¿Qué es la fundición en arena?
Cómo formar piezas fundidas complejas con moldes de arena
Fundición en arena es un proceso que utiliza moldes de arena no reutilizables para formar piezas fundidas de metal. Por un lado, la fundición es un proceso de fabricación engañosamente simple:cualquiera que haya formado castillos en la playa sabe que la arena se puede utilizar para hacer formas detalladas. Sin embargo, en una fundición, que trabaja con el calor del metal fundido, se deben considerar muchos factores para lograr el éxito. La fundición se utiliza para fabricar componentes metálicos de todos los tamaños, desde unas pocas onzas hasta varias toneladas. Se pueden formar moldes de arena para crear piezas fundidas con finos detalles exteriores, núcleos internos y otras formas. Casi cualquier aleación de metal se puede moldear en arena. Los huecos se hacen en arena humedecida, se rellenan con metal fundido y se dejan enfriar.
¿Qué es la arena de moldeo?
La arena para moldes tiene tres ventajas importantes sobre otros materiales para moldes:
- es barato,
- se recicla fácilmente y
- puede soportar temperaturas extremadamente altas.
La fundición en arena es uno de los pocos procesos disponibles para metales con altas temperaturas de fusión, como aceros, níquel y titanio. Debido a su flexibilidad, resistencia al calor y costo relativamente bajo, la fundición en arena es el proceso de fundición más utilizado.
Las piezas fundidas se producen vertiendo metal líquido en la cavidad de un molde. Para que una fundición tenga éxito, la cavidad del molde debe conservar su forma hasta que el metal se haya enfriado y solidificado por completo. La arena pura se rompe con facilidad, pero la arena para moldes contiene material adhesivo que aumenta su capacidad para resistir el calor y mantener la forma.
Arena verde (un agregado de arena, carbón pulverizado, arcilla de bentonita y agua) se ha utilizado tradicionalmente en la fundición en arena, sin embargo, los sistemas modernos de moldeo por unión química se están volviendo más populares. La arena de fundición más utilizada es la sílice (SiO2 ).
Propiedades de la arena de moldeo
Fuerza
La capacidad del molde de arena para mantener su forma geométrica bajo condiciones de tensión mecánica.
Permeabilidad
La capacidad de un molde de arena para permitir el escape de gases y vapor durante el proceso de fundición.
Contenido de humedad
El contenido de humedad afecta la resistencia y la permeabilidad de un molde:un molde con muy poca humedad puede romperse, mientras que un molde con demasiada humedad puede hacer que las burbujas de vapor queden atrapadas en la fundición.
Fluibilidad
La capacidad de la arena para llenar pequeñas cavidades en el patrón. La alta fluidez crea un molde más preciso y, por lo tanto, es útil para fundiciones detalladas.
Tamaño de grano
El tamaño de las partículas individuales de arena.
Forma de grano
Esta propiedad evalúa la forma de los granos de arena individuales en función de su redondez. En general, se utilizan tres categorías de granos en la arena de fundición:
- Grano redondeado Las arenas brindan una fuerza de unión relativamente baja, pero buena fluidez y acabado superficial.
- Granos angulares tienen mayor fuerza de unión debido al entrelazamiento, pero menor fluidez y permeabilidad que las arenas de grano redondeado.
- Granos subangulares son el camino del medio. Poseen mejor resistencia y menor permeabilidad en relación con los granos redondeados, pero menor resistencia y mejor permeabilidad que los granos angulares.
Colapsabilidad
La capacidad de la mezcla de arena para colapsar bajo la fuerza. Una mayor colapsabilidad del molde permite que la fundición de metal se encoja libremente a medida que se solidifica, sin el riesgo de que se rompa o agriete en caliente.
Fuerza refractaria
El molde no debe derretirse, quemarse o agrietarse cuando se vierte metal fundido en él. La resistencia refractaria mide la capacidad de la arena de moldeo para resistir el calor extremo.
Reutilización
La capacidad de la arena de moldeo para ser reutilizada (después del acondicionamiento de la arena) para producir otras piezas fundidas en arena en operaciones de fabricación posteriores.
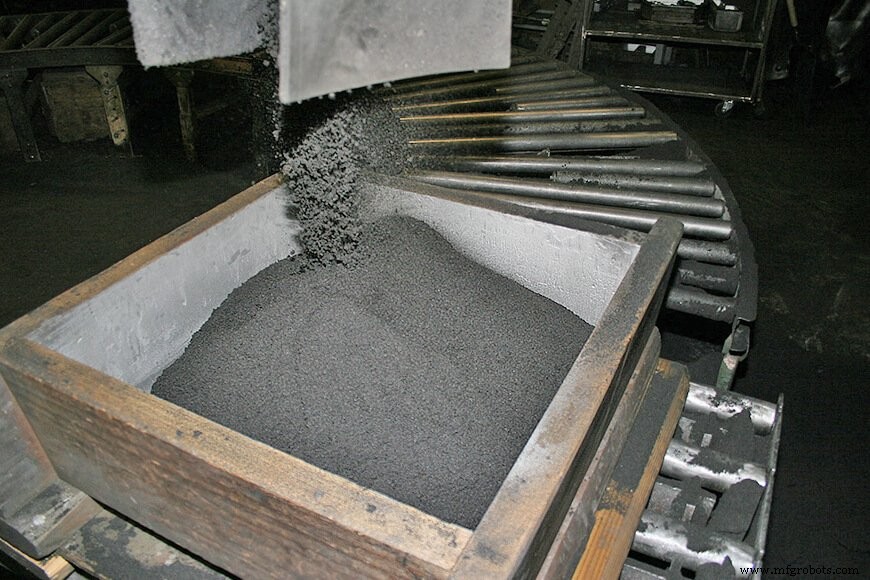
Muchas propiedades de la arena de moldeo dependen del tamaño del grano y la distribución de las partículas de arena:el tamaño de grano pequeño mejora la resistencia del molde, pero el tamaño de grano grande es más permeable. La arena de grano fino proporciona piezas fundidas con un buen acabado superficial, pero posee baja permeabilidad, mientras que la arena de grano grueso proporciona lo contrario.
Aditivos especiales o ligantes puede agregarse al agregado básico de arena, arcilla y agua para aumentar la cohesión. Estos aglutinantes pueden ser orgánicos o inorgánicos. Los aglutinantes comunes incluyen cereales, brea molida, carbón marino, gilsonita, aceite combustible, harina de madera, harina de sílice, óxido de hierro, perlita, melaza, dextrina y materiales patentados.
Encontrar la combinación perfecta no es fácil. Algunas propiedades de un agregado de arena son contradictorias entre sí:una arena de moldeo con mayor colapsabilidad tiene menos resistencia y una con mayor resistencia tiene menos colapsabilidad. A menudo se necesitan compensaciones para lograr un compromiso que proporcione las propiedades adecuadas para la pieza específica y la aplicación de fundición. El control preciso de las propiedades de la arena de moldeo es tan esencial que los laboratorios de arena se han convertido en una adición común a las fundiciones modernas.
Partes de un molde de fundición en arena
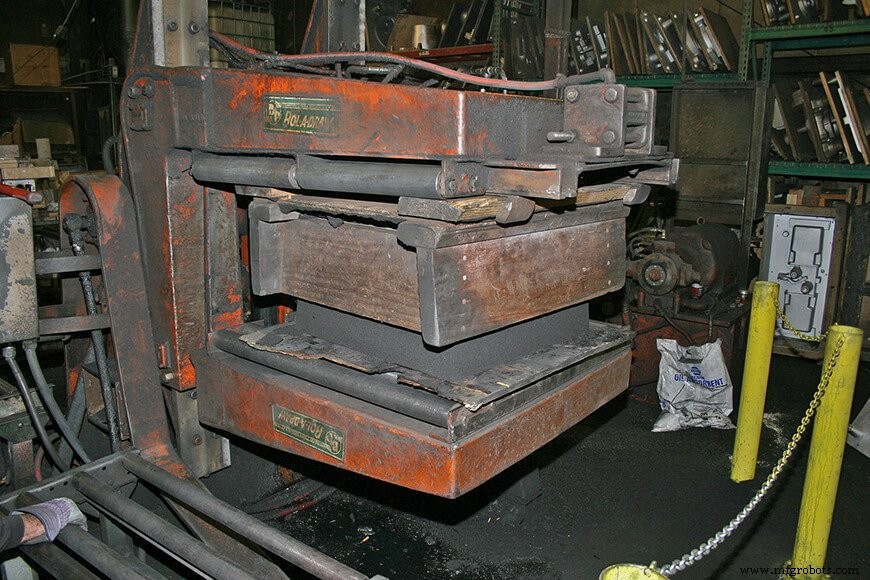
Una fundición de metal está formada por el molde utilizado para producirla:un buen molde es un requisito previo para una buena fundición. Los moldes tienen múltiples partes que trabajan juntas para influir en el producto final.
La cavidad del molde está formada por el patrón , un modelo a tamaño natural de la pieza que se imprime en el molde de arena. Algunas superficies internas no están incluidas en el patrón y, en su lugar, se crearán mediante núcleos separados.
Un núcleo es una forma de arena que se inserta en el molde para dar forma al interior de la fundición, incluidas características como orificios o pasajes. Los núcleos generalmente están hechos de arena de moldeo para que puedan ser sacudidos fuera de la fundición. Una impresión central es una región añadida al patrón, núcleo o molde para ubicar y sostener el núcleo dentro del molde.
Los chaplets proporcionan más apoyo básico – pequeñas piezas de metal que se sujetan entre el núcleo y la superficie de la cavidad. Para mantener ese soporte, las coronas deben estar compuestas de un metal con una temperatura de fusión igual o superior a la del metal que se está colando. Después de la solidificación, las coronas se habrán encajado dentro del yeso.
Los machos de arena se pueden producir utilizando muchos de los mismos métodos que los moldes de arena:así como los moldes se forman según un patrón, los machos de arena se forman con una caja de machos; son similares a un dado y pueden estar hechos de madera, plástico o metal. Las cajas de núcleos también pueden contener múltiples cavidades para producir varios núcleos idénticos.
Un ascensor es un vacío adicional dentro del molde diseñado para contener el exceso de metal. Evita que se formen vacíos de contracción en la fundición principal al alimentar metal fundido a la cavidad del molde a medida que se solidifica y se contrae.
Todo el molde de arena está contenido en una caja llamada frasco . En un molde de dos partes, que es típico de las fundiciones en arena, la mitad superior (que contiene la mitad superior del patrón, la mufla y el núcleo) se denomina copa . La mitad inferior se llama arrastrar . La línea de separación es la línea o superficie que separa la capa y el arrastre.
Cómo hacer un molde de arena
La fundición en arena consta de cuatro pasos básicos:ensamblar el molde de arena, verter metal líquido en el molde, dejar que el metal se enfríe, luego romper la arena y retirar la fundición. Por supuesto, el proceso es más complejo de lo que parece.
El primer paso del ensamblaje del molde es llenar parcialmente el arrastre con arena. El patrón, la impresión del núcleo, los núcleos y el sistema de entrada se colocan cerca de la línea de partición. Luego, la capa se ensambla al arrastre. Se vierte arena adicional sobre la mitad de la cubierta hasta cubrir el patrón, el núcleo y el sistema de entrada, y luego la arena se compacta mediante vibración o medios mecánicos. El exceso de arena se elimina con una barra niveladora.
Ahora que se ha formado el molde, se retira la capa superior del arrastre para poder extraer el patrón del molde.
La extracción del patrón se lleva a cabo con cuidado para evitar romper o deformar la cavidad del molde recién formada. Esto se facilita diseñando un borrador :una conicidad vertical perpendicular a la línea de separación. La conicidad de tiro suele ser de al menos 1°. Cuanto más rugosa sea la superficie del patrón, mayor será el borrador que se proporcionará.
Antes de que pueda llenarse con metal líquido, se debe preparar el molde completo; la cavidad del molde a menudo se lubrica con lavados de molde para facilitar la extracción de la fundición. Luego, se colocan los núcleos, se agregan materiales de molde adicionales, como cuerdas de superposición, para ayudar a evitar que se escapen, y las mitades del molde se cierran y sujetan con abrazaderas de manera segura; las secciones superior y de arrastre mantienen la alineación adecuada con la ayuda de pasadores y guías.
Las mitades del molde deben permanecer seguras para que el metal líquido no se filtre a través de la línea de separación. Antes de verter moldes sin matraz, verter camisas de madera o metal a menudo se colocan alrededor del molde y se colocan pesos en la parte superior para evitar que la capa se levante.
El metal fundido ingresa a la cavidad del molde a través de un sistema de compuertas :el metal fundido se vierte en un molde a través de la taza de vertido , continúa por el bebedero (la parte vertical del sistema de compuertas), y luego a través de los corredores (partes horizontales). Los gases acumulados y el aire desplazado escapan a través de respiraderos . Los múltiples puntos donde el metal se introduce en la cavidad del molde desde los corredores se denominan compuertas. .
Una vez que la fundición se ha enfriado, se desmolda del molde de arena. El proceso de eliminación de arena de las piezas fundidas se llama sacudida . El yeso se puede quitar manualmente o con maquinaria automatizada. Las mesas de agitación y los volteadores giratorios son de uso común.
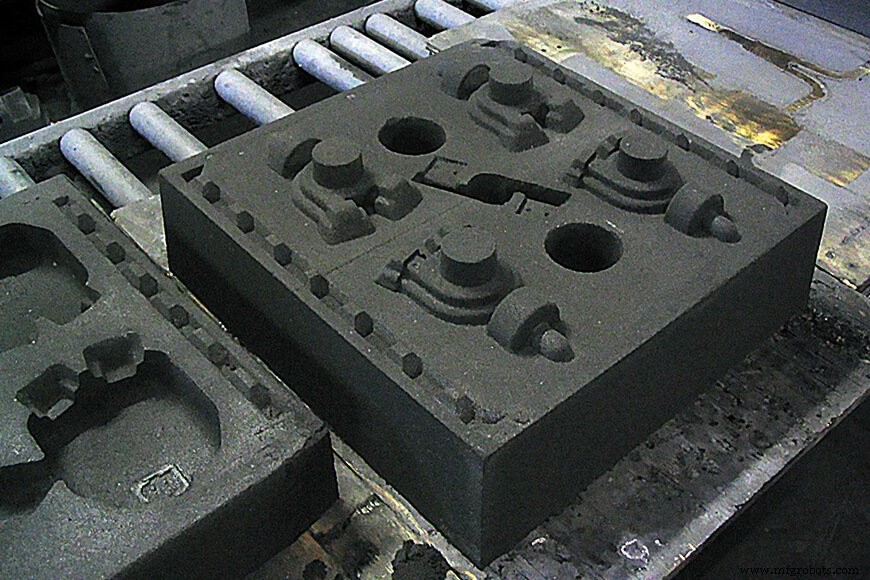
Existen variaciones en este proceso básico según el patrón, el tipo de matraz y el nivel de mecanización:
- Moldura de banco se prefiere para trabajos pequeños. Toda la operación se lleva a cabo en un banco de altura conveniente.
- Moldura de suelo se utiliza para trabajos medianos y grandes. Como sugiere el nombre, el molde se coloca en el suelo antes de verterlo.
- Moldeado a máquina se emplea para la producción en masa. El moldeado a máquina ahorra mano de obra y ofrece una precisión y uniformidad superiores, lo que permite mantener las tolerancias dentro de límites estrechos a un ritmo rápido. Las operaciones primarias realizadas por las máquinas de moldeo son embestir la arena de moldeo, rodar sobre el molde, formar la puerta, golpear el patrón y retirarlo.
Reciclaje de arena de moldeo
Una vez que se ha sacudido la arena de una fundición completa, los grumos se enfrían y se trituran. Todas las partículas y gránulos de metal se eliminan, a menudo con la ayuda de un campo magnético. Toda la arena y los componentes se tamizan con sacudidores, zarandas rotatorias o zarandas vibratorias. La arena limpia se puede volver a introducir al comienzo del ciclo de producción de arena de moldeo.
Las arenas de moldeo se preparan en mullers, que mezclan la arena, el agente aglutinante y el agua. Los aireadores se usan en conjunto para aflojar la arena y hacerla más susceptible al moldeado.
La arena preparada se entrega al piso de moldeo, generalmente mediante camiones con cuchara o mediante cintas transportadoras, donde se forma en moldes; los moldes pueden colocarse en el suelo o transportarse mediante cintas transportadoras a una estación de vertido. Después del vertido, las piezas fundidas se retiran de la arena adherida en una estación de desmoldeo. La arena usada, a su vez, se devuelve a los contenedores de almacenamiento mediante una cinta transportadora u otros medios.
La arena de fundición normalmente se recicla y reutiliza a través de muchos ciclos de producción. Según estimaciones de la industria, anualmente se utilizan aproximadamente 100 millones de toneladas de arena en la producción. De ese número, solo se desechan de cuatro a siete millones de toneladas, e incluso esa arena suele ser reciclada por otras industrias.
Procesos y métodos de moldeo en arena
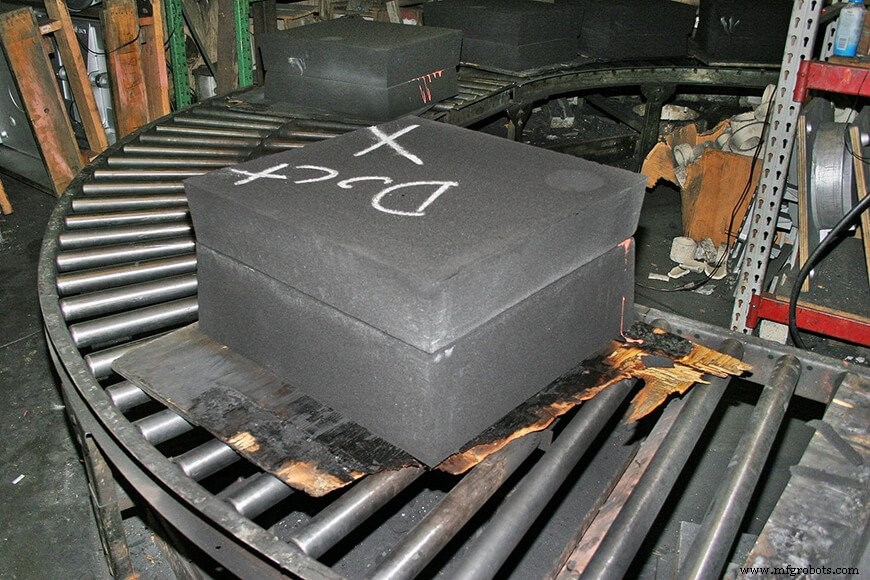
Moldes de arena verde
Una mezcla típica de arena verde contiene 89 por ciento de arena, 4 por ciento de agua y 7 por ciento de arcilla. La arena verde es una de las favoritas de la industria debido a su bajo costo y sólido rendimiento general. El "verde" en arena verde se refiere al contenido de humedad presente en la mezcla durante el vertido.
Los moldes de arena verde tienen la fuerza suficiente para la mayoría de las aplicaciones de fundición en arena. También proporcionan buena colapsabilidad, permeabilidad y reutilización. Las principales dificultades surgen del contenido de humedad. Demasiada humedad puede causar defectos en la fundición, y la tolerancia a la humedad depende del metal fundido.
Procesos de fraguado en frío
A veces se utilizan aglutinantes no tradicionales en la fundición industrial en arena. Los aglutinantes de fundición convencionales requieren calor para curar, mientras que estos aglutinantes alternativos se unen químicamente a temperatura ambiente cuando se mezclan con arena, de ahí el término procesos de fraguado en frío. Técnicamente avanzados, estos procesos de fundición en arena relativamente recientes están ganando popularidad. Los procesos de fraguado en frío son más costosos que los moldes de arena verde, pero producen piezas fundidas con una precisión dimensional excepcional.
Moldeo de cáscara
La fundición en molde de carcasa es una invención relativamente reciente en las técnicas de moldeo para la producción en masa y el acabado liso; Fue utilizado por primera vez por Alemania durante la Segunda Guerra Mundial. El material de moldeo es una mezcla de arena de sílice fina y seca con un contenido mínimo de arcilla y un 3-8 por ciento de resina termoendurecible (fenol formaldehído o grasa de silicona). Cuando la mezcla de moldeo cae sobre la placa modelo calentada, se forma una capa dura de unos 6 mm de espesor. Para curar completamente el caparazón, debe calentarse de 440 a 650 °F (230 a 350 t) durante varios minutos.
Servicios de transmisión personalizados
Reliance Foundry trabaja en colaboración con los clientes para diseñar el patrón y el método de moldeo para cada fundición personalizada. Solicite un presupuesto para obtener más información sobre cómo nuestro servicio de casting puede satisfacer los requisitos de su proyecto.
Artículos relacionados
- Guía de casting en profundidad:La vida de una serie de casting
- Sociedad Americana de Fundición. “Procesos de moldeo en arena”.
Créditos de imagen
- Relleno de la caja del molde:OKFoundry, CC BY 2.0, a través de Flickr
- Copa extraída de la caja del molde:OKFoundry, CC BY 2.0, a través de Flickr
- Abrir molde de arena:OKFoundry, CC BY 2.0, a través de Flickr
- Molde cerrado:OKFoundry, CC BY 2.0, a través de Flickr
Proceso de manufactura
- ¿Qué es la fundición en molde no fungible?
- ¿Qué es la arena afilada?
- ¿Qué es una pantalla de arena?
- Arena verde frente a fundición en arena con resina
- Fundición en arena frente a forja
- ¿Qué es la fundición en arena?
- Tipos de equipos de fundición en arena
- Introducción a la terminología de fundición en arena
- ¿Qué es la fundición CI?
- ¿Qué es la arena de moldeo?
- ¿Qué es una máquina de fundición a presión?