Combinación de AFP con impresión 3D para una producción de piezas flexible
Fundada en 1986, Electroimpact (Mukilteo, Washington, EE. UU.) Es un proveedor global de herramientas y automatización de la producción que afirma ser el integrador de líneas de montaje de aviones más grande del mundo. En materiales compuestos, la empresa es conocida por su tecnología avanzada en sistemas de colocación de cinta automatizada de alta velocidad (ATL) y colocación de fibra (AFP). Electroimpact enfatiza que está impulsado por ingenieros (400 de sus 600 empleados tienen títulos de ingeniería) con desarrollos concebidos y completados por el mismo equipo de ingenieros, desde el concepto hasta el diseño, la fabricación, la instalación y la compra del cliente.
En julio de 2020, CW informó sobre el nuevo sistema Scalable Composite Robotic Additive Manufacturing (SCRAM) de la empresa. A continuación, compartimos nuestra entrevista con parte del equipo de ingeniería de SCRAM:el gerente de proyecto Cody Brown, el ingeniero de control y desarrollo de procesos Ryan Bischoff y el ingeniero mecánico principal Reese Allen. Su explicación del origen, la implementación y el futuro de esta fabricación aditiva de fibra continua proporciona información sobre cómo podría ser la próxima generación de producción de compuestos.
Apuntando a FDM a gran escala
Marrón :“Hemos estado trabajando en esto durante cuatro años, pero queríamos esperar hasta poder demostrar que produciría piezas reales de calidad aeroespacial. Nuestro objetivo original era producir una impresora 3D de fabricación de filamentos fundidos (FFF) a gran escala que pudiera crear piezas complejas utilizando fibra continua. No nos propusimos desarrollar un proceso tipo AFP, pero como intentábamos aumentar el volumen de la fibra y lograr una mayor resistencia física en las piezas impresas, chocamos contra una pared con FFF. Simplemente no es un proceso adecuado para la consolidación in situ con alto contenido de fibra y pocos huecos. Por lo tanto, hemos terminado con un proceso que combina AFP compuesto termoplástico con FFF utilizando filamento relleno de fibra cortada o no reforzada ”.
Allen :“AFP es en realidad un proceso de fabricación aditiva. En SCRAM, sin embargo, no lo usamos de manera convencional con una herramienta dura fija, sino que imprimimos una herramienta que luego podemos lavar para crear geometrías muy complejas que son verdaderamente estructurales ".
Marrón :"Podemos colocar esa herramienta soluble en lugares que no están bloqueados por la red para que pueda crear cavidades internas. El objetivo no es competir con nuestros grandes sistemas AFP, sino crear un sistema muy hábil lo más parecido a una impresora 3D que puedas conseguir. Hacer esto con verdaderos seis grados de libertad y precisión es realmente muy complicado. La celda resultante elimina sujetadores y adhesivos, fabricando piezas integradas y complejas que se pueden iterar muy rápidamente ”.
Alto rendimiento para la industria aeroespacial
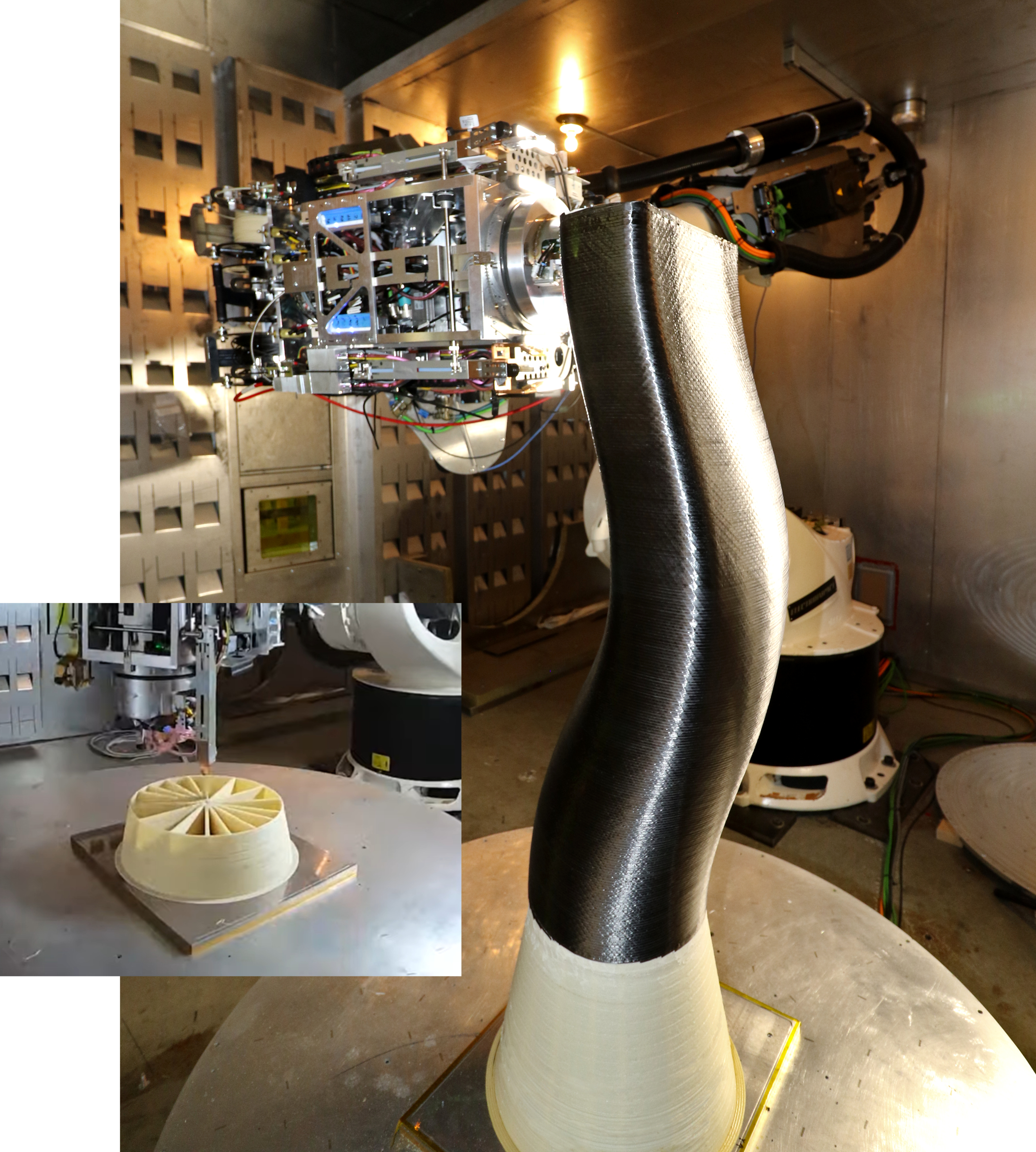
Marrón :“Las aplicaciones iniciales a las que nos dirigimos en la industria aeroespacial y de defensa, comenzamos con PEEK [polieteretercetona]. Luego trabajamos con PEKK [polietercetonacetona] y PAEK [poliariletercetona] de bajo punto de fusión con un éxito espectacular ”.
Bischoff :“El coeficiente de expansión térmica [CTE] es su mayor enemigo. Esta es la razón por la que usar PEEK es tan desafiante:le encanta cristalizar y encoger. Aunque el CTE para PEKK y otras resinas PAEK no es cero, su estructura cristalina es mucho más controlable y, por lo tanto, más fácil de trabajar. Los PAEK alternativos también ofrecen una capacidad de procesamiento mucho mejor y una mayor velocidad de laminado ”.
Allen :“Deben evitarse los gradientes térmicos debido al problema del CTE, por lo que intenta mantener el proceso y la pieza lo más isotérmicos posible. De lo contrario, terminará con deformaciones. Usar la cámara calentada es imprescindible, incluso si no la mantiene a una temperatura alta, solo para asegurarse de que no haya corrientes de aire y que una parte de la impresión no esté a una temperatura diferente al resto ".
Celda basada en láser
Marrón :"Muchas cosas que habilitan este sistema no existían cuando comenzamos, incluida la cinta PAEK y el láser compacto de alta potencia que usamos, así como el verdadero software CAM de fabricación aditiva de seis ejes".
“El cabezal SCRAM utiliza dos boquillas de impresión 3D a cada lado del sistema AFP [imagen de apertura]. Uno se utiliza para imprimir las herramientas solubles y el otro imprime filamento de fibra cortada o no reforzada. Puede ver que uno está equipado con un andamio. Contiene un juego de espejos para redirigir la luz láser alrededor de la punta de la boquilla y calentar el sustrato. Esto nos permite lograr una fuerza de unión entre capas excepcional en comparación con la FFF tradicional. Las luces del sistema deben iluminar la parte de las cámaras [Fig. 2]. Los usamos en todas partes para que el operador pueda ver con seguridad lo que está sucediendo sin peligro del láser ”.
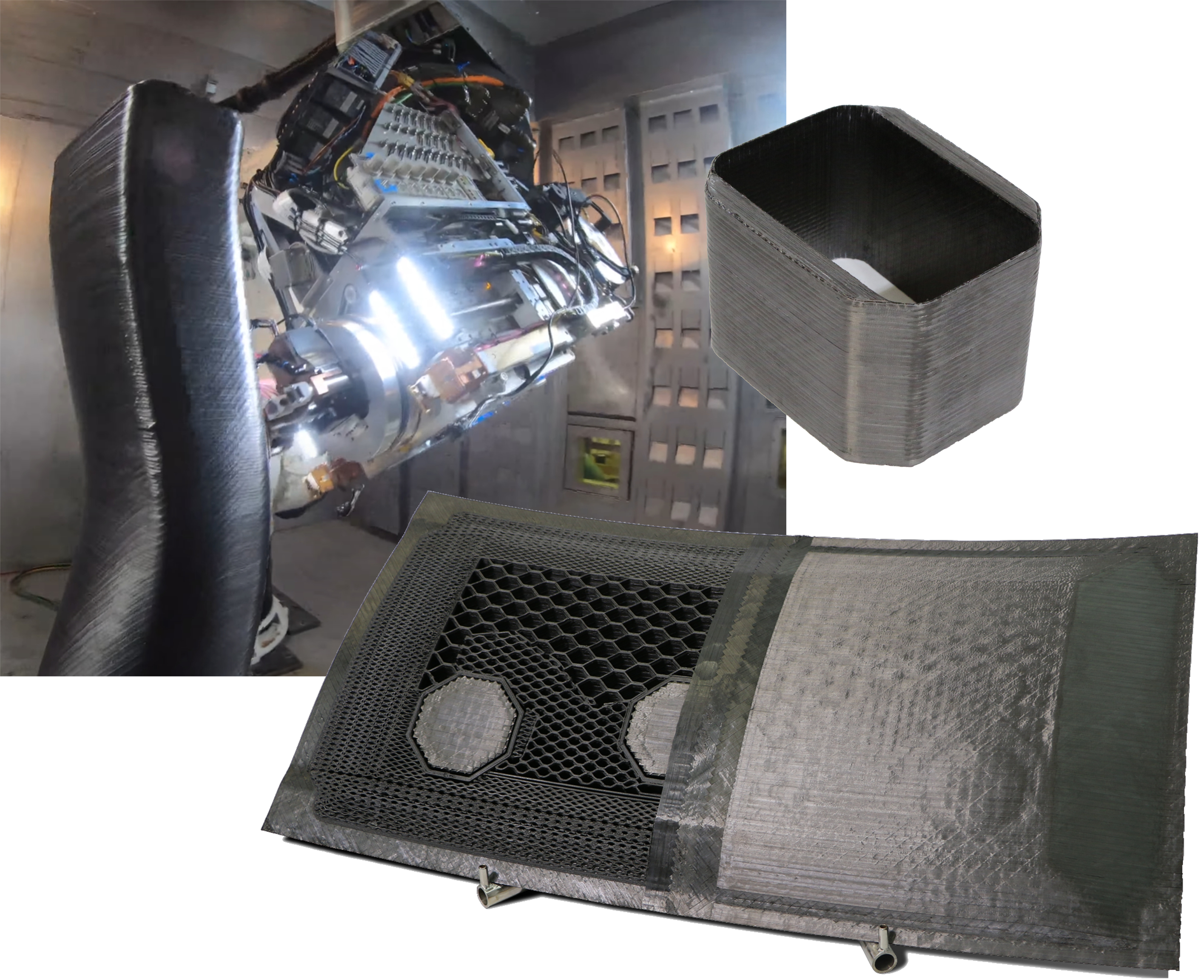
Formatos de material y porosidad
Marrón :“Hemos procesado muchos materiales diferentes, la mayoría de ellos hechos a la medida de nuestras especificaciones de fibra, resina, volumen de fibra y dimensiones. Recientemente, hemos estado experimentando con cables de hendidura más disponibles comercialmente. Los filamentos FFF de fibra cortada también se fabrican según nuestras especificaciones utilizando la misma resina y fibra que seleccionamos para las cintas de fibra continua. Hemos utilizado filamentos de 1, 3,5 y 6,35 milímetros de diámetro. Podemos ir más grandes, pero todavía no hemos tenido la necesidad de hacerlo ".
“Logramos un volumen de fibra del 50-60% para el AFP, pero sustancialmente menos para las porciones de FFF, ya que se extruyen. La porosidad está en el orden de los procesos tradicionales fuera del autoclave, pero ha ido disminuyendo drásticamente a medida que refinamos el proceso. Utilizando materiales de muy alta calidad, y en un entorno de laboratorio, hemos logrado una porosidad por debajo del 0,5%, medida mediante tomografías computarizadas [tomografía computarizada]. Como siempre, hay una gran cantidad de variables que impactan en este número y cuando estamos produciendo piezas muy complejas es un desafío mantener una baja porosidad. Hemos realizado muchas pruebas destructivas y no destructivas de piezas y cupones hechos con el sistema ”.
Control robótico de alta precisión
Bischoff :“SCRAM ofrece tecnología robótica de alta precisión. Los robots estándar disponibles en el mercado son una solución asequible para lograr un movimiento de 6 grados de libertad para colocar e imprimir, pero no son lo suficientemente precisos para AFP de calidad aeroespacial. Empezamos a descubrir cómo aplicar estos robots a los sistemas AFP aeroespaciales hace años. Realmente debe comprender los fundamentos del sistema y los problemas para lograr la precisión. Tenemos un grupo de robots completo de 60 a 70 ingenieros, y esto es todo lo que hacen ”.
“Es un tema increíblemente complejo lograr una alta precisión posicional y de trayectoria. Tiene imprecisiones en el robot (CTE del robot, holgura, vibraciones, etc.) y en el eje externo, calibraciones de puntos de herramienta, un marco de pieza giratoria y varias otras fuentes. No tener en cuenta / abordar ninguno de estos puede ser catastrófico una vez que comience a imprimir en un verdadero espacio 3D. Para lograr esto, desechamos el controlador que viene con el robot y ejecutamos todo con un CNC de Siemens. Luego agregamos la retroalimentación secundaria patentada de Electroimpact en todos los ejes del robot, lo que nos lleva desde una tolerancia de 30-40 mils [0.030-0.040 pulgadas] hasta ± 15 mils [0.015 pulgadas]. Luego aplicamos una compensación cinemática de alto orden para alcanzar ± 10 milésimas de pulgada [0.010 pulgadas] ”.
Velocidad, efectores finales y mesa de impresión giratoria
Marrón :“Estamos utilizando la consolidación in situ, por lo que la velocidad de aplicación no se acercará a la de las cintas preimpregnadas termoendurecibles. Además, este es un robot, no una plataforma de pórtico grande y rígida (como AFP), que está construida para velocidades más altas. Y la velocidad no es solo la colocación y la impresión, sino que también incluye el tiempo de entrega de las herramientas. La métrica real es ¿qué tan rápido puede tener una pieza fabricada digitalmente en la mano? ”
“La parte del video tenía 36 pulgadas de alto (con la base impresa excedía los 4 pies) y su diámetro era de 16 pulgadas. Si corriéramos sin parar en turnos, podríamos producir esto en unos pocos días, que es un tiempo increíblemente corto para tener una parte en la mano. Las piezas también se producen directamente desde el archivo CAD, por lo que si necesita iterar, cambie el CAD, vuelva a publicar las rutas de las herramientas e imprima la nueva pieza ".
Allen :“En este momento, para imprimir la herramienta de soporte, tenemos un proceso basado en filamentos ampliado. El rendimiento es algo lento, lo que afecta el tiempo de impresión. En julio, pusimos en marcha nuestro primer efector final con una extrusora de tornillo de pellets. Esto aumentará la producción pero producirá cordones gruesos, por lo que también agregaremos un efector de extremo de fresado para mecanizar la superficie impresa ”.
Marrón :“Tendremos una familia de efectores finales compatibles que el robot puede recoger y dejar, realizando una amplia variedad de funciones aditivas y sustractivas según sea necesario. El procedimiento de recogida y entrega del efector final está completamente automatizado, lo cual es una característica estándar en todos nuestros sistemas AFP, así como en SCRAM. Todo el efector final está conectado al robot mediante un módulo de interfaz de cambio de herramienta automático y hay soportes para el almacenamiento del efector final ”.
“El sistema imprime en un eje de rotación externo y es controlado por el CNC. Tenemos esto porque el robot por sí solo no puede llegar a todos los puntos de las piezas que queremos hacer. Más adelante, tenemos la intención de poner el sistema sobre rieles para hacer piezas más grandes, pero primero queremos refinar el sistema a esta escala. Hemos hablado del uso de dos robots y sabemos filosóficamente cómo lo haríamos. (Hemos producido otros sistemas integrados de fabricación de múltiples robots). Pero cuando tiene dos robots trabajando en zonas de trabajo superpuestas, los controles se vuelven extremadamente complicados ”.
La futura producción flexible es posible
Marrón :“Esta celda multifuncional brindará valor al cliente final. No siempre tiene que producir piezas termoplásticas continuas reforzadas con fibra. Al agregar extrusión y fresado a la deposición continua de fibra, ampliamos su rango y flexibilidad. Por ejemplo, algunas de las estructuras que hemos demostrado tienen funciones sustractivas dentro de la construcción de la pieza. Luego, el robot revisa la superficie y cierra esa cavidad. Actualmente, esto no es posible sin varios pasos, herramientas especializadas y / o ensamblaje final de algún tipo ”.
“Sin embargo, hay un tema aún mayor que la mera producción de piezas. A largo plazo, este enfoque tiene la oportunidad de cambiar drásticamente la forma en que se diseñan y fabrican los sistemas aeroespaciales y de defensa. Ya no se dedicará una sola línea de producción a un solo producto. En cambio, la producción será flexible. Además, si puede reducir el uso de herramientas, puede reducir los repuestos que se encuentran en el estante. Esta flexibilidad tiene impactos en toda la cadena de suministro, incluida la reducción del desperdicio debido a la caducidad de los materiales ”.
Bischoff :"Con un pequeño puñado de celdas SCRAM y diseños digitales, todo lo que tiene que tener a mano es materia prima, en lugar de docenas de herramientas fijas y materiales termoendurecibles de vida útil limitada".
Marrón :"Tenemos mucho camino por recorrer antes de que la producción se maneje realmente de esta manera, pero ahora puede ver claramente cómo es posible".
Resina
- ACEO® presenta una nueva tecnología para la impresión 3D con silicona
- Emirates adoptará la tecnología de impresión 3D para piezas de aviones
- Introducción a la impresión 3D con sinterización selectiva por láser
- Impresión 3D de TPU:una guía para la impresión 3D de piezas flexibles
- ¿Está lista la impresión 3D para la producción de piezas finales?
- Impresión del fusible 1 con el fusible 1
- Impossible Objects se asocia con BASF para la impresión 3D compuesta
- Broetje-Automation amplía la cartera de AFP para la producción de compuestos en serie
- Victrex y Bond se asocian para la impresión 3D de piezas PAEK
- VDMA desarrollará una hoja de ruta para la impresión 3D con hoja de ruta de fabricación
- Prácticas de trazabilidad para la producción de piezas de mecanizado de precisión