Robots, personal de taller colaboran, maximizando la sinergia y la seguridad
La fabricación eficiente exige sistemas coordinados de personal de taller, equipos y software. Estos sistemas incluyen cada vez más tecnología robótica, ya que los fabricantes reconocen la confiabilidad, la repetibilidad y la flexibilidad que brindan los robots. Según la Federación Internacional de Robótica, la cantidad de robots industriales en uso en todo el mundo aumentará a alrededor de 2,6 millones para 2019, aproximadamente un millón más que en 2015. Aproximadamente el 70 % de los robots industriales se utilizan en los sectores automotriz, eléctrico/electrónico y metalúrgico. e industrias de maquinaria.
La seguridad es la primera consideración en cualquier operación de fabricación; Tradicionalmente, el uso seguro de los robots industriales ha requerido mantener distancias establecidas entre el personal del taller y los robots, y colocar protecciones y jaulas alrededor de los robots para evitar lesiones en los trabajadores. Una variedad cada vez mayor de robots, software y estrategias de implementación tiene como objetivo una interacción más estrecha y productiva entre humanos y robots.
El control de esta relación va desde la interrupción controlada por sensores del movimiento de un robot cuando los trabajadores se mueven hacia áreas potencialmente peligrosas, hasta la aplicación de robots totalmente "colaborativos", también llamados cobots, diseñados para operar de manera segura junto a trabajadores humanos. Los diferentes modos de colaboración permiten a los fabricantes aprovechar todas las capacidades de los sistemas robóticos y el personal del taller.
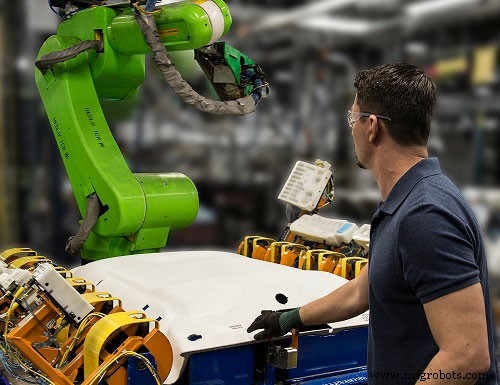
El aburrido, peligroso y sucio
La escasez actual de trabajadores calificados en los EE. UU. impulsa gran parte de la demanda de robots colaborativos. La jubilación del personal de taller veterano y la falta de suficientes trabajadores jóvenes que ingresan a la fuerza laboral de fabricación ha dejado a los propietarios de talleres con escasez de personal.
Para abordar esta brecha de habilidades, los fabricantes están utilizando robots para operaciones repetitivas y/o peligrosas y trasladando a los trabajadores a trabajos que requieren más pensamiento y habilidad. “Estamos viendo que las personas son reasignadas”, dijo Craig Tomita, gerente de ventas de la región occidental de Universal Robots USA Inc. (Ann Arbor, MI), un fabricante de robots totalmente colaborativos.
Tomita dijo que la implementación de robots colaborativos es relativamente simple porque funcionan en un entorno a escala humana y no requieren la protección necesaria con los robots industriales tradicionales. No hay necesidad de reorganizar el piso de producción y la utilización del espacio no cambia. “Simplemente coloca robots colaborativos donde los operadores humanos están haciendo el trabajo actualmente”, dijo, y agregó que si bien los robots colaborativos son seguros, la evaluación de riesgos (determinar todos los peligros potenciales en un sistema y encontrar formas de mitigarlos) es vital.
La facilidad de uso es un atributo clave de los robots totalmente colaborativos. Aunque las capacidades de los pequeños robots colaborativos están a la par con las de los pequeños robots tradicionales, los requisitos de programación y formación colaborativa son mínimos. “La facilidad de programación en el sistema UR cambia las reglas del juego”, dijo Tomita. “Cuando, por ejemplo, es necesario integrar un robot en un sistema de fabricación más grande, las unidades de Universal se pueden programar y ejecutar mediante una pantalla táctil portátil. Si es necesario, los usuarios de nivel superior también pueden programar el robot utilizando su lenguaje de secuencias de comandos similar a Python”.
Los talleres más pequeños pueden usar fácilmente los robots colaborativos, donde los costos de integración han sido una barrera de entrada. “Si lo miras como un iceberg, la parte del robot se asoma por encima del agua”, dijo Tomita. “El proceso de integración es lo que está abajo. Tomas ese iceberg como un todo y se vuelve muy caro. Un robot colaborativo cuesta casi lo mismo que un robot industrial estándar, pero el costo de integración es mucho menor”, dijo.
La utilización de robots también puede ayudar a reducir los costos laborales, dijo Tomita:"Las empresas que usan robots colaborativos a menudo pueden cotizar trabajos que antes no podían cotizar porque sus costos laborales estaban fuera del alcance".
Las aplicaciones potenciales están abiertas de par en par. “Aún no se ha pensado en la cantidad y los tipos de aplicaciones para nuestros robots colaborativos”, dijo Tomita. “La gente está tan acostumbrada a pensar que el robot está detrás de una jaula allí, la gente está aquí y los dos nunca se encontrarán. Eso está cambiando”.
Universal Robots ofrece tres modelos de robots colaborativos de seis ejes, desde unidades UR3 que manejan cargas útiles de hasta 3,3 kg (7,26 lb) y tienen un radio de trabajo de 500 mm (19,7″), hasta robots UR10 con 10 kg (22- lb) carga útil y radio de trabajo de 1300 mm (51,2″).
Un cliente típico de Universal Robots es CleanLogix LLC (Santa Clarita, CA), que desarrolla productos que usan CO2 en limpieza, enfriamiento y otras aplicaciones. El presidente de CleanLogix, David Jackson, dijo:"Podemos esparcir el rociado en una zona de corte y proporcionar un medio muy limpio y ecológico para enfriar una herramienta de corte en un proceso". Señaló que un solo robot es capaz de realizar diferentes tareas; por ejemplo, colocar una pieza en un centro de mecanizado y luego cambiar las herramientas del efector final para proporcionar refrigerante. “Así que tienes un robot multitarea y una solución totalmente ecológica y eficiente. Estamos muy entusiasmados con estos robots de factor de forma pequeño”.
La capacidad de los robots colaborativos para trabajar de forma segura con humanos permite organizar las operaciones para maximizar la sinergia; por ejemplo, un robot puede ensamblar una serie de componentes mientras un trabajador humano realiza la inserción de pequeños cables que requieren destreza y percepción cognitiva. Los robots son ideales para operaciones que requieren repetición, confiabilidad y precisión, incluidas las operaciones de empaque, paletización, ensamblaje y recogida y colocación.
La repetibilidad y la precisión son medidas separadas pero relacionadas del rendimiento del robot. La repetibilidad es una medida de la capacidad de un robot para volver a una posición determinada una y otra vez. La repetibilidad declarada de varios robots colaborativos está en el rango de aproximadamente ±0,02 a ±0,1 mm (0,0008 a 0,004″) o menos.
La precisión, por otro lado, mide qué tan cerca de una posición o ruta deseada puede moverse un robot, y se puede categorizar como precisión posicional y precisión de ruta. Tareas como la perforación, donde el robot se mueve a una posición y se detiene mientras se perfora el orificio, requieren precisión posicional. La precisión de la ruta es necesaria para procesos como el corte por láser o la pintura, donde el proceso se lleva a cabo mientras el robot se mueve entre los puntos.
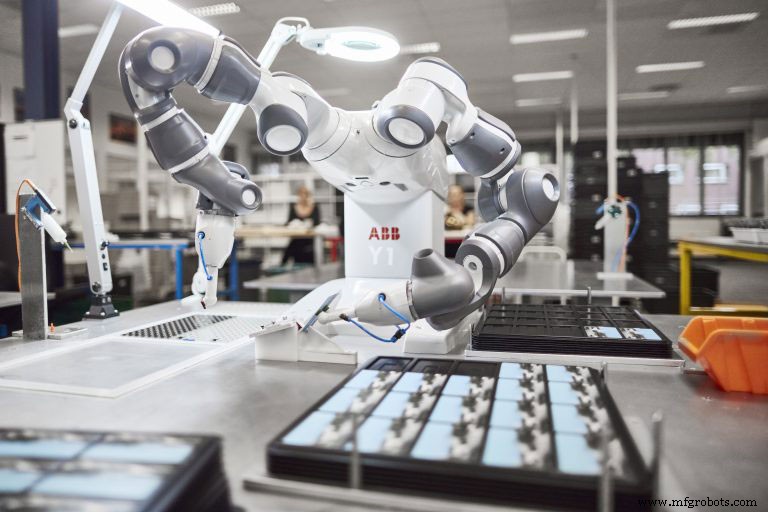
La aplicación determina la colaboración
En general, la actividad de lado a lado del personal del taller y los robots se logra con robots colaborativos que manejan pequeñas cargas útiles a velocidades lentas, generalmente alrededor de 1 m/seg (39,4 ips). Sin embargo, dijo Nicolas De Keijser, gerente de línea de negocios de ensamblaje y prueba de la División de Robótica y Movimiento de ABB Inc. (Cary, NC), la carga que transporta un robot o la velocidad a la que viaja no garantizan por sí mismos una operación segura y colaborativa. . Una carga útil muy ligera pero peligrosa podría ser una hoja de afeitar o una aguja hipodérmica. Una carga útil de movimiento lento pero pesada podría representar un riesgo de aplastamiento para el personal del taller. De manera similar, la falla de la pinza al mover una carga útil de tamaño mediano a una velocidad moderada podría enviar la carga útil a toda velocidad por el taller.
Un sistema de robot solo es colaborativo en relación con su aplicación. “Si la operación es peligrosa, no desea estar cerca del robot, sin importar cuán colaborativo sea el robot”, dijo De Keijser, y agregó que se requiere una evaluación completa de la seguridad de la solución en cualquier aplicación. "Si lees los estándares, siempre dictan que estamos hablando de una operación colaborativa, no de un robot colaborativo".
ABB adopta dos enfoques para garantizar la coexistencia segura de trabajadores y robots. Las aplicaciones verdaderamente colaborativas, como el ensamblaje de piezas pequeñas, generalmente se pueden realizar con el robot YuMi de doble brazo montado en una mesa de la compañía. El alcance del robot de 38 kg (84 lb) es de 599 mm (24″) y la carga útil de 500 kg (1,1 lb) por brazo. Ocupa un área a escala humana mientras opera de forma segura junto con el personal del taller.
Por otro lado, ABB facilita el funcionamiento seguro de grandes robots industriales estándar a través de sistemas redundantes que combinan una cuidadosa programación y un software de supervisión de la seguridad. Después de programar un robot para un rango seguro de operación, el software de monitoreo de robots con certificación de seguridad SafeMove2 de ABB brinda protección de seguridad redundante al monitorear la actividad del robot, incluidos límites de velocidad seguros, monitoreo de parada y rangos de ejes, así como supervisión de posición y orientación. El software está integrado en el controlador del robot y puede ahorrar tiempo de configuración y facilitar una mayor productividad al tiempo que reduce el costo total de inversión, según De Keijser.
El sistema Kinetiq Teach de Yaskawa Motoman es un ejemplo del modo de guía manual de interacción humano/robot descrito en las normas ISO 10218-1 y 10218-2.
Control adaptativo integrado
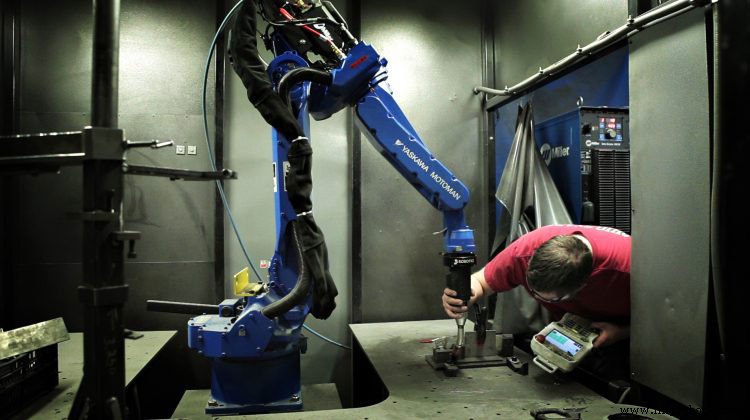
Otra forma de colaboración robótica combina las habilidades y la experiencia de un artesano con la capacidad de un robot para operar en áreas peligrosas. Generalmente, la soldadura no es una operación fácil de usar. Según Zane Michael, director de desarrollo de negocios térmicos de Yaskawa America Inc., Motoman Robotics Division (Miamisburg, OH), “En el mercado actual, la palabra colaborativo significa que tiene una zona de robot y operador que se superponen. Están trabajando en estrecha colaboración. No he visto la palabra colaborativo en ese sentido aplicada al entorno de soldadura”.
Aunque la soldadura robótica no puede llamarse estrictamente colaborativa, una forma de colaboración entre un soldador experto y un robot respalda un rendimiento constante. No es que hacer funcionar un robot de soldadura sea demasiado difícil. “Programar y hacer funcionar el robot es fácil”, dijo Michael. “En Motoman, tenemos un sistema llamado Kinetiq Teach, donde puede agarrar la antorcha y mover el robot por el camino que desea que siga, registrar ese camino y ya está listo para comenzar”. Sin embargo, añadió, hacer funcionar un robot de soldadura sin conocimientos de soldadura es "una batalla cuesta arriba" si se producen defectos de soldadura episódicos, como socavaduras o quemaduras.
En esos casos, un soldador experimentado puede ajustar las acciones del robot para superar los problemas. Los sistemas de control adaptativo que utilizan láseres u otros sensores están disponibles para el seguimiento básico de costuras, pero la mayoría de los sistemas de soldadura se envían sin tales sistemas. “El soldador humano tiene lo que yo llamo control adaptativo incorporado”, dijo Michael.
Según la complejidad operativa y las capacidades de volumen, las células robóticas poseen diferentes formas de automatización y sistemas de seguridad. La celda C30 de una sola estación ArcWorld de Motoman es para el procesamiento de una sola pieza de bajo volumen de piezas más pequeñas. Cuando la puerta de la celda se abre para permitir que un operador cargue una pieza soldada en el posicionador de la celda, el robot está en modo de parada de emergencia. Después de que el operador abandona la celda, la puerta desciende y se realiza la soldadura. Por otro lado, las máquinas de la serie 6000 de alto volumen y piezas grandes de Motoman cuentan con un posicionador que indexa los accesorios de la pieza como una rueda de la fortuna y se puede cargar desde el exterior de la celda mientras varios robots sueldan un ensamblaje en el interior.
Las empresas de soldadura se enfrentan a una escasez de mano de obra similar a la de otros segmentos de fabricación. Según las estadísticas de la Oficina de Trabajo de EE. UU., la Sociedad Estadounidense de Soldadura estima una escasez de soldadores de 290 000 en EE. UU. para 2020. Michael dijo que los proveedores de soldadura con visión de futuro están trabajando con escuelas de oficios y centros profesionales para crear un plan de estudios para soldadores. Por ejemplo, Motoman ha creado un programa STEM de soldadura y un plan de estudios correspondiente para la formación en soldadura de la escuela secundaria y para adultos.
Robots, el IoT
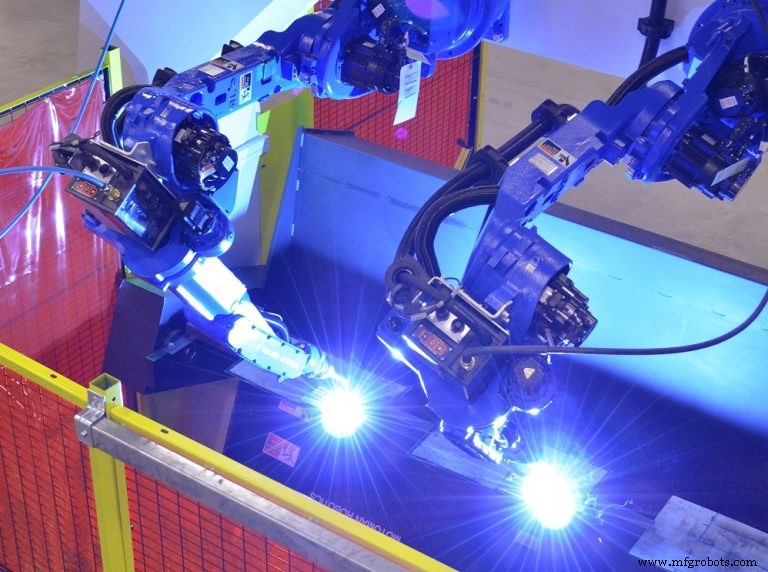
La computación en la nube y el Internet de las cosas facilitan la colaboración entre robots, usuarios y fabricantes de robots. Los fabricantes monitorean rutinariamente el tiempo de actividad del robot para documentar la productividad, dijo Mark Scherler, gerente general, segmento de unión de materiales, para el proveedor de robots FANUC America Corp. (Rochester Hills, MI), “Pero hay más que eso. Estamos utilizando Internet para recopilar datos de los robots y ayudar a los fabricantes a mejorar el tiempo de actividad”.
FANUC proporciona robots industriales estándar y colaborativos. Para aprovechar al máximo los datos que recopilan los robots, la empresa ha desarrollado una aplicación de diagnóstico de tiempo de inactividad cero (ZDT) que detecta y analiza información crítica sobre el estado de mantenimiento y funcionamiento mecánico de un robot. Por ejemplo, ZDT instalado en robots en las instalaciones de un fabricante puede detectar un robot que experimenta niveles de torsión crecientes que pueden indicar un problema con un eje en particular. A través de la tecnología en la nube, la aplicación ZDT envía la información operativa al centro de datos de FANUC para su análisis. Los problemas críticos desencadenan la transmisión de avisos a dispositivos inteligentes designados en el usuario del robot.
Al mismo tiempo, FANUC confirma la disponibilidad de piezas que pueden ser necesarias para resolver el problema. Los datos también se pueden usar para optimizar los sistemas robóticos en términos de mejorar la duración del ciclo, reducir el consumo de energía y extender la vida útil del robot a través de un mejor mantenimiento.
Flexibilidad de automatización
Jeff Estes, gerente de ventas regional del este de la división Morris-South de Morris Group (Charlotte, NC) y ex director, socios en THINC para Okuma America Corp., dijo que la industria automotriz de alto volumen ha liderado la adopción de la automatización durante décadas. Hoy en día, los fabricantes de menor volumen buscan la confiabilidad y la previsibilidad que brinda la automatización, pero también desean la flexibilidad para permitir cambios rápidos de un lote de producción a otro. Con ese fin, la tecnología robótica permite que un taller cambie rápidamente los detalles de programación y los efectores finales.
Estes señaló que la automatización robótica de una máquina herramienta no implica simplemente cargar y descargar piezas. “La clave es cómo lograr una operación de baja o nula asistencia”, dijo. En una celda completamente automatizada, numerosos elementos, que incluyen una máquina herramienta, un robot, un medidor, un sistema de visión y un equipo de manejo de materiales, se unen para crear una "operación de circuito cerrado que puede continuar funcionando y tomar decisiones básicas sin interacción humana, —dijo Estes—. Los múltiples elementos de una celda generan información sobre operaciones individuales pero, "hasta que comiencen a trabajar entre sí, son solo piezas de información". Un integrador elige y organiza los elementos de la celda y coordina sus funciones.
Algunos proveedores de máquinas herramienta mantienen capacidades de integración internas para proporcionar sistemas llave en mano. Methods Machine Tools Inc. (Sudbury, MA) tiene más de 30 ingenieros de automatización en los EE. UU., así como personal de diseño, control, eléctrico/mecánico, integración de sistemas y servicio de campo/instalación. Para complementar sus actividades como proveedor de máquinas herramienta e integrador de sistemas, Methods agregó recientemente un centro de automatización e integración a sus instalaciones de Charlotte, NC. Los especialistas en automatización y los ingenieros de integración de sistemas brindan consultas a los clientes sobre equipos y capacidades que van desde la definición y construcción de celdas hasta la realización de escorrentías. El enfoque de la nueva instalación de 929 m2 (10,000 ft2) "está en brindar una solución completa y personalizada para nuestros clientes", dijo John Lucier, Gerente de Automatización de Métodos.
Automatización integral
Tecnologías como los robots colaborativos están cambiando la forma en que los fabricantes conciben la automatización. Estes alienta a los fabricantes a aprovechar el poder de los datos generados y recopilados por un sistema de automatización.
El análisis de datos puede contribuir a otros aspectos de la producción, incluida la calidad del producto, la gestión de herramientas, el flujo de materiales y la logística. Al implementar la tecnología robótica, los fabricantes deberían adoptar "un enfoque más holístico", dijo Estes. "En lugar de simplemente evitar que una persona cargue y descargue una máquina, un fabricante debería preguntar:'¿Puedo hacer algo más con este robot para que esté más relacionado con IOT o Industria 4.0 también?'". Los robots y los sistemas de automatización no han sido apreciados. capacidades, dijo:"Incluso nosotros, como proveedores de OEM, estamos aprendiendo todos los días cuánto más capaces podemos hacerlos".
¿Qué hace que un robot sea colaborativo?
El término "robótica colaborativa" se usa con frecuencia para describir cualquier situación en la que la acción del robot se controla para acomodar a los trabajadores humanos. En realidad, las posibles relaciones entre trabajadores y robots varían mucho según el robot y la aplicación.
Las normas ISO 10218-1 y 10218-2, "Estándares de seguridad para aplicaciones de robots industriales", se publicaron en 2011. Enumeran los requisitos para el diseño seguro, las medidas de protección y la aplicación de robots industriales. Los estándares definen cuatro modos diferentes de interacción relacionada con la seguridad entre el personal del taller y los robots.
Un modo es la capacidad de realizar una parada supervisada de seguridad. Los sensores monitorean un área predeterminada alrededor de un robot y el movimiento del robot se detiene cuando un humano ingresa a esa área. Este nivel de monitoreo de seguridad es satisfactorio cuando la intervención humana es mínima, aunque las interrupciones frecuentes pueden disminuir la productividad. Un segundo modo implica el guiado manual, en el que un operador le enseña a un robot a seguir una ruta deseada agarrando el brazo del robot y moviéndolo a los puntos deseados en la ruta mientras registra los puntos con un dispositivo de enseñanza. Un sensor de par de fuerza en el robot reconoce la guía manual del operador. El sensor no actúa como un sistema de seguridad y, fuera del modo de enseñanza, el robot debe tener otros dispositivos o sistemas para garantizar una interacción segura con los humanos.
En el modo de monitoreo de velocidad y separación, un sistema de visión detecta humanos en una zona de seguridad designada alrededor del robot. A medida que disminuye la separación entre el robot y el ser humano, el robot se ralentiza gradualmente; a cierta distancia, el movimiento del robot se detiene. Luego, cuando el ser humano sale de la zona de seguridad, el robot vuelve a trabajar a velocidad normal. Este modo de seguridad gradual ayuda a mantener la productividad incluso con las intervenciones de los trabajadores.
El cuarto modo de colaboración permite la actividad lado a lado de robots y humanos y elimina la necesidad de protecciones y jaulas. Los robots descritos se denominan robots limitadores de potencia y fuerza. Cuando los sensores detectan fuerzas anormales en el robot, como las generadas al contactar a un trabajador, el robot reduce la velocidad, se detiene o retrocede inmediatamente. Estos robots descritos se denominan robots limitadores de potencia y fuerza. Cuando los sensores detectan fuerzas anormales en el robot, como las que se accionan al contactar a un trabajador, el robot reduce la velocidad, se detiene o retrocede de inmediato. Estos robots suelen ser más pequeños y menos potentes que los robots industriales tradicionales, y también tienen formas redondeadas y juntas cerradas para evitar lesiones por pellizcos.
En 2016, ISO emitió la especificación técnica ISO/TS 15066 que agrega detalles y aclaraciones a los estándares ISO 10281-1 y 2. TS 15066 define los robots colaborativos como aquellos diseñados para la interacción directa con un ser humano en un espacio de trabajo colaborativo donde el ser humano y el robot pueden realizar tareas simultáneamente. La especificación detalla la cantidad de fuerza que un robot puede infligir a un humano sin causar dolor ni lesiones. Los niveles de fuerza se determinaron mediante pruebas de impacto en áreas específicas del cuerpo humano. Aún así, es fundamental realizar evaluaciones de riesgo de la operación que se realiza y las piezas y herramientas involucradas en una aplicación específica para garantizar la seguridad absoluta.
Sistema de control de automatización
- Robots colaborativos:¿se están generalizando?
- Nuevos robots:económicos y de primera línea
- Robots colaborativos y su impacto en la fabricación
- Trabajar y crecer con robots colaborativos
- Conceptos básicos de Cobot:5 diferencias entre robots colaborativos y robots tradicionales
- Parada de emergencia y controladores de parada
- ¿Por qué usar un robot colaborativo?
- Cobots y fabricación:3 formas en que la automatización colaborativa puede ayudar a su tienda
- Cobots y el futuro de la robótica avanzada en la fabricación
- El futuro de las pruebas:automatización y robots colaborativos
- ¿Qué son los cobots (robots colaborativos)?