Swinburne University y CSIROs Industry 4.0 Testlab para la fabricación de aditivos compuestos
Swinburne University of Technology (Melbourne, Australia) está estableciendo un laboratorio de pruebas de Industria 4.0 para la fabricación de aditivos compuestos en asociación con la Agencia Nacional de Ciencia de Australia, la Organización de Investigación Científica e Industrial de la Commonwealth (CSIRO, consulte "Desarrollo de mayor calidad, mayor resistencia, menor costo de las fibras de carbono ”). La instalación se encuentra actualmente en construcción en el sitio de Clayton de CSIRO y se completará en octubre de 2020.
Con el respaldo del gobierno federal australiano, este laboratorio de pruebas de Industria 4.0 para materiales compuestos es uno de los seis en una red nacional australiana, similar a Labs Network Industrie 4.0 en Alemania. Este Testlab es la primera instalación nacional en la red estatal donde el objetivo es permitir que las pequeñas y medianas empresas (PyMEs) prueben nuevas tecnologías y modelos de negocios creados por la Industria 4.0, explorando aspectos desde el diseño hasta la viabilidad económica, en un contexto precompetitivo. Entorno con mínimo riesgo técnico y financiero. Cada laboratorio de pruebas tiene un enfoque de producto distintivo. Para Swinburne, esta es la fabricación aditiva de compuestos.
“El laboratorio de pruebas Industry 4.0 para compuestos en Swinburne proporcionará un proceso a escala piloto para promover las capacidades de fabricación de Australia”, dice Bronwyn Fox, vicecanciller adjunto de investigación y empresa de la Universidad de Swinburne. Fox se unió a Swinburne en 2015, asumiendo inicialmente el papel de director de Factory of the Future y luego director del Manufacturing Futures Research Institute de la universidad. Antes de unirse a Swinburne, fue directora de investigación de Carbon Nexus en la Universidad de Deakin.
"Testlab de Swinburne demostrará las características de la producción de compuestos digitales en un entorno inmersivo", dice Fox. “Los procesos a escala piloto se controlarán digitalmente desde el diseño y la optimización de la pieza hasta el producto terminado. También crearemos un gemelo digital del proceso y ampliaremos los límites de la puesta en servicio virtual ".
Este hub de compuestos 4.0 se alojará en un edificio nuevo y personalizado. “El Testlab conjunto CSIRO / Swinburne se centra en un proceso pionero en el mundo para la fabricación aditiva de compuestos reforzados con fibra de carbono a escala industrial”, dice el Dr. Marcus Zipper, director ejecutivo de la división Future Industries de CSIRO. “Esto hace que su ubicación, en el corazón del recinto de fabricación aditiva de Clayton, encaje perfectamente. En CSIRO, nuestro objetivo es crear oportunidades para las pymes y el ecosistema de innovación en general, y este Testlab es otro ejemplo de eso ".
Socios y proceso
Hay muchos socios clave en Industry 4.0 Testlab for Composites, con Siemens Australia (Bayswater, Victoria) fue uno de los primeros en extender una subvención de software de digitalización de $ 135 millones a Swinburne en 2017. Esto proporciona a Composites 4.0 Testlab un conjunto de software avanzado de gestión del ciclo de vida del producto (PLM), así como Siemens basado en la nube, plataforma abierta de Internet de las cosas (IoT), MindSphere.
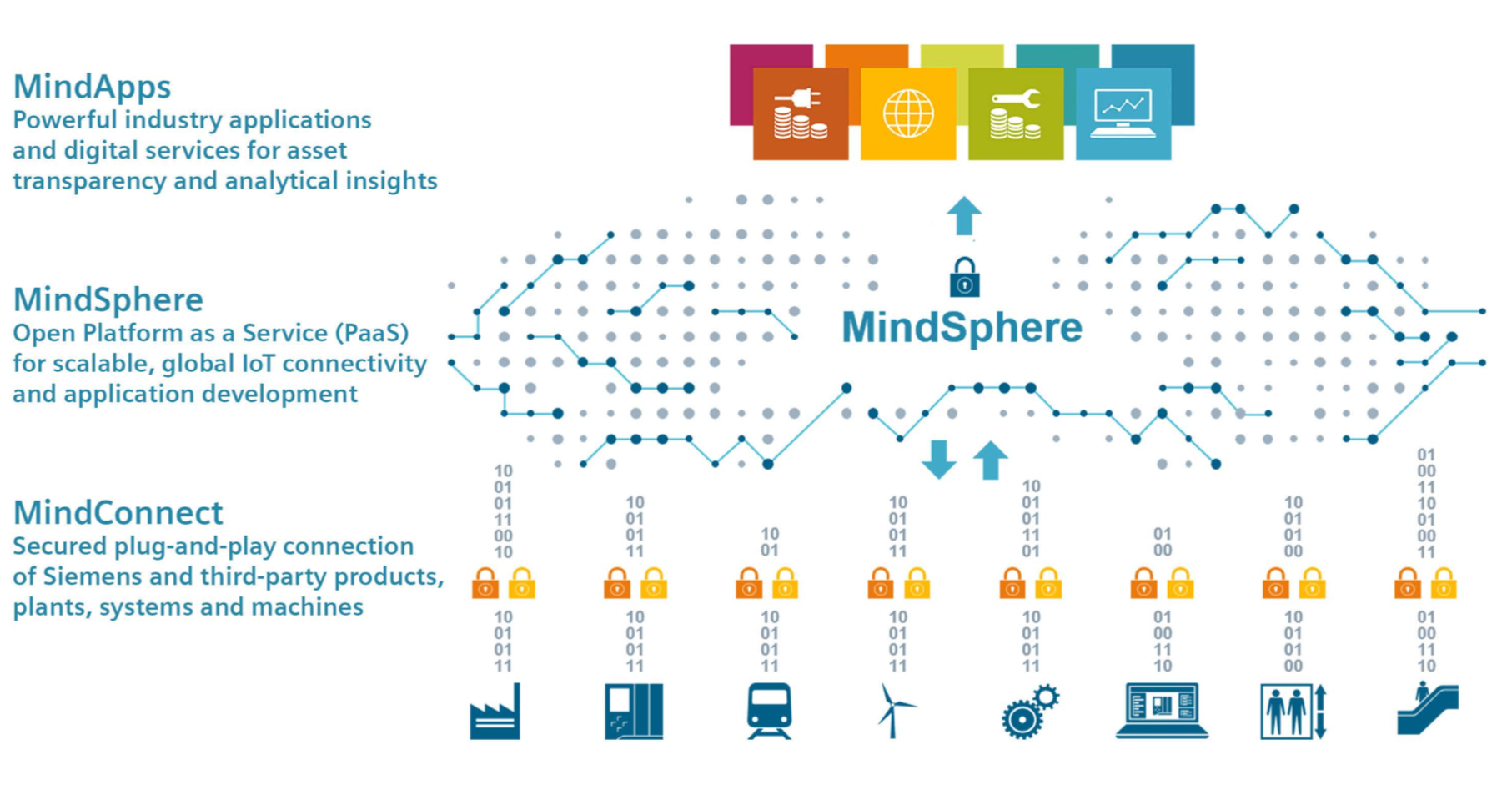
Según una presentación de Siemens Australia, en agosto de 2019, había aproximadamente 500 aplicaciones / ofertas digitales dentro de MindSphere y 1,4 millones de dispositivos y sistemas conectados. "MindSphere permitirá que los equipos de una amplia gama de fabricantes se comuniquen entre sí", explica Fox en su presentación ICCM22, "Un enfoque de la industria 4.0 para la impresión 3D de materiales compuestos". Este documento describe cómo funcionará el laboratorio de pruebas Swinburne Industry 4.0:
“Los sensores ... permitirán que cada etapa de la línea de producción recopile una gran cantidad de datos de proceso. Esta información se almacenará en una nube local segura y también se utilizará inmediatamente para enviar y retroalimentar los datos de producción a otras máquinas de la línea, lo que permitirá un proceso de producción autoadaptable.
La línea propuesta ... está diseñada para permitir la inspección del producto después de cada etapa del proceso de fabricación. Los datos de inspección también se almacenarán en la nube local. El análisis de los grandes conjuntos de datos almacenados en la nube puede conducir al descubrimiento de correlaciones nuevas e inesperadas entre el estado del producto terminado y los parámetros de las diferentes etapas del proceso de fabricación, que a su vez pueden utilizarse para optimizar el producto ”.
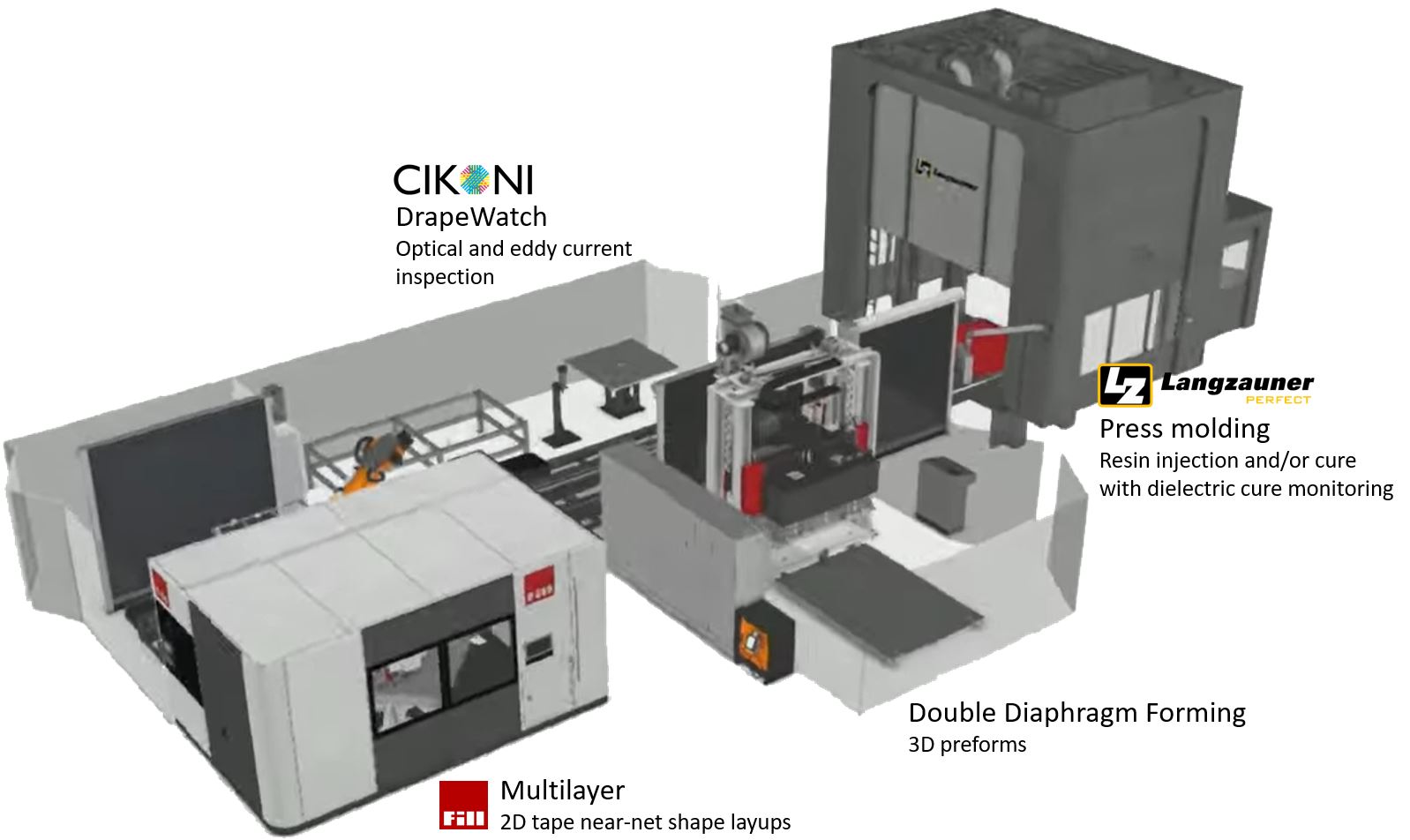
Fox también señala que las líneas de fabricación de compuestos de la Industria 4.0 no se pueden comprar listas para usar. Por lo tanto, Swinburne desarrolló una red de proveedores y usuarios finales para informar el diseño y desarrollo de sus instalaciones y equipos de Composites 4.0 Testlab. Los socios que suministran componentes clave incluyen:
LLENAR (Gurten, Austria) ha suministrado el sistema multicapa, que apila cintas de fibra unidireccionales cortadas y orientadas con precisión en formas casi de red de hasta 1,6 por 1,6 metros de tamaño. Las formas de red cercanas al uso de cinta reducen el desperdicio de más del 60% a menos del 10%. Las cintas se depositan desde carretes sobre una mesa giratoria, con una capa completada cada 15 segundos. Fox señala que la máquina multicapa de Fill puede colocar cintas de preimpregnado termoendurecible y towpreg, así como fibra seca y termoplástico de bajo derretimiento, como poliamida (PA). Hay I + D en curso para termoplásticos de alto punto de fusión, como la polieterétercetona (PEEK) y la polietercetonacetona (PEKK). “La máquina multicapa también permite materiales híbridos, como mezclar vidrio y fibras de carbono y mezclas con fibras naturales, etc.”, agrega.
Paso rápido (Sydney, Australia) es el mayor fabricante independiente de compuestos avanzados de grado aeroespacial de Australia, que ofrece una amplia experiencia en compuestos curados en autoclave y fuera de autoclave (OOA). El sistema OOA patentado de Quickstep, Qure, y su versión de alto rendimiento para aplicaciones aeroespaciales, AeroQure, es un proceso de fabricación de compuestos avanzados que ofrece ventajas significativas sobre las técnicas de fabricación tradicionales, como el curado en autoclave, que incluyen:
- Bajo costo de capital para la configuración
- Tiempos de ciclo de curado significativamente más cortos
- Reducción del consumo de energía
- Flexibilidad de diseño para cumplir o mejorar las propiedades del material del producto final
- Capacidad para producir piezas integradas complejas.
Qure utiliza un fluido de transferencia de calor circulante presurizado (HTF) para soportar el molde y calentar y enfriar rápidamente la pieza. El procesamiento de presión más baja (vacío más hasta 2,5 bar) facilita herramientas de menor costo. El calentamiento rápido del molde y el material reduce la viscosidad del proceso, mejorando la liberación de aire y la humectación de la fibra. La viscosidad más baja mejora la adhesión a los núcleos de espuma y alveolares, lo que da como resultado una mayor resistencia al pelado y una reducción del aplastamiento del núcleo durante el curado. El HTF permite un control térmico superior, incluso para laminados gruesos propensos a reacciones exotérmicas.
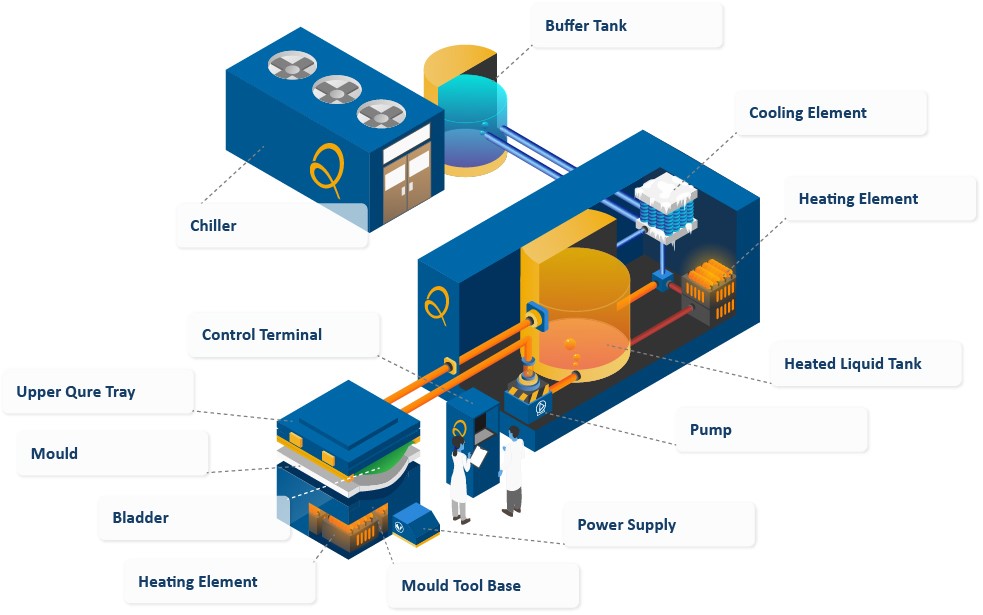
Langzauner (Lambrechten, Austria) está suministrando una prensa automatizada de alta temperatura, con hasta 300 toneladas de fuerza de sujeción que es capaz de realizar múltiples procesos, desde variaciones de moldeo por transferencia de resina (RTM) hasta termoformado. Permitirá la inyección de resina en preformas secas, seguida de curado o moldeo por compresión de preimpregnados termoestables y termoplásticos.
La prensa logra eficiencia / ahorro de energía a través del servohidráulico y la mayor precisión, incluso con carga asimétrica, a través de un solo control de pistón. Un horno de infrarrojos (IR) de alto rendimiento calienta rápidamente los materiales a la temperatura de procesamiento deseada, compensando los diferentes espesores mediante un sistema de control de radiador individual. La transferencia rápida del material precalentado a la estación de prensado está asegurada por un eje lineal. El sistema de calentamiento de placas de alta temperatura puede moldear piezas a temperaturas de al menos 400 ° C, lo que permite el procesamiento de termoplásticos avanzados como la polieteretercetona (PEEK).
La prensa también tiene capacidad para marcos de doble diafragma (consulte el blog de 2020 sobre conformado de doble diafragma). El más alto grado de digitalización y monitoreo está garantizado por un software flexible, robusto y fácil de usar.
NETZSCH (Selb, Alemania) proporcionará tecnología de monitoreo de curado en molde, lo que permitirá el control de la fabricación de compuestos según el comportamiento del material.
Plataine (Israel) ofrece software de digitalización, optimización y gemelos digitales para la fabricación de compuestos que permite el seguimiento de herramientas, piezas y materias primas, la creación de gemelos digitales y el análisis de datos de sensores de máquinas para optimizar la producción de piezas. Plataine tiene una amplia gama de asociaciones con líderes y proveedores de la industria de compuestos, incluido Siemens.
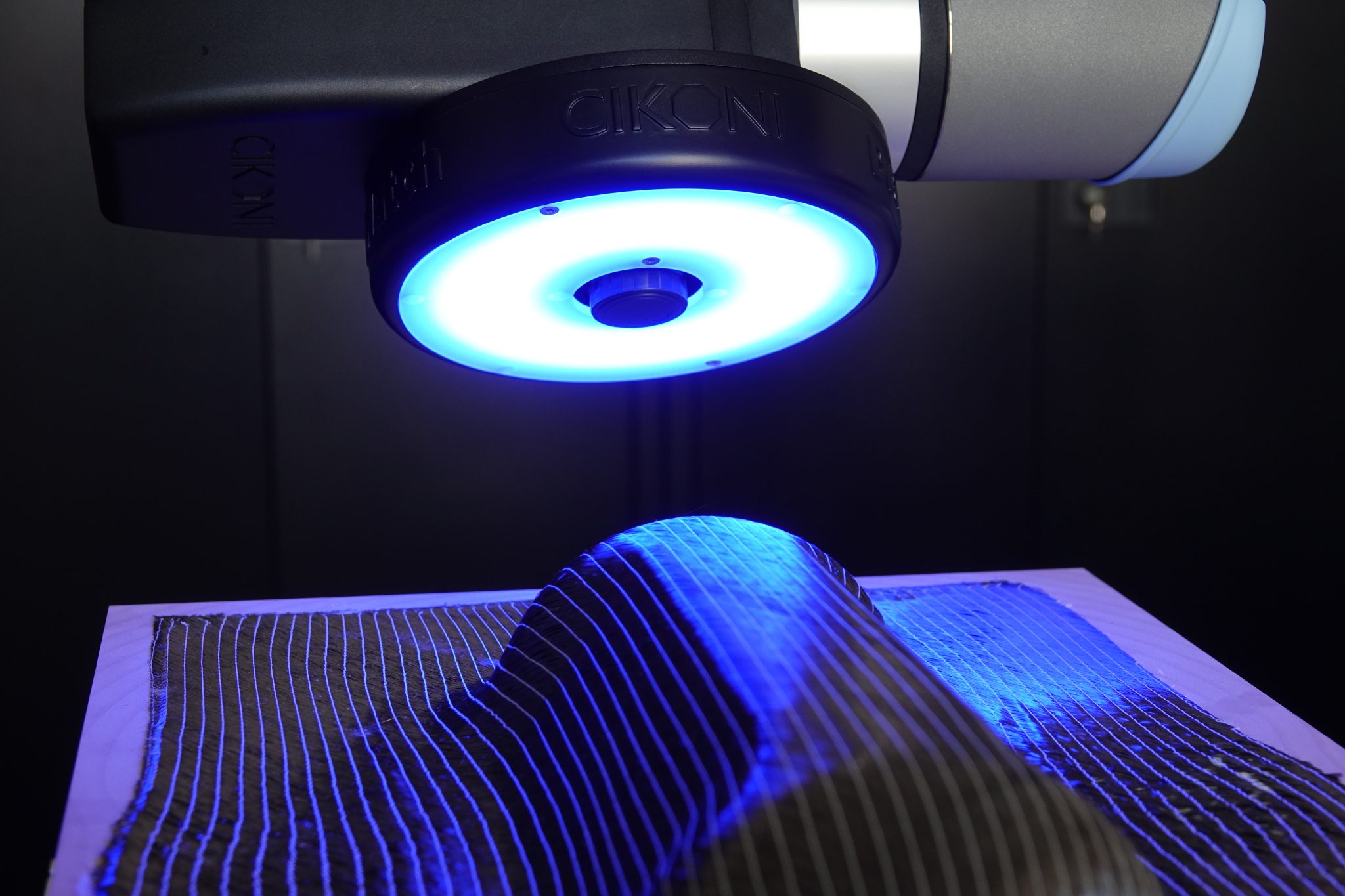
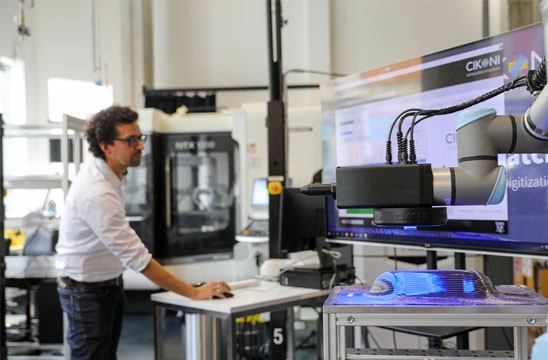
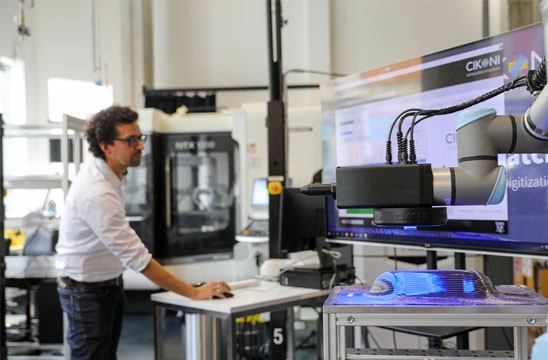
CIKONI (Stuttgart, Alemania) ha suministrado el sistema DrapeWatch para la inspección y digitalización en línea de preformas y piezas consolidadas. Este sistema de análisis 3D basado en robot puede identificar huecos, desalineaciones e irregularidades. Combina un sensor visual para una inspección detallada de la superficie con un sensor EddyCurrent para defectos internos y análisis de material en profundidad. Los datos son analizados por los algoritmos de inteligencia artificial del sistema para proporcionar una detección temprana de defectos, evitando costosas repeticiones. Una interfaz para el análisis de elementos finitos (FEA) permite exportar los resultados del ángulo de la fibra a modelos de simulación para evaluar el impacto de los defectos en el rendimiento de la pieza. El sistema modular también se puede ampliar mediante la integración de dispositivos de escaneo láser, ultrasónicos o termográficos.
Los equipos de Fill y Langzauner se instalarán a mediados de 2020. “Fill ha estado haciendo experimentos para nosotros”, señala Fox, “y hemos enviado personal a Austria para recibir capacitación sobre piezas particulares, así como capacitación en digitalización. Una vez que todos los equipos de proceso estén en servicio, utilizaremos la tecnología RFID (identificación por radiofrecuencia) de Plataine y escalaremos a su última plataforma informática de borde, PlataineEdge, que permitirá el análisis y la comunicación en tiempo real entre máquinas ".
Otra parte de la visión de Swinburne's Composites 4.0 Testlab es permitir una fabricación flexible que pueda adaptarse a las cambiantes demandas de la industria muy rápidamente:
“En una línea de producción típica, un cambio o modificación de producto requiere modificaciones importantes del equipo e intervenciones manuales. Por lo tanto, para que dicho cambio de producto sea rentable, se requiere un tamaño de lote mínimo del nuevo producto. Por el contrario, en la visión de la Industria 4.0, las fábricas inteligentes permiten que los requisitos individuales de los clientes e incluso artículos únicos se fabriquen de manera rentable. Una fábrica de este tipo puede responder fácilmente a los cambios de última hora en nombre de los clientes y proveedores. En consecuencia, uno de los principales objetivos de la línea de fabricación propuesta es permitirle producir diferentes productos con una intervención manual mínima o nula ”. - Fox y Subic, "Un enfoque de la industria 4.0 para la impresión 3D de materiales compuestos"
ARENA2036 y enlaces a cadenas de valor globales
Además de proporcionar una fábrica de compuestos físicos digitalizados 4.0, Swinburne también capacitará a la fuerza laboral de la próxima generación. Esto último es posible gracias a una subvención de $ 1 millón / cuatro años del Programa de Vínculos de Innovación Global de Australia. Un socio clave en esta iniciativa es ARENA2036, el programa de I + D en el campus impulsado por la industria de la Universidad de Stuttgart, que se describe a sí mismo como "La plataforma de investigación altamente flexible para la movilidad y la producción del futuro". Con el apoyo del Ministerio Federal de Educación e Investigación (BMBF, Bonn, Alemania) y gestionado como una asociación registrada con 38 miembros de la ciencia y la industria, ARENA2036 cuenta con un "STARTUP AUTOBAHN" y un edificio de 10,000 metros cuadrados, de los cuales 4700 metros cuadrados es una nave de producción abierta con techo de 16 metros de altura y grúa industrial de 10 toneladas. Swinburne se unió a ARENA2036 como miembro en 2018.
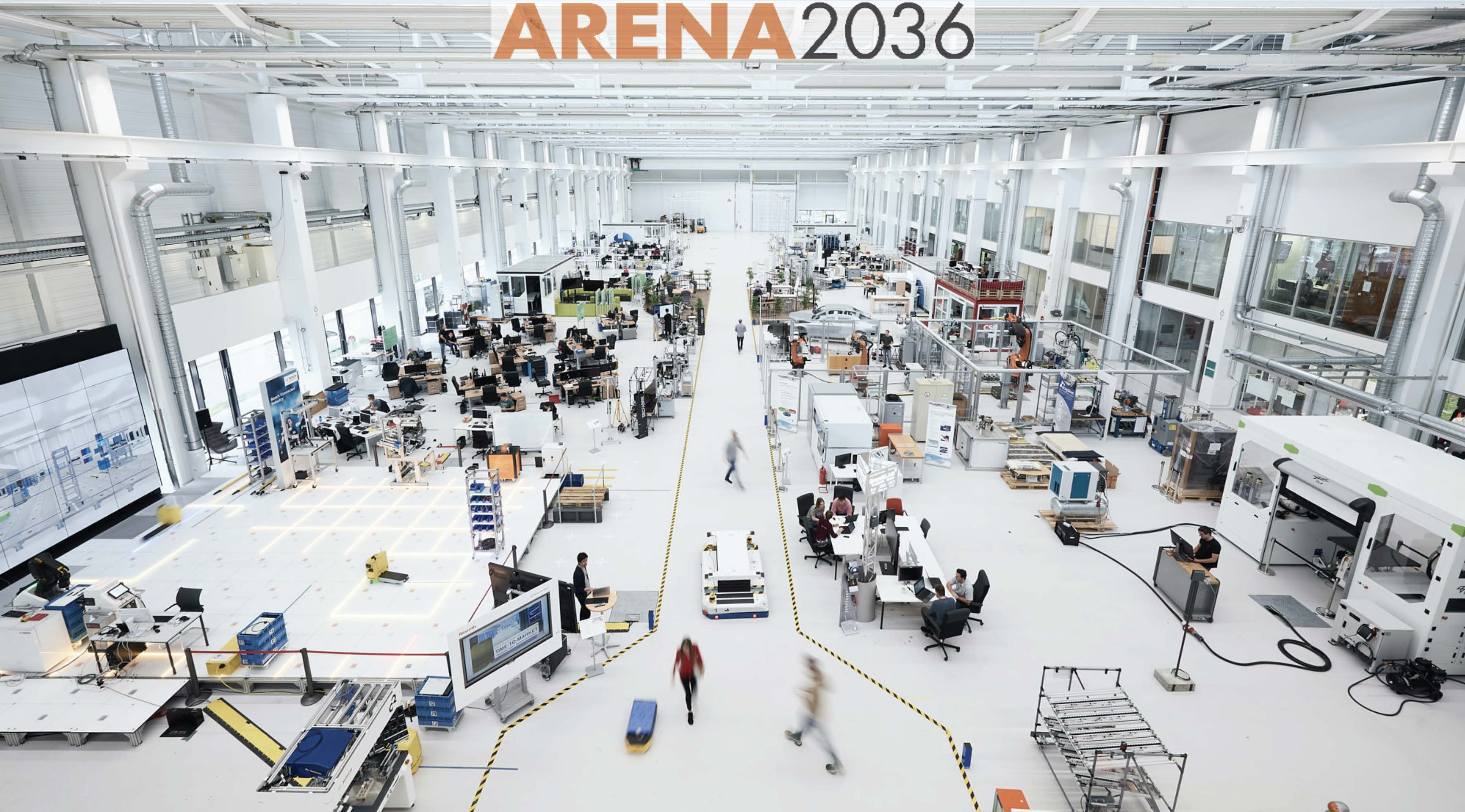
Swinburne's Composites 4.0 Testlab y ARENA2036 están colaborando a través de un programa de $ 3.6 millones respaldado por el esquema Global Innovation Linkage (GIL) del gobierno australiano en la fabricación de Industria 4.0 de compuestos livianos de alto volumen con un enfoque en una tecnología de producción específica habilitada por sistemas de herramientas flexibles y tecnología de gemelo digital. Incluirá:
- I + D y comercialización, facilitando la puesta en marcha conjunta.
- Reclutamiento conjunto, co-supervisión e intercambio de estudiantes de doctorado
- Talleres y simposios de investigación conjunta.
Esta asociación también prevé proyectos conjuntos de I + D con el Instituto Fraunhofer de Ingeniería de Fabricación y Automatización y el Instituto de Ingeniería Industrial (Fraunhofer IPA e IAO, Stuttgart), incluidas pasantías de estudiantes de doctorado en el Instituto de Diseño de Aeronaves (IFB) de la Universidad de Stuttgart en los casos pertinentes. Áreas de Industria 4.0. “El proyecto GIL es un hito importante para los procesos compuestos avanzados y también para la colaboración de SUT, la Universidad de Stuttgart y ARENA2036”, dice el profesor Peter Middendorf, director de la IFB. "Estamos orgullosos de ser socios del proyecto en sí y de anunciar otros dos proyectos de investigación colaborativa apoyados por el gobierno alemán que están directamente vinculados a GIL".
“Formaremos una nueva cohorte de estudiantes de doctorado conjuntos con conocimientos digitales entre Swinburne y la Universidad de Stuttgart”, dice Fox. “No solo desarrollaremos más los procesos de Compuesto 4.0, sino que también consolidaremos las asociaciones globales y crearemos nuevos productos que se pueden exportar desde Australia, particularmente en nuevos mercados de movilidad. A través de estas colaboraciones internacionales, Industry 4.0 Testlab de Swinburne vinculará activamente a las pymes australianas con las cadenas de valor globales. Ya lo hemos demostrado con nuestro socio Imagine Intelligent Materials y esperamos extenderlo a más innovadores australianos ".
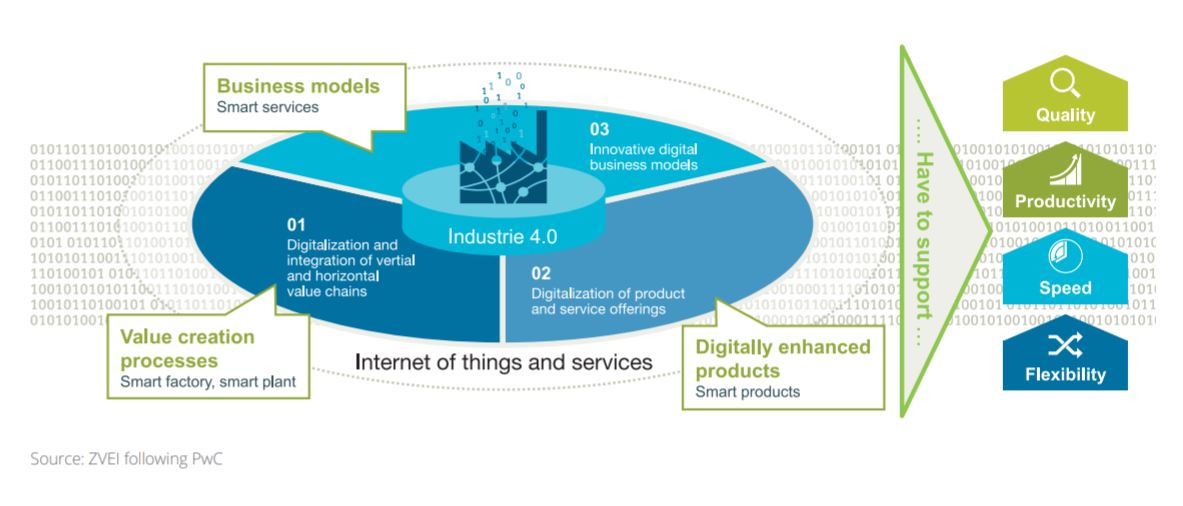
“La competencia internacional será feroz en la fabricación digital del futuro que se acerca rápidamente”, dice Fox. "Es por eso que nuestro desarrollo de la capacidad y la fuerza laboral de los compuestos 4.0 es tan importante ahora".
El laboratorio de pruebas Industry 4.0 para la fabricación de aditivos compuestos en la Universidad de Swinburne se lanzará en diciembre de 2020. Esté atento a CW para futuras actualizaciones y lea nuestra función de julio de 2020, "Composites 4.0:transformación digital, producción adaptativa, nuevos paradigmas" junto con sus cinco barras laterales en línea:
- Composites 4.0:gemelo digital frente a hilo digital
- Actualización del proyecto ZAero
- Composites 4.0:¿por dónde empezar?
- No hay argumentos comerciales para enseñar a los robots
- Arquitectura y ontología de Composites 4.0
Resina
- El valor de la fabricación aditiva en la industria automotriz
- Fabricación aditiva y moldeo por inyección:una nueva visión para los ciclos de vida de producción
- Presentación de AM Fridays y Additive Podcast
- Henkel ofrece una plataforma de materiales para la fabricación aditiva
- Essentium y Lehvoss se asocian para desarrollar materiales para la fabricación aditiva
- POM de alto flujo para la industria médica y sanitaria
- Se forma una alianza de fabricación aditiva y termoplásticos sostenibles en Colorado
- ¿Qué es la fabricación aditiva? - Tipos y funcionamiento
- El caso de la impresión 3D en la fabricación
- Los 5 principales desafíos logísticos y soluciones para la industria manufacturera
- La encuesta de Protolabs y Censuswide sugiere que la fabricación no está preparada para la Industria 4.0