CETMA:I + D e innovación de compuestos en Italia
Establecido en 1994, Centro di Ricerche Europeo di Technologie, Design e Materiali (CETMA, Brindisi, Italia) es una de las organizaciones independientes de investigación y tecnología más grandes de Italia, con una instalación de 4.000 metros cuadrados y 75 empleados. Durante más de 20 años, CETMA ha invertido fuertemente en materiales compuestos, lo que ha resultado en una amplia gama de experiencia:
- Diseño de componentes y creación de prototipos
- Nuevos procesos compuestos
- Procesos de reciclaje de materiales compuestos y plásticos
- Optimización del proceso por costo, sostenibilidad, tasa, etc.
- Monitoreo de procesos en tiempo real
- Pruebas no destructivas (NDT)
- Monitoreo de salud estructural (SHM) en tiempo real y de forma remota durante la producción y el servicio
- Consultoría REACH
- Estampado termoplástico, moldeo por compresión continua (CCM) y moldeo por compresión preimpregnado (PCM)
- Infusión líquida, moldeo por transferencia de resina (RTM) y el mismo RTM calificado (SQRTM)
- Preimpregnado fuera de autoclave (OOA)
- Soldadura por inducción
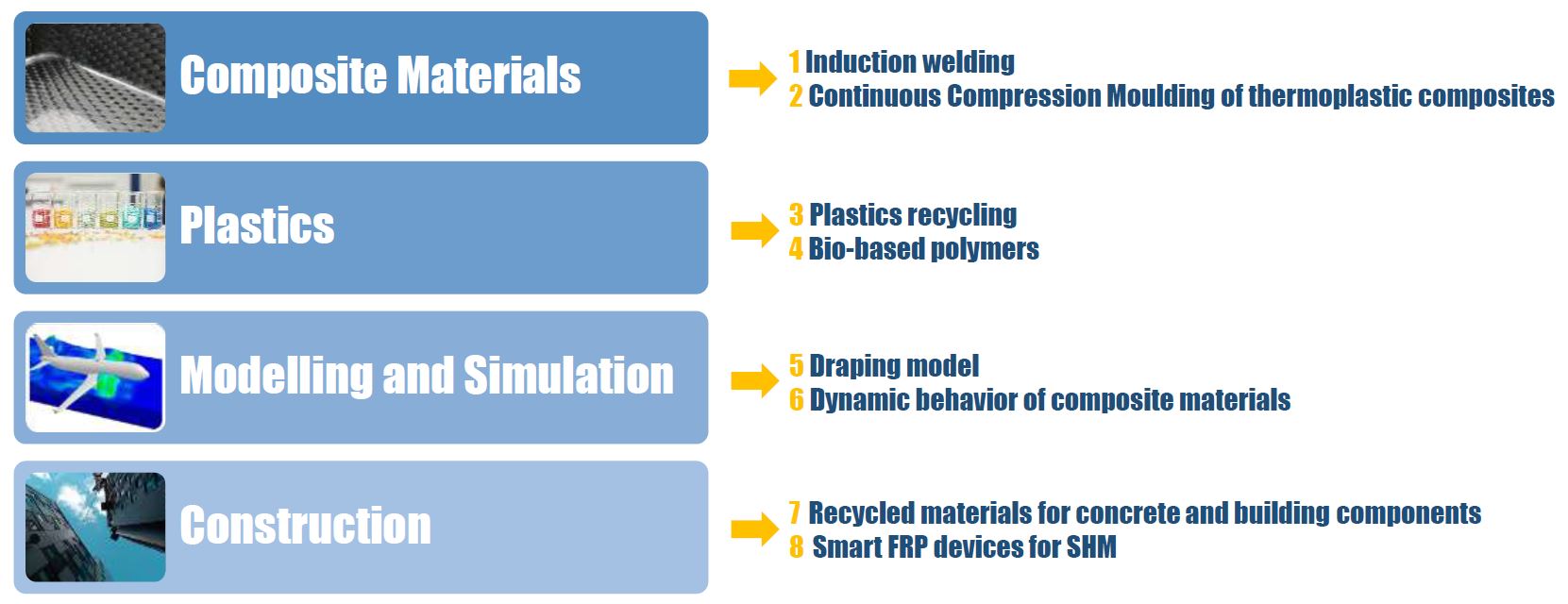
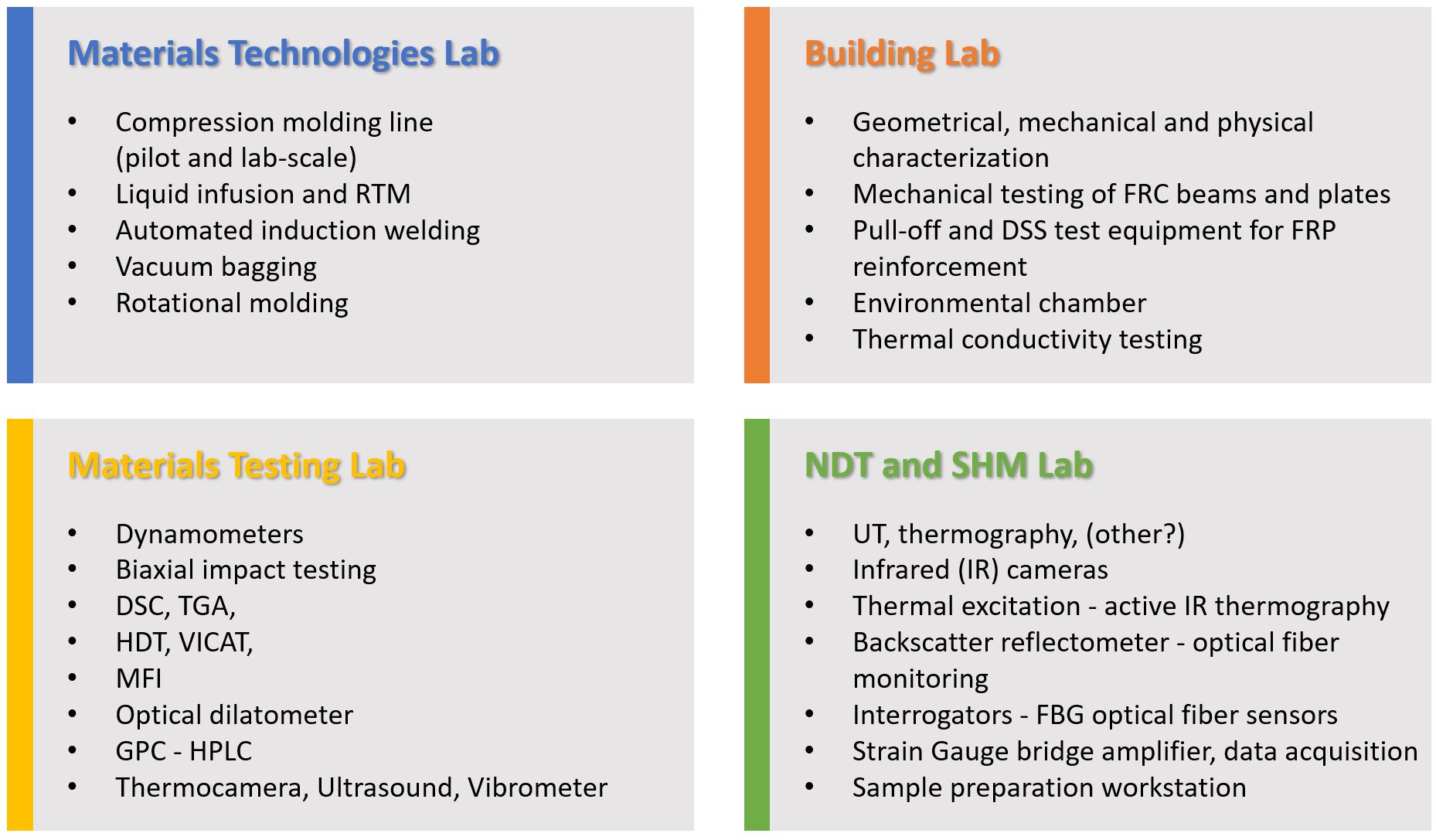
El principal objetivo de CETMA es apoyar a las empresas y la innovación. A cargo de cuatro laboratorios principales, las actividades de compuestos de CETMA se organizan dentro de su departamento de Materiales y Procesos Avanzados (AMP), que también comprende cuatro áreas:
- Materiales y caracterización
- Tecnologías y procesos
- Modelado y simulación
- Diagnóstico y supervisión del estado estructural
AMP emplea a 30 personas, incluidos ingenieros de materiales, aeronáuticos, civiles y químicos, así como un químico, científico de materiales, arquitecto y varios técnicos, de acuerdo con su creencia en equipos multidisciplinarios.
Resistencia en compuestos termoplásticos
“Ofrecemos un espectro completo de servicios en materiales compuestos”, señala Alessandra Passaro, jefa del departamento de AMP en CETMA, “pero nuestras actividades en materiales termoplásticos es una de nuestras áreas prioritarias, actualmente. Todos los diferentes tipos de polímeros de matriz termoplástica se han procesado en nuestro laboratorio. Comenzamos a trabajar con fibra mixta TWINTEX en 2004 y con moldeo por compresión usando una prensa simple hace aproximadamente 15 años. Ahora, hemos desarrollado tecnologías patentadas de moldeo por compresión continua (CCM) y soldadura por inducción. Hemos analizado todos los materiales compuestos termoplásticos que se pueden utilizar en estos procesos ”.
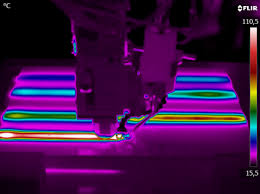
La línea CCM puede fabricar piezas de sección constante utilizando PPS, PEEK, PEKK o PAEK. Pero, ¿en qué se diferencia el proceso CETMA de lo que utilizan empresas como XELIS (Markdorf, Alemania) y ATC Manufacturing (Post Falls, Idaho, EE. UU.)? (Consulte los artículos de CW:“Moldeo por compresión de grado aeroespacial” y “Aceleración de compuestos termoplásticos en la industria aeroespacial”). Passaro explica:“Hay algunos detalles específicos en el diseño del molde que utilizamos. Nuestra tecnología es más flexible en cuanto a geometrías y materiales de matriz que se pueden utilizar. Todavía está en desarrollo ". Aunque está patentada, la tecnología aún se está desarrollando y algunos aspectos son propietarios. La razón por la que CETMA ha seguido CCM no lo es. “Vimos el mayor uso y la necesidad de procesos continuos de compuestos termoplásticos”, dice Passaro. “XELIS es una empresa de productos, no un proveedor de máquinas. Somos una organización de I + D independiente, por lo que invertimos y desarrollamos la tecnología desde un punto de vista diferente ”.
Un ejemplo de esto es la extensa simulación del proceso para analizar la distribución de temperatura en el molde. “Los resultados de la simulación nos permiten tener una imagen completa de la evolución de la temperatura en el material a lo largo del tiempo”, explica, “que es muy difícil de monitorear en línea desde un lado y, sin embargo, es crucial para minimizar los defectos en el material compuesto”.
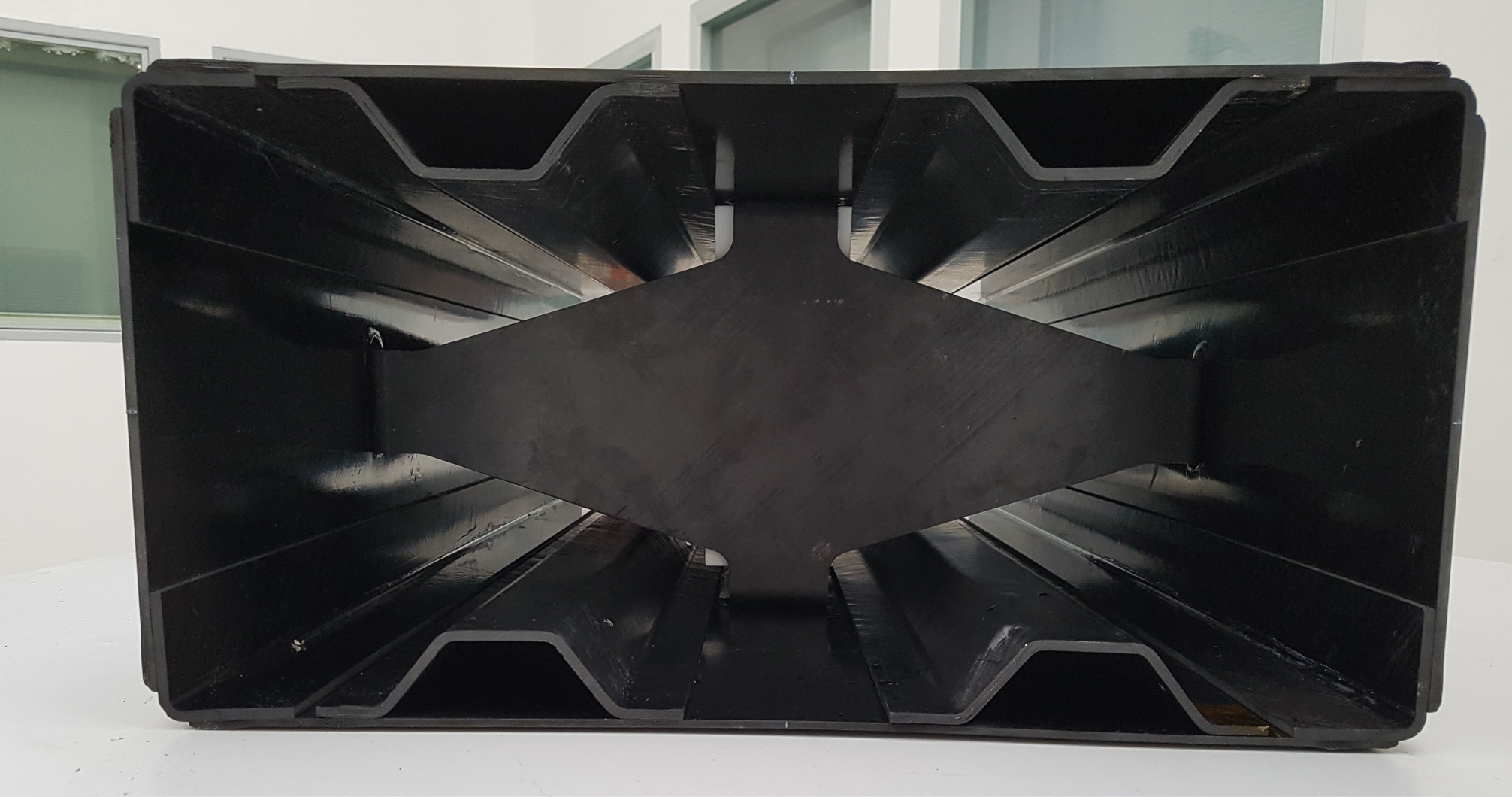
Soldadura por inducción para montaje
Otra parte clave de la experiencia de CETMA en compuestos termoplásticos es la tecnología de soldadura por inducción patentada, que incluye un sistema de control y enfriamiento para mantener el calor dentro de la línea de soldadura. CETMA utilizó la tecnología con su socio EURECAT (Barcelona, España) para ensamblar perfiles y placas CCM en una viga de quilla de material compuesto termoplástico para un avión tipo Airbus A320 en el proyecto Clean Sky 2 KEELBEMAN. Mi blog de enero de 2020, "Avanzando en compuestos termoplásticos y RTM para Clean Sky 2 ...", brinda más detalles sobre este proyecto, así como los detalles de la soldadura de CETMA.
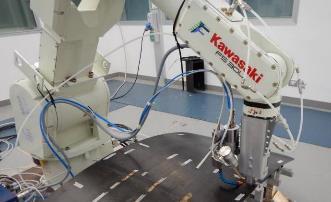
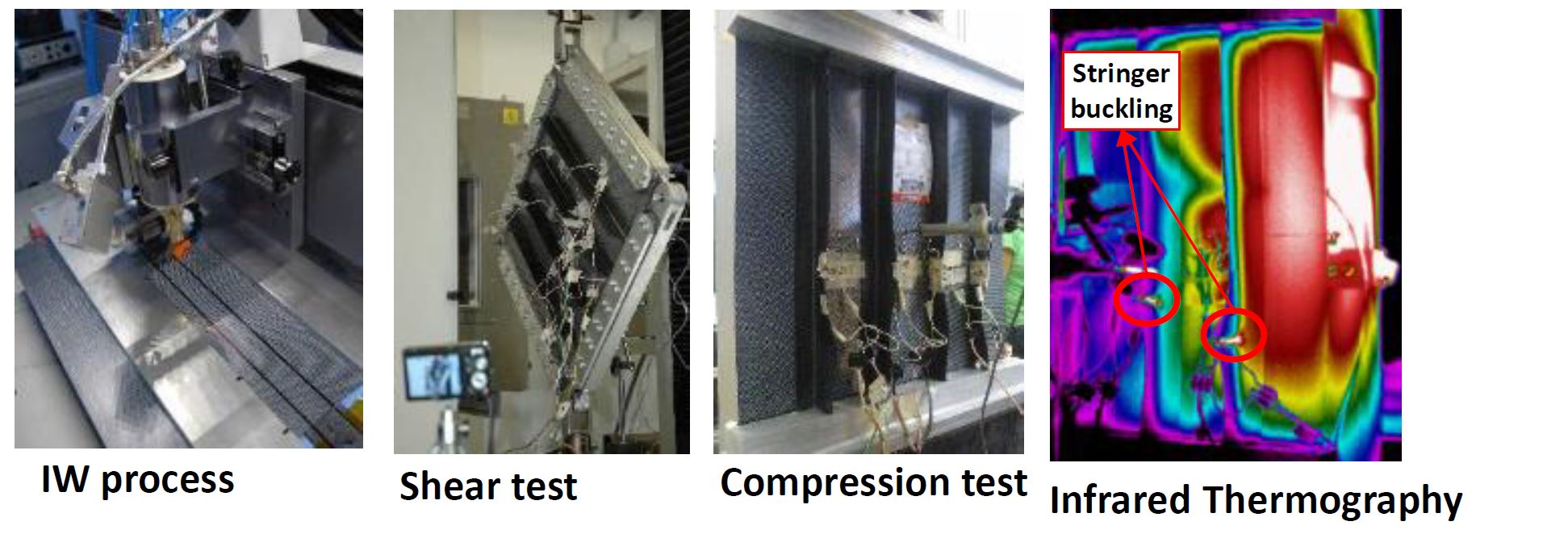
“Hemos desarrollado dos tipos de sistemas de soldadura por inducción”, señala Passaro. “Uno es una máquina fija para superficies planas y otro que está basado en un robot para geometrías 3D complejas. Ambos permiten soldaduras continuas a escala industrial sin requerir materiales adicionales en la línea de soldadura, pero ofrecen un rendimiento de adhesión muy alto en los ensamblajes ”.
CETMA ha demostrado la soldadura por inducción en laminados compuestos hechos con tejido de fibra de carbono y cinta unidireccional (UD), así como una gama de materiales de matriz:PPS, PEEK, PEI, PEKK, PP, PA6, PA12 y un epoxi / PVB termoestable híbrido ( polivinil butiral) sistema termoplástico.
También ha aplicado su experiencia en modelado y simulación por computadora al proceso de soldadura por inducción. “Esto nos permite predecir la evolución de la temperatura en el área de unión durante la soldadura, proporcionando una ayuda fundamental para optimizar los parámetros del proceso”, dice Passaro.

Clean Sky 2 y proyectos de I + D compuestos
Además de KEELBEMAN, el Departamento de AMP de CETMA participa actualmente en otros cuatro proyectos de Clean Sky 2.
TRINITI - Tanques de nitrógeno de alta presión termoplásticos multimaterial para aviones (JTI-CS2-CFP09-2018-02). El proyecto de dos años, que comenzó en 2019, tiene como objetivo construir un tanque de avión prototipo para el almacenamiento a largo plazo de nitrógeno con fines de extinción de incendios. Diehl Aviation (Gilching y Dresden, Alemania) es el administrador de temas del proyecto. Los socios también incluyen el laboratorio de I + D aeroespacial Novotech s.r.l. (Nápoles, Italia), Laboratorio de ensayo de materiales compuestos (Inverin, Co. Galway, Irlanda). El proyecto fabricará tanques compuestos termoplásticos multimaterial mediante una combinación de procesos como la coextrusión para formar un revestimiento / laminado multicapa y multifuncional, seguido de consolidación in situ (ISC) mediante la colocación automatizada de fibra asistida por láser (AFP). ). (Para obtener más información sobre ISC AFP, consulte “Consolidación de aeroestructuras de compuestos termoplásticos en su lugar, Parte 1 y Parte 2”.) Un objetivo dentro de TRINITI es reducir o incluso eliminar las microfisuras en entornos criogénicos. Actualmente, CETMA está trabajando para identificar todos los materiales termoplásticos que pueden satisfacer los requisitos de los recipientes a presión aeroespaciales.
REPUESTO:rejillas de piso de carga y pasajeros compuestos innovadores a gran escala para demostradores regionales en tierra de barriles de fuselaje de aeronaves - (JTI-CS2-2017-CfP07-REG-01-14). Iniciado en octubre de 2018, este proyecto de 18 meses tiene como objetivo fabricar rejillas de piso de pasajeros y carga a gran escala hechas con compuestos termoplásticos reforzados con fibra de carbono (TP). La producción altamente automatizada comprende el perfilado progresivo y la soldadura por inducción para el ensamblaje. El objetivo es reducir el peso y los costos recurrentes en comparación con las soluciones tradicionales de metales y compuestos termoendurecibles. Las rejillas de piso compuesto se ensamblarán en los demostradores de fuselaje de aviones regionales Clean Sky 2 para pruebas en tierra y se evaluarán para determinar el impacto técnico y económico, así como el rendimiento de resistencia a las llamas según las regulaciones FAR 25.583. El líder del tema es Leonardo, mientras que CETMA coordina el proyecto en colaboración con el fabricante de máquinas OMI S.r.l. (Fogliano Redipuglia, Italia).
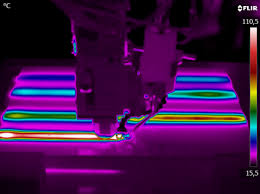
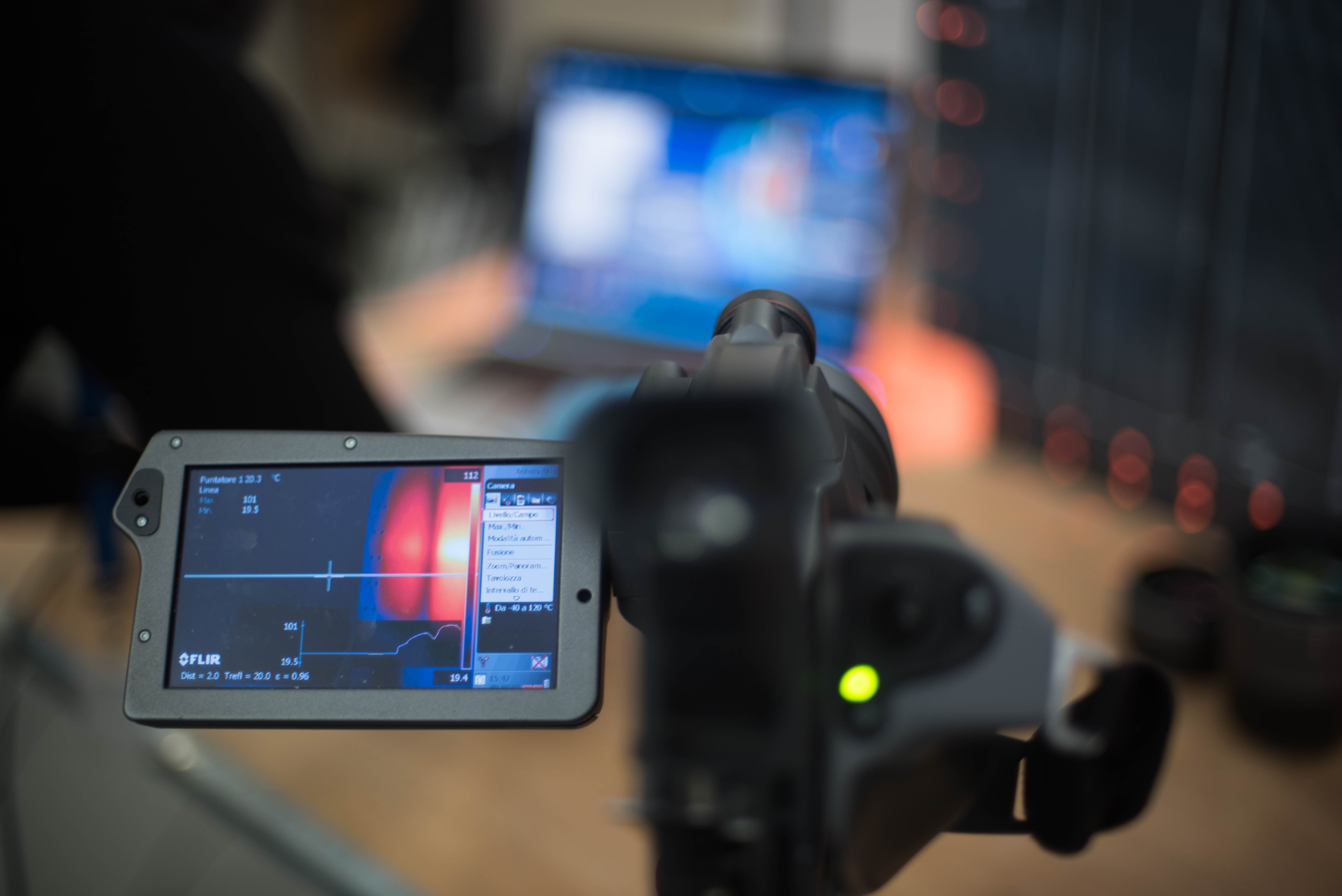
Una de las principales contribuciones de CETMA a SPARE es el desarrollo de la termografía infrarroja (IRT) para el seguimiento en línea del perfilado progresivo. Este proceso somete los rollos de laminado compuesto TP a compactación y calentamiento hasta que se alcanza la temperatura de proceso del material, la forma compleja y el espesor de diseño. “Sin embargo, es importante asegurarse de que las capas más internas experimenten la fusión completa de la matriz y la consolidación”, explica Passaro. “Además, hay una ventana de temperatura estrecha que asegura la fusión pero no degrada el polímero. IRT es un método sin contacto que mide la energía térmica radiada a través de la superficie de la pieza con alta precisión ”.
CETMA usó ventanas hechas de selenurio de zinc (ZnSe) para mirar dentro del equipo cerrado. Transparentes a las ondas IR, funcionan a temperaturas de hasta 500 ° C. Se construyeron dos de estas ventanas en la línea de perfilado progresivo del proyecto SPARE con cámaras IRT suspendidas en la parte superior para tener una vista casi perpendicular del material procesado. El software de control editable hizo posible monitorear, registrar y emitir alarmas si los valores caían fuera del rango objetivo definido.
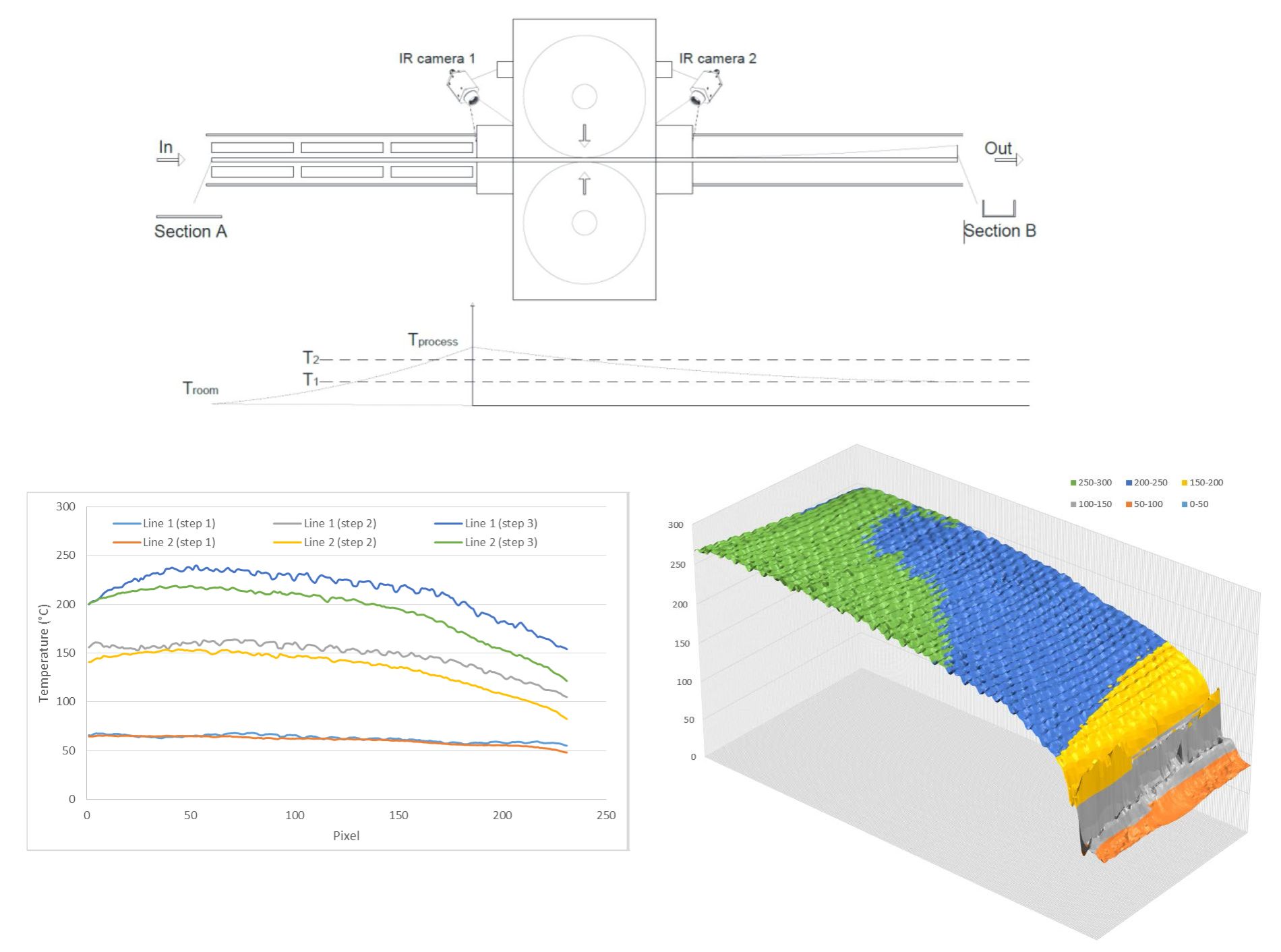
La uniformidad de la temperatura del material a través de la sección transversal del perfil se evaluó en los dos puntos límite:la línea 1 está cerca del paso de calentamiento y la línea 2 está más adelante en el proceso de formación. Cada uno se dividió en 3 pasos sucesivos (Fig. 19):fase inicial (paso 1), proceso de conformado iniciado (paso 2) y conformado con velocidad reducida (paso 3). IRT mostró que la temperatura en los bordes exteriores del laminado era más baja que en el área central, lo que provocó un calentamiento desigual y propiedades mecánicas. Una representación en 3D de las temperaturas de la superficie registradas por IRT (Fig. 20) proporcionó una ayuda visual para comprender mejor la distribución de la temperatura.
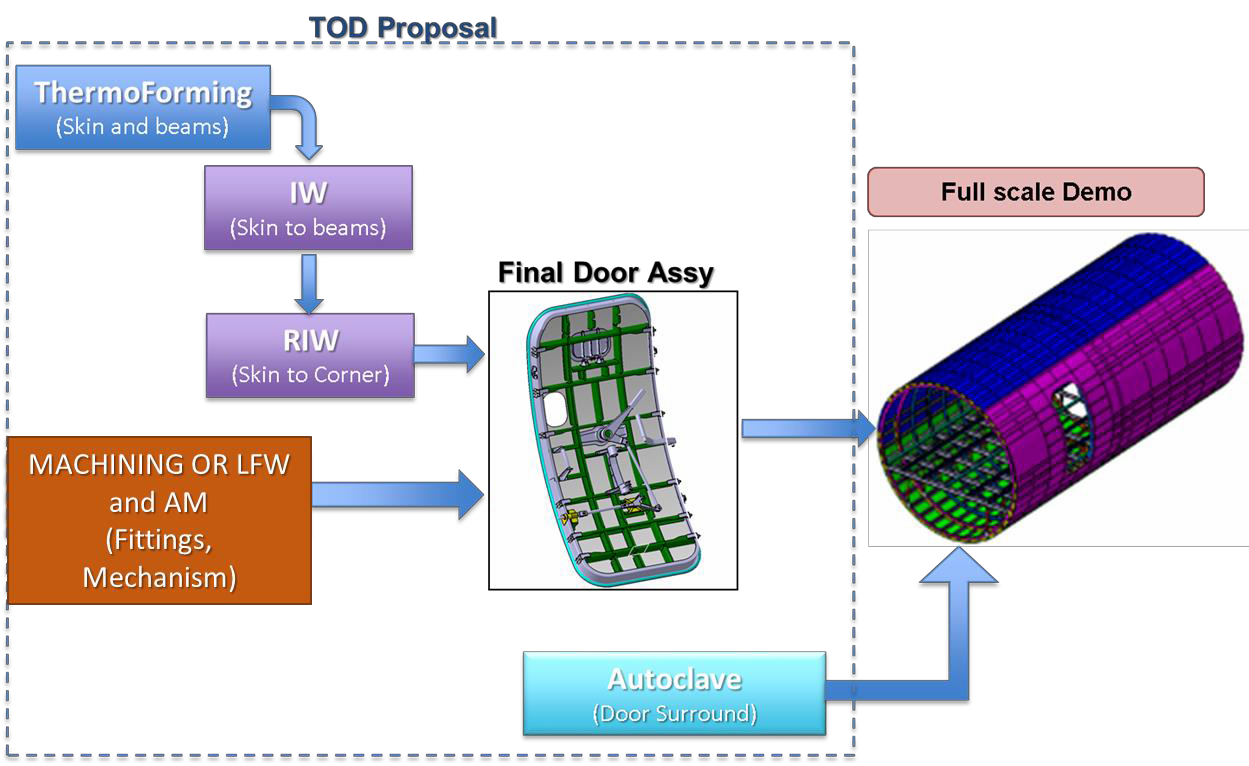
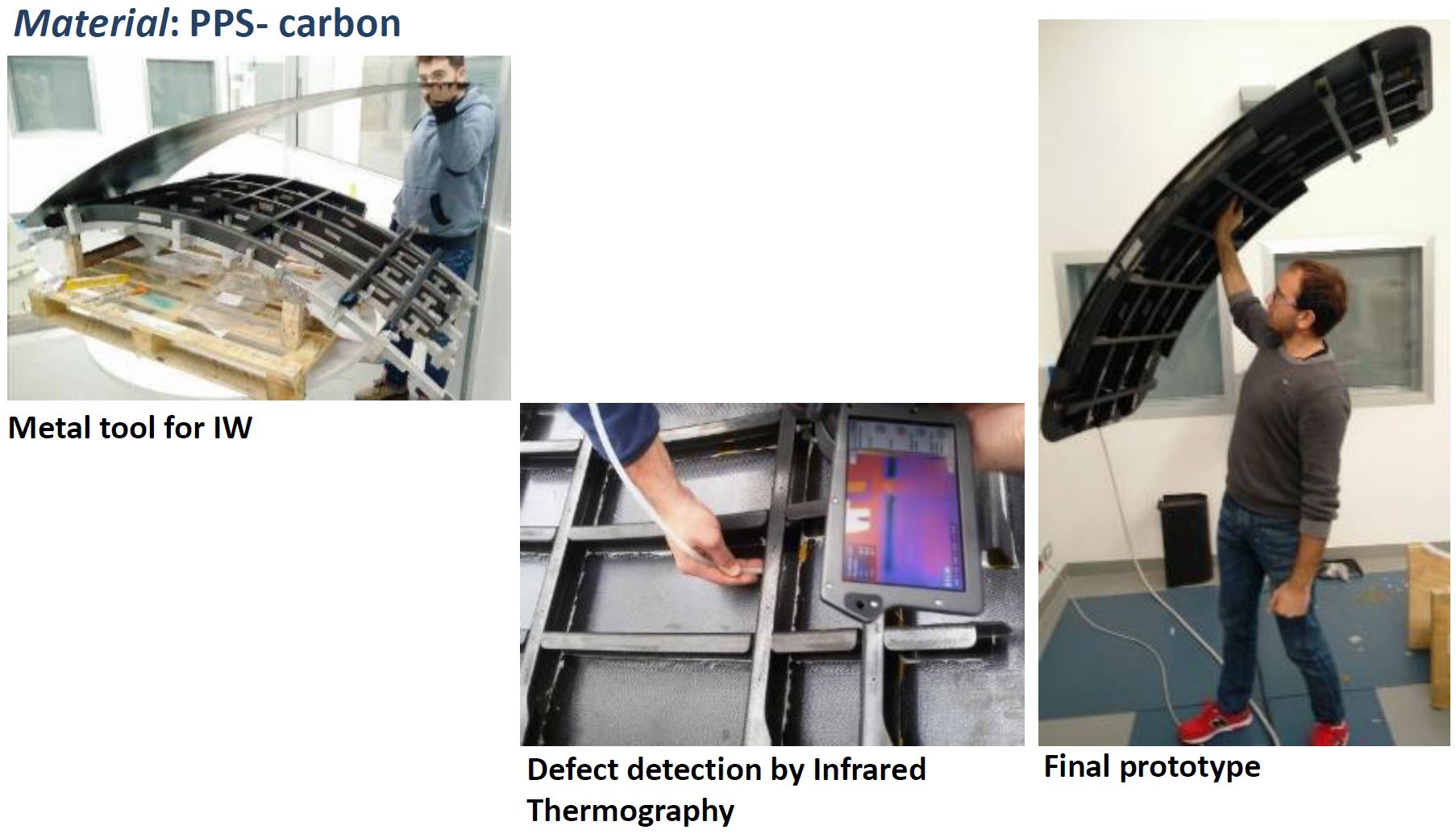
TOD - Termoplástico en puertas (JTI-CS2-2017-CfP07-REG-01-12). TOD tiene como objetivo desarrollar y validar la producción y el montaje rápidos de una puerta compuesta termoplástica a gran escala (incluidas las subestructuras del fuselaje) para un avión regional. TOD es parte de Clean Sky 2 Regional Aircraft IADP (Innovative Aircraft Demonstrator Platform), que lleva la integración de tecnologías desarrolladas en la fase uno de Clean Sky Green Regional Aircraft ITD (Innovative Technology Demonstrator) a un nivel superior de complejidad y madurez a través de dos bancos de pruebas voladores y tres grandes demostradores terrestres integrados. Liderado por Leonardo, CETMA trabajará con los socios del proyecto The Welding Institute (TWI, Cambridge, Reino Unido) y la empresa aeroespacial Tier 1 y de ingeniería / industrialización DEMA (Design Manufacturing SpA, Somma Vesuviana, Italia).
El enfoque propuesto incluye la optimización y validación del termoformado para la fabricación de componentes y los procesos de unión, como la soldadura por inducción (IW) y la soldadura por implante resistiva (RIW), que permiten la reducción de peso al eliminar los sujetadores mecánicos. TOD también promoverá la automatización de la industria 4.0 y el monitoreo en línea para respaldar la producción de alta velocidad de piezas de alta calidad (cero defectos) con un control de proceso sólido. Los beneficios esperados incluyen:
- Reducción de peso mínima del 15%
- Reducción de desperdicios y desechos en un 10% a través de sensores y monitoreo en línea
- Hasta un 75% de ahorro de energía en comparación con el procesamiento en autoclave estándar
- Reducción de los costos recurrentes mediante la fabricación inteligente adaptativa (mayor flexibilidad, menor costo de herramientas de línea completa)
- Emisiones mejoradas de CO2 durante la fabricación y operación de aeronaves más livianas.
CETMA participa en muchos otros proyectos de desarrollo. Un ejemplo es NHYTE (Nuevas aeroestructuras compuestas termoplásticas híbridas fabricadas por Out of Autoclave Continuous Automated Technologies) cuyo objetivo es demostrar aeroestructuras integradas innovadoras hechas de materiales de matriz termoplástica híbrida con capacidades multifuncionales.
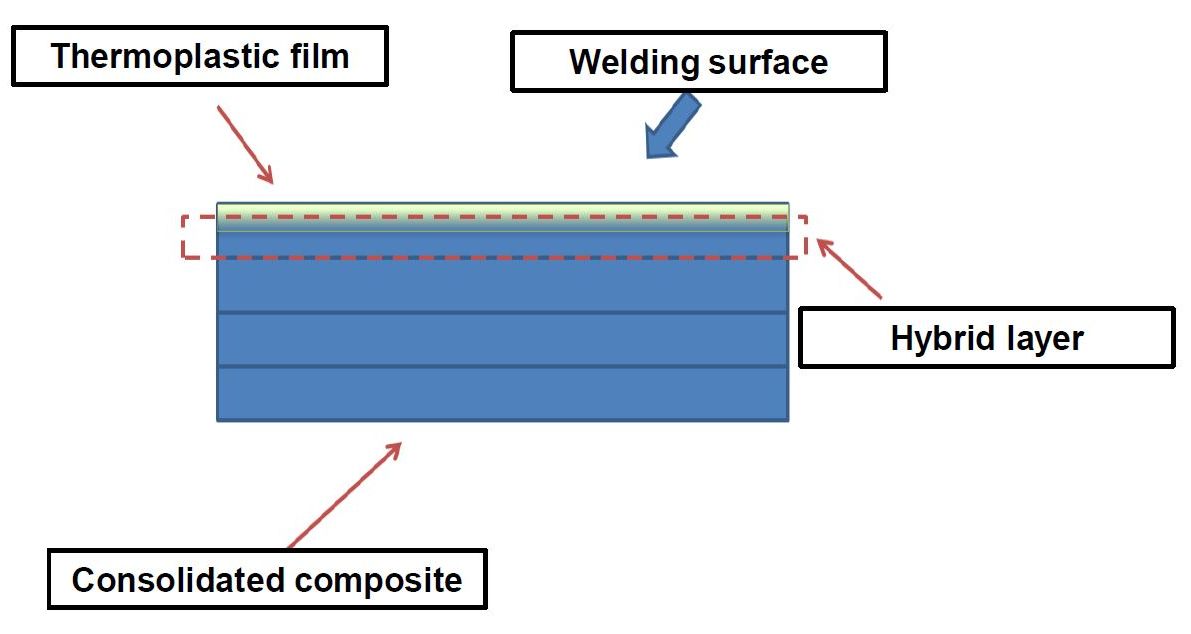
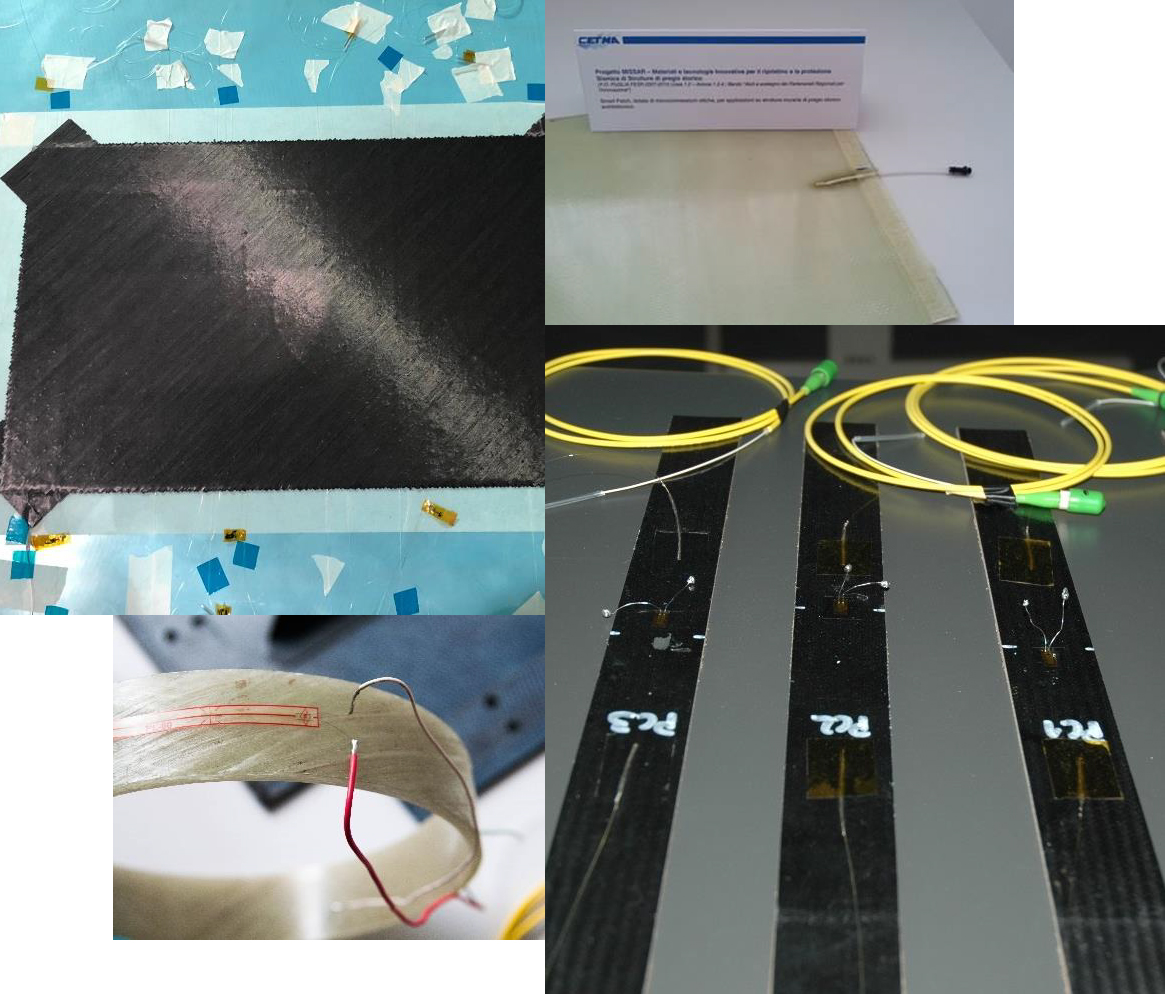
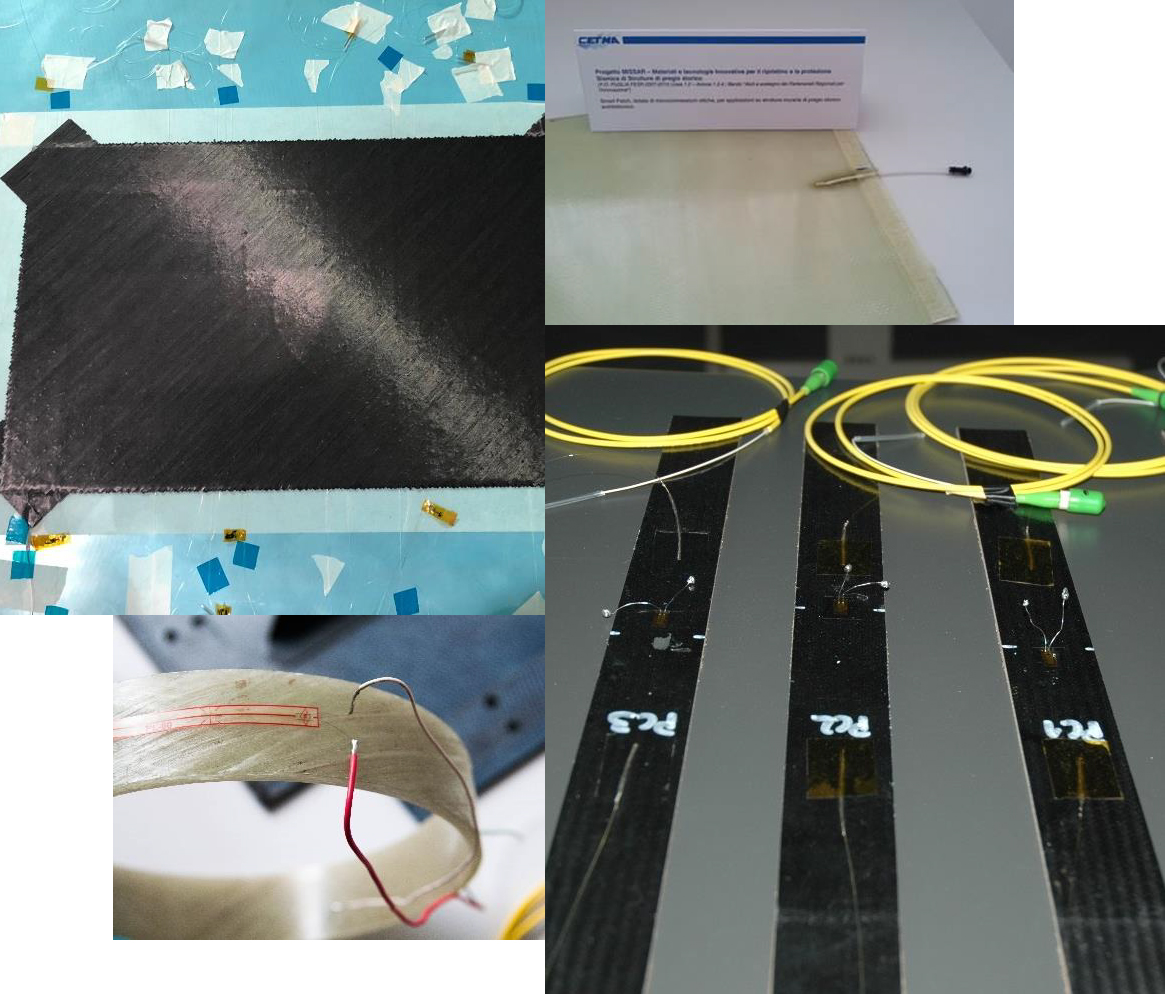
Financiado por el programa Horizonte 2020 y dirigido por NOVOTECH (Nápoles, Italia), NHYTE comenzó en septiembre de 2018 y estaba programado para finalizar en enero de 2020. El material híbrido de alto rendimiento se basa en un preimpregnado comercial de fibra de carbono / PEEK con PEI amorfo añadido. películas para permitir la consolidación in situ con colocación automatizada de fibra (ISC AFP) y luego ensamblar a través de la tecnología de soldadura por inducción patentada de CETMA. CETMA ha completado una amplia campaña de caracterización que comprende pruebas físico-mecánicas y virtuales del material compuesto híbrido y la configuración del proceso de soldadura por inducción.
Reciclaje de fibra de carbono
Otra área clave para CETMA es el reciclaje. El CIRCE El proyecto tiene como objetivo utilizar desechos de preimpregnado generados durante la fabricación de piezas compuestas reciclándolos en un compuesto de moldeo por compresión, que luego se utilizará para moldear insertos en los dedos de los pies para zapatos de seguridad. CETMA caracterizará esta materia prima secundaria y desarrollará un modelo numérico para predecir el desempeño estructural de las plantillas de calzado. Este modelo ayudará a analizar y verificar el comportamiento del impacto para cumplir con las normas de seguridad, y los resultados se utilizarán para refinar y finalizar el diseño de las inserciones de los dedos. El equipo italiano del proyecto incluye Base Protection (Barletta), el fabricante de componentes compuestos de automovilismo / piezas de automoción HP Composites (Ascoli Piceno), el especialista en máquinas y líneas de producción Elks Group (Ascoli Piceno) y Petroceramics (Stezzano).
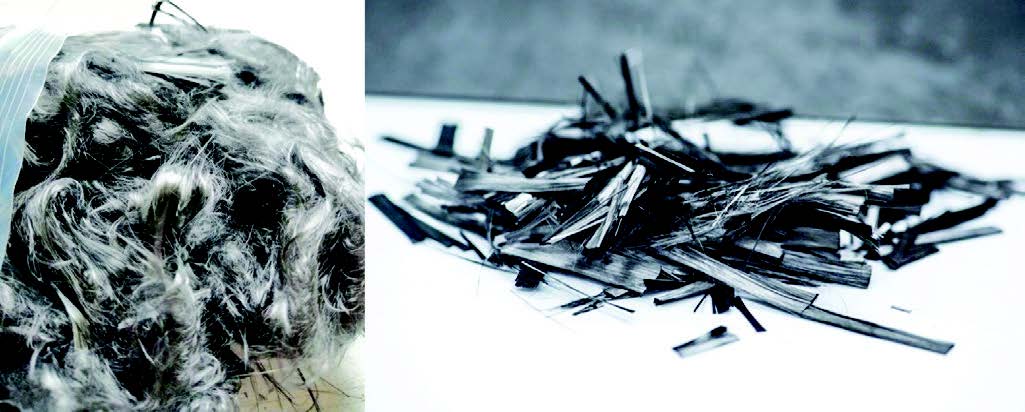
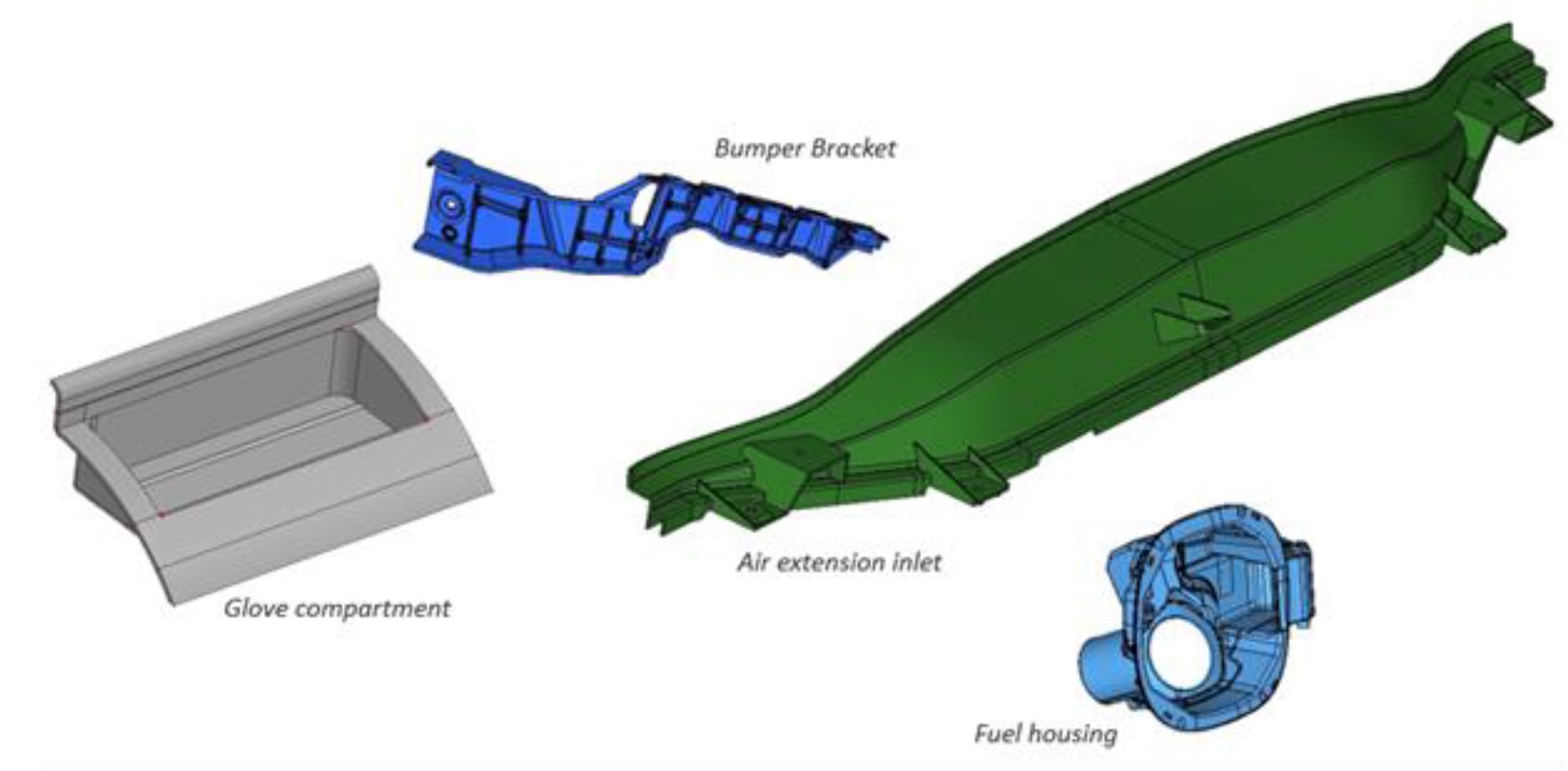
Quizás la mayor inversión de CETMA en reciclaje hasta la fecha ha sido a través de REVALUE proyecto dirigido a fibras de carbono RECICLADAS para composites de alto VALOR. Financiado por el Instituto Europeo de Innovación y Tecnología (EIT, Budapest, Hungría), el objetivo del proyecto REVALUE es tomar fibra de carbono reciclada (RCF) proporcionada por el productor líder ELG Carbon Fiber (Coseley, Reino Unido) mediante pirólisis y combinarla con polímeros termoplásticos vírgenes y reciclados para reemplazar los materiales actuales utilizados por Centro Ricerche Fiat (CRF, Turín, Italia) para la producción de componentes automotrices seleccionados.
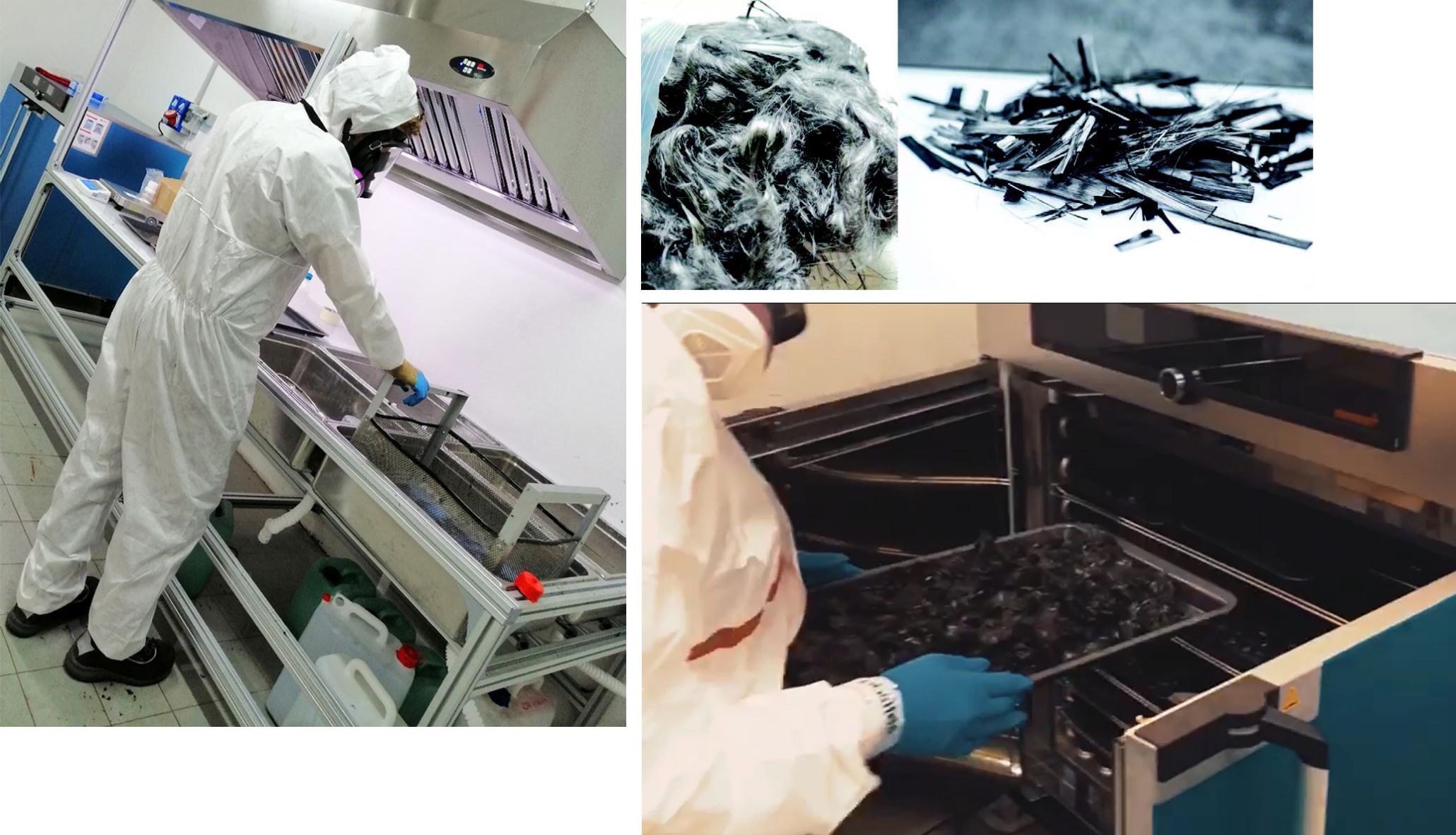
Sin embargo, como se indica en la revista JEC Composites de enero-febrero de 2020 artículo, “Nueva formulación de apresto para fibras de carbono recicladas” por Alessandra Passaro, et. al., el RCF producido por pirólisis no tiene apresto, lo que hace que las fibras quebradizas sean propensas a romperse con frecuencia durante la manipulación, así como a la separación de los hilos de fibra en filamentos, lo que da como resultado una forma "esponjosa" enredada con baja densidad aparente. Como parte de REVALUE, CETMA desarrolló una formulación específica de apresto para RCF, compatible con polipropileno (PP) virgen o reciclado y PA6. Luego evaluó la capacidad de dimensionamiento para mejorar la procesabilidad de RCF y aumentar la interfaz con las matrices termoplásticas seleccionadas.
Para ello, CETMA desarrolló una planta piloto de calibrado de RCF, capaz de aplicar el calibrado en cantidades de kilogramos y, al mismo tiempo, evaluar el efecto de los principales parámetros en el proceso de deposición. La planta consta de tres estaciones principales:tratamiento de encolado y lavado de las fibras; manipular las fibras secas antes y después del tratamiento; y secar en horno las fibras. Se pueden tratar cuatro kilogramos de RCF por día en un ciclo continuo.
Los RCF encolados de CETMA fueron luego utilizados por el centro de investigación francés CEA y el mezclador francés SUEZ para producir un compuesto de moldeo utilizando polímeros termoplásticos vírgenes y reciclados. Se completó la caracterización físico-química de los compuestos y se verificó la capacidad del encolado CETMA para mejorar el rendimiento mecánico final del compuesto.
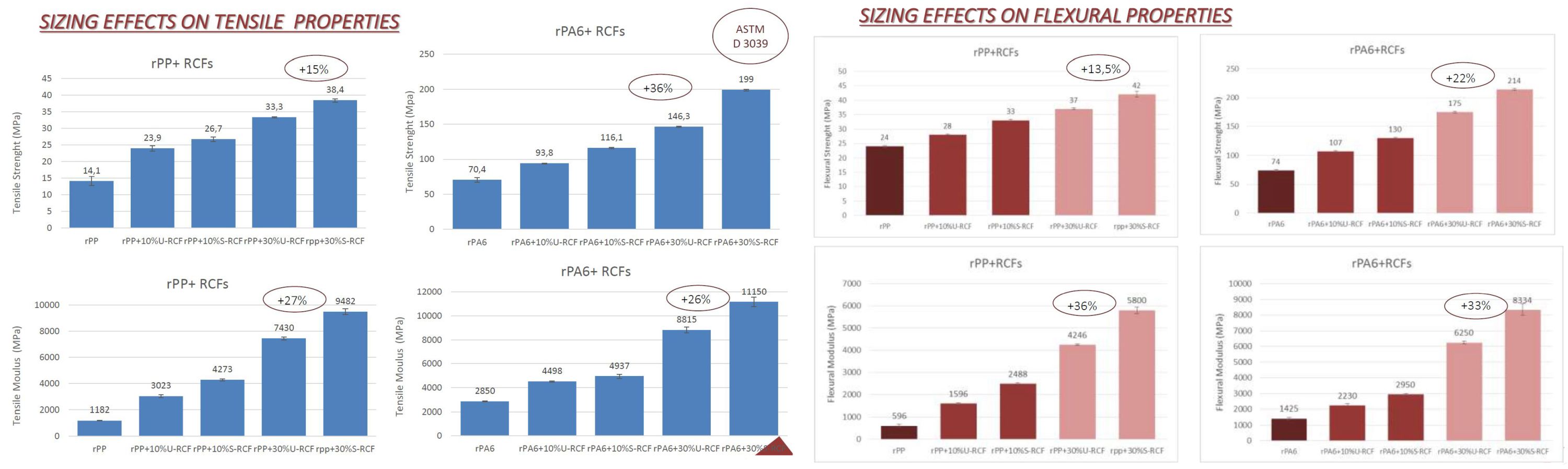
Los innovadores compuestos de moldeo RCF se utilizaron luego para moldear por inyección componentes semiestructurales automotrices que actualmente están hechos con PP o PA6 reforzado con fibra de vidrio. Más allá de la ventaja obvia en el reciclaje y la reutilización de materiales, también se demostró la reducción del peso del vehículo, el consumo de combustible y las emisiones de CO2.
Fuera de REVALUE, CETMA también ha desarrollado y evaluado aún más el dimensionamiento para RCF en múltiples procesos de composites, incluido el moldeo por compresión, la infusión al vacío y RTM, mostrando propiedades mejoradas en todos los casos.
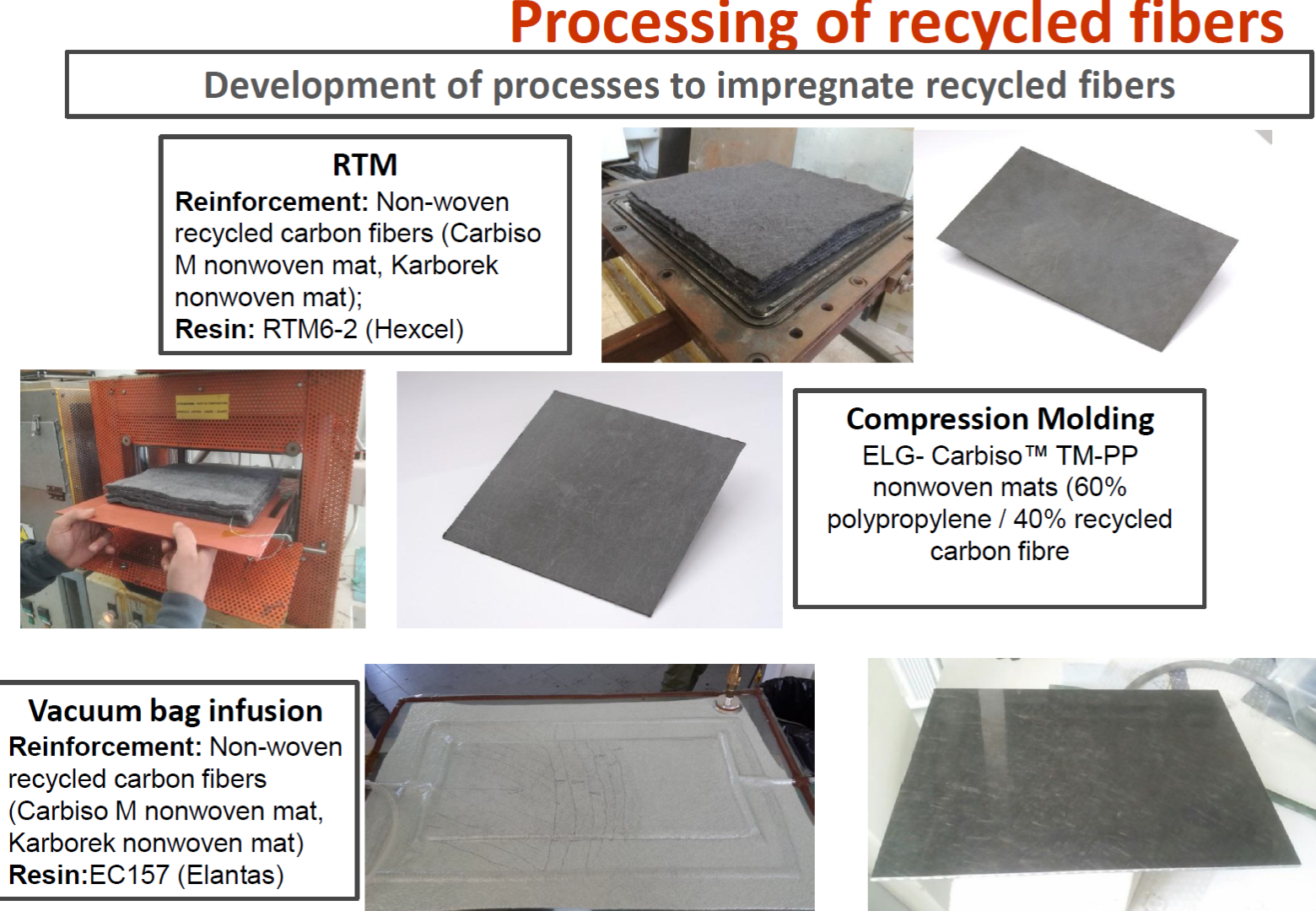
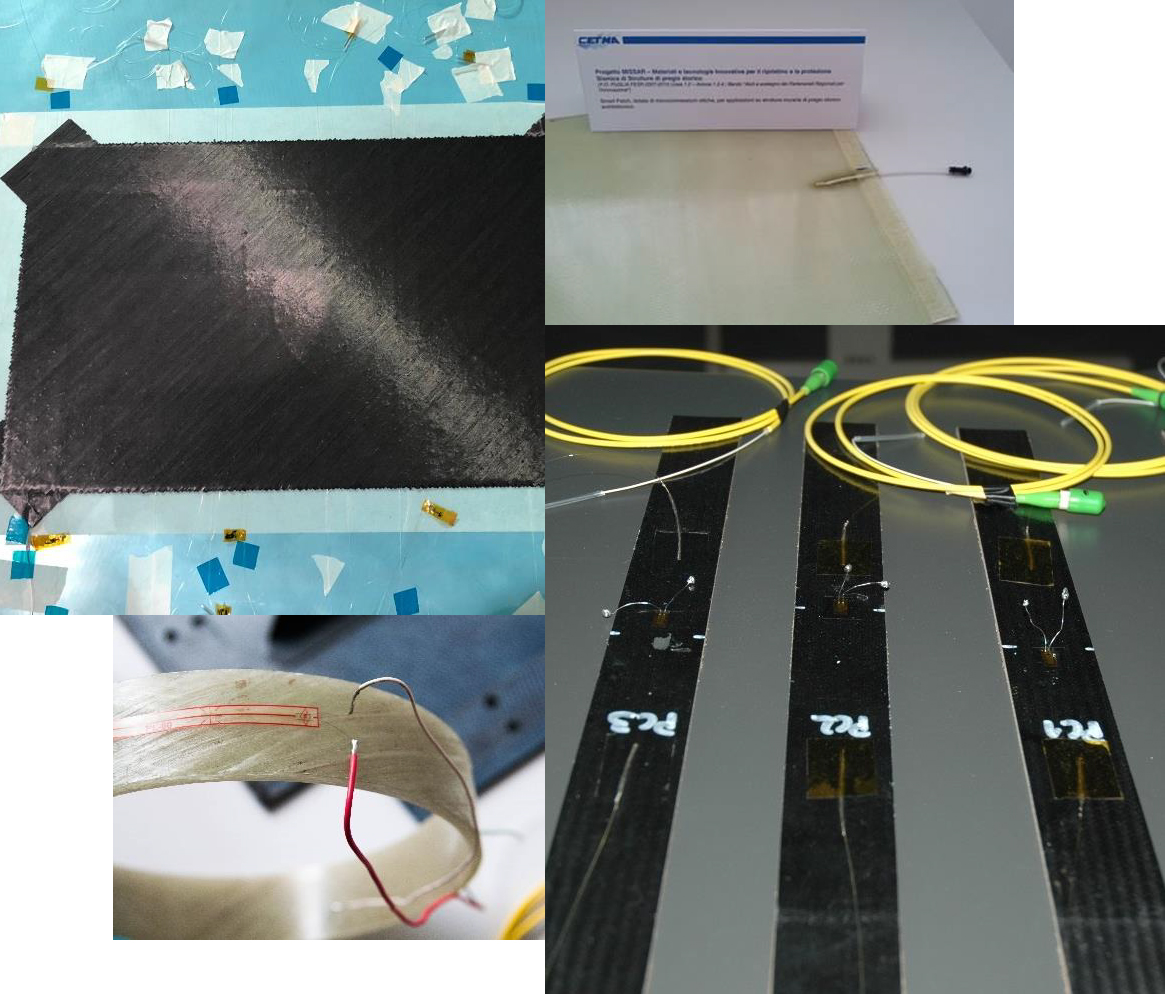
Supervisión del estado estructural (SHM)
Esta última área clave de la actividad de compuestos para CETMA también es un énfasis creciente en la industria. “Tenemos muchos años de experiencia en la aplicación de SHM para aplicaciones de construcción y edificación”, señala Passaro. “Y también hemos trabajado mucho con SHM en composites. Sabemos que esto será importante para aplicaciones futuras y estamos interesados en seguir trabajando con los fabricantes de compuestos y la industria para impulsar esta tecnología ”.
Resina
- Personalización de sensores ultrasónicos para la optimización y el control de procesos compuestos
- Resinas epoxi reprocesables, reparables y reciclables para composites
- Combinación de medidas dieléctricas de CA y CC para el control del curado de compuestos
- Composites One e IACMI organizarán un taller de dos días
- Medición de temperatura dentro de materiales compuestos y líneas de unión
- TPAC y TPRC desarrollan un proceso de reciclaje de compuestos termoplásticos
- El aditivo PES aumenta la resistencia a la fractura y al micro-agrietamiento en compuestos epoxi
- SABIC y Nottingham Spirk se asocian para acelerar el desarrollo de la innovación
- Al servicio del mundo de los compuestos en Israel y los EE. UU.
- Desafíos de corte:compuestos de matriz mixta y compuestos reforzados con fibra
- ABB Robotics:Innovación tecnológica e I+D en robótica