Celebrando los últimos cinco años
El mes pasado celebramos cinco años desde que un puñado de personas en un garaje diseñó la primera impresora 3D de fibra de carbono. Gracias a nuestros clientes por contribuir a nuestro éxito y por creer en nosotros durante los últimos cinco años. Aquí está la historia de cómo comenzamos, los primeros usuarios que creyeron en nosotros y cómo nuestros clientes hicieron posible que continuamos por el camino de la innovación.
El Mark One
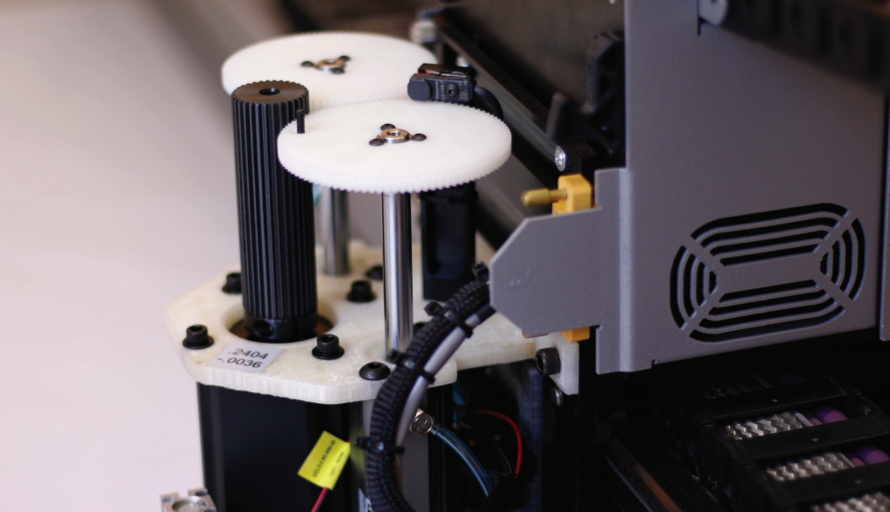
En enero de 2014, presentamos la primera impresora 3D del mundo capaz de imprimir en fibra de carbono continua en SolidWorks World:The Mark One. Autometrix creyó en el concepto y compró una de las primeras impresoras Markforged.
Autometrix proporciona equipos de corte y software de modelado para una variedad de aplicaciones industriales, que se utilizan para cualquier cosa, desde el transporte hasta los dispositivos médicos. La compañía quería llevar la creación de prototipos internamente, pero los ingenieros "necesitaban asegurarse de que los resultados del proceso de creación de prototipos fueran reales para lo que [ellos] estaban tratando de diseñar", según Tyler Green, ingeniero eléctrico de Autometrix. Después de darse cuenta de que el equipo podía imprimir en 3D una pieza reforzada con fibra que realmente funcionaba en su cabezal de corte, el equipo se convenció de la Mark One.
Eso fue solo el comienzo. Luego, Autometrix imprimió un cabezal de corte completo utilizando el Mark One, y los ingenieros descubrieron que el cabezal de corte impreso pesaba media libra menos que su contraparte de aluminio. Las piezas livianas fabricadas en el Mark One resistieron todo el impacto que hacen sus contrapartes de metal y más, lo que permitió a Green y a otros ingenieros de Autometrix mejorar y expandir sus sistemas mecánicos.
La marca dos
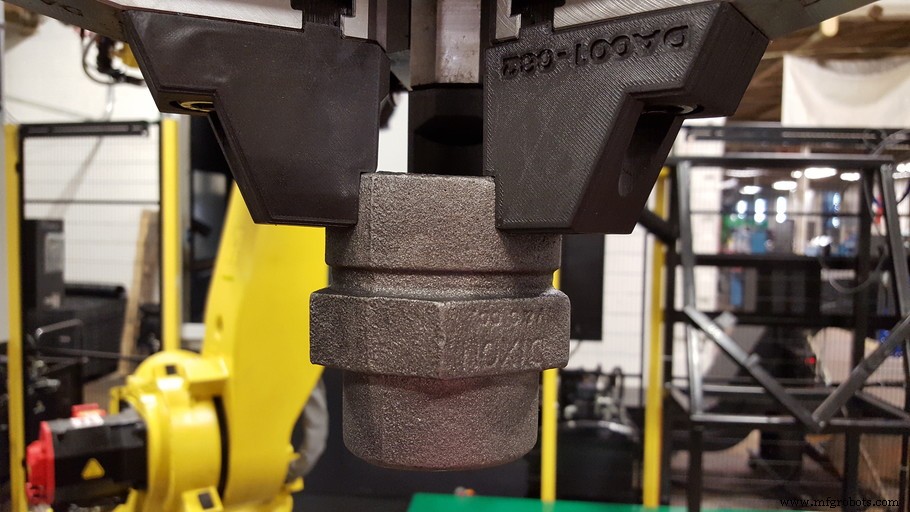
Lanzamos la Mark Two, la próxima generación de la Mark One, en febrero de 2016. La Mark Two presentaba un sistema de impresión compuesta completamente rediseñado que permitía piezas de mayor resistencia y calidad que su predecesor. El fabricante de accesorios y válvulas Dixon Valve necesitaba una impresora que pudiera crear piezas de alta resistencia, lo que hacía que la Mark Two fuera una gran opción para la empresa.
Válvula Dixon buscaba mejorar sus soluciones de línea de producción. Los ingenieros Max de Arriz y J.R. Everett necesitaban crear mordazas de agarre de alta resistencia para brazos robóticos industriales en su proceso de fabricación. El brazo robótico transfiere varias piezas diferentes entre dos centros de torneado vertical, y la empresa necesitaba que las mordazas fueran fuertes, seguras y resistentes a los productos químicos. La configuración de cada línea de productos requería un equipo personalizado para sujetar piezas específicas de manera eficiente. La empresa sabía que necesitaba una impresora 3D para piezas personalizables, lo que llevó a sus ingenieros a la Mark Two.
“Con el Mark Two, pudimos reacondicionar un brazo robótico en una celda de fabricación en menos de 24 horas”, exclamó Everett. El Mark Two permitió a Dixon Valve producir nuevas soluciones de fabricación a una velocidad y un costo sin precedentes, proporcionando a la empresa una nueva y poderosa herramienta en su caja de herramientas. Everett siente que el Mark Two es un componente crítico en el proceso de diseño de la empresa, y dice que "realmente está cambiando la forma en que trabajamos hasta el punto en que realmente estamos alterando nuestros procedimientos y planes para acomodar este innovador producto".
La introducción de Onyx
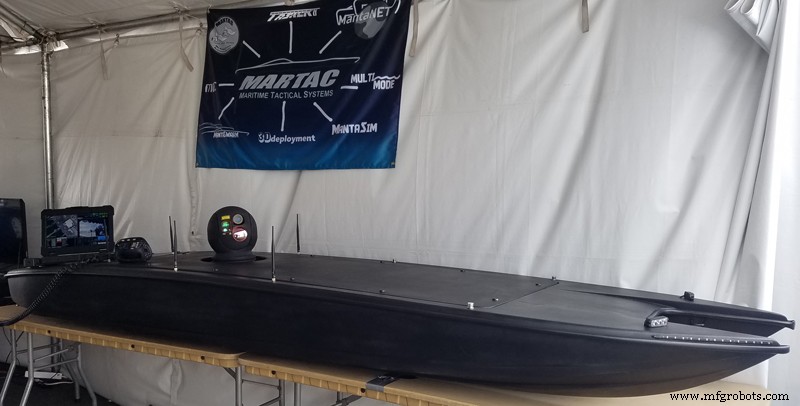
En 2016, lanzamos Onyx, nuestro termoplástico reforzado compuesto de próxima generación especialmente adecuado para entornos de fabricación. Como Onyx tiene una estabilidad térmica muy alta, no es propenso a deformarse. Tiene una resistencia y rigidez superiores, y es un material de alta precisión y alta repetibilidad. Fue esta alta precisión la que atrajo por primera vez a MARTAC a imprimir en Onyx.
MARTAC (Maritime Tactical Systems) diseña y fabrica embarcaciones acuáticas no tripuladas de alto rendimiento. La compañía buscaba crear tomas geométricamente complejas que pudieran ayudar a enrutar el agua de mar a través de los canales de enfriamiento. Al imprimir en 3D esta pieza en Onyx, MARTAC pudo crear una geometría compleja y personalizada que no necesitaba ajustarse a las restricciones de mecanizado sustractivo.
Onyx es ahora el material principal para los vasos MARTAC. “Lo bueno de usar Onyx es que no se corroe por estar constantemente en agua salada. Estas partes también han demostrado ser bastante resistentes a los escombros en el agua ”, dice Ian Weaver, coordinador de operaciones de MARTAC. La impresión de estas tomas redujo drásticamente los costos de fabricación para la empresa en lo que sería una pieza increíblemente difícil de fabricar.
Hacia la industria
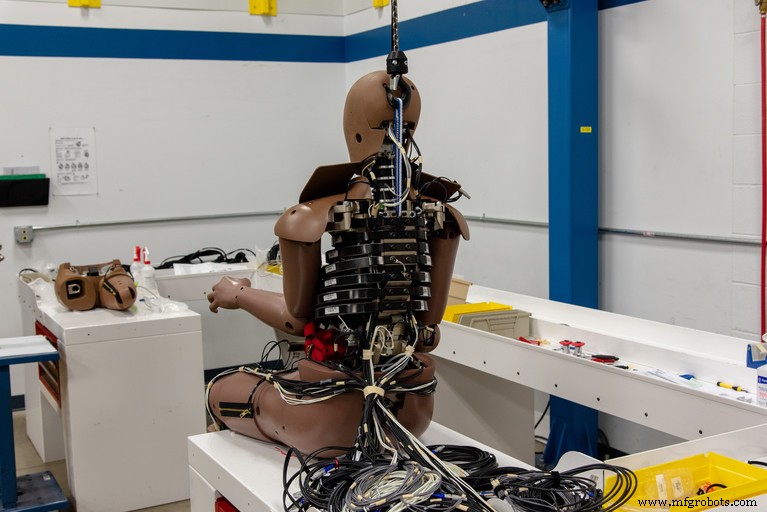
Con casi tres veces el volumen de construcción y un conjunto de sensores de autocontrol avanzado, la X7 fue nuestra primera impresora 3D de formato industrial. Humanetics, el principal proveedor mundial de maniquíes para pruebas de choque, necesitaba una nueva tecnología para acelerar su proceso de sustitución de piezas grandes. El X7 fue la solución perfecta para ellos.
Humatética Los maniquíes de prueba de choque se utilizan en las industrias automotriz, militar y aeroespacial. Ante el problema del desgaste de los moldes demasiado rápido, Humanetics buscaba una forma rentable de fabricar piezas duraderas que soportaran altas temperaturas. Kris Sullenberger, ingeniero de diseño de Humanetics, examinó los moldes de impresión 3D para las piezas de prueba de choque y se encontró con el X7.
Humanetics ha impreso entre cinco y diez moldes y planea reemplazar muchos de los 150 moldes de la compañía con impresiones Markforged. Además de los beneficios de costo y durabilidad, Kris descubrió que los moldes impresos producen mejores piezas. Donde los moldes de silicona dejan costuras y otras imperfecciones, el ajuste preciso de los moldes impresos resulta en una pieza casi perfecta. Desde la impresión de piezas ficticias de prueba de choque de producción para su equipo de diseño hasta el reemplazo de accesorios masivos y antiguos para los técnicos de ensamblaje, Humanetics casi siempre tiene la máquina de impresión. A Kris le gusta cómo puede optar por gastar "miles y miles de dólares para que estos se mecanicen o produzcan en el exterior" o "hacerlos en casa por literalmente decenas o cientos de dólares".
Metal X
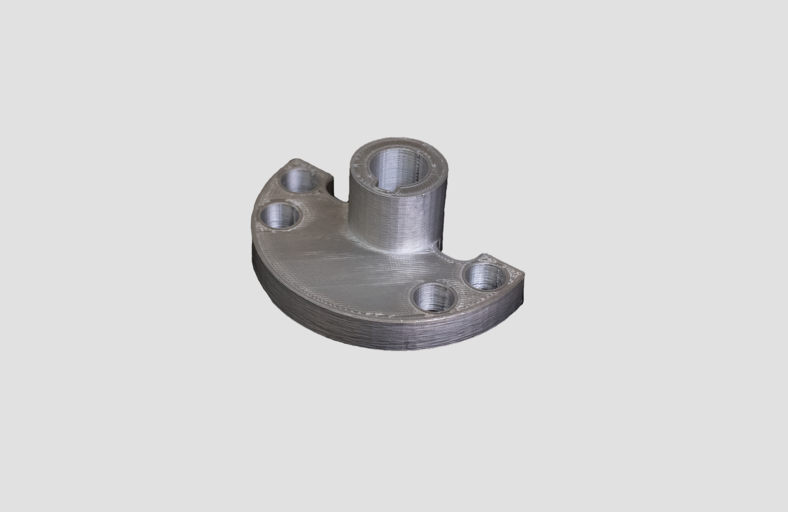
En el último año, agregamos impresión 3D de metal a nuestra línea de productos en forma de Metal X. La capacidad de imprimir piezas de acero inoxidable abre nuevas oportunidades para imprimir reemplazos iguales para una amplia variedad de líneas de productos. . Stanley Infrastructure adoptó el Metal X para investigar la sustitución de piezas caras hechas a medida por piezas impresas baratas.
Infraestructura Stanley , una división de Stanley Black &Decker, es el fabricante de herramientas hidráulicas de mano más grande del mundo. La empresa necesitaba una pieza para sujetar las ruedas guía ajustables de una amoladora de ranas de ferrocarril, que era difícil de mecanizar. Los ingenieros optaron por mecanizar ejes de rueda con un solo bloque de acero, pero ~ 90% del material de stock se desperdició en cada parte debido al diámetro de la brida y la longitud del eje. Con la ayuda de los ingenieros de Markforged, Stanley Infrastructure rediseñó el eje de la rueda para que fuera un conjunto de tres partes. Al comprar un eje y una llave listos para usar, la compañía pudo imprimir fácilmente la brida más compleja en un Metal X. El nuevo ensamblaje pasó las pruebas de durabilidad y caída por abuso.
Según un ingeniero de Innovación de Infraestructura de Stanley, "es muy factible aprovechar la plataforma Metal X para fabricar aditivamente la carcasa del actuador discutida con una inversión mínima de capital y tiempo". Desde que adquirió la impresora, Stanley Infrastructure se ha centrado en imprimir piezas de alta calidad, lo que ha minimizado el tiempo de mecanizado y reducido los costes.
Qué sigue
Desde empresas Fortune 100 hasta fabricantes familiares, miles de empresas utilizan la tecnología Markforged para mejorar sus productos y procesos. Y, al igual que estas empresas, buscamos constantemente nuevas formas de hacer que nuestros productos y procesos sean mejores que nunca.
¡Por muchos años más de innovación de nuestros clientes!
¿Quiere probar la resistencia de nuestras impresoras? Solicite una pieza de muestra gratuita de Markforged aquí .
¿Quieres ver más publicaciones como esta? Síguenos en Facebook , Twitter , Instagram y LinkedIn para obtener más actualizaciones
Impresión 3d
- Cómo la impresión 3D está dejando su huella en el mundo de la medicina
- Celebrando 10 años de impresión 3D de Formlabs
- Guía de Carl Calabria para el uso de inserciones en Mark One
- Cómo usar la barra de pegamento en su cama de impresión Mark One
- Amazon-Whole Foods:dos años después del acuerdo
- Cinco formas de lograr una última milla más ecológica
- Las cinco empresas de equipos de construcción más populares
- Los ingresos de 5G IoT se dispararán en los próximos cinco años
- La fabricación digital se triplica en dos años
- Protocalabazas a través de los años
- Mecanizado, disrupción y los próximos años