Avanzando en compuestos termoplásticos y RTM para Clean Sky 2 en España
EURECAT Centro Tecnológico de Catalunya (EURECAT Technology Centre Catalonia, Barcelona, España) es una organización privada de I + D sin ánimo de lucro con 11 instalaciones, 650 empleados y 50 millones de euros de ingresos anuales. “Es el segundo centro de I + D + i más grande de España”, explica Angel Lagraña Hernández, director de programas para el mercado aeronáutico y espacial de EURECAT. Explica que parte de los ingresos de EURECAT proviene del gobierno catalán y del resto, la mitad debe provenir de empresas privadas, en su mayoría pequeñas y medianas empresas (pymes), mientras que la otra mitad puede ser pública, como las financiadas por la Unión Europea. Programa Clean Sky 2. “Ahora tenemos 18 proyectos Clean Sky”, señala Lagraña, “que nos adjudicaron únicamente sobre la base de presentaciones competitivas en respuesta a convocatorias de propuestas”.
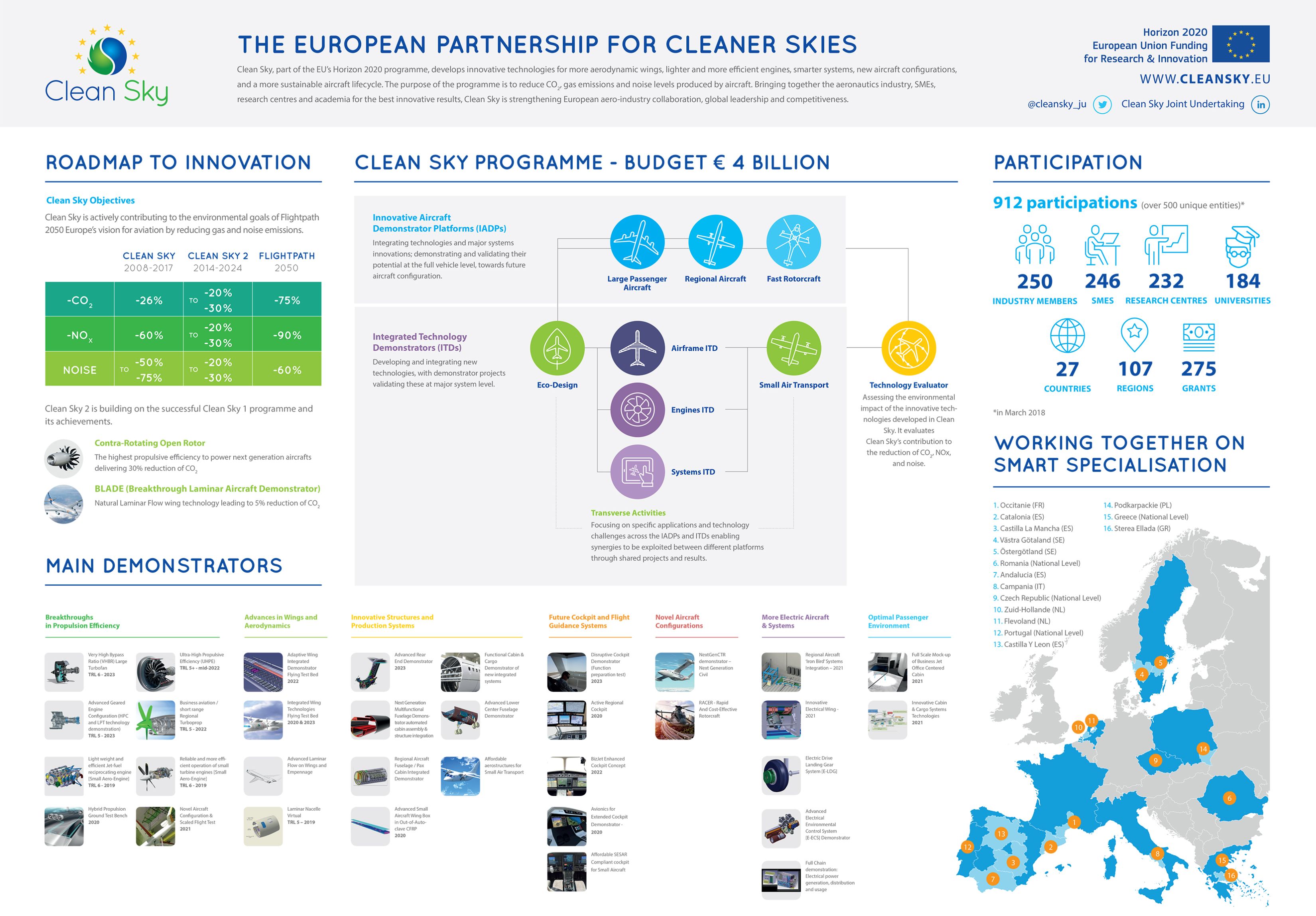
Entre los ejemplos de cómo los materiales compuestos se incluyen en los numerosos objetivos y demostradores de tecnología planificados de Clean Sky 2 se incluyen:
- El demostrador de fuselaje multifuncional de próxima generación:aprovecha los termoplásticos para obtener cielos más limpios
- Economía circular:toma forma el fuselaje compuesto para aviones regionales
- Aprovechamiento de la experiencia en automovilismo para FastCan de Clean Sky
“EURECAT es altamente transversal, trabajando en la industria automotriz, ferroviaria y otras, además de su trabajo en el aeroespacial”, dice Lagraña. "También tiene muchas actividades en TI, como análisis de datos y blockchain, etc. Composites 4.0 es una de sus áreas estratégicas". Dentro de los compuestos, señala que EURECAT trabaja principalmente con tecnologías fuera de autoclave (OOA). "Nos enfocamos en termoplásticos y moldeo por compresión de líquidos, incluido el monitoreo del proceso en tiempo real, incluido el monitoreo de la temperatura de transición vítrea (Tg) de la resina durante el procesamiento". (Siga leyendo la sección sobre COFRARE, al final de este blog, para ver más sobre este monitoreo de Tg).
Los proyectos más recientes de EURECAT relacionados con compuestos en Clean Sky 2 incluyen:
- KEELBEMAN para demostrar una viga de quilla de material compuesto termoplástico (Este proyecto ha recibido financiación de la Empresa Común Clean Sky 2 en el marco del programa de investigación e innovación Horizon de la Unión Europea bajo GAP n ° 785435 KEELBEMAN) ;
- WINFRAME 4.0 para construir marcos de ventanas compuestos termoplásticos (TPC) para el demostrador Green Regional Aircraft (GRA) en Clean Sky (2008-2017) y extendido al Regional Aircraft IADP (Innovative Aircraft Demonstrator Platform) en Clean Sky 2 (2014-2024);
(Este proyecto ha recibido financiación de la Empresa Común Clean Sky 2 en el marco del programa de investigación e innovación Horizon de la Unión Europea bajo GAP n ° 821323 WINFRAME 4.0). - COFRARE 2020 para marcos de fuselaje termoendurecibles fabricados con moldeo por transferencia de resina (RTM) con bridas de corte de TPC.
(Este proyecto ha recibido financiación de la Empresa Común Clean Sky 2 en el marco del programa de investigación e innovación Horizonte de la Unión Europea bajo GAP n ° 821261 COFRARE 2020.)
Viga de quilla de material compuesto termoplástico
Cielo limpio 2 - JTI-CS2-2017-CFP06-LPA-02-20. Duración del proyecto:marzo de 2018 a diciembre de 2019
El objetivo del proyecto KEELBEMAN es desarrollar una estructura de viga de quilla orientada a la fabricación para un avión tipo A320 que permita altas tasas de producción de aviones pero a un costo asequible a través de compuestos termoplásticos. Además de EURECAT como coordinador del proyecto, los socios incluyen:
- Airbus (Toulouse, Francia) como administrador de temas
- CETMA (Centro Europeo de Investigación para el Diseño y los Materiales de Tecnologías, Brindisi, Italia)
- The CT Engineering Group (CT Ingenieros, Madrid, España), una firma con numerosas oficinas globales que tiene un contrato de varios años con Airbus para el desarrollo de aeronaves, como investigación en el fuselaje, alas y parte trasera a través de su oficina de Hamburgo, Alemania; investigación sobre la parte trasera (España); investigación sobre estructuras relacionadas con el fuselaje y las centrales eléctricas (Toulouse, Francia) y el desarrollo de alas (Bristol, Reino Unido)
- Sofitec (Sevilla, España), especialista en fabricación y montaje de aeroestructuras con experiencia y capacidad de producción en composites.
CT Engineering Group proporcionó un modelado completo de la geometría de la viga de la quilla a través de su oficina de Toulouse, mientras que Sofitec desarrolló la inspección de ensayos no destructivos (NDT). “Esto es muy desafiante con una estructura de caja tan cerrada”, señala Lagraña.
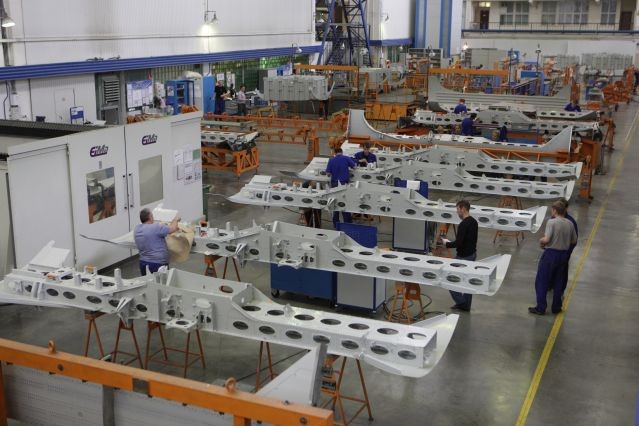
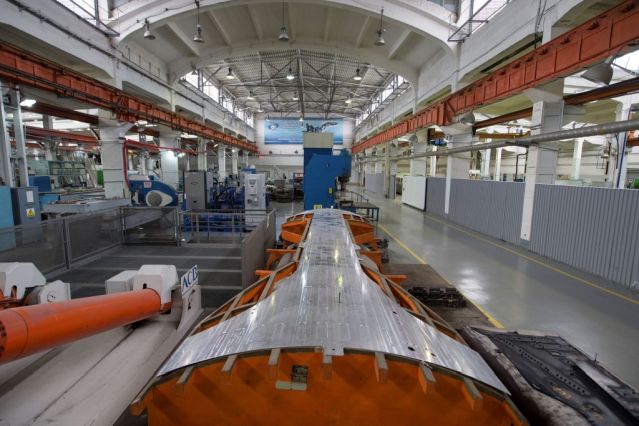
Aquí se muestra el conjunto de viga de quilla A320, fabricado en metal por Irkut Corporation (Moscú, Rusia). Según los informes, Irkut firmó un contrato con Airbus en 2004 para suministrar componentes, incluido el compartimento del tren de aterrizaje de nariz, la viga de la quilla y la pista de flaps, que se instalan, en promedio, en cada tercer avión de la familia A320. FUENTE | Irkut
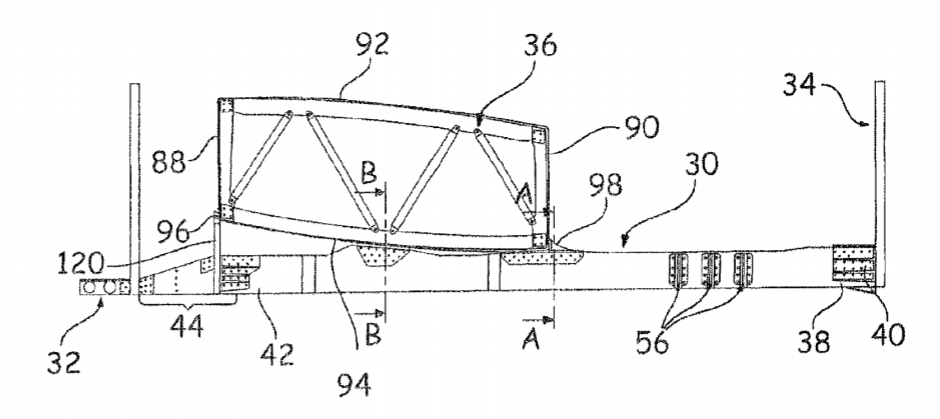
Desarrollo de estructuras de vigas de quilla
“Hoy en día, la mayoría de las vigas de quilla de los aviones están hechas de metal, excepto el Airbus
A350, que es un compuesto monolítico de fibra de carbono ”, dice Lagraña. "Esto requiere una gran cantidad de remaches y una cantidad significativa de tiempo para el montaje". Explica que la viga de la quilla es una estructura crítica en el fuselaje, “Ha habido casos en los que la viga de la quilla se ha roto durante el aterrizaje, provocando que todo el fuselaje se agriete y se rompa.
Según un artículo de 2011 de Steve Wilhelm, la viga de la quilla del A350 tiene un 70% de material compuesto, 54 pies (16,5 metros) de largo, junto con 10.000 sujetadores, pesa 1,2 toneladas y forma la columna vertebral del avión. Wilhelm señala que el competitivo avión Boeing 787 "no depende de una estructura de quilla tan robusta, porque la mayor parte de la resistencia del casco proviene de los barriles compuestos que se sujetan entre sí de un extremo a otro". El artículo luego cita a Michel Merluzeau, socio gerente de la consultora aeroespacial G2 Solutions LLC (Kirkland, Washington, EE. UU.), Quien describe el diseño de Airbus como "más convencional" y "menos riesgoso", pero señala que la viga de la quilla es "esencial para el integridad estructural de esa aeronave ".
Airbus fue pionero en la fabricación de una viga de quilla compuesta para el A340 en 2001. Pero, como se describió anteriormente, la gran cantidad de remaches necesarios va en contra del ahorro de peso posible mediante el uso de compuestos. Por lo tanto, un objetivo clave en el proyecto KEELBEMAN es minimizar los sujetadores mediante el uso de componentes compuestos termoplásticos que se sueldan entre sí.
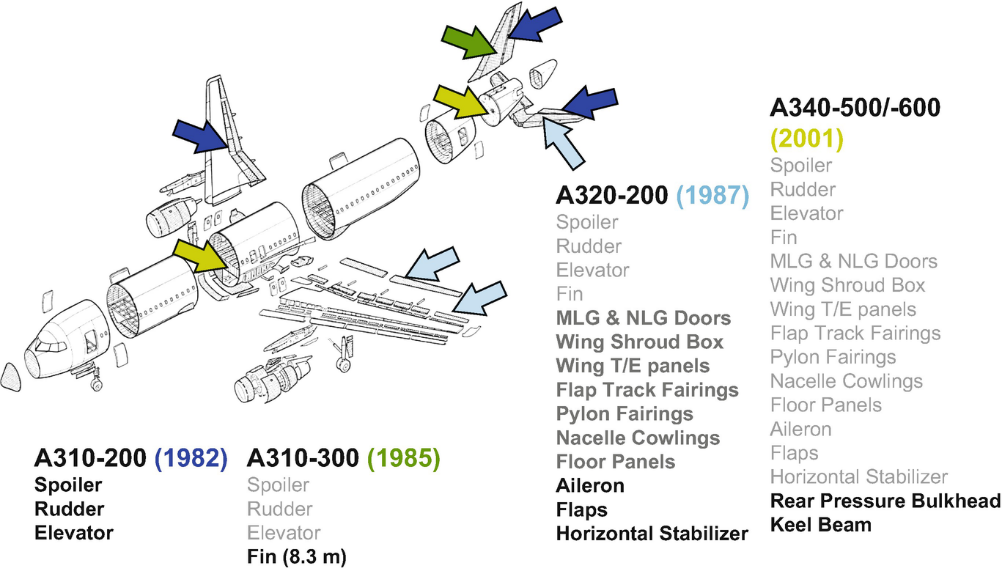
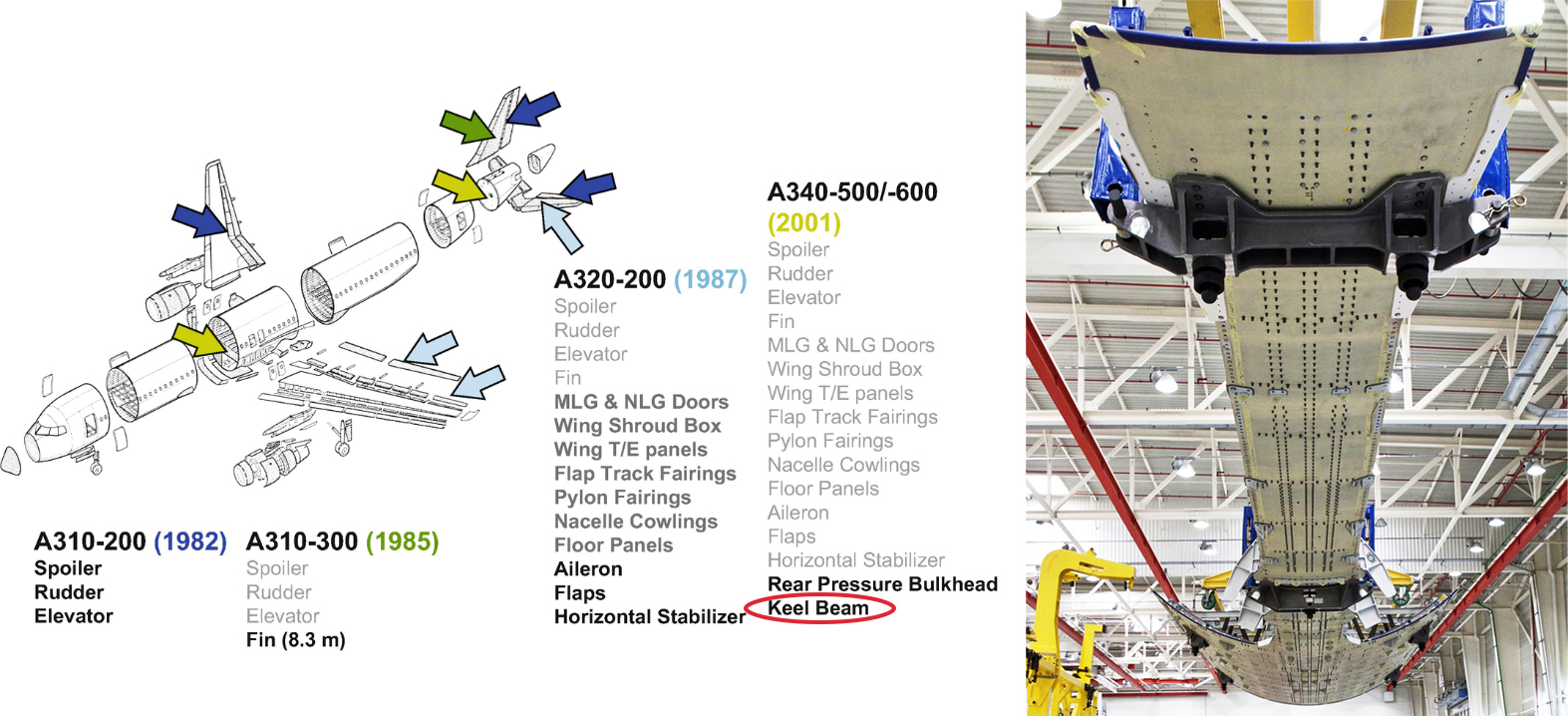
Viga de quilla TPC
“El desarrollo de una viga de quilla de material compuesto termoplástico utilizando soldadura para el ensamblaje es parte del desarrollo de Airbus del avión del mañana, que incluye programas como el Ala del Mañana y el Fuselaje del Mañana”, dice Lagraña. “Dentro de KEELBEMAN, hemos producido una sección de demostración de 250 milímetros por 500 milímetros por 1 metro de largo de una viga de quilla con largueros y hemos demostrado la viabilidad de soldar esta estructura con la mayor automatización posible”.
Lagraña señala que las placas de pared de demostración y los largueros se fabricaron con cinta de fibra de carbono / polietercetonacetona (PEKK) unidireccional (UD) en un proceso de moldeo por compresión continua (CCM) desarrollado por CETMA (consulte “Moldeo por compresión de grado aeroespacial” y “PEEK vs. PEKK vs. PAEK y moldeo por compresión continua ”). “También hay nervaduras para refuerzos transversales que se realizaron mediante el tradicional moldeo por compresión no isotérmica de EURECAT”, añade Lagraña.
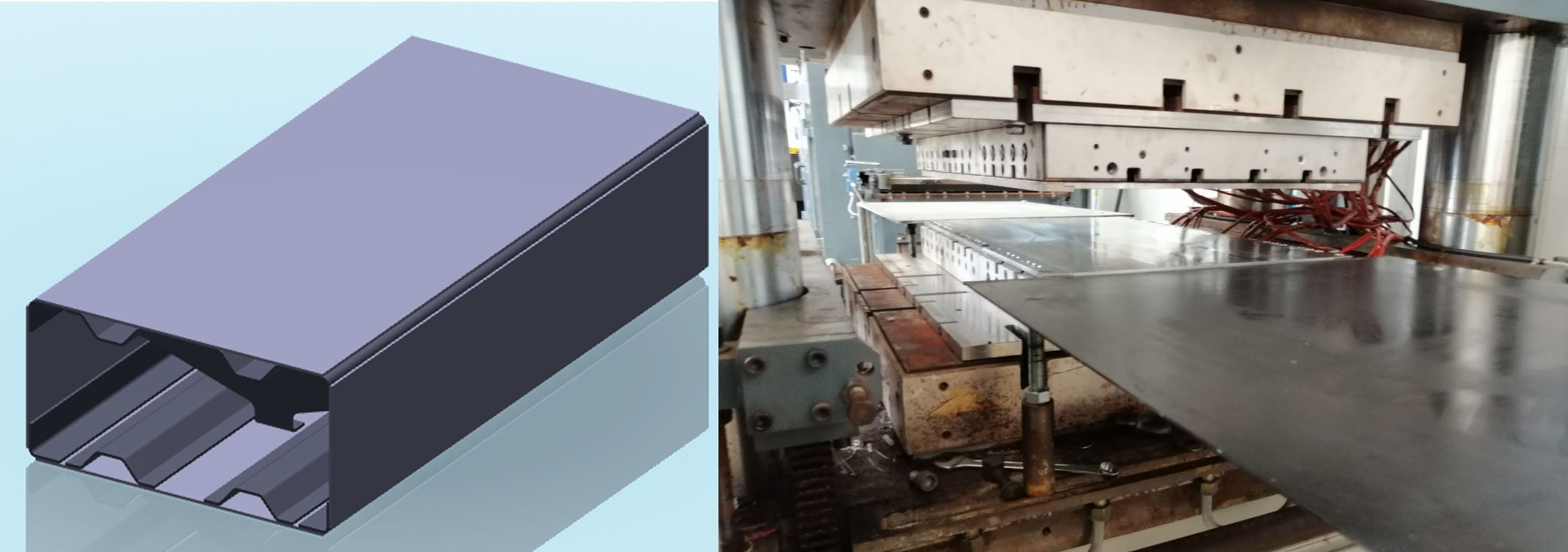
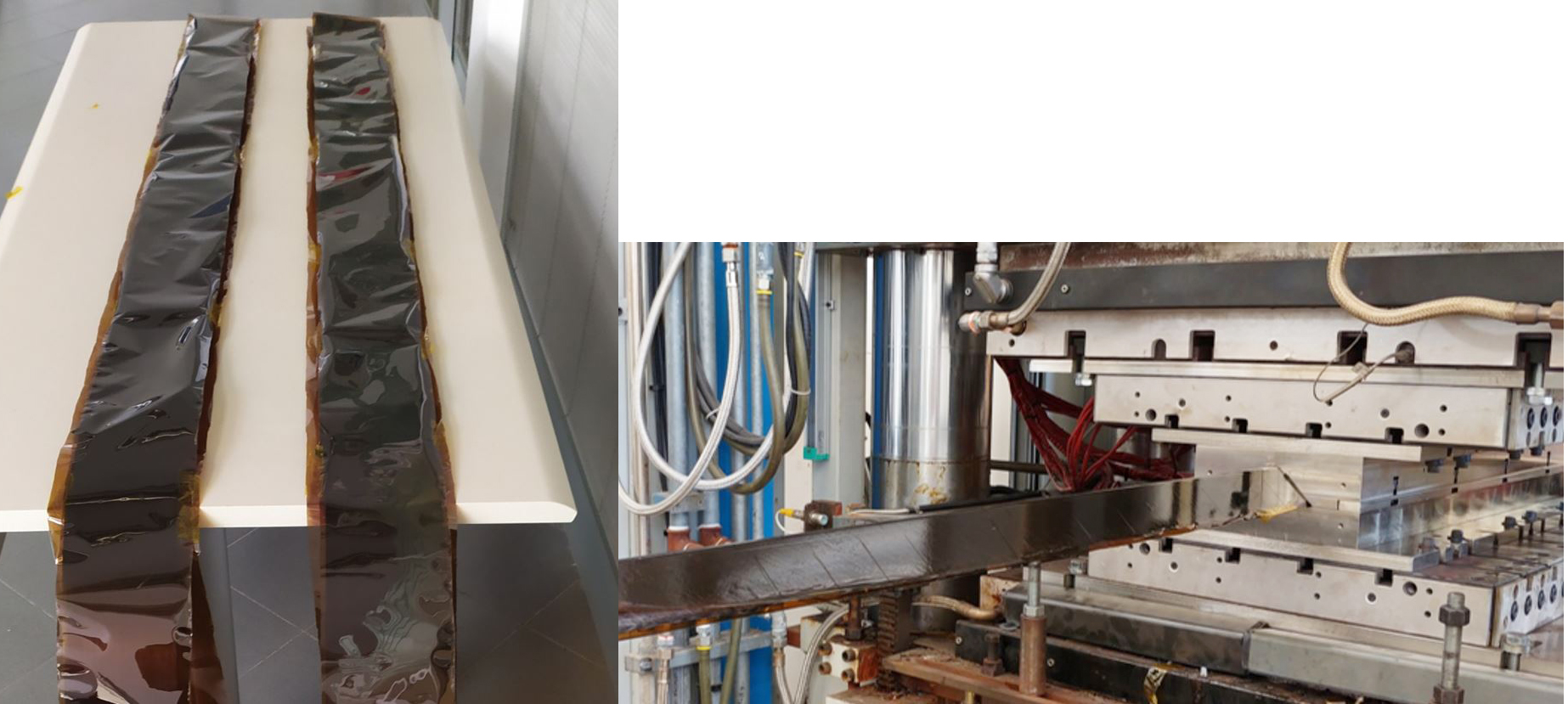
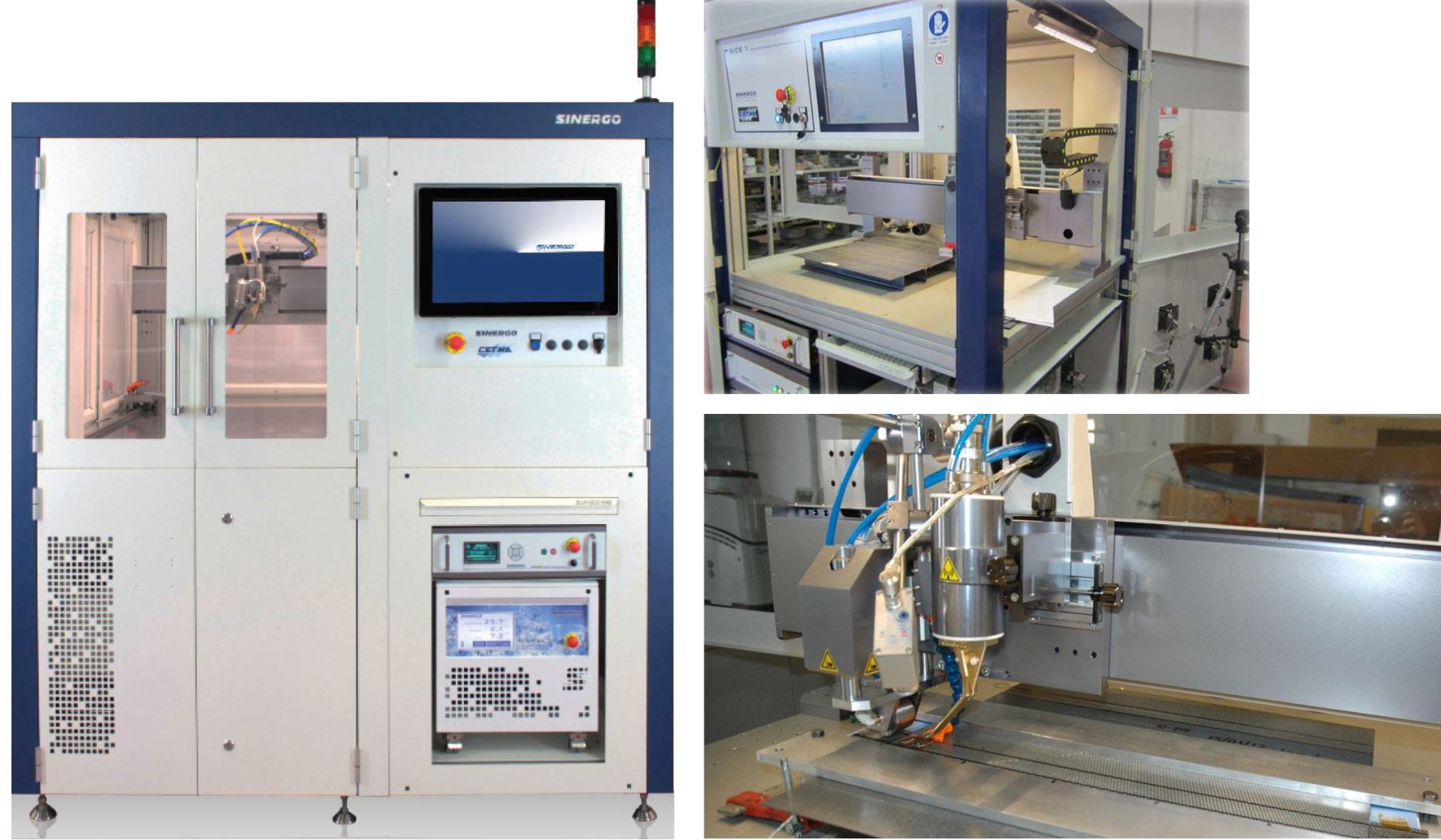
Soldadura por inducción como habilitador clave
Lagraña destaca que CETMA jugó un papel clave no solo en la producción de piezas para KEELBEMAN, sino también en el montaje del demostrador utilizando su máquina y tecnología de soldadura por inducción patentada. Esta soldadura se desarrolló originalmente en el primer proyecto ECO FAIRS del programa Clean Sky (2011-2014), junto con el moldeo por compresión isotérmico y no isotérmico de las estructuras de TPC que se muestran arriba. En ECO FAIRS, CETMA utilizó todas estas tecnologías para producir un prototipo de demostrador basado en el panel superior existente (panel de piel reforzado con largueros) de una cola de helicóptero Agusta Westland, así como un demostrador de carenado de esponja curvo. Aunque estos se fabricaron con CETEX (proporcionado por TenCate, ahora Toray Advanced Composites) T300 3K 5HS textil de fibra de carbono con película de PPS (sulfuro de polifenileno) de doble cara, CETMA también demostró su eficacia en la soldadura por inducción con compuestos de PEEK y PEI.
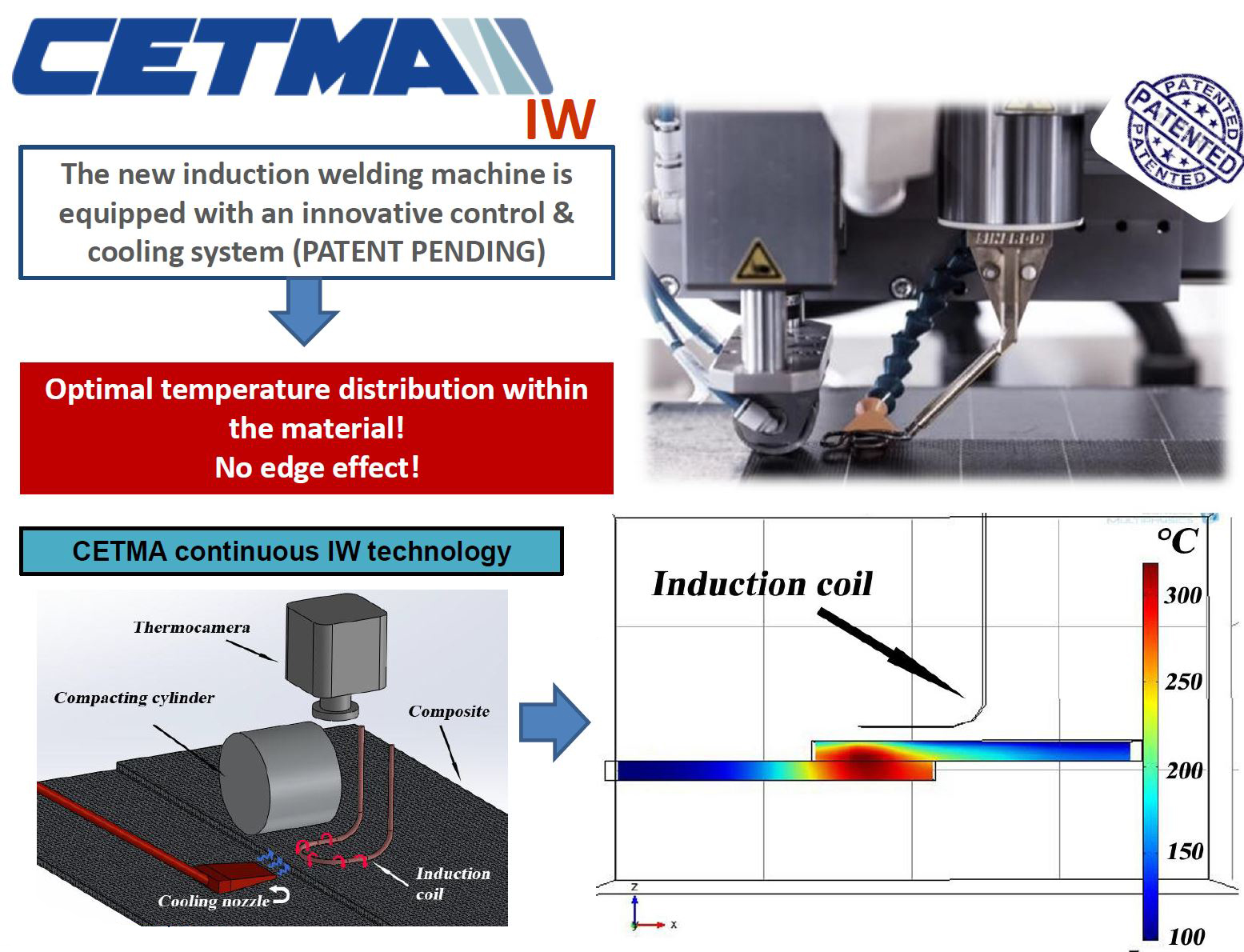
CETMA seleccionó la soldadura por inducción (IW) como la más prometedora de las técnicas de soldadura de compuestos termoplásticos y trabajó con el especialista en ingeniería electrónica y soldadura SINERGO srl (Valdobbiadene, Treviso, Italia) para desarrollar una nueva máquina de soldadura por inducción. La máquina SICE 1 WIDE basada en pórtico ofrecida por SINERGO (ver imagen a continuación) es capaz de soldar continuamente piezas de calidad aeroespacial de hasta 1 metro por 1 metro. Incluye un sistema de control robusto para asegurar que se logren distribuciones de temperatura optimizadas dentro de los materiales que se sueldan. La máquina está equipada con un cilindro enfriado para aplicar presión de consolidación y con un sistema de enfriamiento por aire para eliminar el calor donde sea necesario, como en los bordes, donde el flujo de las corrientes parásitas eléctricas inducidas está restringido, lo que resulta en una alta densidad de corriente y sobrecalentamiento. . También es posible instalar el cabezal de soldadura por inducción CETMA en un brazo robótico de 6 ejes para soldar formas geométricamente complejas.
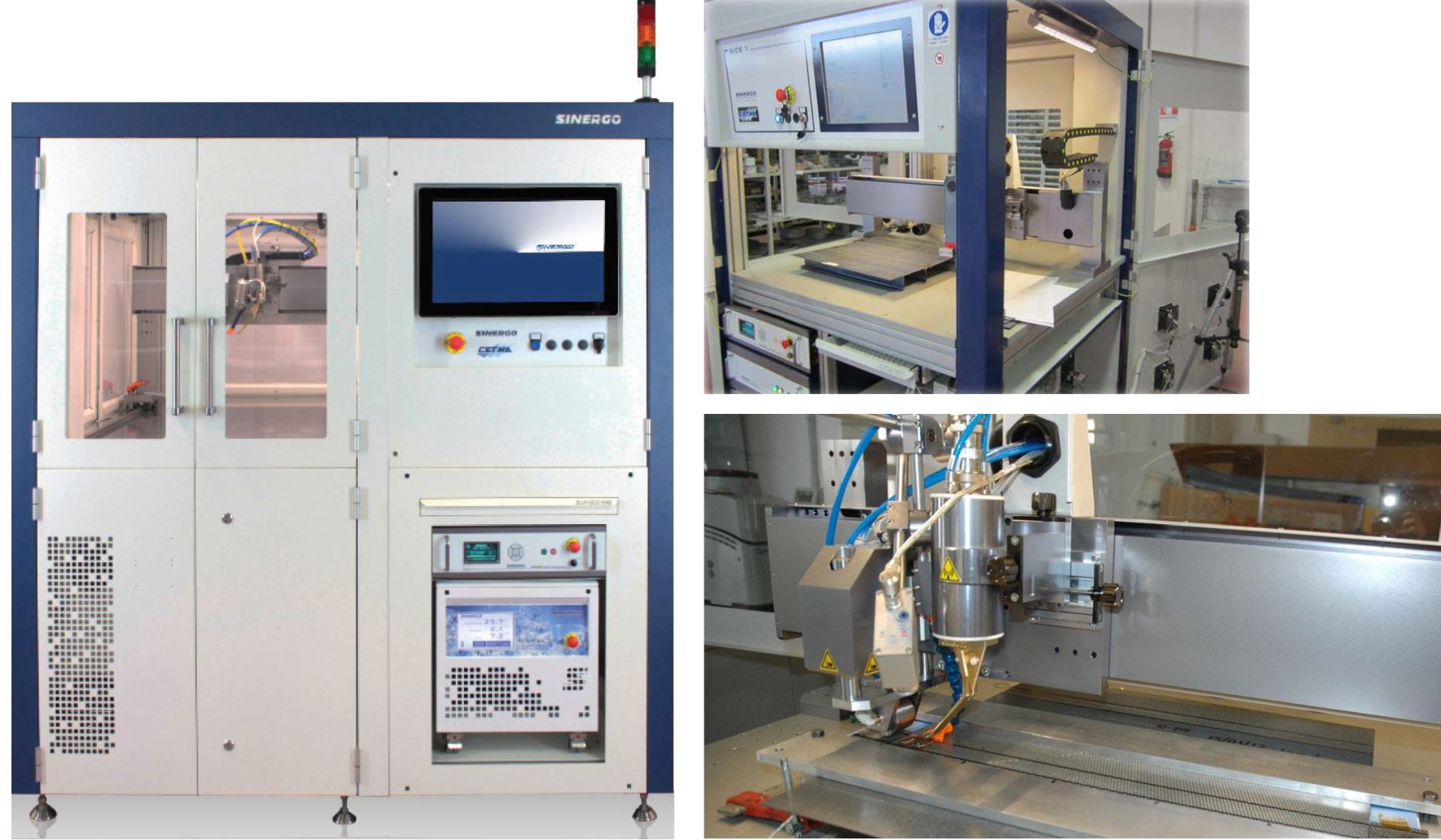
CETMA también ha desarrollado la capacidad de optimizar su proceso de soldadura por inducción mediante el uso de herramientas de simulación, realizando análisis numéricos utilizando el software COMSOL Multiphysics (COMSOL Inc., Burlington, Mass, EE. UU.) De modelado de elementos finitos (FEM). Verificó estos modelos a través de una gran cantidad de pruebas físicas. CETMA confirmó sus parámetros de proceso optimizados mediante pruebas de una sola vuelta en cupones soldados, en los que los valores de resistencia al corte estaban muy cerca del máximo informado en la literatura. En particular, estos también fueron mucho más altos que los valores máximos cuando se usaron adhesivos estructurales, dice CETMA.
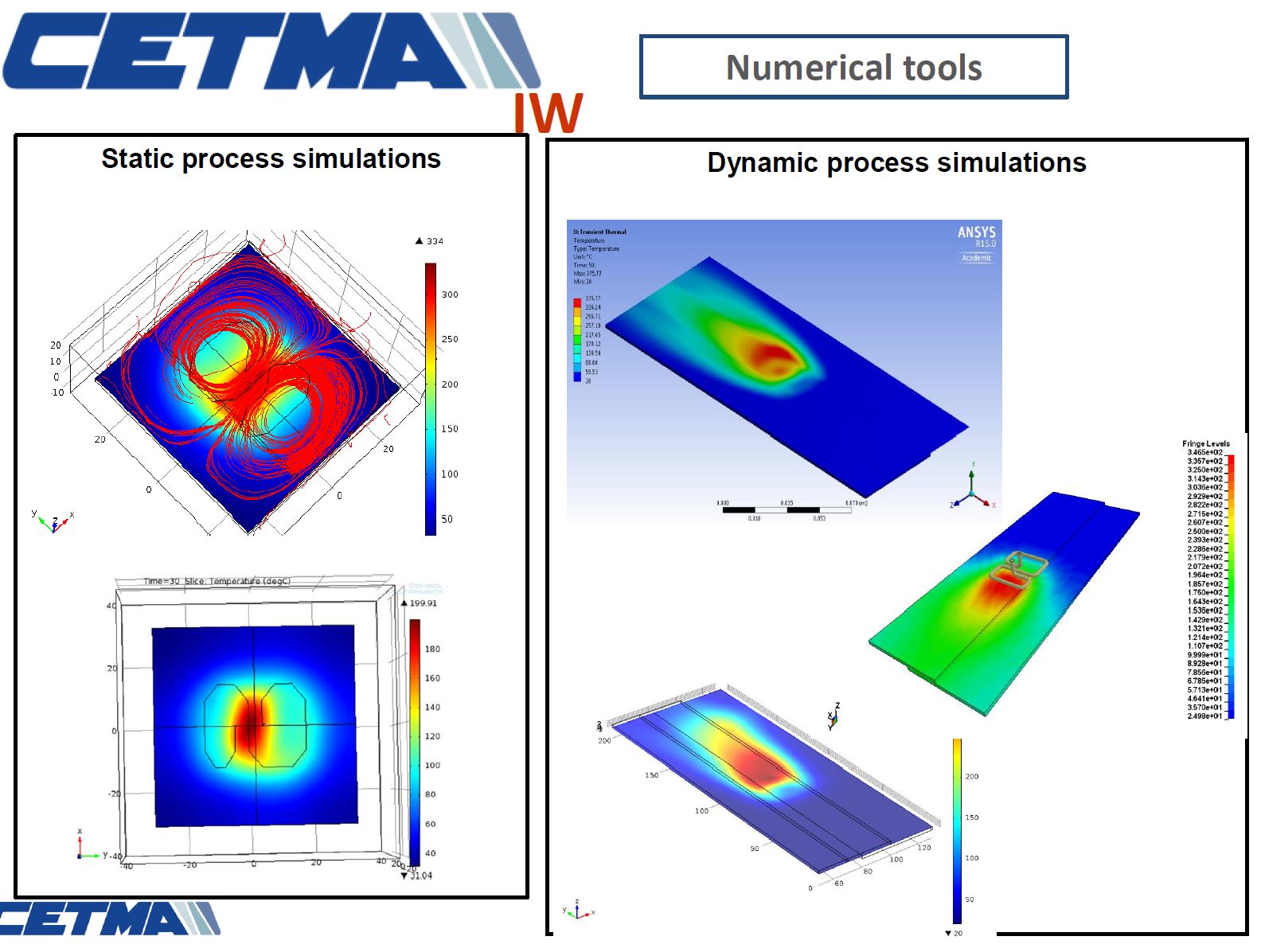
CETMA ha demostrado su capacidad de soldadura para una amplia variedad de materiales, incluida la fibra de carbono tejida y UD, así como PEEK, PEI, PEKK, PP, PA6, PA12 e incluso soldar a CF / epoxi utilizando un híbrido termoplástico de PVB (polivinil butiral). capa para la transición del sustrato termoestable a la cara termoplástica para soldar. (Gran parte de los detalles de esta sección se obtuvieron de la presentación de competencias CETMA y la Informe final de CORDIS para ECO FAIRS.) CETMA solicitó una patente europea en 2014 y los inventores Silvio Pappada y Andrea Salomi recibieron la patente EP2801472A1 en 2016. CETMA ha publicado numerosos artículos y presentaciones sobre esta tecnología, que incluyen:
- "Simulaciones de elementos finitos para apoyar el desarrollo de tecnologías fuera de autoclave", A&D, 11-12 de octubre de 2012
- "Simulaciones de elementos finitos para admitir la soldadura por inducción continua de compuestos de carbono y PPS", SEICO 13, 11-13 de marzo de 2013 "París"
- “Desarrollo de una nueva máquina de soldadura por inducción para compuestos termoplásticos en el sector aeroespacial”, XXII Conferencia de la Asociación Italiana de Aeronáutica y Astronáutica en Nápoles, 9-12 de septiembre de 2013
- “Soldadura por inducción en el sector aeroespacial”, TPRC, Consorcio europeo de compuestos termoplásticos, reunión web, diciembre de 2013.
- "Pruebas a gran escala de componentes termoplásticos para el sector aeroespacial", SEICO 14, 10-11 de marzo de 2014 "París"
- “Nuevo equipo de soldadura por inducción para el sector aeroespacial”, revista JEC, No. 87, marzo de 2014, págs. 89-91.
Estado de KEELBEMAN y ruta a seguir
Airbus visitó CETMA en diciembre para ver la soldadura final de la sección de demostración de 1 metro, y el equipo de KEELBEMAN también realizó una revisión final del nivel de preparación tecnológica (TRL). “Estamos obteniendo buenos resultados y estamos madurando la tecnología de TRL 3 a TRL 4”, dice Lagraña. Los próximos pasos podrían incluir un mayor desarrollo de TRL 6 y la producción de una viga de quilla a gran escala que se instalará en uno de los demostradores de Clean Sky 2, como el fuselaje central inferior de tamaño completo WP 2.3.2, pero esto aún no se ha realizado. decidido.
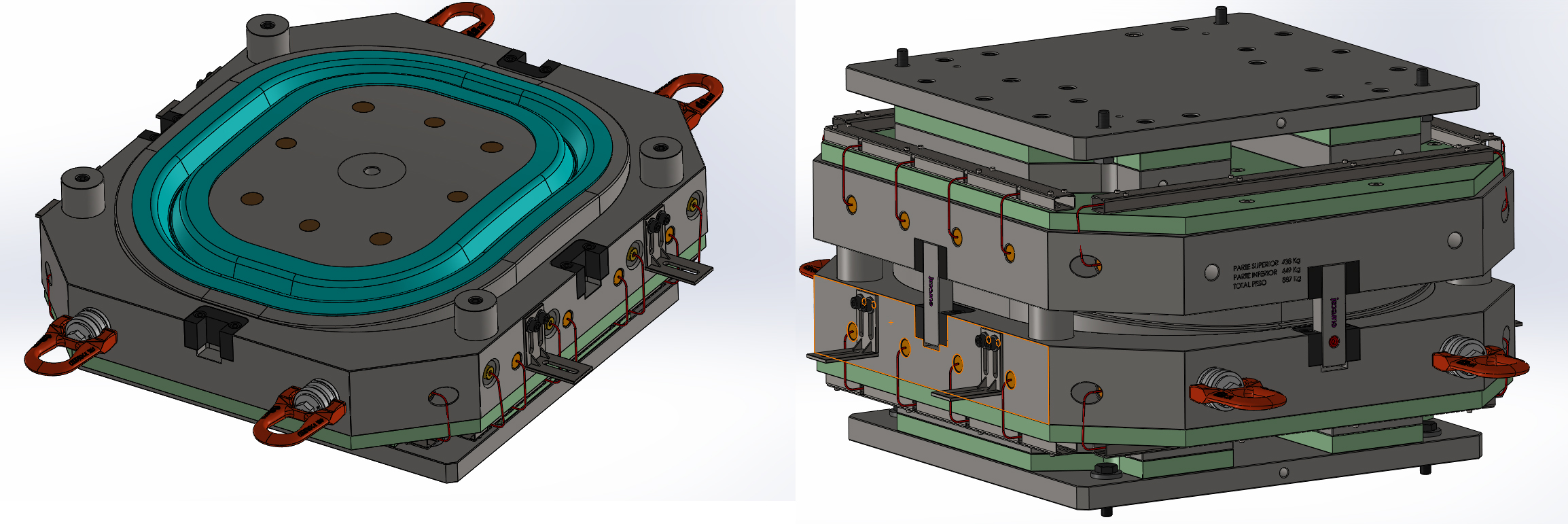
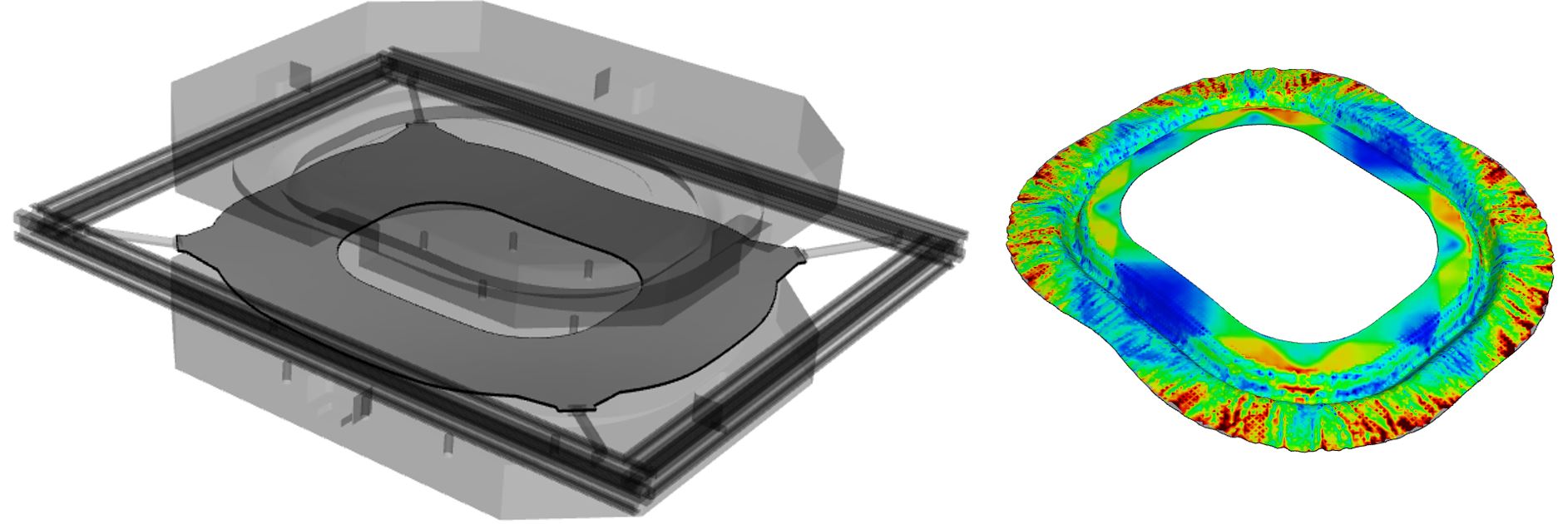
Proyecto WINFRAME 4.0 para marcos de ventanas TPC
Otro programa de compuestos termoplásticos (TPC) para EURECAT es WINFRAME 4.0, con el objetivo de desarrollar y fabricar 24 marcos de ventanas para un demostrador de tierra integrado en el fuselaje / cabina de una aeronave regional (ver explicación de los desarrollos de Clean Sky 2 para Regional Aircraft y Full Demostrador innovador de cabina de pasajeros y fuselaje a escala debajo). Los socios de WINFRAME 4.0 incluyen:
- Compañía aeroespacial multinacional Leonardo (Roma, Italia) como administrador de temas
- EURECAT
- Sofitec.
“El método que estamos usando puede producir un marco de ventana cada 10 minutos”, dice Lagraña. Los pasos de producción incluyen:calentar los espacios en blanco de laminado TPC en un horno, trasladarlos a un molde, cerrar el molde en una prensa, aplicar calor y presión durante 10-20 minutos y desmoldar las piezas terminadas. “Este enfoque no solo logra ciclos más cortos que el moldeado líquido, sino también herramientas mucho menos costosas”, agrega. “El proceso es bien conocido en la industria automotriz, es el moldeo por compresión en una configuración altamente automatizada lo que aumenta la calidad de la pieza, pero los materiales aeroespaciales utilizados son diferentes, en este caso un PPS reforzado con fibra de carbono y fibra de carbono de Toray. Compuestos avanzados (anteriormente TenCate). Al final de este proyecto, habremos logrado un TRL 6 para estas tecnologías ”, dice Lagraña.
Proyecto COFRARE:marcos en C RTM y bridas de seguridad termoplásticas
El proyecto COFRARE 2020 es una extensión del proyecto COFRARE 2.0 inicial:
Clean Sky 2 - JTI-CS2-2015-CFP02-AIR-02-16. “Desarrollo de procesos para la fabricación de marcos compuestos con alta tasa de producción y bajo costo” Duración del proyecto:2016 a 2018.
El objetivo del proyecto Clean Sky 2 COFRARE 2.0 era desarrollar un proceso de fabricación competitivo y factible para marcos compuestos de fibra de carbono para su uso en un fuselaje basado en paneles compuestos para aviones regionales. Socios incluidos:
- Proveedor aeroespacial Tier 1 y empresa de ingeniería / industrialización con sede en Nápoles DEMA (Design Manufacturing SpA, Somma Vesuviana, Italia)
- EURECAT
- LGAI Technological Center S.A., una división de Applus + Laboratories en Barcelona, España proporcionó pruebas.
El objetivo del proyecto COFRARE 2020 de próxima generación es fabricar marcos compuestos a gran escala y tirantes de cizalla para ser utilizados en el demostrador terrestre integrado de cabina / fuselaje Clean Sky 2. Este demostrador está organizado dentro del IADP de aviones regionales de Clean Sky 2 (Plataforma de demostradores de aviones innovadores) y se detalla en la Sección 5.2.2 del documento del Programa técnico conjunto de marzo de 2015:
“ Los aviones regionales son un elemento clave de Clean Sky a través de un ITD (Demostrador de tecnología integrada) dedicado: Green Regional Aircraft (GRA) , proporcionando los pilares fundamentales de un sistema de transporte aéreo que respete el medio ambiente, garantice una movilidad segura y sin problemas y construya el liderazgo industrial en Europa. En Clean Sky 2 , … Los objetivos de demostración del IADP Regional Aircraft son mucho más complejos, completos y desafiantes que los del actual Clean Sky Proyecto GRA , que se vio obligada a trabajar dentro de las limitaciones de tiempo y presupuesto. … ”
El Programa Técnico Conjunto de 2015 describe el desarrollo de Aeronaves Regionales para incluir dos bancos de pruebas voladores y cinco grandes demostradores terrestres integrados. Este último incluye el demostrador de cabina de pasajeros y fuselaje innovador a gran escala :“El fuselaje será una demostración a gran escala de tecnologías para materiales compuestos, estructuras y fabricación con el objetivo de [lograr] la reducción de peso y costos y minimizar el impacto ambiental a través del diseño ecológico y la optimización del consumo de energía a lo largo del ciclo de vida (hacia un impacto cero) ”.
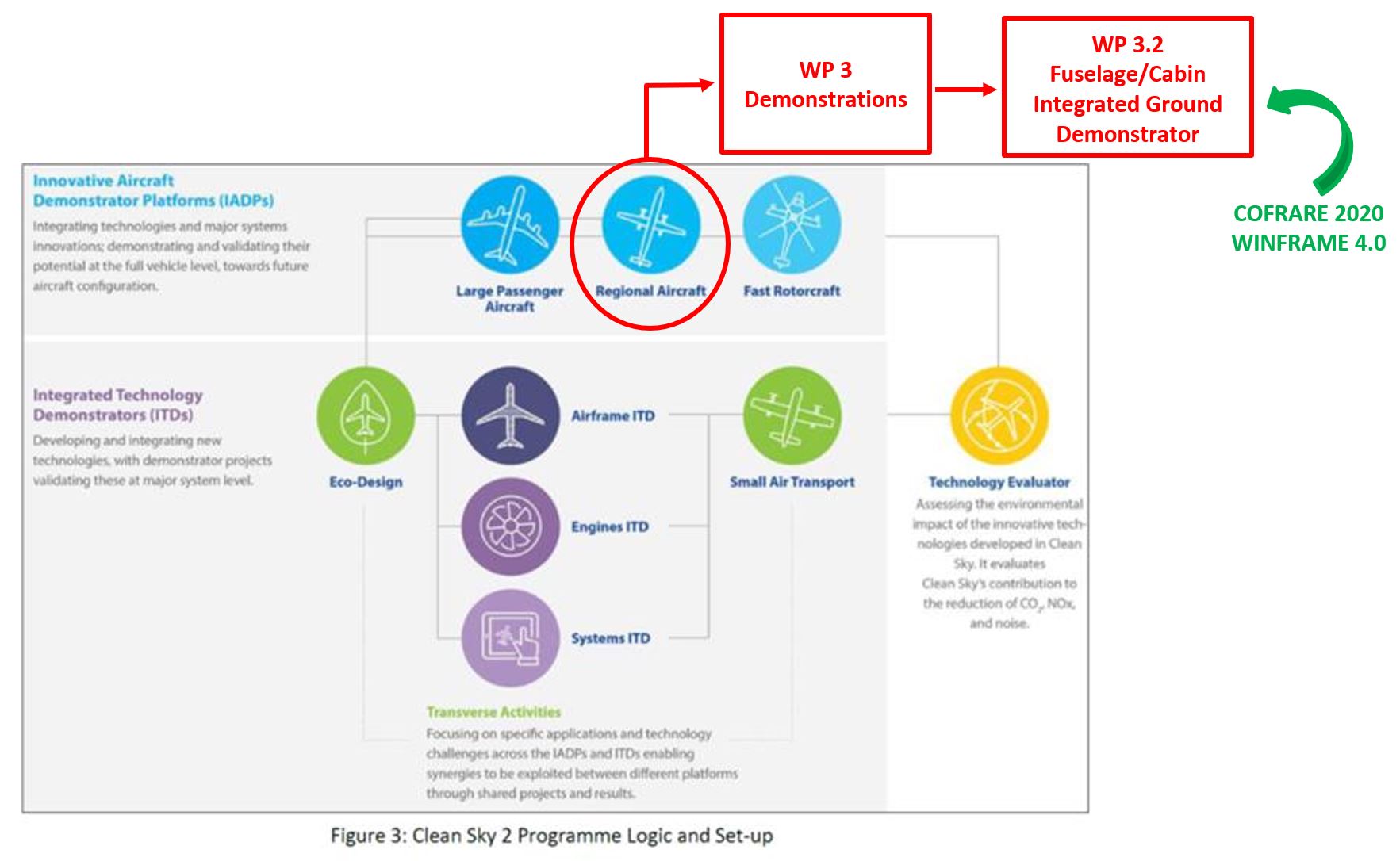
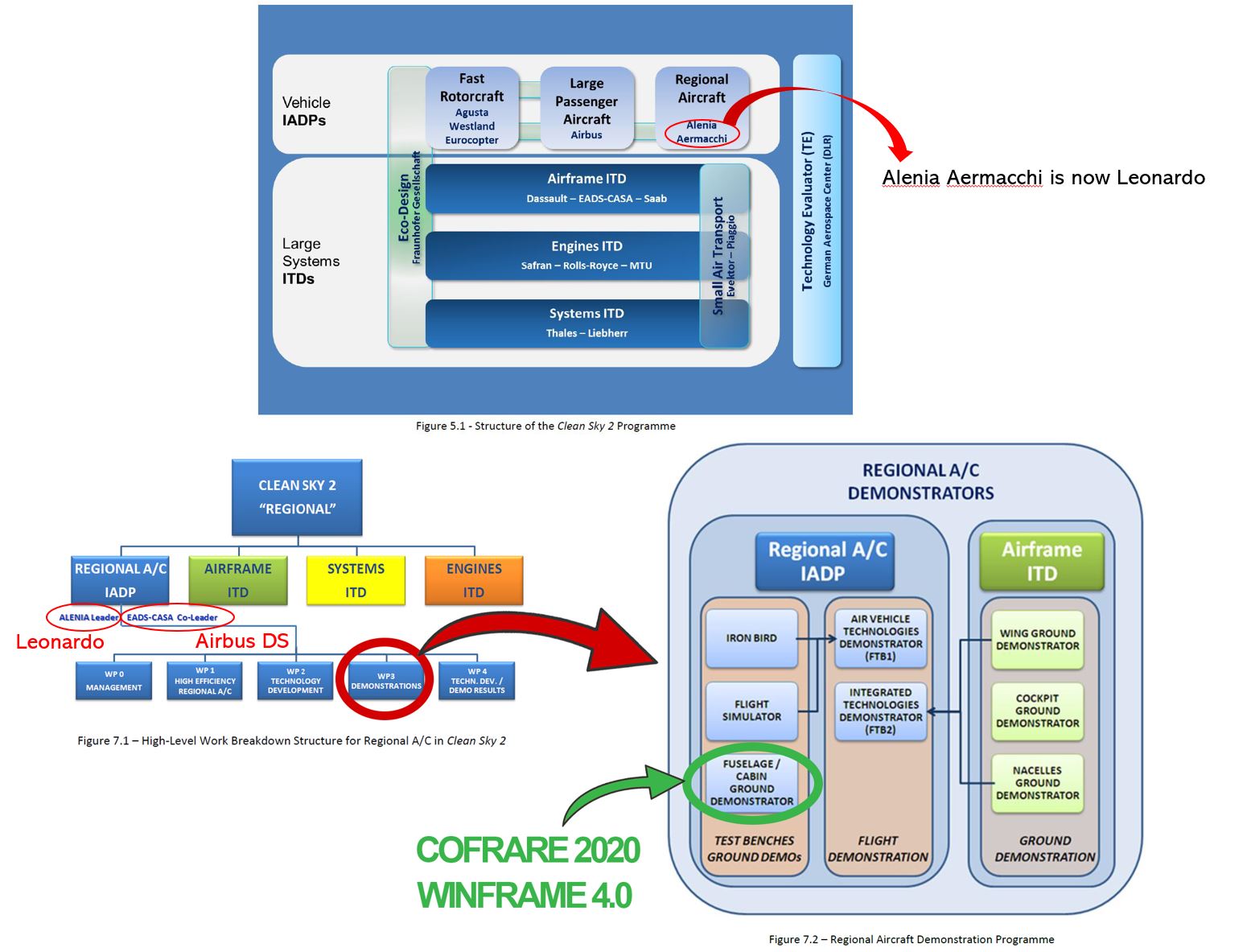
Los socios del proyecto COFRARE 2020 incluyen:
- Leonardo como administrador de temas
- EURECAT
- DEMA
- Fabricación de componentes y conjuntos de aeronaves A. Abete (Nola / Marigliano, Italia).
“En COFRARE 2020, estamos fabricando marcos de fuselaje con RTM (moldeo por transferencia de resina), que se integrará en el demostrador de fuselaje”, explica Lagraña. "Estamos utilizando la tecnología Ziplus de Shikibo (Osaka, Japón) que produce preformas que son adecuadas para la inyección de resina". Shikibo Ltd. es parte de Composite Alliance Corp. (Dallas, Texas, EE. UU.) Y ofrece una variedad de tecnologías de preformado textil.
Un aspecto interesante de este programa es el uso de sensores de Synthesites (Uccle, Bélgica) para el monitoreo en tiempo real de la llegada de resina, temperatura, presión, Tg y curado. “Los sensores están ubicados en áreas específicas de la pieza compuesta y la herramienta RTM para optimizar la estrategia de inyección de resina”, apunta Lagraña. La inyección se logra mediante un sistema altamente automatizado suministrado por ISOJET (Corba, Francia), que también forma parte de Composite Alliance Corp.Los sensores Synthesites son sensores dieléctricos, pero a diferencia de la mayoría de los análisis dieléctricos (DEA), que se basan en corriente alterna (CA) , Synthesites utiliza corriente continua (CC). “Nuestros sensores funcionan bien con materiales de alta resistividad como las resinas y debido a que estamos aplicando un solo voltaje, no tenemos que analizar múltiples frecuencias, pero logramos una alta precisión, incluso al final del curado”, explica el director de Synthesites, Dr. Nikos Pantelelis.
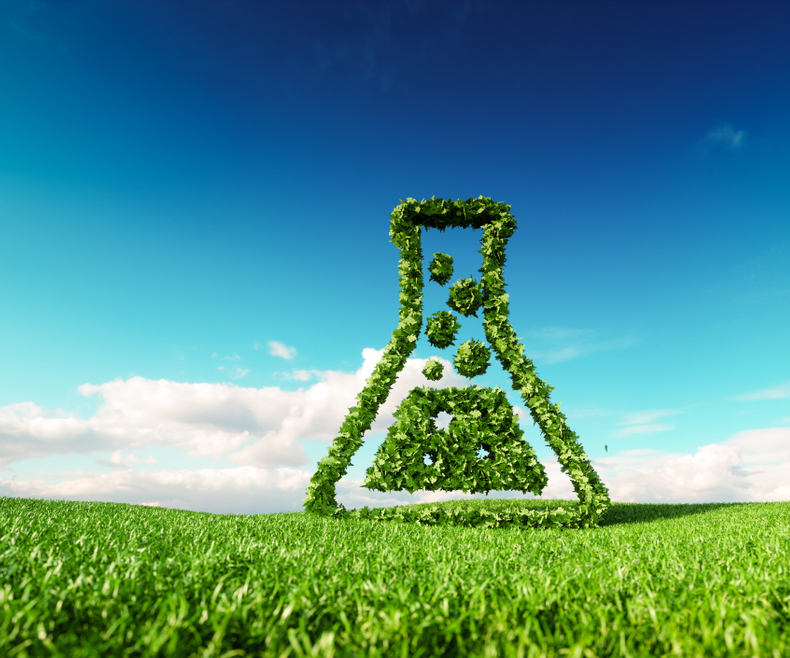
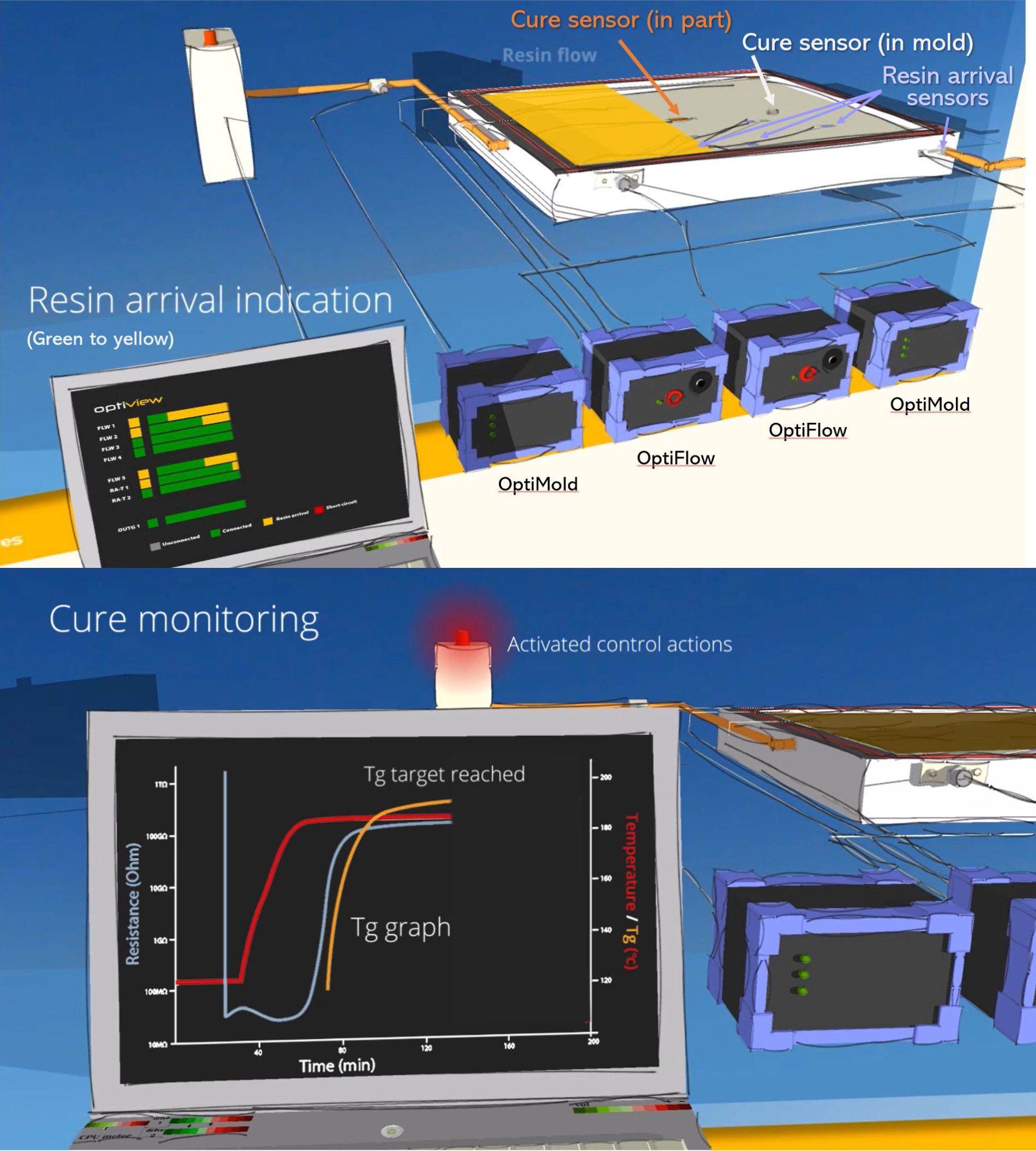
“Conocimos a Synthesites en una conferencia de SAMPE en 2011”, recuerda Lagraña. “Hablaron de sensores para acortar el ciclo de curado. Estamos explorando cómo automatizar las preformas para los marcos del fuselaje e incluso utilizando un procesamiento más rápido con HP-RTM (RTM de alta presión), pero aún así se encuentra en un tiempo de proceso de 3-4 horas. Sin embargo, con Synthesites, hemos reducido el ciclo de curado en un 50 por ciento al monitorear la Tg. Ahora estamos probando propiedades. Estos sensores pueden funcionar a alta presión, pero en nuestro procesamiento RTM, usamos solo 8 bar de presión ”.
Los sensores dieléctricos de CC de Synthesites, el sistema de monitoreo de flujo de resina líquida OptiFlow y el sistema de monitoreo de curado OptiMold han sido demostrados en producción por varios fabricantes de palas de viento. También son utilizados por Bombardier Aerospace (Belfast, Reino Unido) para producir el ala moldeada de compuesto líquido para la Serie C, ahora Airbus 220. El Centro Aeroespacial Alemán (DLR, Stade, Alemania) ha demostrado una reducción del ciclo de curado de hasta un 50% con ambos autoclave preimpregnado y RTM, mientras que el Centro Nacional de Compuestos (NCC, Bristol, Reino Unido) ha demostrado que incluso para resinas altamente reactivas, los cálculos de Tg en tiempo real hechos a partir de mediciones de sensor de temperatura y resistividad de la resina son tan precisos como la Tg medida a partir de paneles curados. utilizando calorimetría diferencial de barrido (DSC).
Unión de marcos con tirantes de TPC
Otra parte clave de COFRARE 2020 es un método de producción de mayor volumen para producir los cientos de tirantes y soportes que se requieren para unir los marcos en C del fuselaje RTM a los paneles compuestos del fuselaje. “Estamos desarrollando 255 geometrías diferentes para brackets de compuestos termoplásticos producidos por moldeo por compresión”, dice Lagraña. (Tenga en cuenta que GKN Fokker tiene varios proyectos Clean Sky 2 en los que producirá soportes TPC para el demostrador de fuselaje multifuncional en el IADP de aviones de pasajeros grandes; este trabajo en COFRARE 2020 es para aviones regionales más pequeños). El método básico se muestra a continuación, utilizando herramientas de acero combinadas y una prensa calentada. “El costo de estas herramientas de moldeo por compresión es de solo 2.000 euros, lo que es muy asequible en comparación con las herramientas RTM”, agrega. "El estampado también logra tiempos de ciclo muy cortos".
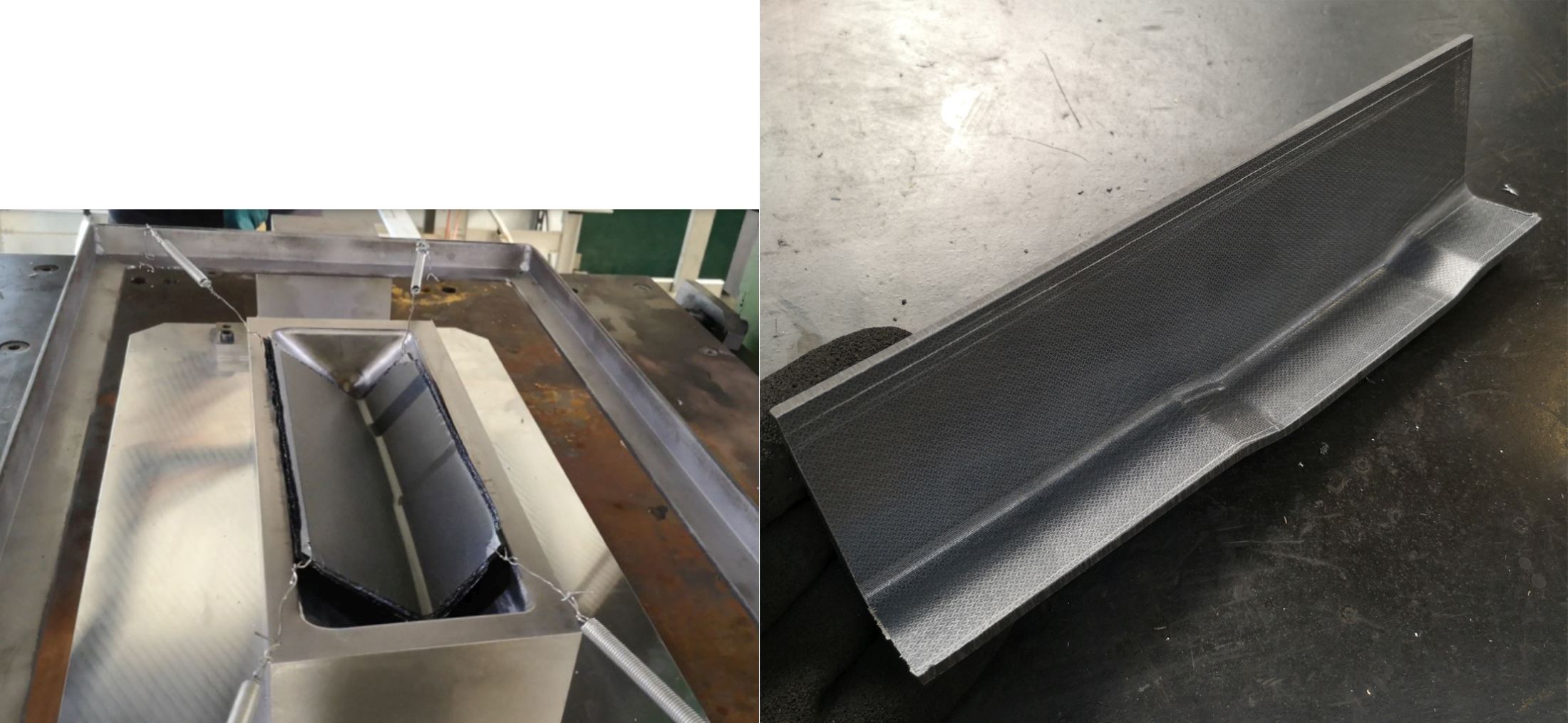
EURECAT invierte en permanecer a la vanguardia del desarrollo de tecnología de composites, dice Lagraña. “Creemos que la presión por un medio ambiente limpio aumentará drásticamente el uso de materiales compuestos en todo el transporte, y que la asequibilidad y el rendimiento irán de la mano. Es por eso que nos enfocamos en tecnologías automatizadas fuera de autoclave para ofrecer a nuestros clientes ”.
Estén atentos a mi próximo blog sobre los proyectos Clean Sky 2 STUNNING y MECATESTERS, que discutirán el desarrollo de soportes de TPC soldados para el Demostrador de Fuselaje Multifuncional y una caracterización completa de PAEK para este proyecto. También escribiré en un blog sobre Synthesites con más detalle, así como más sobre los desarrollos de CETMA en compuestos. ¡2020 va a ser un año muy interesante para los composites!
Resina
- Sándwich de nido de abeja termoplástico para sobremoldear en compuestos más delgados y livianos
- Personalización de sensores ultrasónicos para la optimización y el control de procesos compuestos
- Resinas epoxi reprocesables, reparables y reciclables para composites
- Combinación de medidas dieléctricas de CA y CC para el control del curado de compuestos
- Solvay y Leonardo lanzan un laboratorio de investigación conjunto para compuestos termoplásticos
- Cintas termoplásticas multicapa, AFP e infusión de resina para composites más democráticos
- Puerta termoplástica por primera vez para compuestos automotrices
- LANXESS amplía la capacidad de producción de compuestos termoplásticos continuos reforzados con fibra
- TPAC y TPRC desarrollan un proceso de reciclaje de compuestos termoplásticos
- Soldadura de compuestos termoplásticos
- El consorcio de compuestos termoplásticos tiene como objetivo la producción de alto volumen para la industria automotriz y aeroespacial