Avanzando en el demostrador de fuselaje multifuncional (MFFD)
La reducción de las emisiones de combustible y el consumo de energía, y la capacidad de producir aviones comerciales de pasillo único a un ritmo de al menos 60 por mes, están impulsando el desarrollo tecnológico de la asociación europea Clean Sky 2 para la próxima generación de aviones que surcan los cielos en 2035 y más allá. . Los materiales compuestos livianos y los procesos de fabricación más rápidos y respetuosos con el medio ambiente están haciendo realidad estos objetivos, especialmente para el proyecto Multifunctional Fuselage Demonstrator (MFFD).
El principal resultado de este proyecto, dirigido por Airbus (Hamburgo, Alemania) con socios del mundo académico y la industria de la aviación, es un demostrador de cañón de fuselaje de avión comercial de un solo pasillo, compuesto termoplástico y de 8 metros de largo, que será producido por 2022. El MFFD es una de las tres secciones de fuselaje a gran escala que se producen dentro de la Plataforma de demostración de aviones innovadores (IADP) de grandes aviones de pasajeros (LPA) de Clean Sky 2.
Iniciado en 2014, los objetivos del proyecto MFFD incluyen:
- Habilite tasas de producción de 60 a 100 aviones por mes
- Reducir el peso del fuselaje en 1,000 kilogramos
- Reducir los costos recurrentes en un 20%.
Para lograr estos objetivos, se están completando docenas de proyectos individuales y paquetes de trabajo, con dos estructuras principales que se están produciendo:una carcasa de fuselaje superior y una carcasa de fuselaje inferior, que se soldarán entre sí para formar el demostrador final. De hecho, la unión sin polvo (sin sujetadores ni agujeros) mediante soldadura es un componente importante del programa. Ambas mitades se fabrican a partir de un preimpregnado termoplástico de fibra de carbono de poliariletercetona (PAEK) de bajo punto de fusión Toray Cetex TC1225 de Toray Advanced Composites (Morgan Hill, California, EE. UU.). Según el Dr.-Ing. Lars Larsen, jefe de tecnologías de ensamblaje y unión en el Centro Aeroespacial Alemán (DLR; Augsburg, Alemania), ambas mitades probarán el uso de diferentes técnicas de fabricación.
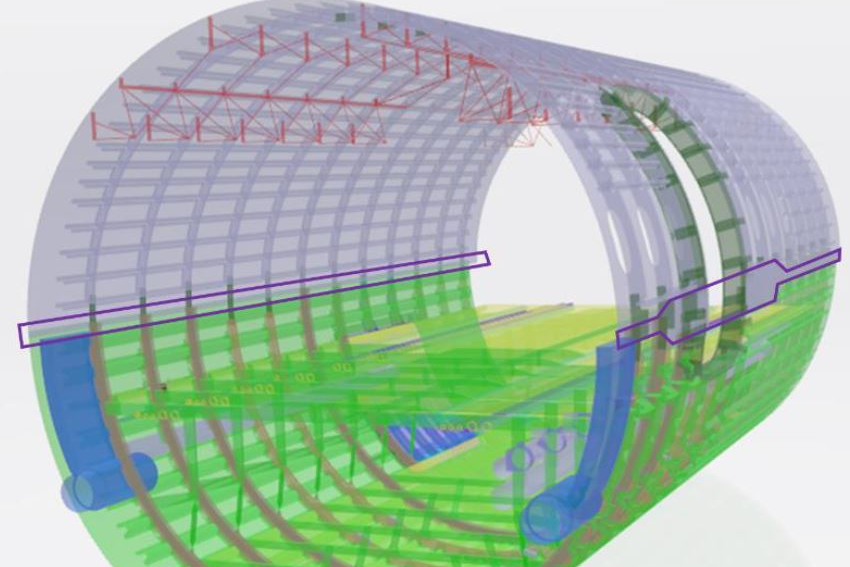
La sección inferior del fuselaje del MFFD se está produciendo a través del proyecto STUNNING (Fuselaje termoplástico multifuncional e integrado de SmarT), que a su vez tiene muchos proyectos debajo (como MECATESTERS, centrado en la soldadura por inducción). La sección inferior comprenderá la carcasa del fuselaje inferior con largueros y marcos soldados, la estructura del piso de la cabina y de carga y los elementos del sistema e interior relevantes.
STUNNING está dirigida por GKN Fokker (Papendrecht, Países Bajos) con socios clave Diehl Aviation (Laupheim, Alemania), Netherlands Aerospace Center (NLR; Amsterdam, Países Bajos) y la Universidad Tecnológica de Delft (TU Delft; Delft, Países Bajos). El proyecto tiene como objetivo madurar aún más los procesos de ensamblaje automatizados, las tecnologías de soldadura y fabricación de termoplásticos, el diseño integrado y el desarrollo de la fabricación y las arquitecturas de sistemas eléctricos avanzados.
“Nuestro impacto en la industria es doble:el nivel de automatización que estamos aplicando al ensamblaje del demostrador y el desarrollo de formas sostenibles de producir piezas”, dice el Dr. Bas Veldman, gerente de programa de GKN Fokker.
Según un artículo publicado por Veldman en febrero de 2020, el montaje modular del fuselaje inferior es clave para lograr el objetivo de tiempos de producción rápidos. Para fabricar el revestimiento principal del fuselaje, se colocan grandes preformas hechas de fibra de carbono / preimpregnado termoplástico mediante una máquina de colocación de cinta automatizada (ATL) calentada por ultrasonido o láser, pero no consolidada in situ. Los detalles se colocan mediante una máquina de colocación automática de fibra (AFP). Luego, los robots colocan las preformas en un molde de consolidación hembra y, después de embolsar, la piel se consolida en un autoclave. Según Veldman, también se están investigando los procesos fuera del autoclave. Los largueros y los marcos se soldarán a la piel.
“Originalmente, el plan era fabricar todas las piezas este año”, dice Veldman, pero debido a los retrasos relacionados con el coronavirus, “ahora también está pasando al próximo año. Pero tenemos bastantes piezas que ya se han completado ”, incluidas muchas de las piezas más pequeñas formadas a presión, como clips, puntales y soportes que se utilizarán para sujetar los asientos de los aviones y otros componentes. Enfatizando la fabricación sostenible, Veldman agrega que algunos de los clips se fabrican a partir de recortes reutilizados de otras partes del demostrador, a través de un proyecto Clean Sky 2 llamado ECO-CLIP.
A partir de principios de 2020, el consorcio que produce la carcasa superior de 8 metros de largo incluye a Airbus, Premium Aerotec (Augsburg, Alemania), que es el líder del diseño industrial y estructural; DLR, a cargo del desarrollo de la tecnología de laminado y soldadura; y Aernnova (Vitoria-Gasteiz, España), que produce los largueros.
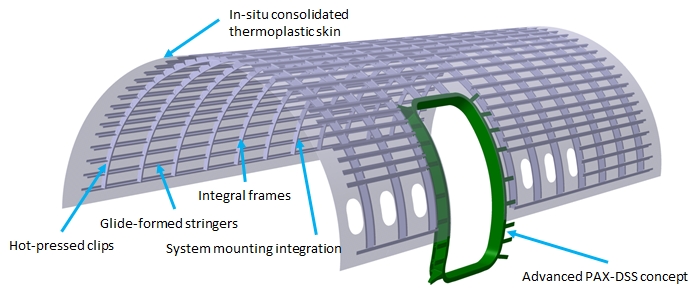
Para que la industria aeroespacial haga la transición a materiales termoplásticos más costosos, Larsen dice:"Tenemos que demostrar que podemos ahorrar costos durante la producción". La mitad superior del consorcio está desarrollando una nueva tecnología avanzada de colocación de fibra (AFP) con, en particular, consolidación in situ para la capa de revestimiento de fibra de carbono / PAEK, así como la industrialización de la soldadura ultrasónica continua y la soldadura por resistencia para la integración de los largueros, marcos y otros componentes, mejorando la seguridad y reduciendo los costos. DLR está construyendo por primera vez una carcasa de prueba previa a la demostración de 1 metro de largo para validar las tecnologías antes de que se construya el demostrador a gran escala, y planea tener la carcasa para la carcasa previa a la demostración fabricada para fines de 2020. Integración de los largueros están programados para principios de 2021.
Se espera que las versiones a gran escala de ambas mitades estén terminadas para fines de 2021. Una vez completadas, se soldarán en el demostrador final en el Instituto Fraunhofer de Tecnología de Fabricación y Materiales Avanzados IFAM (Stade, Alemania).
Resina
- Más allá de lo básico:aprendizaje automático y AM
- Las ventajas del diseño de aeronaves compuestas en aviones de todos los tamaños
- Por qué la automatización es el único camino a seguir para la fabricación
- 5 aplicaciones robóticas en la industria aeroespacial
- El panorama de la fabricación:mirar hacia atrás y hacia adelante
- Tres beneficios de trasladar la gestión de gastos a la nube
- Fabricación de la mitad superior del demostrador de fuselaje multifuncional (MFFD)
- La primera sección de fuselaje compuesto para el primer avión comercial compuesto
- Al servicio del mundo de los compuestos en Israel y los EE. UU.
- ¿Cuál es el voltaje directo del diodo?
- Generación de nitrógeno en la industria aeroespacial