Las piezas híbridas sobremoldeadas abren nuevos mercados de compuestos
Complejidad y fuerza. Los componentes como el soporte B para contenedores de almacenamiento de aviones exhiben una gran complejidad y un requisito de alta resistencia, una combinación para la que la técnica de sobremoldeo híbrido es especialmente adecuada. Fuente, todas las imágenes | TxV Aero Composites
A menudo, en el mercado aeroespacial, un OEM está dispuesto a pagar más por un componente compuesto, sabiendo que la inversión generará dividendos en ahorros de combustible debido al peso liviano del componente, una vida más larga debido a un menor desgaste u otras reducciones en el funcionamiento. y costos de mantenimiento. Esta vista del "ciclo de vida del producto" ha abierto muchos mercados y aplicaciones a los compuestos. Más inusual es un componente compuesto para el que el costo de adquisición en sí es menor que el de la versión metálica. Pero esto está cambiando. Algunos nuevos procesos automatizados de fabricación de compuestos están comenzando a inclinar la balanza a favor de los compuestos, y entre ellos se encuentra un proceso de sobremoldeo híbrido desarrollado por TxV Aero Composites (Bristol, R.I., EE. UU.).
Una empresa conjunta de Tri-Mack Plastics Manufacturing (Bristol, R.I., EE. UU.) Y Victrex (Thornton Cleveleys, Reino Unido), TxV ha avanzado su técnica de sobremoldeo híbrido hasta el punto del estado de producción comercial. La compañía se ha asociado con SFS intec Aircraft Components (Althengstett, Alemania) para rediseñar y producir comercialmente un soporte para contenedores de almacenamiento de aviones fabricado anteriormente con aluminio de grado aeroespacial. Una historia de éxito en sí misma, el soporte también demuestra el potencial del sobremoldeo híbrido y la cinta unidireccional de fibra de carbono / poliariletercetona (PAEK) VICTREX AE 250 para un valioso ahorro de peso y costos en numerosas aplicaciones aeroespaciales:ventajas logradas al reemplazar un proceso de mecanizado de metal sustractivo con un proceso de compuestos en el que se agrega material, no se resta.
De la resta a la suma
Los maquinistas y talleres mecánicos que producen componentes metálicos en máquinas CNC se han apodado a sí mismos como "fabricantes de chips" por la razón obvia de que sus procesos cortan el material innecesario de los espacios en blanco de metal para fabricar componentes, creando virutas de chatarra. Estos chips representan un aspecto costoso del mecanizado de metales, ya sea que se eliminen, se envíen a un reciclador o se reprocesen internamente. En el caso del soporte del compartimento de almacenamiento superior de SFS intec, del 60 al 70% del aluminio se convierte en chatarra durante los diversos pasos de fresado necesarios para mecanizarlo.
Esta alta tasa de desperdicio hace que el costo de la materia prima para una versión compuesta de forma neta o casi neta del soporte sea potencialmente más bajo que el costo del material metálico. “Podemos competir con el aluminio menos costoso (por libra) debido a los chips; si la relación de compra / venta es de 8:1, la mayor parte del aluminio comprado se convierte en chatarra ”, señala Jonathan Sourkes, gerente de cuentas senior de TxV. “Otro factor es el tiempo que dedica cada componente al fresado. Podemos fabricar piezas [compuestas] en minutos, no en horas ".
Más allá de los costos de materia prima, las versiones compuestas de componentes como el soporte, que presentan una geometría compleja y requieren un alto rendimiento de carga, no han sido económicamente viables con las opciones de fabricación históricamente disponibles. Por un lado, si los componentes se fabricaran con refuerzo de fibra cortada de bajo costo en un proceso de alta velocidad y bajo contacto como el moldeo por inyección, el componente no alcanzaría un rendimiento de carga suficiente. Por otro lado, si se hiciera con un refuerzo de fibra continua de mayor capacidad de carga a través de un proceso de baja velocidad y alto contacto, que generalmente implica un laminado manual, la producción sería demasiado lenta y / o impondría costos de fabricación que harían que el producto final demasiado caro.
Debido a estos obstáculos a las nuevas aplicaciones de compuestos de este tipo, la industria de los compuestos en su conjunto ha dedicado importantes recursos al desarrollo de procesos automatizados que pueden producir dichos componentes a tasas de producción adecuadamente altas y con suficiente capacidad de carga para satisfacer las necesidades y especificaciones de los clientes aeroespaciales. . Con miras a la producción comercial de dichos componentes compuestos, TxV nació en 2017 específicamente para acelerar la adopción comercial de procesos de fabricación innovadores para aplicaciones de compuestos a base de policetona en toda la industria aeroespacial.
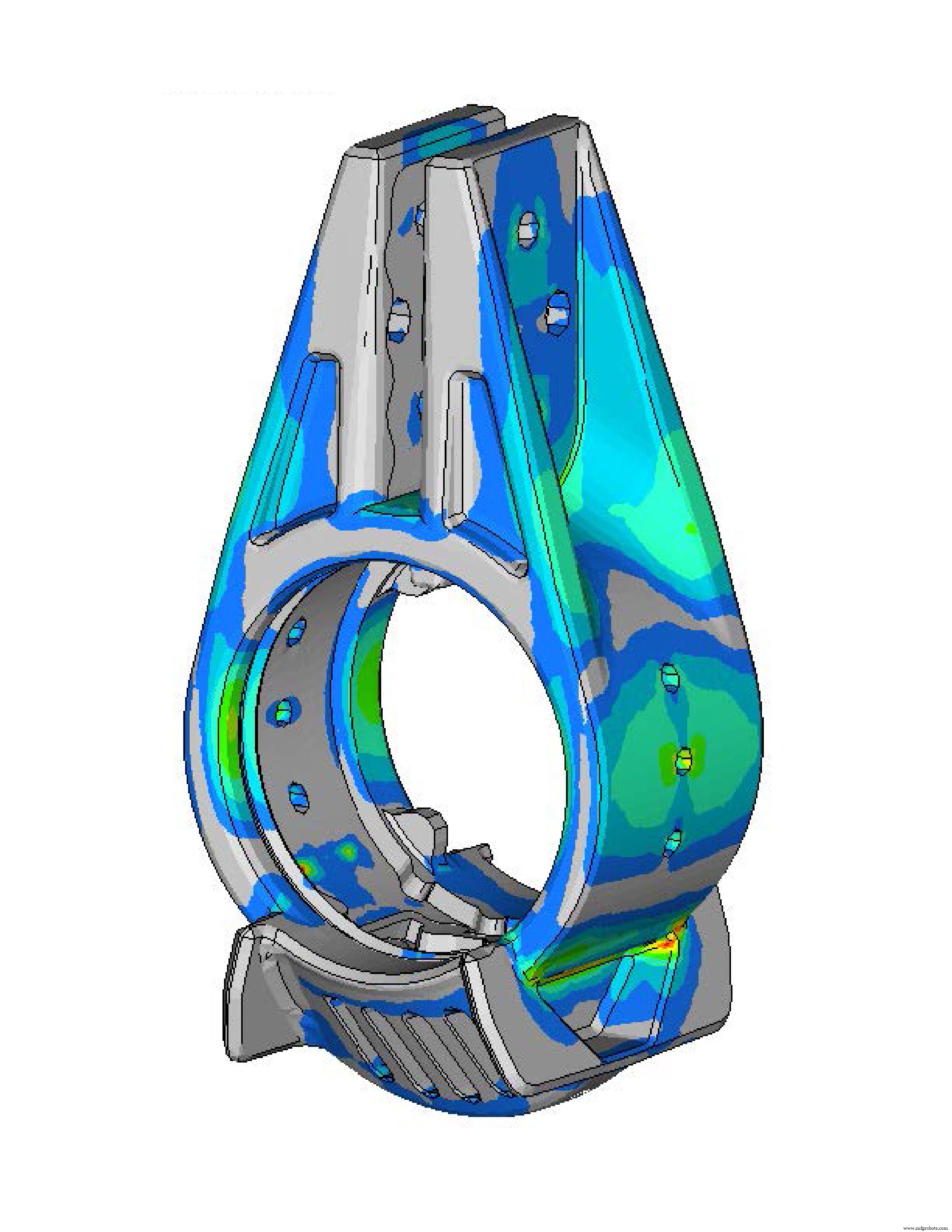
Creación de prototipos virtuales. Utilizando datos patentados desarrollados para caracterizar la relación entre el laminado y el sobremolde, TxV iteraba las capas y las orientaciones de las capas sin tener que fabricar y probar un prototipo físico. Las iteraciones continúan hasta que las tensiones visibles, como se muestra aquí, están dentro del rango de casos de carga proporcionados.
La solución híbrida sobremoldeada de TxV incorpora dos avances clave al estado del arte en la fabricación de componentes compuestos. Primero, automatiza la producción de aquellas partes del componente que requieren la resistencia o rigidez de un refuerzo de fibra continuo. En segundo lugar, aprovecha la velocidad del moldeo por inyección para completar las complejas geometrías del componente. Más específicamente, produce un laminado a medida para manejar cargas, que luego se sobremoldea para funcionalizar y crear geometrías de piezas finales. La técnica híbrida, según Sascha Costabel, jefe de innovación de SFS intec Aircraft Components, “es una buena opción para componentes que deben soportar altos niveles de tensión mecánica y geometrías que requieren múltiples pasos de procesamiento donde se utiliza el mecanizado convencional”.
Asociarse con SFS intec ha sido una gran elección, dice Sourkes. “Como líder mundial en accesorios de sistemas, SFS siempre está haciendo algo realmente interesante. Son muy innovadores y están dispuestos a invertir en nuevas tecnologías ”, apunta. SFS intec también tiene una relación sólida con sus clientes de aeronaves, agrega, y poseen la capacidad para realizar procesos de calificación, clave para la adopción de un componente rediseñado en la industria aeroespacial.
El soporte del compartimiento de almacenamiento de la aeronave, específicamente denominado “soporte B”, fue elegido como el primer componente de fijación para el rediseño de materiales compuestos porque es representativo de los componentes que son difíciles de diseñar y producir. Después de la ingeniería colaborativa, la conceptualización y el diseño de piezas y el modelado del rendimiento a través de una herramienta de análisis de elementos finitos (FEA) de Altair (Troy, Michigan, EE. UU.), El equipo del proyecto repitió desde el primer artículo para validar, probar y probar el modelo. El diseño para la fabricación fue fundamental para el desarrollo del soporte compuesto, que aprovecha las ventajas de fabricación de la colocación de cinta automatizada para los elementos continuos reforzados con fibra y el moldeo por inyección de alta velocidad para los elementos reforzados con fibra cortada.
Soportes del edificio B
Un aspecto clave del proceso de sobremoldeo híbrido es el uso de distintos polímeros de la misma clase. PAEK sirve como resina de matriz para las porciones de compuesto de fibra continua del soporte, mientras que la polieteretercetona (PEEK) se usa en las áreas sobremoldeadas. VICTREX PAEK y PEEK cuentan con una resistencia superior a la fatiga, los productos químicos y la corrosión; excelente resistencia al humo, las llamas y la toxicidad; conformabilidad rápida; y soldabilidad. VICTREX AE 250, un PAEK (LM PAEK) de bajo punto de fusión, ofrece una temperatura de fusión de 40 grados C más bajo que PEEK. “Cuando el PEEK fundido fluye sobre la superficie del compuesto LM PAEK, la temperatura de fusión más baja permite una unión fuerte”, explica Sourkes.
Las materias primas específicas para el soporte B son la cinta PAEK reforzada con fibra de carbono unidireccional VICTREX AE 250 (58% fibra de carbono) en anchos de dos pulgadas; y VICTREX PEEK 150CA30 corto relleno de fibra de carbono (30% fibra de carbono). Estos materiales alimentan las células de trabajo de producción de sobremoldeo híbrido, que crean los soportes a través del siguiente proceso de varios pasos.
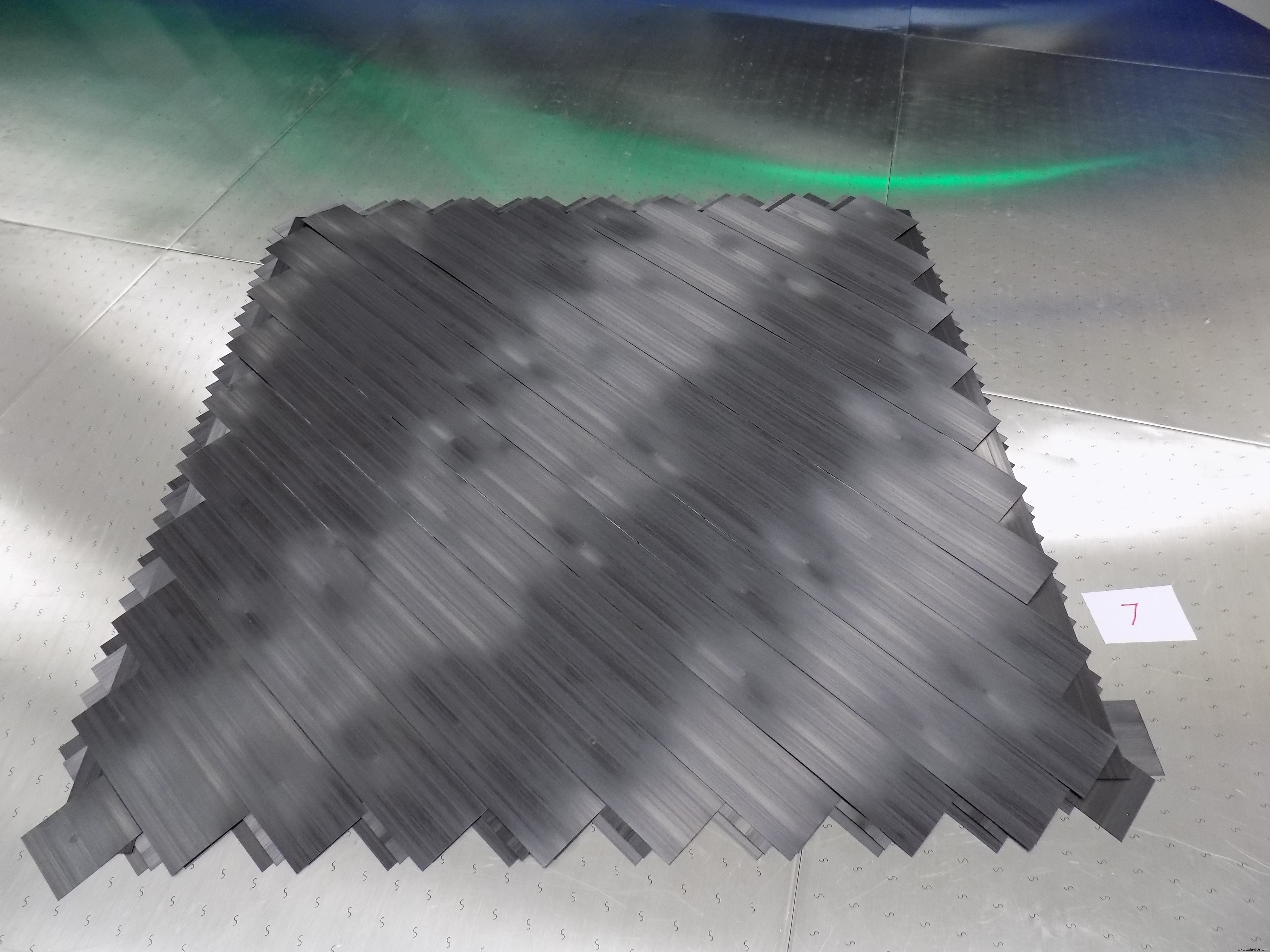
Paso 1. Un sistema automatizado de colocación de cinta Dieffenbacher Fiberforge 2000 produce láminas en bruto personalizadas.
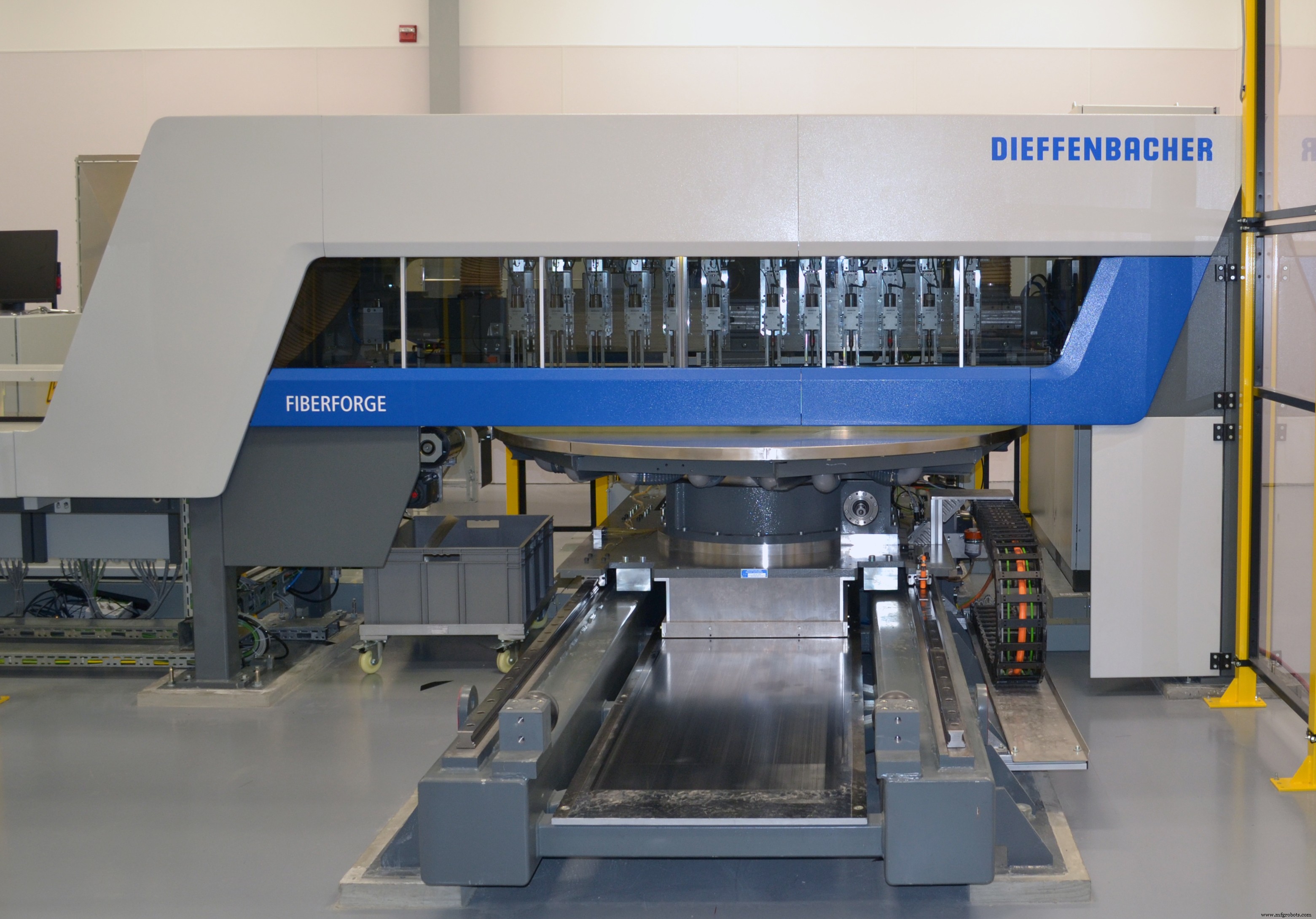
Primero, las cintas de fibra de carbono / PAEK se colocan en una pieza en bruto a medida utilizando un sistema de colocación de cinta Dieffenbacher (Eppingen, Alemania) Fiberforge 2000. “Esta máquina es actualmente uno de los sistemas de colocación de cinta más rápidos del mundo”, atestigua Sourkes. Está equipado con robots para cargar y recargar carretes de cinta, de modo que pueda funcionar sin interrupciones, minimizando el tiempo de contacto manual. Layup está diseñado para minimizar los espacios entre las cintas. Cada capa de la pieza en bruto adaptada al soporte B se inspecciona antes de colocar la siguiente capa. El proceso se realiza en un área ambientalmente controlada para minimizar el potencial de objetos extraños y escombros (FOD).
Los espacios en blanco hechos a medida se consolidan luego en una celda automatizada a medida que requiere una manipulación manual mínima para cargar y descargar los laminados. En la celda, los platos calentados combinados presionan y consolidan un panel, eliminando los huecos. Planchas frías emparejadas y luego enfriar el panel. Los dos juegos de platos, mantenidos a temperatura, son mucho más eficientes que una prensa estática con un solo juego de platos. "El resultado es un tiempo de ciclo drásticamente reducido medido en minutos frente a horas", dice Sourkes.
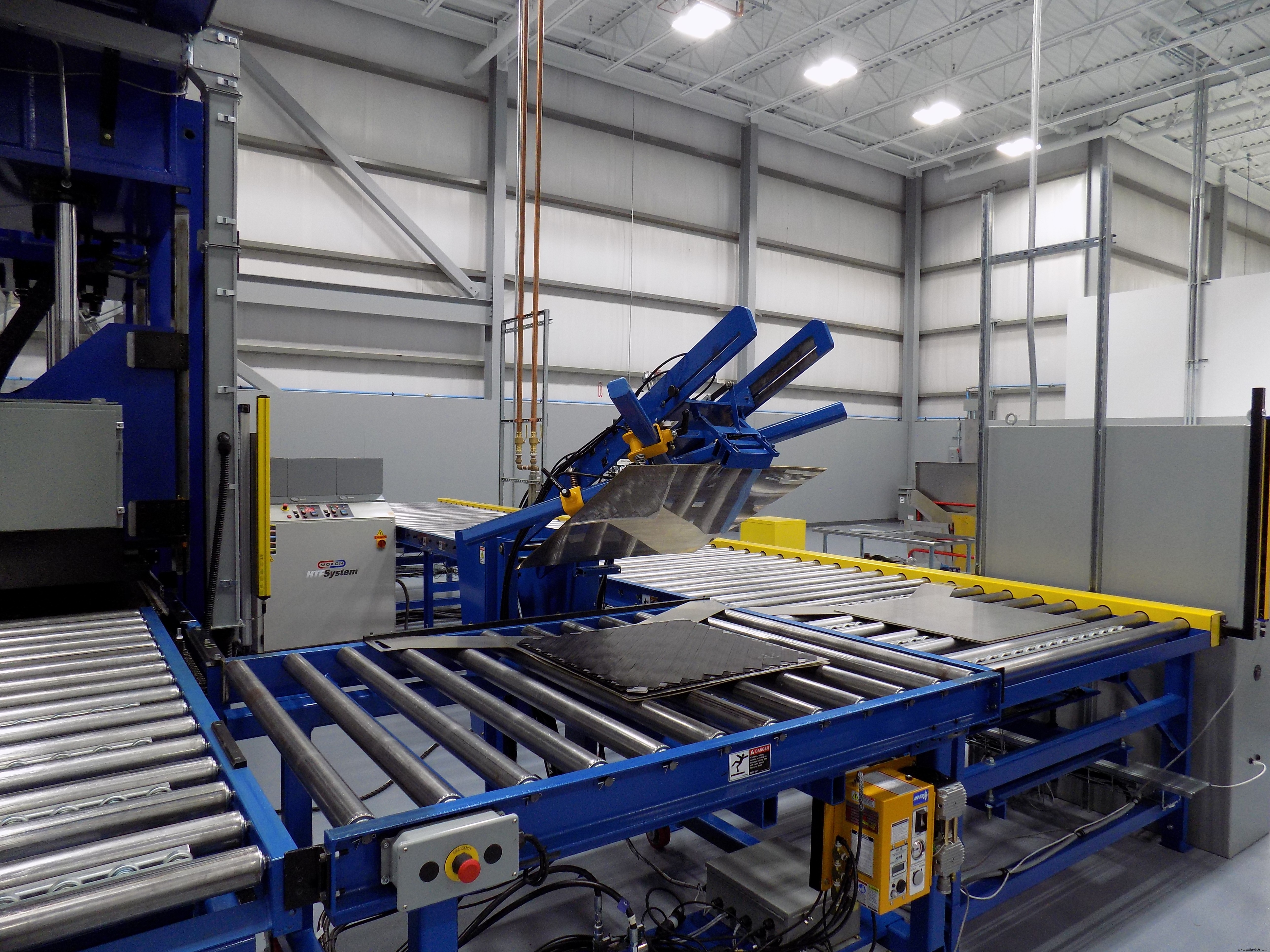
Paso 2. Los espacios en blanco personalizados se consolidan en una celda de consolidación automatizada a medida, que cuenta con dos juegos de platos que se mantienen a temperatura (uno caliente y otro frío) para acelerar este paso.
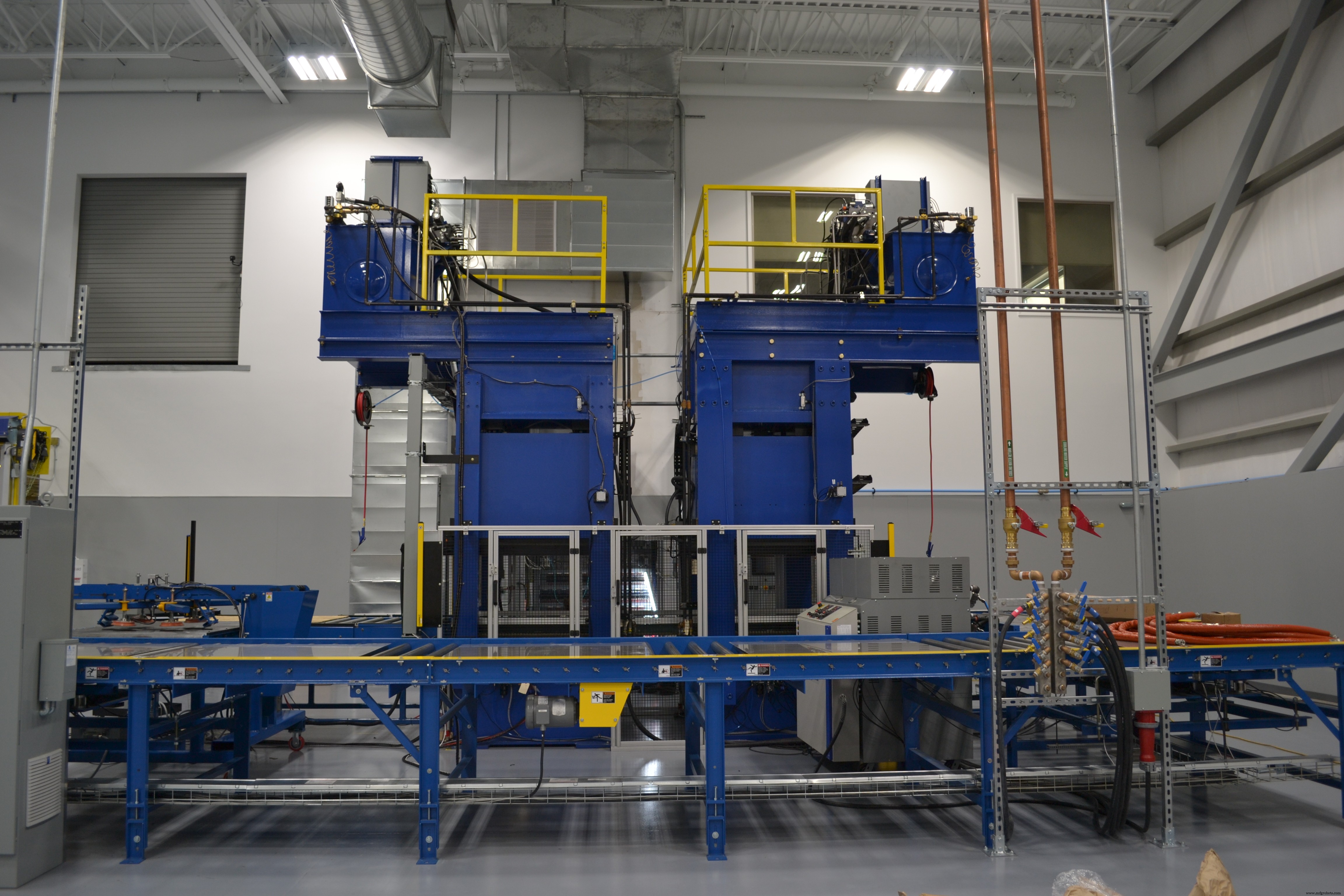
Las preformas laminadas consolidadas se procesan luego en una celda de trabajo patentada para formar la forma primaria del soporte (Paso 3). A continuación, se cortan las inserciones finales de fibra de carbono / PAEK de los espacios en blanco formados utilizando un cortador de chorro de agua Flow International (Kent, Washington, EE. UU.) (Paso 4)
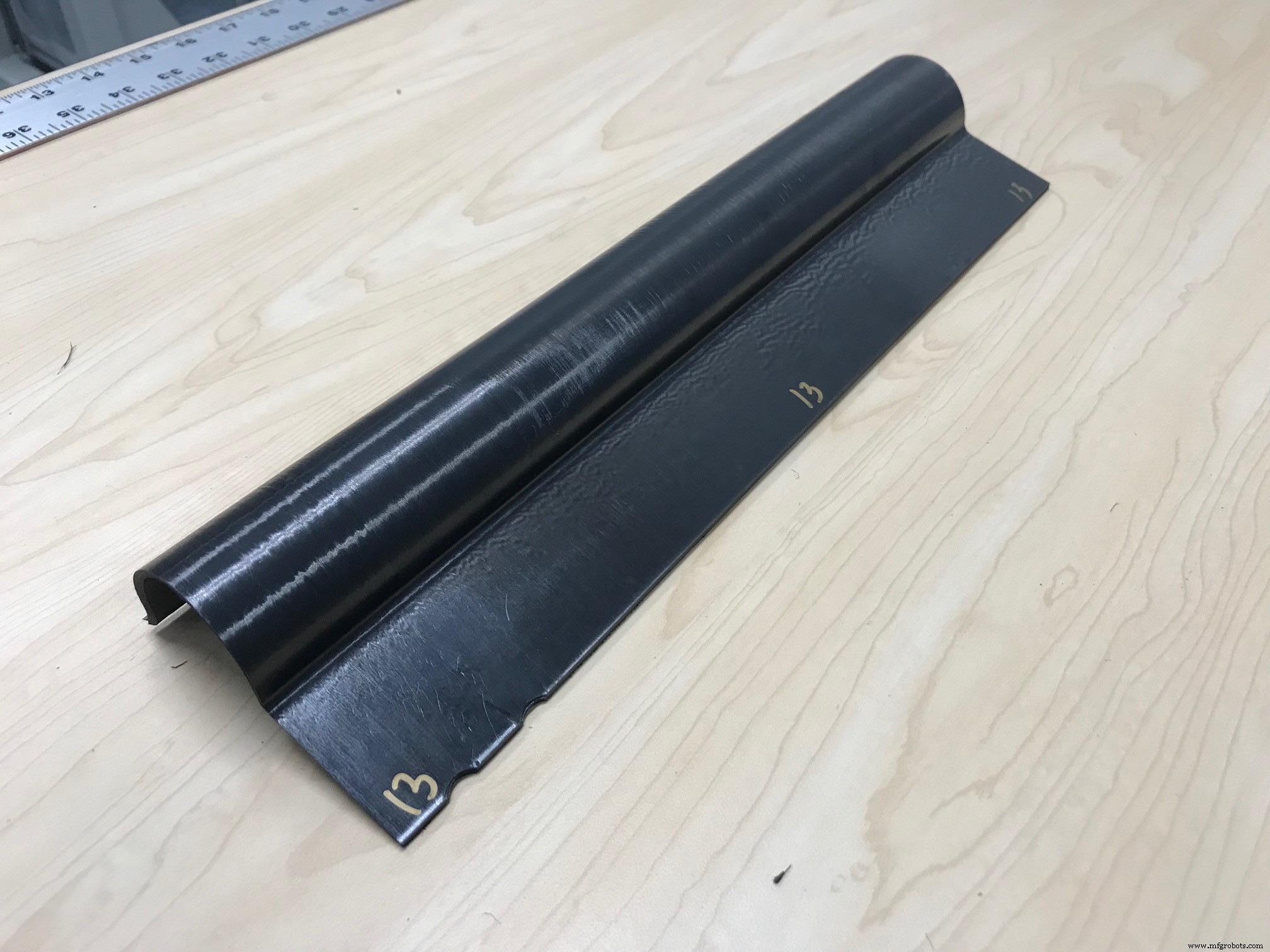
Paso 3. Una celda de trabajo patentada forma la forma principal del soporte.
Al determinar el tamaño del espacio en blanco adaptado, Sourkes señala que se debe deliberar una compensación para cada proyecto. “Podemos dimensionar el laminado de modo que podamos comprimir tres o cuatro rectángulos de un solo cuadrado en blanco. Al colocar un espacio en blanco tan grande como sea posible y luego cortarlo en preformas, maximiza la relación entre compra y vuelo; pero cortar las preformas significa más tiempo para las operaciones de corte con chorro de agua ". En el proyecto de soporte B, cada laminado consolidado se corta en múltiples preformas
A continuación, se realiza el paso de sobremoldeo, que se realiza con una máquina de moldeo por inyección de alta temperatura de Engel (Schwertberg, Austria) (paso 5). Los insertos se colocan en una cavidad de moldeo por inyección que luego se llena con PEEK fundido. Los insertos se colocan en una cavidad de moldeo por inyección que se llena con PEEK fundido, que derrite la capa superior de los laminados VICTREX AE 250 para crear un componente fuerte unido por fusión.
Cuando es necesario, un componente se termina mediante mecanizado hasta la forma neta. "Si bien nuestro objetivo es moldear piezas casi netas", admite Sourkes, "a menudo se requiere un nivel mínimo de mecanizado después del hecho para limpiar la geometría del proceso". El mecanizado se puede realizar con chorro de agua o mecanizado CNC.
Resultados revolucionarios
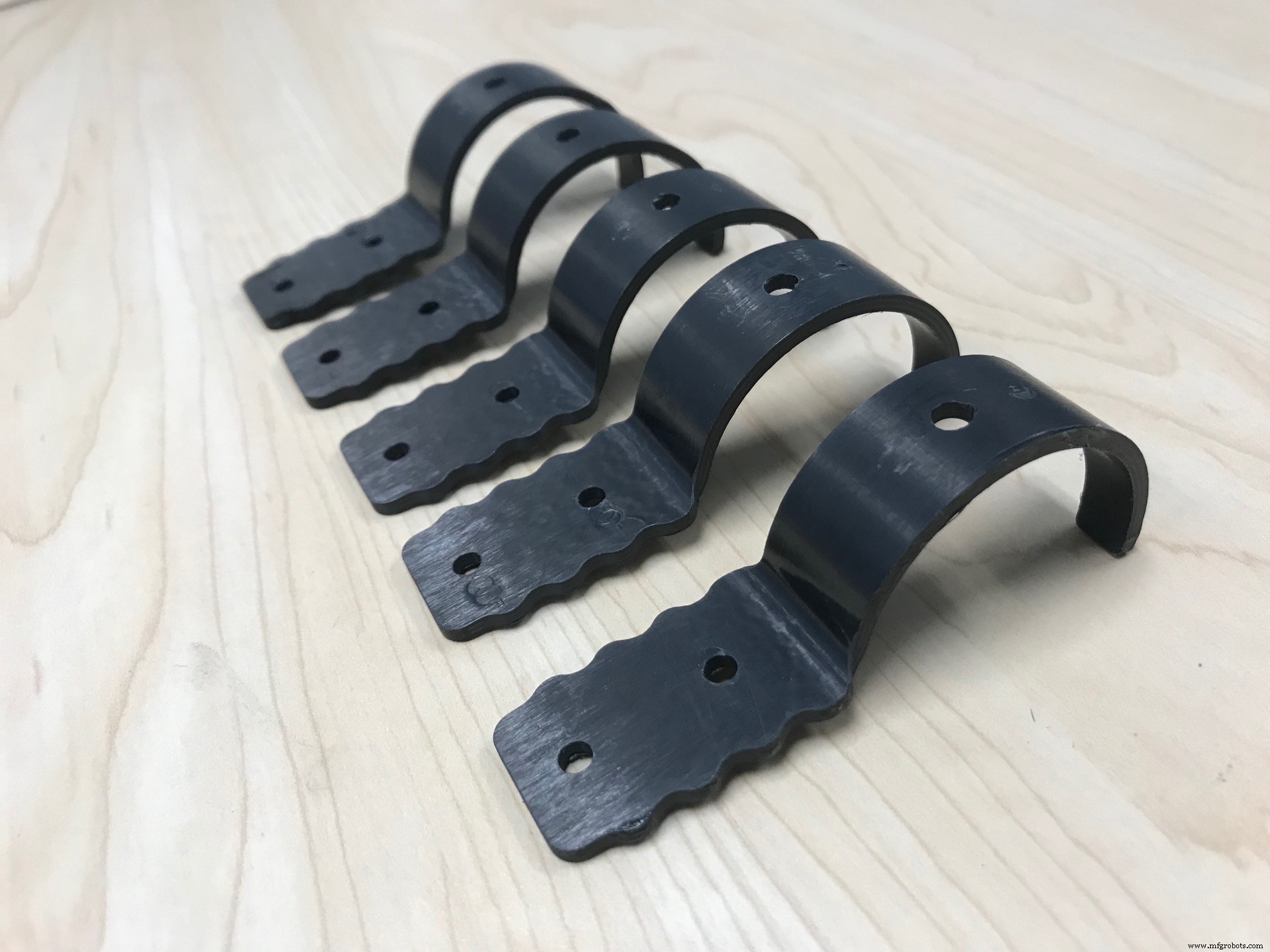
Paso 4. Una cortadora de chorro de agua de Flow International corta las inserciones de fibra de carbono / PAEK de los espacios en blanco formados. Se utilizan dos de estos insertos en cada soporte.
Al fabricar el soporte SFS intec, el proceso de sobremoldeo híbrido TxV logra tiempos de ciclo de tres minutos y una relación de compra-venta de 1.06:1. “Es el uso eficiente de los materiales y el proceso de fabricación rápido lo que nos permite producir piezas compuestas termoplásticas de valor agregado, y que hace posible la reducción de costos del sistema sobre los diseños de metal existentes”, enfatiza Sourkes. "Efectivamente, estamos reemplazando una materia prima de menor costo con una alta proporción de compra-venta y un tiempo de procesamiento significativo con una solución de material de alta ingeniería". El resultado es un ahorro de peso en el rango del 30 al 40% y un ahorro de costos en el rango del 20 al 30% en un reemplazo similar, es decir, una pieza de repuesto que sigue las mismas especificaciones geométricas y operativas que el componente existente. “El ahorro de peso en particular puede ser tan grande como el 60% cuando se nos brinda la oportunidad de rediseñar completamente un sistema de piezas”, señala.
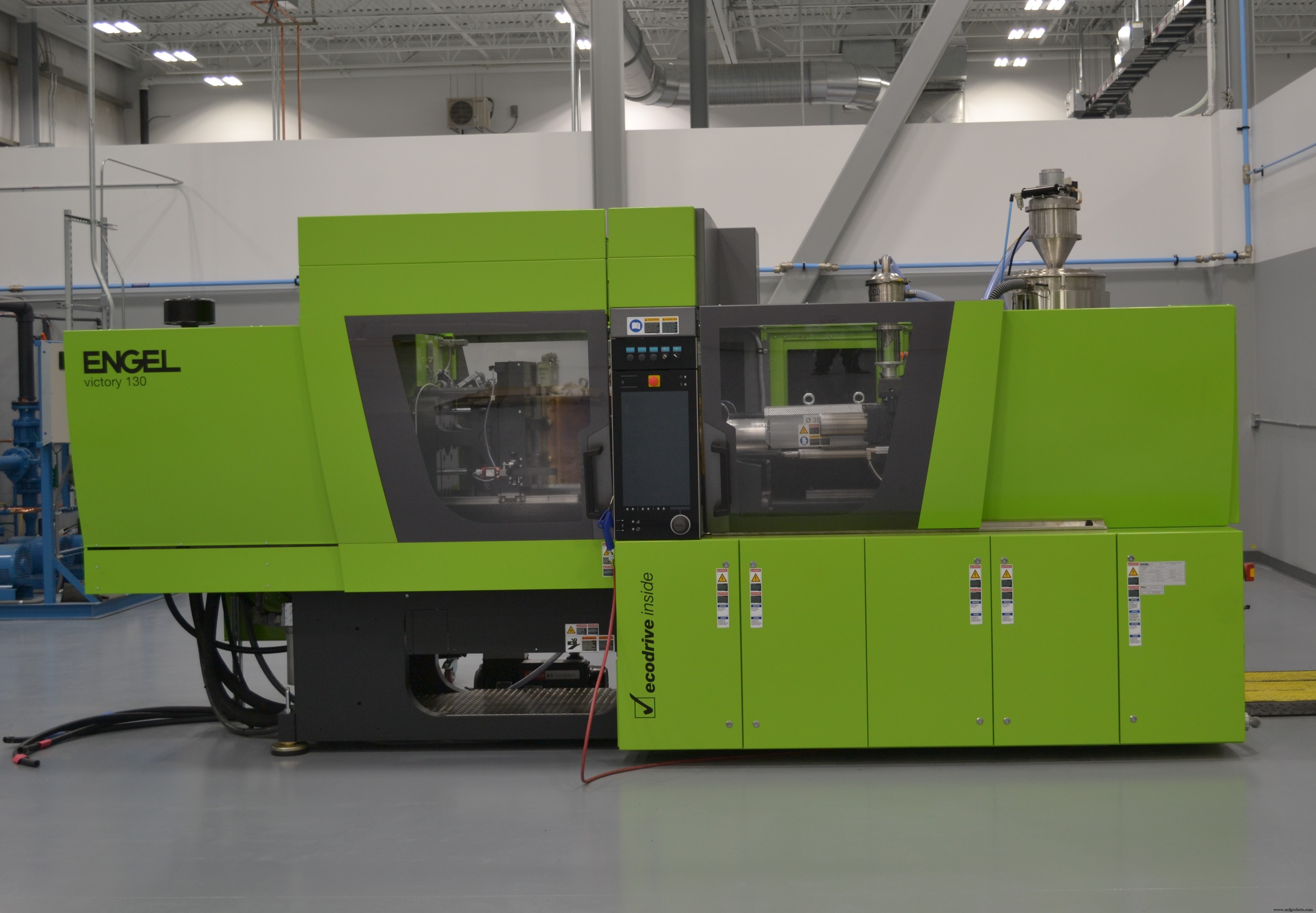
Paso 5. Una máquina de moldeo por inyección Engel optimizada para el sobremoldeo híbrido de PEEK completa la pieza compuesta sobremoldeando las inserciones.
El soporte de fibra de carbono / PAEK / PEEK también ha consolidado el recuento de piezas:TxV y SFS acordaron moldear por inyección una punta esparcidora en la parte inferior de la pieza en la misma operación utilizada para funcionalizar y agregar otras características. Anteriormente, la punta del esparcidor estaba hecha de PEEK y luego se mantenía en su lugar con dos remaches. Por tanto, la consolidación da como resultado tanto un recuento de piezas reducido como la eliminación de un paso de montaje.
Sin duda, la experiencia de las dos empresas que lanzaron TxV ha permitido el éxito del sobremoldeo híbrido. Sourkes explica que, después de desarrollar el material PAEK y la tecnología de procesamiento, Victrex primero exploró oportunidades con socios comerciales existentes. "Sin embargo, las empresas con experiencia en moldeo por inyección no tenían la experiencia para trabajar con compuestos continuos reforzados con fibra y viceversa". Victrex y Tri-Mack se asociaron durante varios años antes de formar TxV en 2017 y construir el centro de excelencia de compuestos de policetona especialmente diseñado para la empresa, que está altamente automatizado y diseñado para una producción en serie de alta tasa.
Cuando se le pidió que comparara el proceso y los resultados de TxV con un enfoque de fabricación convencional, Sourkes señala que el soporte B no es compatible con los enfoques de fabricación de compuestos estándar. “Esto sería un gran desafío sin mecanizar el soporte a partir de una palanquilla compuesta, lo que tendría un costo prohibitivo”, dice.
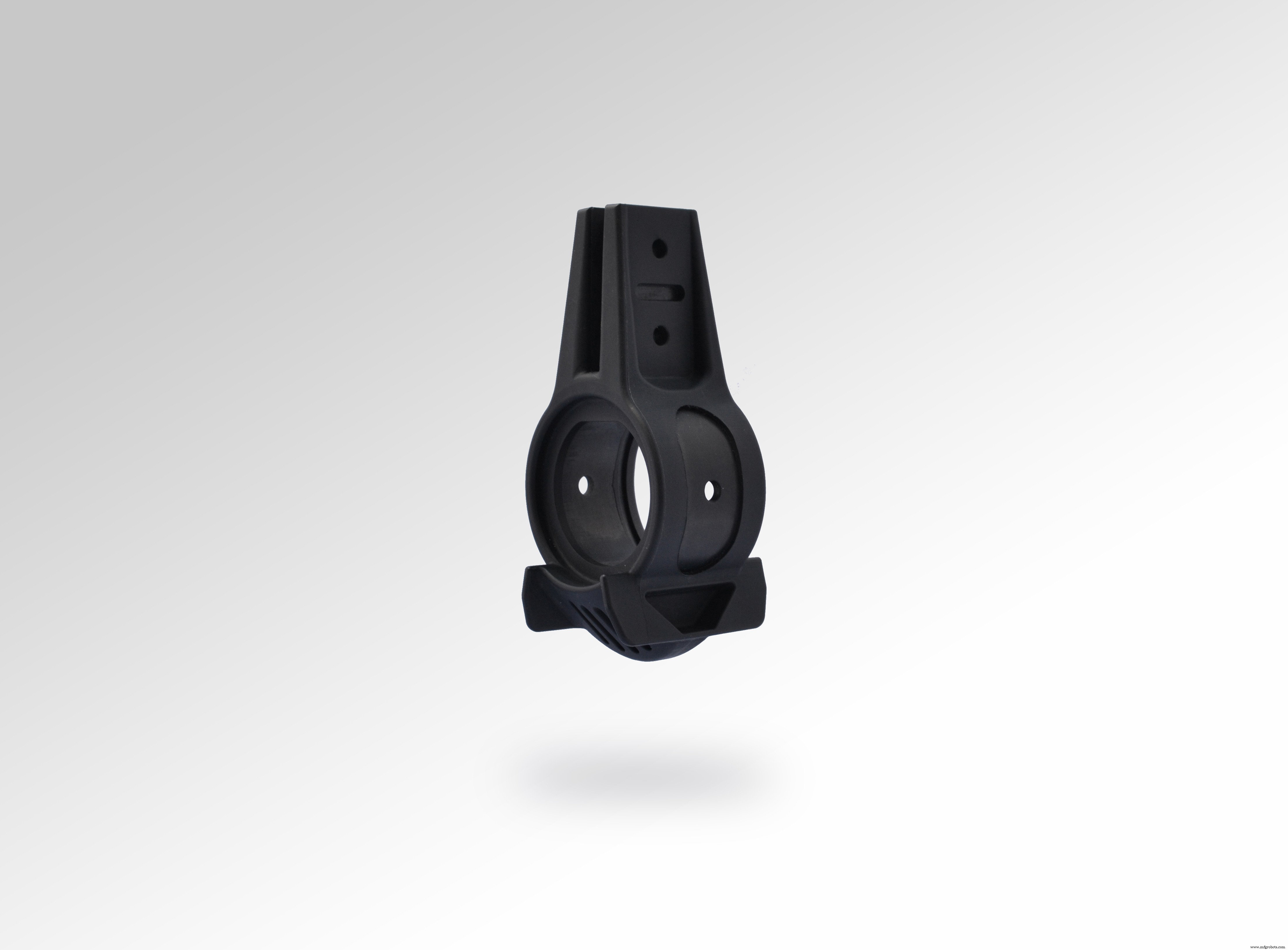
Paso 6. El soporte B final se produce con un tiempo de ciclo de tres minutos, una relación de compra a vuelo de 1.06:1 y un ahorro de peso del 30 al 40%.
Califica y luego vuela
Aprovechando la capacidad de SFS intec para ejecutar la calificación, las dos compañías han procedido con la certificación a través del "diseño de puntos", lo que significa que solo esta geometría de la pieza en particular obtiene la aprobación de vuelo. Las piezas fueron producidas y sujetas a las pruebas establecidas en el documento de calificación. “Dado que la pieza es un soporte para compartimentos superiores, las cargas operativas se logran con bastante facilidad”, señala Sourkes. "Sin embargo, los requisitos de rendimiento van más allá de las cargas típicas y deben cubrir algunas maniobras extremas de despegue y aterrizaje". Como CW va a la imprenta, el paquete de calificación ha sido enviado y está a la espera de la aprobación final del custodio de especificaciones. TxV y SFS intec esperan que la pieza esté volando a principios de 2020.
Una vez que el grupo B esté calificado, TxV escalará a los volúmenes de producción. Si bien la compañía está utilizando su línea de sobremoldeo híbrido existente para producir estos soportes, Sourkes enfatiza que la compañía tiene un mandato doble:fabricar piezas con la tecnología y apoyar a los fabricantes de la industria interesados en adoptar la tecnología ellos mismos. En otras palabras, los fabricantes de composites pueden adoptar esta técnica de fabricación en sus propias instalaciones.
Los soportes compuestos como el producto SFS intec tienen el potencial de hacerse cargo de un mercado bastante grande para este tipo de componentes. Los aviones comerciales utilizan miles de soportes y accesorios del sistema, lo que representa una contribución significativa al costo y al peso de la aeronave en general. “Estamos convencidos de que los componentes compuestos termoplásticos desempeñarán un papel cada vez más importante en la fabricación de aviones”, anticipa Costabel.
fibra
- MMF # 5:Guía para incrustar componentes en piezas impresas en 3D
- Una nueva y revolucionaria forma de fabricar piezas metálicas
- Presentamos nuestro nuevo material Markforged:Onyx
- AT&T y Tech Mahindra colaboran en una nueva plataforma de inteligencia artificial de código abierto
- LANXESS encarga dos nuevas líneas de producción para compuestos termoplásticos Tepex
- Aceleración de compuestos termoplásticos en la industria aeroespacial
- ¿Una nueva definición de compuestos?
- Nèos International establece una nueva sede, una instalación de materiales compuestos en el Reino Unido
- Cómo fabricar componentes mecánicos de precisión
- Comprender los componentes de alta precisión
- Acabado de piezas y componentes