Las soluciones de IoT basadas en IA extienden el mantenimiento predictivo en toda la línea de producción
Brad Hopkins de HID Global
Históricamente, el uso de soluciones de monitoreo de condición para el mantenimiento predictivo se ha restringido a equipos de misión crítica de alto valor, dejando un promedio del 85% del equipo de una instalación de producción vulnerable a costosos tiempos de inactividad inesperados y reparaciones.
El problema con las soluciones actuales, dice Brad M. Hopkins, director de Gestión de Productos de Monitoreo de Condiciones de HID Global , Es que no están bien alineados con los requisitos de la planta o se considera que su implementación en toda la instalación es prohibitivamente costosa.
Ahora, una nueva clase de soluciones de monitoreo de condición combina la tecnología de Internet de las cosas (IoT) de bajo costo y bajo consumo de energía con análisis en la nube impulsados por inteligencia artificial (AI) para reducir el costo y la complejidad de implementación del mantenimiento predictivo en toda una flota de activos.
El alto costo de fallar
Aunque los motores se clasifican generalmente como críticos / costosos, semicríticos o parte del "equilibrio de la planta" (BoP), la realidad es que todos los equipos son críticos desde el punto de vista operativo. Independientemente de la categoría de equipo que falle y cause tiempo de inactividad, los costos por hora asociados pueden oscilar entre 30 000 dólares estadounidenses en las plantas de procesamiento de alimentos y 87 000 dólares en la industria petroquímica y hasta 200 000 dólares en una fábrica de automóviles.
Las fallas también pueden generar otros costos de reparación y reemplazo de mano de obra y equipos en las flotas de activos de cientos o miles de motores BoP. También hay que considerar los costos de las pérdidas de producción de la planta cuando las fallas afectan los plazos y los acuerdos de nivel de servicio (SLA) de producción o extienden los retrasos.
Estos riesgos se pueden mitigar utilizando soluciones de monitoreo de condición basadas en IoT que integran sensores de bajo costo y baja potencia en una plataforma de comunicación inalámbrica con capacidades de análisis en la nube impulsadas por IA. Este enfoque reduce los costos y las barreras de implementación para mover el mantenimiento de un enfoque reactivo o preventivo a un enfoque más predictivo y basado en el conocimiento que abarca toda la línea de producción.
Un nuevo monitoreo de condición
Modelo de implementación
Las soluciones actuales basadas en IoT e impulsadas por inteligencia artificial emplean sensores de bajo costo que son fáciles de instalar, lo que hace que sea económicamente viable usar el monitoreo de condición en toda la gama de activos de la línea de producción, incluidos los motores BoP. Las soluciones utilizan algoritmos y análisis de datos para ayudar a determinar el estado de los activos y predecir problemas o fallas, y aprovechan los potentes motores de políticas para identificar y advertir a los usuarios sobre problemas inminentes en tiempo real.
A diferencia de las soluciones tradicionales de monitoreo de condiciones, las ofertas basadas en IoT no requieren infraestructura cableada, servidores o antenas, y son más fáciles de integrar en las prácticas de inspección, mantenimiento y operaciones de un gerente de planta en múltiples flotas de activos. Las balizas Bluetooth de baja energía (BLE) con sensores de vibración y temperatura se instalan en cada activo y se utilizan para la detección de encendido / apagado y el monitoreo en tiempo real de los ciclos de trabajo, la temperatura y la vibración.
Las balizas utilizan el procesamiento de borde para calcular las métricas de estado de la máquina para ayudar a reducir la cantidad de datos transmitidos a través de una puerta de enlace de Bluetooth a WiFi a la nube, donde se realizan más análisis. Esto también permite una recopilación de datos más frecuente, proporcionando visibilidad casi en tiempo real del estado de vibración de la máquina con nuevos datos cada dos minutos.
Después de un período de entrenamiento inicial para aprender el comportamiento de vibración de línea de base para cada activo en el que se instala una baliza, la solución genera modelos de actividad normal. Luego, utiliza un motor de políticas para identificar desviaciones significativas de esta línea de base y notificar a las organizaciones sobre estos cambios para ayudarlas a tomar medidas para reducir el tiempo de inactividad. A partir de este momento, la administración de la planta tiene una herramienta fundamental para mejorar las estrategias proactivas de mantenimiento, inspección y operación y tomar mejores decisiones sobre qué acciones tomar.
Estas herramientas de habilitación de mantenimiento predictivo se entregan a través de suscripciones de software como servicio (SaaS) basadas en la nube. Esto brinda a las organizaciones una mayor flexibilidad para implementar las capacidades que necesitan, cuando las necesitan, desde la administración básica de la flota para la configuración remota del hardware, pasando por un monitoreo más profundo del estado del equipo, hasta una gama completa de monitoreo avanzado del estado, incluida la detección de fallas para alertas basadas en IA. .
Éxitos tempranos
Los fabricantes de múltiples industrias están obteniendo valiosos beneficios al adoptar soluciones de monitoreo de condición basadas en IoT utilizando análisis en la nube impulsados por IA. Por ejemplo, uno de los fabricantes de acero más grandes del mundo está monitoreando la temperatura y la vibración del motor en un entorno de 70 a 80 grados Celsius para mejorar su estrategia de mantenimiento predictivo y reducir el tiempo de inactividad no planificado del equipo en toda la planta.
Estas soluciones a menudo encuentran problemas que se pasan por alto durante la inspección.
Un importante fabricante de productos farmacéuticos fue alertado sobre este problema, que se puso en observación ya que no se pudo validar visualmente (ver Fig. 1). La alerta se volvió a activar en una semana, lo que llevó a una verificación exhaustiva con instrumentación de laboratorio de gran ancho de banda y procesamiento de datos avanzado. Se confirmó la degradación y la planta realizó las reparaciones necesarias para evitar costosos tiempos de inactividad no planificados.
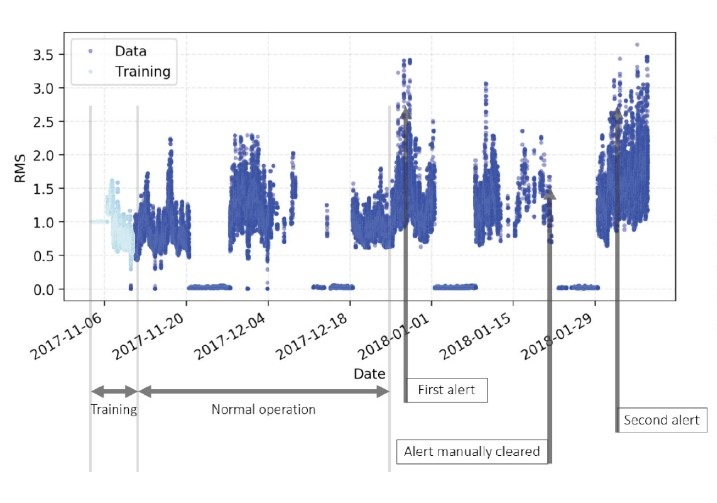
Tradicionalmente, las plantas no han implementado soluciones de monitoreo de condición en equipos que no sean los más costosos o de misión crítica. Ahora, con esta nueva visibilidad mejorada en toda la línea de producción, las organizaciones pueden frustrar el tiempo de inactividad no planificado y las reparaciones inesperadas, el reemplazo de equipos y los requisitos de mano de obra asociados relacionados con la mayor parte de su flota.
Al combinar balizas Bluetooth con un motor de análisis basado en inteligencia artificial basado en la nube, las últimas soluciones abordan estos desafíos de una manera muy diferente a la del pasado. Brindan a las organizaciones una manera rápida y fácil de recopilar y monitorear los datos procesables que necesitan para programas de mantenimiento predictivo en toda la planta y operaciones generales más inteligentes.
El autor es Brad M. Hopkins, director de gestión de productos de monitorización de condiciones de HID Global.
Tecnología de Internet de las cosas
- OSGi para soluciones de IoT:una combinación perfecta
- El mercado de monitoreo de condiciones alcanzará los $ 3.9B para 2025
- Honeywell adquiere la empresa de soluciones de monitorización inteligente
- Mejora del mantenimiento proactivo con monitoreo de lubricación en tiempo real
- La monitorización del estado aumenta y mantiene la eficiencia en la producción de papel
- Mantenimiento predictivo para fabricantes
- Aprovechamiento del gemelo digital de circuito cerrado para ampliar las capacidades de mantenimiento predictivo
- Por qué necesita el mantenimiento predictivo
- Peligros del monitoreo de condición y potencial para el mantenimiento de la fábrica
- IoT para mantenimiento predictivo
- El monitoreo de condición de 4 vías beneficia a los equipos rotativos