Desafíos del bobinado de cinta asistido por láser de compuestos termoplásticos
Los compuestos termoplásticos (TPC) se han promocionado ampliamente en los últimos años debido a su alto potencial para aumentar las tasas de producción y permitir la reducción de peso. Uno de los temas más discutidos para aumentar las tasas de producción con TPC es la consolidación in situ (ISC) durante la colocación automatizada de fibra y cinta (AFP / ATP).
En realidad, ISC se demostró por primera vez con estructuras restringidas, como tubos, y continúa ofreciendo un gran potencial para recipientes a presión y tanques de almacenamiento con envoltura. Estas estructuras se pueden producir mediante el devanado de cinta asistido por láser (LATW), que comprende una máquina de colocación de cinta asistida por láser (LATP) y un mandril giratorio (Fig. 1).
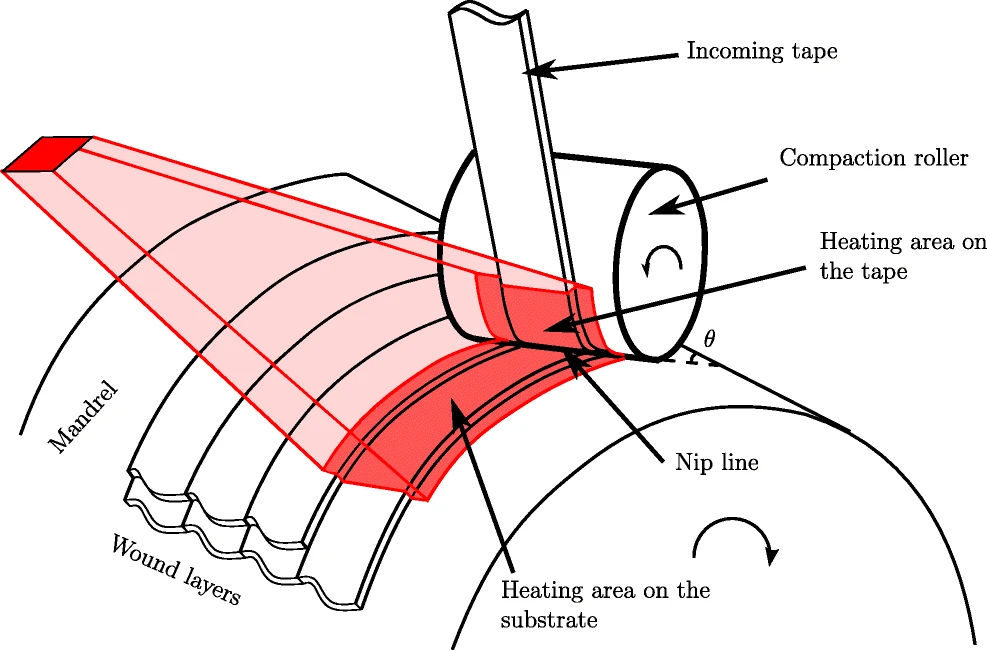
El cabezal AFP / ATP se instala en un robot CNC de seis ejes y utiliza un láser para calentar la cinta entrante y el sustrato para derretir el polímero termoplástico. Luego, la cinta se presiona sobre el sustrato con un rodillo para promover la adhesión y consolidación de las capas intermedias.
Estrategias de primera mano
Como cualquier proceso de fabricación aditiva, la primera capa en LATW es un problema que debe abordarse. Para un tubo producido en un mandril de metal (se prefiere el aluminio), se debe considerar la extracción del mandril después del enrollado y se debe aplicar un agente de liberación.
Otra consideración es la fijación. Si se aplica enrollamiento de aro a la primera capa (en comparación con una disposición helicoidal o axial, Fig. 2), la cinta adhesiva se puede colocar manualmente al principio y al final de la hilada para mejorar la estabilidad y la adhesión a la cinta entrante. Si se requiere una colocación helicoidal o axial, entonces se deben aplicar anillos de cinta completos y fijarlos en los bordes del cilindro, utilizando cinta adhesiva para evitar deslizamientos.
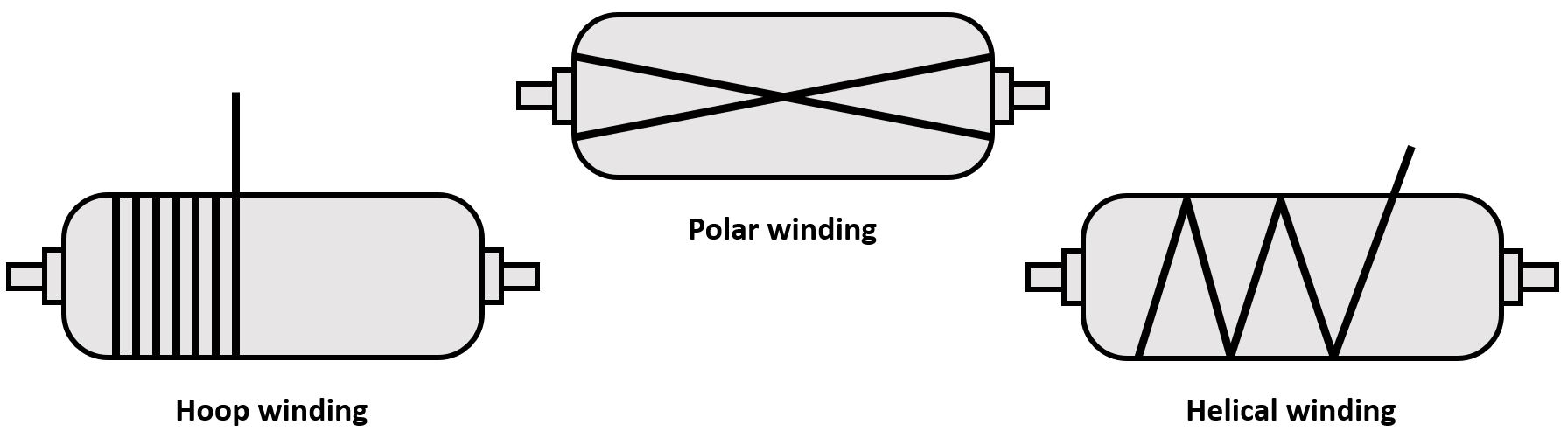
Para un recipiente a presión Tipo IV (revestimiento de plástico con envoltura de compuesto de fibra de carbono), o cuando se envolvía una tubería de plástico, la cinta entrante se fusionará con el revestimiento. Esto elimina la necesidad de fijar con cinta adhesiva, pero el revestimiento de plástico y la cinta TPC deben tener el mismo polímero base para asegurar una unión adecuada.
Pueden surgir problemas al calentar el revestimiento de plástico. Por ejemplo, si no puede absorber el calentamiento del láser, o si se usa un mandril de metal, considere ajustar el ángulo del láser para calentar completamente la cinta entrante. En otras palabras, en lugar del posicionamiento típico para que el láser se distribuya entre la cinta entrante y el sustrato (Fig. 1), incline el láser más hacia La cinta. Esto evitará los reflejos del láser, garantizará un calentamiento más uniforme de la cinta y reducirá el consumo de energía.
La distribución del láser cambia con el ángulo de la capa o la geometría cambiante
Como se describió anteriormente, normalmente durante los procesos LATP y LATW, el láser se distribuye entre la cinta entrante y el sustrato. Esta distribución es constante en los casos en que la geometría del radio y la dirección de colocación son constantes. Sin embargo, hay algunas consideraciones. Por ejemplo, durante un axial colocada en un mandril tubular (que sería aproximadamente equivalente al molde plano en la Fig. 3), la cinta entrante recibirá el mismo radiación en comparación con una colocación de aro, mientras que el sustrato recibirá más proyección láser que en una bandeja de aro. Tenga en cuenta que esto es insignificante en tubos de gran diámetro.
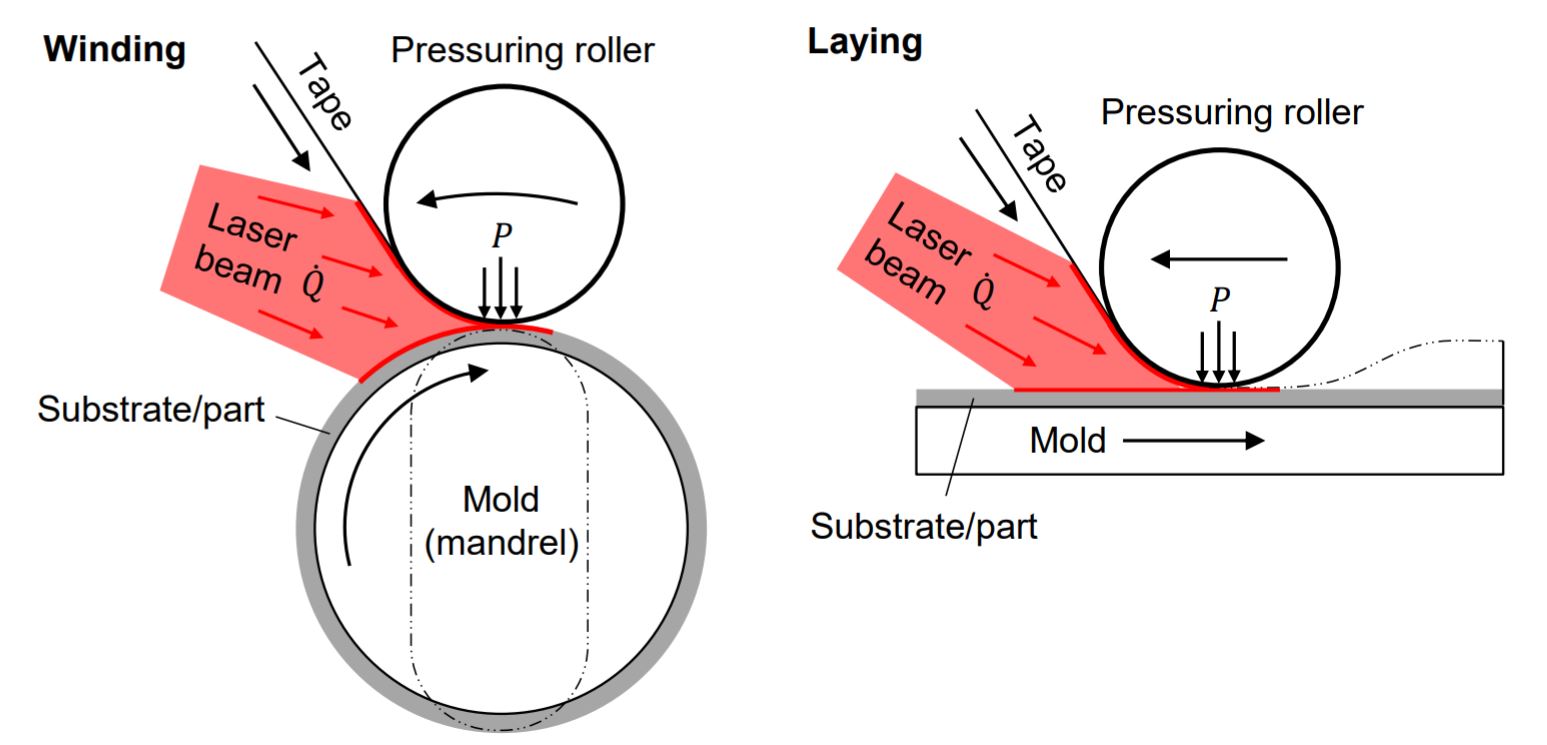
Durante el calentamiento, la cinta termoplástica se extiende y se vuelve más ancha y más delgada, dependiendo de la temperatura y la velocidad de laminación (tiempo de calentamiento), debido a la viscosidad reducida del polímero. En un sistema con control de circuito cerrado, donde temperatura se mantiene constante en el área de calentamiento:una disposición axial terminará con una cinta más ancha que en una disposición de aro. Alternativamente, en un sistema con potencia constante control, el laminado axial se desarrollará a temperaturas más bajas y, por lo tanto, la cinta se ensanchará menos. Es importante comprender y abordar esto porque pueden producirse cambios desiguales en las dimensiones de la cinta y causar espacios no deseados y superposiciones que podrían aumentar el contenido vacío.
Al envolver tubos, la geometría del radio es constante, pero esto cambia al envolver recipientes a presión debido a las cúpulas de los extremos. Al entrar o salir de estos domos, el robot se ralentiza y el tamaño del punto láser disminuye en el sustrato. Ambas acciones pueden provocar un fuerte aumento de temperatura, lo que puede provocar secciones más delgadas, diferentes propiedades del material o incluso dañar el polímero.
Otra consideración es que a medida que las capas de fibra de la pieza se acumulan durante el bobinado, las dimensiones del núcleo sobre el que se está enrollando (mandril más capas hasta ahora) están cambiando. Por lo tanto, los ángulos de colocación deben ajustarse para evitar espacios. Algunos proveedores pueden ofrecer un sistema LATP / LATW con software que actualiza el diámetro del mandril. De lo contrario, el devanado deberá inspeccionarse manualmente o con un sistema de inspección en línea y corregirse según sea necesario.
Si bien abordar las consideraciones anteriores ayuda, no es posible lograr la eliminación del 100% de defectos como espacios, superposiciones y variaciones de espesor. Por lo tanto, el proceso de bobinado debe desarrollarse para lograr los límites de diseño de la pieza en lugar de buscar una "pieza perfecta", lo que puede agregar costos innecesarios.
Maximización de propiedades mecánicas, adhesión entre capas y cristalinidad
La gestión térmica es un factor clave para lograr una adhesión adecuada entre capas, así como una cristalinidad potencial total en la matriz termoplástica. Las primeras capas están cerca del mandril, que actúa como disipador de calor. Esto puede prevenir la interdifusión molecular y promover una mala adhesión entre capas, una baja cristalinidad y un mayor contenido de huecos. Para superar este desafío, se debe considerar reducir la velocidad de laminado, aumentar la temperatura y ajustar el ángulo del láser para permitir un tiempo de calentamiento más prolongado para asegurar la difusión molecular.
Sin embargo, esto no asegura una cristalinidad total. Esto se debe a que la difusión molecular (reformar los reenredos moleculares después de la fusión durante el enfriamiento) es un proceso mucho más rápido que la cristalización, donde las moléculas se alinean para formar una estructura cristalina ordenada. Si la pieza que se está fabricando es delgada (aproximadamente menos de 2 milímetros), se esperaría una cristalinidad más baja que para una pieza más gruesa, que recibe más pasadas de consolidación y menos pérdida de calor hacia el mandril. Tanto para como delgadas piezas gruesas, considere velocidades de laminado más lentas para las capas iniciales.
Para alcanzar la cristalinidad total, considere lo siguiente:
- Después de enrollar, recocer (remojo en calor) a una temperatura entre la matriz termoplástica T g (temperatura de transición vítrea) y T m (temperatura de fusión). Como regla general, el medio entre las dos temperaturas proporciona la cinética de cristalización más rápida.
- Use un mandril calentado que promoverá la cristalinidad de las capas iniciales. Esto no siempre es posible y puede resultar más caro. Si un mandril calentado es utilizado, asegúrese de tener en cuenta que el mandril puede sufrir expansión térmica.
- Programe pasadas para la consolidación; en otras palabras, incluya pasadas de bobinado sin cinta entrante pero con láser totalmente proyectado sobre el sustrato. Esto se hace principalmente en las últimas capas que reciben menos pasadas, pero también se puede hacer en las primeras capas para mejorar la adhesión entre capas.
Dimensiones de la cinta:flexibilidad de diseño y tasas de producción
Las dimensiones de la cinta son un parámetro crucial en el bobinado de la cinta. Obviamente, recibir un ancho y un grosor de cinta constantes del proveedor permitirá obtener productos uniformes y repetibles. Sin embargo, las dimensiones de la cinta también definen la flexibilidad del diseño. Por ejemplo, con una disposición axial sobre un mandril tubular, el ancho de la cinta debe ser lo suficientemente estrecho para adaptarse a la curvatura del mandril. Cuanto mayor sea el diámetro del mandril, más ancha será la cinta que se puede utilizar. Una cinta más ancha significa un rendimiento más rápido, mientras que una cinta más estrecha es más amigable con el diseño, ya que es más compatible con los cambios de curvatura y más fácil de dirigir.
Aunque hay más problemas y desafíos con LATW, es posible obtener buenas piezas, y este método de fabricación continuará avanzando a medida que los tubos y tanques compuestos se utilicen para aplicaciones de almacenamiento de hidrógeno y otras aplicaciones de gas.
Acerca del autor
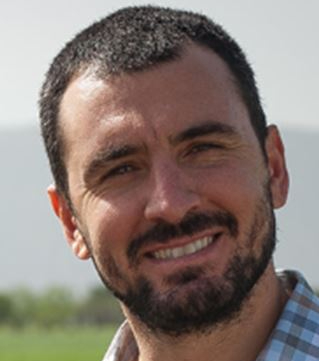
Yehiel Shaham
Yehiel Shaham es un ingeniero de plásticos y polímeros con casi 12 años de experiencia en el desarrollo y fabricación de termoplásticos de las principales empresas israelíes de defensa y plásticos. Durante 2016-2020, fue ingeniero líder de compuestos termoplásticos (TPCs) en RAFAEL, donde se especializó en TP-AFP. Actualmente, su objetivo es promover los TPC en la industria israelí.
Resina
- Covestro intensifica la inversión en compuestos termoplásticos
- Cinta unidireccional termoplástica de fibra de carbono basada en PPS
- Fraunhofer IPT desarrolla compuestos termoplásticos en almacenamiento de hidrógeno, álabes de motores y más
- Compuestos termoplásticos en Oribi Composites:CW Trending, episodio 4
- El proyecto RECONTRAS valida el uso de microondas y soldadura láser para obtener composites reciclables
- OTOMcomposite desarrolla software para la producción de Composites 4.0 utilizando colocación de cinta asistida por láser y bobinado
- Solución de problemas de termoformado de compuestos termoplásticos
- ACMA lanza el programa Thermoplastic Composites Conference 2020
- INOMETA invierte en una nueva tecnología de bobinado de cinta asistida por láser
- Compuestos termoplásticos:vista panorámica
- Soldadura de compuestos termoplásticos