El diseño de la compuerta trasera pone a prueba el devanado de filamento modificado
Las compuertas elevadoras automotrices, o las puertas traseras, han ido pasando lentamente de los metales a los compuestos durante décadas. Si bien no fue hasta 2013 que se comercializó la primera puerta trasera completamente de plástico / compuesto, menos la estructura de soporte de metal, la mayoría de las puertas traseras todavía cuentan con este componente de soporte en el que se unen revestimientos exteriores y paneles internos, particularmente en los modelos deportivos más grandes y pesados. vehículos utilitarios (SUV) y vehículos utilitarios cruzados (CUV) con puertas traseras más grandes.
Sin embargo, lo que bien podría ser la próxima evolución en compuertas levadizas debutó en 2019 en el Toyota Supra coche deportivo de Toyota Motor Corp. (Toyota City, Japón). Un marco compuesto de filamento enrollado reemplazó a un marco metálico y se dice que ofrece mayor rigidez y resistencia con un peso menor que las estructuras metálicas tradicionales, con una mayor flexibilidad de diseño, especialmente en espacios reducidos de embalaje. Según se informa, el proceso de bobinado de filamentos se ha modificado hasta tal punto que, a medida que crece el interés y proliferan las aplicaciones, puede cumplir con los objetivos de velocidad y costo de la producción de vehículos de mayor volumen. Así es como surgieron el diseño y la tecnología.
Fabricación trilateral
Magna International Inc. (Aurora, Ontario, Canadá) es un integrador de nivel 1 en América del Norte, pero en Europa, su subsidiaria Magna Steyr AG &Co. KG (Graz, Austria) también diseña y ensambla autos completos para OEM que necesitan fabricación adicional. capacidad.
Recientemente, Magna participó en un programa interesante en el que participaron los fabricantes de automóviles Toyota y BMW AG (Múnich, Alemania), que han trabajado de manera cooperativa en proyectos de diseño y fabricación desde 2013. Para su último esfuerzo, Toyota buscaba revivir su Supra placa de identificación y se había asociado con BMW para proporcionar diseño y puesta a punto para el vehículo y un automóvil hermano, el Z4 de 2 plazas de BMW . Los dos vehículos comparten los sistemas de motor, suspensión y dirección. Magna Steyr ensamblaría ambos autos en Graz, además de suministrar el Supra con asientos, paneles de carrocería, pestillos de puertas y compuertas levadizas. Si bien hay mucha innovación en ambos autos, la puerta trasera incorporada en el Supra es donde la innovación en el diseño de compuestos es más evidente.
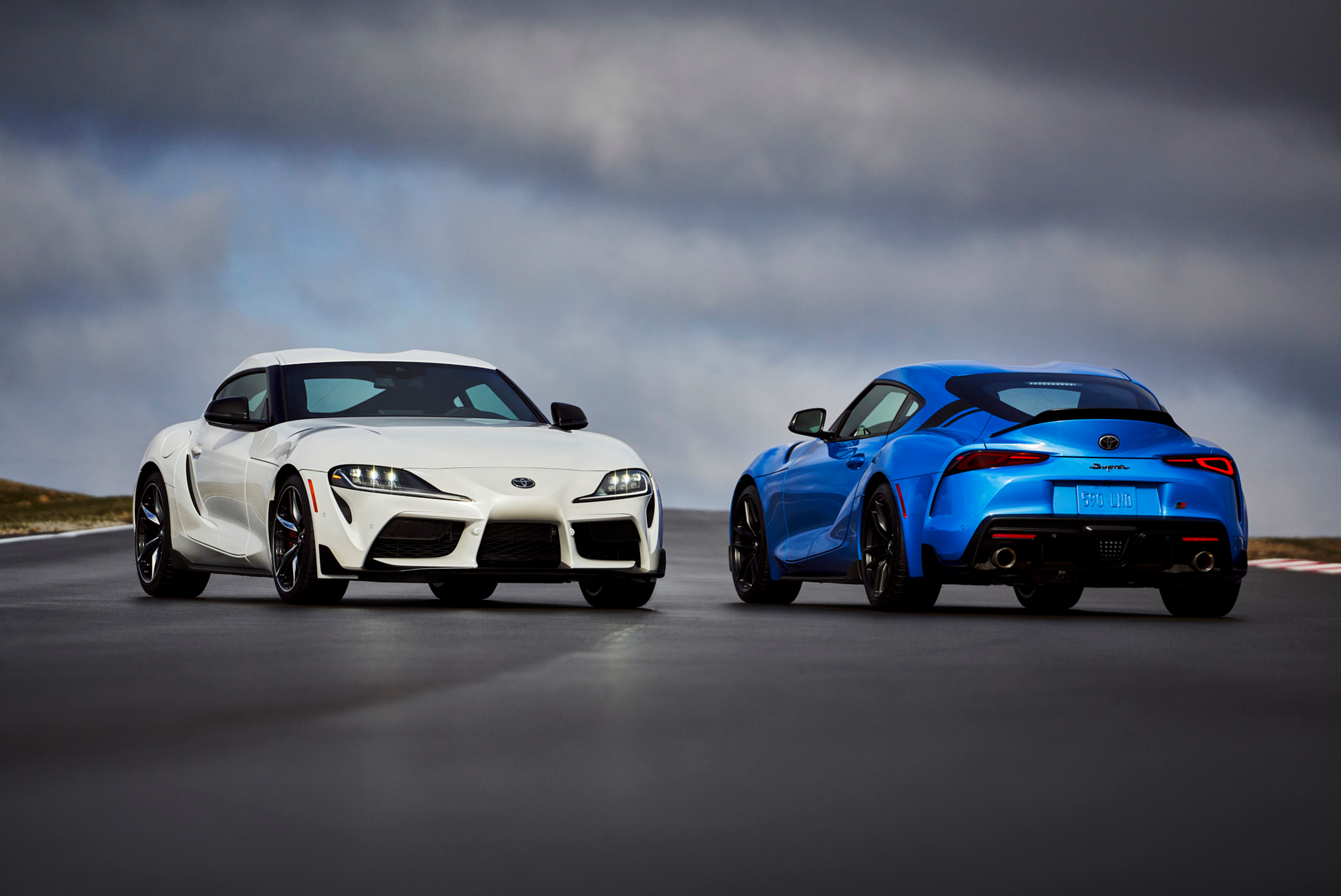
Manchester de Bohemia
Años antes de la participación de Magna en el 2020 año modelo Supra , su operación en Liberec, República Checa, había estado explorando tecnologías para marcos espaciales compuestos para varias aplicaciones potenciales. Por suerte, la zona tiene una rica tradición como centro textil líder y una vez fue conocida como "el Manchester de Bohemia". El equipo de Liberec buscó una arquitectura tecnológica que soportara cargas elevadas, masa total reducida, mantuviera tolerancias dimensionales estrictas y pudiera producirse en un proceso con alta repetibilidad y reproducibilidad (R&R) para satisfacer las demandas de rendimiento y fabricación de los fabricantes de automóviles europeos.
“Llegamos a la conclusión de que necesitábamos un producto termoestable con alta estabilidad térmica y dimensional”, recuerda Riad Chaaya, director de la línea global de productos de Magna:compuertas elevadoras compuestas. “También sabíamos que necesitábamos una forma cerrada con la capacidad de producir secciones transversales de formas y espesores variables, necesarias para optimizar el rendimiento mecánico, el espacio del paquete, la masa y el costo, que pudiera producirse en un proceso capaz de fabricar 150.000 piezas al año. Analizamos muchas tecnologías, incluido el moldeo por soplado, el trenzado y el devanado de filamentos, pero ninguna satisfizo nuestras necesidades. Después de muchas pruebas, seleccionamos el devanado de filamentos como la mejor combinación para lo que queríamos, ya que nos dio control de las orientaciones y el número de filamentos para extraer el módulo más alto con el peso más bajo ”.
A pesar de los muchos beneficios, existía la preocupación de que el devanado de filamentos fuera demasiado lento para la producción automotriz convencional. Además, el equipo necesitaba un método para comenzar y finalizar el proceso de enrollado con el fin de crear un marco de forma cerrada. Afortunadamente, aunque el equipo no tenía antecedentes de bobinado de filamentos, el legado de fabricación textil de Liberec significaba que la comunidad local estaba llena de expertos en mechas y bobinado de filamentos.
“Por suerte para nosotros, estos expertos tuvieron la pasión de resucitar sus conocimientos tradicionales para ayudarnos a aplicarlos de nuevas formas para satisfacer las necesidades automotrices de gran volumen”, agrega Dr.-Ing. Josef Půta, líder tecnológico de Magna Exteriors - República Checa.
“Debido a que el bobinado de filamentos tradicional era demasiado lento para nuestras necesidades, nosotros y nuestros socios buscamos muchas formas de hacerlo funcionar más rápido”, recuerda Lukáš Strouhal, director de industrialización de Magna Liberec. “Consideramos formas de acelerar cada paso del proceso y de hacer las cosas de manera bastante diferente. Si bien no podemos decir mucho sobre cómo lo hicimos, podemos decir que logramos enormes mejoras en la velocidad, de modo que nuestro proceso modificado podría convertirse en 'apto para automóviles' ".
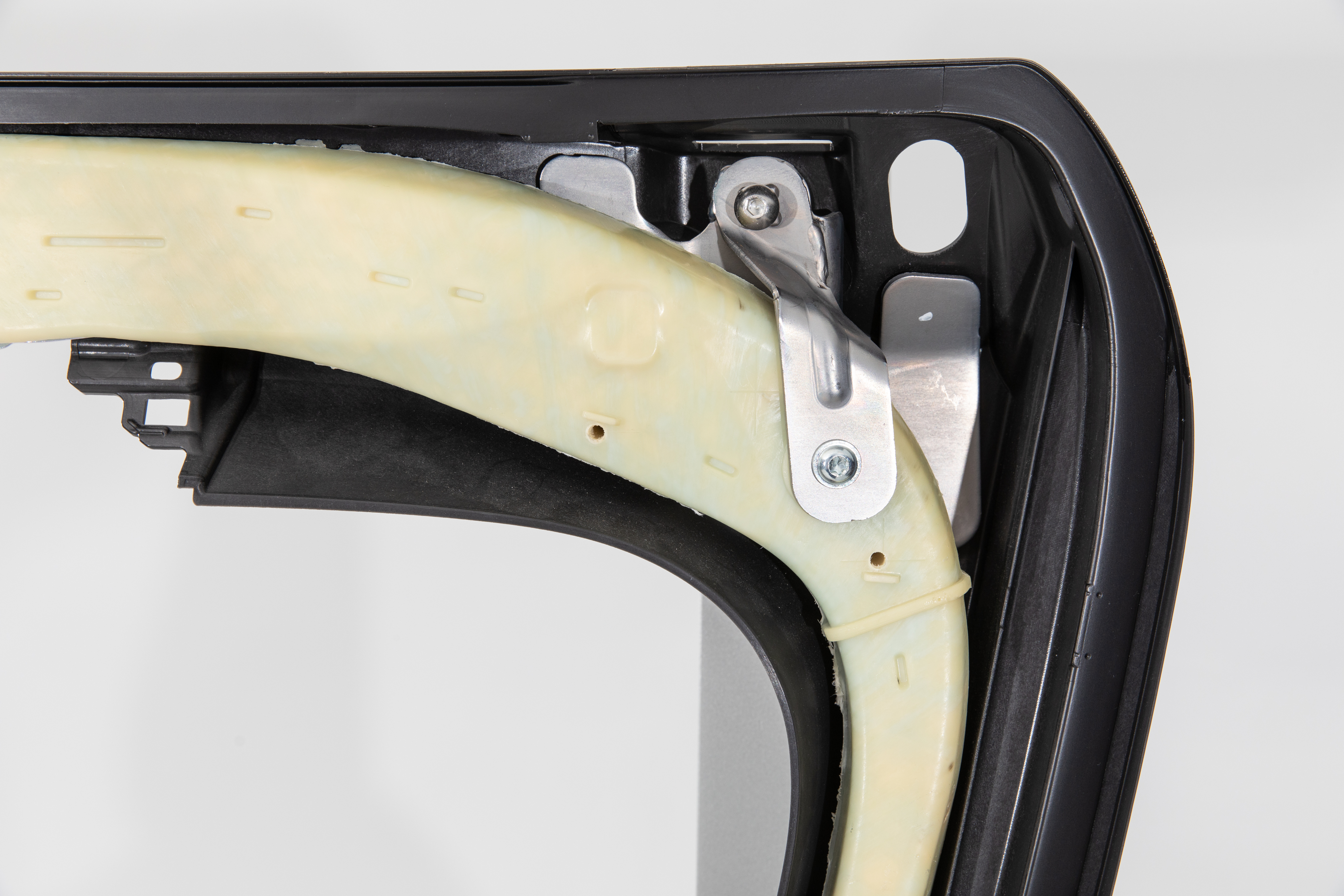
Magna y sus socios exploraron muchos sistemas de resina, incluidos epoxi, poliuretano (PUR) y una mezcla de PUR / éster de vinilo, además de una variedad de refuerzos, desde vidrio hasta fibras de carbono y basalto. El sistema final cuenta con PUR y fibras de vidrio, que ofrecen el mejor equilibrio entre eficiencia, rendimiento, costo y velocidad de producción de la fibra.
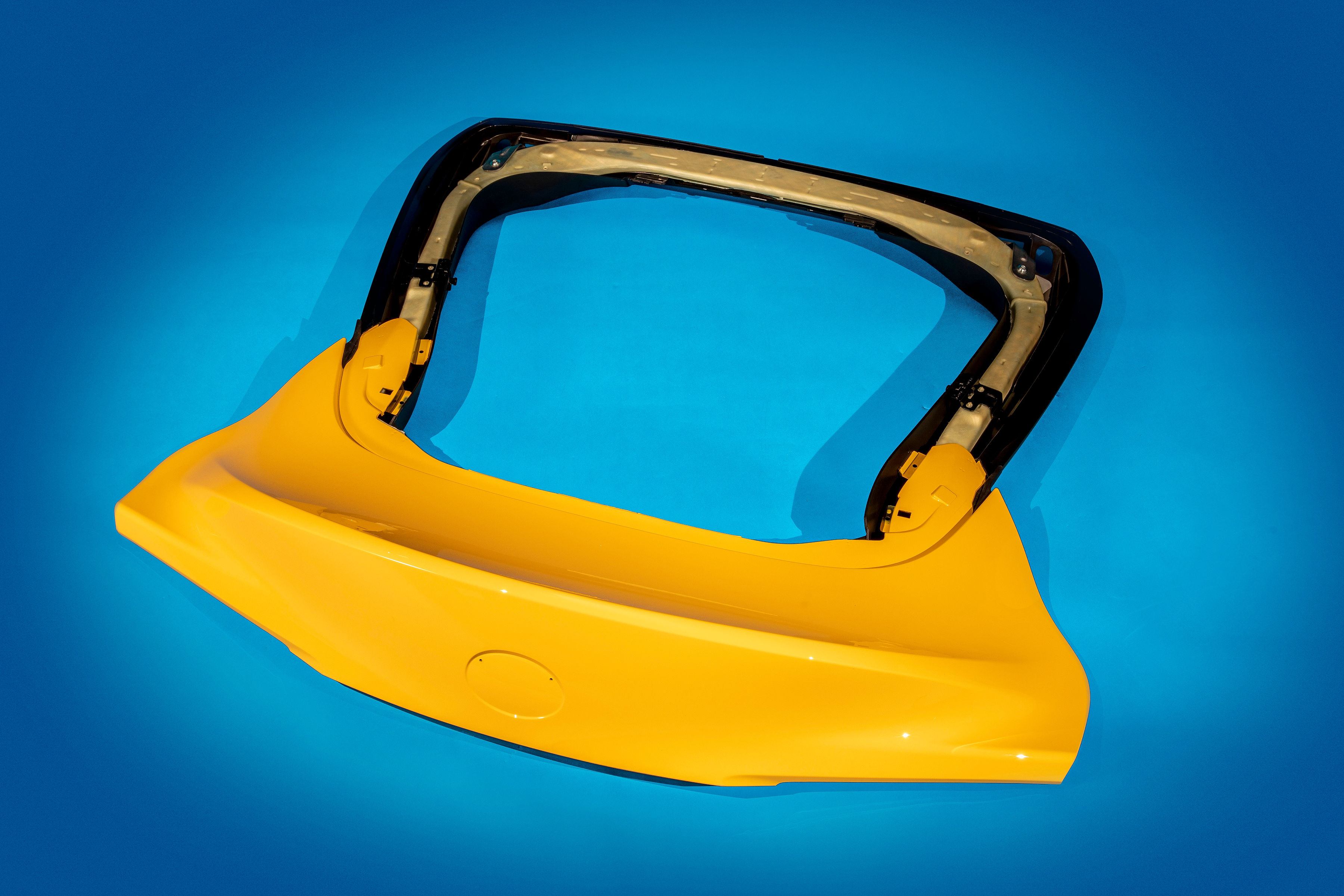
El marco de espacio enrollado de filamento genérico de Magna se produce en tres pasos, cada uno cuidadosamente optimizado para la velocidad. En primer lugar, se produce un núcleo de PUR celular rígido mediante moldeo por inyección de reacción (RIM); segundo, ese núcleo, que funciona como mandril, está enrollado con fibra de vidrio; y tercero, esa estructura de la herida se infunde luego con PUR y se consolida en el proceso de moldeo por transferencia de resina a alta presión (HP-RTM). Se tiene cuidado para garantizar que el núcleo no se colapse durante la infusión / consolidación. Půta explica que se trabajó mucho para especificar los tipos de mechas, tamaños y resinas utilizados, lo que requiere un trabajo cercano con los proveedores en las modificaciones del material, así como para determinar el número de devanados y la orientación de los filamentos en cada capa. No es sorprendente que la empresa haya obtenido numerosas patentes que cubren todo, desde el diseño y la producción de núcleos, hasta la máquina bobinadora de filamentos, además de secretos comerciales adicionales que guardan de cerca.
“Hemos realizado múltiples innovaciones en cada paso del proceso y producto”, explica Strouhal. "Podrías romper uno de nuestros marcos, ver las formas y geometrías utilizadas, y aún te preguntarías por qué y cómo lo hicimos".
Aunque el equipo de Magna Liberec no había desarrollado su tecnología de estructura espacial para una aplicación en particular, estaban a punto de tener una oportunidad interesante para usarla.
Puerta trasera desafiante
Magna tiene una larga trayectoria en la producción de compuertas elevadoras para vehículos de pasajeros. Según se informa, la compañía construyó las primeras compuertas elevadoras totalmente de olefina en América del Norte y Europa para el BMW i3 2013 automóvil urbano eléctrico, y diseñé y construyó una puerta trasera levadiza totalmente de olefina de última generación para el Jeep Cherokee 2019 de FCA NA LLC (Auburn Hills, Michigan, EE. UU.) SUV. Dado que la producción de la compuerta levadiza fue un entregable para el Supra Magna no solo se basó en el trabajo realizado en Liberec, sino también en su larga historia de conversión de estructuras metálicas de compuertas levadizas en materiales compuestos y plásticos.
"El Supra La compuerta levadiza ofrecía una serie de desafíos inmediatos ”, recuerda Chaaya. “Primero, el espacio del paquete era muy limitado, lo que significa que las tolerancias eran muy ajustadas y los valores del coeficiente de expansión térmica lineal deben manejarse con cuidado para mantener las puertas traseras abriéndose y cerrándose libremente. En segundo lugar, la forma de esta puerta fue aún más desafiante. Toyota no solo quería una puerta trasera más liviana, sino que tenía requisitos de estilo muy específicos sobre cómo se cubría la parte trasera del vehículo. En tercer lugar, con los volúmenes de fabricación proyectados del vehículo, las herramientas para lograr esa forma en metales serían muy costosas. De hecho, llegamos a la conclusión de que el marco de la puerta trasera no se podía producir en una sola pieza de metal y aún así cumplir con los requisitos de diseño y rendimiento de Toyota. Eso significaba que el marco espacial tenía que estar hecho de compuestos y, más específicamente, compuestos termoendurecibles ".
La piel exterior sería un panel de TPO reforzado con talco moldeado por inyección pintado para manejar la forma agresiva, mientras que el panel interior sería de polipropileno (PP) de vidrio largo; ambos se unirían al marco con un adhesivo estructural 2K PUR. Chaaya agrega que se hizo mucho trabajo para optimizar el marco espacial y completar la puerta trasera para cumplir con los requisitos de carga torsional. Uno de los primeros desafíos fue encontrar una manera de simular con precisión las propiedades del material para lograr una correlación precisa entre los resultados predichos y los medidos.
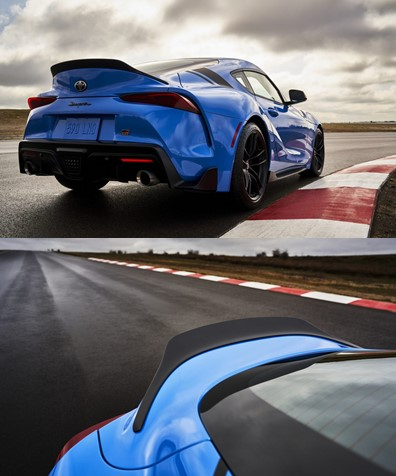
“Fue una lucha difícil conseguir una buena correlación con nuestros modelos de materiales, ya que teníamos que simular cada capa de bobinado e incorporar la forma, los radios y los propios requisitos de bobinado”, añade. “Aunque comenzamos con un 20% de descuento, después de muchos ajustes y de determinar la mejor manera de mejorar nuestra rigidez, nuestras predicciones finales fueron muy cercanas. En un marco tan grande, también logramos mantener las tolerancias dimensionales en 1 milímetro ”.
Muchos beneficios
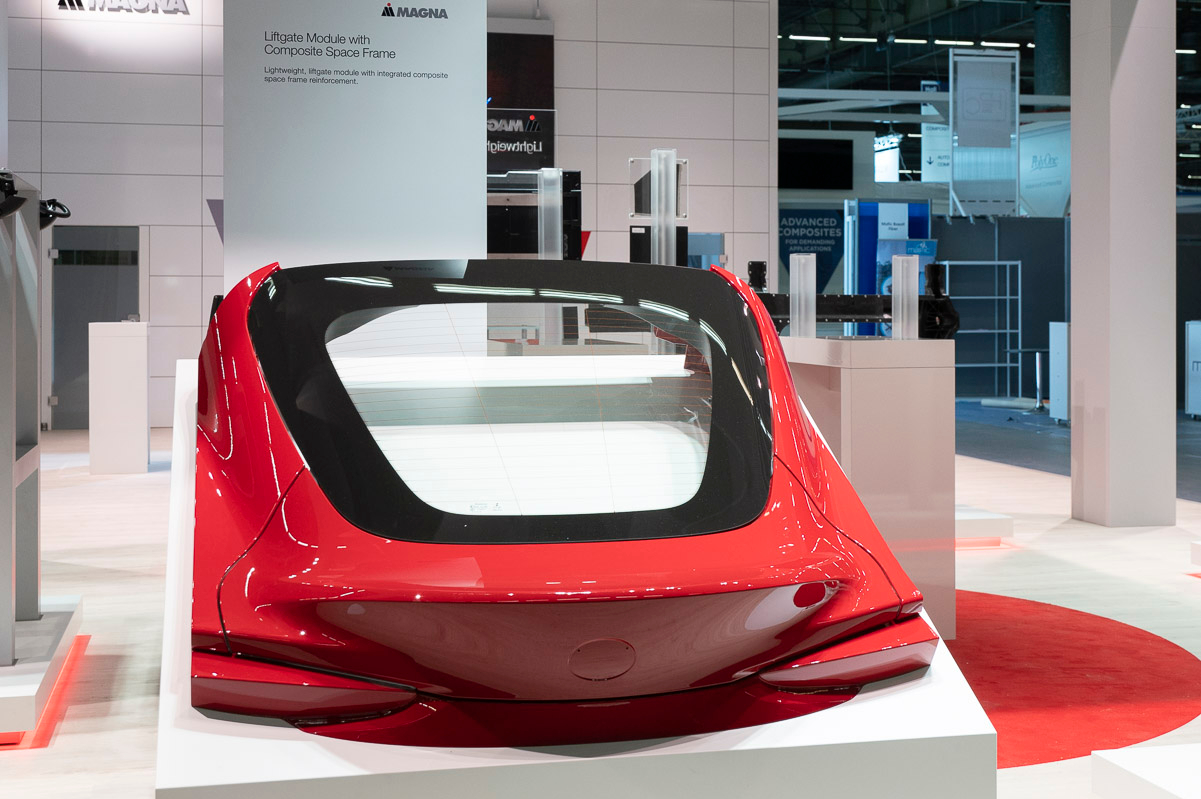
El marco final en forma de rosquilla presenta diámetros y espesores de pared variables en todas partes, pero tiene un diámetro nominal de 50-60 milímetros. Aparte de un pequeño soporte en la esquina y accesorios duros como pestillos y bisagras, además de papel de aluminio para conectar a tierra las antenas integrales, todo el marco, que mide 104 x 111 centímetros, es completamente compuesto. Incluso los soportes de "oreja", que se utilizan para conectar el panel de moldura interior a la mitad inferior de la puerta trasera, son compuestos y fabricados mediante HP-RTM. Aunque el marco compuesto es un 10% más liviano que un marco de metal comparable, los efectos de descomposición masiva significan que la puerta trasera completa es ~ 20-25% más liviana que una puerta trasera metálica. Las compuertas levadizas más livianas requieren menos esfuerzo para que los consumidores se abran / cierren, son más fáciles de instalar para un trabajador durante el ensamblaje del vehículo, ahorran combustible durante la vida útil del vehículo y brindan lo que Strouhal describe como "un sonido sólido increíble" cuando se cierra la compuerta levadiza. El sistema compuesto también eliminó pasos como el dobladillo de los bordes y los puntos / juntas de soldadura requeridos con las compuertas elevadoras metálicas.
Chaaya insinúa que su compañía tiene en marcha otro importante proyecto automotriz de bobinado de filamentos. También dice que Magna ve otros usos para la tecnología más allá de las compuertas elevadoras. “Puertas, cubiertas, capós, FEM (módulos frontales) e incluso vehículos autónomos, como un autobús que se compone de un marco envuelto en vidrio - podría usar un marco de espacio así ”, agrega. “Y ni siquiera tendría que estar oculto. Si usáramos tejido de fibra de carbono, sería una señal de prestigio dejar esa hermosa superficie expuesta y no esconder el marco en el interior ”.
Resina
- La guía para principiantes sobre la fabricación de filamentos fundidos (FFF)
- El papel del diseño asistido por computadora (CAD) en la impresión 3D
- Los desafíos del diseño de productos
- El triodo
- Qué es el diseño de sistemas integrados:pasos en el proceso de diseño
- Diseño industrial en la era de IoT
- Optimización de la línea de alimentación de RF en el diseño de PCB
- Las nuevas tecnologías y los mercados en Mundial de bobinado de filamentos caso
- Devanadora de filamento Roth para facilitar los principales recortes de peso / costo de Ariane 6
- Los beneficios de la creación de prototipos de PCB
- Conozca la importancia de la lista de materiales en el diseño de PCB