La industrialización del epoxi termoplástico
Cecence (Salisbury, Reino Unido) fue fundada en 2014 por tres fundadores con décadas de experiencia en materiales compuestos. El director Mike Orange tenía una larga trayectoria en aparejos y mástiles de polímero reforzado con fibra de carbono (CFRP) para yates. Jefe de innovación Humphrey Bunyan fue anteriormente jefe de innovación en Future Fibers (Valencia, España). "Ellos [Future Fibers] estaban fabricando aparejos totalmente compuestos para la America’s Cup y otras embarcaciones de carreras, así como amarres de CFRP para sujetar las ruedas a los autos de Fórmula 1", dice Orange (ver "Materiales compuestos para la construcción de yates:aparejados para el éxito"). "Comprendemos las ventajas de la ligereza, pero nos relacionamos con otros sectores que no tenían nuestra experiencia y luchaban con los costos, ampliando la fabricación y cumpliendo con las regulaciones contra incendios".
Por lo tanto, Cecence (pronunciado "sentido común", como en el sentido común con los compuestos de fibra de carbono) se fundó para centrarse en la resistencia al fuego, la fabricación industrializada y la sostenibilidad. Esto dio como resultado desarrollos como un respaldo de asiento compuesto de fibra de carbono / biorresina moldeado por compresión para aviones de pasajeros que pesaba solo 7.5 kilogramos, un grosor de asiento reducido a menos de 20 milímetros y un mayor espacio para pasajeros y comodidad, al tiempo que cumple con todos los requisitos de fuego, humo y toxicidad (FST).
“En un proyecto anterior, Cecence había desarrollado un método de fabricación de prensado en caliente que acortaba el tiempo de ciclo de 2,5 horas a 7 minutos para un respaldo de clase económica utilizando fenólicos de curado instantáneo desarrollado con prepregger FTI (Somerset) del Reino Unido ”, dice Orange. Para este último respaldo descrito anteriormente, que desarrolló con Design Q (Redditch, Reino Unido), Cecence amplió su cartera de FST utilizando un preimpregnado de resina de alcohol polifurílico (PFA) desarrollado por SHD Composites (Sleaford, Reino Unido). El PFA es un polímero termoestable derivado de la biomasa que se comporta como un fenólico con un excelente procesamiento de superficie y sostenibilidad (consulte “Resistencia al fuego sin peso”). “Trabajamos con SHD Composites e impulsamos su química para una cura más rápida”, dice Orange. "Eso es lo que hacemos:tomamos materiales, procesos y diseños y los desarrollamos más para que los productos compuestos puedan fabricarse a escala de una manera que sea comercialmente viable pero sostenible".
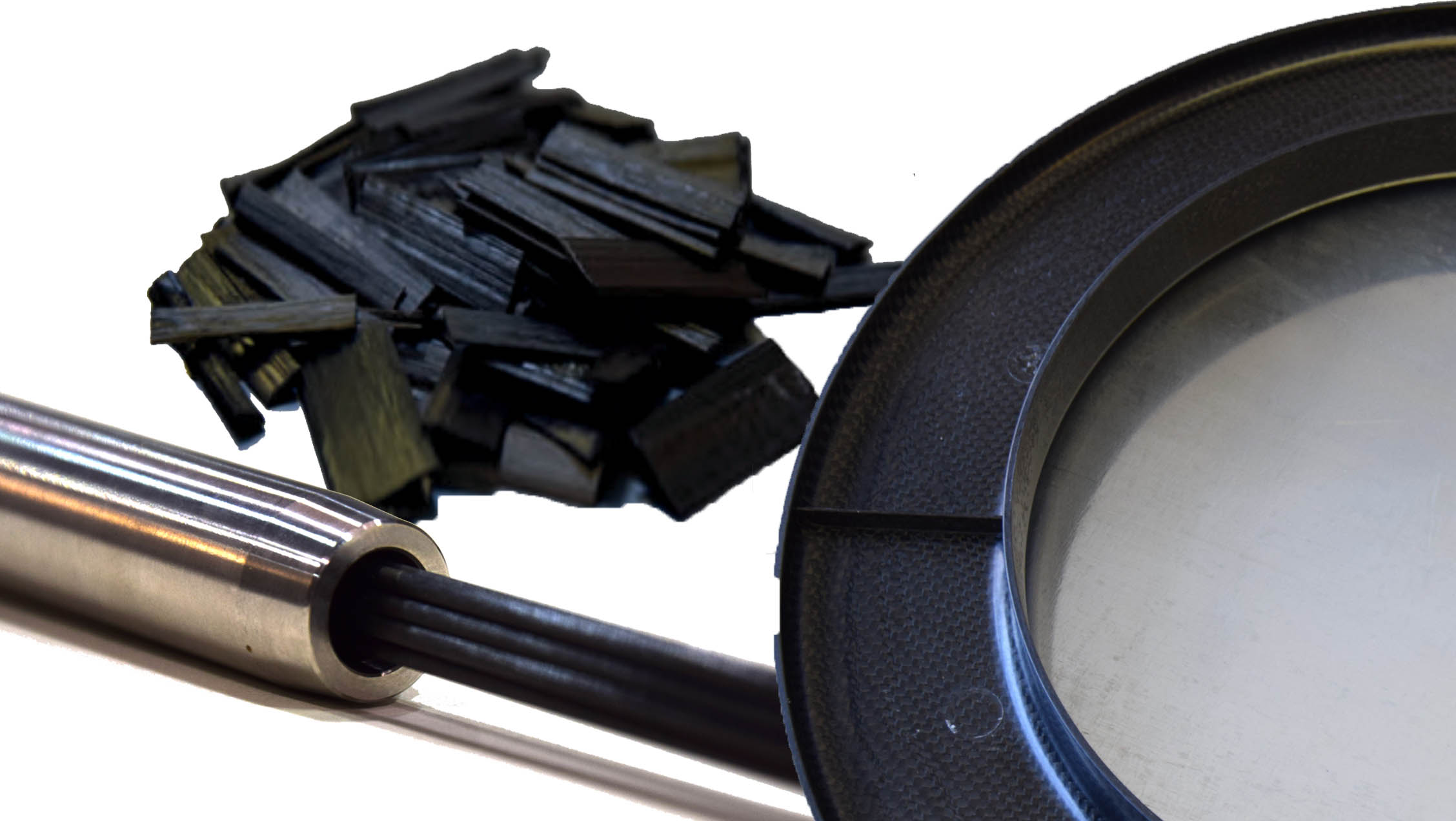
La velocidad de fabricación y la sostenibilidad fueron factores clave cuando Cecence encontró un sistema de resina epoxi termoplástica hace varios años. "Este termoplástico con componentes epoxi al final de sus cadenas de polímero estaba siendo utilizado por una empresa de telas que no se dio cuenta de su potencial en compuestos", explica Orange.
“Entendimos de inmediato las ventajas de un termoplástico de baja viscosidad que podría impregnar las fibras muy bien al mismo tiempo que permite un epoxi termoformable”, dice Humphrey Bunyan. Cecence desarrolló un preimpregnado basado en esta tecnología epoxi termoplástica, y luego una familia de productos bajo la marca K_Series:K_Rod enrollable, K_Plate semiimpregnado de 0,25 a 1,98 milímetros de espesor y compuesto de moldeo K_Chip (Fig. 1). “Hemos podido moldear a presión los componentes en menos de tres minutos”, dice Orange, “y hemos demostrado una variante FR que cumple con los requisitos de FST para interiores de aviones”. Cecence también ha utilizado el material para desarrollar un sistema compuesto de equipos de líneas aéreas (COHLE) para líneas ferroviarias eléctricas que reduce la cantidad de postes / postes de soporte a la mitad y el costo total de instalación y operación en £ 100,000 ($ 124,200) por kilómetro.
Epoxi termoformable
“Con los termoplásticos típicos, tiene un polímero de matriz de alta viscosidad que es difícil de forzar en las fibras”, explica Bunyan. “Por lo tanto, es difícil lograr una buena impregnación de las estopas o telas. Pero el epoxi termoformable K_Series tiene una viscosidad muy baja:80 centipoise a 100 ° C. Esto nos permite preimpregnar refuerzos de vidrio, carbono y fibra natural con una excelente distribución de resina a fibra y, por lo general, un 60% de contenido de fibra por peso. También podemos utilizar fibras con encolado para epoxi, que normalmente no es compatible con termoplásticos ". Y, sin embargo, este sistema es un verdadero termoplástico, que permite el reformado de piezas terminadas a 180-200 ° C sin reacción química ni exotermia.
“Al igual que el epoxi, se adhiere bien a la fibra, por lo que no hay separación de la fibra de la matriz, incluso si usa presiones más altas durante el moldeado”, señala Orange. Esto se refiere a un problema que ha visto con compuestos de polipropileno y poliamida reforzada con fibra corta (PA). “Estábamos trabajando con una capa de PA fundida sobre una tela mediante prensado en caliente para hacer una hoja plana. La matriz no se pegaba a las fibras, solo las rodeaba. Por lo tanto, cuando se presiona en una pieza, se extrae la fibra ".
K_Plate, que procesa a 150-220 ° C, ofrece una temperatura de servicio de 100 ° C para exposiciones breves y uso continuo a 90 ° C. Los compuestos K_Chip de estopa unidireccional picados se prensan a 240 ° C. "El T g [la temperatura de transición vítrea] y el inicio de la deformación por calor para K_Series son más bajos que los epóxicos típicos, pero esto es también lo que hace que el reformado y el reciclaje sean factibles ”, dice Orange. Los procesos de K_Series también son rápidos. “Cecence trabajó con RocTool [Le Bourget du Lac, Francia] en JEC 2016 para demostrar el termoplástico de formación más rápida que habían visto”, dice, señalando un tiempo de ciclo de 2 minutos, 40 segundos para un capó de automóvil. “El tiempo de permanencia fue de solo 25 segundos antes del enfriamiento, usando 8-9 bar de presión por encima de la membrana de vacío. También quedaron satisfechos con el acabado de las superficies mate y brillante [ver imagen de apertura], y señalaron que nuestro material proporcionó el mejor acabado de todos los que se probaron ”.
Además, los componentes epoxi de los productos K_Series hacen que las piezas compuestas sean fáciles de pintar y unir, sin las imprimaciones especiales ni la preparación necesaria para los termoplásticos tradicionales. “Puede unirlos de forma secundaria utilizando adhesivos estándar”, agrega Bunyan. “También se obtienen buenas propiedades de cizallamiento interlaminar y, en general, se obtienen estructuras resistentes que absorben energía gracias al termoplástico”.
Catenaria CFRP para ferrocarriles eléctricos de menor costo
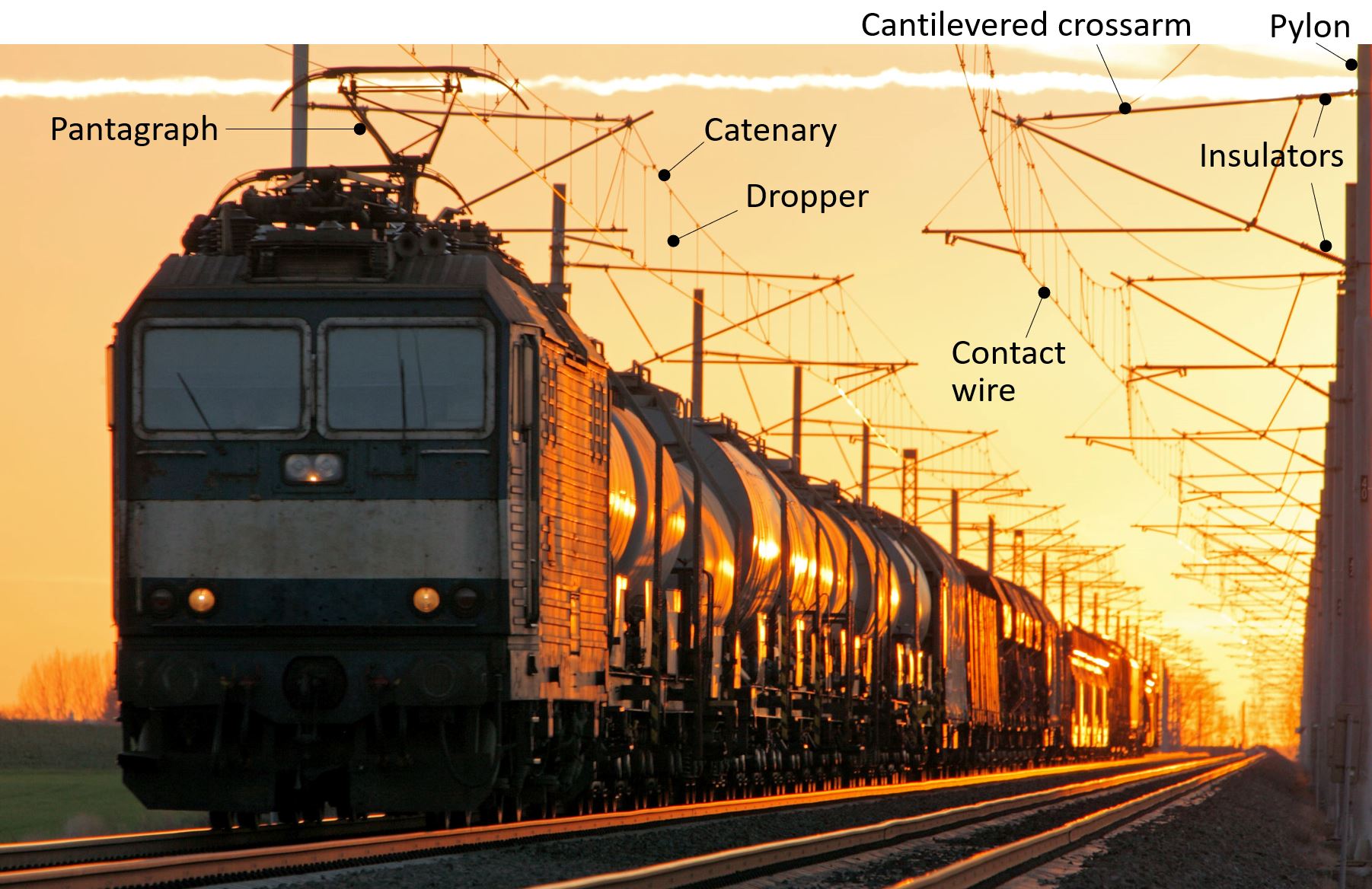
La naturaleza dual de este epoxi termoplástico se ejemplifica en un sistema de equipo de línea aérea (OHLE) desarrollado por Cecence utilizando una catenaria CFRP hecha con K_Rod. La catenaria y el cable de contacto portador de corriente son los dos cables principales en el OHLE de un ferrocarril eléctrico (Fig. 2). La electricidad se entrega a la locomotora de un tren a través de un pantógrafo, que se extiende desde la parte superior de la locomotora para presionar contra el cable de contacto. “La catenaria actúa como un puente colgante entre pilones (mástiles, postes), que están espaciados cada 25 metros a lo largo de las vías”, explica Orange. El cable de contacto de cobre está suspendido de la catenaria mediante cables cuentagotas verticales o cuentagotas, al igual que la calzada está sostenida por cables en un puente colgante.
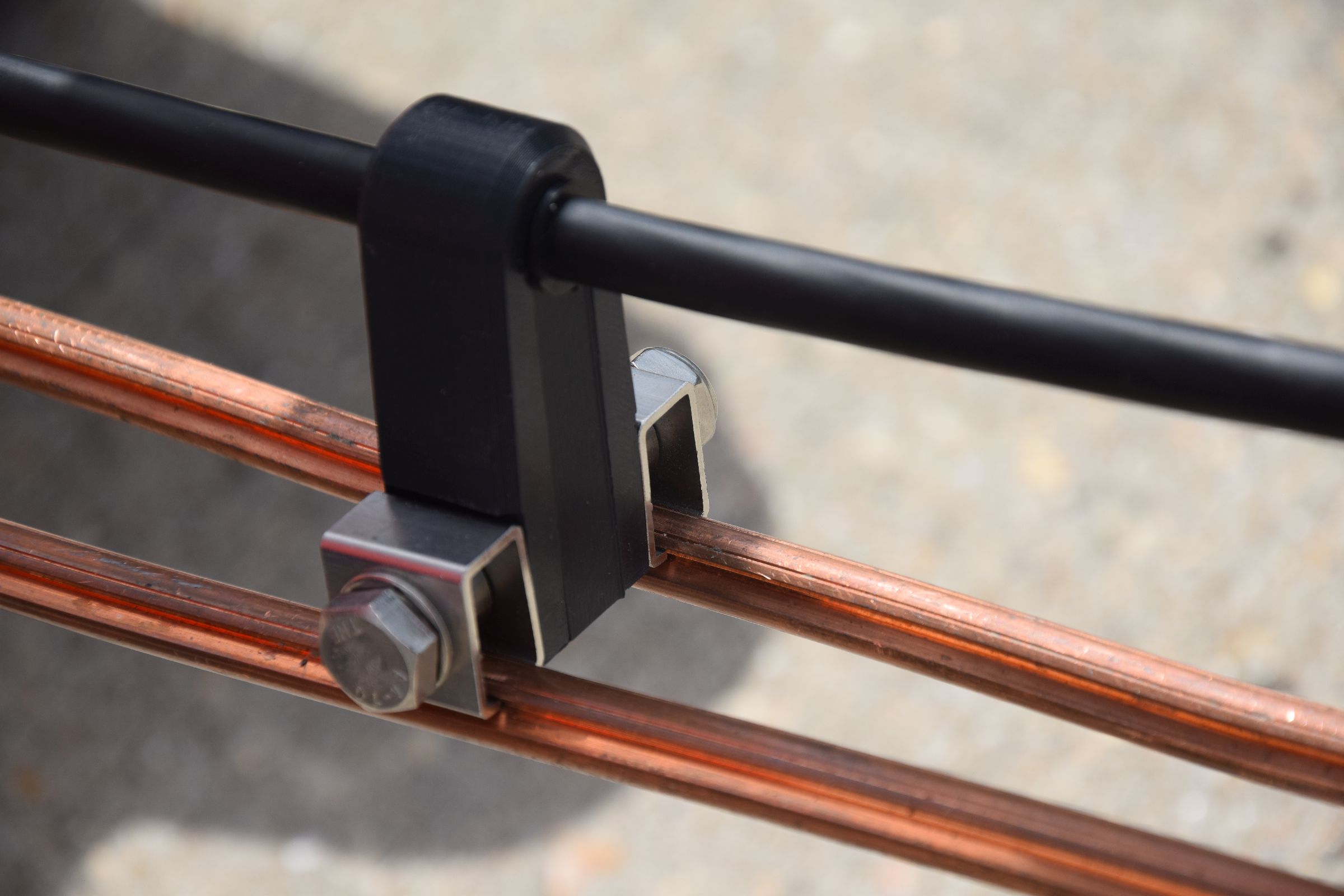
“Al usar un cable de tensión K_Rod como catenaria, puede colocarse solo 70 milímetros por encima del cable de contacto de cobre”, señala Orange (Fig. 3). "Todo el sistema es más compacto con un impacto visual mucho menor en el medio ambiente". Los sistemas OHLE actuales utilizan cables de catenaria de acero, que cambian de longitud con el cambio de temperatura. “En verano, se extienden hasta 400 milímetros por kilómetro”, señala. Para contrarrestar esta flacidez en las líneas, se instalan contrapesos de concreto en poleas como un sistema de tensión automática, pero aumentan el costo total.
“El peso de la línea de acero y su perfil de pandeo también son la razón por la que se necesitan tantos postes”, señala Orange. “Nuestro cable de CFRP cambia de longitud solo 7 milímetros por kilómetro en el verano porque la expansión térmica insignificante de la fibra de carbono crea un compuesto térmicamente estable. También es un 80 por ciento más liviano que el cable de acero, no se dobla y permite espaciar los pilones a 50 metros, lo que reduce a la mitad el número de pilones necesarios ". Esto permite un mayor ahorro de costes porque por cada pilón hay una cruceta en voladizo, sostenida por un tirante.
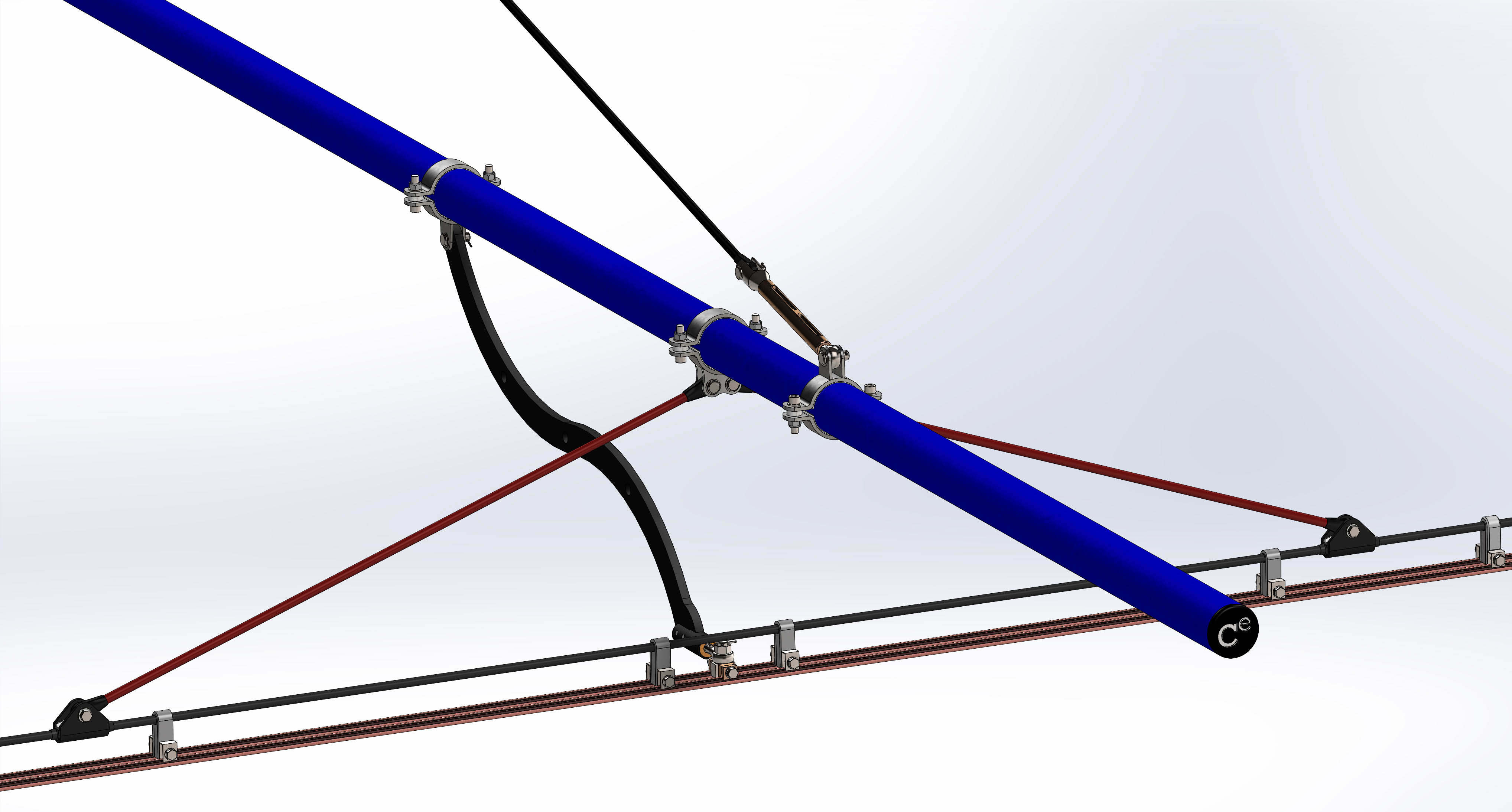
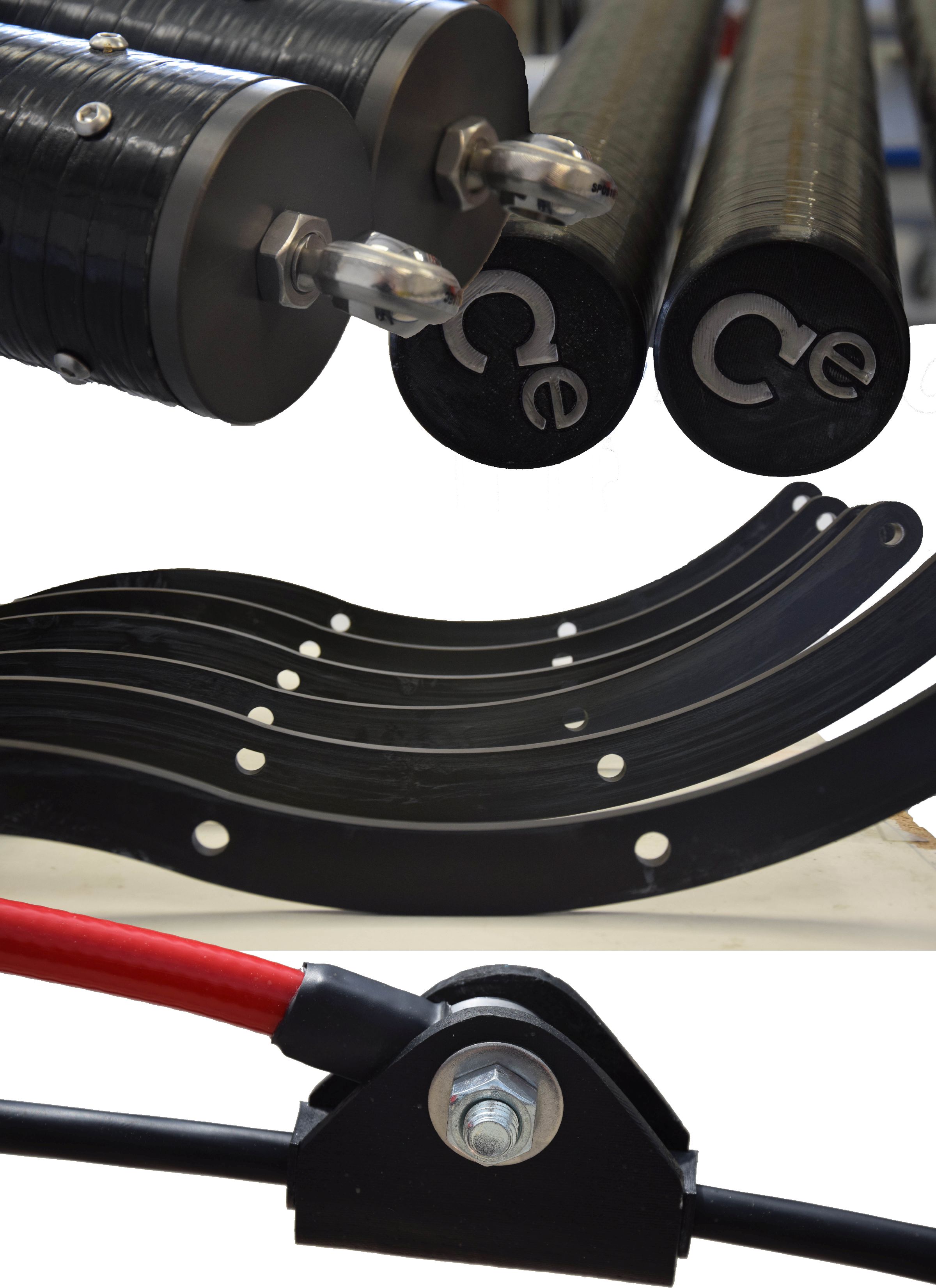
Además, los sistemas OHLE convencionales utilizan componentes totalmente metálicos, lo que requiere la adición de aislantes para evitar la conducción no deseada de la corriente eléctrica. “El Cecence COHLE no necesita todos los aisladores porque utiliza postes compuestos de fibra de vidrio no conductora (GF) y brazos cruzados con tirantes de cables compuestos no conductores”, explica Orange. “También utilizamos goteros intermedios hechos de ácido poliláctico (PLA) impreso en 3D. A diferencia de un sistema de metal, los postes no necesitan pintura regular y los compuestos resistentes a la corrosión requieren menos mantenimiento ”.
“El epoxi termoplástico juega un papel clave en la catenaria CFRP”, continúa. “Cecence lo usa tanto en el núcleo de fibra de carbono K_Rod como en la chaqueta de compuesto GF trenzado. El resultado es un cable aislado, liviano y de alta resistencia que se puede enrollar y se adhiere bien cuando se pega en un enchufe, lo que resuelve el problema de terminación normalmente complicado para los cables compuestos de fibra de carbono. Gracias a la increíble transferencia de carga desde el núcleo al enchufe a través de la trenza superior, no necesitamos un enchufe de gran longitud y este sistema es fácil, por lo que es práctico de instalar en el campo por técnicos ferroviarios ".
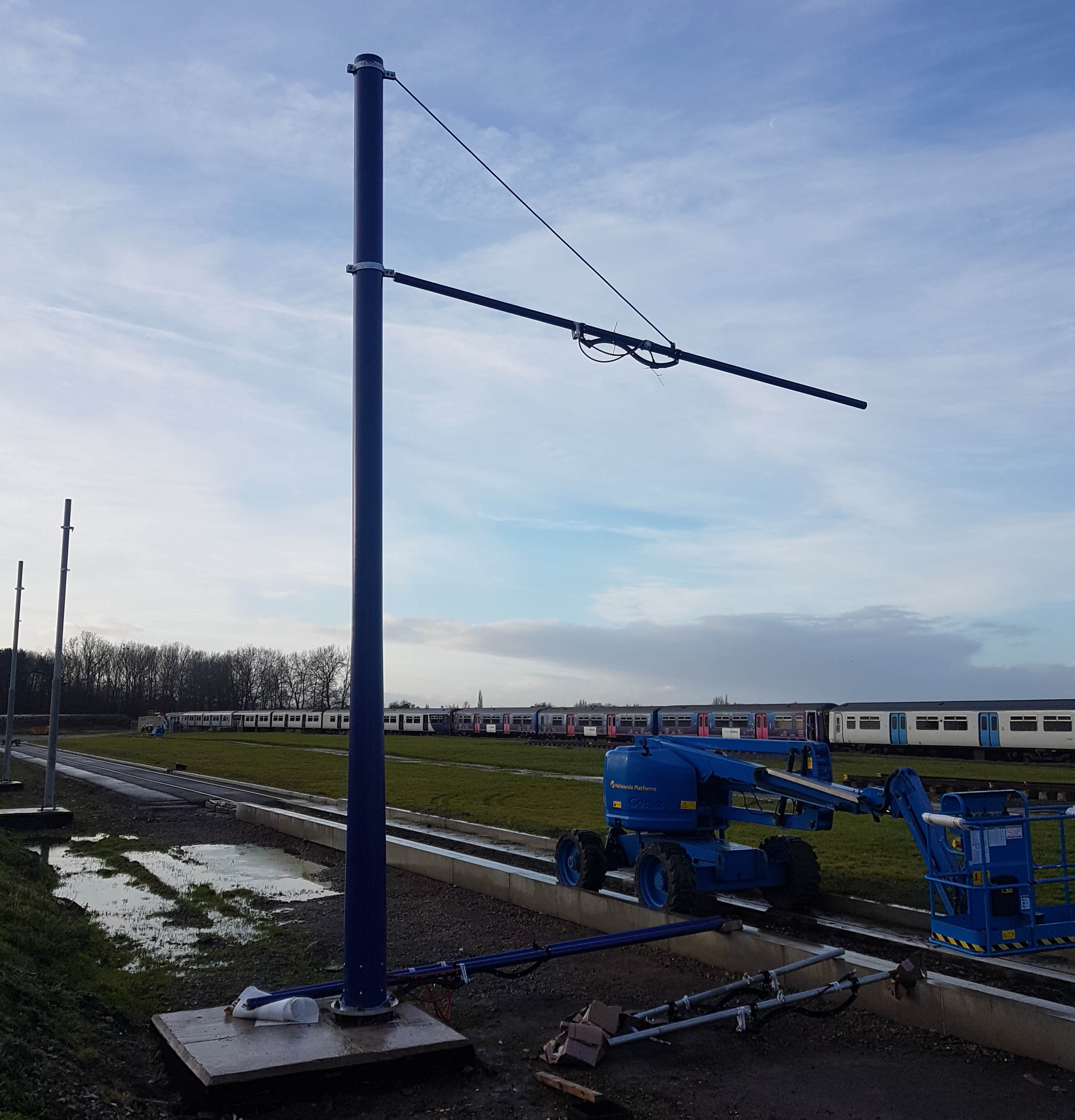
Aunque el cable CFRP cuesta tres veces más que una catenaria de acero, el costo total del sistema se reduce de £ 512,000 a £ 413,000 por kilómetro, dice Orange. Estos costos, calculados con la firma multinacional de ingeniería e infraestructura Atkins (Londres, Reino Unido), incluyen ahorros en operaciones / mantenimiento de £ 400,000 a £ 3.4 millones por kilómetro durante la vida útil del sistema.
“Cecence entregó los componentes del prototipo en mayo de 2019”, dice Orange, “y nuestros socios de desarrollo habían programado instalar las líneas eléctricas para febrero de 2020, pero eso se retrasó debido al COVID-19. Todo el sistema se mostró en el Advanced Engineering Show de 2019 y ganó el premio a la innovación Composites UK ”.
Más aplicaciones y desarrollo de K_Series
Más allá de la aplicación OHLE, Cecence está buscando otras oportunidades para aplicar sus productos K_Series. “Cecence también ha trabajado en proyectos en los que los cables K_Rod se utilizaron como anclajes para un acantilado de piedra en un proyecto de construcción en Suiza”, dice Orange. “Nuestros socios del proyecto debían perforar pozos de 80 metros de profundidad en la roca, insertar los cables de CFRP y luego rellenar con concreto. Hubo algunos resultados de pruebas sorprendentes, pero el socio académico nunca se conectó con la industria para desarrollar el proyecto más allá de la escala de laboratorio . Estamos realizando otras demostraciones, sin embargo, este sistema es a prueba de corrosión y proporciona una buena transferencia de carga. También podría aplicarse como anclaje al suelo para varios sistemas de construcción, como edificios a prueba de huracanes ”.
Los videos en YouTube y el sitio web de Cecence demuestran la termoformabilidad de sus productos K_Plate. “También ha habido discusiones para explorar aplicaciones para perfiles aerodinámicos de geometría variable / morphing con una empresa aeroespacial del Reino Unido”, dice Orange. Cecence demostró un material automotriz rentable utilizando K_Chip hecho con cables compuestos cortados como un material híbrido CF / GF / epoxi termoplástico, manteniendo una proporción de 2:1 de carbono a vidrio, confirmada mediante pruebas. . ”
La empresa también ha desarrollado una K_Series de alta temperatura con una T g de 250-300 ° C que procesa a 360-400 ° C. “Esto se usó para un fabricante de automóviles que quería que las piezas de CFRP sobrevivieran a su proceso de pintura E-Coat a 180 ° C”, dice Orange. “También tenemos el material K-FR, que puede pasar los requisitos de quemado vertical FST de aeronaves, liberación de calor y toxicidad del humo, y estamos estudiando cómo ayudar con la amortiguación de vibraciones para reducir el ruido de la cabina de la aeronave. Podemos ajustar el termoplástico y agregar capas de material elastomérico para lograr una reducción significativa del ruido ”.
Samantha Bunyan, la tercera fundadora de Cecence y su jefa de participación en la industria, señala que la reciclabilidad también es un área clave de desarrollo. Cecence es parte del consorcio ReDisCoveR Composites, operado por el National Composites Centre (Bristol, Reino Unido). Se estableció en abril de 2019 y está llevando a cabo 24 proyectos a lo largo de las cuatro corrientes:reciclaje, desmontaje, materiales circulares y reutilización. “Dentro de estos proyectos, estamos analizando el desmontaje de componentes y demostrando la reciclabilidad real de los compuestos termoplásticos”, dice Bunyan. “La industria finalmente se ve obligada a demuestre la reciclabilidad que ha reclamado durante muchos años. Cecence ve los beneficios de poder reciclar productos epoxi termoplásticos K_Series, pero también tiene que demostrar los procesos y la viabilidad económica para esto ”.
“Creemos que hay mucho más espacio para los compuestos sostenibles en el transporte masivo, incluidos los interiores de aviones, asientos y aplicaciones ferroviarias”, dice Orange, y agrega que Cecence no es solo un socio en el desarrollo sino también en la fabricación. “Hemos fabricado 2.500 respaldos de asiento compuestos para aviones tipo A320 hasta la fecha y estábamos en camino de producir los respaldos de asiento más livianos y delgados de la industria antes del brote de COVID-19. Los restos de los asientos compuestos se pueden reutilizar en reposapiés y reposabrazos. El reciclado también se puede utilizar en otras piezas auxiliares que actualmente utilizan plásticos vírgenes. Todo esto puede ayudar a reducir el consumo y las emisiones de combustibles fósiles, además de facilitar la electrificación y aumentar la sostenibilidad ”.
En los compuestos, señala Samantha Bunyan, “la sostenibilidad es triple:materiales, procesamiento (rápido y de bajo consumo energético) y cadena de suministro. Estamos interrumpiendo todo esto, trabajando con innovadores de todo el mundo que no son vistos porque la mayoría de la gente solo mira a las grandes empresas. El mundo necesita nuevas soluciones que funcionen para la industria. Esto es lo que hace Cecence ".
Resina
- Fabricación de materiales compuestos:Fabricación de materiales compuestos
- Covestro intensifica la inversión en compuestos termoplásticos
- La historia de la resina epoxi
- Compuestos termoplásticos en Oribi Composites:CW Trending, episodio 4
- Solución de problemas de termoformado de compuestos termoplásticos
- La evolución de los compuestos aditivos
- Compuestos termoplásticos:soporte de parachoques estructural
- Toray Advanced Composites expande las capacidades de los compuestos termoplásticos
- Mar-Ball, Lattice Composites se fusionan para ampliar las capacidades de epoxi
- Compuestos termoplásticos:vista panorámica
- Soldadura de compuestos termoplásticos