Efecto de los medios fluidos sobre la eliminación de material y los defectos del subsuelo Evolución del cobre monocristalino en el proceso de nanocorte
Resumen
El efecto de los medios fluidos sobre la eliminación de material y la evolución de los defectos del subsuelo en el proceso de nano-corte de cobre monocristalino se investiga mediante simulación de dinámica molecular. En este artículo, el mecanismo de remoción de la viruta y el mecanismo de formación de la superficie mecanizada se investigan mediante el análisis de la migración atómica y la evolución de la dislocación de la pieza de trabajo durante el proceso de nano-corte con el uso de medios acuosos. Se investiga la distribución de la temperatura y la transformación estructural del cristal del defecto subsuperficial, que se analizan mediante el parámetro de centro-simetría y métodos de análisis de vecinos comunes. Los resultados muestran que el material de la pieza de trabajo se elimina mediante la acción de corte por extrusión de la herramienta de corte. La lubricación del medio acuoso puede reducir la fuerza de corte y disminuir la altura de la viruta de corte. Particularmente, la acción de enfriamiento del medio fluido da como resultado la formación de un defecto típico "límite similar al grano" en el subsuelo de la pieza de trabajo. Y la temperatura de la pieza de trabajo tiene una clara disminución durante el proceso de nanocorte con el uso de medios fluidos.
Antecedentes
El corte con diamante se considera una técnica eficaz para la generación de superficies nanoestructuradas con precisión dimensional submicrométrica y acabado superficial nanométrico [1]. El mecanismo de eliminación de material y formación de la superficie mecanizada a nanoescala es fundamental para la mejora de la precisión del mecanizado en el proceso de corte nanométrico. En los primeros estudios, los investigadores se centraron en la deformación del material [2, 3, 4], la evolución del defecto superficial [5, 6, 7], la tensión residual [8, 9] y la transición de la fase cristalina [10, 11] durante el proceso de nanocorte en un entorno de vacío. Sin embargo, en el corte nanométrico real de material metálico, el papel del fluido refrigerante y lubricante es muy crucial para mejorar el rendimiento del mecanizado [12]. Por lo tanto, es necesario estudiar la influencia de los medios fluidos en el mecanismo de remoción de material y la evolución de defectos subsuperficiales en el proceso de nano-corte.
En los últimos años, el mecanismo de mecanizado del proceso de nanocorte se ha investigado ampliamente mediante simulación de dinámica molecular (MD), que ha demostrado ser un método eficaz para estudiar el proceso de corte nanométrico. Por ejemplo, el efecto de la recuperación y el flujo lateral sobre la generación de la superficie y la transformación de fase en el nanocorte es estudiado por Fang [13]. Y se encuentra que la supresión del flujo lateral es una forma eficaz de mejorar la rugosidad superficial generada en el nanocorte. Urbassek [14] adoptó la simulación MD para estudiar el rayado de metales nanocristalinos y encontró que la orientación del grano genera un efecto dominante en la forma de acumulación y también influye fuertemente en el coeficiente de fricción. Sharma [15] investigó el efecto de seis orientaciones de cristal diferentes sobre el mecanismo de deformación del material, los defectos del subsuelo, las fuerzas de corte, la energía de corte específica, el efecto de arado y la rugosidad de la superficie en el corte a nanoescala. Luo [16] demostró la transferibilidad de la forma mediante el uso de herramientas de diamante de múltiples puntas a nanoescala en el torneado de diamantes para la fabricación a escala de nanoestructuras.
La formación de defectos subsuperficiales y la rugosidad de la superficie del nanocomponente pueden limitarse mediante una selección razonable de parámetros de corte, como la dirección de corte, la profundidad de corte, la velocidad de corte y la geometría de la herramienta. Sin embargo, no puede tener éxito en inhibir la formación de defectos superficiales y mejorar la calidad de la superficie a partir del mecanismo de generación. Además, estas investigaciones se centran en el proceso de nanocorte en un entorno de vacío. En realidad, en el corte nanométrico, la atmósfera y el medio líquido refrigerante existían entre la herramienta y la pieza de trabajo, lo que puede afectar el mecanismo de nanocorte y la calidad de la superficie de la nanoestructura.
Con base en la consideración anterior, muchos académicos llevaron a cabo la investigación sobre el proceso de nano-mecanizado con el uso de medios fluidos. Por ejemplo, Mylvaganam [17] exploró el efecto de O 2 en la nano-indentación de silicio cúbico de diamante usando simulación MD y encontró que el O 2 La molécula se disocia en átomos de oxígeno y forma enlaces químicos con átomos de silicio. Rentsch [18] descubrió que el fluido de corte tiene un gran efecto en la distribución de la tensión y la temperatura y señaló que el fluido de corte puede reducir el desgaste de la herramienta. Liu [19] estudió la influencia de las moléculas atmosféricas en la calidad de la superficie y el desgaste de las herramientas en el nanocorte. Los resultados indicaron que la fuerza de corte disminuye y el desgaste de la herramienta se reduce debido a la lubricación de las moléculas atmosféricas. Singh [20] investigó la influencia del fluido de corte de nanopartículas en el proceso de remoción de metales. Wang [21] discutió el efecto de las moléculas de agua sobre el comportamiento tribológico y las mediciones de propiedades en los procesos de nano-indentación y encontró que la participación de moléculas de agua hace que la fuerza de indentación inicial aumente y la mayor fuerza de indentación disminuya. Chavoshi [22] estudió nano-arañazos a alta temperatura de silicio monocristalino en condiciones de oxígeno reducido, y no se observaron restos de fases de silicio a alta presión en la simulación.
De la literatura disponible, las investigaciones previas sobre el proceso de nano-corte utilizando medios fluidos se basan en los modelos de simulación de pocas moléculas o nanopartículas, que se ubica en el área de interfaz herramienta-chip. Sin embargo, no se agrega ningún medio fluido en otras áreas, y la lubricación del medio fluido se analiza de forma restringida. Debido a la insuficiencia de medios fluidos en los modelos, la acción de enfriamiento de los medios fluidos no afecta el proceso de nano-corte, mientras que la acción de enfriamiento de los medios fluidos es tan importante como la acción de lubricación en la precisión del mecanizado y la calidad de la superficie.
Por lo tanto, en este documento, la herramienta de corte y la pieza de trabajo están completamente rodeadas por los medios de fluido de corte que no solo existen en el área de acción de la interfaz herramienta-viruta, sino que también existen en las áreas de la superficie de la pieza de trabajo, la superficie mecanizada y el área posterior. de la herramienta. Por lo tanto, se puede investigar la lubricación adecuada del medio fluido entre la herramienta de corte y la pieza de trabajo. Además, los medios fluidos se establecen como una temperatura constante durante el proceso de nano-corte, y la acción de enfriamiento de los medios fluidos también se puede estudiar bien. El fluido de corte a base de agua se usa ampliamente en el proceso de mecanizado de ultra precisión, que contiene no solo agua, sino también aceite base soluble, aceite de ricino, trietanolamina, ácido bórico, tensioactivo, polietilenglicol y fosfato de sodio. Sin embargo, el componente principal del fluido de corte es el medio de agua, y la fracción de masa de agua en el fluido de corte alcanzó aproximadamente el 70%. Debido a las dificultades en la construcción de modelos MD de todas las demás sustancias, y los parámetros de función potencial desconocidos, el estudio de nanocorte con el uso de fluido de corte a base de agua no puede llevarse a cabo mediante métodos de simulación computacional dinámica molecular. Por lo tanto, el medio de agua, que es el componente principal del fluido de corte, se adopta en esta investigación para reemplazar el fluido de corte a base de agua durante la simulación del proceso de nanocorte. Basado en el modelo MD establecido, el proceso de nano-corte se realiza para estudiar el efecto de los medios de agua en la remoción de material y el mecanismo de formación de defectos subsuperficiales. La evolución del defecto del subsuelo, la variación de la fuerza de corte, la distribución de temperatura de la pieza de trabajo y la transformación del cristal del defecto del subsuelo se investigan mediante el uso de métodos de parámetro de centro-simetría (CSP), análisis de vecino común (CNA) y algoritmo de extracción de dislocación (DXA). .
Métodos
Modelo de simulación
Para investigar el efecto de los medios fluidos en la remoción de material y la evolución de los defectos del subsuelo en el nano-corte, se establecen los modelos MD con y sin medios acuosos, como se muestra en la Fig. 1. En los modelos, las moléculas de agua se construyen de acuerdo con la Modelo TIP4P [23,24,25]. El campo de fuerza CHARMM y la función potencial de Lennard-Jones (L-J) se utilizan para calcular con precisión el movimiento de las moléculas de agua. Puede analizar exhaustivamente el efecto de la energía potencial no ligante, el potencial de expansión del enlace, la energía potencial de flexión del ángulo del enlace y la vibración molecular, lo que hace que la simulación de moléculas de agua sea más precisa. El material de la pieza de trabajo es cobre monocristalino y la herramienta de mecanizado es de materiales diamantados. Contiene 62835 moléculas de agua, 368208 átomos de Cu y 2452 átomos de C. La pieza de trabajo se divide en tres partes, que son la capa de Newton, la capa de temperatura y la capa límite. Para reducir el efecto de tamaño, se adopta la condición de límite periódica (PBC) en [001] y [010]. Para mantener la presión y la densidad de los medios de agua, las paredes reflectantes se utilizan en ambos lados de la dirección [001]. En el proceso de mecanizado real, el refrigerante elimina la mayor parte del calor de corte, por lo que el entorno del agua se establece a una temperatura constante de 300 K en este trabajo. El modelo de simulación MD con entorno de vacío se muestra en la Fig. 1b, donde las condiciones iniciales de simulación son similares con el modelo de entorno de fluidos. Los diferentes ajustes entre los dos modelos son los ajustes relevantes para los medios acuosos. Los parámetros de corte detallados se muestran en la Tabla 1.

Los modelos de simulación MD en nanocorte. un El uso de medios acuosos. b El uso del entorno de vacío
Funciones potenciales interatómicas
En las simulaciones MD, la función potencial juega un papel decisivo en los resultados de la simulación. Las propiedades de los materiales están fundamentalmente controladas por la interacción entre átomos. En esta investigación, el modelo se divide en tres partes que son pieza de trabajo, herramienta de corte y medio acuoso, y contiene cuatro tipos atómicos, que son átomos de Cu, C, H y O. Las interacciones entre diferentes átomos se calculan mediante el potencial de Morse, el potencial del método del átomo incrustado (EAM), el potencial de Lennard-Jones (L-J) y el potencial de Tersoff. La introducción detallada de la función potencial seleccionada entre diferentes átomos se muestra en la Tabla 2.
Potencial Morse
La interacción entre los átomos de Cu en la pieza de trabajo y los átomos de C en la herramienta de corte se calcula mediante el potencial Morse que se muestra como Eq. (1) [26].
$$ u \ left ({r} _ {ij} \ right) =D \ left [\ exp \ left (-2 \ alpha \ left ({r} _ {ij} - {r} _0 \ right) \ right ) -2 \ exp \ left (- \ alpha \ left ({r} _ {ij} - {r} _0 \ right) \ right) \ right] $$ (1)donde r 0 , α y D , respectivamente, son el espaciado atómico, el módulo de elasticidad y la energía de enlace. Los valores de r 0 , α y D se muestran en la Tabla 3.
Potencial de EAM
La función interatómica entre los átomos de Cu en la pieza de trabajo se describe mediante el potencial EAM que se muestra como Ecs. (2) y (3) [27, 28].
$$ E \ kern0.5em =\ kern0.5em \ sum \ limits_i ^ N \ left [F \ left ({\ rho} _i \ right) \ kern0.5em + \ kern0.5em \ sum \ limits_ {j \ kern0 .5em> \ kern0.5em i} ^ Nu \ left ({r} _ {ij} \ right) \ right] $$ (2) $$ {\ rho} _i \ kern0.5em =\ kern0.5em \ sum \ límites_jf \ izquierda ({r} _ {ij} \ derecha) $$ (3)Potencial de Lennard-Jones
La función de potencial de Lennard-Jones es un potencial dual, que incluye la interacción de la fuerza de Coulomb de largo alcance y la fuerza de van der Waals de corto alcance entre átomos. El potencial L-J se usa a menudo para simular los materiales líquidos. En este artículo, el potencial de Lennard-Jones se utiliza para calcular la interacción entre las moléculas de agua y otros átomos, que se muestra como Eq. (4) [29].
$$ {U} _ {LJ} (r) \ kern0.5em =\ kern0.5em 4 \ varepsilon \ left [{\ left (\ frac {\ sigma} {r} \ right)} ^ {12} \ kern0 .5em - \ kern0.5em {\ left (\ frac {\ sigma} {r} \ right)} ^ 6 \ right] $$ (4)donde σ es la separación de equilibrio cuando la energía potencial de interacción es igual a cero y ε es la profundidad de la trampa de energía potencial.
Para diferentes materiales, σ y ε puede calcularse mediante las ecuaciones. (5) y (6) [29].
$$ {\ sigma} _ {\ alpha \ beta} \ kern0.5em =\ kern0.5em \ frac {\ sigma _ {\ alpha \ alpha} \ kern0.5em + \ kern0.5em {\ sigma} _ {\ beta \ beta}} {2} $$ (5) $$ {\ varepsilon} _ {\ alpha \ beta} \ kern0.5em =\ kern0.5em \ sqrt {\ varepsilon _ {\ alpha \ alpha} \ cdot {\ varepsilon } _ {\ beta \ beta}} $$ (6)Los parámetros de potencial interatómico L-J que se utilizan en esta investigación se enumeran en la Tabla 4.
Potencial de Terseff
La interacción entre los átomos de carbono en la herramienta de diamante se calcula mediante el potencial de Tersoff que se muestra como Ecs. (7) y (8) [30].
$$ E \ kern0.5em =\ kern0.5em \ frac {1} {2} \ sum \ limits_ {i \ ne j} {V} _ {ij} $$ (7) $$ {V} _ {ij } \ kern0.5em =\ kern0.5em {f} _c \ left ({r} _ {ij} \ right) \ left [{V} _R ^ {\ hbox {'}} \ left ({r} _ { ij} \ derecha) \ kern0.5em + \ kern0.5em {b} _ {ij} {V} _A \ izquierda ({r} _ {ij} \ derecha) \ derecha] $$ (8)donde f c ( r ij ) es la función de truncamiento entre átomos, V A ( r ij ) es el potencial dual del término de absorción, V R ( r ij ) es el potencial dual del término de repulsión, y r ij es la distancia atómica entre el átomo i y atom j .
Métodos de análisis de defectos
En el nanocorte de cobre monocristalino, la deformación y las dislocaciones se nuclean en el subsuelo de la pieza de trabajo. En este artículo, se introduce el parámetro de centro-simetría (CSP) para analizar la nucleación de la dislocación y la evolución del defecto de la pieza de trabajo. Para materiales cúbicos de centro frontal (FCC), el valor de CSP se puede calcular mediante la ecuación. (9) [31].
$$ CSP \ kern0.5em =\ kern0.5em \ sum \ limits_ {i \ kern0.5em =\ kern0.5em 1} ^ 6 {\ left | {R} _i \ kern0.5em + \ kern0.5em {R } _ {i + 6} \ right |} ^ 2 $$ (9)donde R i son los átomos vecinos con la misma distancia y R i + 6 son los átomos vecinos con dirección opuesta. Los valores de CSP de cristal de FCC, dislocación parcial, fallas de apilamiento y átomos de superficie son 0, 2,1, 8,3 y 24,9, respectivamente [32]. El rango de valor de CSP para la estructura cristalina típica y la coloración atómica se muestra en la Tabla 5.
El método CSP puede identificar la configuración atómica, pero no puede reconocer el estado de la estructura del cristal atómico local de la pieza de trabajo. Por lo tanto, se introduce el análisis de vecino común (CNA) para identificar la estructura cristalina local de la pieza de trabajo. En el método CNA original propuesto por Honeycutt [33], las diversas estructuras están representadas por diagramas. Actualmente, se ha mejorado para identificar rápidamente cinco tipos de estructuras en el software OVITO [34, 35], que, respectivamente, son cúbicos de centro de cara (FCC), hexagonales compactos (HCP), cúbicos centrados en el cuerpo (BCC), icosoédricos (ICO) y desconocido. En este artículo, también se introduce el algoritmo de extracto de dislocación (DXA) [36] para analizar la evolución del defecto de dislocación. Mediante el método DXA, las diferentes estructuras de cristal en la pieza de trabajo se marcarán con diferentes colores y los defectos de dislocación en la pieza de trabajo se representarán con líneas de diferentes colores.
Resultados y discusión
Evolución de defectos subsuperficiales en procesos de nanocorte con medios acuosos
La vista en sección del sistema de corte se muestra en la Fig. 2, que contiene la herramienta de corte, la pieza de trabajo y el medio de agua durante el proceso de nano-corte. Para percibir claramente la deformación plástica de la pieza de trabajo, se utiliza el método CSP para analizar los resultados. Las instantáneas están coloreadas por el valor de CSP parcialmente como se muestra en la Fig. 2, en la que la Fig. 2a está a 5 nm de distancia de corte y la Fig. 2b está a 15 nm de distancia de corte. Puede verse que se forma una capa de película de agua compacta en la superficie del cobre monocristalino que se muestra como "película monomolecular de agua" en la Fig. 2a. La película de agua se extendió por todas las superficies de la herramienta de corte y la pieza de trabajo, en la que los átomos de oxígeno ocupan el centro de la red de cobre monocristalino. La disposición regular de las moléculas de agua es el resultado de la acción combinada de la fuerza de Coulomb de largo alcance y la fuerza de van der Waals entre las moléculas de agua y los átomos de cobre.
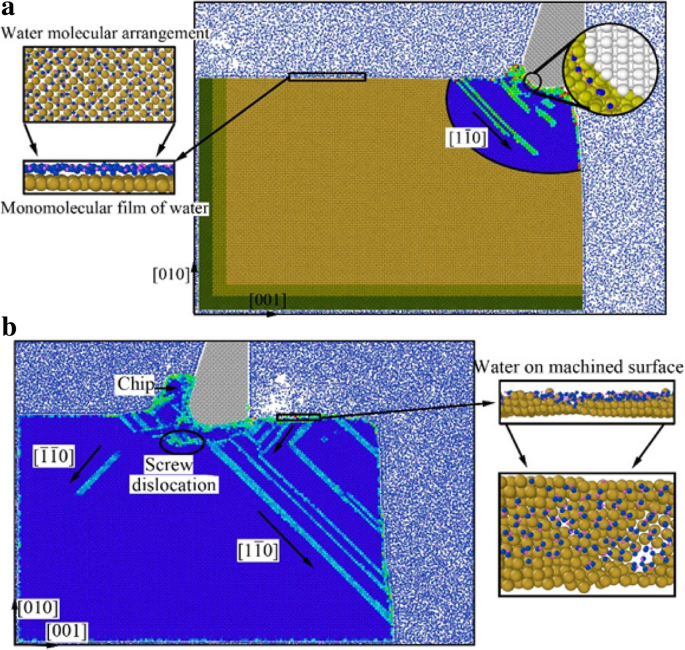
Vista en sección del sistema de corte con medios acuosos en proceso de nano-corte (color online). un Distancia de corte l =5 nm. b Distancia de corte l =15 nm
En el proceso de nano-corte, la deformación por deslizamiento es resultado de la acción de corte por compresión temprana de la herramienta de corte y se almacena en la red cristalina formada como energía de deformación. Cuando la acumulación de energía de deformación alcanza un cierto nivel, se libera la energía de deformación. Y luego, la red de cobre monocristalino se reordena, lo que provocó la nucleación y la extensión de la dislocación a lo largo de la dirección \ (\ left [1 \ overline {1} 0 \ right] \), como se muestra en la Fig. 2a. A partir de la figura 2a se puede mostrar que la película monomolecular de agua se forma en la superficie de la pieza de trabajo. Además, las moléculas de agua penetran en el subsuelo de la pieza de trabajo en el área de acción de la interfaz herramienta-viruta, que se muestra como la ilustración superior derecha en la Fig. 2a. Debido a la acción lubricante de las moléculas de agua que existían entre la herramienta de corte y la pieza de trabajo, se atenúa la acción de cizallamiento por compresión de la herramienta de corte. Y la acumulación de energía de deformación disminuye y las dislocaciones se extienden insuficientemente. Además, los medios acuosos eliminan mucho calor de corte y la energía de expansión de la dislocación nucleada es insuficiente. Por lo tanto, la extensión de la dislocación es insuficiente y la línea de dislocación en el subsuelo de la pieza de trabajo pasa desapercibida, como se muestra en la Fig. 2a.
A medida que la herramienta de corte avanza, la pieza de trabajo sufrió la acción de extrusión y fricción generada por la cara del flanco de la herramienta de corte. Bajo la acción de extrusión y frotamiento de la herramienta de corte, un gran número de dislocaciones se nucleó y extendió en el subsuelo de la pieza de trabajo. Una parte de estas dislocaciones se mueve hacia arriba a lo largo de la cara de inclinación y finalmente se elimina como una viruta de corte, como se muestra en la Fig. 2b. Otra parte de estas dislocaciones se mueve hacia abajo a lo largo de la cara de inclinación de la herramienta de corte y se transforma en una superficie mecanizada de rugosidad después de la acción de fricción de extrusión de la cara del flanco de la herramienta de corte, que se muestra en la Fig.2b como "disposición de agua sobre la superficie mecanizada". " Otras partes de las dislocaciones se mueven hacia adentro a lo largo del plano de deslizamiento \ (\ left [\ overline {1} \ overline {1} 0 \ right] \) y \ (\ left [1 \ overline {1} 0 \ right] \) y desaparecen dentro de la pieza de trabajo, lo que da como resultado la formación de una dislocación del tornillo, como se muestra en la Fig. 2b. Debido a que la altura de la viruta aumenta gradualmente, las moléculas de agua en frente de la viruta no pueden fluir sobre la viruta hacia atrás de la herramienta de corte en el período posterior del proceso de corte. Y la densidad y la presión de los medios de agua detrás de la herramienta de corte disminuyen rápidamente, lo que provoca que el calor de corte se elimine prematuramente durante el proceso de nanocorte. Por lo tanto, las dislocaciones nucleadas tienen suficiente energía para extenderse dentro de la pieza de trabajo, como se muestra en la Fig. 2b.
Con el fin de dilucidar la deformación subyacente de las dislocaciones y la estructura cristalina atómica local del cobre monocristalino durante el proceso de nano-corte, se introducen los métodos de análisis CSP y DXA. Los resultados del análisis se muestran como se muestra en las Figs. 3, 4, 5 y 6, entre las que se encuentran las Figs. 3 y 4 se representan de acuerdo con el valor de CSP y las Figs. 5 y 6 están coloreados por el resultado del análisis DXA.
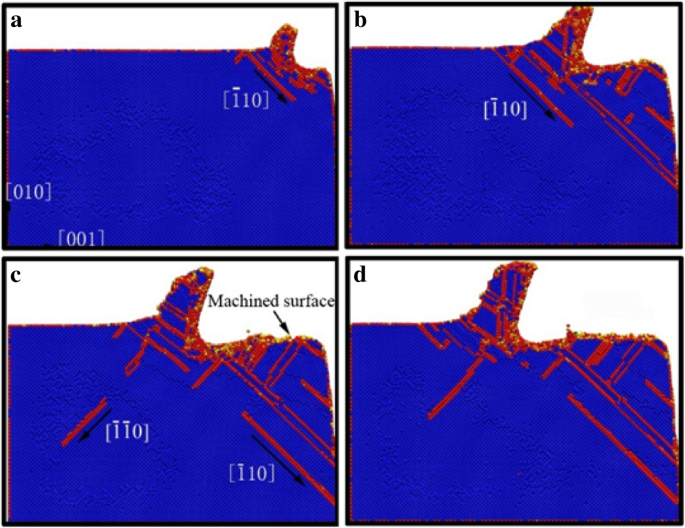
Distribución de defectos del subsuelo de la pieza de trabajo con medios acuosos en el proceso de nano-corte. Las distancias de corte de a , b , c y d son 5 nm, 8 nm, 12 nm y 15 nm, respectivamente.
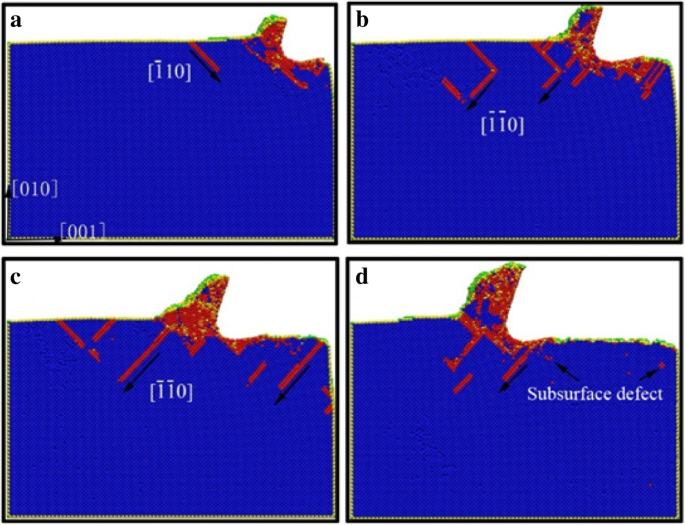
Distribución de defectos subsuperficiales de la pieza de trabajo durante el proceso de nano-corte en un entorno de vacío. Las distancias de corte de a , b , c y d son 5 nm, 8 nm, 12 nm y 15 nm, respectivamente.
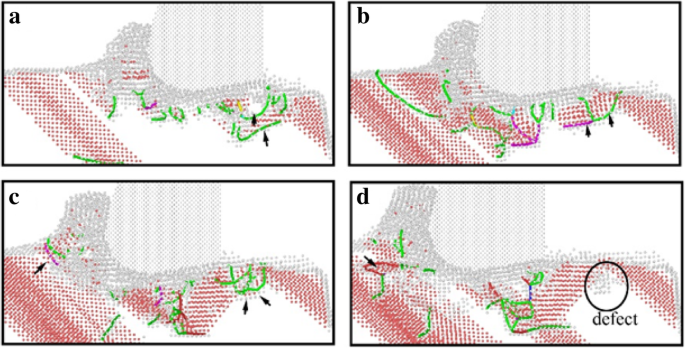
La imagen DXA de la pieza de trabajo en la etapa inicial del nanocorte. Las dislocaciones se colorean según el esquema siguiente:azul profundo para dislocaciones perfectas, verde para dislocaciones de Shockley, rosa para dislocaciones de varilla de escalera, amarillo para dislocaciones de Hirth, azul claro para dislocaciones de Frank y rojo para dislocaciones no identificadas. Las distancias de corte de a , b , c y d son 7 nm, 8 nm, 9 nm y 10 nm, respectivamente
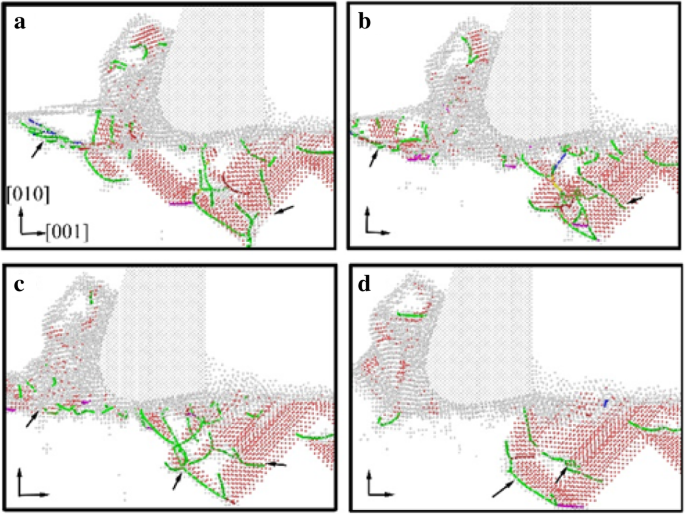
La imagen DXA de la pieza de trabajo en el período posterior del nanocorte. El esquema de coloración de las dislocaciones es el mismo que en la Fig. 5. Las distancias de corte de a , b , c y d son 17 nm, 18 nm, 19 nm y 20 nm, respectivamente
La distribución del defecto subsuperficial de la pieza de trabajo en el proceso de nano-corte con medio acuoso se muestra en la Fig. 3, en la que el medio de agua no se muestra para observar con mayor claridad la evolución del defecto de dislocación. Las áreas amarilla, verde, roja y naranja representan átomos de superficie, átomos de defecto de superficie, átomos de dislocación y átomos de defecto del subsuelo, respectivamente. La distribución de la dislocación y la extensión de la pieza de trabajo en el proceso de nano-corte sin el medio acuoso se muestra en la Fig. 4. Se puede ver en las dos figuras que las dislocaciones nucleadas migran a lo largo de \ (\ left [\ overline {1} 10 \ right] \) vector de deslizamiento durante el proceso de nanocorte con medio acuoso, pero se extiende a lo largo del vector de deslizamiento \ (\ left [\ overline {1} \ overline {1} 0 \ right] \) en nanocorte bajo medio de vacío . Como sabemos, la acción cortante de la herramienta de corte produce dislocaciones que se extienden a lo largo de la dirección contra la herramienta hacia adelante, que es \ (\ left [\ overline {1} 10 \ right] \) vector de deslizamiento. La acción de fricción de la herramienta de corte hace que la dislocación migre a lo largo de la dirección del movimiento ortocinético de la herramienta, que es un vector de deslizamiento \ (\ left [\ overline {1} \ overline {1} 0 \ right] \). Durante el proceso de nanocorte en un entorno de vacío, las acciones de la herramienta de corte sobre la pieza de trabajo son la acción de corte de la cara de desprendimiento y la acción de fricción de la cara del flanco, mientras que la formación de defectos superficiales y subsuperficiales mecanizados se desencadena por la acción de fricción de la cara del flanco. Por lo tanto, la extensión de la dislocación se extendió a lo largo del vector de deslizamiento \ (\ left [\ overline {1} \ overline {1} 0 \ right] \) durante el proceso de nanocorte en vacío. Debido a la lubricación de las moléculas de agua que existen entre la herramienta y la pieza de trabajo, se reduce la acción de fricción de la herramienta de corte. Por tanto, la acción de cizallamiento juega un papel importante en la formación de defectos superficiales y subterráneos mecanizados. Por lo tanto, las dislocaciones se extienden principalmente a lo largo del vector de deslizamiento \ (\ left [\ overline {1} 10 \ right] \) en nanocortes con medios acuosos.
De las Figs. 3 y 4, se puede encontrar que la escala de defectos del subsuelo en los medios de agua es mayor que en el vacío durante el proceso de nano-corte. En realidad, los defectos de dislocación se extienden por toda el área mecanizada y se extienden profundamente dentro de la pieza de trabajo. El medio de agua quita el calor de corte y disminuye la energía del defecto atómico. Por lo tanto, los defectos del subsuelo no tienen suficiente energía para ser aniquilados. Por tanto, aumenta el residuo del defecto de dislocación. La profundidad de la capa del defecto del subsuelo es relativamente mayor para el proceso de nano-corte con agua. Debido a las interacciones entre moléculas de agua, átomos de carbono y átomos de cobre, la fricción de extrusión entre la herramienta de corte y la pieza de trabajo se atenúa y el desorden atómico de la superficie mecanizada se agrava en el proceso de formación de la superficie mecanizada. Además, el residuo del defecto en el subsuelo se agrava y la tensión residual del subsuelo aumenta.
Con el fin de revelar mejor el efecto de los medios de agua en el proceso de evolución del defecto de dislocación, el método DXA se utiliza para analizar la pieza de trabajo en el proceso de nano-corte con medios acuosos, en el que la etapa inicial y el período tardío se muestran en la Fig.5 y 6, respectivamente. Se encuentra un defecto de cristal estable que existe en varias capas de átomos debajo de la superficie mecanizada en la etapa inicial del proceso de nano-corte, que se encuentra entre dos fallas de apilamiento, como se muestra en la Fig. 5d. La existencia de los defectos del cristal afectará la calidad de la superficie mecanizada e incluso conducirá a la generación de microgrietas en la superficie mecanizada. Por tanto, se estudia la formación del proceso de evolución del defecto. Puede verse en la Fig. 5a que muchas dislocaciones parciales de Shockley se nuclean bajo la acción de fricción de la cara del flanco de la herramienta de corte en el instante temprano de la formación del defecto. Estas dislocaciones de Shockley se convierten en un bucle de dislocación en forma de V durante el avance de la herramienta de corte, como se muestra en la Fig. 5b. Posteriormente, la luxación en forma de V evoluciona gradualmente a luxaciones parciales de Shockley en serie. Finalmente, las dislocaciones parciales se transforman en defecto residual en el subsuelo. Debido a que el medio de agua elimina el calor de corte, los átomos defectuosos tienen muy poca energía para ser aniquilados y se transforman en defectos inmóviles debajo de la superficie mecanizada. La rugosidad de la superficie mecanizada aumentará y la tensión residual en el subsuelo causará más agravamiento. Además, el defecto puede inducir una microfisura superficial.
El efecto del medio de agua sobre la acción de deslizamiento de la herramienta de corte durante el proceso de remoción de viruta se investiga mediante el método DXA, que se muestra en la Fig. 6. Se puede ver en la Fig. 6a que un gran número de dislocaciones parciales de Shockley están nucleadas en parte delantera de la herramienta de corte. Y el plano de deslizamiento cortante está constituido por estas dislocaciones. En el siguiente proceso de corte, las fallas de apilamiento en serie y las dislocaciones parciales se nuclean y se extienden en el plano de deslizamiento cortante. Bajo la nucleación y el movimiento de las dislocaciones delante de la herramienta de corte, la viruta de corte se retira gradualmente a lo largo del plano de deslizamiento cortante, como se muestra en la Fig. 6c. Mientras tanto, el efecto de fricción por extrusión de la cara de inclinación de la herramienta se reduce debido a la acción de lubricación del medio de agua. La nucleación y propagación de la dislocación es insuficiente y el defecto subsuperficial residual no es evidente durante el proceso de nanocorte, como se muestra en la Fig. 6a-d. En consecuencia, la acción de corte de la herramienta de corte sobre la pieza de trabajo se vuelve más significativa. Por lo tanto, la viruta formada se elimina más fácilmente con la participación de medios de agua en el proceso de nanocorte. Y la fuerza de corte principal disminuirá simultáneamente, lo que se discutirá en detalle más adelante en este documento.
Efecto de los medios de agua sobre la variación de la fuerza de corte y el calor de corte
En el proceso de corte, la eliminación de material se realiza mediante la acción de extrusión y corte de la herramienta de corte. Debido a la resistencia, rigidez y tenacidad del material metálico, la superficie de desprendimiento de la herramienta de corte sufrió la fuerza de reacción generada por la resistencia a la deformación del material de la pieza de trabajo durante el proceso de remoción del material. Y la superficie del flanco de la herramienta se ve afectada por la resistencia a la fuerza de fricción de la superficie mecanizada. Estas fuerzas componían juntas la fuerza de corte. Sincrónicamente, el trabajo aplicado por la deformación por cizallamiento de las virutas de corte, así como la acción de fricción entre la herramienta de corte y la pieza de trabajo, se convierte en calor de corte, lo que resulta en un aumento de temperatura de la pieza de trabajo. Junto con la acumulación y liberación de energía de deformación del material, se produjo una nucleación y expansión de dislocación en la capa subsuperficial de la pieza de trabajo, lo que indujo la fluctuación de la fuerza de corte y el calor de corte con la distancia de corte.
En esta investigación, la participación de los medios de agua tiene una gran influencia en la variación de la fuerza de corte y el calor de corte. Las curvas de variación de la fuerza de corte con la distancia de corte en el proceso de nanocorte con y sin el uso de medios acuosos se muestran en las Figs. 7 y 8, en las que las curvas negra, roja y azul, respectivamente, son la fuerza de avance (Fx), la fuerza de retroceso (Fy) y la fuerza tangencial (Fz). Debido a que el PBC se adoptó en la dirección Z y la herramienta de diamante es columnar a lo largo de la dirección Z en la simulación, la fuerza tangencial promedio (Fz) está al nivel de 0 nN en ambas Figs. 7 y 8.
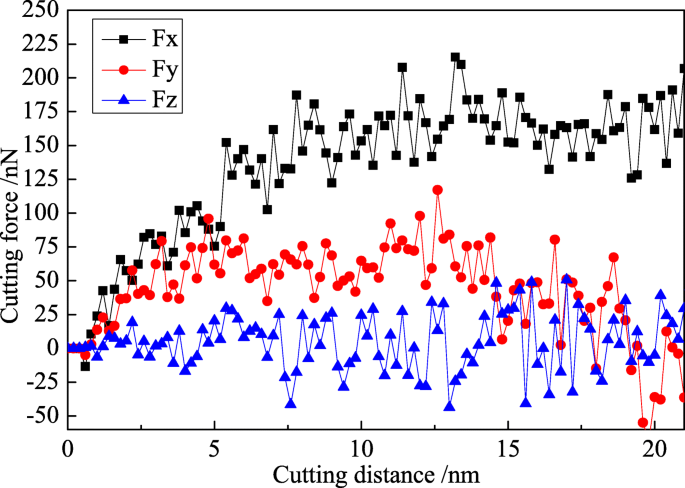
Curva de variación de la fuerza de corte en nanocorte con entorno de vacío
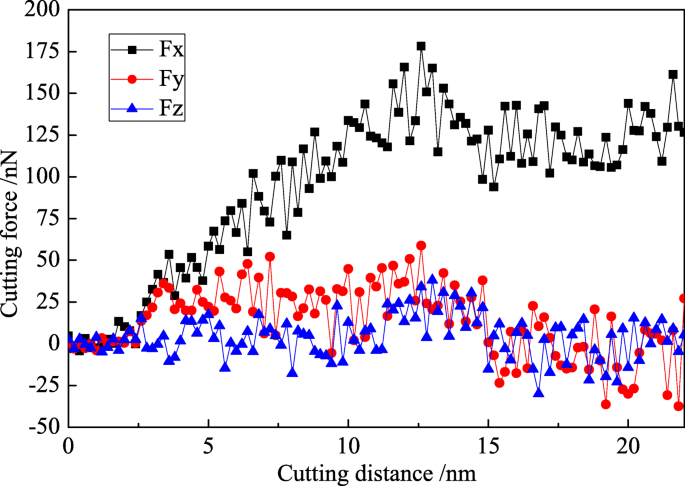
Curva de variación de la fuerza de corte en nanocorte con medio acuoso
El proceso de corte se divide en la etapa de corte inicial y la etapa de corte estable como se muestra en la Fig. 7. En la etapa de corte inicial, la fuerza de avance y la fuerza de retroceso aumentan bruscamente en línea recta. Y alcanzaron sus valores máximos cuando la herramienta de corte cortó completamente la pieza de trabajo. En la etapa de corte estable, las fuerzas de corte fluctúan hacia arriba y hacia abajo en su posición de equilibrio, y la fuerza de avance alcanza más de 200 nN y la fuerza de corte media es de aproximadamente 180 nN. La fuerza de retroceso es muy pequeña y disminuye gradualmente en la última etapa de corte estable. El valor máximo de la fuerza de horneado es inferior a 100 nN y el valor medio es de alrededor de 50 nN. Generally speaking, the specific value between average back force and average feed force (Fy/Fx) represents the friction coefficient between tool material and workpiece material in machining process. In this research, the friction coefficient between diamond and monocrystal copper is 0.278 under vacuum environment.
The feed force and the back force are decreased in nano-cutting with water media compared with vacuum environment, as shown in Fig. 8. The maximum feed force reaches 150 nN, and the mean feed force fluctuates at 120 nN. The variation tendency of back force is similar with the back force in vacuum environment, and the mean force is at about 25 nN. In nano-cutting process with the use of water medium, the friction coefficient between the cutting tool and the workpiece is reduced due to the lubrication of water. And then the frictional resistance suffered by the flank surface of cutting tool is reduced, which effectively enhances the extrusion shearing action of the rake surface of cutting tool. The removal of the workpiece material is easier to be removed. Hence, the cutting force is reduced. It can be seen from the foregoing analysis that the water molecules acted as a lubricant to prevent the friction between the cutting tool and the workpiece. Therefore, the values of feed force and back force are reduced in the water media. The specific value between the feed force and the back force is 0.208. In another words, the frictional coefficient between diamond and copper in water media is 0.208, much fewer than they are in vacuum environment (0.278).
Compared with the fluctuation of the Fy in Figs. 7 and 8, it is indicated that the Fy component decreases considerably after 15 nm of cutting distance in both cases with vacuum and water media while the Fx value is almost stable until 20 nm of cutting distance. The dynamic balance between dislocation nucleation and annihilation is achieved, and the chip is removed steadily in nano-cutting process, which results in the cutting force almost stable with the cutting distance before 20 nm. When the cutting process is carried out at a certain distance (15 nm in this research), the dynamic equilibrium between the new dislocation nucleation and the previous dislocation annihilation is established. And the scale of the internal defects of the workpiece is stabilized at a certain level. The dislocation nucleation and annihilation applied an effect on cutting tool along +Y direction, which leads to the Fy component decrease. Besides, the stable cutting chip is removed after 15 nm of cutting distance, and the applied force on the cutting tool from the chip is decreased along the Y direction. Thereby, the value of Fy is reduced. However, when the cutting distance is greater than 15 nm till 20 nm, the emotion of dislocation defect and the removal of chip cannot bring a different influence on the cutting tool along the X direction. Therefore, the value of main cutting force (Fx) is almost stable.
The temperature distribution of the workpiece during the nano-cutting process with and without the use of aqueous media is shown as Fig. 9. The cutting distances of Figs. 9a and b and Figs. 9c and d are 5 nm and 12 nm, respectively. It can be seen from Figs. 9b and d that the temperature of workpiece is distributed as a concentric gradient. The highest temperature is spread all over shear-slip zone and friction zone of the workpiece in a vacuum environment, which is above 420 K. The temperature of the chip and machined surface is higher than other regions, which is ranged from 360 to 390 K. For the whole workpiece, the temperature is at a high level, which is ranged from 340 to 360 K. From Figs. 9a and c, the temperature of the workpiece is also distributed as a concentric gradient and the highest temperature is distributed at the top area of the chip, which is around 370 K. The temperature value of the whole workpiece is at a lower level which is lower than 320 K. The temperature of the shear-slip area, the friction zone, and the machined surface are higher than other areas, which is ranged from 320 to 340 K.
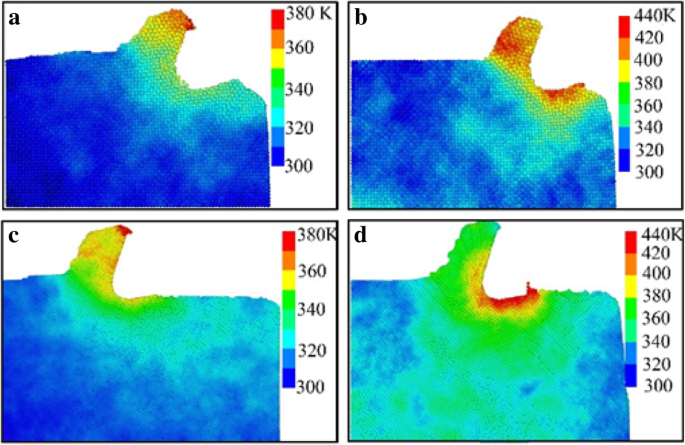
Temperature distribution of workpiece in nano-cutting. un y c are in water media, b y d are in vacuum environment
The highest temperature area of workpiece is transferred from the friction area to the cutting chip during nano-cutting process with water media as shown in Fig 9. And the highest and whole temperature of the workpiece are significantly reduced with the additional use of water media, and the temperature drop reached about 40–60 K. Due to the lubrication effect of water molecules, the friction between cutting tool and machined surface is reduced during nano-cutting process with water media. Hence, the temperature of the friction area declined dramatically. Meanwhile, the maximum shearing deformation occurred at the chip area and the maximum lattice deformation energy is stored in the chip, which makes the temperature of the chip higher than the friction area. Therefore, the highest temperature area is transferred from friction area to the cutting chip. Synchronously, a large amount of cutting heat is taken away by the water media which play a role in cooling the tool, workpiece, and cutting area. And the thermal movement of the monocrystal copper molecules is weakened. Furthermore, the kinetic energy of atomic thermal motion and the lattice deformation energy are decreased significantly. Therefore, the overall temperature and the highest temperature of the workpiece is reduced, whose degree of reduction arrived at 40–60 K. Finally, the thermal stress and thermal deformation of the workpiece are significantly reduced. Because of the participation of water media, the friction action between the flank surface of cutting tool and workpiece is weakened in cutting process. Then, the generation of heat by friction between cutting tool and workpiece is reduced. Thereby, the highest temperature area of the workpiece is transferred from the friction area of flank surface to the chip area. More importantly, the cooling effect and lubrication of water media will affect the nucleation, expansion, and annihilation of the dislocation in subsurface of the workpiece and ultimately affect the formation and evolution of the subsurface damage layers of the workpiece.
Effect of Aqueous Media on Subsurface Defects Structural Transformation
In order to clearly identify the subsurface defects of the workpiece in nano-cutting, the CNA method is used to analyze the workpiece after nano-cutting. The workpiece is colored by different atomic structure. The defect structural distribution of the workpiece during nano-cutting process with and without the use of aqueous media is shown as Figs. 10 and 11, in which the green, red, blue, and grey are FCC, HCP, BCC, and unknown structure, respectively.
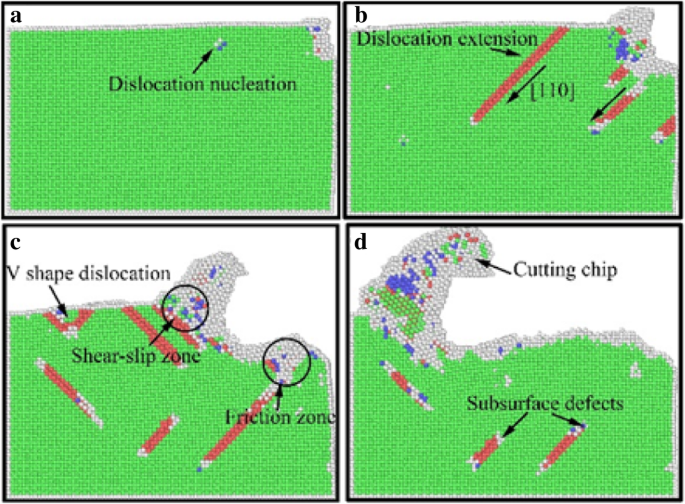
Subsurface defect evolution of workpiece in nano-cutting without aqueous media. The green, red, blue, and grey area are representative of FCC, HCP, BCC, and unknown structure. The cutting distances of a, b, c, and d are 1 nm, 3 nm, 8 nm, and 15 nm, respectively
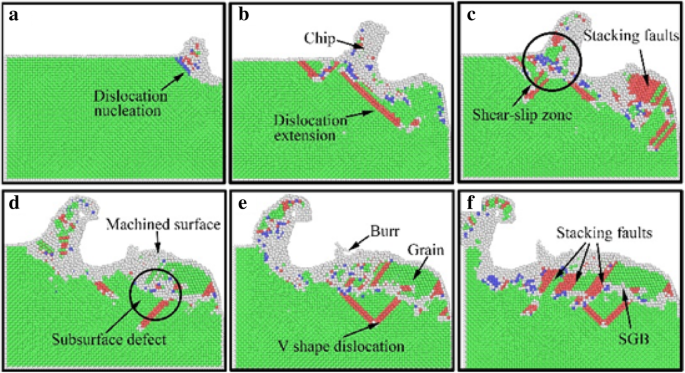
Surface and subsurface defect distribution in nano-cutting for workpiece with water media. The green, red, blue, and grey area are representative of FCC, HCP, BCC, and unknown structure. The cutting distances of a, b, c, d, e, and f are 3 nm, 8 nm, 12 nm, 15 nm, 18nm, and 20nm respectively
In nano-cutting process under vacuum environment, dislocation nucleation occurred at the subsurface of workpiece under the extrusion and shearing action of the cutting tool, and the crystal structure is transformed into BCC, which is shown as Fig. 10a. The nucleated dislocation is extended along \( \left[\overline{1}\overline{1}0\right] \) direction, and the crystal structure is transformed into HCP. The crystal structure of many atoms in the shear-slip region become BCC, as shown in Fig. 10b. Two partial dislocations are extended along the \( \left[\overline{1}\overline{1}0\right] \) and \( \left[1\overline{1}0\right] \) directions, hindered each other, and be composed of Lomer-Cottrell dislocation lock. Finally, a typical V-shaped dislocation loop is formed, as shown in Fig. 10c. Part of the atoms in the shear-slip zone are moved upward along the rake face and are removed as cutting chip. The other part of the atoms are migrated downward along the flank face and are formed into the roughness machined surface by the extrusion and friction of the cutting tool, as shown in Fig. 10d.
The subsurface defect distribution and evolution of workpiece in nano-cutting with the use of water media is shown as Fig. 11. It can be seen from the figure that the mechanisms of dislocation nucleation and crystal structure transformation are similar with the cutting process in vacuum environment. The main difference is that the dislocation nucleation and expansion is insufficient in the nano-cutting process of water media. Besides, there are many stacking faults nucleated in the subsurface of the workpiece. The structure of stacking faults is transformed into HCP structure. Nevertheless, a typical defect “similar-to-grain boundary (SGB)” is formed in the subsurface of the workpiece.
In nano-cutting process, under the action of extrusion, shearing and friction by cutting tool, intense deformation of the workpiece is generated. Plenty of deformation energy and cutting heat are produced. The atomic lattice reconfiguration of subsurface is produced by the release of cutting heat and strain energy. And the subsurface defects and local crystal structure transformation are formed, as shown in Fig. 11a and 11b. When the water media participated in the nano-cutting process, most of the heat and energy is taken away. Hence, the dislocation defects have inadequate energy to extension and movement. Furthermore, the stacking faults are annihilated in the subsurface of the workpiece where the crystal defect structure stayed behind, as shown in Fig. 11c, whereafter these crystal defect structures are connected as a whole and are composed of the subsurface damage (SSD) layer together with the newly formed dislocations, as shown in Fig. 11d. After the following MD relaxation, some subsurface dislocation defects are disappeared and transformed into FCC structure, and the structure similar to “grain” is formed between machined surface and subsurface defects layer, as shown in Fig. 11e, while the original subsurface defects are transformed into a typical structure “similar-to-grain boundary (SGB),” as shown in Fig. 11f. On the SGB structure, a typical V shape dislocation loop is formed, as shown in Fig. 11e, f.
The metamorphic layer is obviously formed by the influence of the formation of SGB and “grain” structure in the subsurface of workpiece. Moreover, the new formed crystal structures which are similar with polycrystalline material can influence the mechanical performance and processability of single-crystal materials. Besides, it will affect even the performance of machined nano-components.
Conclusiones
Based on the established MD models of single-crystal copper with and without the use of aqueous media, the simulation of nano-cutting process is carried out. The effects of fluid media on material removal and subsurface defect evolution are analyzed. The subsurface defect evolution, variation of the cutting force, the temperature distribution, and the subsurface defects crystal structure transformation of the workpiece are investigated by using CSP, DXA, and CNA methods. The novel results can be summarized as follows.
(1) The material removal of workpiece is realized by the shearing extrusion action of cutting tool on workpiece; the participation of water media has no effect on the mechanism of materials removal. Due to the lubrication action of water molecules existing between the cutting tool and the workpiece, the deformation of workpiece is decreased, the cutting force is reduced, and the height of cutting chip and depth of subsurface damage layer are lowered.
(2) The highest temperature area is transferred from the friction area to the cutting chip during nano-cutting process with the additional use of water media. And the highest and whole temperature of the workpiece are significantly reduced, and the temperature drop reached about 40–60 K. Thereby, the thermal deformation of the workpiece is reduced and the amount of subsurface defect atoms is decreased.
(3) In the subsurface layer of the workpiece, the crystal structures of nucleated dislocations are transformed into BCC, and the extended dislocations are transformed into HCP. The atomic crystal structures in the shear-slip region are becoming BCC. Under the effect of fluid media, the subsurface defects are transformed into a typical defect structure “similar-to-grain boundary (SGB)” in SSD layer, which can influence the mechanical performance and processability of single-crystal materials. Besides, it will affect even the performance of the machined nano-components.
Abreviaturas
- MD:
-
Dinámica molecular
- CSP:
-
Centro-symmetry parameter
- CNA:
-
Common neighbor analysis
- DXA:
-
Dislocation extract algorithm
- PBC:
-
Periodic boundary condition
- EAM:
-
Embedded-atom method
- L-J:
-
Lennard-Jones
- FCC:
-
Face center cubic
- HCP:
-
Close-packed hexagonal
- BCC:
-
Body centered cubic
- ICO:
-
Icosohedral
- SGB:
-
Similar-to-grain boundary
- SSD:
-
Subsurface damage
Nanomateriales
- Estudio del efecto de la dirección de impacto en el proceso de corte nanométrico abrasivo con dinámica molecular
- Efecto de la dispersión superficial de electrones en las relaciones de absorción óptica y dispersión hasta la extinción de la nanocapa de oro
- Tipos y clasificación de procesos de mecanizado | Ciencias de la fabricación
- ¿Qué es el Mecanizado? - Definición, Proceso y Herramienta
- ¿Qué es el corte con oxicombustible? - Proceso, pros y contras
- ¿Qué es el recocido? - Definición, proceso y etapas
- Defectos de interconexión:Falla de enlace de cobre y basada en escombros
- Comprender la precisión y el proceso de la tecnología de corte por láser
- Elija el fluido de corte correcto según el material de corte
- 5 Proceso de corte de metal en la fabricación
- Servicios de rectificado de superficies:proceso y precisión