Visita a la planta:Holland Composites, Lelystad, Países Bajos
Catamaranes de foiling, fachadas de edificios y más. Situado a menos de una hora en coche de Ámsterdam, Holland Composites persigue una amplia variedad de proyectos altamente técnicos en sus 4.500 m 2 instalaciones. Fuente, todas las imágenes | Holland Composites
Holland Composites (Lelystad, Países Bajos), ubicado en un edificio de 4.500 metros cuadrados, a menos de una hora en coche de Ámsterdam, se centra en cuatro mercados:marino / offshore, arquitectura, energías renovables y proyectos especiales. Holland Composites utiliza una mezcla de polímero reforzado con fibra de carbono preimpregnado (CFRP) y nido de abeja Nomex para piezas muy cargadas, e infusión de resina y fibra de vidrio para la industria de la construcción y proyectos de menor margen. "Aún podemos lograr un alto rendimiento incluso con estas construcciones más rentables, y mantenemos bajos gastos generales para las piezas que utilizan materiales avanzados", dice Sven Erik Janssen, socio co-director de Holland Composites, junto con el fundador Pieterjan. Dwarshuis. "Esto es único".
La compañía también opera la marca DNA Performance Sailing, produciendo veleros multicasco con foil, incluido el catamarán F1X de 5,5 metros, el trimarán TF10 de 11 metros y el catamarán F4 de 14 metros. El catamarán G4 de 12 metros ya no está en producción, "pero muestra nuestras capacidades para la construcción avanzada de yates compuestos y alto rendimiento", señala Janssen. “Este barco es un barco de regata con foiling de doble propósito y un crucero familiar con literas, cocina y cabecera, pero alcanza una velocidad de más de 35 nudos. La capacidad de navegar con más de 4.000 kilogramos de peso y solo una tripulación de seis personas:todavía no hay competencia en este campo a excepción de los yates multimillonarios de la Copa América ".
Transporte marítimo a terrestre y aéreo
Antes de que comience el recorrido, Janssen relata la historia de la empresa y las estructuras compuestas que produce. Holland Composites se formó en 1992 por Janssen y Dwarshuis, que en ese momento eran estudiantes de la Universidad Técnica de Delft (TU Delft, Países Bajos). Construyeron mástiles de fibra de carbono para los catamaranes de vela Hobie, un barco auxiliar de 18 metros con CFRP y nido de abeja Nomex en 1993, y un yate de vela de 100 pies con procesamiento de infusión de resina en 1994. “En ese momento, todo lo que estábamos construyendo estaba hecho de fibra de carbono mediante preimpregnación o infusión ”, recuerda Janssen. Sin embargo, agrega, debido a que el negocio estaba sujeto a los típicos altibajos del mercado marino y proyectos puntuales, “Buscábamos diversificarnos, pero queríamos mantenernos en compuestos avanzados frente a FRP [es decir, fibra de vidrio menos avanzada y más básica y resina de poliéster]. ”
La compañía comenzó a explorar soluciones livianas para el transporte por carretera, produciendo 35 remolques de camión con un chasis monocasco compuesto de fibra de vidrio / carbono, que redujo el peso en 3.500 kilogramos. “Los camiones transportaban cargas densas, como patatas, y su peso era máximo antes de llenar su volumen”, explica Janssen. Holland Composites también fabricó remolques refrigerados, agrega, “Pero llegamos demasiado pronto; el mercado aún no estaba listo:las empresas aún no podían calcular las ganancias anuales derivadas del transporte de más carga y los ahorros de mantenimiento de los remolques compuestos frente a su mayor costo inicial ”.
Casi al mismo tiempo, VRR (Rotterdam, Países Bajos), un proveedor de soluciones personalizadas de carga aérea, se acercó a la empresa. “Estaban trabajando para Airbus, Boeing y las aerolíneas”, recuerda Janssen. “Desarrollamos un contenedor de peso pluma con un monocasco compuesto de fibra de carbono / aramida, que todavía no tiene un peso reducido en la actualidad”, dice. Aunque Holland Composites fabricó algunos miles de estos, el mercado se saturó rápidamente con productos FRP de bajo costo.
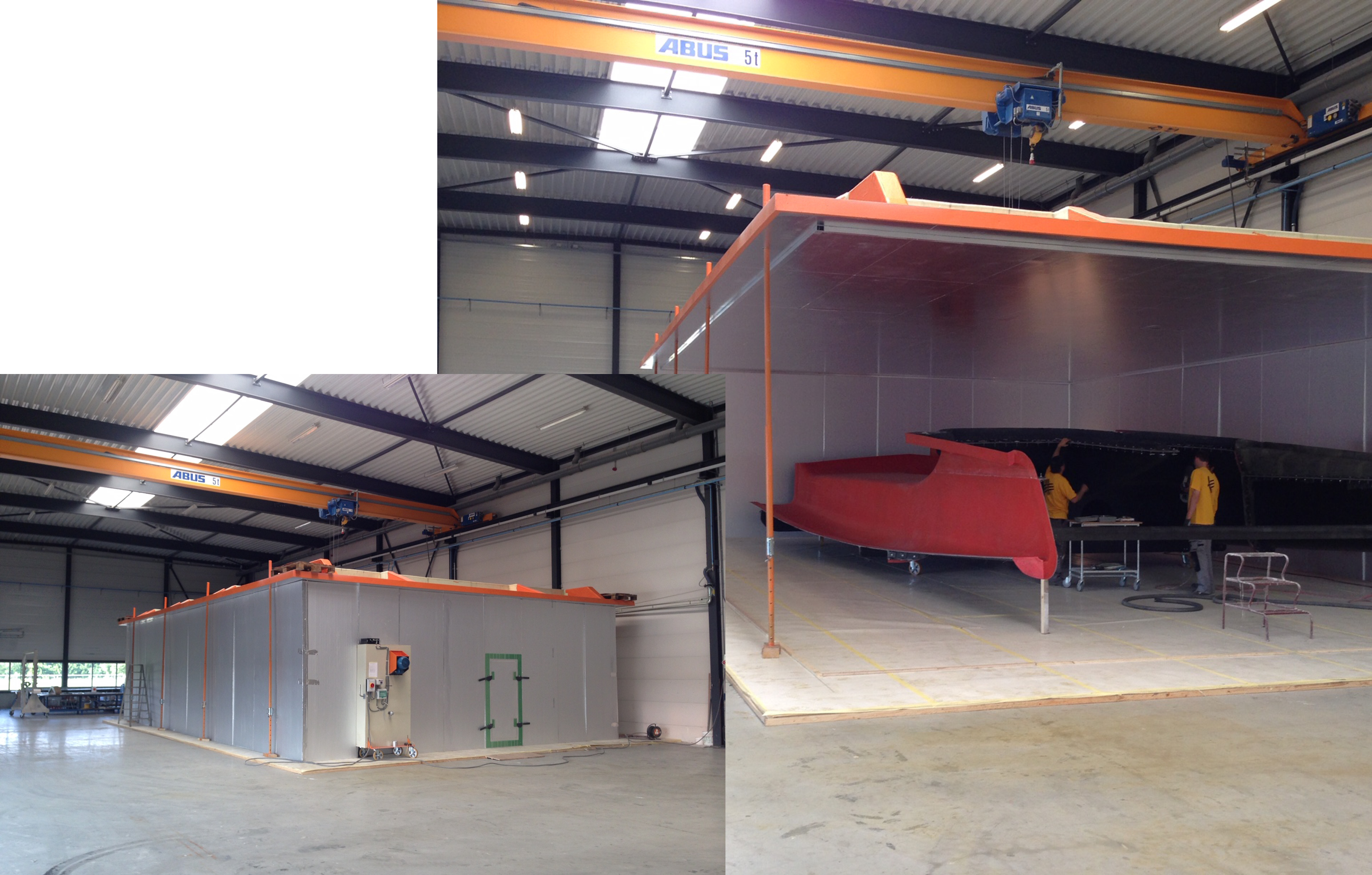
Estructuras curadas con OOA. Las grandes estructuras de compuestos de carbono para su marca DNA Performance Sailing de veleros multicasco con foiling se curan en hornos flexibles (derecha) que comprenden paneles aislados con calefacción y circulación de aire controlados por computadora desde una unidad exterior (recuadro).
La marina sigue siendo una de las fortalezas principales
En 1999, la Armada holandesa se acercó a Holland Composites para producir domos de sonar compuestos de fibra de vidrio sólida para submarinos. “Estos se construían tradicionalmente en dos mitades que estaban unidas entre sí”, dice Janssen, “pero la unión causa una interrupción en el campo de 'visión'. Se nos pidió que los construyéramos en una sola pieza. Estos domos de sonar son grandes (11,5 por 3 por 3 metros y de 45 a 110 milímetros de espesor) y difíciles de infundir, y comprenden 5.000 kilogramos de resina híbrida de éster vinílico / epoxi suministrada por Romar-Voss Composites (Roggel, Países Bajos). La estructura terminada pesa 6.500 kilogramos. Deben ser rígidos y resistir golpes de carga porque están ubicados en la sección delantera del casco. “También tenemos que igualar la densidad y la transparencia del sonar del agua”, dice Janssen. "Hacemos esto para los buques de tipo destructor para bastantes fuerzas navales en todo el mundo".
En el otro extremo del espectro de peso se encuentran los multicascos que frustran el desempeño del ADN. “Nuestros botes pequeños fueron los primeros catamaranes con foiling en competencia”, dice Janssen. Holland Composites también produce hidroalas compuestas para yates de carreras que establecen récords como el Team ARGO de MOD70 y Beau Geste . "Tenemos una técnica interna que puede crear piezas realmente muy cargadas sin fallas, y un método de producción único de una sola vez para estas láminas de muy alto rendimiento", agrega. "Trabajamos con los mejores navegantes del mundo para alcanzar el siguiente nivel de rendimiento de foil y producir todos los foils para los barcos de la clase olímpica NACMA17".
La caseta liviana de CFRP que Holland Composites produce para las embarcaciones de servicio / soporte de parques eólicos Windcat Workboats (ver "Casetas de cubierta compuestas reducen el peso") utiliza una construcción de sándwich de espuma CFRP infundida con resina para brindar rigidez y lograr un tramo grande y abierto sin pilares dentro de la cabina. “La caseta de cubierta monocasco es lo suficientemente liviana como para poder colocarla en buenos amortiguadores para aislarla del motor y las vibraciones de las olas en el casco”, dice Janssen. “Windcat es conocido por su paseo realmente silencioso, y los barcos son muy apreciados por los fabricantes de equipos originales de grandes turbinas eólicas. Todos estos parques eólicos deben recibir mantenimiento, por lo que hay un nuevo mercado para catamaranes de alta velocidad de 50 a 60 pies de largo ”.

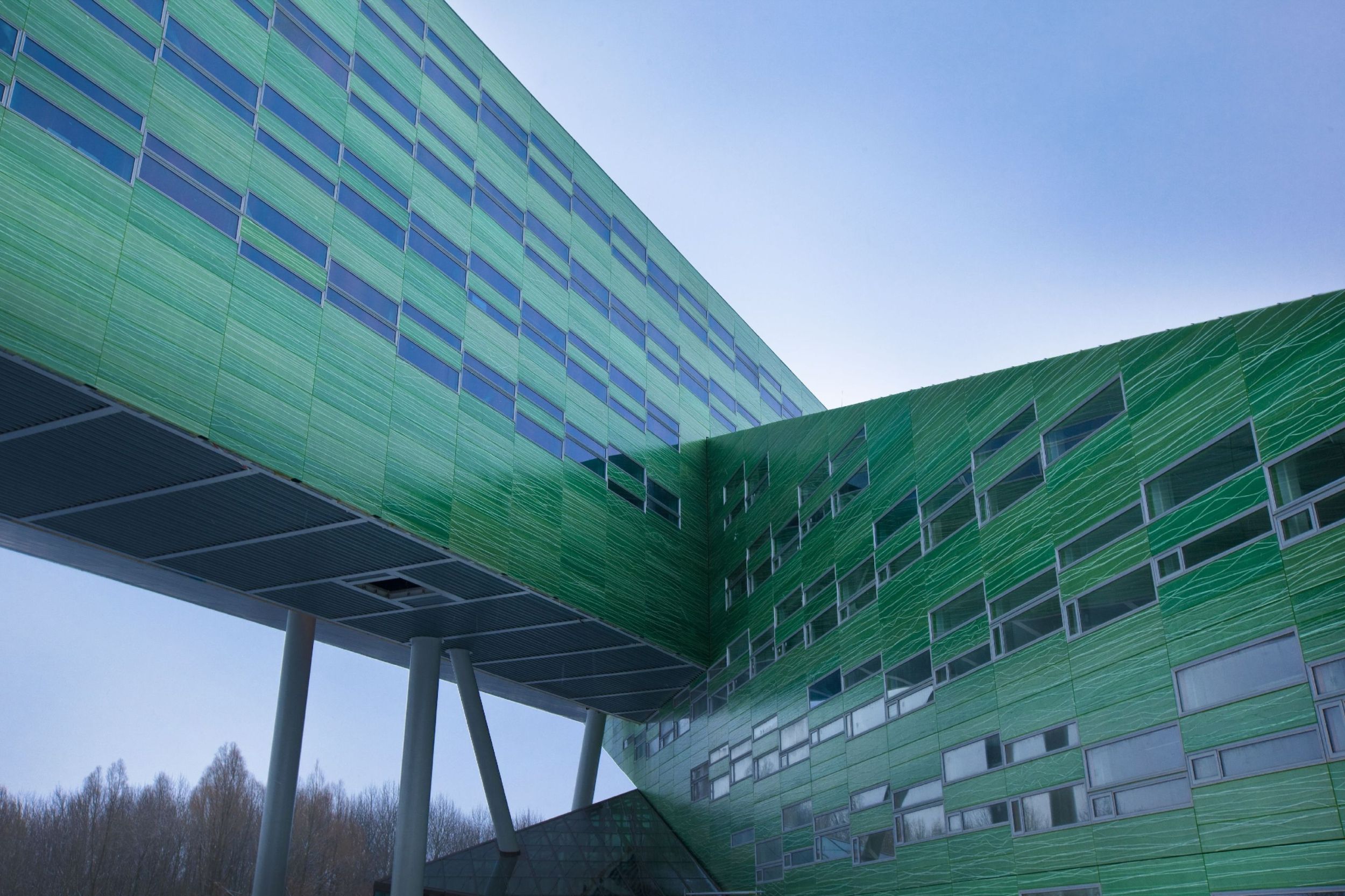
Holland Composites suministró la fachada compuesta estructural para la Universidad de Groningen Life Edificio de Ciencias, utilizando su sistema de paneles translúcidos RAFICLAD y paneles de gran tamaño (3,6 por 3,3 metros), logrando ahorro de peso y máximo aislamiento térmico.
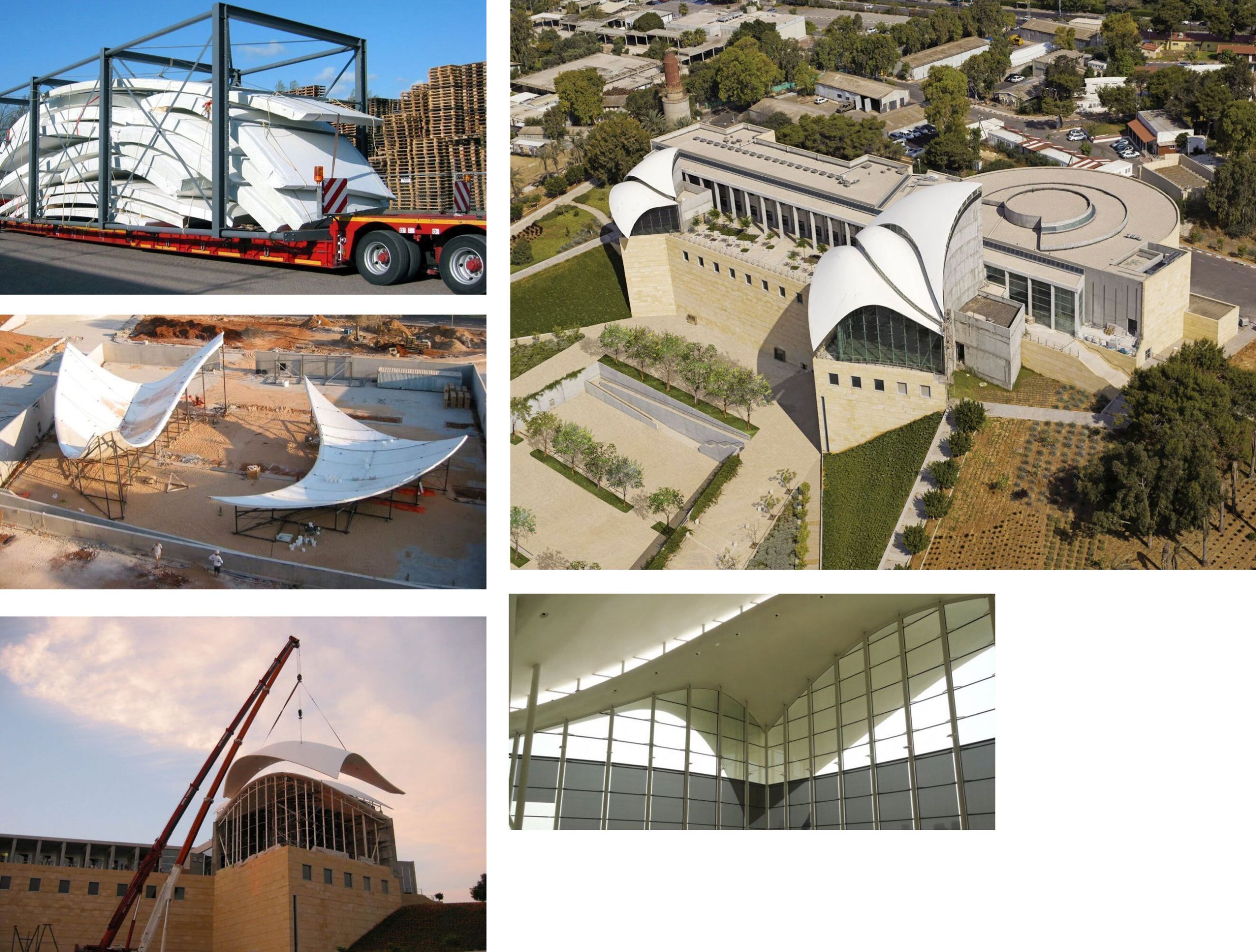
Se enviaron setenta y cinco secciones compuestas de 40 por 60 metros a Israel, se laminaron juntas y se colocaron en su lugar para crear las secciones del techo en forma de ala para el Centro Yitzak Rabin en Tel Aviv.
"Todo lo que hacemos es estructural"
Para el Centro Yitzak Rabin (Tel Aviv, Israel), se pidió a la empresa que construyera estructuras de techo en forma de ala que serían demasiado pesadas si estuvieran hechas de hormigón. “Nuevamente, hicimos las secciones más grandes posibles”, dice Janssen. Se infundieron resina setenta y cinco secciones de 40 por 60 metros utilizando fibra de vidrio y resina de éster de vinilo a base de epoxi, y luego se enviaron a Israel. En el sitio, estos se colocaron boca abajo en plantillas para laminarlos juntos en "techos de alas" con una luz máxima de 31 metros. Janssen señala que el proyecto fue muy desafiante estructuralmente. “Estos paneles tienen un espesor de 200 a 300 milímetros y mantienen unida la fachada de vidrio, incluida una sección en voladizo de 11 metros. El material compuesto puede resistir todas las fuerzas, lo que le brinda la posibilidad de diseñar tales tramos de techo que cuelgan libremente ”.
La torre del Hotel Fletcher es otro proyecto de este tipo, completado en 2012-2013. Comenzó como un centro comercial al lado de una carretera, pero requirió una atenuación acústica sustancial en la estructura después de que se tomó la decisión de convertir el edificio en un hotel de alta gama. “El esqueleto de hormigón no podía soportar mucha carga adicional, por lo que nos llamaron para proporcionar una solución liviana”, dice Janssen. Holland Composites diseñó paneles compuestos de 8,5 por 3 metros a los que se podía sujetar la fachada de placas de vidrio. “El vidrio en realidad cuelga de nuestros paneles, lo que ayuda a manejar la carga”, señala. “Luego sujetamos nuestros paneles al esqueleto de hormigón. Esta combinación del vidrio frente a los paneles sándwich compuestos con el espacio de aire entre ellos crea una enorme barrera acústica ". Cada panel compuesto estaba listo para pintar para paredes interiores en un lado y se terminó con revestimientos resistentes a los rayos UV en el lado exterior que mira hacia el vidrio.
“Esta fue también una forma muy rápida de montar un revestimiento en un edificio de forma redonda”, dice Janssen. “Montamos la fachada completa en un solo paso y logramos un valor R de aislamiento de 8, que es el doble de la calificación de los materiales exteriores de construcción normales ". Ampliando esta idea, Janssen dice que cree que la neutralidad energética es fundamental para la construcción de edificios en el futuro. “No se necesita mucha energía para calentar los edificios que usan nuestro revestimiento compuesto estructural, por lo que nuestro enfoque es muy eficiente para lograr una huella neta cero. BREEAM es la certificación holandesa de eficiencia energética, y los dos primeros edificios que lo lograron utilizan nuestros compuestos ”.
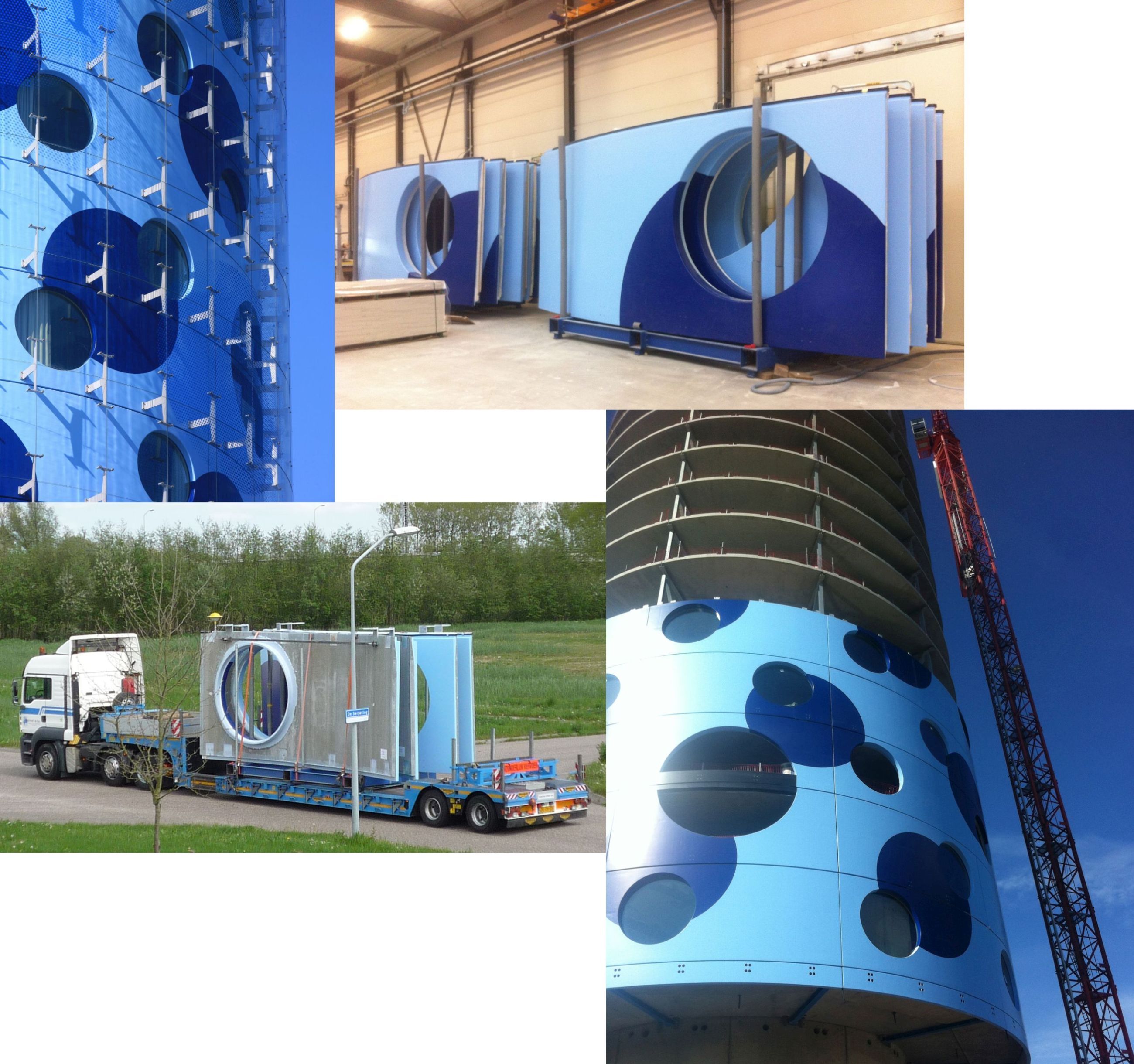
Para el hotel Fletcher, Holland Composites realizó un exterior estético que reducía el ruido al colocar paneles compuestos curvos en el esqueleto de hormigón del edificio, al que se podía sujetar la fachada de vidrio sin agregar una carga muerta excesiva.
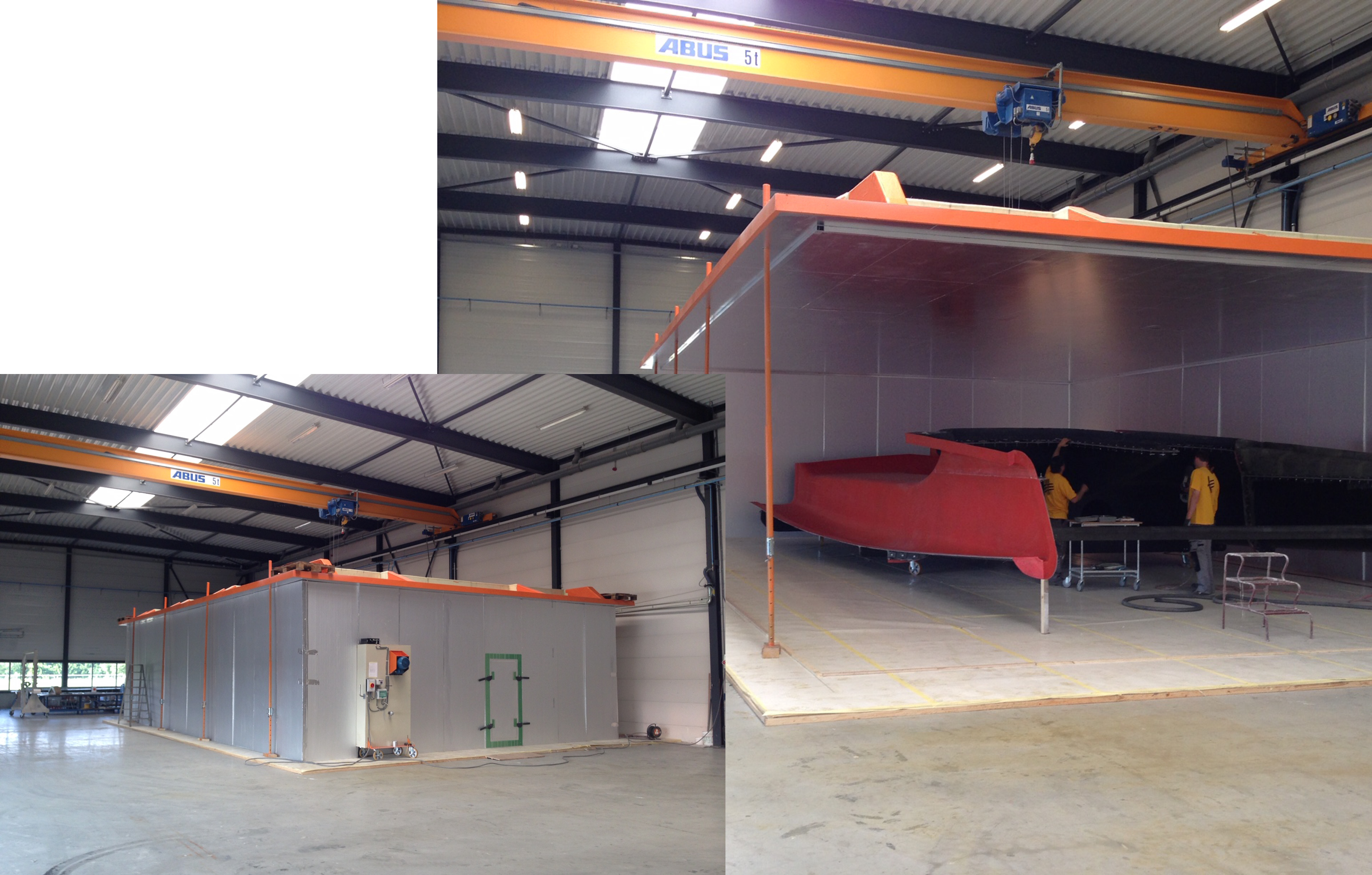
Janssen destaca el Museo Stedelijk de arte contemporáneo en el centro de Ámsterdam como el pináculo de los proyectos de construcción técnica de Holland Composites (ver "Gran museo, grandes estructuras"). "Fue un ejercicio extremo en la gestión de la expansión térmica e ilustra lo que hacemos". Holland Composites también ha sido pionero en fachadas estructurales a prueba de terremotos, que ahora se requieren en ciertas partes de los Países Bajos, explica Janssen, porque el suelo se ha desestabilizado debido a la fracturación hidráulica (fracking). El edificio Wiebenga en Groningen cuenta con una fachada a prueba de terremotos que puede moverse 30 centímetros sin fallar. "El acero y el hormigón típicos no pueden soportar este tipo de movimiento", añade.
Aunque equilibrar la miríada de requisitos con el costo y el cronograma es un desafío cuando se construyen estructuras, Janssen señala que el problema más grande actualmente es la resistencia al fuego. “Las implementaciones incorrectas de los compuestos han hecho que la industria de los compuestos tenga una mala reputación en ese sentido ”, explica. "Ahora usamos solo materiales resistentes al fuego en estos proyectos de construcción y completamos las pruebas de fuego según las regulaciones aprobadas".
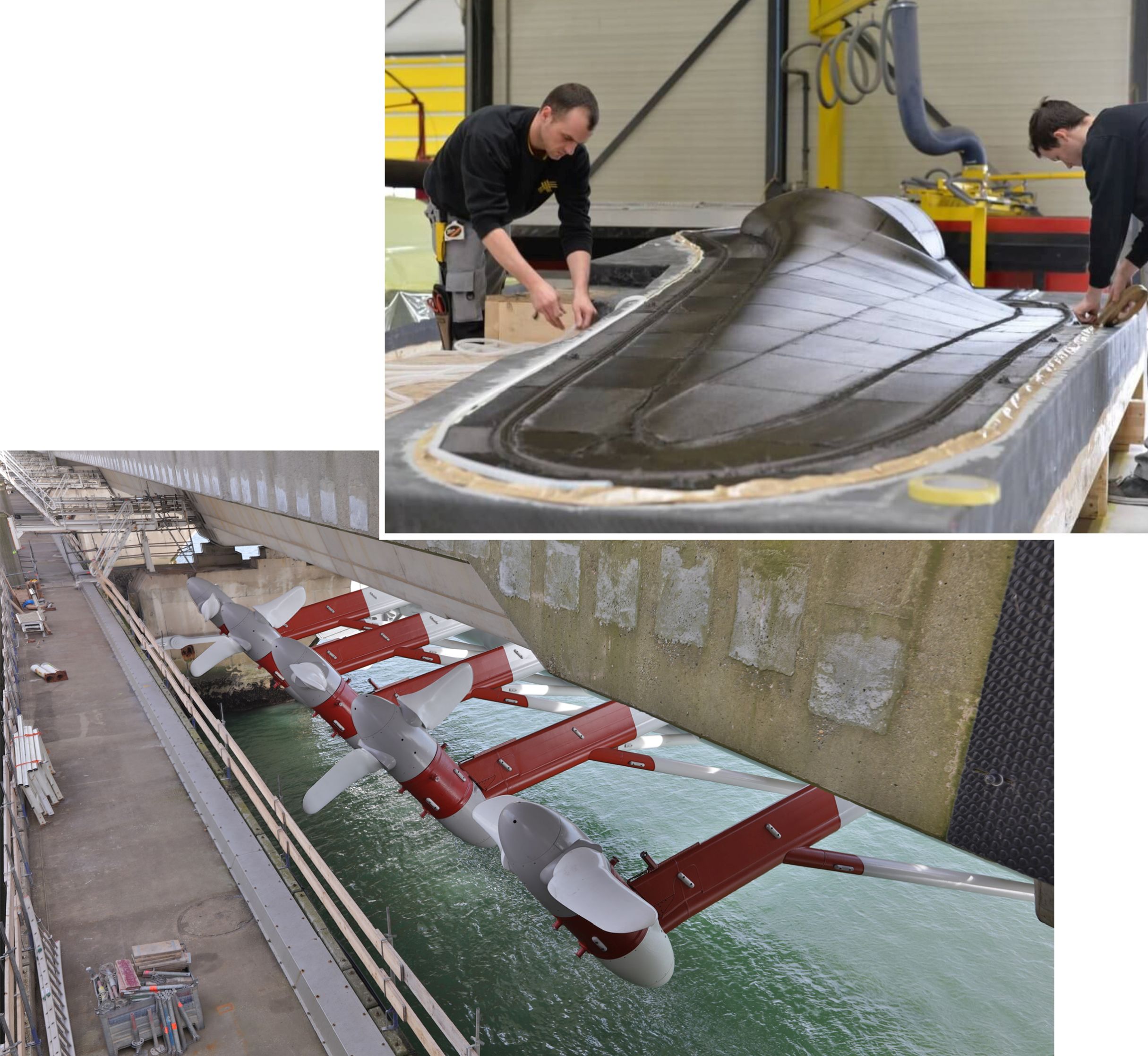
Holland Composites construye palas para generadores de turbinas de marea utilizando preimpregnado de fibra de carbono, curado en un autoclave, para manejar las grandes cargas colocadas en estas estructuras de alta torsión y baja velocidad.
Energía marina y renovable
Holland Composites también tiene contratos a largo plazo en la industria del gas y el petróleo en alta mar. “Los composites aquí ofrecen no solo un peso ligero y resistencia a la corrosión, sino también una fácil reparación”, dice Janssen. “No se permite el tiempo de inactividad a las plataformas y barcos costa afuera. Sin embargo, la reparación de estructuras metálicas requiere soldadura y chispas, por lo que la producción debe detenerse debido al peligro de incendio. Podemos parchear compuestos sin esta interrupción ". La compañía tiene nuevos clientes que solicitan dichos productos para una variedad de construcciones costa afuera.
También ha fabricado palas para turbinas mareomotrices. La recolección de energía mareomotriz es todavía nueva, dice Janssen, pero los primeros proyectos se han completado y los resultados son impresionantes. “Las turbinas mareomotrices ofrecen una fuente de energía confiable”, explica. "Las mareas siempre están ahí, en comparación con la eólica y la solar, por lo que puede predecir de manera confiable la producción de energía, que es clave para las empresas de energía". Holland Composites utiliza preimpregnado de fibra de carbono curado en autoclave para estas hojas porque las cargas son enormes. “Las cuchillas se mueven a baja velocidad pero con un par elevado”, dice Janssen. "Usted quiere la máxima traducción de la velocidad del rotor en el motor para producir energía, por lo que los fabricantes de turbinas necesitan estructuras fuertes pero eficientes que estén diseñadas para obtener la mayor cantidad de energía posible de los movimientos de las mareas".
Cada turbina tiene dos palas de 3 metros de largo y 18 milímetros de grosor. Hay cinco turbinas por generador de mareas. “La carga en estas palas de la turbina se describe como igual a la de un remolcador de 13.600 caballos de fuerza que avanza a plena potencia”, dice Janssen, “pero el cliente también necesita palas rígidas, livianas y de bajo mantenimiento con buena resistencia a la fatiga para mayor durabilidad. El acero habría sido demasiado pesado, lo que habría hecho que los generadores fueran menos eficientes ". Holland Composites fabrica solo las hojas; los carenados, el cono de la nariz y el revestimiento no estructural están hechos por fabricantes de FRP.
Instalación orientada al futuro
El recorrido comienza en el área de disposición, que cuenta con una gran mesa de disposición, partes para los veleros de alto rendimiento DNA y una variedad de láminas de CFRP que se están preparando para su instalación. El techo es bajo aquí debido a un entrepiso para almacenamiento de materiales. Esto se abre a un piso de producción de techos altos, con una máquina de corte automatizada Zünd (Altstätten, Suiza) justo más allá del área de colocación. El cortador tiene un rango de corte de 5.7 por 2.8 por 0.3 metros para procesar materiales preimpregnados, fibras secas y espuma de hasta 25 milímetros de espesor.
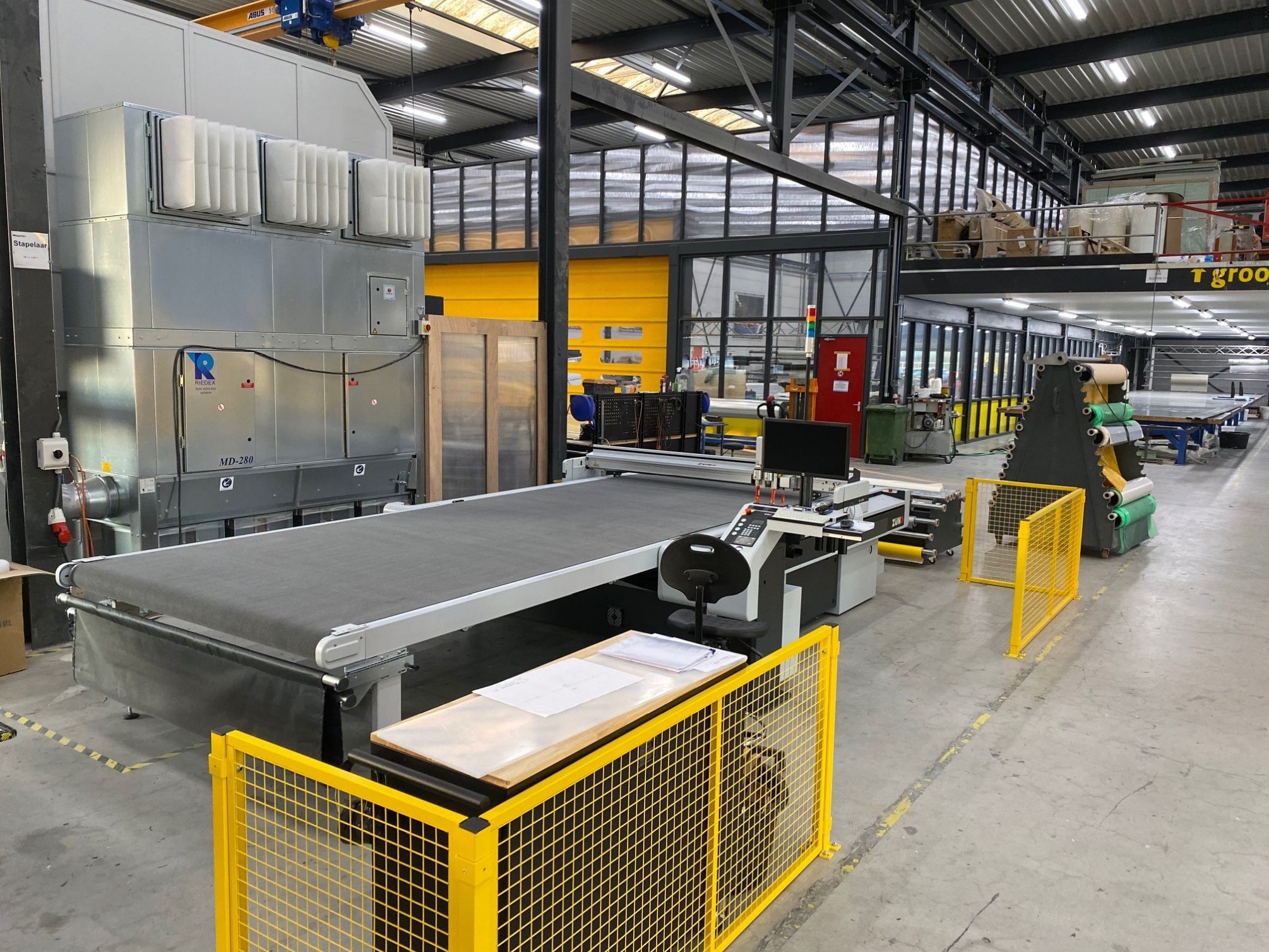
La cortadora automática Zünd en primer plano suministra refuerzos cortados y espuma al área de colocación, que se puede ver en la parte posterior, a la derecha, con el entrepiso de almacenamiento de materiales arriba. El área de herramientas cerrada se encuentra detrás de la puerta enrollable amarilla, que se ve aquí detrás del lado del centro de mecanizado CMS, que está al lado de la mesa de corte Zünd.
Dando la vuelta desde el cortador Zünd, caminamos hacia una sala de herramientas con mampara de vidrio que linda con el área de colocación. Al entrar por una puerta enrollable amarilla, hay varias herramientas en proceso y las piezas se están curando bajo bolsas de vacío. “Hacemos nuestros propios moldes”, dice Janssen. "Para las piezas de CFRP, utilizamos CFRP o aluminio para las herramientas, así como orificios de ventilación para la circulación de aire dentro de las herramientas, lo que ayuda a garantizar un curado uniforme en toda la pieza".
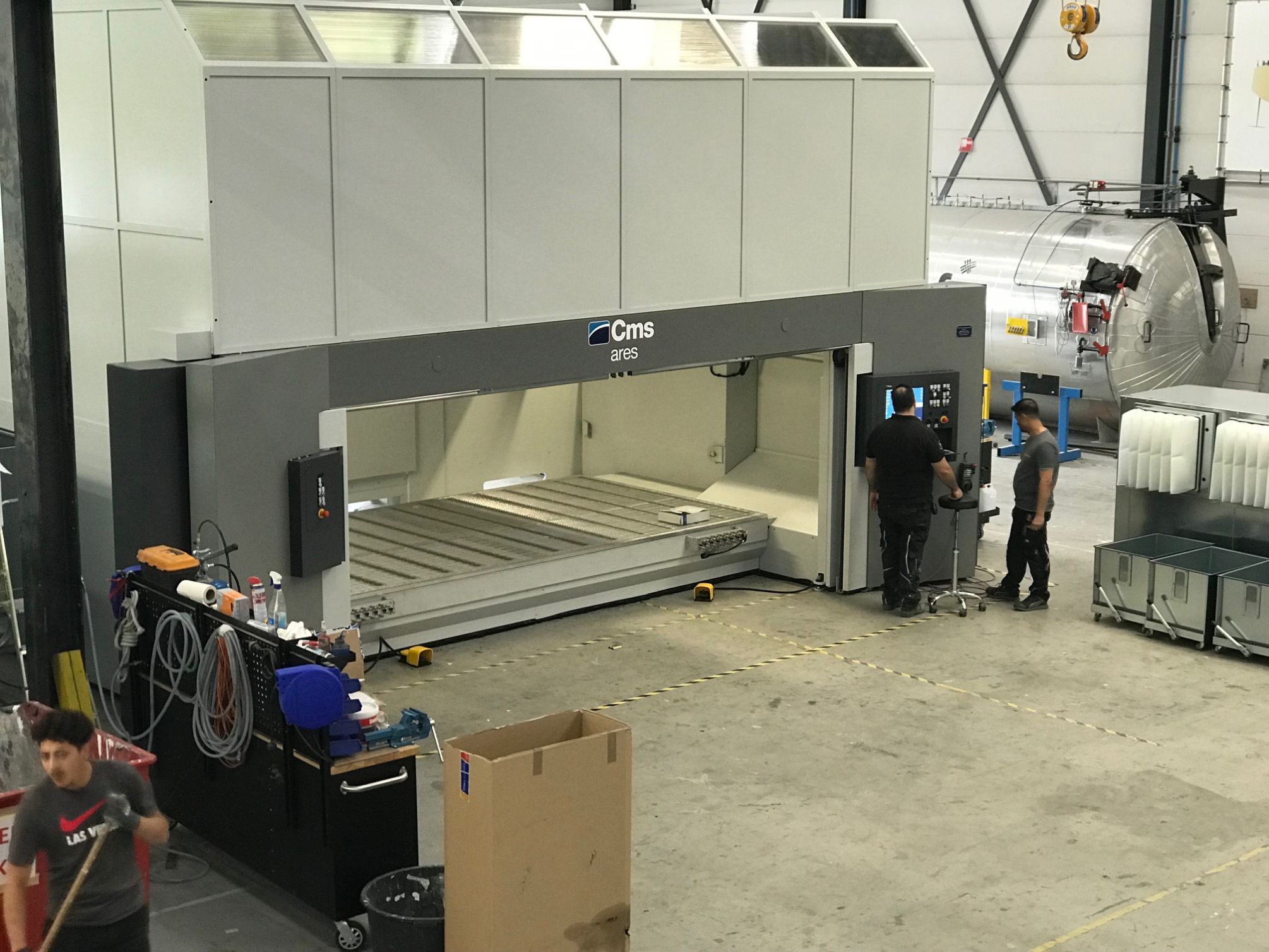
El centro de mecanizado CMS está situado entre la mesa de corte a su izquierda (fuera de la vista) y el autoclave (en el extremo derecho, contra la pared).
Al salir de la sala de herramientas, pasamos por el centro de fresado CNC de 5 por 2 por 1,8 metros y 5 ejes (CMS SpA, Zogno, Italia) y podemos ver el autoclave de 6,5 por 2,2 metros (Tankbouw Rootselaar, Nijkerk, Países Bajos). "Normalmente curamos a 125 ° C con una presión de 6 bar ”, señala Janssen.
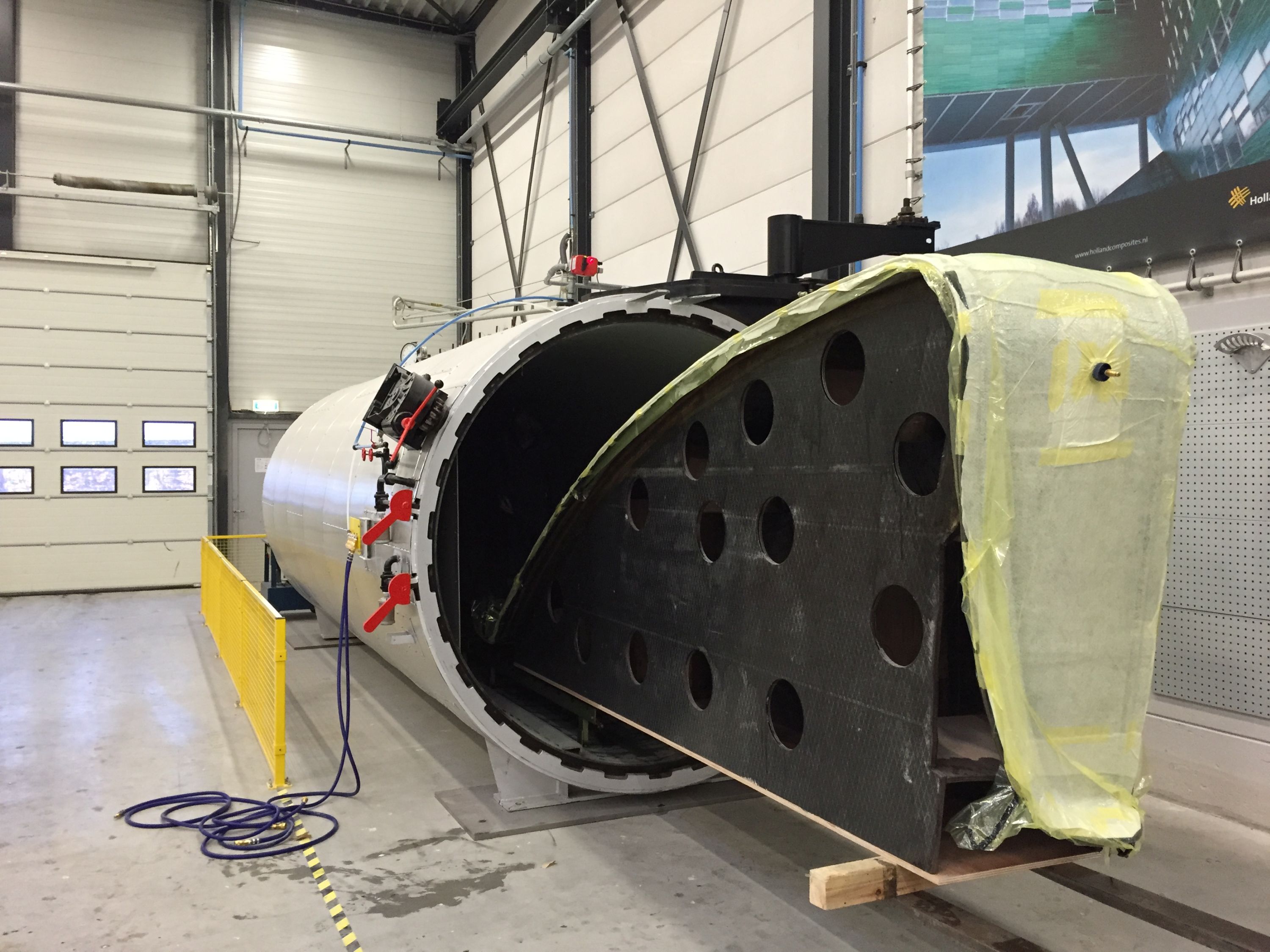
El autoclave también se ve a continuación con una herramienta de CFRP (observe los orificios para la ventilación del aire) y una lámina de CFRP grande que se cura bajo una bolsa de vacío para un velero multicasco de alto rendimiento.
La pared al lado del autoclave corta el área de producción en dos mitades, a lo largo del edificio a lo largo de la sala de herramientas. Damos la vuelta y pasamos por una puerta a la segunda mitad de la instalación de Holland Composites, que contiene una máquina de corte por chorro de agua (rango de corte de 8 por 2 por 0,5 metros), varios hornos de hasta 15 por 10 por 3,5 metros y la cabina de pintura de la empresa de 19 x 12 x 3,5 metros. “Actualmente, estamos produciendo paneles grandes para un proyecto en Qatar y una serie de casetas de cubierta de CFRP para los barcos Windcat”, dice Janssen.
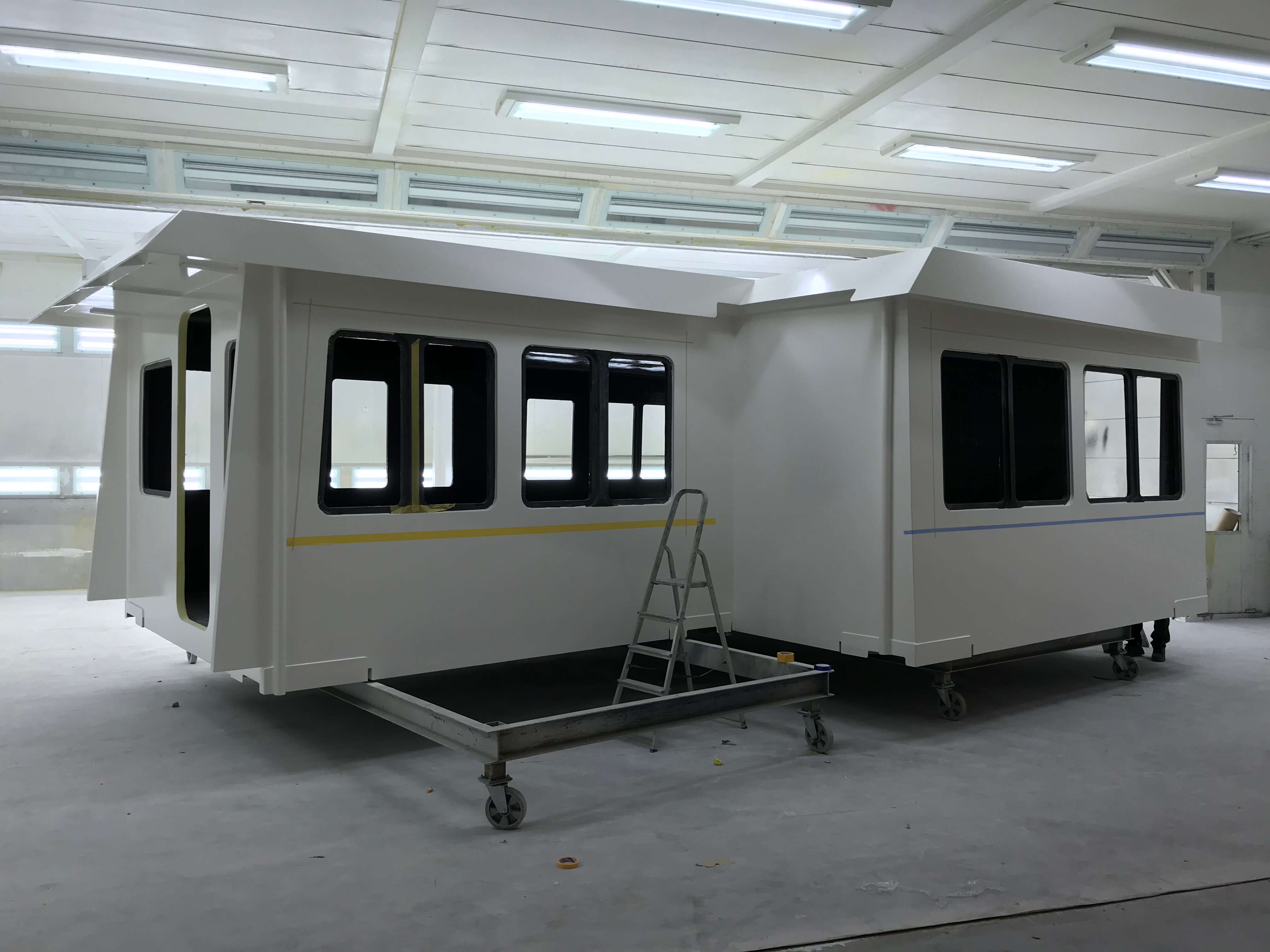
Las casetas de CFRP que Holland Composites produce para los catamaranes Windcat Workboats están pintadas en la cabina de pintura de la empresa de 19 x 12 x 3,5 metros.
La última instalación de Holland Composites es una impresora Massivit 3D (Lod, Israel) 1800 Pro con un volumen de construcción de 145 por 111 por 180 centímetros. “Somos socios que innovan en la impresión 3D de moldes con tres cabezales de impresión, donde dos imprimen las pieles de un sándwich y la boquilla central imprime el relleno o la estructura de celosía en el medio”, explica Janssen. “Usaremos material reforzado con fibra en desarrollos futuros, pero por ahora, podemos imprimir herramientas precisas con un mínimo de fresado necesario. Usamos mucho menos material y vemos tiempos de producción de moldes muy rápidos. Ahora tenemos una cadena de proceso completa, con la capacidad de pasar del diseño a los moldes y a las piezas pintadas en un corto período de tiempo ”.
Señala que la compañía todavía está explorando cómo aumentar el uso de la automatización para avanzar aún más en sus productos, pero sin aumentar los costos. “Todo se reduce al ingenio. Nos atraen problemas muy complejos que pocos se atreven a abordar, pero como constructores de barcos, siempre hemos tenido que ser muy creativos con recursos limitados. Para lo que hacemos en materiales compuestos, vemos muchas oportunidades en el futuro ”.
Resina
- Los fabricantes visitan United Safety para un recorrido por la planta, debate sobre las mejores prácticas
- CompositesWorld SourceBook 2022
- Solución de problemas de termoformado de compuestos termoplásticos
- La evolución de los compuestos aditivos
- Compuestos termoplásticos:soporte de parachoques estructural
- Compuestos como refuerzos de carrocería automática
- Vista previa de CAMX 2020
- Los Países Bajos mostrarán la experiencia del país en materiales compuestos en JEC World 2019
- TPAC y TPRC desarrollan un proceso de reciclaje de compuestos termoplásticos
- Soldadura de compuestos termoplásticos
- Compuestos de alto rendimiento en Israel