El sistema de corte preimpregnado reduce el desperdicio y acelera el montaje del jet de negocios suizo
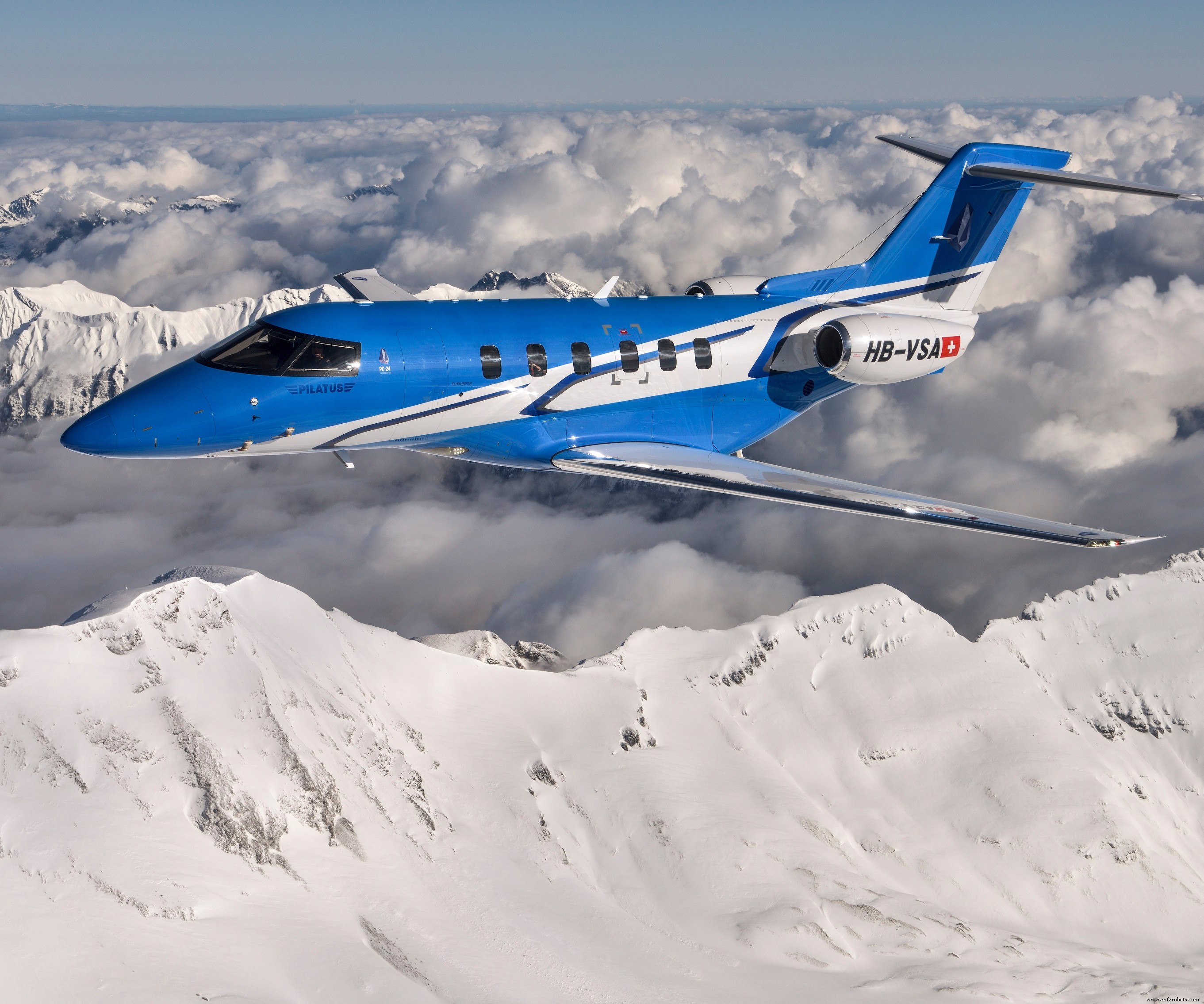
Fuente | Zünd
Gracias a los componentes de fibra de carbono y vidrio, el PC-24 El jet de negocios, fabricado por Pilatus Aircraft AG (Stans, Suiza), cuenta con un peso base de solo 5.3 toneladas (menos de 12,000 libras), lo que lo ayuda a despegar y aterrizar en pistas cortas, sin pavimentar o de grava generalmente reservadas para aviones turbohélice. De hecho, el PC-24 es capaz de despegar en una pista tan corta como 890 metros (2920 pies) y solo requiere 720 metros (2362,2 pies) para aterrizar.
Pilatus comenzó a usar piezas de fibra de carbono al principio de su historia de fabricación de aviones, comenzando con sus primeros componentes de plástico reforzado con fibra de carbono (CFRP) y plástico reforzado con fibra de vidrio (GFRP) para el PC-6 Avión universal de metal Porter. Los pocos componentes compuestos en la PC-6 , que despegó por primera vez en 1959 y pasó por una producción de alrededor de 500 aviones antes de ser reemplazado por su sucesor el PC-12 , fueron colocados a mano. PC-6 el ensamblaje, por lo tanto, requirió una mano de obra experimentada y altas tolerancias para las piezas.
Por el contrario, el último tipo de avión de la empresa, el PC-24 , consta de muchas piezas, muchas de ellas fresadas con tolerancias en el rango Mμ. El PC-24 utiliza composites principalmente para revestimientos interiores y exteriores. Las carcasas del motor y las puntas de las alas también están hechas de fibra de carbono, así como las puertas del tren de aterrizaje, los conductos de aire, varios tubos, cubiertas y los bordes de salida de las alas.
El PC-24 no solo incluir más componentes compuestos que el PC-6 Lo hizo en 1959, pero el montaje es mucho más rápido ahora, hecho posible, dice Pilatus, debido a los avances en las tecnologías de producción. La clave para esto es la reducción permanente de costos, la optimización de la productividad y la capacidad de implementar tecnologías de producción modernas.
Los sistemas de corte de preimpregnado digital son parte de esta tendencia. Pilatus ha confiado en los sistemas de corte de Zünd (Altstätten, Suiza) durante años, y en 2019 agregó un sistema de corte preimpregnado Zünd G3 L-2500. El sistema G3 corta materiales de una sola capa para los componentes respectivos en un proceso en gran parte automatizado y luego etiqueta las piezas cortadas con un módulo de inyección de tinta integrado.
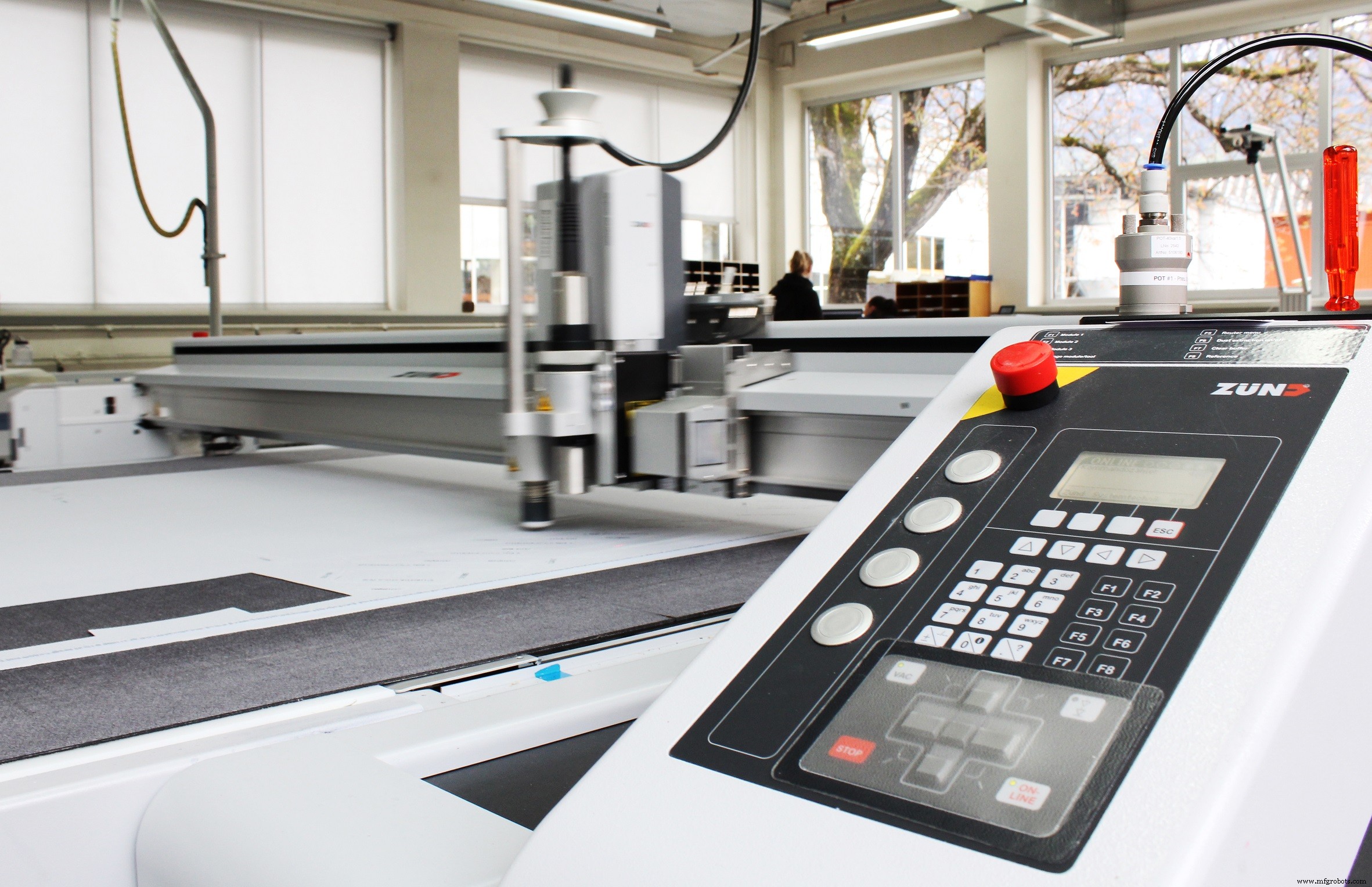
Fuente | Zünd
Pilatus procesa unos cinco rollos de preimpregnado por día (aproximadamente 90 metros cuadrados), o unos 90.000 metros cuadrados por año, y la tasa de consumo aumenta constantemente a medida que se utilizan cada vez más componentes de CFRP y GFRP en los aviones de la empresa. Pilatus ha confiado en el corte digital de Zünd durante más de 15 años, comenzando con un cortador de la serie PN. La mayor demanda de componentes de fibra de carbono comenzó a exceder la capacidad, lo que llevó a la adición de un Zünd G3 L-2500 en 2019. Una vez que se completa el corte, las piezas se preparan y almacenan en frío hasta su posterior procesamiento. Las estructuras compuestas de Pilatus pueden constar de hasta 350 capas de preimpregnado.
Otro factor del éxito de Pilatus ha sido el enfoque en aumentar la productividad. Según Patrick Rohrer, gerente de proyectos de adquisición de sistemas de Pilatus, “Cuando se trata de materiales costosos como el carbono o la fibra de vidrio, la eficiencia y la optimización del material son siempre una preocupación. Trabajamos constantemente para aumentar la utilización y, por lo tanto, reducir el desperdicio, especialmente porque todavía tenemos pocas opciones de reciclaje ”.
La compañía dice que ha reducido las tasas de desperdicio del 30% al 20%, y cita las funciones de anidamiento eficientes en el software Zünd's Cut Center - ZCC como un factor importante en este éxito. Las diferentes capas de una pieza están anidadas estáticamente, lo que significa que las capas individuales de una pieza están anidadas en la cantidad solicitada según el pedido . El anidamiento dinámico, que es cuando las capas individuales de piezas de varios pedidos se anidan y combinan en un solo archivo de corte, también se puede utilizar siempre que tenga sentido. Esto, dice Zünd, aumenta aún más el grado de utilización de la materia prima.
fibra
- ¿Cómo funciona el corte por chorro de agua?
- 5 beneficios del corte por chorro de agua
- Chorro de agua frente a corte por láser:¿Cuál es la diferencia?
- Business Jet
- ¿Cómo optimizar la máquina de corte por chorro de agua de manera eficiente?
- ¿Qué considerar antes de comprar una máquina de corte por chorro de agua abrasiva?
- La solución reduce las explosiones del sistema para Solvay
- La confiabilidad reduce la pérdida de tiempo, talento y recursos
- Mecanizado y corte por chorro de agua abrasivo
- ¿La automatización de su sistema de corte por láser es adecuada para su aplicación?
- ICS presentado en el Hartford Business Journal