Unión automatizada de estructuras de compuestos híbridos metal-termoplásticos
Habilitación de la unión híbrida a escala industrial
FlexHyJoin demuestra un proceso de producción en masa para producir un refuerzo de techo compuesto termoplástico con soportes de metal soldados para ensamblar en una carrocería de metal en blanco, como el caso de uso del proyecto, el Fiat Panda coche de la ciudad. Fuente | IVW
Las estructuras híbridas de compuestos metálicos continúan siendo de interés para aplicaciones automotrices y aeroespaciales, ya que ofrecen un peso reducido y un rendimiento mejorado al colocar "el material correcto en el lugar correcto". Los compuestos termoplásticos (TPC) son atractivos para tales estructuras de materiales múltiples debido a su procesamiento rápido, incluida la capacidad de ser soldados y termoformados. Sin embargo, hasta ahora, la unión de materiales compuestos a metales se ha basado principalmente en sujetadores mecánicos, que requieren taladrar agujeros que dañan las fibras que soportan la carga. También se ha utilizado la unión adhesiva, pero varios termoplásticos son difíciles de unir de esta manera; además, los adhesivos añaden material y peso. Por ejemplo, el BMW i3 , que utiliza un chasis de plástico reforzado con fibra de carbono (CFRP) y paneles de carrocería de plástico, utiliza 16 kilogramos de adhesivo, que contrarresta parcialmente el potencial de ahorro de peso de los compuestos.
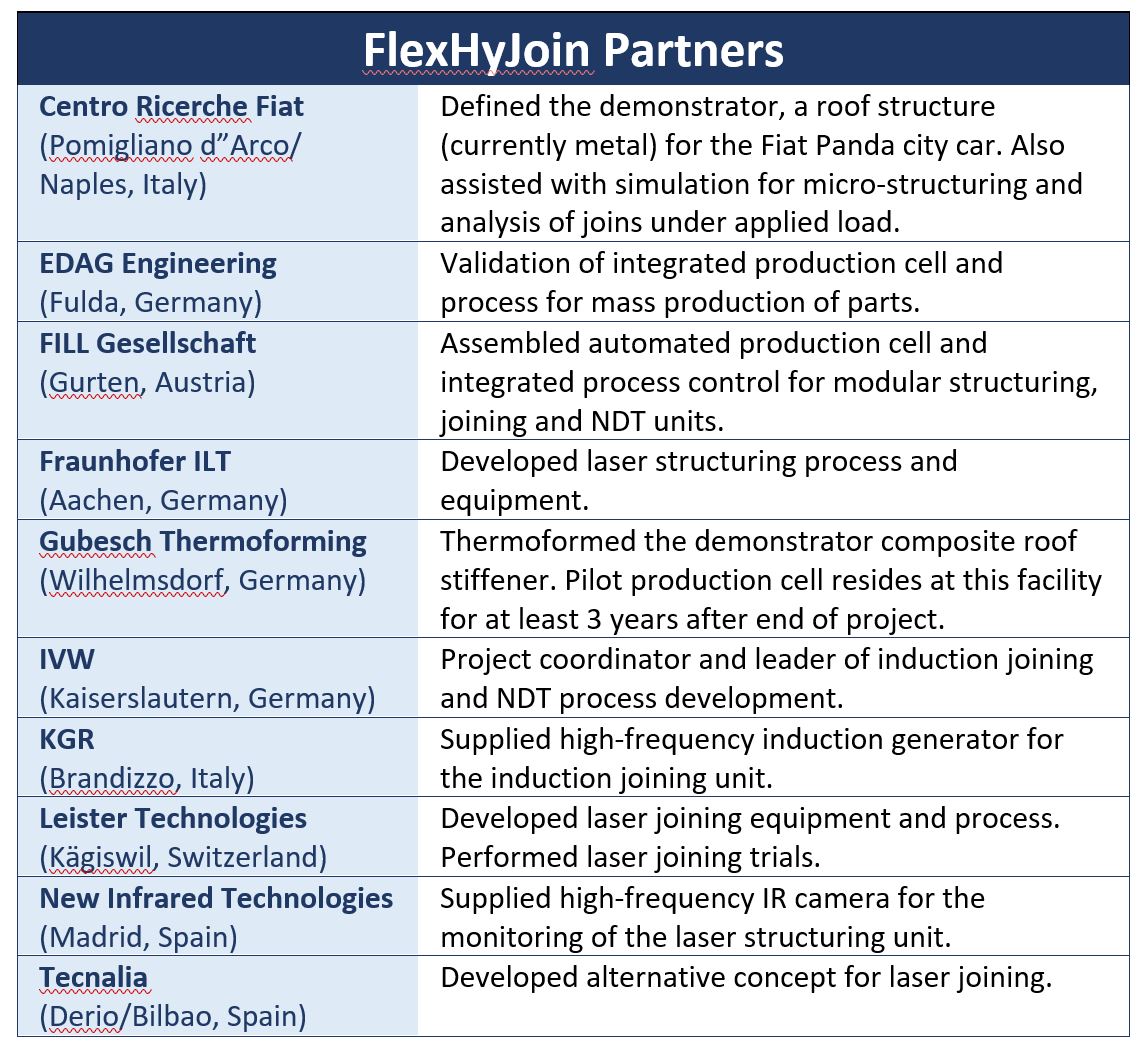
FlexHyJoin es un proyecto financiado por el programa de investigación e innovación Horizonte 2020 de la Unión Europea, realizado entre octubre de 2015 y diciembre de 2018, que buscaba abordar los desafíos de unir TPC y piezas metálicas. Coordinado por el Institut für Verbundwerkstoffe (IVW), una institución de investigación sin fines de lucro del estado de Renania-Palatinado y la Universidad Técnica de Kaiserslautern, Alemania, FlexHyJoin reunió a 10 socios de toda Europa para desarrollar un proceso automatizado que permite un techo de automóvil de TPC estructura para ensamblar en una carrocería metálica en blanco (BIW). La estrategia consistía en producir una unión de alta resistencia y peso neutro, sin adhesivos ni sujetadores, mediante el tratamiento previo con láser de los soportes metálicos y uniéndolos al refuerzo del techo mediante inducción y unión por láser. Esto se logró en una sola celda de producción automatizada con control de proceso integrado y pruebas no destructivas en línea (NDT).
Demostrador híbrido en 140 segundos
El socio del proyecto Centro Ricerche Fiat (Pomigliano d’Arco / Nápoles, Italia) proporcionó especificaciones para la parte del demostrador:un refuerzo de techo para el Fiat Panda coche urbano que actualmente se fabrica en acero. Para FlexHyJoin, la pieza fue termoformada a partir de un compuesto termoplástico (Fig.1) por Gubesch Thermoforming (Wilhelmsdorf, Alemania) utilizando una lámina orgánica de fibra de vidrio tejida Tepex Dynalite 102 de 1,5 milímetros de espesor / poliamida 6 (PA6) suministrada por Bond-Laminates (Brilon, Alemania). Para unir este refuerzo de techo TPC en el Panda BIW de acero, un conjunto de soportes laterales (izquierdo y derecho) hechos de acero DC04 de 0,7 milímetros de espesor se unieron con láser en los extremos. Se colocó un soporte central hecho del mismo material mediante unión por inducción. FlexHyJoin demostró que ambos métodos de unión se pueden utilizar para la producción de estructuras híbridas industriales.
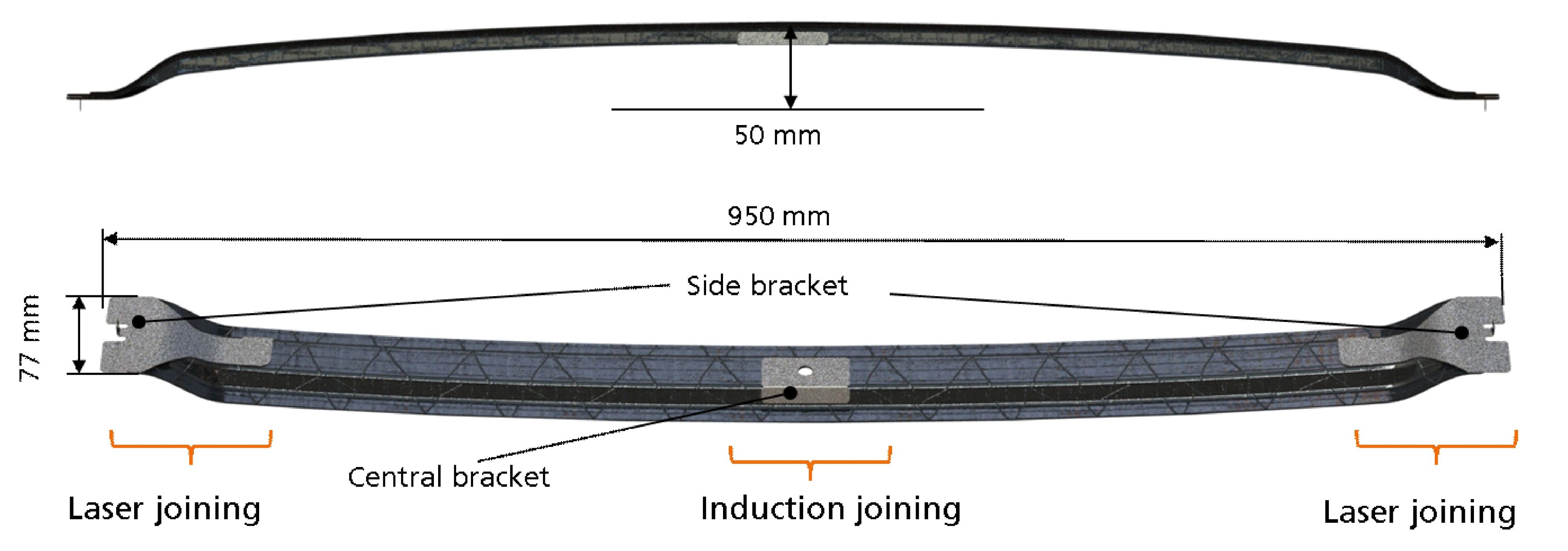
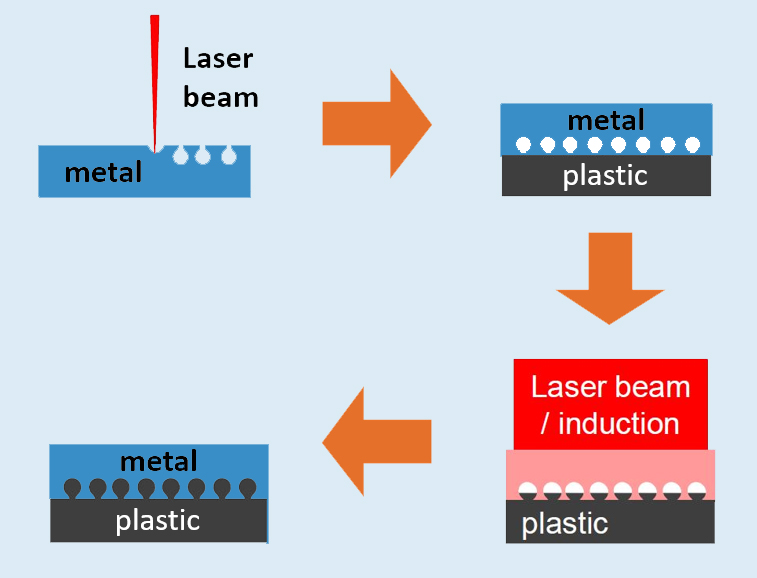
Fig. 1 Estructuración de superficies para uniones híbridas
FlexHyJoin demuestra la unión por láser e inducción de soportes de acero a un refuerzo de techo GF / PA6 estampado ( top ). Estas uniones híbridas se basan en el tratamiento de la superficie de los soportes metálicos para crear cortes, que se rellenan con plástico derretido durante los pasos del proceso de unión ( parte inferior ).
Fuente | IVW
La simple fusión de la matriz PA6 sobre los soportes de acero no produciría una unión con la resistencia suficiente para cumplir con los requisitos estructurales. Por lo tanto, se requirió un tratamiento de superficie con láser antes de unir. “La superficie de los soportes se estructuró con un láser para crear socavados”, explica Johannes Voithofer, director de proyectos de Fill Gesellschaft (Gurten, Austria), que tenía la tarea de ensamblar e integrar la celda de producción automatizada. “Los brackets tratados se colocan sobre la pieza compuesta. Luego, se aplica calor y presión durante la unión, lo que hace que la matriz de PA6 del compuesto fluya hacia los cortes inducidos por láser [ver Fig. 1] ". El proceso de estructuración fue desarrollado por otro socio, el Instituto Fraunhofer de Tecnología Láser (ILT, Aachen, Alemania), y da como resultado una unión de metal-compuesto que combina la adhesión del material y el bloqueo mecánico.
Las piezas unidas se transfieren luego a una estación de END donde se escanean en busca de defectos utilizando un tipo de termografía. “Los focos halógenos se utilizan para el calentamiento modulado de la superficie compuesta”, explica Vitalij Popow, investigador asociado de IVW y líder para el desarrollo de FlexHyJoin NDT y el control de procesos. “Esto conduce a un campo de temperatura oscilante dentro de la estructura compuesta. Analizamos la respuesta térmica en la superficie a lo largo del tiempo e identificamos defectos en las juntas ”. La prueba totalmente automatizada se completa dentro de la celda de producción para cada componente fabricado. La validación del proceso se realizó en unas 400 juntas.
La celda de producción automatizada FlexHyJoin, como está configurada actualmente, ejecuta la estructuración láser, la unión y el END en paralelo con tiempos de ciclo de 81 segundos, 98-108 segundos y 100 segundos, respectivamente, sin incluir el tiempo para la transferencia robótica de piezas entre estaciones. Voithofer dice que el tiempo de ciclo por pieza híbrida completada es de aproximadamente 140 segundos.
Fig. 2 Habilitación de la unión híbrida a escala industrial
La celda de producción piloto FlexHyJoin cuenta con tres estaciones modulares para estructuración de superficies, unión y END. El robot de manipulación individual de la celda transfiere los componentes del cajón de carga a cada una de estas estaciones, colocando las piezas híbridas terminadas en un cajón contiguo. Fuente | IVW y relleno
Estructuración láser
El proceso de estructuración por láser produce líneas con geometrías socavadas en la superficie de unión de los soportes metálicos. Para FlexHyJoin, los cortes miden 75 micrómetros de ancho y 215 micrómetros de profundidad. Estas medidas, así como el número de líneas y el patrón general de líneas, se pueden adaptar e, idealmente, se combinan para cumplir con los requisitos de tiempo de ciclo y pieza.
“La posición y el número de microestructuras en la superficie de unión se pueden adaptar a la carga en el componente”, explica Stefan Weidmann, investigador asociado de IVW y líder del equipo de desarrollo de la unidad de unión por inducción FlexHyJoin. “La distancia entre microestructuras se puede reducir en áreas muy cargadas de la superficie de unión y aumentar en áreas menos cargadas para permitir un proceso de microestructuración eficiente”.
La estructura se logra mediante la ablación de la superficie del soporte metálico utilizando un láser de fibra monomodo de alta potencia suministrado por IPG Photonics (Burbach, Alemania). Este láser YLR-1000-WC tiene una potencia máxima de 1.000 vatios a una longitud de onda de emisión de 1.070 nanómetros. "Usamos el láser de fibra monomodo para el proceso de microestructuración debido a su alta capacidad de enfoque, manteniendo un tamaño de punto de aproximadamente 40 micrómetros", explica Christoph Engelmann, líder del equipo de procesamiento de polímeros en Fraunhofer ILT.
El láser está contenido dentro de un cabezal óptico montado en un brazo robótico ABB 1200. “Dentro del cabezal óptico, tenemos dos espejos galvanométricos para desviar el haz en un campo de trabajo de 240 por 240 milímetros”, detalla Engelmann. “Además, hay una lente móvil para rastrear la altura z (palanca de cambios z). Solo usamos el robot para colocar el cabezal de escaneo sobre los componentes metálicos, y luego el rayo es desviado por los espejos y la posición z para cada línea de la microestructura es adaptada por la palanca de cambios z. Por lo tanto, no hay movimiento del cabezal durante el procesamiento. De esta manera, podemos tratar piezas 2.5D, manteniéndonos en la misma posición z para cada línea discreta pero capaces de ajustarnos entre líneas ”.
“Por razones de seguridad, tanto las unidades de estructuración como de unión están encerradas”, explica Voithofer, señalando los gabinetes negros en la celda de producción piloto (Fig. 2). Por lo tanto, un portón / puerta automatizado permanece bajado durante las operaciones con láser, abriéndose para retirar las piezas terminadas e insertar otras nuevas.
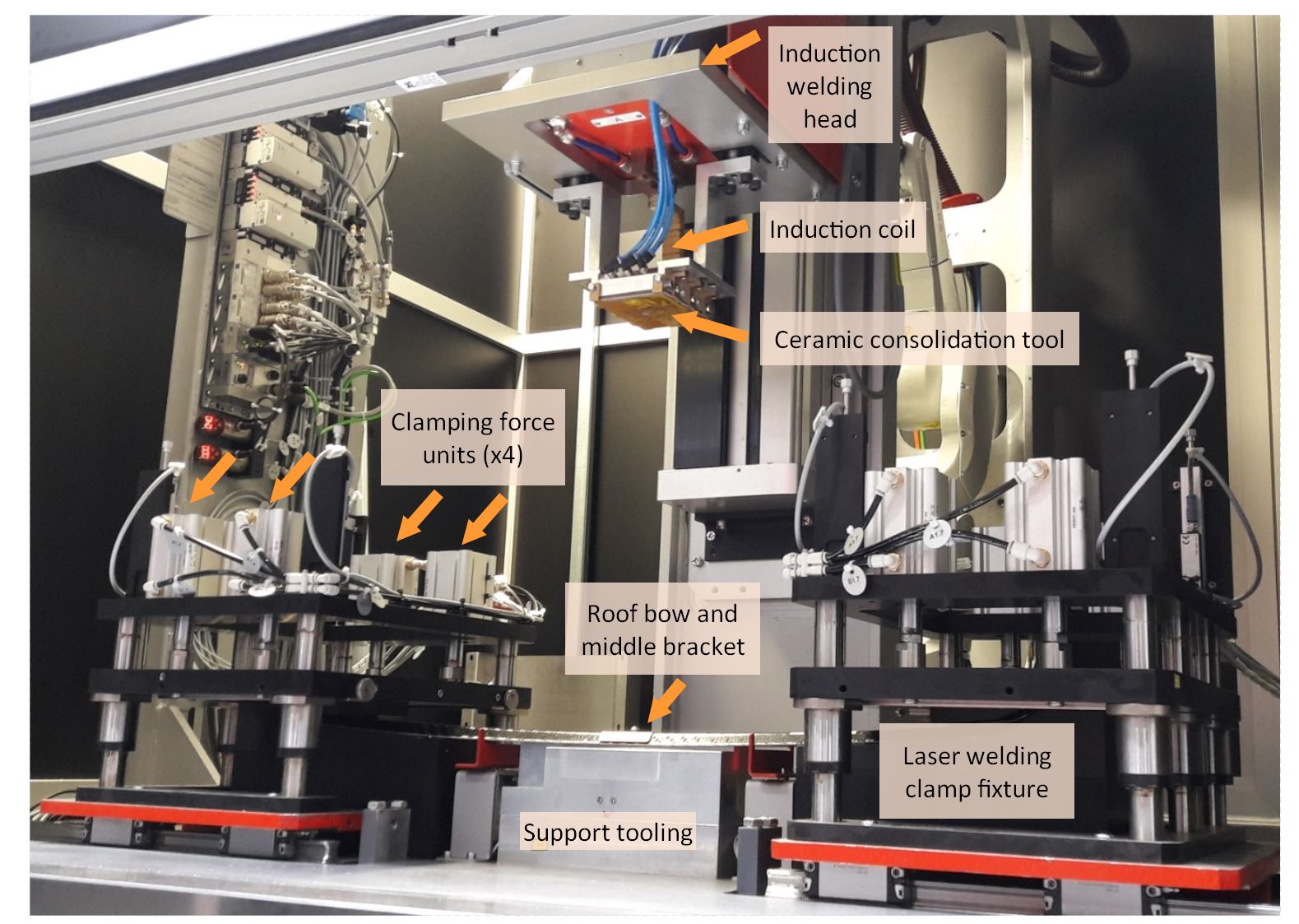
Fig. 3 Celda de unión láser e inducción
En la celda de unión, la unión por inducción se usa para unir el soporte del medio, mientras que la unión por láser se usa para unir los soportes laterales en cada extremo del arco de techo compuesto. Fuente | IVW y relleno
Inducción y unión por láser
Adyacente a la celda de estructuración se encuentra la celda de unión, que comprende dos operaciones distintas:unión por inducción del soporte central y unión por láser de los soportes laterales izquierdo y derecho. “Para piezas más grandes con una complejidad moderada como el soporte central, la unión por inducción es un método de unión más adecuado”, dice Weidmann. “Una herramienta de consolidación de cerámica con inductor aplica presión en el área de unión y es permeable al campo electromagnético, lo que conduce a una entrada de energía eficiente en el soporte metálico para calentar. Esto es conveniente para formas planas, pero más desafiante para formas complejas, como la geometría de los soportes laterales. Por lo tanto, fue más eficaz utilizar la unión láser para estos ". Weidmann agrega:"La unión por inducción es mejor para piezas grandes y de complejidad moderada, mientras que la unión por láser es más adecuada para piezas con alta complejidad".
Un orificio perforado en el refuerzo de techo compuesto lo alinea en la parte superior de la herramienta de soporte, con la forma que corresponde a la curvatura del refuerzo termoformado. Un orificio cortado con láser en el soporte central lo ubica en el refuerzo del techo, mientras que los soportes laterales están alineados por su forma que coincide con los extremos del refuerzo del techo.
“El soporte central se unió usando discontinuo unión por inducción. "Esto es esencialmente una unión a presión cuasi-estática", dice Weidmann, "lo que simplemente significa que es un proceso estático, logrando una unión de área en un lugar, pero hay movimiento en la dirección z porque el espesor del compuesto cambia ligeramente debido a a la presión de consolidación aplicada durante la unión (por inducción) ".
La unidad de unión por inducción contiene un generador de alta frecuencia KGR (Brandizzo, Italia) para suministrar un campo eléctrico alterno a la bobina de inducción. El cabezal se mueve mediante un motor eléctrico y un husillo (Fig. 3) de modo que la herramienta de consolidación de cerámica presiona hacia abajo sobre el soporte metálico. La bobina de inducción en la herramienta de consolidación hace que el metal se caliente, lo que derrite la matriz compuesta y crea la junta. "La presión se aplica durante el calentamiento y el enfriamiento", señala Weidmann.
La unión por láser de los soportes laterales comienza simultáneamente a la unión por inducción. Dos dispositivos de sujeción, ubicados a cada lado de las herramientas de soporte, pueden aplicar 4.000 Newtons de fuerza de sujeción a los soportes laterales. “La sujeción es necesaria para minimizar la brecha entre los componentes compuestos y metálicos”, explica Voithofer. "Esto evita huecos en la articulación". Una vez aplicada la fuerza de sujeción, el cabezal láser se coloca en posición. Está equipado con un láser de diodo LineBeam suministrado por Leister Technologies (Kägiswil, Suiza). Johannes Eckstaedt de Leister explica que este láser tiene una potencia de salida máxima de 600 vatios a una longitud de onda de emisión de 980 nanómetros. El rayo se forma en una línea de 27 milímetros por 1 milímetro mediante lentes ópticas y se enfoca en el soporte de metal. El cabezal láser está montado en un brazo robótico que le permite moverse a lo largo de la superficie del soporte con forma. "Establecemos diferentes velocidades para cada área de los soportes para lograr una temperatura de unión homogénea, reduciendo el estrés térmico para obtener los mejores resultados de unión", dice Eckstaedt.
En general, la unión por láser puede utilizar unión por transmisión o por conducción de calor. Para la unión por transmisión láser, el material compuesto que se une debe ser transparente para la longitud de onda seleccionada del láser. Luego, el láser atraviesa el material compuesto, golpea la superficie metálica del soporte y lo calienta. Sin embargo, este método no se utilizó en el demostrador FlexHyJoin porque el laminado de lámina orgánica del refuerzo del techo no era transparente al láser. En su lugar, se utilizó el método alternativo de unión por conducción de calor. Esto simplemente aplica el láser directamente a la superficie del metal, que conduce el calor a través del material de base del metal al compuesto, derritiendo la matriz PA6 a 220-300ºC y creando la junta. “Debido a la alta conductividad térmica de los soportes de acero, el calor del láser se propaga rápidamente, uniendo de manera eficiente los soportes laterales”, dice Voithofer.
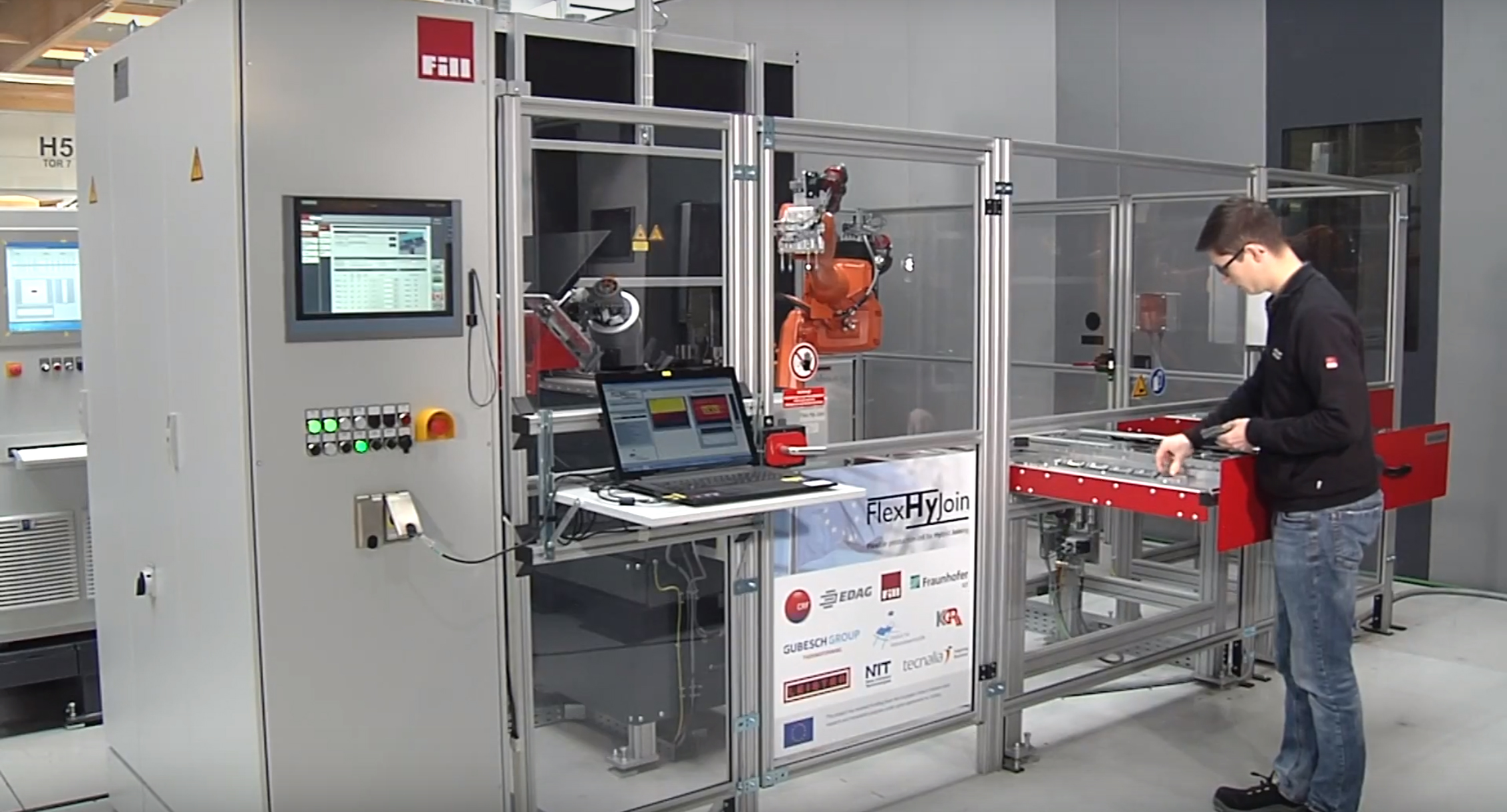
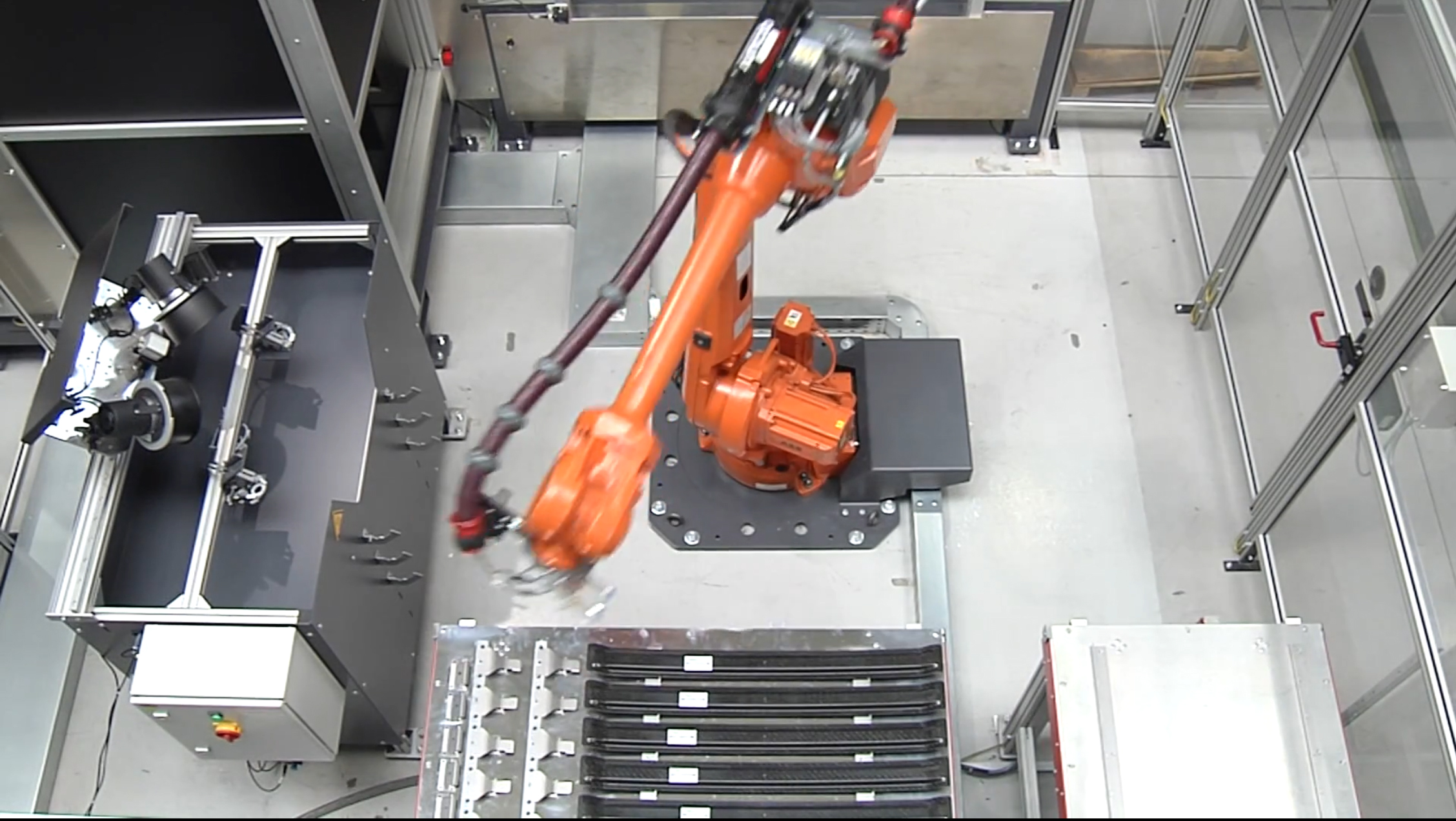
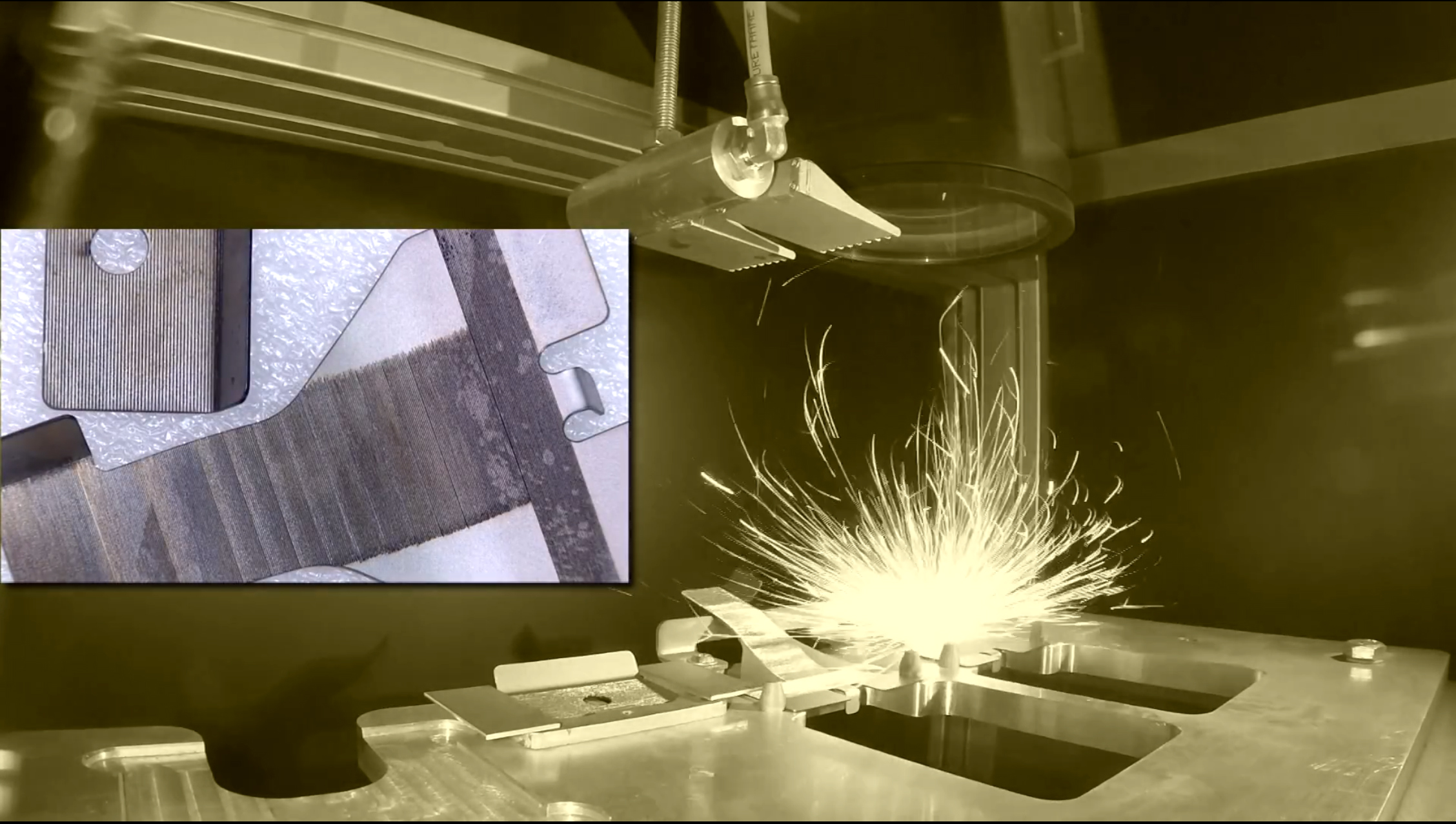
Paso 3. Dentro de la celda de estructuración, un láser de fibra de alta potencia crea cortes en la superficie del soporte que se unirá en el refuerzo de techo compuesto.
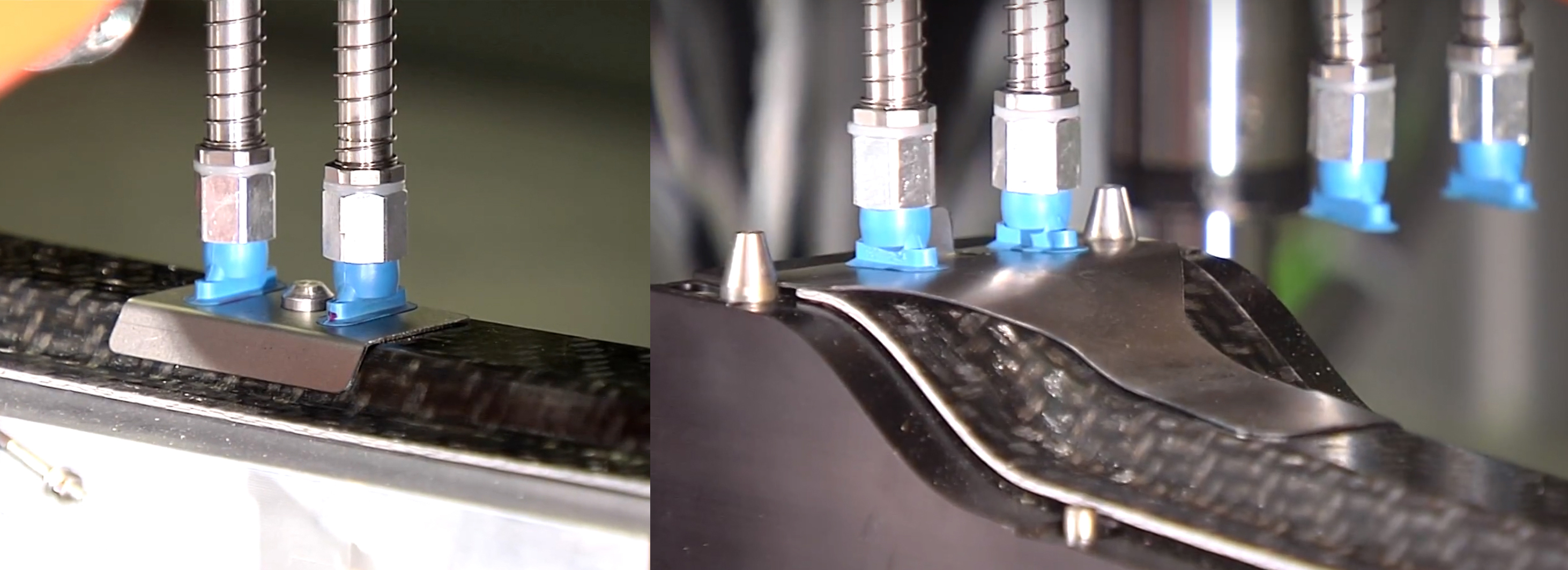
Paso 5. El robot regresa a la celda de estructuración, toma los soportes tratados y los coloca, con el lado estructurado hacia abajo, sobre el arco del techo de TPC.
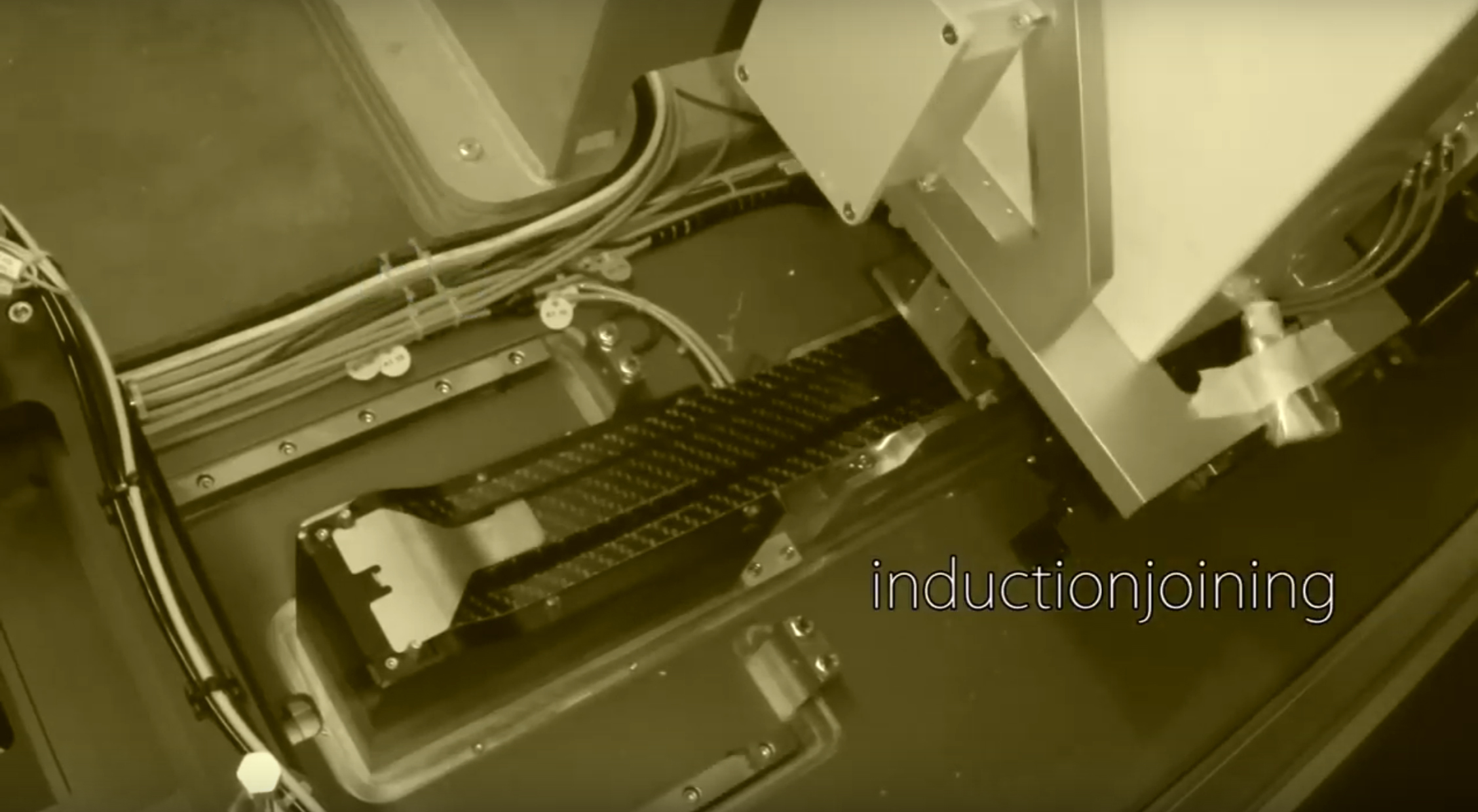
Paso 6. A continuación, el robot coloca las unidades de sujeción en los tres soportes. La unidad de unión por inducción desciende sobre el soporte central. La bobina de inducción hace que el soporte de metal se caliente, derritiendo la matriz PA6 del compuesto subyacente.
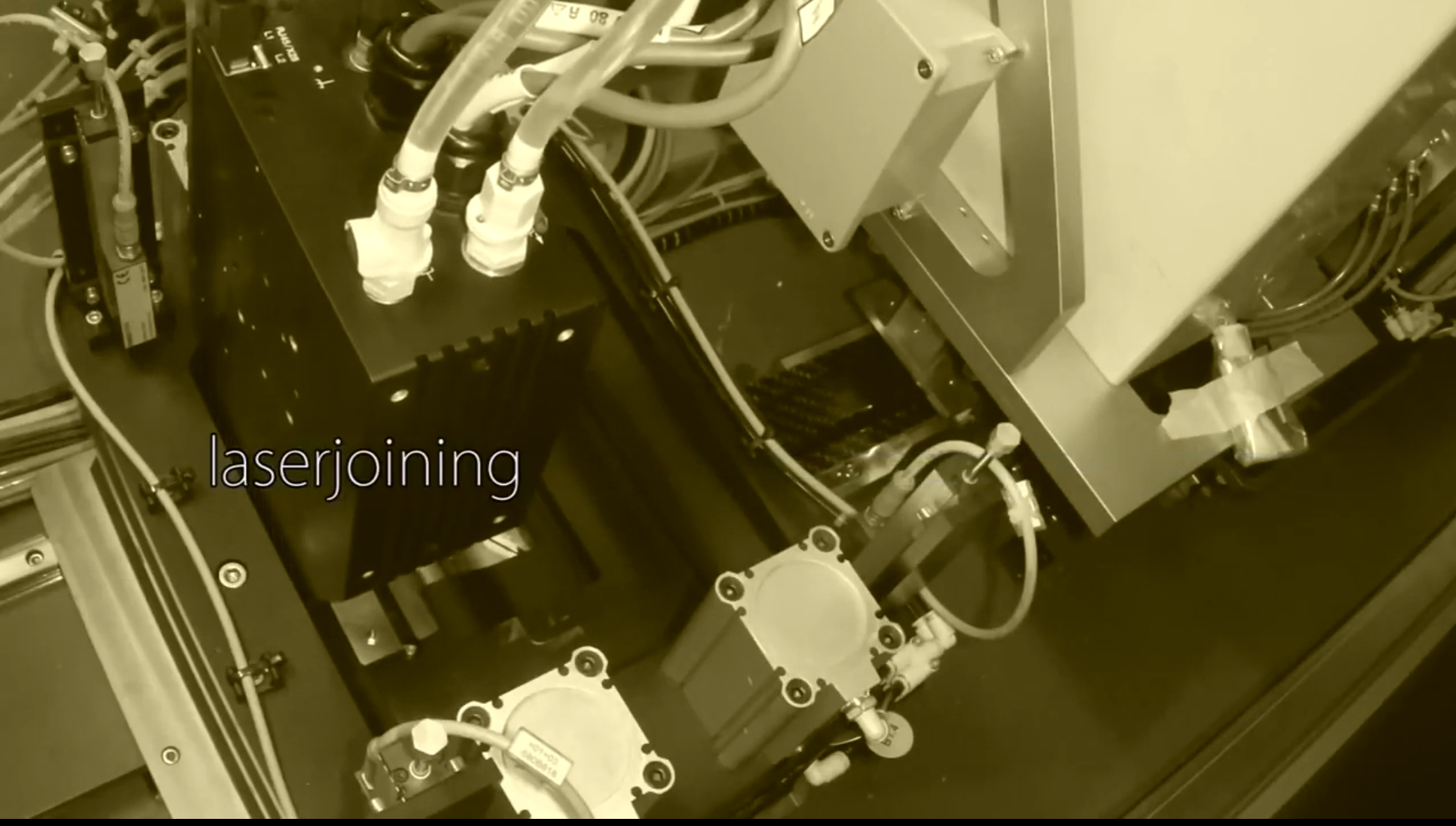
Paso 7. Mientras se completa la unión por inducción, la unidad de unión por láser se baja para unir los soportes del lado izquierdo y luego del derecho. El láser calienta el metal, lo que hace que la matriz PA6 subyacente se derrita en los cortes, creando una unión de alta resistencia.
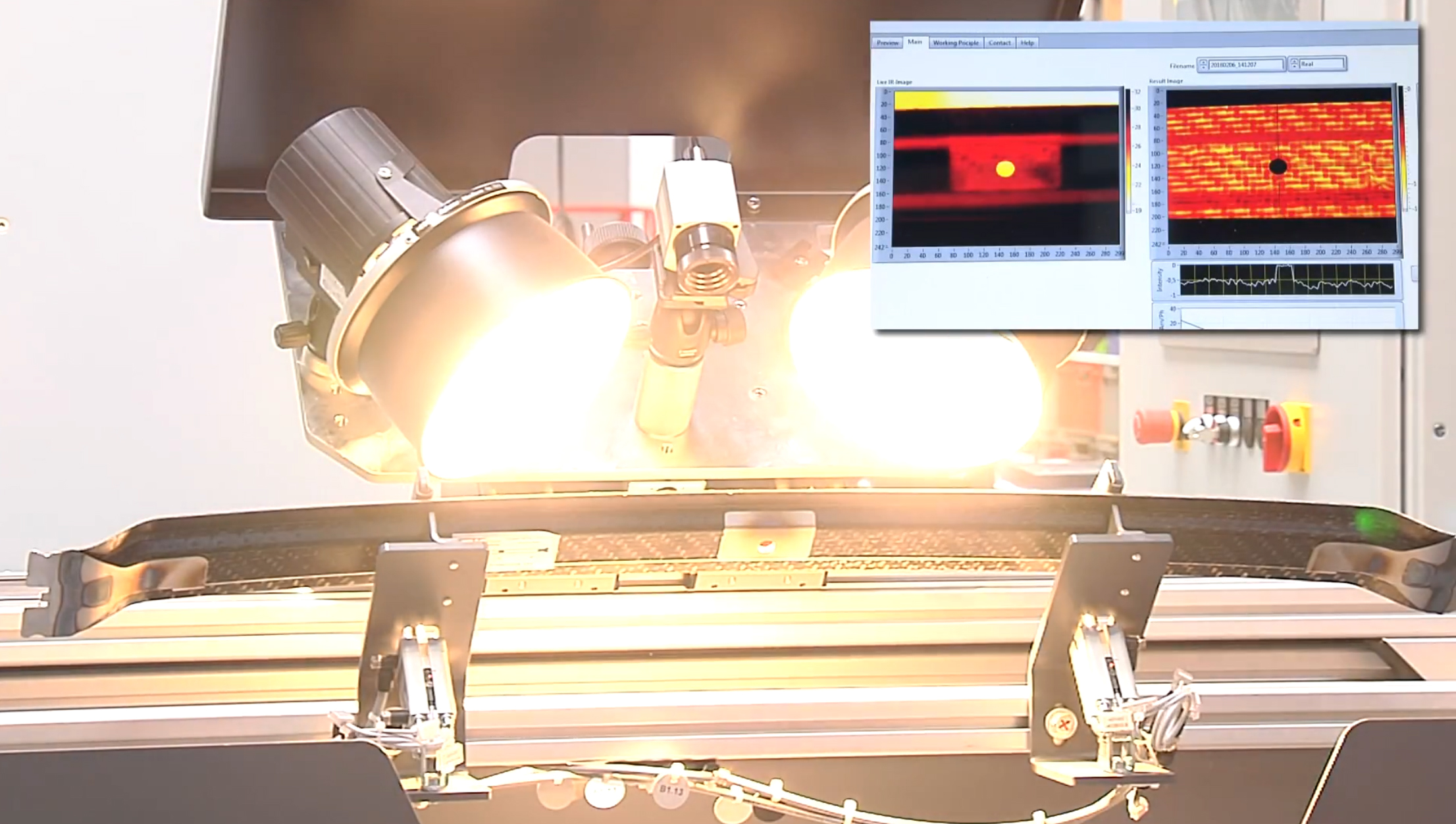
Unirse al control de procesos
El método básico para controlar ambos procesos de unión es medir la temperatura y el tiempo frente a un conjunto de parámetros optimizados que se definieron mediante pruebas. “Por lo tanto, producimos muestras de prueba de unión con diferentes parámetros y realizamos pruebas mecánicas para cada conjunto de parámetros utilizando configuraciones de prueba especiales. Para el soporte lateral, se desarrolló una combinación de una prueba de cizallamiento y una prueba de pelado, y para el soporte central usamos una prueba de carga de presión, comparable a una prueba de cizallamiento traslapado, pero usted empuja en lugar de tirar, para obtener una carga de corte. en el área de unión ”, dice Popow. La configuración de estas pruebas especiales se diseñó junto con EDAG Engineering GmbH (EDAG, Fulda, Alemania), que también realizó el análisis de los resultados de las pruebas. Siguiendo este procedimiento, se identificó el mejor conjunto de parámetros para los procesos de unión y luego se utilizó en la celda de producción piloto.
“El proceso de unión por inducción se calibró de antemano”, dice Weidmann. "Sabemos que alcanzamos la temperatura de unión después de aproximadamente 30 segundos, pero también medimos la temperatura in situ por razones de seguridad para evitar un sobrecalentamiento". Se utilizó un pirómetro, que mide de forma remota la radiación de una superficie, para medir un punto caliente conocido en el área de unión por inducción. “Pero no puede proporcionar mediciones precisas de la unión láser debido al alto nivel de luz irradiada y calor in situ”, explica. Sin embargo, los sensores de contacto podrían usarse en el lado compuesto de las áreas de unión por láser, aunque no eran aplicables para el proceso de unión por inducción porque generalmente están hechos de metal y se calentarían por inducción y distorsionarían la medición.
“Las áreas calentadas para todas las juntas también están cubiertas por la herramienta de prensado y los dispositivos de sujeción”, señala Weidmann. "Por lo tanto, hemos validado el cambio de espesor del componente debido a la presión y el calor antes y después de la unión como método de garantía de calidad". Este cambio de espesor se mide mediante un sensor de distancia integrado en la herramienta de posicionamiento para el refuerzo de techo (también mostrado en la Fig. 3). “Cuando presionamos las piezas juntas, el sensor de distancia se mueve”, explica. “Cuando aplicamos calor y presión de unión, el polímero de matriz fundido fluye hacia las cavidades de la estructura del láser y se exprime ligeramente fuera de la zona de unión hasta que la unión se enfría. Esto conduce a un cambio en el espesor que es registrado por el sensor de distancia ". Weidmann y el equipo de IVW han correlacionado esta distancia con la calidad de la pieza. “Un cambio de espesor, en otras palabras, una compactación, superior a 0,1 milímetros significa que la calidad de la junta es buena”, señala Weidmann.
NDT en línea
IVW desarrolló otro método para garantizar la calidad:las pruebas termográficas en línea. “Para garantizar la calidad, el objetivo principal era ver las propiedades en el área de unión”, explica Popow. "Pero esto fue muy difícil, por lo que realizamos termografía en el lado compuesto de las uniones después de que se completó la pieza".
IVW eligió una técnica de termografía activa llamada termografía de bloqueo porque ofrece una mejor relación señal-ruido que otros métodos activos (por ejemplo, termografía de fase de pulso) y también puede inspeccionar defectos más profundos. “La idea básica es poner calor en el material compuesto, que luego se conduce hacia el área de unión y regresa a la superficie”, dice Popow. "Con la termografía de bloqueo, el componente se excita con una frecuencia definida en varios períodos. Luego analizamos esta respuesta a lo largo del tiempo. Si tiene áreas entre la superficie compuesta y el área de unión que no son homogéneas debido a un vacío o defecto, se mostrarán en la respuesta térmica ”.
La respuesta térmica se captura como una imagen. Los puntos que componen estas imágenes son píxeles, abreviatura de elementos de imagen. Cada píxel es también un punto de medición. Por tanto, se analiza la señal de temperatura para cada píxel en toda el área de inspección. “Como resultado, obtienes información de amplitud y fase para cada píxel, y el software luego reconstruye esto en una imagen nuevamente, que se puede inspeccionar visualmente”, agrega. Pero también proporcionó grandes conjuntos de medidas para las 126 piezas probadas. “Hemos correlacionado estos resultados de NDT con los resultados de las pruebas mecánicas realizadas por EDAG”, dice Popow. Su equipo también probó el área de unión después de quitar los soportes, es decir, pruebas destructivas. “Por lo tanto, hemos correlacionado tres conjuntos de resultados de pruebas y ahora podemos identificar áreas de unión de baja resistencia frente a áreas de alta resistencia a partir del análisis visual de los resultados de la termografía”, dice.
Celda integrada para producción en masa
Uno de los mayores logros de FlexHyJoin, dice Weidmann, es integrar todas las unidades de tecnología, cada una desarrollada por un socio de proyecto diferente, en una línea de producción automatizada y optimizada. Voithofer, el que integra el equipo en Fill, explica que “cada conjunto de equipos que nos enviaron usaba un controlador diferente. Tuve que diseñar un PLC maestro para controlar todas las diferentes unidades de proceso ". Esto incluyó los recintos láser y el robot de manipulación de la celda, que fueron suministrados por Fill. “También fue muy difícil hacer que todos estos pasos del proceso funcionen juntos porque toman diferentes cantidades de tiempo”, agrega.
Voithofer comenzó desarrollando una arquitectura para cada unidad de proceso y robot, considerando cómo colocarlos para obtener el mejor flujo. “Nuestro concepto era mantener las tres estaciones - estructuración, unión y END - modulares, en tres carcasas separadas”, dice. “De esta manera, podríamos extraer unidades individuales y usarlas en ferias comerciales u otros proyectos de demostración, y luego devolverlas. Por lo tanto, la celda de trabajo es modular, pero integrada ”.
Las décadas de experiencia de Fill en este tipo de integración de sistemas para la producción de compuestos en serie ayudaron a lograr lo que Popow considera la mayor hazaña de FlexHyJoin:pasar de la escala de laboratorio a la escala industrial. “Somos el primer consorcio en realizar un proceso como este, que es adecuado para la producción en masa de compuestos unidos al metal”, dice. “Este proceso se puede utilizar para muchas piezas de automóviles, como eslabones estabilizadores, parachoques y puertas”, señala Voithofer. "Hay muchas piezas compuestas que se conectan a piezas metálicas en un BIW ligero".
Adaptación para múltiples industrias
Sin embargo, se necesitan algunos cambios antes de que la celda se ponga en producción en serie. "Ya no mantendríamos la estructura y unión del láser en recintos separados, sino que los combinaríamos en uno", dice Voithofer. "Esto eliminaría la necesidad de que las puertas de los gabinetes se abran y cierren entre estos procesos, reduciendo el tiempo de ciclo". También conectaría todas las estaciones linealmente en una cinta transportadora. Por lo tanto, la línea funcionaría de manera continua, con las piezas recogidas y colocadas nuevamente en el transportador para cada estación antes de salir de la celda listas para ensamblarse en un BIW. Esto reduciría aún más el tiempo del ciclo. Además, los cajones expandidos capaces de alimentar cientos de piezas permitirían que la línea funcione en turnos completos sin necesidad de reabastecimiento.
Aunque esta celda de producción piloto estaba destinada a la industria automotriz, Popow señala que se puede adaptar fácilmente a aplicaciones aeroespaciales, deportivas / de bienes de consumo e industriales. “Esa fue en realidad una de las pautas principales”, dice Weidmann, “que debe poder unir diferentes geometrías y piezas. El único cambio debe ser la herramienta de compactación de unión por inducción, los accesorios de sujeción para unión por láser y las herramientas de soporte. Las partes principales de la celda deben permanecer iguales ". Señala que IVW también ha demostrado la unión híbrida de titanio y acero con compuestos de láminas orgánicas tejidas de fibra de carbono / sulfuro de polifenileno (PPS) y ahora está desarrollando demostraciones de polieteretercetona (PEEK) y polietercetonacetona (PEKK). “Esto simplemente requiere adaptar los procesos de unión para temperaturas más altas y redefinir los parámetros óptimos del proceso”, dice Weidmann. “La celda está abierta a una variedad de materiales, incluidos aluminio y cobre, así como otros sistemas de matriz de compuestos termoplásticos como polipropileno y polietileno”.
“Los socios del proyecto han trabajado bien juntos y están emocionados de avanzar más en el desarrollo”, señala. "Creemos que este tipo de producción es muy prometedor, y la respuesta que hemos recibido de la industria hasta ahora muestra que hay una variedad de empresas que también ven esta promesa".
Resina
- Solvay expande la capacidad de compuestos termoplásticos
- Síntesis y estudio de las características ópticas de estructuras de esferas híbridas Ti0.91O2 / CdS
- Impedancia de superficie de estructuras híbridas de grafeno / metauperficies
- Fraunhofer encarga células de producción automatizadas de Engel para I + D de compuestos termoplásticos
- La importancia de la selección de resina
- El Instituto de Estructuras y Diseño DLR aumenta la madurez de las estructuras de fuselaje de compuestos termoplásticos
- Los kits fáciles de usar permiten la reparación dentro del campo de estructuras compuestas
- Desarrollo de estructuras de isogrid compuestas utilizando tecnología innovadora de deposición
- El consorcio busca soluciones para estructuras compuestas termoplásticas de fibra de carbono
- Se presentó el compuesto de revestimiento arquitectónico
- Compuesto + metal:Tecnología híbrida de perfil hueco