Moldes de fundición a presión:una guía detallada de herramientas de moldes de fundición a presión
La fundición a presión es un proceso importante para aplicaciones en diversas industrias. Un componente esencial del proceso de fundición a presión es el molde de fundición a presión. La forma y las características del molde afectan a las prestaciones del producto final.
Por lo tanto, es necesario comprender el diseño del molde de fundición a presión. Esto le ayudará a diseñar y elegir el molde adecuado para sus proyectos de fundición a presión. Además, puede estar seguro de que el producto final cumplirá con los requisitos de fabricación únicos.
Por lo tanto, este artículo le brindará una descripción detallada de los diferentes tipos de herramientas de fundición a presión. También aprenderá a diseñar un molde y los factores que debe tener en cuenta al fabricar herramientas de fundición a presión.
¿Por qué es importante el molde para la fundición a presión?
El diseño del molde de fundición a presión juega un papel vital en la forma de la pieza. Además, afecta la calidad, uniformidad y configuración de los componentes del proceso de fundición a presión .
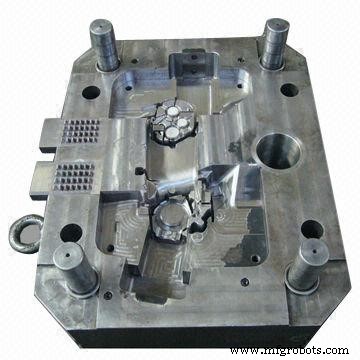
Las especificaciones incorrectas pueden provocar la corrosión del material o de la herramienta. Sin embargo, un diseño de molde adecuado puede aumentar el tiempo y la eficiencia del producto. En última instancia, la calidad de la estructura del molde determinará si la producción se desarrollará sin problemas y si las piezas fundidas serán de la mejor calidad.
Además, el diseño de la herramienta de fundición a presión refleja esencialmente los diferentes factores que pueden ocurrir durante la producción. Por lo tanto, debe analizar la estructura de una fundición durante el diseño. También es esencial dominar las condiciones de archivo, implementar parámetros de proceso críticos y considerar otros efectos económicos. Esto asegurará que las herramientas de fundición a presión puedan cumplir con los requisitos de producción esenciales.
Molde de fundición a presión Componentes
La comprensión del molde de fundición a presión comienza con el conocimiento de la estructura del molde. Los componentes esenciales del molde de fundición a presión incluyen:
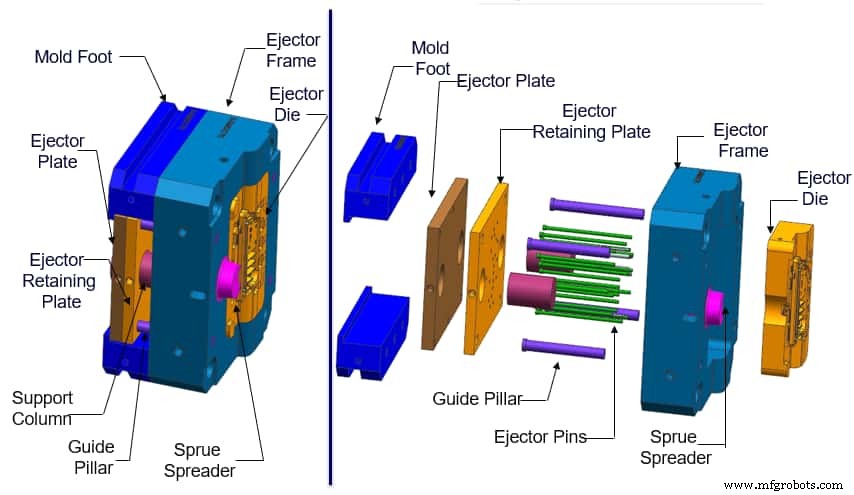
· Sistema de Moldeo
Esto incluye la cavidad, el núcleo, los insertos, los deslizadores y los pines de inserción. La cavidad de fundición a presión determina la forma de fundición a medida que se cierra el núcleo móvil.
· Sistema de base de molde
Los componentes principales del sistema de base de molde de fundición a presión son placas y marcos de acero. Este sistema combina diferentes partes del molde y permite la instalación del molde en la máquina de fundición a presión.
· Sistema de expulsión
Este sistema funciona para expulsar piezas del molde. Estas piezas incluyen piezas de expulsión, retorno y guía.
· Sistema de corredores
El sistema de corredores se conecta con la pieza de fundición a presión y la cámara de presión. Por lo tanto, guía el material metálico hacia la cavidad del troquel en una dirección específica. Este sistema afecta directamente la presión y la velocidad del metal fundido. Los componentes del sistema de correderas son una corredera, un bebedero, una puerta interior, etc.
· Sistema de desbordamiento
Este canal elimina el aire de la cámara de presión. En general, los componentes principales son las ranuras de desbordamiento y las ranuras de ventilación. Sin embargo, los fabricantes instalan tapones de ventilación en las cavidades profundas para mejorar las condiciones de ventilación.
· Otros
Otros componentes del molde de fundición a presión incluyen piezas de posicionamiento para colocar las piezas correctamente en el molde. Además, hay pasadores y pernos para fines de sujeción.
Tipos de moldes de fundición a presión
Hay varios tipos de herramientas de fundición a presión, y tienen diferentes funciones según los requisitos. Incluyen:
Matrices de prototipos
Una inversión importante en la fundición a presión es un troquel hecho a medida con todas las funciones. Por lo tanto, un troquel prototipo ayuda a hacer una gran cantidad de moldes para probar las diferentes partes. Las estrategias de creación de prototipos son la fundición por gravedad, las piezas mecanizadas y las piezas impresas en 3D. Sin embargo, implican compensaciones en cuanto a propiedades, tolerancia y diseño.
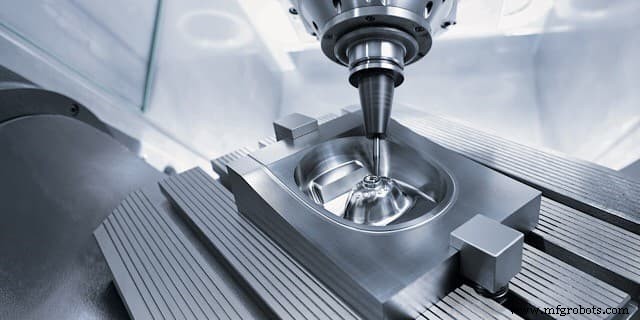
Un prototipo de fundición a presión a alta presión será su mejor opción siempre que necesite la misma aleación, propiedades, proceso y geometría para la producción. Los troqueles de creación de prototipos pueden utilizar aceros para herramientas preendurecidos y sin recubrimiento y componentes estandarizados. Como resultado, se pueden producir en tiempos cortos y a un costo reducido.
A diferencia de otras técnicas de producción, estos moldes también utilizan técnicas de eyección o enfriamiento menos eficientes. Por lo tanto, debe tener en cuenta que la herramienta no durará mucho y el troquel no será tan eficiente como una producción. Sin embargo, esto no será un problema si solo necesita una pequeña cantidad de yeso.
Troqueles de herramientas rápidas
El herramental rápido se refiere a insertos y troqueles producidos utilizando métodos con plazos de entrega más cortos que los métodos convencionales. A diferencia del mecanizado de desbaste y el tratamiento térmico, los métodos de herramientas rápidas son la sinterización selectiva por láser, la deposición directa de metal, la conformación de redes con ingeniería láser, etc.
Por lo tanto, esperaría que la creación de estos troqueles de herramientas de fundición a presión fuera mucho más rápida. Los fabricantes pueden usar estos troqueles como troqueles de creación de prototipos o como troqueles de producción. La elección más viable dependerá de los requisitos de volumen de producción.
Muere la producción
Estos troqueles son los tipos más comunes de troqueles de fundición a presión. Los troqueles de producción son esenciales cuando se ha finalizado todo el diseño y está listo para lanzar un producto auténtico.
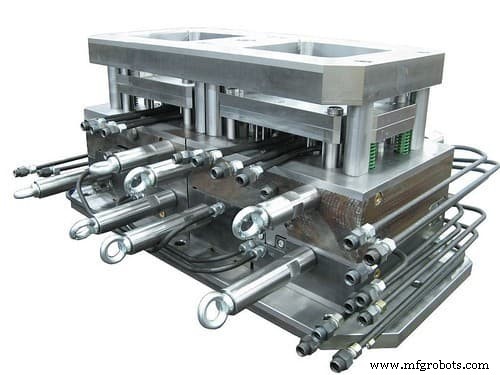
Podemos tener:
- Troqueles de una sola cavidad sin portaobjetos
- Troqueles de múltiples cavidades con varias opciones de deslizamiento
El material de la cavidad es acero de alta calidad y, a menudo, se retiene en un bloque de soporte. El diseño de los troqueles de producción garantiza que tengan dimensiones críticas. Por lo tanto, puede estar seguro de que permiten las especificaciones de mecanizado requeridas.
Muere la unidad
El troquel unitario es un tipo especial de molde de fundición a presión. Un soporte de la unidad de fundición a presión mantiene intacta la matriz de la unidad o la cavidad propiedad del cliente dentro de la cavidad. Podemos tener partícipes simples o dobles. Los ejemplos típicos de tamaños de bloques de cavidad que sostienen los troqueles son 8 x 10, 10 x 12, 12 x 15 y 15 x 18 (todos en pulgadas).
Los troqueles unitarios emplean piezas genéricas utilizadas para componentes menos complejos y de bajo volumen. Un troquel personalizado es más efectivo para piezas de mayor volumen con geometría compleja. Estos troqueles están diseñados específicamente para una pieza, lo que proporciona el máximo control y eficiencia.
Troqueles de corte
CMW utiliza troqueles de recorte para la producción de alto volumen y los troqueles de producción. El troquel de recorte recorta el flash, el corredor y el desbordamiento de la pieza inmediatamente después de que se completa la colada. Algunos troqueles de recorte necesitan movimientos o levas accionados hidráulicamente, mientras que otros requieren funciones de apertura y cierre para eliminar el flash de manera efectiva.
La geometría de la pieza impide la posibilidad de eliminar totalmente el rebaba con un troquel de recorte. Por lo tanto, las estrategias de desbarbado manual y el servicio de recorte personalizado son una opción ideal en esta situación.
¿Necesita piezas de aspecto moderno con mejor resistencia y mayor durabilidad? Elija el proceso de fundición a presión que requiera herramientas para producir sus piezas de uso final. Y la buena noticia es que los servicios de fundición a presión de RapidDirect le brindan una solución integral.
Proceso de diseño de moldes para fundición a presión
Esta sección describirá el proceso involucrado en el diseño de un molde para proyectos de fundición a presión a alta presión. El proceso tiene cinco categorías amplias:
Fase Preliminar
Antes de diseñar el molde, es importante comprobar la capacidad de fabricación de la pieza con la tecnología de fundición a presión. Esta fase consiste en juzgar la viabilidad del producto desde un punto de vista geométrico y dimensional.
Vista dimensional :Es necesario conocer la dimensión de la pieza y el número de cavidades requeridas para cada fundición. Esto ayudará a conocer la fuerza de apertura y el volumen del colado. El conocimiento de estos datos facilitará mucho los estudios de viabilidad.
Vista geométrica :La geometría de las piezas incluye el dibujo de la línea de separación. La línea divisoria divide el molde de fundición a presión en dos, lo que permite una fácil apertura del molde y la expulsión de la fundición. Además, la superficie de las piezas depende de su posición respecto a las líneas de separación. En consecuencia, las superficies deben diseñarse en la dirección de apertura del molde.
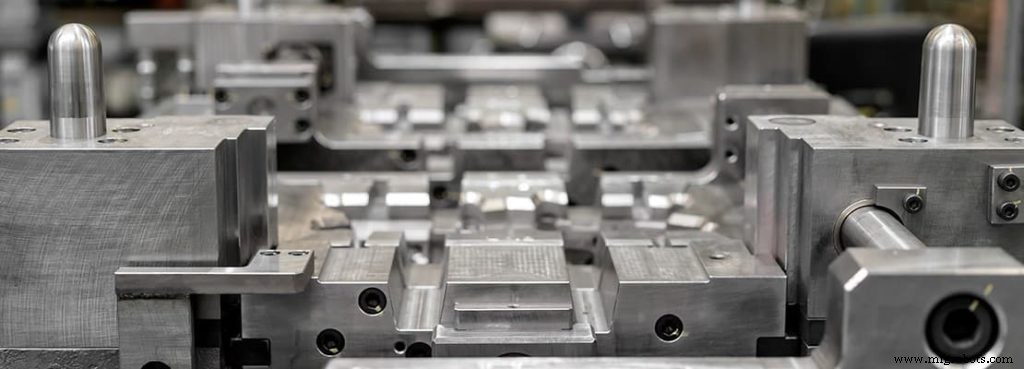
La tolerancia geométrica de las comillas que se encuentran en el modelo 2D puede ser bastante difícil de producir debido a la contracción causada por el enfriamiento del metal. Cuanto mayor sea el número de cotizaciones, más difícil será obtener el mismo valor en el casting. Por lo tanto, puede continuar con el diseño del molde de fundición a presión tan pronto como confirme la capacidad de fabricación de la pieza.
Número de cavidades
Para conocer el número de cavidades, debe considerar el número de piezas a producir, la orientación de la cavidad y el tiempo hipotético del ciclo. De esta manera, puede decidir la mejor opción entre un molde de varias cavidades o uno de una sola cavidad.
Cuando opte por un molde de múltiples cavidades, recuerde que además del hecho de que aumentan las fases de expulsión y la complejidad del llenado, el proceso de producción puede verse afectado por la dimensión de la cavidad y la disposición del producto.
Área de proyección
El área de proyección es la superficie obtenida de la proyección de cavidades sobre la planta. Es perpendicular a la dirección de la apertura del molde. El área de proyección es un componente vital de la fase de diseño. Relaciona la fuerza de apertura del metal fundido con las paredes del troquel. Como resultado, la intensidad de la fuerza dependerá de la orientación de la dimensión de la forma. Una fuerza fuerte provocará un desbordamiento de material, lo que resultará en la formación de rebabas.
Por lo tanto, debe estimar las fuerzas producidas por el metal fundido para evitar este defecto de fundición. La fuerza es el producto de la presión específica de la máquina, el área de proyección y los factores de seguridad preestablecidos. El factor ofrece un margen más amplio para ayudar a contrarrestar la presión máxima después del llenado. Mucha gente se refiere a él como un golpe de ariete.
La máquina transfiere la fuerza dinámica y estática al final del proceso. Así, se produce un pico de presión que debe absorber la fuerza de la máquina de cierre. Esta fuerza de cierre depende de la dimensión de la carrera y del modelo de prensa.
Volumen y forma del troquel
El volumen y la forma del troquel son esenciales para el diseño del molde. Además del volumen deseado, tenga en cuenta que las piezas grandes se encogerán debido a un mayor tiempo de enfriamiento, aumentando la tasa de contracción. Por lo tanto, existe la necesidad de dimensionar las cavidades del molde en consecuencia.
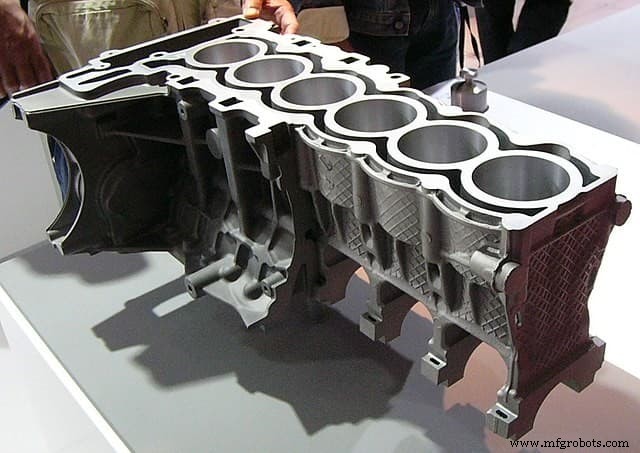
Además, es recomendable considerar diferentes variables que afectan el tamaño final del molde. Los factores más importantes a considerar son:
Canales de inyección :El tamaño de los canales de inyección varía con el número de cavidades y la posición de las compuertas y piezas. La forma de los canales de inyección debe cumplir algunos requisitos de dinámica de fluidos. Por ejemplo, los fabricantes reducen la sección para adherirse correctamente a la pared del molde cuando se mueve en la dirección del metal fundido. Debido a la contracción, hay un flujo acelerado y se desprenden de las paredes. Una capa externa más suave evitará turbulencias, atrapamientos de aire y otros defectos.
Tipo de cierre de troquel :El cierre de molde abierto/cerrado es el cierre de troquel más simple. Es mejor para productos con formas limpias y simples que se pueden expulsar fácilmente. Sin embargo, no es la mejor opción para piezas con geometría compleja. Los productos con geometría compleja serían difíciles de eliminar, por lo que el fabricante debe aumentar el tamaño total del troquel.
Presencia de desbordamientos :Los desbordamientos son pequeños pozos diseñados en partes estratégicas del molde de fundición a presión. Son importantes en la recogida de los primeros tiros de metal porque suele hacer más frío que los siguientes. Como resultado, puede evitar vueltas frías y otros defectos estéticos similares. Además, los desbordamientos sirven como fuente de calor, lo que aumenta la temperatura del troquel en áreas críticas para la fundición final.
Simulación mediante modos semiempíricos
Una vez completada la etapa de diseño inicial, la siguiente etapa es la simulación del llenado del troquel utilizando modos semiempíricos. La simulación ayuda a calcular la modalidad de llenado del molde. Además, la modalidad depende de la función de la pieza colada y del proceso de llenado. Para piezas con estructuras complejas, es mejor inducir compacidad y resistencia mecánica. Mientras tanto, para las piezas estéticas, el acabado de la superficie debe ser de primera.
Las características se pueden modificar variando el tiempo de llenado. Cuanto más rápido se lima, mayor es la calidad de la superficie, mientras que un relleno más largo impactará con más fuerza en los componentes. Una vez que se completa el análisis, es más fácil notar si habrá algún problema de transmisión.
The aluminum die casting mold design starts with analyzing the manufacturability, then calculating the forces and checking the injection channels. The optimization and design of these channels are done through simulation to know filing mode and detect any issue. After successful completion of this stage, you can move on to producing the designed mold.
Factors to Consider for Making Perfect Die Casting Tooling
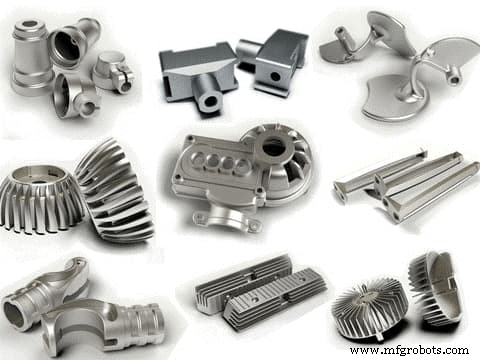
Before making die cast tooling, there are some things to look out for to guide in die cast tool design. They include:
Die Draft
The draft is the degree to which you can tamper with a mold core. You need a precise draft to remove the casting from the die safely. However, the draft is not constant, varying according to the angle of the wall. Thus, characteristics like the type of molten alloy used, the mold’s depth, and the mold’s shape can affect the whole process.
Another factor that can affect drafts is mold geometry. Generally, untapped holes need tapping because of the risk of shrinkage. Likewise, inner walls need more drafting than outer walls because inner walls tend to shrink.
Fillets
A Fillet is a concave junction that helps to smoothen an angled surface. A curved surface disturbs the casting process, so folds have fillets to produce a honed edge and limit the risk of production errors. Although there is an exception to the parting lines, you can add fillets to any part of the mold.
The fillet will increase the lifespan of the tool. To allow for continuity of smoothness, make a constant-radius fillet. Furthermore, tools that have a deep inside will need larger fillets.
Parting Lines
Parting lines, also known as parting surfaces, join various mold sections together. If the parting line is deformed due to work strain or it is wrongly positioned, materials can pass through the space between the mold pieces. This may lead to excessive and non-uniform seaming.
Bosses
Bosses are die-cast knobs that serve as stand-offs or mounting points in die cast tooling. Manufacturing industries usually add a hole to the internal structure of the boss to make sure the walls have a uniform thickness. It is challenging to fill bosses with metal, and thus, ribbing and filleting are essential to eliminate this issue.
Ribs
Die casting ribs to help improve the strength of the material for a product lacking the desired wall thickness. Selective rib placement improves fill capability and decreases product weight. It also reduces the occurrence of non-uniform thickness and stress cracking.
Holes and Windows
Having holes and windows in aluminum die casting mold allows for the creation of substantial drafts and ease in removing a completed mold. However, features like flashovers, cross feeders, and overflow are necessary to prevent material flow and unwanted cast in the holes. Holes and windows are among the essential things in design geometry. They affect the flow of molten metal and play a vital role in the product’s final quality.
Symbols
Manufacturers always add product logos or brand names in the mold design in die casting. Some casting has a date to differentiate a batch from another batch. Although symbols do not make the design process complex, they can add to the cost of production. A raised logo will require a different metal for every manufactured part, while an indented symbol will require a lesser amount of metal.
Wall Thickness
Die castings have a thin wall that has no fast and hard rules for maximum and minimum wall thickness. It is necessary to create a uniform wall thickness throughout the part. Uniformity will provide a smooth metal flow when filling and reduce distortion resulting from cooling and shrinkage. The main aim is for the die casting mould to fill before the solidification process to prevent cold shuts.
RapidDirect Chasing for Perfect Die Casting Parts
Understanding die casting mold design will make your die casting project easier. It will also help you save some time and money. However, you need the service of experts to get the right tool for the best results. RapidDirect offers the best precision die casting services for custom metal parts, providing quality tools, experts, and easy processes.
We have a wide range of materials, manufacturing processes, and surface finishing options for your die casting parts. Also, our experts offer you manufacturing suggestions to ensure you get the most effective solution. After placing the order for die casting parts, RapidDirect manufacturing partners would produce perfect die casting tooling to make the best die-casted parts. Upload your design file today and get an instant quote.
Preguntas frecuentes
Is Die Casting Permanent Mold? For permanent mold, the metal flows directly into the cavity from the reservoir. The molten metal is forced into the cavity under high pressure in die casting.
What is the Mold in Die Casting?The mold consists of two parts – the ejector and the stationary part. It contains the space forming the dimension and contour of the casting. The mold is also known as the die, and they are made from hardened steel to meet the shape requirement of the die casting part.
How are Molds Made for Die Casting?Molds production involves passing a molten metal under high pressure into a metal die. The creation of the mold occurs in sections to allow for easy removal before placing them in machines such that one is removable and the other is fixed. The molten metal would pass through the cavity, and it will then solidify.
Tecnología Industrial
- ¿Qué es la fundición en molde no fungible?
- ¿Qué es el moldeado permanente?
- Cómo soldar hierro fundido:una guía completa
- Una guía para principiantes sobre la fundición de metales
- Fundición a presión frente a moldeo por inyección
- Control de temperatura e influencia durante el proceso de fundición a presión
- Comprender la fundición a presión
- Guía de fundición de precisión
- ¿Qué es la fundición CI?
- ¿Qué es una máquina de fundición a presión?
- Comprender la fundición a presión