Puedes llevarlo contigo:los métodos de trabajo híbridos trasladan algunas tareas a cualquier parte
El aumento en el uso de herramientas de comunicación y producción digital durante la pandemia de COVID-19 ha acelerado el futuro del lugar de trabajo híbrido, en el que algunos empleados y tareas pueden redirigirse fuera de las instalaciones de fabricación.
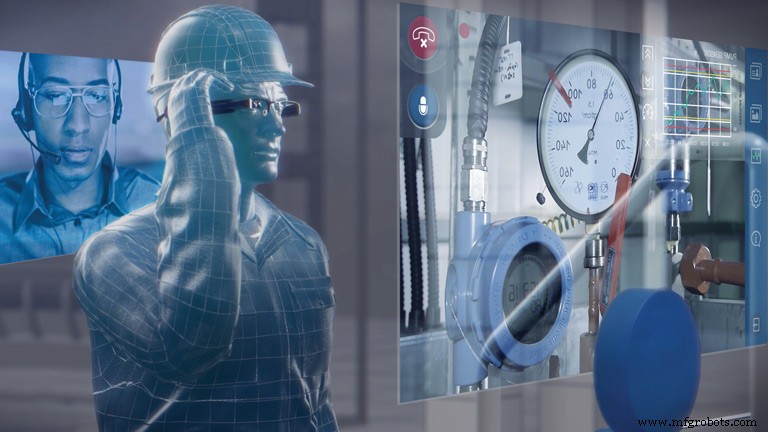
Sin embargo, si bien el personal, como los diseñadores e ingenieros, puede trabajar fácilmente de forma remota y, según la empresa, lo hacía antes de la pandemia, las máquinas aún necesitan operadores en el sitio. Dicho esto, las soluciones como la realidad virtual o mixta y la conectividad basada en la nube están impulsando a las organizaciones a repensar cómo programan y realizan ciertas tareas de fabricación.
Los beneficios de los híbridos
Enfrentados no solo a la escasez de trabajadores calificados, sino también a la necesidad de renovar sus lugares de trabajo para adaptarse a los protocolos pandémicos, los fabricantes han intensificado su búsqueda para encontrar y optimizar herramientas digitales para sus entornos únicos.
“Si bien los beneficios desde una perspectiva de salud y seguridad son claros durante una pandemia global, los fabricantes en particular vieron beneficios de productividad y retención de empleados” al buscar acuerdos de trabajo híbridos, dijo Reid Paquin, director de investigación de IDC Manufacturing Insights de Needham, Massachusetts. un tercio también experimentó una mayor experiencia/satisfacción de los empleados, lo que creemos que desempeñará un papel en los esfuerzos de la industria para abordar los problemas de talento/laborales”.
Además de la fabricación, "la mayoría de los OEM grandes tienen elementos de servicio de campo, y un problema que es casi universal en este momento es la pérdida de empleados y los problemas con la transferencia de conocimientos", dijo Charlie Neagoy, vicepresidente senior de éxito del cliente de Librestream. “Actualmente estamos unos tres millones de personas adelantadas en términos de jubilación, y eso ha acelerado esta brecha de conocimiento. La fuerza de trabajo híbrida, la capacidad de hacer cosas desde diferentes lugares, ayuda a compensar la pérdida de conocimiento que proviene de la jubilación anticipada. Las fuerzas de trabajo híbridas pueden ofrecer trabajos en todo el mundo y diferentes tipos de flexibilidad para sus empleados”.
Librestream, con sede en Winnipeg, Manitoba, Canadá, ofrece una plataforma de solución remota de realidad aumentada (AR). “Un beneficio relacionado de los lugares de trabajo híbridos es que permite plataformas de colaboración compartida entre múltiples partes”, agregó Neagoy. “La seguridad también es una de las principales razones para utilizar fuerzas de trabajo híbridas. Muchos de los lugares y equipos de fabricación son peligrosos, por lo que acceder a un sitio de forma remota reduce el riesgo de accidente”.
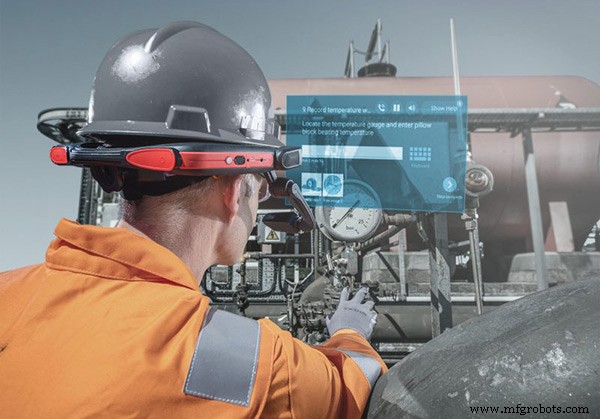
Además, las inspecciones y certificaciones requeridas se pueden realizar de forma remota, continuó Neagoy. “Nuestra plataforma Onsight nos permite rastrear cuántas inspecciones realizan nuestros clientes cada semana. Nuestros clientes realizan entre 7.000 y 8.000 inspecciones de forma remota cada semana. Antes de COVID, registrábamos alrededor de 2000 inspecciones por semana”.
La pandemia ha demostrado que una fuerza laboral híbrida brinda mayor resiliencia organizacional y eficiencia de los trabajadores, según Federico Sciammarella, presidente y CTO de MxD, Chicago, que se enfoca en la fabricación digital y es parte de Manufacturing USA, una red de 14 institutos de fabricación avanzada.
“Si una organización cuenta con la infraestructura de red adecuada y es segura, es posible ejecutar operaciones de forma remota”, dijo Sciammarella. "La infraestructura de red adecuada hace que una empresa sea más resistente porque las personas aún pueden acceder a los datos necesarios para mantener las operaciones en funcionamiento incluso cuando trabajan de forma remota".
Cómo y dónde empezar
Al igual que con cualquier transformación organizacional o industrial, la tecnología por sí sola no resolverá los problemas emergentes. Las herramientas de supervisión y colaboración remotas se han vuelto comunes, pero como siempre, la planificación adecuada es fundamental para adoptar un modelo híbrido.
“Las plataformas/aplicaciones de colaboración, videoconferencia y uso compartido de contenido son algunas de las áreas en las que los fabricantes han invertido o buscan invertir para habilitar mejor los modelos de trabajo híbrido”, señaló Paquin de IDC Manufacturing Insights. “La mayoría de los fabricantes casi siempre necesitarán tener algunos empleados en el sitio. El mantenimiento/gestión de activos es una de esas áreas en las que este será el caso; tiene que haber alguien girando una llave inglesa. En el futuro, los fabricantes podrán cambiar más de eso a los robots, pero por el momento, la madurez de la tecnología y los costos de inversión no hacen que eso sea una realidad para la mayoría de los fabricantes”.
Los fabricantes que ya habían realizado grandes inversiones en automatización, recopilación de datos y conectividad remota tenían la infraestructura para respaldar este cambio antes de la pandemia, reconoció Paquin. “Vimos que los fabricantes que tenían sistemas en la nube, como ERP, se adaptaban mejor al trabajo híbrido. El mejor enfoque es construir una estrategia/hoja de ruta en toda la organización, pero implementarla en pasos más pequeños. Comience con funciones de tipo administrativo, ya que se necesitaría menos inversión para permitir el trabajo remoto para estos grupos. Preste atención a las políticas de trabajo remoto vigentes y cómo administrar empleados remotos, e incorpore las mejores prácticas y las lecciones aprendidas a medida que continúa expandiéndose a más funciones”.
Al señalar que el trabajador promedio pasa 240 horas al año (10 días) esperando información, Neagoy de Librestream aconsejó que “si usted es un operador en el piso, una buena estrategia es tomar el conocimiento de un experto en la materia e integrarlo en digital”. instrucciones de trabajo, por lo que ya no tendrá que esperar a ese experto”.
Es esencial poner la nueva tecnología en manos de los trabajadores adecuados, continuó Neagoy. “Si va a introducir una nueva tecnología, comience con el experto en tecnología. Nuestros clientes suelen ver una distribución bimodal de captación de usuarios:es radicalmente diferente entre las personas a 10 años de jubilarse y las personas con menos de 10 años de carrera”.
Tenga la seguridad, dijo, que “esto es algo que se puede implementar en tres meses. No se realizará por completo en tres meses, pero en tres meses debería poder mover la aguja".
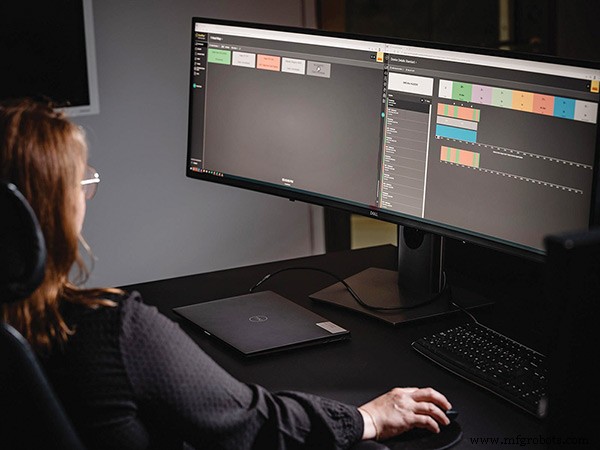
Al igual que cuando se abordan otras operaciones de fabricación, dijo Sciammarella de MxD, “las acciones deben planificarse de manera cuidadosa y holística, teniendo en cuenta las herramientas básicas de mejora continua. Es importante revisar primero lo que tiene actualmente y por qué. El "por qué" es fundamental y puede parecer obvio, pero no siempre es así, especialmente si tiene un largo historial de flujos de trabajo. Una empresa querrá llegar a un punto en el que el equipo sepa qué datos e información se pueden digitalizar, si aún no lo han hecho, y cómo se pueden usar para respaldar no solo horarios de trabajo flexibles, sino también un proceso de mejora continua que se puede aprovechar. de forma remota para que la producción pueda continuar fabricando productos y optimizar el trabajo según sea necesario”.
Si una organización ha comenzado a implementar tecnologías en la nube para datos comerciales, agregó, "podría aprovechar esas tecnologías en la nube para la recopilación de datos operativos y hacer que los archivos y la información estén fácilmente disponibles para esa fuerza laboral".
Éxitos recientes
Para Fives Lund de Seattle, un productor de maquinaria altamente personalizada, la flexibilidad en el lugar de trabajo y tener las herramientas adecuadas para realizar tareas críticas de forma remota ha sido parte de la cultura durante años.
Aprovechar las oportunidades para garantizar que sus empleados puedan ser lo más efectivos posible dondequiera que estén "ha sido un proceso continuo desde que nos unimos al grupo Fives en 2015", dijo el CEO Casey McGarity. “Incluso antes de la COVID, era un proceso continuo y un viaje, no un destino”.
Antes de la pandemia, “nuestra fuerza laboral estaba bastante concentrada en nuestras instalaciones en Seattle, pero siempre teníamos ingenieros y técnicos que estaban en el campo apoyando equipos”, agregó Jonathan Schwedhelm, ingeniero mecánico principal y director de ingeniería. "También co-diseñamos algunos de nuestros complejos equipos de automatización con nuestras empresas hermanas en todo el mundo".
Luego vino la pandemia. Y aunque Fives Lund estaba al mismo ritmo que otros grandes empleadores de su región en lo que respecta a las personas que trabajan desde casa, "tenemos un entorno bastante práctico", explicó Schwedhelm. “Nuestros ingenieros y técnicos trabajan muy de cerca para construir, probar y dar soporte a nuestros equipos”. Eso significó ser creativo para continuar con la ingeniería y la entrega de equipos y el apoyo a los clientes.
“Al principio, eso significaba que algunos ingenieros se llevaban a casa proyectos y ensamblajes más pequeños para trabajar en ellos. Algunos de nuestros ingenieros de control instalaron hardware en sus hogares para poder programar las máquinas, pero eso realmente no escala”.
Ahí es donde entró en juego Run MyVirtual Machine de Siemens. El software de simulación de operación de la máquina “abre oportunidades para que los ingenieros de control puedan comenzar a construir los controles 'viscerales' de la máquina y probar la cinemática y la operación, así como simular las máquinas a escala para asegúrese de que hagan las cosas tan rápido como cree que lo harán”, dijo Schwedhelm.
Run MyVirtual Machine ha hecho maravillas en un proyecto que comenzó el año anterior a la pandemia, continuó.
“En 2019, comenzamos a trabajar en un gran equipo de automatización y nuestro cliente nos pidió que usáramos controles CNC de Siemens. Estamos familiarizados con varios sistemas de control NC diferentes, pero la máquina que estábamos construyendo tenía una cinemática realmente única, y sabíamos que tenía algunos obstáculos técnicos importantes que teníamos que eliminar antes de que el hardware estuviera disponible, y asegurarnos de que podríamos hacerlo sin tener que sentarnos frente a los paneles de control aquí en nuestras instalaciones”.
Si bien tenía experiencia con otro software de modelado, continuó, “dado que se trataba de un proyecto de Siemens, por primera vez nos permitió aprovechar esta herramienta:usarla en la planificación, usarla para eliminar riesgos y asegurarnos de que estamos tomar buenas decisiones a medida que avanzábamos en el proceso de diseño. Y ahora que la cadena de suministro se está convirtiendo en un problema mayor y los plazos de entrega de nuestros componentes de control pueden ser desafiantes, nos permite seguir avanzando sin estancarnos por completo”.
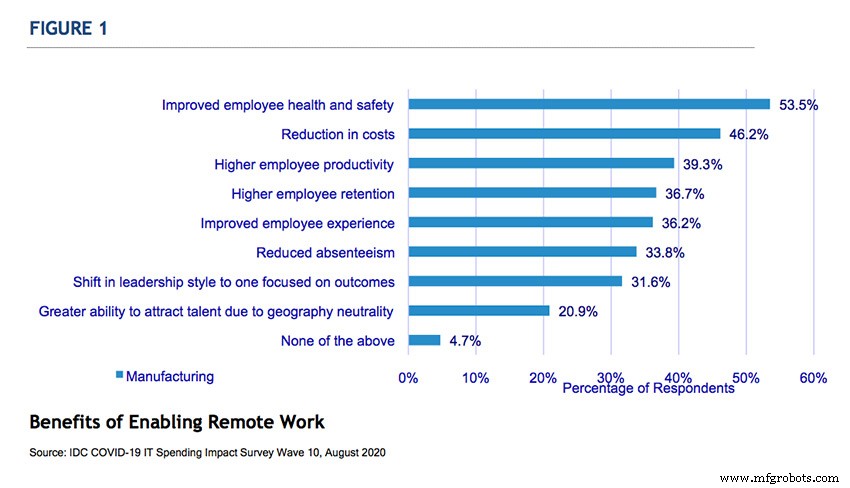
El núcleo de la cultura de Fives Lund es el hecho de que "nuestros ingenieros (mecánicos, eléctricos y de software) a menudo trabajan hombro con hombro en el piso y construyen máquinas y solucionan problemas", señaló McGarity. “Como mínimo, los ingenieros están disponibles para visitar el taller si se encuentran con problemas” o para ayudar en la planificación, el montaje o las pruebas. En la medida en que los ingenieros no estén "participando activamente" en las tareas del taller, "están profundamente involucrados en la planificación de esas cosas".
Al abordar el problema central de implementar flujos de trabajo híbridos en la fabricación, McGarity señaló que, si bien el personal de la planta de producción tenía que permanecer en el sitio, “era muy difícil y muy diferente para Fives Lund no tener a los ingenieros allí para ayudar con ese proceso. Al igual que muchas empresas, sopesamos los riesgos de COVID frente al riesgo de la cultura y la eficiencia que conlleva tener un equipo fuerte y cohesionado. Las herramientas que tenemos ayudan a mantener esa cultura. Empezamos con un grupo especialmente sano y fuerte, pero esos músculos colectivos se atrofian un poco, incluso con buenas herramientas. Cuanto más eficaces sean las herramientas, más capaces seremos de mantener nuestras fuerzas durante más tiempo. Pero también necesitamos regresar y recordarnos a nosotros mismos:'Somos más fuertes cuando estamos físicamente cerca'".
Adaptación con flujos de trabajo ajustados
Las soluciones híbridas también son algo natural para Sandvik Coromant, que no solo proporciona herramientas que fomentan las oportunidades de trabajo remoto para sus clientes, sino que también ha ajustado los flujos de trabajo en sus propias fábricas de herramientas de corte.
“Tener la tecnología implementada, en lo que respecta a CAD/CAM, nos ha ayudado, pero obviamente todavía necesitamos personas aquí para operar el equipo”, dijo el gerente de la unidad de producción, Richard Boyle. “No hemos llegado al punto de que nuestro equipo se quede sin luz (todavía necesitamos a nuestros operadores aquí), pero nos dio una buena oportunidad para seguir adelante con los aspectos de ingeniería de nuestra planta de fabricación, con ingenieros de fabricación en la oficina, en la planta de producción y también poder trabajar desde casa un porcentaje del tiempo”.
Cuando llegó la pandemia, los diseñadores de Sandvik también trabajaron de forma remota la mayor parte del tiempo, dijo Boyle, yendo en bicicleta al taller cada semana en un horario rotativo para brindar apoyo a la producción y al mismo tiempo limitar la exposición de cualquier persona. Mientras tanto, la compañía emplea lo que llama producción no tripulada, alternando operadores de máquinas "cuando tenemos un equipo que tiene automatización y funciona sin la presencia de un operador".
Boyle explicó que entre dos turnos de operador de máquina de ocho horas, se programa un intervalo de cuatro horas. Con dos celdas una frente a la otra, esos horarios se pueden escalonar para que solo un operador tenga que estar en el sitio para atender una interrupción en cualquiera de las celdas. "Tenemos personas que comienzan a trabajar casi todo el día para asegurarnos de que tengamos una cobertura completa".
También le da crédito a la asociación de Sandvik con Microsoft y su tecnología de realidad mixta HoloLens por facilitar el trabajo híbrido. “La mayor parte de la tecnología que utilizamos en producción desde nuestro MES y nuestros tableros (todos los datos disponibles) proviene de sus soluciones. Hemos tenido una interrupción aquí y allá, tal vez durante un par de horas en las que no podemos iniciar sesión en un servicio, pero son pocas y distantes entre sí”.
Durante la pandemia, Sandvik encargó un nuevo equipo que llegó desde Suecia cuando se cancelaron todos los viajes de pasajeros, recordó Boyle. “En lugar de esperar hasta que se permitiera viajar nuevamente y el técnico de Suecia pudiera venir y terminar de instalarlo, mediante el uso de tecnología como HoloLens, pudimos hacer que nuestro personal de mantenimiento local trabajara directamente con esta persona, que podía ver directamente a través de su observar lo que estaban haciendo y asegurarnos de que nos concentráramos en las cosas correctas para poner en marcha y operar esta máquina”.
En última instancia, dijo Boyle, equilibrar los flujos de trabajo híbridos y tradicionales es “siempre una lucha. Es algo en lo que tienes que trabajar. Con híbrido, no decimos que nadie es 100 por ciento remoto. Si puede intentar abrir un proceso para que sea remoto y aún no esté listo, a veces es difícil recuperarlo. Hemos sido muy lentos y meticulosos al abrir un proceso para que sea híbrido, asegurándonos de que estamos capaz de mantenerlo y modificarlo rápidamente para que no falle”.
Para los clientes, Sandvik ofrece productos listos para usar de forma remota, incluidos CoroPlus Machining Insights y CoroPlus Process Control, dijo Jeff Rizzie, director de ventas de mecanizado digital para las Américas.
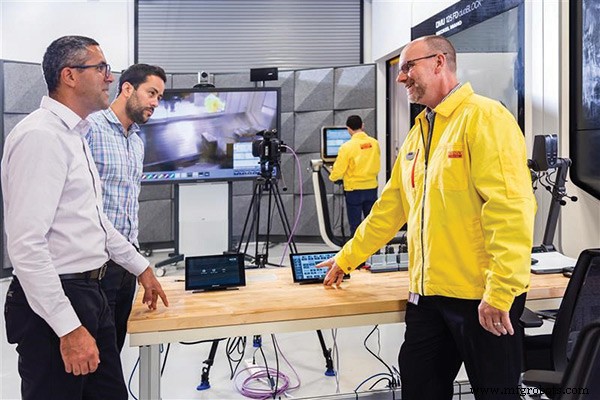
Machining Insights es una plataforma de software como servicio que monitorea las condiciones de la máquina, explicó Rizzie. “Podemos saber lo que está sucediendo con una máquina herramienta en particular simplemente iniciando sesión en un sitio. Puedo comprender los datos de utilización, cuántas piezas estoy fabricando y mirar la programación y múltiples puntos de datos que provienen directamente de la máquina. Este tipo de soluciones son de gran valor, incluso desde el punto de vista de las operaciones. Ahora ya no tengo que estar en el taller para comprender lo que sucede en mi tienda mediante el uso de los datos de la manera correcta”.
CoroPlus Process Control va un paso más allá en la medición del estado de todo un proceso de fabricación, continuó Rizzie. “Puede realizar un control adaptativo y anular la máquina. Si detecta una colisión o una herramienta rota, puede apagar automáticamente la máquina. Puede emitir un comando para adquirir una herramienta hermana o una herramienta redundante y reiniciar la fabricación. Y puede ayudar con el mecanizado no tripulado:agrega una medida adicional de seguridad al proceso”.
Además, Sandvik se esfuerza por "mejorar las habilidades" de sus empleados para equiparlos mejor para brindar asistencia a los clientes de forma remota, señaló Annika Langeen, vicepresidenta de marketing de las Américas. “Hemos equipado nuestros Centros Sandvik Coromant con la última tecnología para permitir el soporte remoto en proyectos de clientes y clases de capacitación virtual en vivo”, dijo. “Con la última tecnología de audio y video, los clientes pueden ver lo que sucede dentro y fuera de las máquinas en nuestros Centros Sandvik Coromant e interactuar con nuestros expertos de bata amarilla en tiempo real desde cualquier lugar que deseen. Durante muchos años, también hemos ofrecido un extenso programa de aprendizaje electrónico para proporcionar a los clientes, estudiantes y empleados conocimientos sobre corte de metales. Los participantes pueden tomar el programa de capacitación y obtener la certificación desde donde quieran, en cualquier momento”.
Trabajo híbrido en el futuro
La fabricación digital a menudo se promociona como una herramienta de contratación y retención de trabajadores. Paquin de IDC está de acuerdo.
“El trabajo híbrido/remoto puede ampliar un grupo de candidatos para ciertos roles, y escuchamos constantemente de los fabricantes que es la porción más joven de su fuerza laboral la que desea más flexibilidad y opciones en torno a los modelos de trabajo”, señaló. "Para una industria que lucha por atraer nuevos talentos, no adoptar modelos de trabajo híbridos podría hacer que esto sea un desafío aún mayor".
El gran desafío, señaló Neagoy de Librestream, “es simplemente comprender dónde se puede aplicar un lugar de trabajo híbrido. El ochenta por ciento de la fuerza laboral está en el campo, por lo que crear fuerzas de trabajo híbridas puede ser una perspectiva abrumadora. La receta para el éxito en la implementación de una fuerza laboral híbrida es identificar objetivos comerciales muy claros. Tenga algo que sea cuantificable y medible, y comience poco a poco. Si tiene diferentes áreas funcionales que son esencialmente duplicados entre sí, elija una y tenga éxito con eso y luego aplique lo que aprendió en toda la organización".
Tenga en cuenta también que "existe una extraña dualidad en la forma en que las personas se adaptan a las fuerzas de trabajo híbridas", aconsejó Neagoy. “Las personas con más conocimiento sobre el negocio pueden ser las menos hábiles tecnológicamente. Hágales saber a los empleados experimentados que las nuevas tecnologías híbridas no están ahí para ayudarlos, están ahí para ayudar a los demás”.
Si bien las plataformas y tecnologías que existen para hacer de lo híbrido una realidad hicieron la transición durante COVID, el problema ahora es “cómo integrarlas de una manera que sea efectiva para las necesidades de cada empresa”, observó Sciammarella. “¿Están presentes las redes y la conectividad correctas, es decir, 5G, y cómo se puede garantizar su seguridad? Esto puede ser costoso y requerirá una cuidadosa reflexión sobre cómo incorporar estas herramientas y plataformas de la manera más económica posible.
“MxD siempre ha visto que a las empresas que están habilitadas digitalmente les va mejor cuando surgen crisis. La pandemia no fue diferente”, continuó. "Las organizaciones están en caminos diferentes para lograr la transformación digital, y aquellas que eran más avanzadas naturalmente podrían hacer la transición fácilmente a las prácticas híbridas en general".
En última instancia, el hecho de que las herramientas estén disponibles para crear una fuerza de trabajo híbrida depende realmente de la cultura de una empresa determinada y su voluntad de “invertir en un cambio significativo para que su empresa no solo sobreviva sino que prospere”. Honestamente, el mayor desafío es el cambio cultural. En la fabricación, las personas son criaturas de hábitos, y es difícil salir de eso. El otro gran desafío son los costos financieros de la digitalización para empoderar a una fuerza laboral híbrida”, señaló Sciammarella. "Es extremadamente difícil para las pequeñas empresas evaluar qué podría generar el mayor retorno de la inversión cuando hay tanto por ahí".
Sistema de control de automatización
- ¿Cómo pueden las empresas aeroespaciales llevar la fabricación aditiva al siguiente nivel con MES?
- ¿Qué se puede hacer con una máquina enrutador CNC?
- ¿Qué se puede hacer con una impresora 3D?
- Con IA, las grandes tiendas pueden enfrentarse a los rivales de E-Tail
- Enrutador CNC en venta:¿Qué puede hacer con él?
- 5 maneras en que la automatización del proceso de fabricación puede ahorrarle dinero
- Cómo los robots de software pueden ayudarlo a tomar el control de la 'nueva normalidad'
- ¿Qué se puede hacer con una máquina CNC?
- Conectividad en la fabricación:¿cómo se puede mejorar?
- ¿Puede la IA crear puestos de trabajo en la fabricación?
- ABB dice que se necesita flexibilidad con el cambio a la electrificación de vehículos