Visita a la planta:STELIA Aerospace, Méaulte, Francia
Con 7.000 empleados en todo el mundo y unos ingresos de 2.200 millones de euros en 2018, STELIA Aerospace (Toulouse, Francia) afirma claramente sus principales productos y su posición en la industria:No 1 en Europa / No. 3 en el mundo para aeroestructuras, No. 1 mundial para asientos de piloto y tripulación y No. 3 en todo el mundo para asientos de pasajeros de primera clase y clase ejecutiva.
El uso de materiales compuestos de STELIA Aerospace se extiende a las secciones delanteras del fuselaje del Airbus A350, alas para aviones turbohélice ATR, varias estructuras de helicópteros y en algunos productos de asientos, incluido su asiento OPAL más nuevo. Las instalaciones de producción de materiales compuestos incluyen los sitios franceses Méaulte (grandes secciones de fuselaje) y Salaunes (piezas compuestas más pequeñas), piezas detalladas y ensamblaje en Marruecos y Túnez y una amplia gama de piezas compuestas para aviones, defensa y espacio en el sitio anterior de Composites Atlantic en Lunenburg. Nueva Escocia, Canadá.
STELIA Aerospace se formó a través de la fusión en 2015 de dos subsidiarias anteriores de Airbus:Aerolia y Sogerma. Su emplazamiento en Méaulte, a 1,5 horas en coche al norte de París, cubre 49 hectáreas con 150.000 metros cuadrados de espacio de producción, 1.500 empleados y 500 subcontratistas, y es una parte clave de la cadena de suministro de Airbus. Su ubicación en una pequeña ciudad oculta una potencia de producción, "entregando 860 secciones de fuselaje delantero para el A320, A330, A350, A380 y A400M en 2018", dice el gerente de comunicaciones de STELIA Méaulte, Francois Fournier. Él es mi guía a través de la producción del fuselaje de nariz del A350 “Factory of the Future” del sitio y la instalación STELIALAB R&T, acompañado por Olivier Canal, jefe de fabricación, ensamblaje y automatización, composites y digital de R&T de STELIA Aerospace Méaulte, y Simon Maire-Vigeur , jefe de fabricación de composites R&T, STELIALAB.
"Fábrica del futuro"
Durante una presentación introductoria en el edificio de la sede del sitio, Fournier explica que STELIA Aerospace ha invertido en tecnologías futuras, como la fabricación digital y la automatización, incluida la realidad aumentada / realidad virtual utilizada para aumentar la eficiencia en la producción y robots / cobots para un ensamblaje más eficiente.
“El futuro son los compuestos y estructuras metálicas ”, apunta Canal. "Estamos tratando de definir soluciones futuras no para reemplazar a nuestros trabajadores, sino para hacerlos más eficientes".
Este impulso por la eficiencia se ejemplifica quizás mejor en la iniciativa “Fábrica del futuro” que comenzó hace cinco años para cumplir con las rampas en la producción de A320 y A350. “Adoptamos una nueva estrategia industrial para este sitio”, recuerda Canal, quien fue gerente de proyecto de la iniciativa. "Queríamos tener la capacidad de cumplir con tasas de producción variables y desarrollamos herramientas flexibles que pudiéramos reutilizar de un programa a otro".
Otro resultado de este replanteamiento fue la dedicación de edificios a programas específicos. “Cada uno tendría una línea y un equipo”, dice Canal, “y estaría diseñado con un enfoque de manufactura esbelta que se enfoca en eliminar el desperdicio en mano de obra, movimiento, materiales y procesos”. STELIA Aerospace también rediseñó la línea A320 y obtuvo un aumento del 10-20 por ciento en la productividad, “lo que en realidad es una mejora significativa”, dice Canal. “Logramos esto en 2.5 años, cambiando más del 50 por ciento de la huella de la fabricación de este sitio mientras mantuvimos la producción y Entrega 100% a tiempo sin pérdida de calidad ". Este éxito se atribuye al respaldo de la gerencia de alto nivel, "pero también trabajamos duro para que los trabajadores tuvieran la propiedad", señala.
Canal explica que el diseño del edificio de producción del A350 de 30.000 metros cuadrados fue dictado por el flujo, ejemplificado en su forma de U, con materias primas entrando por un extremo y secciones terminadas del fuselaje saliendo por el otro. “Todo para la producción de estructuras de nuestro A350 se encuentra en este edificio, desde el inicio hasta el montaje final. Esto es importante, por ejemplo, permitir que cualquier problema de calidad se identifique y aborde rápida y fácilmente ”, dice.
Para el A350, STELIA Aerospace produce la sección 11 del fuselaje de la nariz, que es totalmente de metal para resistir mejor el daño por impacto de aves, así como el complejo conjunto híbrido de metal / compuesto para la sección 12 y la unidad inferior de la sección 11/12, que incluye la nariz. bahía del tren de aterrizaje. Fournier muestra el video "Factory of the Future" de STELIA Aerospace, señalando la línea pulsada, como la que se usa para el ensamblaje de automóviles. “Establecimos una línea de demostración para permitir que los trabajadores capaciten y desmitifiquen esta línea en movimiento, que trabaja en un tiempo específico para cumplir con la producción a velocidad completa”, dice Canal.
Otro aspecto fue la tecnología digital. “Las soluciones digitales nos permitieron poner todos los esquemas técnicos y pasos en una tableta y asegurar el acceso a la última maqueta 3D para cada sección”, dice Canal. Por lo tanto, los trabajadores se mantienen informados sobre los detalles y cambios cruciales, mientras que los gerentes son notificados fácilmente sobre los problemas potenciales. “También desarrollamos la realidad aumentada para ayudar al ensamblaje, por ejemplo, la proyección sobre las carcasas del fuselaje que muestra qué partes y dónde se realizarán los accesorios”, señala Canal. Agrega que la inspección cobots se utilizan para completar escaneos 3D de secciones terminadas que luego se comparan con la maqueta digital, identificando objetos extraños o piezas faltantes, problemas de calidad, etc.
Nuestro recorrido comenzó en la sala limpia del edificio de producción del A350, donde las máquinas de colocación automatizada de fibra (AFP) de Coriolis (Quéven, Francia) colocan grandes carcasas de fuselaje de polímero reforzado con fibra de carbono (CFRP) para la unidad inferior de la sección 11/12 y la corona y dos carcasas laterales para la sección 12. Estas carcasas se acoplan luego con largueros prefabricados, se embolsan al vacío y se curan en un autoclave. Después del curado, se recortan y se cargan en herramientas de manipulación que permiten un fácil transporte a lo largo de todos los pasos para el ensamblaje, que incluyen la perforación robótica y la instalación de sujetadores. Cada panel se inspecciona mediante pruebas no destructivas automatizadas (NDT). Los ensamblajes completos se entregan a la línea de ensamblaje del fuselaje de Airbus en Saint Nazaire, Francia.
STELIALAB
La siguiente parada es el centro de I + T STELIALAB de 2.000 metros cuadrados, que ocupa la mitad izquierda de IndustriLAB, una instalación regional de tecnología y capacitación ubicada justo al sur del complejo cerrado STELIA. Las actividades de STELIALAB están dedicadas a los materiales compuestos, el ensamblaje y las tecnologías digitales.
El recorrido aquí comienza de nuevo en la salle blanche (sala limpia), una sala bastante grande y abierta con suministros de ensacado y herramientas de almacenamiento. Simon Maire-Vigueur explica que la misión del grupo es identificar el futuro de la producción de bajo costo y alto volumen para piezas en su mayoría grandes y complejas. La industrialización de compuestos termoendurecibles incluye AFP de alta velocidad y procesos de infusión de resina líquida (LRI), incluido el moldeo por transferencia de resina (RTM), para estructuras grandes de caja cerrada, como componentes de ala, planos de cola horizontales y planos de cola verticales.
Saliendo de la sala limpia, ingresamos a la sala AFP ocupada por una máquina Coriolis que puede colocar piezas de hasta 4 metros de longitud. Dedicado a R&T, Maire-Vigueur señala que está ocupado durante más de 200 días al año. STELIALAB ha desarrollado un proceso para integrar endurecedores secos creados por AFP y pieles que se curan en autoclave (OOA) utilizando un horno o herramientas autocalentables. “Preferimos LRI con menor presión de inyección porque podemos usar herramientas más baratas”, dice Maire-Vigueur.
Hoja de ruta del TPC
Esta máquina AFP también se utilizó para preparar la piel del demostrador de fuselaje / cola de helicóptero de compuesto totalmente termoplástico (TPC) como parte del programa de desarrollo ARCHES TP. Exhibido en el Salón Aeronáutico de París 2017 y también en el JEC World en 2018 y 2019, se fabricó con 8 cables de cinta de fibra de carbono / polietercetonecetona (PEKK) de 0,25 pulgadas de ancho con calentamiento por láser. “Integramos la protección contra rayos con la AFP durante la bandeja”, señala Maire-Vigueur. "La piel se curó con OOA con película de empaquetado Kapton, que en realidad no es muy conveniente". Los largueros en forma de omega se fabricaron a partir de paneles planos de cinta unidireccional comprados que fueron estampados por Aviacomp (Toulouse, Francia). El mismo proceso se utilizó para los marcos, pero utilizando planchas de material tejido suministradas por Porcher (Badinières, Francia) y estampadas en Cetim (Nantes, Francia). Aunque los marcos se sujetaron mecánicamente de manera estándar, los largueros se sujetaron mediante soldadura automática por inducción dinámica. “Esto permite un menor costo y nuevas posibilidades de diseño”, señala Maire-Vigueur. “También demostramos sobremoldeado para puntos de sujeción, como arneses eléctricos”.
Cuando se le preguntó acerca de los desafíos del programa, Maire-Vigueur cita las capas, la soldadura y el cronograma de 15 meses. “Incluso lograr el estampado sin demasiada distorsión en el material tejido no fue fácil”, agrega. Aunque el diseño de la cola fue completado por la oficina de diseño de Toulouse de STELIA Aerospace, toda la producción fue supervisada por STELIALAB. Sin embargo, ARCHES TP fue solo un paso en la hoja de ruta de compuestos termoplásticos de STELIA Aerospace. La empresa continúa desarrollando tecnologías TPC para demostrar la viabilidad de un fuselaje TPC a gran escala en los años siguientes.
Rediseño de aeroestructuras futuras
Al salir de la sala de AFP, el recorrido avanza a través de un pasillo abierto muy grande que está dividido en "celdas de desarrollo" seguras por paredes temporales para proteger la propiedad intelectual. Caminando por el pasillo y girando a la izquierda, llegamos a una zona con un pequeño autoclave Scholz (Coesfeld, Alemania) capaz de 450 ° C, y una máquina de inyección para infusión de resina. “Debido a que nuestra hoja de ruta es curar OOA, en realidad usamos el autoclave como un horno, curando compuestos termoplásticos sin presión”, explica Maire-Vigueur. Hay una sala de molduras con cortinas y un área junto a ella con equipo NDT, incluido un pequeño sistema C-scan.
Damos la vuelta de nuevo y entramos en un gran laboratorio de pruebas. “Podemos estudiar secciones transversales pulidas para control de calidad e investigaciones de materiales y procesos”, dice Maire-Vigueur. El laboratorio también cuenta con un brazo Romer (Hexagon Manufacturing Intelligence, Shropshire, Reino Unido) para la medición de coordenadas y equipo para la relación de volumen de fibra, dureza y pruebas químicas. “Todos los ingenieros de nuestro equipo de I + T pueden realizar sus propios controles de procesos y materiales”, señala Maire-Vigueur. “Los capacitamos para que puedan operar desde el diseño hasta la fabricación y la inspección y prueba de las piezas finales. Esto es importante para comprender todo el proceso y permite una evaluación rápida de los problemas sospechosos y sus causas. El diseño no está separado de la fabricación y las pruebas de calidad ”.
La última parada es un gran laboratorio de automatización dentro de una de las áreas amuralladas. Un breve vistazo al interior muestra el trabajo que explora nuevos ensamblajes utilizando robots y cobots. “Buscamos un mayor desarrollo de herramientas más pequeñas y funcionales y tratamos de imaginar cómo podría ensamblar piezas más rápido y con menor costo”, dice Canal. “Nuestra cultura consiste en superar los límites y abrir nuevos caminos. Hemos sido líderes en la implementación de robótica y ahora somos líderes en impulsar la tecnología de compuestos. Hemos demostrado nuestra capacidad para repensar y volver a imaginar el futuro y nunca nos detendremos ”.
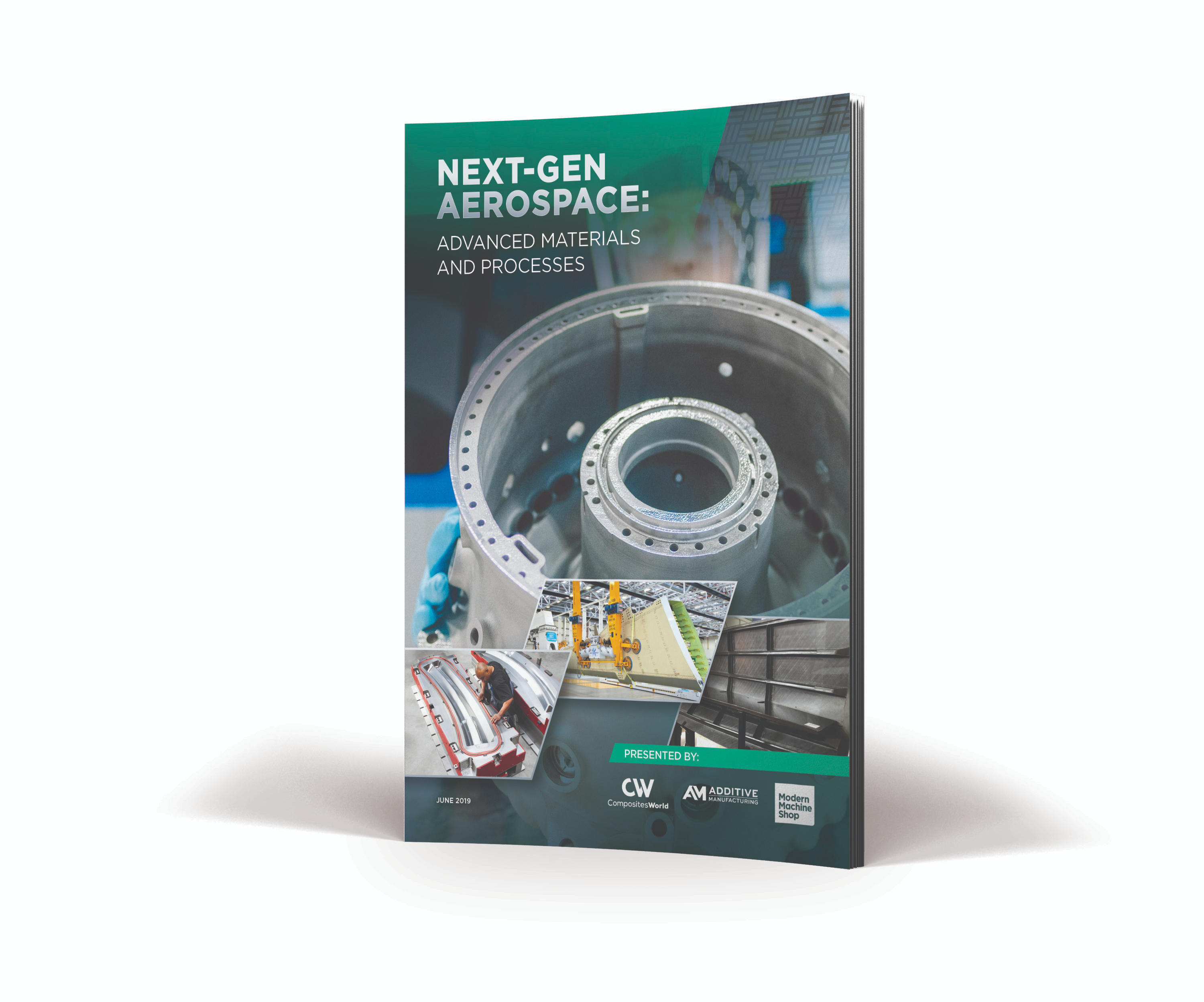
La próxima generación de fabricación aeroespacial
Con la proyección de que la industria de la aviación comercial se duplicará en los próximos 20 años, satisfacer la demanda de aviones de pasajeros y de carga requerirá nuevas tecnologías y tasas de fabricación sin precedentes.
Obtenga más información sobre los materiales y procesos que darán forma a los aviones de próxima generación en una colección de historias de CompositesWorld, Modern Machine Shop y Fabricación aditiva , disponible para leer o descargar gratis . Consíguelo aquí.
Resina
- Vespel®:el material aeroespacial
- Poliplásticos para expandir la producción de COC de Topas
- Radici está expandiendo significativamente la capacidad de producción global
- Polykemi invierte en su propia planta de compuestos de EE. UU.
- Rethink Robotics obtiene nueva sede y planta de producción
- Toyota elige el sitio de Carolina del Norte para la planta de producción de baterías para vehículos eléctricos
- Los fabricantes visitan Southco para un recorrido por la planta, debate sobre las mejores prácticas de mejora continua
- Arkema Inc. construye una planta de producción de PEKK de EE. UU.
- Hexion presenta una solución epoxi de dos componentes para la producción de compuestos aeroespaciales
- Kaneka Aerospace obtiene la certificación aeroespacial AS9100D
- El consorcio de compuestos termoplásticos tiene como objetivo la producción de alto volumen para la industria automotriz y aeroespacial