El proyecto PASSARO de Clean Sky 2 apunta a una cabina compuesta OOA de un solo disparo
El proyecto PASSARO (Capacidades para pruebas estructurales y funcionales innovadoras de AeROstructures) tiene como objetivo desarrollar nuevos materiales multifuncionales, que integran aislamiento acústico y resistencia al impacto de alta energía, y soluciones de inspección para una nueva cabina compuesta fabricada de una sola vez y complementada con fuera de autoclave (OOA). tecnologías como la consolidación in situ de compuestos termoplásticos y la infusión de resina líquida. Esta cabina compuesta fue desarrollada por Airbus Defence and Space (Madrid, España) durante Clean Sky 1, basada en el avión C295. El proyecto también tiene como objetivo la automatización de los procesos de fabricación, así como nuevos enfoques de prueba basados en conceptos de la Industria 4.0 y el desarrollo de conceptos ergonómicos avanzados que promueven la comodidad del piloto y una interfaz hombre-máquina mejorada.
El proyecto PASSARO, parte de la plataforma Airframe de Clean Sky 2, comenzó en julio de 2016 con una duración total de 48 meses. Está compuesto por once socios de Portugal y España que trabajan en estrecha colaboración con Airbus Defence and Space.
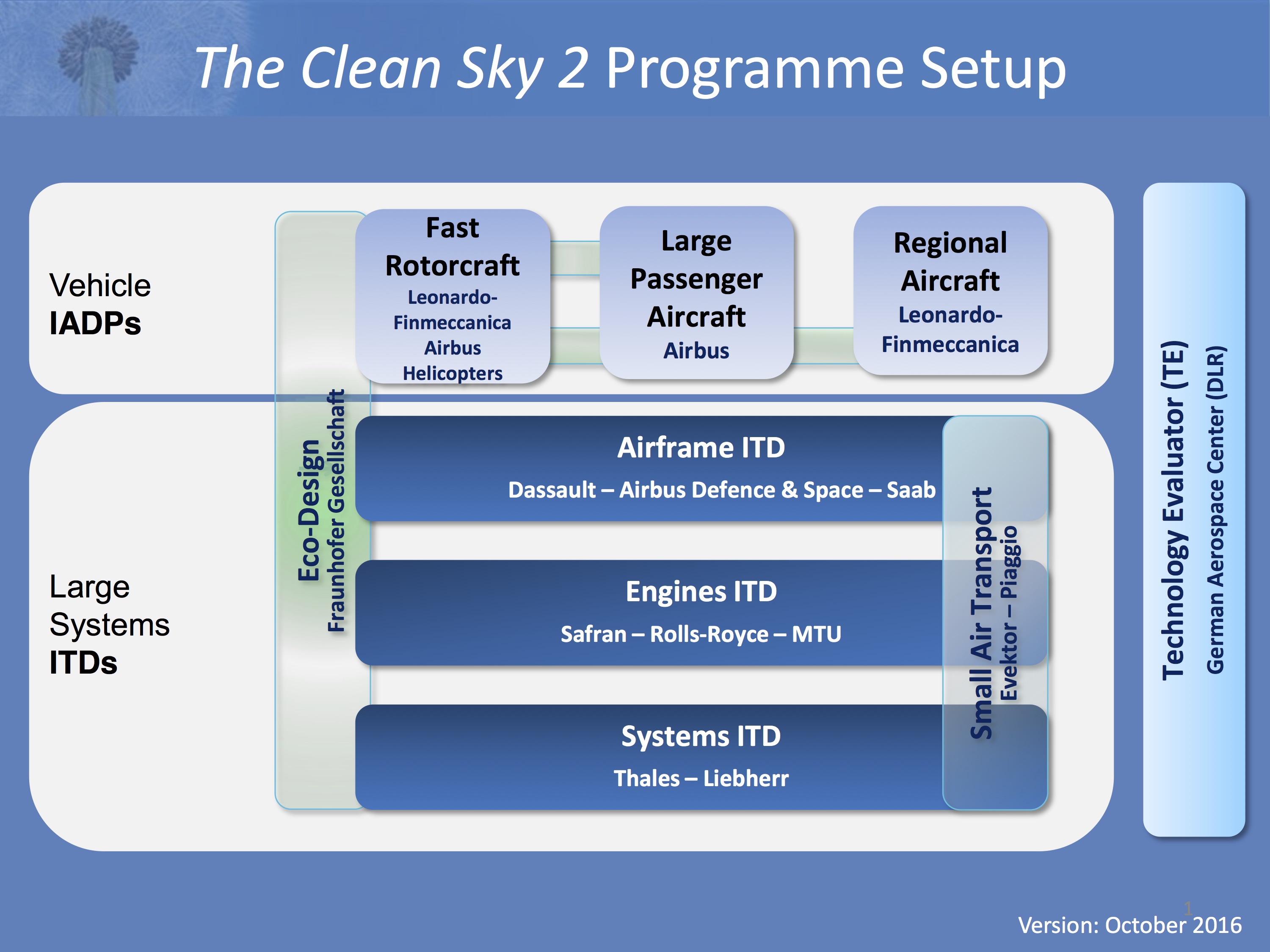
FUENTE:Clean Sky 2
Sinergias con el proyecto regional MOSHO de Portugal
Muchos proyectos Clean Sky 2 (CS2) comparten sinergias con iniciativas regionales de miembros de la UE (por ejemplo, CORAC en Francia). El proyecto PASSARO ha promovido actividades complementarias con iniciativas nacionales portuguesas de I + D. El proyecto MOSHO (Soluciones avanzadas para materiales de impacto, reparación de aeroestructuras compuestas y su monitorización) complementa las actividades de PASSARO en las que participan algunos de los socios y cuenta con el apoyo de ADS (Airbus Defence and Space) como coordinador de Clean Sky 2 para el ITD de fuselaje. El proyecto desarrollará e integrará soluciones avanzadas para la reparación de aeroestructuras compuestas.
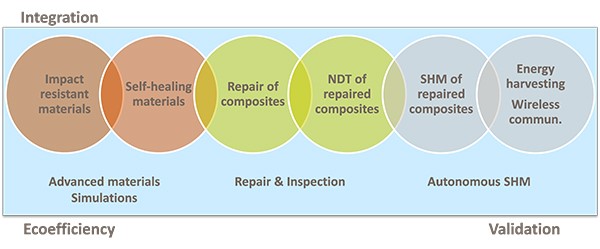
Figura 3:Alcance técnico del proyecto MOSHO FUENTE: https://www.cleansky.eu/commissioner-moedas-meets-passaro-at-isq
Los robots colaborativos de PASSARO reducen el tiempo del ciclo de colocación manual hasta en un 70%
Como parte de los objetivos del proyecto PASSARO de investigar y desarrollar cómo emplear robots colaborativos en la fabricación de compuestos, el proyecto OPTIMAL desarrolló una solución automatizada práctica y rentable para reemplazar la colocación manual tradicional, utilizando materiales calificados.
Tradicionalmente, la fabricación de componentes compuestos utilizando preimpregnado es esencialmente una actividad artesanal, pero se están dando pasos hacia la automatización. Durante la última década, han surgido varias soluciones de laminado automatizado para piezas geométricas relativamente simples. Estas soluciones suelen ser bastante caras y, por lo general, exigen que las fábricas se diseñen desde cero para su instalación. Por lo general, requieren entornos especiales en forma de celdas aisladas con sistemas de seguridad dedicados. Como alternativa, los robots colaborativos (cobots) podrían integrarse en los flujos de trabajo de fabricación existentes para automatizar algunas tareas y mejorar la productividad sin cambiar drásticamente el entorno circundante.
Los robots industriales son rápidos, fuertes y tienen una precisión y repetibilidad excepcionales, pero se desarrollan con el único objetivo de optimizar el resultado final. En comparación, los cobots son más lentos, menos precisos y manejan cargas útiles más pequeñas, pero tienen lo que se necesita para automatizar tareas simples, especialmente junto con humanos, a un costo considerablemente menor. Los cobots tienen sensores de carga que detectan los impactos más pequeños y se detienen de manera segura.
El objetivo de OPTIMAL al desarrollar tecnologías de cobot es mejorar su propia capacidad, y la de otras empresas, para ofrecer productos más repetibles, de mayor calidad, en grandes cantidades ya menor precio.
Dentro del paquete de trabajo 10 del proyecto PASSARO, se desarrollaron tres pasos principales utilizando robots colaborativos:
- Recogida y clasificación de capas, directamente desde el cortador de capas automático;
- Peeling de capas usando una celda dedicada;
- Colocación y apilado de capas en una herramienta.
Para implementar estas actividades, se desarrolló una celda que recibe capas preimpregnadas del cortador de capas y las pela y apila automáticamente en un molde.
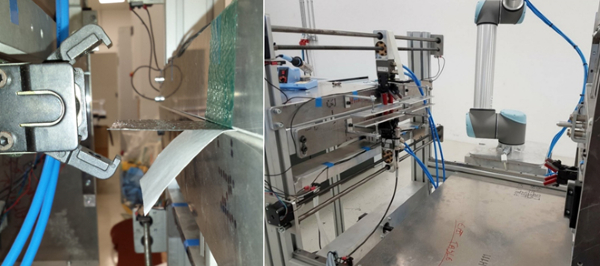
Robots colaborativos utilizados para la fabricación de composites en el proyecto PASSARO. FUENTE: Grupo ISQ
El brazo robótico completa las tareas de posicionamiento y apilado mediante ventosas especiales para la manipulación del preimpregnado. El pelador es una máquina más compleja, que utiliza aire comprimido para pelar el preimpregnado, que está protegido por dos revestimientos, típicamente un plástico y un papel, o simplemente por dos plásticos. El concepto de peeling se basa en el hecho de que diferentes materiales tienden a vibrar a diferentes frecuencias cuando se aplica el mismo estímulo. Las diferentes frecuencias de vibración producen bolsas de aire entre el preimpregnado y las capas de recubrimiento. El resonador de placa ajusta la amplitud de vibración para diferentes materiales. Este prototipo podría alcanzar tasas de pelado con un éxito cercano al 100% para materiales específicos y una precisión de apilado de ± 0,5 mm, en cada uno de los dos grados de libertad en el plano del molde, y ± 0,1º en rotación.
El enfoque modular adoptado para este sistema lo hace independiente de las dimensiones de las capas. El ancho se cubre agregando más módulos de pelado paralelos y el largo ajustando el rango de apertura del pelador. Esta tecnología, en comparación con un operador humano, ofrece una clara mejora en la precisión del proceso, la repetibilidad y especialmente el tiempo de ciclo, con reducciones de hasta el 70%.
Autores:António Reis, Nicole Cruz, Marco Neves (OPTIMAL) y Rúben Buelga Sanchez (ADS). Para mas informacion contacte:
INEGI
Campus da FEUP
Rua Dr. Roberto Frias, 400
4200-465, Oporto, Portugal
Tel:(+351) 229 578 710
Correo electrónico:[email protected]
Resina
- Solvay expande la capacidad de compuestos termoplásticos
- Proyecto Toray en holandés para tanques de hidrógeno líquido para aviones
- El proyecto Clean Sky 2 FUSINBUL desarrolla mamparos de presión de fibra de carbono a gran escala
- La importancia de la selección de resina
- El proyecto Clean Sky 2 FRAMES avanza en la simulación de calentamiento de compuestos termoplásticos AFP con lámpara de destellos de xenón
- Clean Sky 2 publica los resultados del proyecto
- El especialista alemán en compuestos INVENT colabora en SUSTAINair para aumentar la circularidad de las aeronaves
- Costillas Wing of Tomorrow:consolidación OOA, termoplástico, de un solo uso
- El proyecto Clean Sky 2 IMCOLOR desarrolla un proceso de fabricación integrado para el diseño de productos ligeros
- El consorcio busca soluciones para estructuras compuestas termoplásticas de fibra de carbono
- Fabricación rápida de espacios en blanco compuestos a medida