Impresión magnética en 3D la próxima generación de compuestos personalizados
Fortify (Boston, Ma., EE. UU.) Se fundó en 2016, sobre la base de la investigación de impresión 3D compuesta por Josh Martin (CEO de Fortify) y Randall Erb, director del DAPS Lab en Northeastern University en Boston. (Erb también es cofundador de Boston Materials y Fortify). Su objetivo era permitir la producción rápida de compuestos con microestructuras optimizadas. La tecnología Fluxprint patentada que desarrollaron utiliza campos magnéticos y procesamiento de luz digital (DLP), pero con sistemas de resina altamente llenos, para producir microestructuras personalizadas en piezas compuestas impresas en 3D de alta resolución.
Fluxprint frente a DLP
Tanto la DLP como la estereolitografía (SLA) se consideran actualmente las tecnologías de impresión 3D que ofrecen la mayor complejidad y precisión de piezas. Ambos se basan en el uso de luz, generalmente ultravioleta (UV), para curar una resina fotosensible que generalmente comprende monómeros epoxi o acrílicos y metacrílicos. La luz se dirige digitalmente para que brille sobre la resina en el tanque del sistema para crear las formas o patrones de cada capa. La plataforma de fabricación se mueve después de cada capa, lo que permite que se imprima la siguiente capa y proceda a una pieza sólida terminada.
Los proyectores DLP y SLA se remontan al comienzo de la impresión 3D en la década de 1980. Las impresoras DLP tienden a ser más grandes porque albergan el proyector de luz real. La mayoría de las máquinas SLA y DLP utilizan polímeros termoendurecibles, pero EnvisionTEC fabrica una impresora que también puede utilizar termoplásticos. Ambos han utilizado tradicionalmente polímeros puros sin refuerzo.
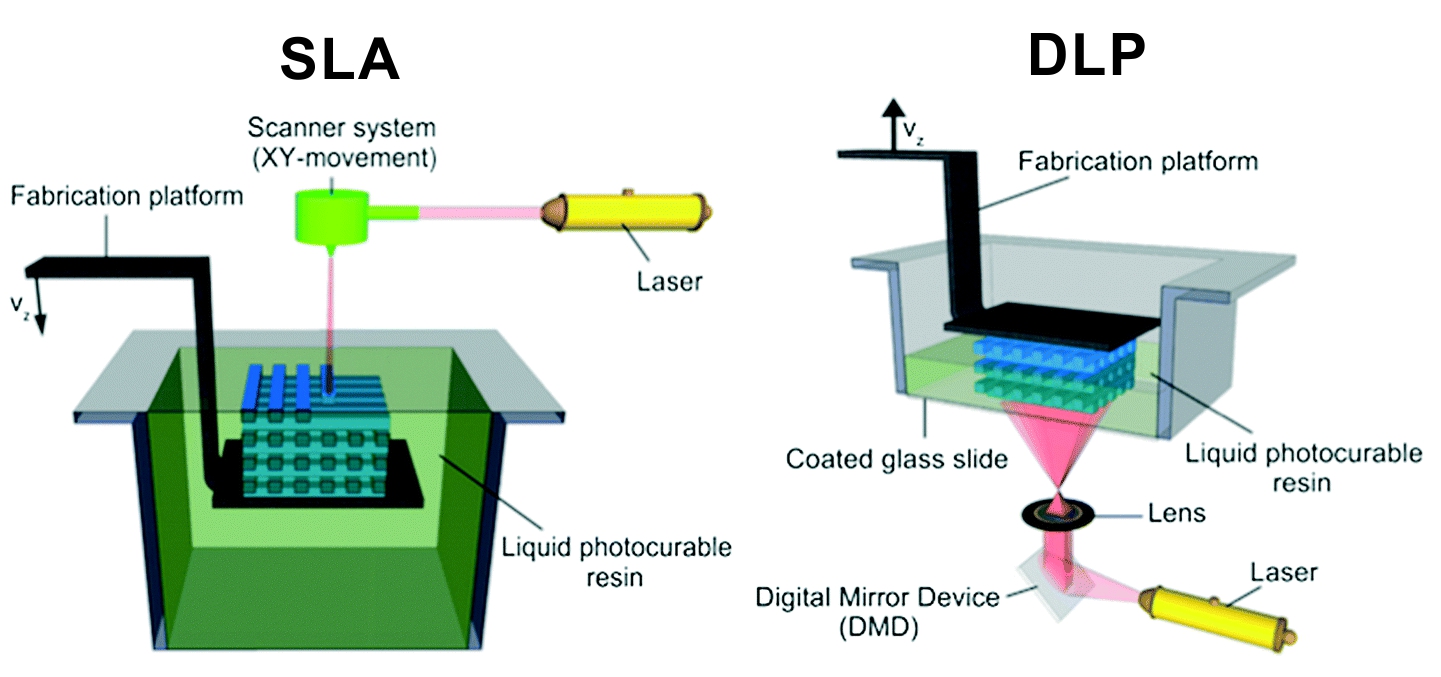
“Las plataformas DLP son capaces de alcanzar tasas de producción y calidad suficientes”, dice el CEO de Fortify, Josh Martin, “pero las propiedades mecánicas siempre han sido un desafío. Nuestra tesis principal es que un cambio radical en el rendimiento no se logrará únicamente con la química de los polímeros. Sin embargo, explotar las propiedades únicas de los compuestos en la industria de los aditivos de alta resolución cambiará las reglas del juego ”.
Explica que Fortify se especializa en el curado UV de resinas técnicas altamente rellenas utilizando aditivos únicos y controlando la orientación de estos aditivos que mejoran las propiedades en la impresión. Los rellenos incluyen fibras de vidrio, carbono y cerámica, así como partículas. Las resinas técnicas incluyen acrilato y metacrilato (PMMA) o epoxi, catiónico, que según Martin son más convencionales para la industria de los recubrimientos. Los principales fabricantes de resinas de todo el mundo (BASF, DSM, Dupont y otros) están invirtiendo mucho para mejorar las propiedades de sus materiales aditivos. Fortify puede seleccionar lo mejor de estos avances para agregar su tecnología de refuerzo.
El control de la orientación de la fibra se logra mediante el uso de un campo magnético. A medida que Fortify 3D imprime una pieza utilizando su tecnología Fluxprint, las fibras se alinean magnéticamente vóxel por vóxel para cumplir con los requisitos de carga de la pieza. (Vea el proceso en acción en el video de arriba). Para materiales de refuerzo no magnéticos, como partículas y fibras de cerámica y vidrio, se utilizan técnicas patentadas de etiquetado magnético para recubrir los rellenos de una manera que los hace magnéticamente sensibles y compatibles con la resina.
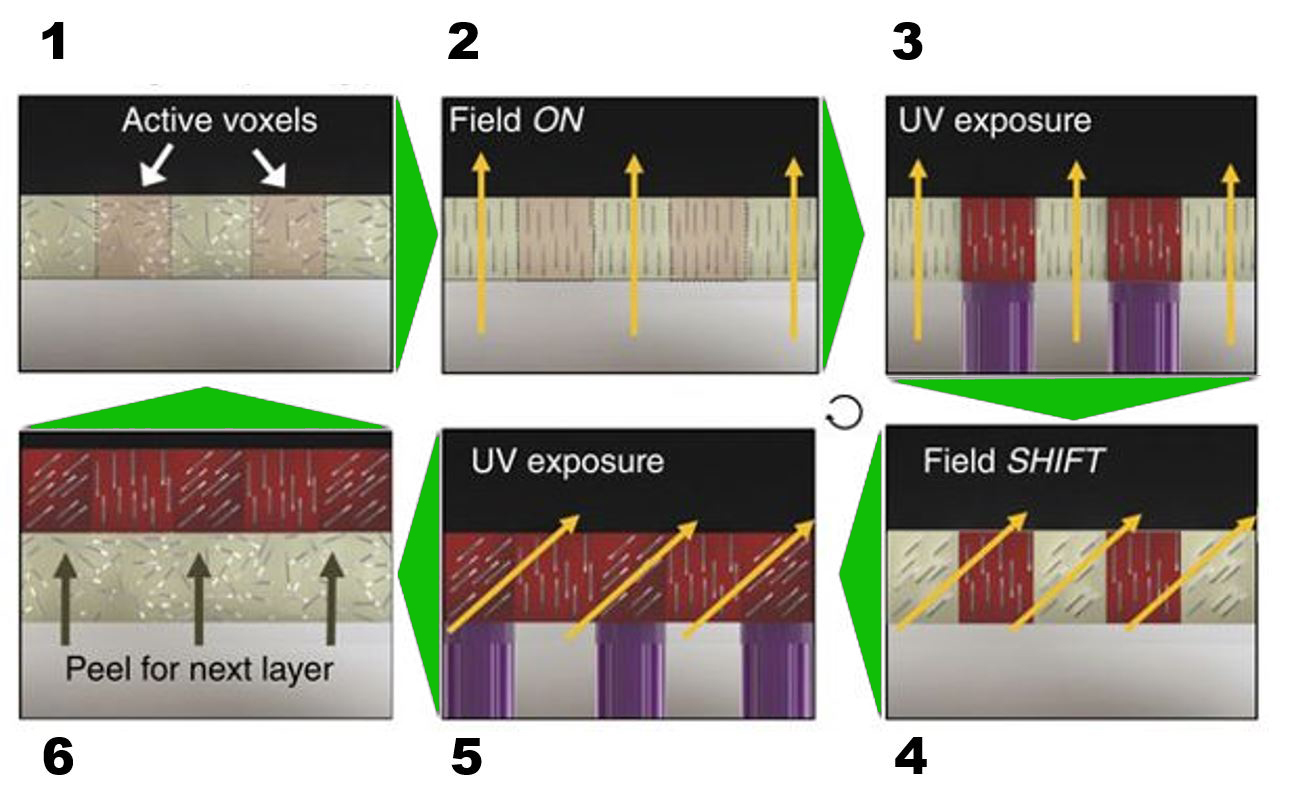
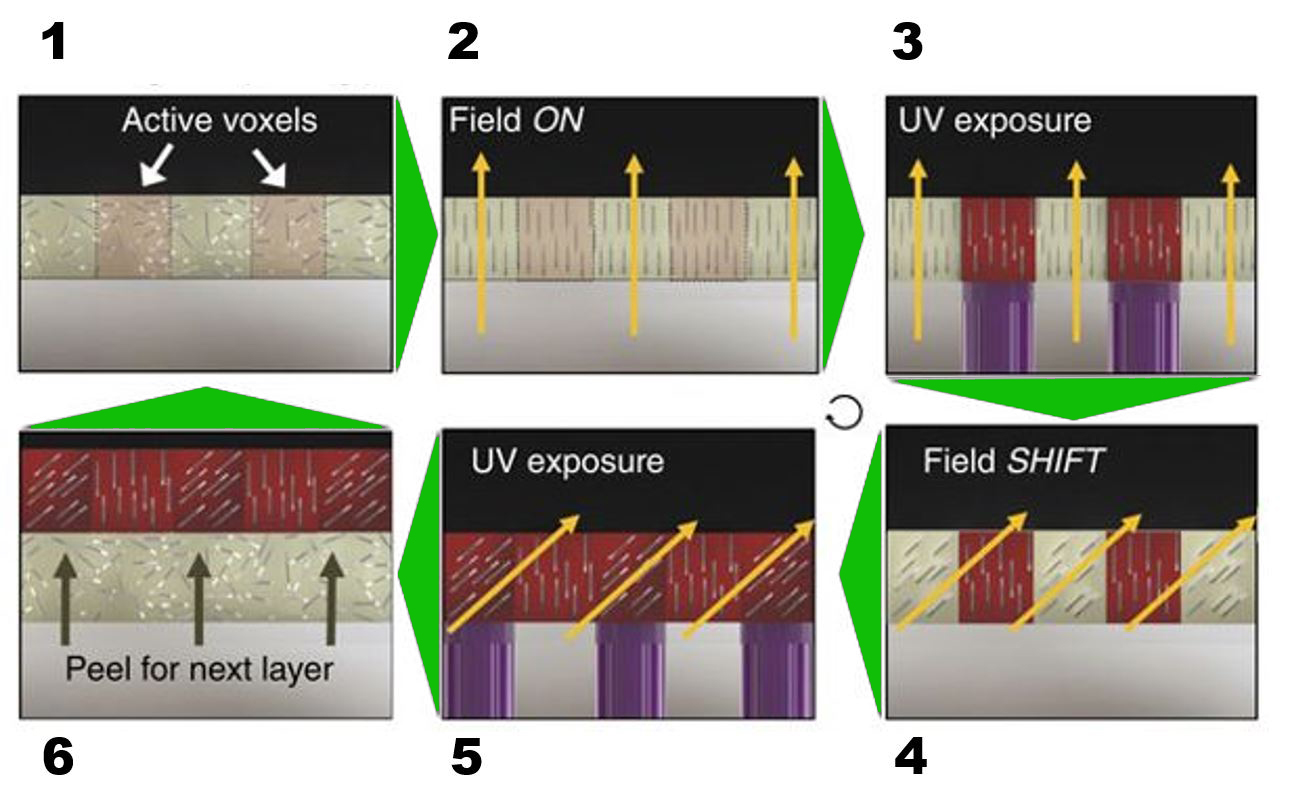
El proceso de Fluxprint se muestra en la imagen de arriba y se describe a continuación:
- Se suministra una capa de material de alimentación al área de construcción con refuerzo alineado al azar.
- Se aplica un campo magnético para alinear el refuerzo.
- Los vóxeles activos se exponen a la luz ultravioleta, lo que fija la orientación del refuerzo en esos vóxeles (que ahora se muestran en rojo).
- El campo magnético se desplaza para establecer una nueva orientación de refuerzo.
- Repita el paso de exposición a los rayos UV para fijar la orientación del siguiente conjunto de vóxeles (repita según sea necesario).
- La placa de construcción se ajusta para traer la matriz de material de alimentación sin curar para la siguiente capa de impresión.
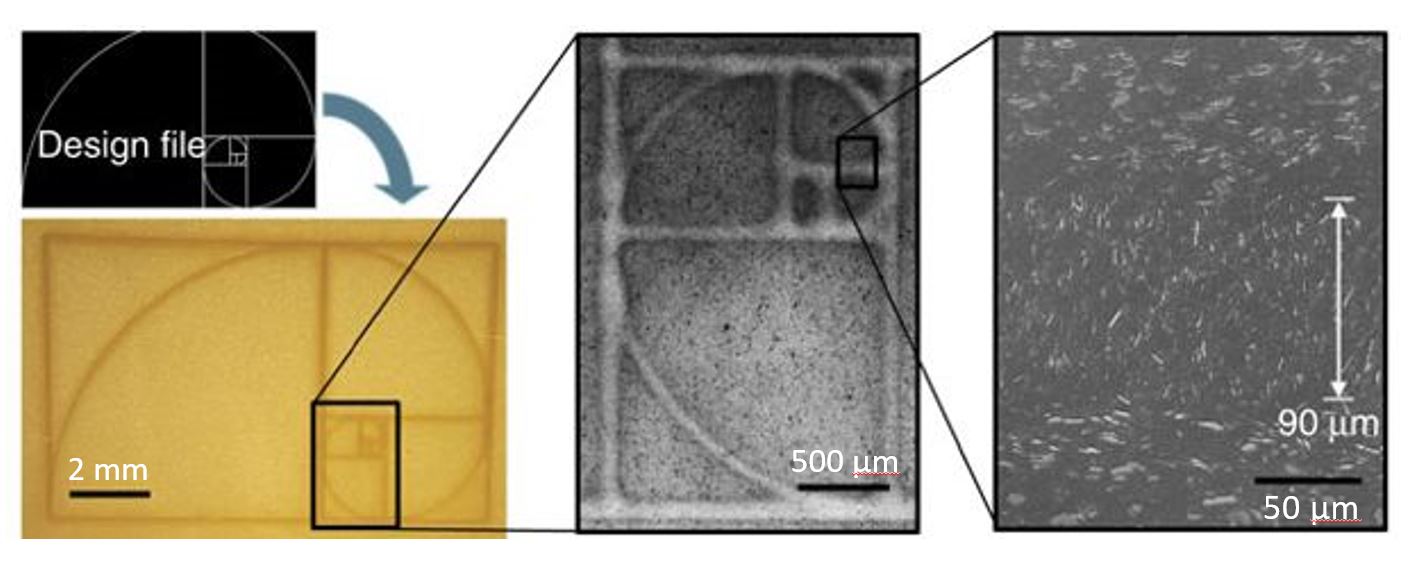
La tecnología Fluxprint permite el control de nivel de voxel sobre la orientación de la fibra durante el proceso de impresión. Fuente | "Diseño de arquitecturas de refuerzo de compuestos bioinspiradas mediante impresión magnética 3D" por Joshua J. Martin, Brad E. Fiore y Randall M. Erb, Nature Communications volumen 6, número de artículo:8641 (2015).
¿Por qué voxel por voxel?
“Cada geometría tiene estados de deformación y tensión únicos”, explica Martin. “La mayoría de los compuestos se fabrican a mano para dar cuenta de esto. Estamos digitalizando el proceso. Por ejemplo, si puede reforzar adecuadamente un marco de UAV, puede usar menos material. Cualquier aplicación que trabaje contra la gravedad se beneficiará fundamentalmente de esto ".
La impresión vóxel por vóxel también es inherentemente de alta resolución. "Este es el proceso de fabricación de compuestos de mayor resolución hasta la fecha", dice Martin, y señala que el modelado de deposición fundida (FDM), donde el filamento de plástico reforzado con fibra molido o no reforzado se funde y se deposita en una cama de impresión, tiene una resolución de cientos. de micrómetros, mientras que el de Fluxprint está dentro de decenas de micrómetros. “Entonces, esa es una mejora de orden de magnitud, que ingresa al territorio más allá de lo que se percibe a simple vista. Este tipo de resolución es muy importante para una amplia variedad de piezas de uso final ".
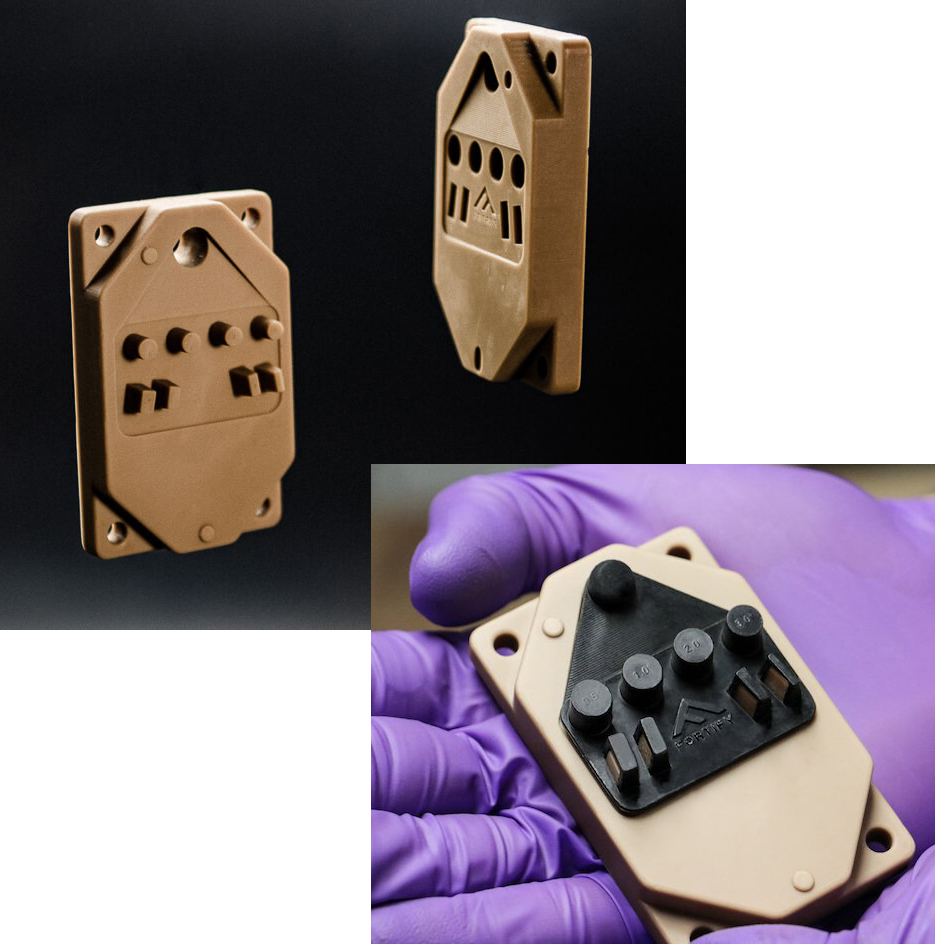
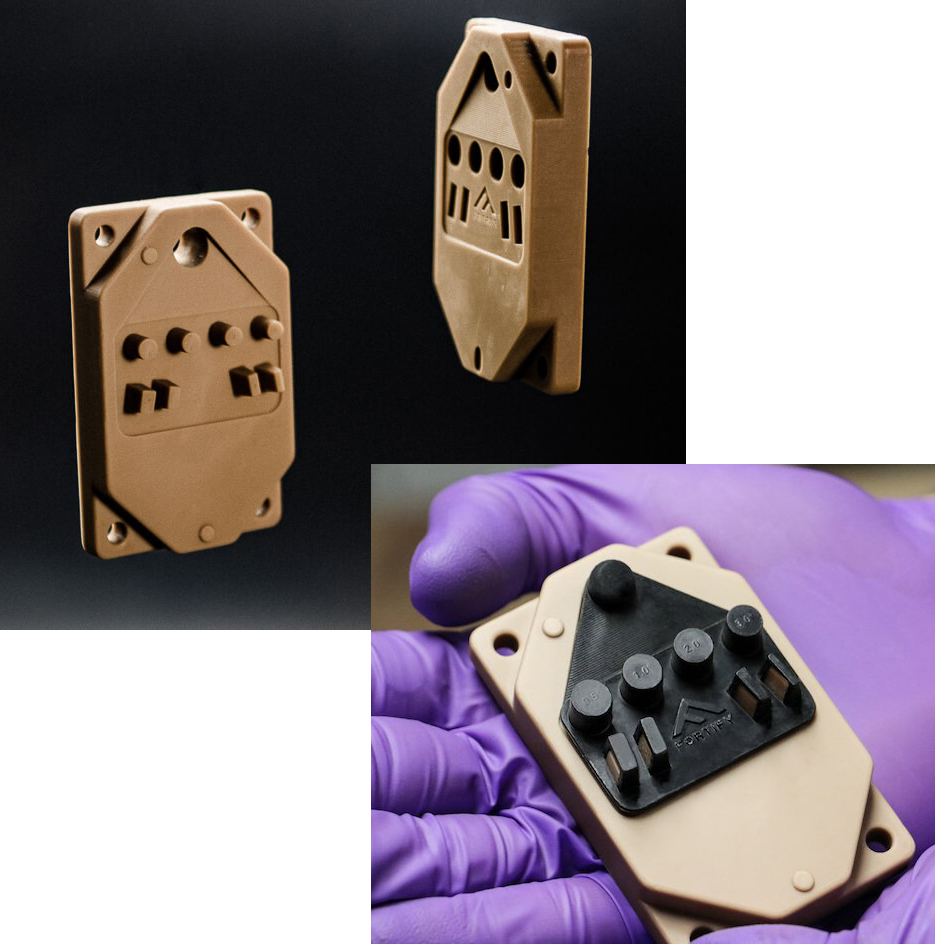
La tecnología de impresión 3D magnética Fluxprint de Fortify puede orientar las fibras para reforzar las proyecciones de "clavijas" en las herramientas de moldeo por inyección. Fuente | Fortificar.
“Ofrecemos herramientas de moldeo por inyección que son significativamente más baratas que el metal mecanizado tradicionalmente, se pueden entregar en una fracción del tiempo y brindan características que las prácticas de mecanizado convencionales no podrían lograr”, continúa Martin. “Un cliente iteraría a través de 12 diseños diferentes por año mecanizados a partir de aluminio. Hemos reducido significativamente su tiempo de comercialización, produciendo más de una docena de diseños en varios meses. Ahora pueden pasar del diseño a las piezas en el estante en cuestión de semanas ". Otro beneficio es la capacidad de reforzar las proyecciones, denominadas "clavijas". Estas extrusiones de alta relación de aspecto a menudo se salen. El refuerzo evita eso, mientras mantiene tolerancias estrictas.
Lea más sobre los beneficios de Fortify en herramientas de moldeo por inyección en la revista hermana de CW, Additive Manufacturing.
Materiales abiertos, nuevos desarrollos
Fortify persigue un enfoque de materiales abiertos. "No queremos limitar la capacidad de nuestros clientes para el crecimiento y la exploración dentro de aditivos", explica el vicepresidente de aplicaciones de Fortify, Karlo Delos Reyes. "Garantizamos a nuestros clientes flexibilidad y los mejores materiales disponibles adoptando la innovación abierta".
“Nos asociamos con grandes fabricantes de polímeros y adaptamos la química de la superficie de los aditivos”, dice Martin. Señala que cada relleno tiene sus pros y sus contras en cuanto a resistencia al desgaste, rendimiento a temperatura, etc. “Para las fibras, la longitud varía de unos pocos µm a unos pocos mm, dependiendo de la aplicación. Cuando necesitamos una resolución de superficie, utilizamos un mayor porcentaje de aditivos de menor longitud. Donde podemos permitirnos una superficie más rugosa, pero queremos optimizar la resistencia a la tracción, por ejemplo, usamos aditivos de fibra más largos ”.
Una de las estrategias de Fortify es asociarse con líderes de la industria y proveedores para aprovechar la experiencia y permitir la polinización cruzada de ideas. Fortify anunció recientemente una asociación con DSM Additive Manufacturing (Hoek van Holland, Países Bajos y Elgin, Illinois, EE. UU.) Para desarrollar materiales compuestos de alto rendimiento que se utilizarán en los sistemas de impresión de Fortify para lograr un mayor rendimiento mecánico y de temperatura. "Ampliarán nuestra paleta de resinas", dice Martin, "y estamos entusiasmados de trabajar con ellos para desarrollar resinas de vanguardia".
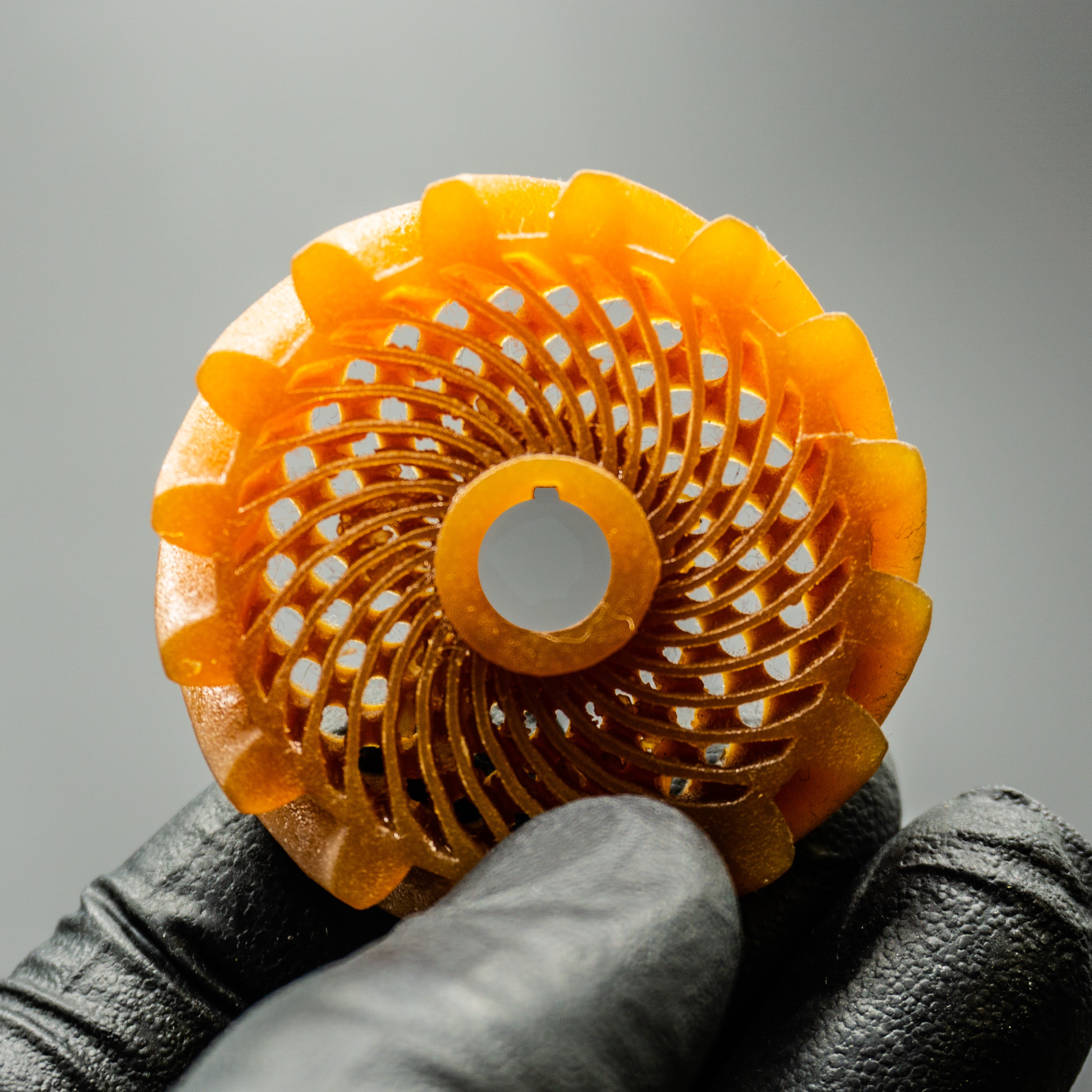
Pieza compuesta reforzada con fibra de vidrio fabricada con Fluxprint. FUENTE | Fortificar.
Aplicaciones y refuerzo en la dirección Z
Fluxprint todavía imprime por capas. Entonces, ¿es posible lograr un refuerzo en la dirección z? "Si está imprimiendo fibras de 2 milímetros de largo, no puede colocarlas en la dirección z", dice Martin. "Pero podrías ser más corto fibras en orientación z. Estamos analizando varias escalas de longitud y vemos que eso se desarrollará en el futuro para optimizar la transferencia de carga ".
Fortify ya está produciendo piezas para vehículos aéreos no tripulados, incluidas hélices, y ve muchas más aplicaciones de este tipo en la industria aeroespacial. “Tenemos un área de construcción pequeña, por lo que nos estamos enfocando en aplicaciones en las que podemos cumplir fácilmente con volúmenes de piezas más pequeños”, dice Martin. "Este es un ecosistema maduro, pero ofrecemos un nuevo nivel de rendimiento en propiedades mecánicas a altas temperaturas y tolerancias". Cita poder mejorar la temperatura de deflexión de calor de una pieza y explica que hay docenas de piezas bajo el capó en la industria automotriz que necesitan proporcionar resistencia y rigidez mientras se exponen a temperaturas de 160 ° C. "Estas piezas con geometrías complejas se prestan bien a la impresión 3D con nuestra tecnología. En comparación con el método actual de moldeo y mecanizado de piezas de PEI (polieterimida), ofrecemos un mayor rendimiento, un tiempo de entrega más corto y un alto potencial de menor costo . ”
El utillaje también es un mercado actual, que incluye matrices, plantillas y accesorios para moldeo por inyección. “Nuevamente, nuestras piezas son más rígidas, más fuertes y tienen una mayor resistencia a la temperatura, lo que mantiene la precisión dimensional en servicio”, dice Martin. "Pero su valor real radica en no que requieren un posprocesamiento significativo, como el que se necesita cuando se utilizan máquinas de electroerosión, y sin embargo coinciden con la calidad de los accesorios fabricados con estos métodos tradicionales, incluido el fresado CNC ”.
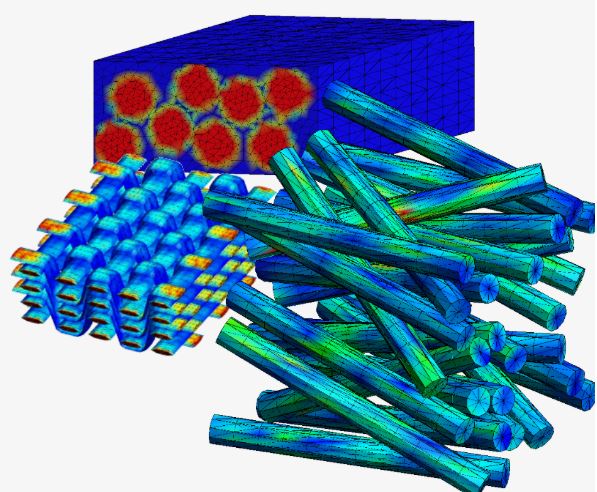
Fuente | Multimecánica
Avanzando en la próxima generación de compuestos multifuncionales y multiescala
Fortify se ha asociado con MultiMechanics (Omaha, Neb., EE. UU.), Un desarrollador de software de simulación y modelado multiescala para materiales avanzados. Esta asociación es interesante por varias razones. En primer lugar, Fortify utilizará el producto estrella de MultiMechanics, MultiMech, para predecir el rendimiento de las piezas y optimizar su diseño y orientación de la fibra antes de que se impriman. Por lo tanto, MultiMech actuará para proporcionar la retroalimentación para el diseño iterativo de ciclo cerrado , lo que permite a los usuarios adaptar y optimizar más rápidamente las piezas compuestas impresas con Flux. Fortify y MultiMechanics también planean integrar MultiMech en INFORM de Fortify software de diseño generativo y control de impresión. Por lo tanto, desde el diseño hasta las pruebas virtuales y la impresión, todas las funciones se controlarán en un solo flujo digital.
Para el segundo punto, es importante comprender lo que ofrece MultiMechanics a través de su software MultiMech:
- Análisis de elementos finitos multiescala , incluido el modelado de un número prácticamente ilimitado de escalas (por ejemplo, nano, micro, capas, laminado, pieza).
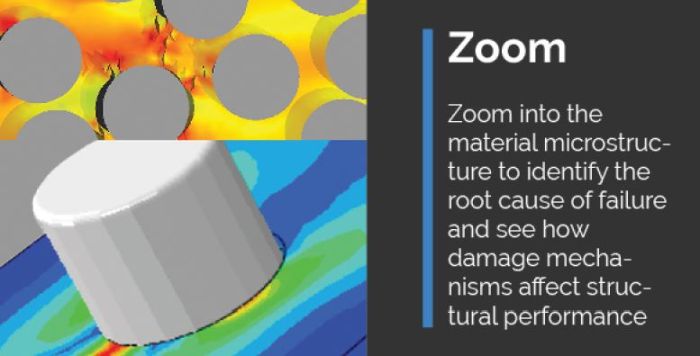
- Generación automática de microestructuras complejas de elementos finitos en 3D y modelado de casi cualquier microestructura de material, incluidas fibras, partículas, huecos, espumas, tejidos, etc.
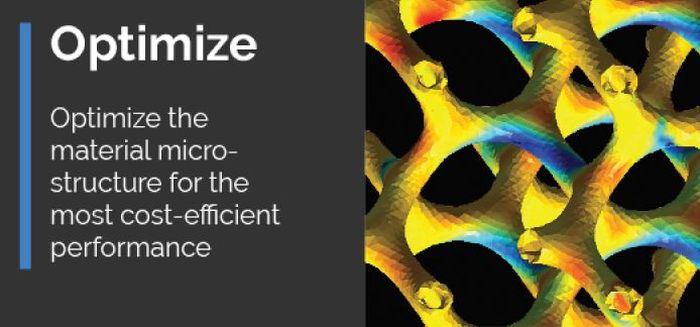
- Modele los efectos de los componentes a microescala, incluido interacciones , fracciones de volumen, distribución y orientación, además de importación p variación inducida por el proceso de programas (por ejemplo, Moldex3D, Moldflow).
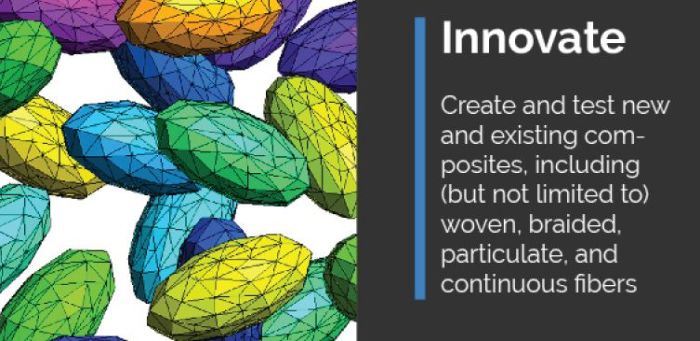
- Analice cómo la variación de fabricación afecta el rendimiento de la pieza y realizar da modelado de magos incluida la transición multiescala de microgrietas a macrogrietas.
Esto se remonta a por qué Martin y Erb comenzaron Fortify en primer lugar. En su artículo de 2015, "Diseño de arquitecturas de refuerzo de compuestos bioinspiradas a través de la impresión magnética 3D", afirman:
Martin y Erb analizan los compuestos naturales que utilizan fibras discontinuas y partículas de refuerzo organizadas en arquitecturas complejas de múltiples escalas para lograr propiedades superiores frente a sus componentes. Un ejemplo dado por Qunfeng Cheng en un Materials Today de 2017 El artículo es nácar en conchas de abulón. Compuesto por un 95% en volumen de aragonito inorgánico y un 5% en volumen de matriz de proteína orgánica, la resistencia a la fractura del nácar es 3000 veces mayor que el de aragonito. Cheng señala que esto muestra un "efecto de amplificación" en las propiedades mecánicas que va mucho más allá de la regla de las mezclas en los compuestos tradicionales .
En los Materiales avanzados de 2018 artículo, "Fabricación aditiva como método para diseñar y optimizar estructuras bioinspiradas", los autores Audrey Velasco-Hogan, Jun Xu y Marc A. Meyers afirman que la estructura jerárquica de materiales como nácar, hueso, bambú y conchas de crustáceos son los que permiten su impresionante combinación de fuerza, módulo, peso ligero, tenacidad y resistencia a la fatiga. Sus partículas / filamentos constituyentes y su matriz están organizados de manera diferente en cada nivel (por ejemplo, nano, micro, meso, macro), variando las propiedades en cada nivel (es decir, un compuesto multiescala). Cuando se combina con interfaces eficientes entre los niveles, esta estructura jerárquica funciona sinérgicamente para mitigar la propagación de grietas y mejorar la resistencia manteniendo la dureza, algo que aún no se ha logrado en cerámica después de aproximadamente un siglo de intentos.
Futuro de los compuestos e INFORM
Este es el futuro de los compuestos:diseñar compuestos jerárquicos con propiedades únicas adaptado para aplicaciones precisas. Y ya está avanzando, rápidamente. Por ejemplo, el Instituto de Estructuras y Diseño del Centro Aeroespacial Alemán (DLR) en Stuttgart también se ha asociado con MultiMechanics comprender cómo el cambio de temperatura afecta la microestructura y el comportamiento del material de compuestos de matriz cerámica (CMC) . Este análisis se considera crucial para la futura producción de componentes CMC de DLR, incluidas boquillas para cohetes y sistemas de protección térmica para vehículos de reentrada, entre otros. “Nuestro trabajo en MultiMechanics durante los últimos diez años se ha dedicado a conectar con precisión el comportamiento microestructural de materiales avanzados al rendimiento general de la pieza y su fabricación ”, Dice el Dr. Flavio Souza, presidente y CTO de MultiMechanics. “MultiMech nos permite modelar grietas microestructurales y determinar cómo afectarían la pieza compuesta en general”, afirma Neraj Jain, líder del grupo en el Departamento de Estructuras y Compuestos Cerámicos de DLR. “La integración eficiente de MultiMech con nuestras otras herramientas FEA como Abaqus y ANSYS aumenta nuestra productividad y nos acerca a nuestro objetivo de optimizar los materiales CMC virtualmente . "
Una vez que estos compuestos se han optimizado virtualmente, se imprimen con MultiMech integrado en el software INFORM de Fortify, que ya está orientado hacia arquitecturas orgánicas con carga optimizada a través de su columna vertebral de diseño generativo . . (Tenga en cuenta que la unidad de negocio de materiales compuestos de Solvay también ha invertido en tecnología de impresión 3D y multimecánica).
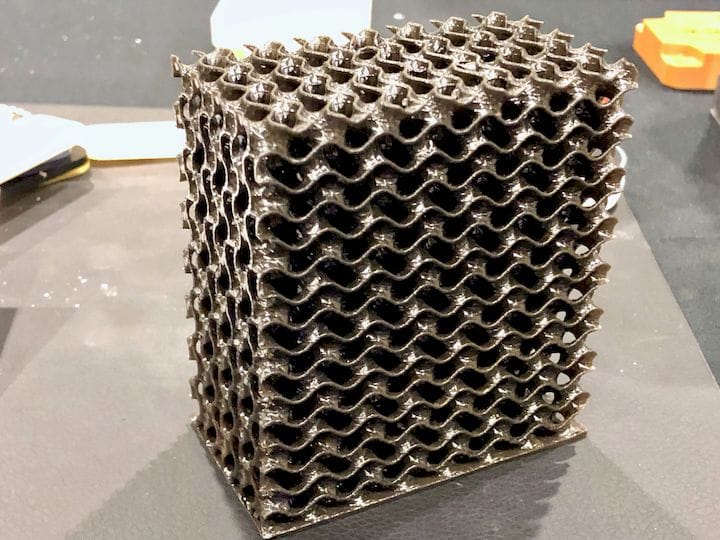
Celosía reforzada con fibra, diseño proporcionado por nTopology. Fuente | Fortificar.
"INFORM utiliza algoritmos avanzados para optimizar la orientación de la fibra para cada pieza ”, explica Martin. “Donde tradicionalmente, el flujo de trabajo de impresión 3D comienza con STL para cortar el diseño, el nuestro comienza con FEA (un modelo con tensión y deformación) y luego decide en qué vóxeles separar ese diseño modelado y cómo orientar las fibras. Avanzamos a través de iteraciones, alineando las fibras con vectores de campo de tensión / deformación, y luego simulamos cómo se comportará esa impresión y usamos esos datos para refinar y optimizar el diseño, logrando diseño generativo microestructural . ”
Solo el comienzo
Tenga en cuenta que estos futuros compuestos incluyen una variedad de materiales. El Laboratorio de Investigación Naval (NRL, Arlington, Va., EE. UU.) Está desarrollando CMC utilizando una matriz cerámica con un refuerzo cerámico secundario a través de nanopartículas y / o filamentos. Estos CMC también pueden usar refuerzo de fibra continua. En otras palabras, se pueden usar diferentes componentes y arquitecturas en cada nivel para obtener la dureza mejorada y las propiedades eléctricas y térmicas personalizadas requeridas (por ejemplo, en hipersónica, lea más en mi artículo de julio de 2019 sobre nanocompuestos).
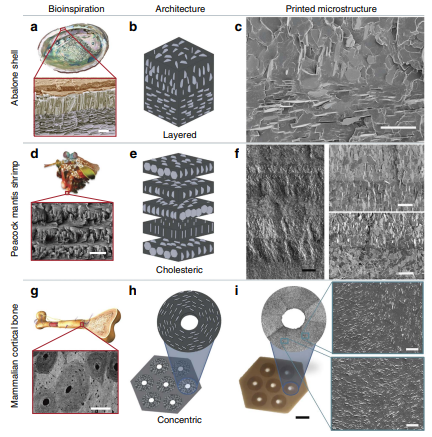
FUENTE | Figura 3, "Diseño de arquitecturas de refuerzo de compuestos bioinspirados mediante impresión magnética 3D" por Joshua J. Martin, Brad E. Fiore y Randall M. Erb, Nature Communications, volumen 6 (2015).
También se están imprimiendo y probando compuestos jerárquicos utilizando tintas epoxi reforzadas y matrices de polímeros termoplásticos. Esta es quizás la mayor ventaja para Fortify como startup. No solo se está preparando para los compuestos del futuro, sino que ya los está diseñando y produciendo. Y aunque lo que ya ha logrado es impresionante, es solo el comienzo.
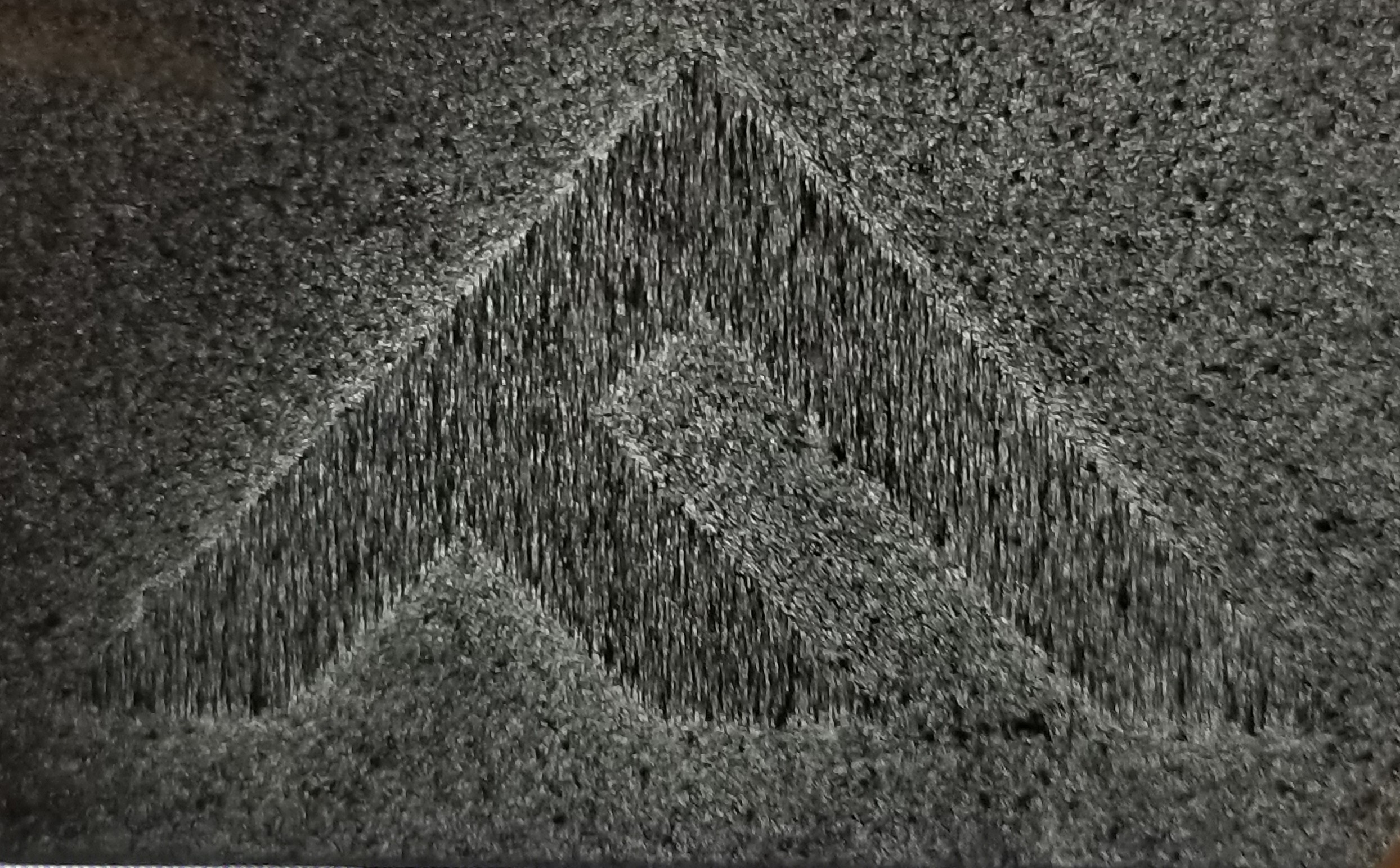
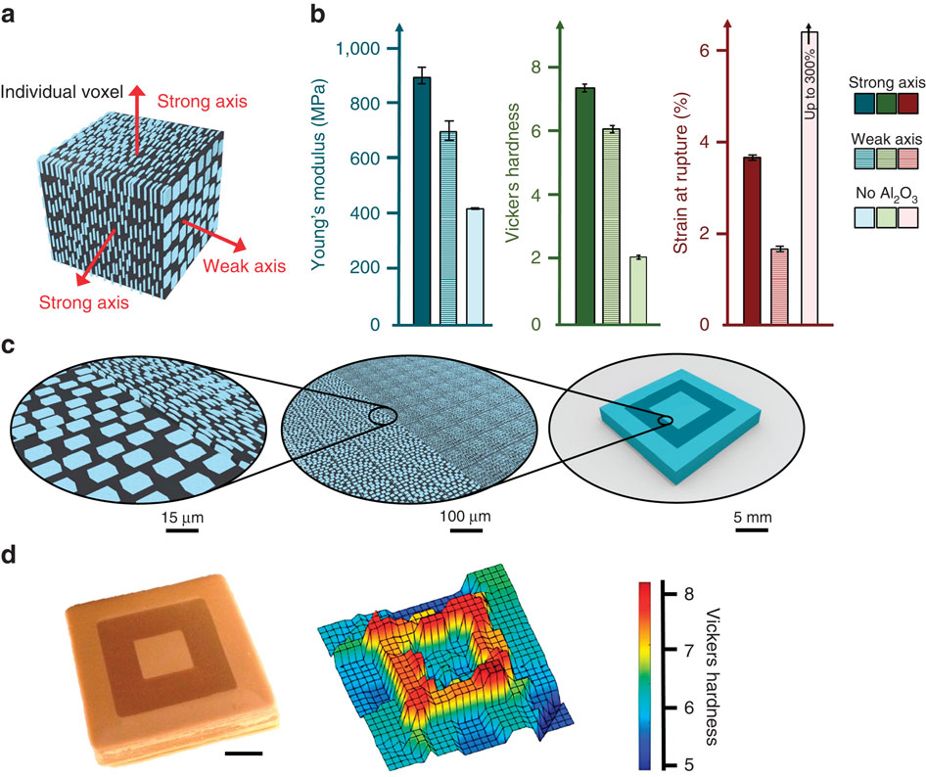
Resina
- Los 3 pasos básicos de la impresión 3D
- ¿Podría la impresión 3D multimaterial ser el siguiente paso para AM?
- El ABC de la impresión 3D
- La evolución de la impresión 3D
- Colegios comunitarios:formación de la próxima generación de fabricantes
- Día de la fabricación 2017:Educando a la próxima generación de trabajadores
- La evolución de los compuestos aditivos
- Compuestos de impresión 3D con fibra continua
- Material para la próxima generación de sensores inteligentes
- La fuente ultradelgada de terahercios allana el camino hacia la próxima generación de tecnología de la comunicación
- COVID-19:demanda de la próxima generación de fábricas inteligentes