.). El programa demostró que HP-RTM resultó en una reducción del 30 por ciento en el costo de un marco de puerta A350 y un desarrollo tecnológico significativo, incluido el uso de un sistema de resina de dos componentes (2K), monitoreo inteligente de inyección y curado a través de sensores en el molde y el capacidad para reducir aún más el tiempo de ciclo parcial. Alpex ha continuado su desarrollo y ve el potencial de esta tecnología HP-RTM para ayudar a superar los problemas actuales de producción de CFRP.
Apoyando este punto de vista, el Composites Technology Center (CTC), una subsidiaria de Airbus Operations GmbH, también ha estado desarrollando RTM automatizado durante una década, primero con LP-RTM y luego haciendo la transición a HP-RTM hace unos cinco años. ( CompositesWorld señaló la máquina KraussMaffei HP-RTM de CTC y el trabajo de desarrollo durante una visita a sus instalaciones en 2016). “HP-RTM resuelve el cuello de botella de la inyección y el curado debido a su mezcla de alta velocidad, que permite el uso de resinas altamente reactivas”, explica Jan Schiller. Líder de proyecto CTC para sistemas de producción y contacto líder para tecnologías RTM. "Hemos desarrollado un proceso que produce piezas geométricas algo complejas de 1 a 2 metros de tamaño, que cumplen con los requisitos aeroespaciales (por ejemplo, 60 por ciento de volumen de fibra y menos del 2 por ciento de huecos) en un ciclo de 20 minutos". Añade que después de las visitas y conversaciones con los proveedores de Airbus el año pasado, se identificaron varias piezas para la transición a HP-RTM, lo que permitió una mayor tasa de producción para el avión A320. "Ahora estamos desarrollando un procesamiento específico para estos y estamos trabajando este año para llevarlos a la producción en serie".
Marco de puerta HP-RTM A350
El desarrollo de Alpex se completó a través del programa austriaco TAKE OFF a través de un proyecto llamado SPARTA. "Airbus Helicopters eligió el papel", recuerda Rittenschober. “Este marco de puerta es lo que ves cuando entras en un A350 con la puerta abierta. Tiene aproximadamente 2 metros de alto, 200-250 milímetros de ancho y 8-10 milímetros de grosor, con una forma compleja y características de diseño para cumplir con los diversos requisitos de la puerta ensamblada, que es la estructura primaria ”. La puerta del A350 consta de 14 piezas fabricadas por Airbus Helicopters en Donauworth, Alemania, utilizando LP-RTM. El marco elegido para SPARTA es una de las partes más desafiantes de la puerta. “Es una buena parte de demostración porque podemos comparar HP-RTM directamente con LP-RTM aeroespacial estándar”, agrega Rittenschober.
Alpex diseñó y construyó las herramientas LP-RTM que se utilizan actualmente para la producción de marcos de puertas A350 en Airbus Helicopters. Para el diseño y la construcción de las herramientas HP-RTM, aplicaría una mentalidad más automotriz. “Nuestro objetivo era permitir la automatización de tipo automotriz en la producción de piezas compuestas aeroespaciales”, dice Rittenschober. "Esto es necesario si Airbus va a construir un futuro A320 con más piezas compuestas y a un ritmo de 60 a 100 aviones por mes".
Continúa:“Veníamos de producir moldes para BMW, que estaba tratando activamente de simplificar sus piezas y procesos para reducir el tiempo de ciclo, mientras que Airbus provenía de la complejidad aeroespacial anterior. Por ejemplo, cuando comenzamos, Airbus Helicopters preguntó cuántas piezas tendría este molde ”. Tenga en cuenta que la producción actual de puertas LP-RTM incluía complejas herramientas de varias piezas. “Explicamos que la herramienta HP-RTM solo tendrá un molde superior y otro inferior”, dice Rittenschober.
Por lo tanto, Alpex comenzó con un diseño de molde simple y luego agregó características para hacer que el procesamiento sea más robusto y flexible, por ejemplo, los sistemas de sellado utilizados para la producción automotriz de alto volumen. “Además, tenemos todos los sensores integrados en el molde”, señala.
Preformas y proceso
Las preformas que se utilizan actualmente para el marco de la puerta A350 utilizan material tejido y requieren varios pasos de reducción de volumen, lo que da como resultado un ciclo de producción de tres días. “En su lugar, decidimos utilizar tela sin ondulación (NCF)”, dice Rittenschober. “Esto reduce significativamente el precio y el tiempo de ciclo. También terminamos demostrando algunas piezas con las preformas tejidas calificadas por Hexcel, pero vemos un cambio en la industria de los compuestos fuera del aeroespacial, con el desarrollo por parte de SGL y otros de las telas tejidas hacia cintas y formas de menor costo como los NCF ”.
Cuando se le preguntó sobre los puntos de inyección y cualquier problema con el lavado de fibras, Rittenschober explica que la herramienta HP-RTM tiene un solo punto de inyección, pero no hay lavado de fibras porque la preforma está sujeta para que quede fija en el molde y sea muy estable.
Otro punto clave es que Alpex eligió utilizar un sistema de resina de dos componentes (2K) en lugar del RTM6 de un componente que utiliza actualmente Airbus Helicopters. Rittenschober afirma que el sistema 2K puede ser más reactivo, lo que se adapta mejor a HP-RTM y puede ahorrar costos porque no está premezclado y no requiere el envío de materiales peligrosos. Sin embargo, requiere una temperatura más alta de 180 ° C. "Esta fue la parte más desafiante para nosotros", dice Rittenschober, "porque estábamos más acostumbrados a procesar a 120 ° C".
KraussMaffei instaló, en su centro de tecnología liviana en Munich, Alemania, las herramientas terminadas en su sistema RimStar Compact HP-RTM con mezcla, medidor e inyección automatizados de alta presión (hasta 80 bar / 1100 psi). Luego fabricó 20 piezas de demostración. Rittenschober describe el proceso de referencia:inyectar a 80 ° C, aumentar a 120 ° C, mantener durante una hora, aumentar a 180 ° y mantener durante 90 minutos, disminuir (2 ° C / min) y desmoldar. "La inyección solo toma 20 segundos", dice, "pero el ciclo total de moldeo es de aproximadamente cuatro horas".
Duración y coste del ciclo
El ciclo de curado aún largo para el marco de la puerta SPARTA está impulsado por la formulación y el procesamiento de resina Hexcel RTM6 que está calificado por Airbus. "Pudimos lograr ciclos de curado de 30 minutos a 180 ° C con un poscurado adicional al vacío después para eliminar el estrés térmico y asegurar las propiedades mecánicas", señala Rittenschober, y agrega que las propiedades eran bastante buenas y comparables a las del LP -RTM parte.
“Demostramos que se puede utilizar el proceso y automatizar la producción para volúmenes de piezas más altos”, dice Rittenschober. "Puede inyectar y curar en el molde y luego postcurar fuera de la prensa". Admite que esto requiere juegos adicionales de herramientas, pero solo una sola unidad de inyección y prensa. “Con este sistema, puede reducir el costo de la pieza en 700 €, lo que le permite pagar el equipo fácilmente con una tasa de producción de 500 a 1,000 piezas / año, que ni siquiera es un volumen muy alto”.
Demostradores y desarrollo de procesos CTC
Dejando a un lado las herramientas y el proceso, el proyecto de la puerta HP-RTM también incluyó el uso innovador del formato de fibra. “Comenzamos con textiles tejidos ya calificados por Airbus y tuvimos mucho éxito”, recuerda Schiller. "Luego continuamos con NCF y textiles más innovadores". Este último incluía la colocación de fibras secas y el intercalado con capas de estopa extendidas para aumentar la tenacidad, pero el último presentaba problemas con el empaquetamiento apretado de fibras y capas, lo que provocaba una mala permeabilidad y dificultaba la infiltración de resina. “También hay desarrollos para abordar esto, como NCF con fibras especiales para mejorar la permeabilidad”, agrega.
Con respecto a las presiones para HP-RTM, Schiller enfatiza que la decisión de utilizar el proceso fue impulsada más por la tecnología de mezcla de la industria del poliuretano que por las altas presiones del proceso. “Utilizamos HP-RTM solo para obtener una buena mezcla de resinas altamente reactivas”, explica. “Puede haber algo de presión más alta en el molde, pero esto es un efecto secundario de la inyección rápida. Para las piezas de automóviles con tiempos de ciclo de 2 minutos, deben infiltrar la preforma seca con resina mucho más rápido que nosotros. Nuestro tiempo de curado de 15 minutos permite más tiempo para la infiltración de resina, lo que también reduce la presión en el molde ”.
Mientras tanto, el tonelaje de la prensa depende del tamaño de la pieza. “Fabricar piezas de hasta 2 metros de tamaño funciona bien (alrededor de 1.500 toneladas), pero las piezas de 4 a 6 metros requieren calcular el caso comercial porque la inversión en la prensa es muy alta”, dice Schiller. CTC mostró una nervadura de CFRP de 1,5 metros por 0,5 metros que representa cualquier posible estructura primaria aeroespacial en JEC World en 2018. También recibirá una prensa de mayor tonelaje a fines de 2019.
Resinas 2K y control de calidad basado en sensores
Schiller observa que todas las estructuras de aviones RTM anteriores solo han utilizado sistemas 1K mezclados por el proveedor, quien luego certifica la mezcla y asume la responsabilidad de asegurarse de que la resina cumpla con los requisitos de calificación. “Ahora estamos considerando sistemas 2K, pero el desafío es garantizar la calidad de la mezcla”, explica. Los sistemas 1K premezclados requieren envío y almacenamiento en frío para evitar reacciones hasta el procesamiento de la pieza. Por lo tanto, las ventajas de los sistemas 2K incluyen la eliminación de este gasto, así como una mayor reactividad para un procesamiento más rápido. Sin embargo, un problema es que la garantía de calidad (QA) se transferirá del proveedor de resina al fabricante de las piezas. "Este control de calidad requiere la detección de la proporción de mezcla y la calidad de la resina mezclada. Ambos son necesarios para la calificación de Airbus de un nuevo material. Entonces, esto significa mediciones de los dos componentes justo antes de mezclar y de la resina después de mezclar. Hoy en día, solo tenemos sensores antes del cabezal de mezcla, que muestran cuánta resina y cuánto endurecedor se dosificaron en la mezcla. Esto no es suficiente para calificar ”.
Mientras tanto, Alpex está trabajando para desarrollar un sistema de calidad en línea que proporcione la verificación del 100% de resina correctamente mezclada que requiere Airbus. “Hemos trabajado con sensores en molde Netzsch desde el comienzo de este desarrollo”, señala Rittenschober. “Ahora que Netzsch está asociado con Kistler (Winterthur, Suiza), hay nueva tecnología disponible. Podemos controlar la temperatura, la presión y el curado de la resina desde un solo sensor, que incluimos en el molde ”.
“Alpex dice que use sensores en el molde, y los proveedores de equipos de mezcla / inyección dicen que los sensores deben estar en su sistemas ”, dice Schiller. "Ambos tienen razón". Pero señala que también es necesario mejorar en este último. “En HP-RTM automotriz, la proporción de mezcla de resina se mide durante todo el proceso, por lo que es un promedio”, explica Schiller. “Sin embargo, necesito esta medición en cada punto discreto durante el proceso, para saber que la proporción de mezcla siempre es correcta, incluso durante la última mitad de un segundo durante la inyección. Necesitamos una mejor resolución de tiempo en los sistemas de medición ”. Schiller sugiere que probablemente se necesitarán sensores antes del cabezal de mezcla, dentro del cabezal de mezcla y en el molde. “Estamos trabajando en este desarrollo de control de calidad en paralelo a la evaluación de resinas 2K en aplicaciones aeroespaciales y, junto con los proveedores de máquinas, hemos identificado sistemas de sensores que prometen una resolución suficiente. Serán validados dentro de este año ”.
Alpex también está probando un nuevo sensor piezoeléctrico multifuncional híbrido desarrollado por Aerospace &Advanced Composites (AAC, Wiener Neustadt, Austria). Colocado en el molde RTM, actúa como un sensor de presión para monitorear el frente de flujo de resina en el molde. Una vez que la resina impregna la preforma y comienza el curado, el sensor utiliza el cambio en el espectro de impedancia para determinar el grado de curado. Una vez que se completa el curado, los sensores piezoeléctricos se curan conjuntamente en la superficie de la pieza que se usará para el monitoreo de la salud estructural, ya sea en modo pasivo como sensores de emisión acústica o en modo activo usando ondas ultrasónicas guiadas. Se han demostrado para el seguimiento de impactos y daños en piezas acabadas.
Tenga en cuenta que estos datos de proceso pueden ser analizados por sistemas de producción inteligentes de Industria 4.0 para identificar rutas para mejoras adicionales en calidad y eficiencia. Estos datos de proceso también se pueden registrar para el gemelo digital de cada pieza.
Potencial futuro
Rittenschober dice que el único obstáculo real para la tecnología HP-RTM es la certificación:"Estamos demostrando con Airbus Helicopters que este proceso puede funcionar, pero alguien tiene que certificarlo". Schiller está de acuerdo en que siempre es un obstáculo encontrar quién será el primero, pero también ha calculado casos comerciales para muchas partes durante el último año. “Por 200 piezas por año, no tiene sentido. Sin embargo, para las piezas del A320, por ejemplo, resulta atractivo. Cada mes, vemos una tasa objetivo más alta para el programa A320. Muchas de estas piezas se diseñaron en la década de 1980 y se producen manualmente, por lo que fácilmente podrían hacerse mucho más eficientes con HP-RTM ”.
Con tiempos de ciclo parcial de 20 minutos demostrados por CTC, HP-RTM también podría ser atractivo para el mercado de aviones de despegue y aterrizaje verticales eléctricos (eVTOL), donde los volúmenes de producción de 5.000 aviones por año han sido sugeridos como límite superior por el fabricante de taxis aéreos. UBER.
Alpex continuará desarrollando una gama de avances de RTM, dice Rittenschober. "Creemos que HP-RTM tiene un potencial real para ayudar a resolver algunos de los problemas con una producción industrializada más rentable de aeroestructuras de CFRP". Schiller está de acuerdo y señala que para muchas de las aplicaciones específicas del A320, hay numerosas piezas de CFRP por conjunto de envío. “Así, el beneficio de un proceso más eficiente comienza a acumularse. Si podemos obtener la primera aplicación en producción, habrá otras ”.
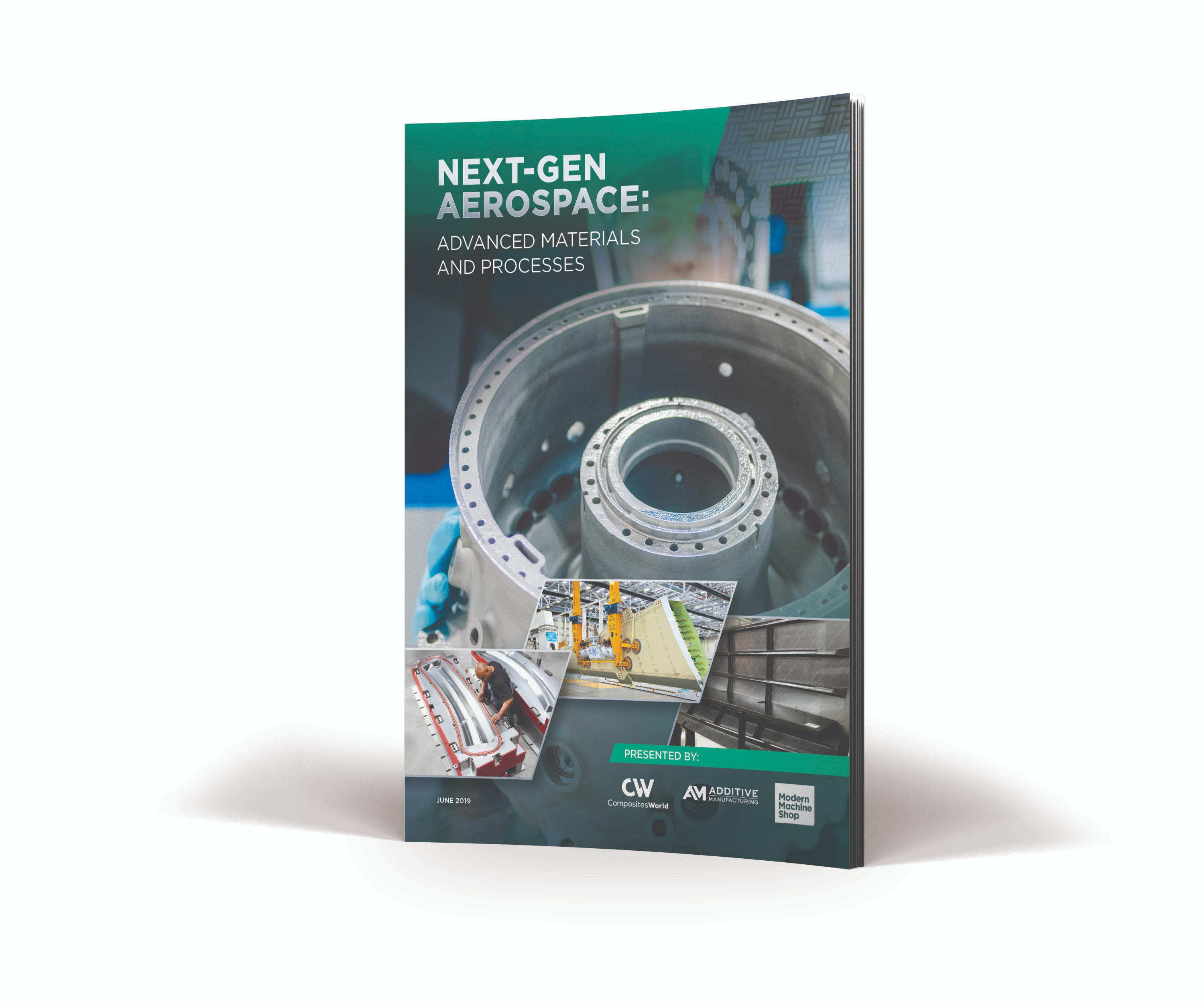
La próxima generación de
Fabricación aeroespacial
Con la proyección de que la industria de la aviación comercial se duplicará en los próximos 20 años, satisfacer la demanda de aviones de pasajeros y de carga requerirá nuevas tecnologías y tasas de fabricación sin precedentes.
Obtenga más información sobre los materiales y procesos que darán forma a los aviones de próxima generación en una colección de historias de CompositesWorld, Modern Machine Shop y Fabricación aditiva , disponible para leer o descargar gratis . Consíguelo aquí.
Resina
- Aditivos:colorantes rentables para aplicaciones de alambres y cables
- Compuestos de purga para la producción de empaques de poliolefina de pared delgada
- Fraunhofer encarga células de producción automatizadas de Engel para I + D de compuestos termoplásticos
- Diseño para la fabricación automatizada de composites de aeroestructuras de bajo volumen
- Las cintas termoplásticas continúan mostrando potencial para aeroestructuras compuestas
- Combinación de AFP con impresión 3D para una producción de piezas flexible
- Karl Mayer lanza la línea de producción de cintas termoplásticas UD
- Fusión por chorro de agua, láser para mayor eficiencia en el mecanizado CFRP / CMC
- Broetje-Automation amplía la cartera de AFP para la producción de compuestos en serie
- INEOS Styrolution para construir un sitio de producción para el compuesto termoplástico StyLight
- Prácticas de trazabilidad para la producción de fundición