El tanque tipo V totalmente compuesto de NCC demuestra la futura tecnología de tanques espaciales compuestos
El Centro Nacional de Compuestos (NCC, Bristol, Reino Unido), con la orientación de la industria del fabricante aeroespacial Thales Alenia Space (Cannes, Francia), ha fabricado un demostrador de tanque sin revestimiento (Tipo V) totalmente compuesto en el marco del proyecto SpaceTank. Se dice que es representativo de los que se utilizan para los tanques de propulsante de vehículos de lanzamiento y satélites, proporcionando un ahorro de peso estimado del 30% en comparación con los tanques de propulsante metálicos convencionales en uso actual. La NCC ha demostrado esto para atraer el interés del Reino Unido en la fabricación de tanques compuestos para futuras necesidades de propulsión espacial. Según la NCC, este proyecto de exhibición demuestra cómo la tecnología de compuestos avanzados puede desempeñar un papel vital en las estructuras de ingeniería del futuro en la propulsión espacial al reducir el peso estructural del tanque y los costos de lanzamiento del satélite (descargue el PDF del estudio de caso).
El objetivo general del proyecto SpaceTank era desarrollar herramientas de investigación y desarrollo basadas en el Reino Unido necesarias para la fabricación e inspección de recipientes a presión criogénicos. Más específicamente, el proyecto de un año se centró en el desarrollo de una nueva solución de fabricación de tanques para contener propelentes criogénicos.
La industria espacial reconoce el papel fundamental de los materiales compuestos en el espacio, y algunas empresas ya están explorando su uso en el diseño de tanques espaciales. Por ejemplo, Virgin Orbit (Long Beach, California, EE. UU.) Y RocketLab (Auckland, Nueva Zelanda) han desarrollado y demostrado tanques compuestos como alternativas al metal para el Launcher One y Electron cohetes respectivamente. En Australia, Omni Tanker (Smeaton Grange) y sus socios buscan desarrollar y comercializar un tanque de hidrógeno líquido compuesto sin revestimiento (LH 2 ), y más cerca de casa en Europa, MT Aerospace (Augsburg, Alemania) está desarrollando materiales y métodos de fabricación y sometiéndose a pruebas para un nuevo tanque de combustible para cohetes. Se espera que el proyecto NCC SpaceTank nivele al Reino Unido como actor clave en este campo.
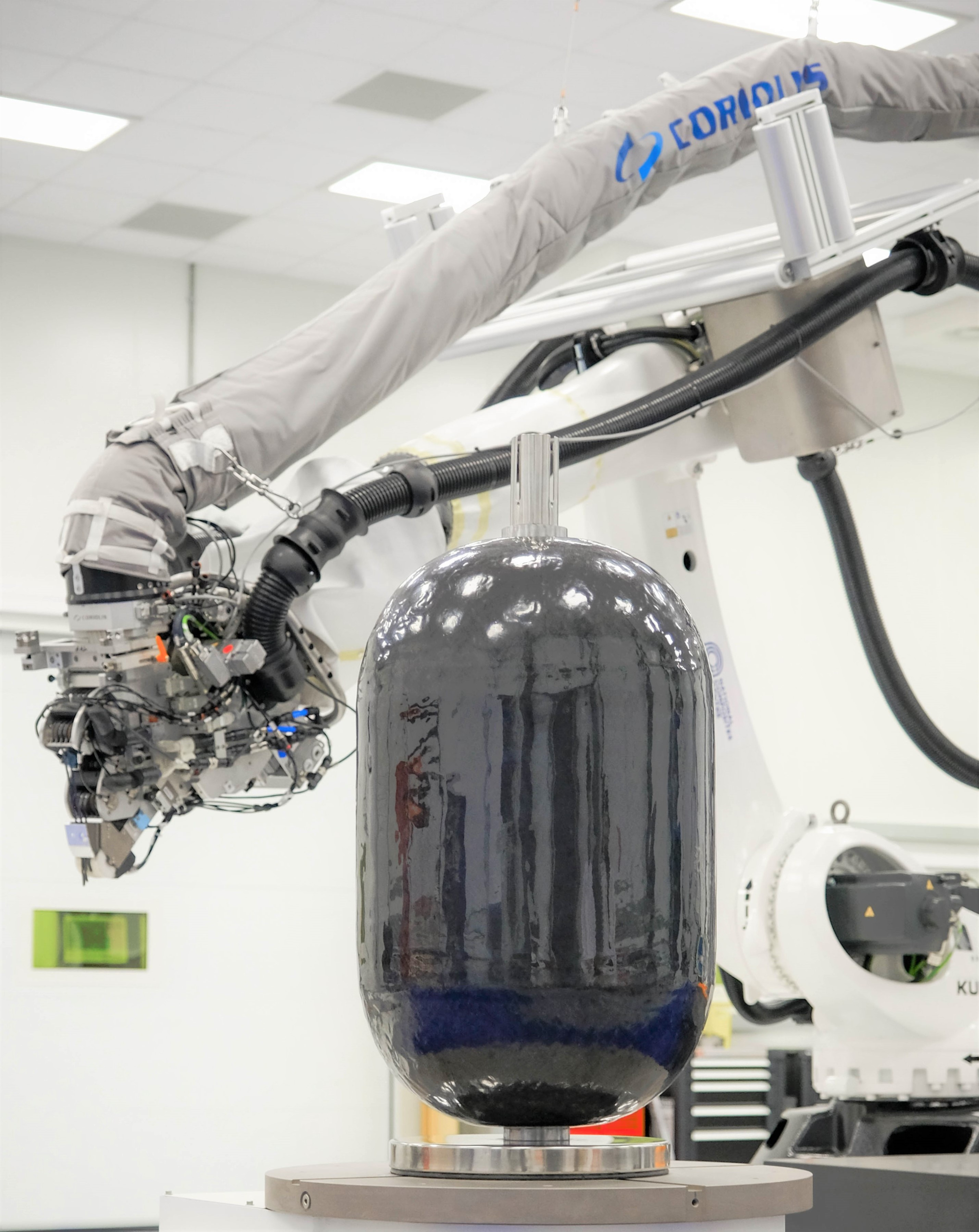
El demostrador NCC SpaceTank creado tiene 750 milímetros de largo, 450 milímetros de diámetro y una capacidad de almacenamiento de fluidos de más de 96 litros. Ha sido diseñado y fabricado con un espesor de pared nominal de 4.0-5.5 milímetros, lo que permite que el tanque resista 85 bar de propelente a presión. El cuerpo principal compuesto de fibra de carbono consta de 8 kilogramos de masa de material, pero según la NCC, como con todas las estructuras de ingeniería, hay más oportunidades con SpaceTank para optimizar aún más esta reducción de peso. Además, la clasificación de presión del NCC SpaceTank se puede aumentar con el uso de fibras de carbono de mayor resistencia y aumentando el espesor del compuesto. Alternativamente, el SpaceTank podría optimizarse en peso y costo para aplicaciones de presión mucho más baja utilizando un material compuesto más delgado y de menor rigidez.
Durante el proyecto SpaceTank, el equipo de NCC desarrolló un método innovador para incluir los puertos de la válvula de fluido de metal en la herramienta lavable, para eliminar la necesidad de cualquier ensamblaje secundario y operaciones de unión necesarias para el producto final. Estos puertos de la válvula de fluido se mantuvieron en las herramientas novedosas, lo que les permitió unirse a la fibra de carbono durante la última etapa del proceso de fabricación.
El cuerpo principal del tanque utiliza preimpregnado de fibra de carbono epoxi MTC510 suministrado por SHD Composites (Mooresville, N.C., EE. UU.) En un ancho de cinta de 300 milímetros. MTC510 es un sistema de resina epoxi que está diseñado específicamente para curar entre 80 ° C y 120 ° C y está endurecido para aumentar su tolerancia al daño.
Este material fue preparado para el proceso de fabricación de SpaceTank por Bindatex (Bolton, Reino Unido), que también realizó un corte de precisión de ancho estrecho de la cinta y devolvió 22.000 metros (aproximadamente 72.178 pies) del material en un formato de 6,35 milímetros preparado de acuerdo con la Requisito de NCC para su uso en su celda de fabricación de colocación automatizada de fibra (AFP) Coriolis (Queven, Francia).
La cinta de hendidura se depositó sobre las herramientas lavables utilizando la operación de bobinado de filamento tensado del sistema Coriolis AFP. Se utilizó una combinación de bobinado helicoidal y de aro diseñada por los ingenieros de NCC utilizando el software de bobinado de filamentos Cadwind (Bruselas, Bélgica) de Material para depositar más de 24 capas del material con un espesor nominal de 5,5 milímetros. El grosor y la dirección / ángulo del devanado utilizados aquí fueron solo para demostración; Es posible que el NCC aumente o disminuya el espesor de la pared compuesta y altere el ángulo de enrollamiento y la estructura de la capa para optimizar completamente el tanque para una presión específica o un requisito de carga.
Inmediatamente después de la deposición del material, se inspeccionó el NCC SpaceTank para detectar defectos y variaciones de espesor. A continuación, se curó en autoclave a 100 ° C y se volvió a inspeccionar posteriormente. Después del curado se utilizaron técnicas de inspección ultrasónica C-Scanning y termografía de prueba no destructiva (NDT), y estos métodos se compararon y contrastaron para determinar la idoneidad de inspeccionar futuros tanques para detectar defectos como delaminación y porosidad. Finalmente, después de completar la evaluación de la calidad del END, el núcleo interno de las herramientas se lavó con agua fría a presión para dejar la cavidad interna del tanque vacía.
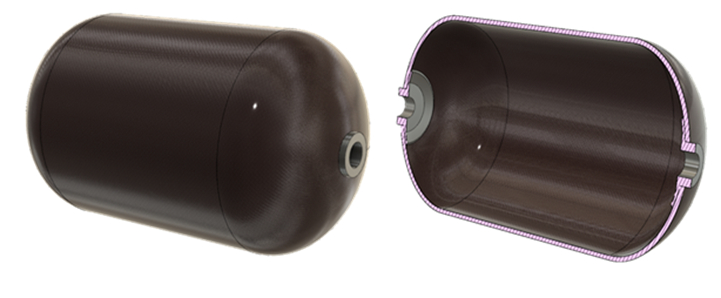
Según la NCC, la técnica de mecanizado para el SpaceTank sin revestimiento resultó ser difícil, lo que llevó al desarrollo de un proceso de fundición en asociación con AeroConsultants (Huntingdon, Reino Unido) utilizando el material de núcleo soluble en agua Aqua de la empresa. La herramienta terminada presenta un núcleo macho centralizado con un espesor de pared nominal de 30 milímetros que se moldea en dos partes y luego se une. La herramienta tiene tres anillos de refuerzo internos (lavables) que fueron diseñados y fabricados para ayudar a soportar la carga de torsión esperada durante el laminado automatizado del composite y la presión ejercida durante el curado en autoclave.
Esta demostración de la NCC ahora proporciona una base de investigación en el Reino Unido para el desarrollo futuro de tanques de propulsores y ayuda a respaldar una nueva cadena de suministro en el Reino Unido para componentes y equipos de última generación para la fabricación de tanques compuestos.
Según se informa, la actividad de investigación futura en esta área también apoyará el aumento de la participación del 5% del Reino Unido en la economía espacial global. Un informe del gobierno del Reino Unido en mayo de 2021 mostró que los ingresos de la industria espacial del Reino Unido aumentaron de £ 14,8 mil millones en 2016/2017 a £ 16,4 mil millones en 2018/2019. El informe resumido de la Agencia Espacial del Reino Unido también destacó que se han creado más de 3.000 puestos de trabajo en el sector espacial del Reino Unido durante los últimos dos años (2019-2021).
fibra
- ¿Es la tecnología de fabricación híbrida el futuro de la fabricación aditiva?
- Impresión 3D compuesta:una tecnología emergente con un futuro brillante
- SMI proporciona la tecnología compuesta de la más alta calidad para aplicaciones militares
- Su guía de ciencia y tecnología compuestas
- La tecnología de realidad aumentada se está calentando en el espacio industrial
- Varilla compuesta para infraestructura futura
- Innovate UK otorga a NCC £ 355k para ayudar a lograr un futuro neto cero
- Fabricación de compuestos futuros:AFP y fabricación aditiva
- Compuesto + metal:Tecnología híbrida de perfil hueco
- AMRC, NCC, Dowty Propellers para desarrollar palas de hélice de material compuesto ligero
- 7 asombrosas tendencias tecnológicas para dar forma a la ingeniería del futuro