Herramientas aditivas híbridas de gran formato:moldes más ligeros, más rápidos y menos costosos para piezas grandes
Durante más de tres décadas, la aviación comercial ha adoptado cada vez más los materiales compuestos. De hecho, más de la mitad de los componentes estructurales críticos de varios modelos de aviones comerciales importantes en la actualidad son compuestos. A medida que el uso de estos materiales ha crecido en términos de volumen y tamaño de las piezas, se ha vuelto cada vez más difícil construir herramientas, especialmente herramientas asequibles, para prototipar y fabricar más rápidamente estas piezas. Por ejemplo, las alas del A350 XWB de Airbus SE (Leiden, Países Bajos) tienen 32 metros de largo por 6 metros de ancho y representan algunas de las estructuras de aviación compuestas más grandes jamás producidas.
"Ahora existen tecnologías de fabricación tan revolucionarias en el mercado que podemos esperar grandes pasos en la evolución de las herramientas, ayudándonos a afrontar los desafíos que enfrentamos en el desarrollo de componentes compuestos de aeronaves", señala M. Pilar Muñoz López, ingeniera de fabricación de compuestos en Planta de Airbus en Illescas, España. “Para nosotros es crucial investigar estas tecnologías, capacidades y limitaciones para poder estar preparados para el futuro”.
Dado que las herramientas representan una proporción significativa de los costos totales del programa para las piezas de aeroestructura, y dado el tamaño cada vez mayor de esas piezas, se necesitan nuevas opciones de herramientas con menores costos y plazos de entrega. Airbus, Northrop Grumman Aeronautics Systems - Aerospace Structures Business Unit (Clearfield, Utah, EE. UU.) Y la Universidad completaron recientemente un interesante estudio sobre herramientas híbridas de gran formato fabricadas aditivamente (LFAM) para prototipos y piezas de aeroestructuras de producción de bajo volumen. del Dayton Research Institute (UDRI, Dayton, Ohio, EE. UU.) con resultados alentadores.
Controlar los problemas de expansión térmica
La mayoría de las aeroestructuras de plástico reforzado con fibra de carbono (CFRP) se producen a partir de preimpregnados de matriz epoxi. Para moldear tales piezas, las herramientas deben resistir temperaturas de curado en horno o autoclave de hasta 180 ° C / 356 ° F. Además, dado el muy bajo coeficiente de expansión térmica (lineal) de CFRP (CLTE o CTE), es fundamental igualar, lo más cerca posible, los CLTE de herramientas y materiales de moldeo a temperatura ambiente y temperaturas elevadas. Esto asegura que los moldes mantengan las dimensiones para que las piezas resultantes también cumplan con los requisitos dimensionales. Para evitar distorsiones o tensiones en las estructuras finales, también es importante evitar el uso de un material de herramientas que se enfríe más rápido que el material de la pieza. Como consecuencia, las herramientas más comunes utilizadas para moldear grandes aeroestructuras de CFRP están hechas de CFRP mismo o de Invar, una aleación ferrosa de níquel y hierro conocida por su bajo CLTE. Ambos son costosos y pueden tener tiempos de entrega importantes. Además, Invar es difícil, requiere mucho tiempo de mecanizar y es pesado de enviar. Si bien las herramientas de acero o aluminio pueden reducir los costos, sus valores CLTE relativamente más altos limitan el uso en muchas aplicaciones, particularmente al moldear piezas grandes o largas.
Muchos estudios del sector público y privado han evaluado herramientas fabricadas aditivamente impresas en materiales termoplásticos y concluyeron que potencialmente ofrecen beneficios que incluyen costos más bajos y plazos de entrega más cortos para producir compuestos laminados termoendurecibles. Desafortunadamente, las herramientas LFAM basadas en polímeros tienen problemas como la porosidad de la herramienta, lo que puede provocar una pérdida significativa de vacío a temperaturas / presiones de curado. La solución de este problema requiere un reelaborado de relleno de herramientas adicional y recubrimientos de superficie. Un desafío aún mayor son los valores de CLTE altamente anisotrópicos, debido a la alineación del relleno de la materia prima en el plano durante la extrusión / impresión, lo que puede conducir a diferencias de expansión / contracción de 5 a 10 veces mayores en el eje Z que en los ejes de impresión X e Y. Eso hace que sea un desafío obtener piezas dimensionalmente precisas de forma repetible y reproducible, especialmente cuando las piezas son grandes, tienen una relación de aspecto alta y / o presentan superficies complejas.
“Todos los interesados en las herramientas aditivas se han enfrentado a los mismos problemas de porosidad y expansión térmica incontrolada con pocas formas efectivas de abordar esos problemas”, explica Scott Huelskamp, líder del equipo UDRI, desarrollo de procesos de fabricación avanzados, División de Materiales Estructurales. "Hay muchas personas que quieren usar herramientas de AM, pero están esperando que alguien resuelva estos problemas".
Dado el potencial de AM para reducir el costo de las herramientas y los tiempos de entrega, la industria ha centrado un esfuerzo considerable en abordar los problemas de expansión mediante la exploración de nuevos materiales imprimibles, modificaciones de hardware de impresoras y enfoques de modelado innovadores. Por ejemplo, algunos grupos han desarrollado un “valor de compensación” para diseñar herramientas de AM para abordar los diferenciales de CLTE. Sin embargo, Huelskamp señala que determinar cuál El valor de compensación a utilizar es difícil y propenso a errores. Además, estos enfoques han sido ineficaces para las herramientas de cavidad hembra y las herramientas con características de atrapamiento a lo largo de su longitud que crean condiciones de bloqueo de matriz capaces de dañar las piezas durante el ciclo térmico de la herramienta.
"No existe un factor de compensación que vaya a solucionar ese tipo de problema", agrega. “Hasta la fecha, ningún estudio de herramientas AM ha abordado por completo la necesidad de valores CTE bajos e isotrópicos a temperaturas elevadas. Sin esta característica, los tamaños y geometrías de las herramientas siempre serán limitados, y las herramientas más grandes sufrirán errores dimensionales más altos a las temperaturas de curado ”.
En un esfuerzo por probar nuevos enfoques para resolver los desafíos de las herramientas de LFAM, varias empresas miembro emprendieron un proyecto de 18 meses bajo los auspicios del Institute for Advanced Composites Manufacturing Innovation (IACMI, Knoxville, Tennessee, EE. UU.) Y con el apoyo de EE. UU. Departamento de Energía y Empleos de Ohio (Columbus, Ohio). El equipo estaba dirigido por UDRI e incluía a Airbus y Northrop Grumman. Estas organizaciones habían colaborado previamente en otras investigaciones, tanto dentro como fuera de la IACMI, y por lo tanto estaban familiarizadas con las capacidades de cada una.
Enfoque de "fuerza bruta"
UDRI ya tenía una experiencia considerable trabajando en estudios de herramientas AM y es un miembro activo de America Makes (Youngstown, Ohio, EE. UU.), El consorcio AM de EE. UU. Además, el instituto había realizado una investigación para la Fuerza Aérea de EE. UU. Que involucraba estructuras AM con soportes metálicos, y ha trabajado con Cincinnati Inc. (Harrison, Ohio, EE. UU.), Productor de impresoras de Fabricación Aditiva de Grandes Áreas (BAAM), en herramientas AM puras.
“También habíamos estado trabajando con compositores personalizados en nuevas materias primas para impresoras 3D, pero nada de lo que estábamos haciendo parecía estar avanzando mucho y no sabíamos que nadie más tuviera más éxito que nosotros”, recuerda Huelskamp. “Fue entonces cuando tuvimos la idea de abordar el problema de otra manera. Si no pudiéramos cambiar la forma en que se comportan los materiales de AM o predecir ese comportamiento directamente , entonces quizás podríamos obligarlos a comportarse como queríamos indirectamente . " Tomando lo que Huelskamp llama un enfoque de "fuerza bruta", UDRI propuso un estudio LFAM híbrido que produciría herramientas de aeroestructura aplicando convencionales Pieles de CFRP para compuesto termoplástico Núcleos AM.
Los objetivos del proyecto eran simples:encontrar un método menos costoso y más rápido para fabricar herramientas grandes para aeroestructuras. El equipo buscó una opción que redujera los costos en un 50% y produjo al menos 10 prototipos aceptables o piezas de producción de bajo volumen para pruebas posteriores
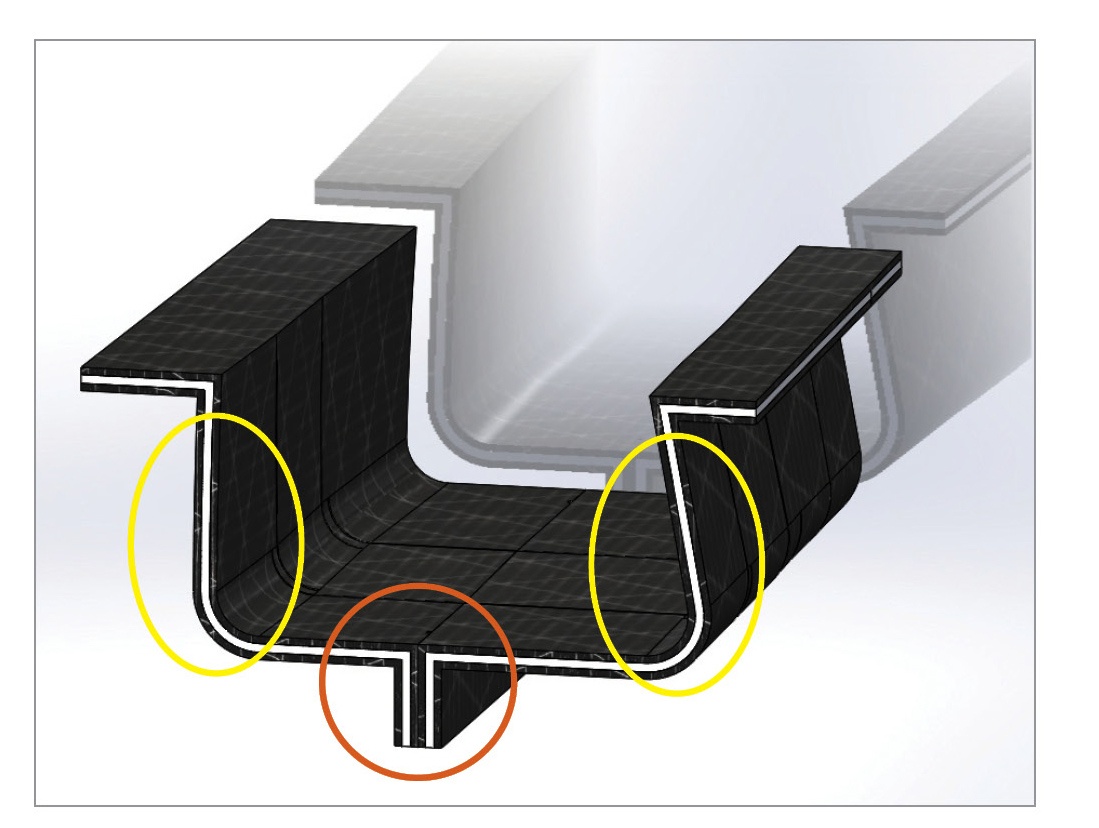
El equipo decidió utilizar una estructura tipo sándwich para producir herramientas de un solo lado para una sección de un larguero de ala genérico utilizando datos de herramientas de Airbus. Aparte de producir herramientas para moldear solo una sección del larguero en C a gran escala, debido a las limitaciones de espacio en la instalación de UDRI, no se realizó ningún cambio de diseño importante.
Se diseñó una herramienta hembra para garantizar que la geometría de la pieza crítica se formara utilizando superficies labradas. Esta herramienta de tapa de larguero tenía un ligero ángulo hacia adentro que creaba un tiro negativo y una condición de bloqueo de la matriz, al ser una herramienta de una sola pieza. Esto llevó a los investigadores a modificar el diseño a una herramienta dividida que se selló con juntas / cordstock. Para mitigar el riesgo, el equipo comenzó con una herramienta de subescala de 0,6 metros / 2,0 pies para probar el concepto. Una vez que el proceso de desarrollo de la herramienta y las piezas del prototipo producidas en esa herramienta se probaron y se encontró que funcionaban, el equipo construyó una herramienta más grande de 3.3 metros / 11 pies de largo para moldear una sección más grande del larguero para la prueba del prototipo.
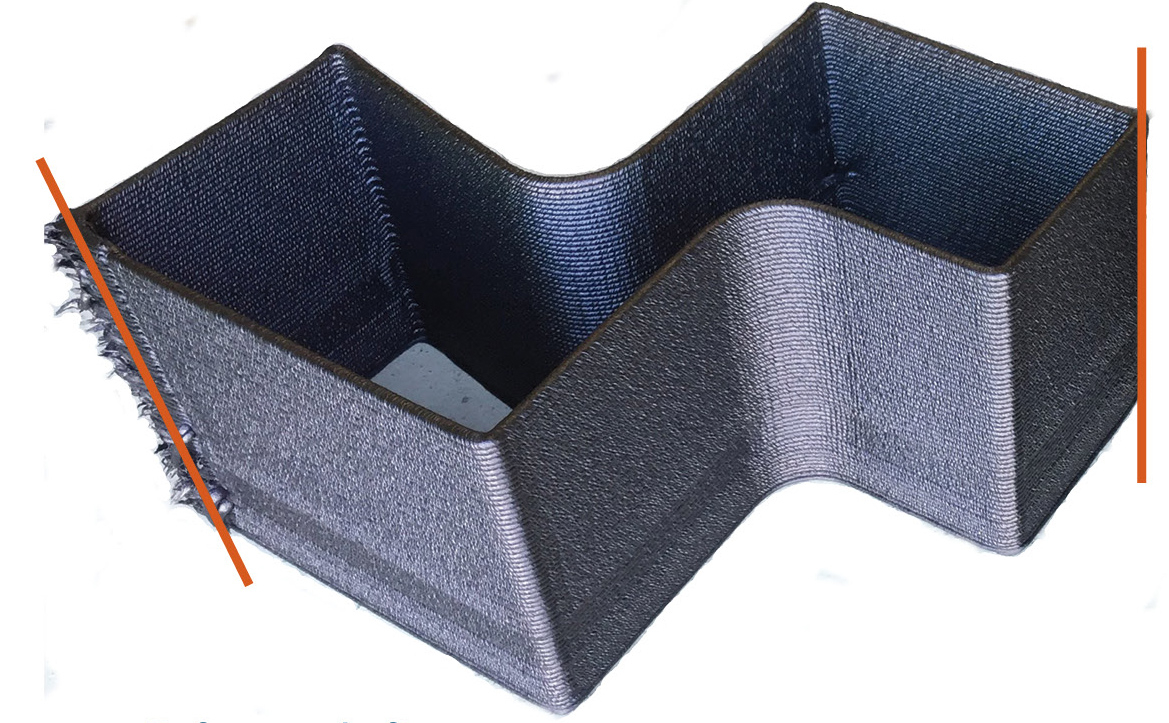
Dado que las herramientas de CFRP tienen un valor CLTE tan bajo, son más livianas que Invar y la herramienta era para piezas de producción de prototipos / de bajo volumen, el equipo decidió usar máscaras de CFRP para restringir el núcleo AM. Las pieles se hicieron con preimpregnado de herramientas epoxi Hextool M81 de Hexcel (Corp., Stamford, Connecticut, EE. UU.).
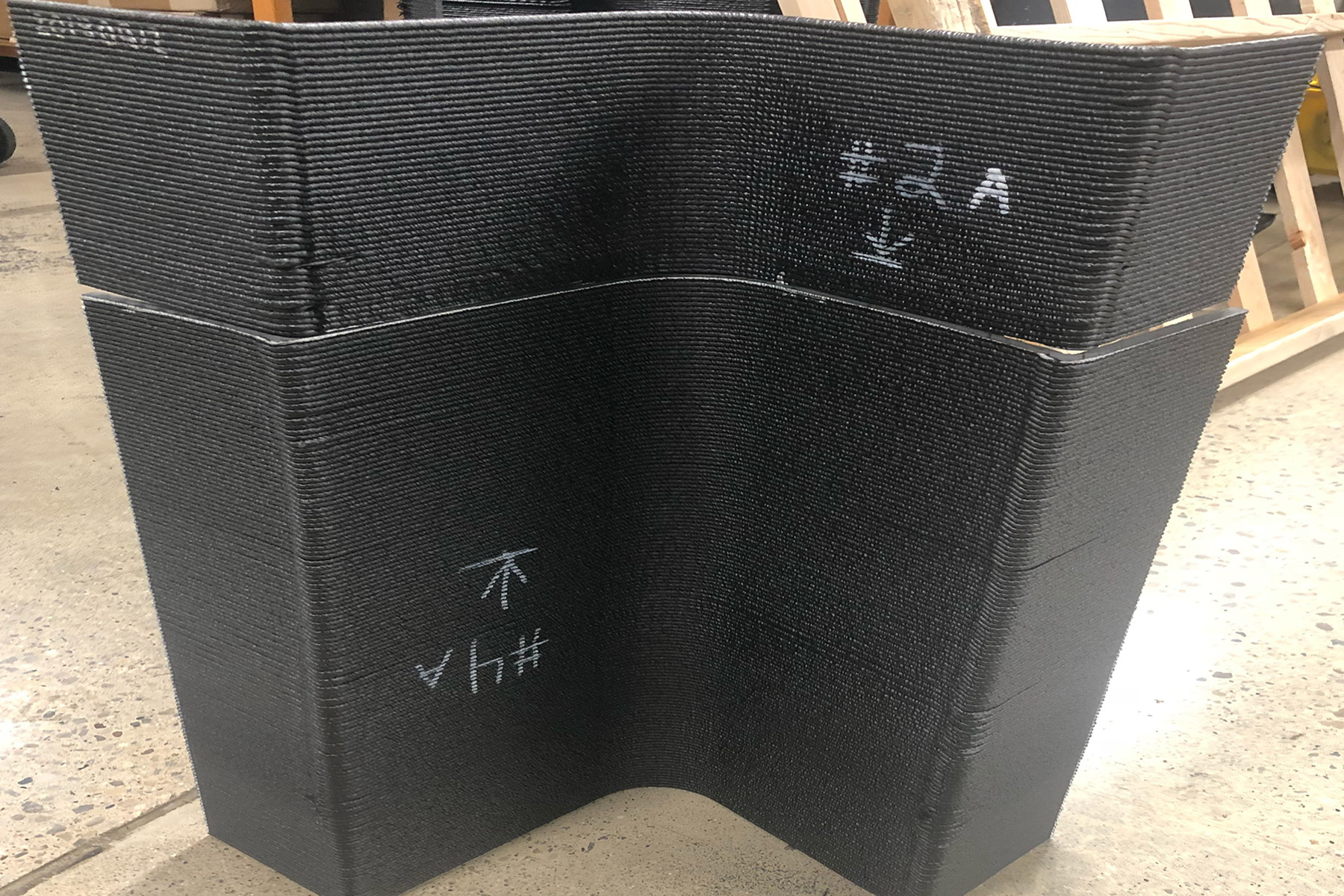
La imagen superior muestra una sección de la mitad derecha de la subescala, herramienta impresa en BAAM con líneas rojas que indican líneas de corte después de la impresión. La imagen inferior muestra la mitad derecha de la herramienta después de unir las secciones. Crédito de la foto:Instituto de Investigación de la Universidad de Dayton.
El formato del material era un tapete de 2.000 gramos por metro cuadrado / 59 onzas por yarda cuadrada de fibra de carbono cortada impregnada con epoxi endurecido 8552 de Hexcel. Este material se usa a menudo para herramientas compuestas debido a sus propiedades casi isotrópicas, que permiten el mecanizado posterior al molde sin movimiento de la herramienta que de otro modo podría ser causado por la relajación de la tensión residual.
Dado que el núcleo se imprimiría en una impresora Cincinnati Inc. BAAM 1000 en Additive Engineering Solutions (Akron, Ohio, EE. UU.), Y dado que UDRI y Cincinnati tenían una experiencia significativa trabajando con polieterimida termoplástica de alta temperatura (PEI), seleccionaron PEI reforzado con fibra de carbono corto al 20% (Thermocomp EX004EXAR1 Ultem) de SABIC, (Riyadh, Arabia Saudita) para imprimir un núcleo con forma casi neta. (La presencia de fibras de carbono estabiliza el polímero durante la impresión y evita que se desplome; en la estructura terminada, las fibras reducen el CLTE en la dirección de impresión). Para mantener bajos los costos, el núcleo funcionó como el maestro de herramientas y los revestimientos de las caras se laminaron directamente hasta el núcleo sin adhesivo, pero con alguna modificación en la superficie del núcleo que está cubierta por la propiedad intelectual (IP) desarrollada durante el proyecto. Ese enfoque fue efectivo, sin delaminación incluso después de múltiples ciclos térmicos.
Fabricación condensada
En la fabricación convencional de herramientas de CFRP para aeroestructuras, primero se crea un maestro de bajo costo. Esto generalmente implica unir bloques de tablero de herramientas en un horno o autoclave, luego mecanizar la estructura monolítica a la geometría de la pieza deseada. Luego, el material de las herramientas se coloca, se ensaca y se cura en el maestro en un autoclave. Después del desmoldeo y la limpieza, se une una estructura de respaldo a la herramienta y la superficie de la herramienta se vuelve a mecanizar para garantizar una buena tolerancia geométrica y un acabado superficial.
Con herramientas híbridas de AM, el equipo desarrolló un proceso de fabricación condensado para reducir el tiempo de entrega y los costos. Primero, se imprimió en 3D un núcleo de forma casi neta (maestro de herramientas) (en fibra de carbono corta / PEI). A continuación, el preimpregnado de herramientas de CFRP se laminó directamente en ambos lados del núcleo (con cúmulos en caliente entre las capas uno, cuatro y siete según las recomendaciones del proveedor). A continuación, toda la estructura se embolsa al vacío y se cura en autoclave.
Proceso de fabricación condensado para la herramienta C-spar de subescala.
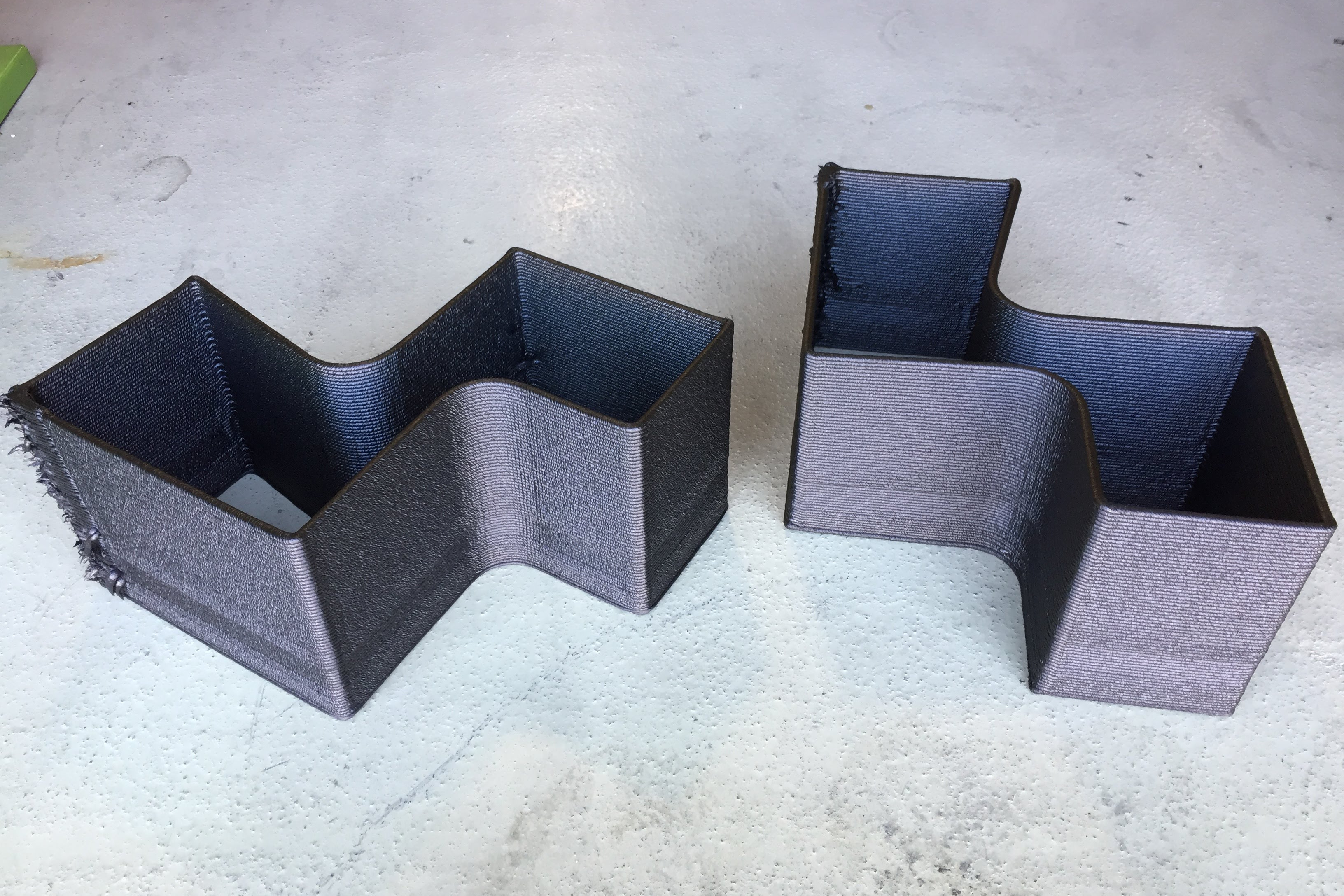
Paso 2:corte la impresión BAAM por la mitad y en mitades izquierda y derecha.
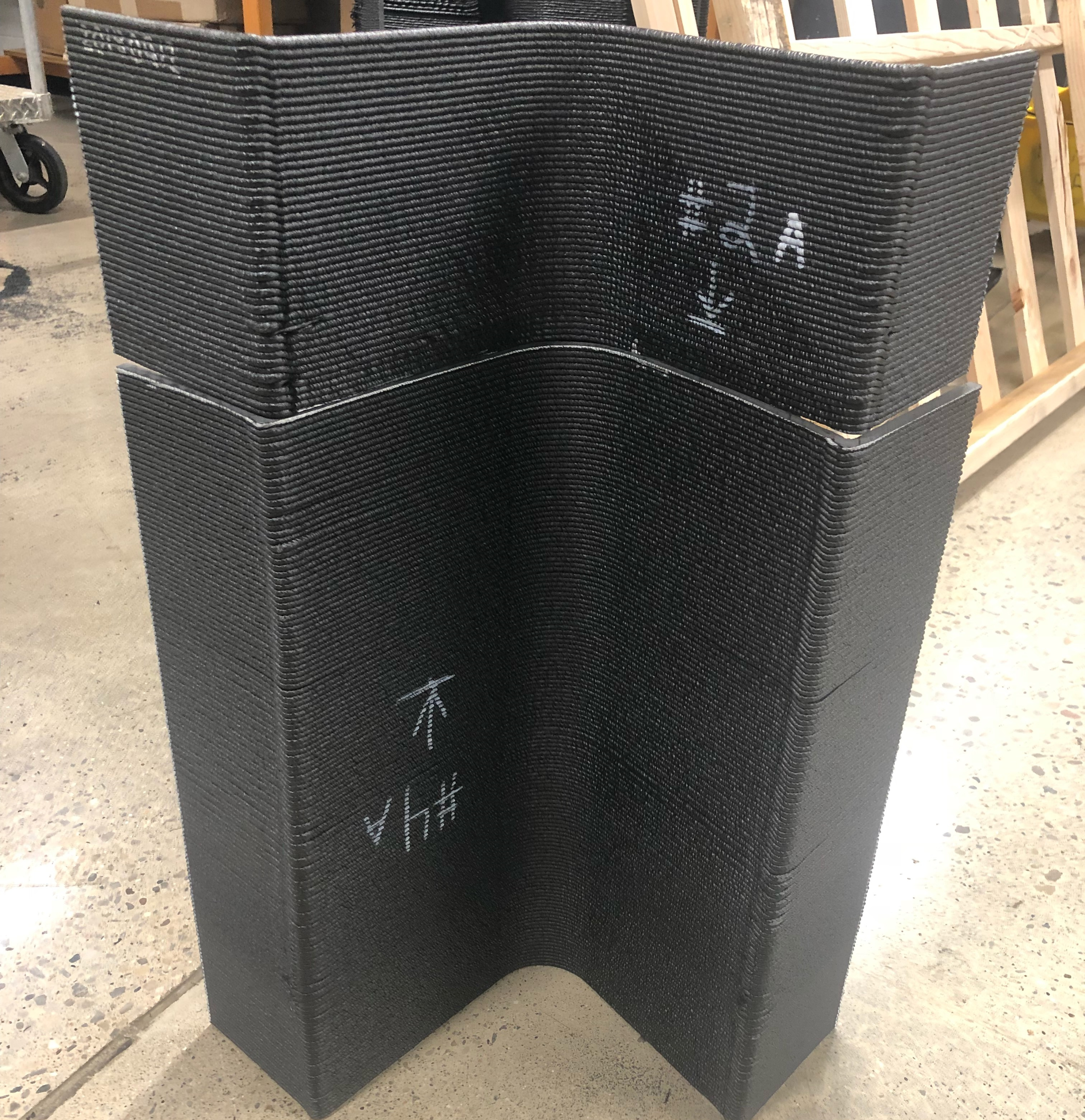
Paso 3:Pegue la impresión BAAM para lograr la longitud requerida y deje curar.
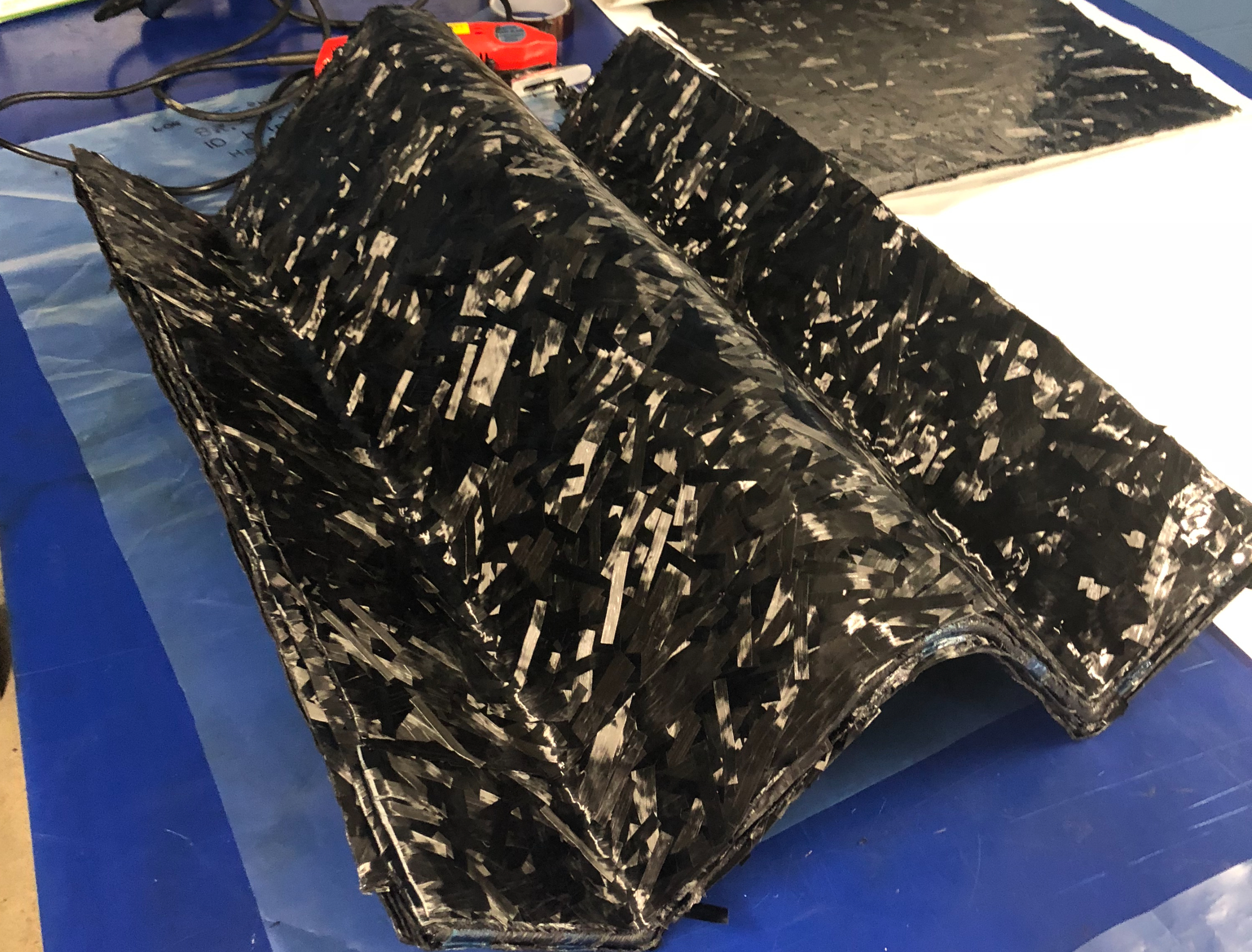
Paso 4:lamine el preimpregnado de herramientas a ambos lados del núcleo con disgregadores en caliente según las instrucciones del fabricante.
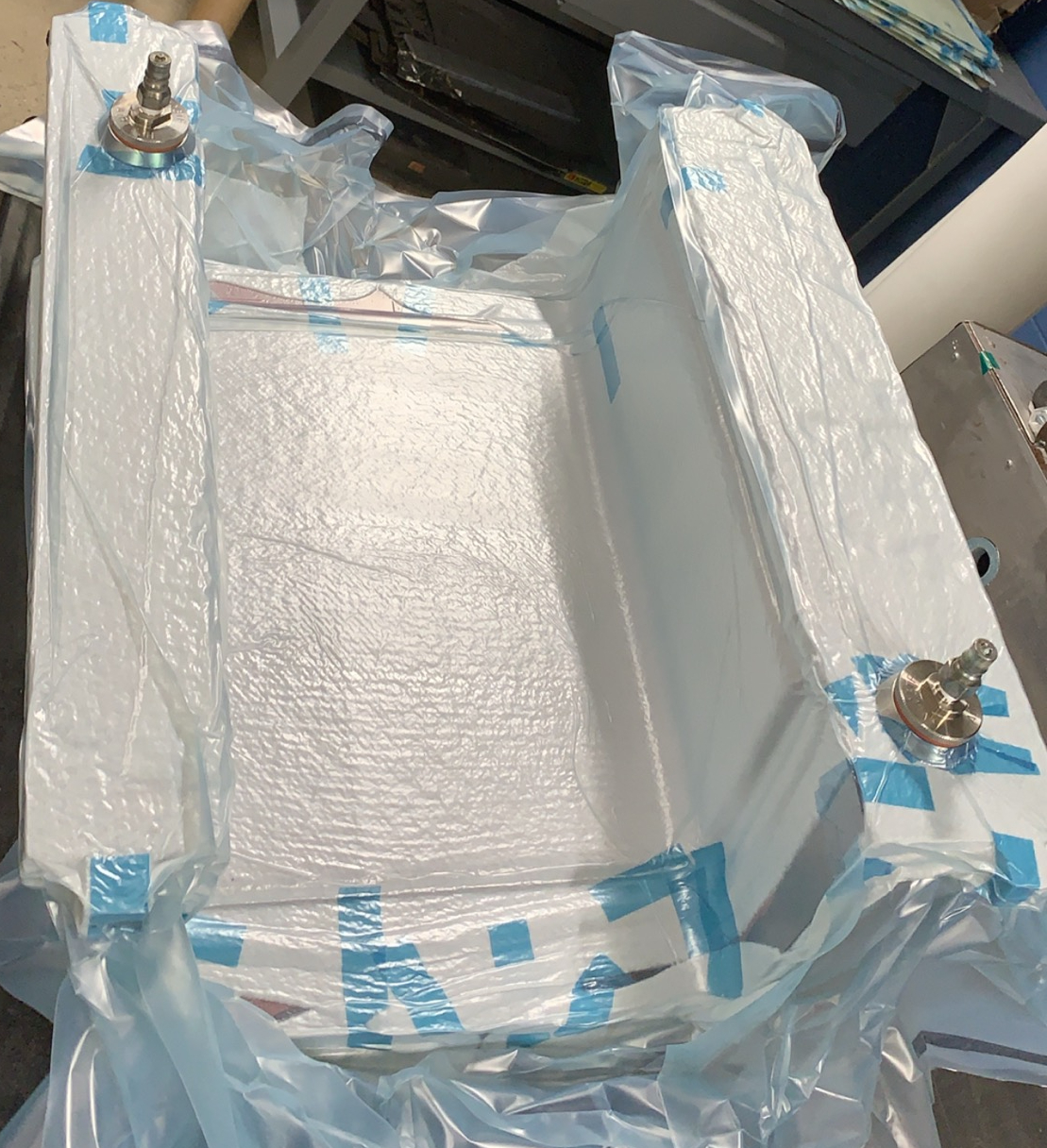
Paso 5:Aspire la bolsa y cure en autoclave.
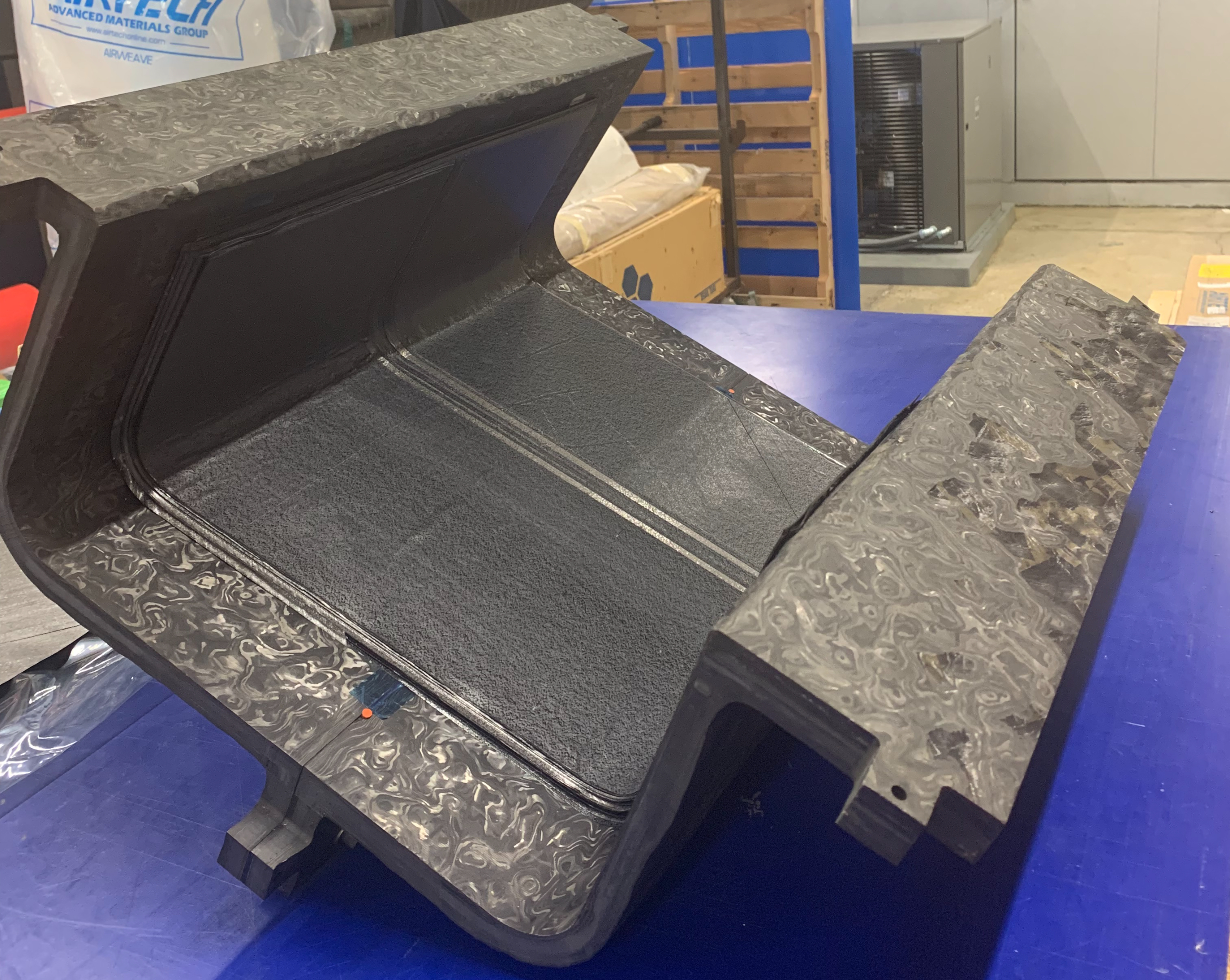
Paso 6:Herramienta curada a máquina para lograr las dimensiones finales y el acabado de la superficie.
Anterior SiguienteSe logró una buena adhesión entre el núcleo de PEI y las pieles epóxicas durante el curado del laminado, por lo que no se requirió adhesivo. Las pieles de CFRP no solo son no porosas y más duraderas que el núcleo AM, sino que también restringen físicamente el movimiento del núcleo durante las variaciones de temperatura debido a sus valores CLTE mucho más bajos. Solo un curado único y una sola operación de mecanizado, ambos gastos importantes durante producción de herramientas:eran necesarias para lograr las dimensiones finales y el acabado de la superficie. Además, no se requirió respaldo, debido a la estructura tipo sándwich y la forma de la herramienta, que incluía bridas de retorno en la parte superior del molde para la rigidez lateral y una junta atornillada en el centro del molde para la rigidez vertical, eliminando una operación de unión.
Desafíos iniciales
Los investigadores enfrentaron varios desafíos manejables con el nuevo proceso.
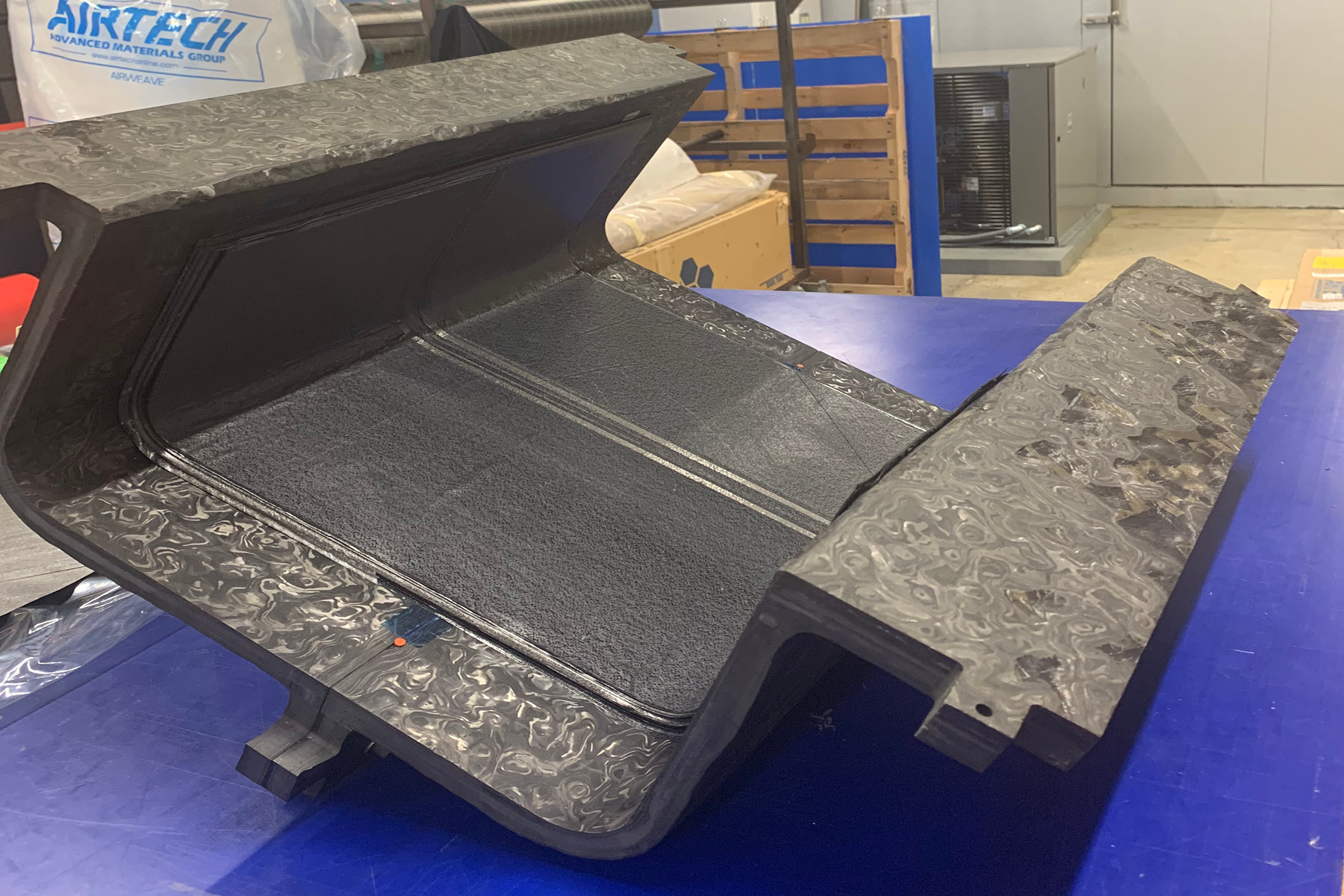
Para facilitar la fabricación en el BAAM, la dirección de fabricación preferida para el núcleo fue imprimir la sección transversal como una construcción vertical. Eso no fue un problema para la herramienta de 0,6 metros; sin embargo, para la herramienta más grande, 3,3 metros era más alta de lo que la BAAM 1000 podía imprimir verticalmente. Debido a las limitaciones de espacio de impresión del eje Z de la impresora, los investigadores optaron por dividir a la mitad ambas herramientas de subescala a lo largo de su longitud y luego dividirlas nuevamente en secciones izquierda y derecha (para abordar los problemas de socavamiento de la tapa y facilitar el desmoldeo).
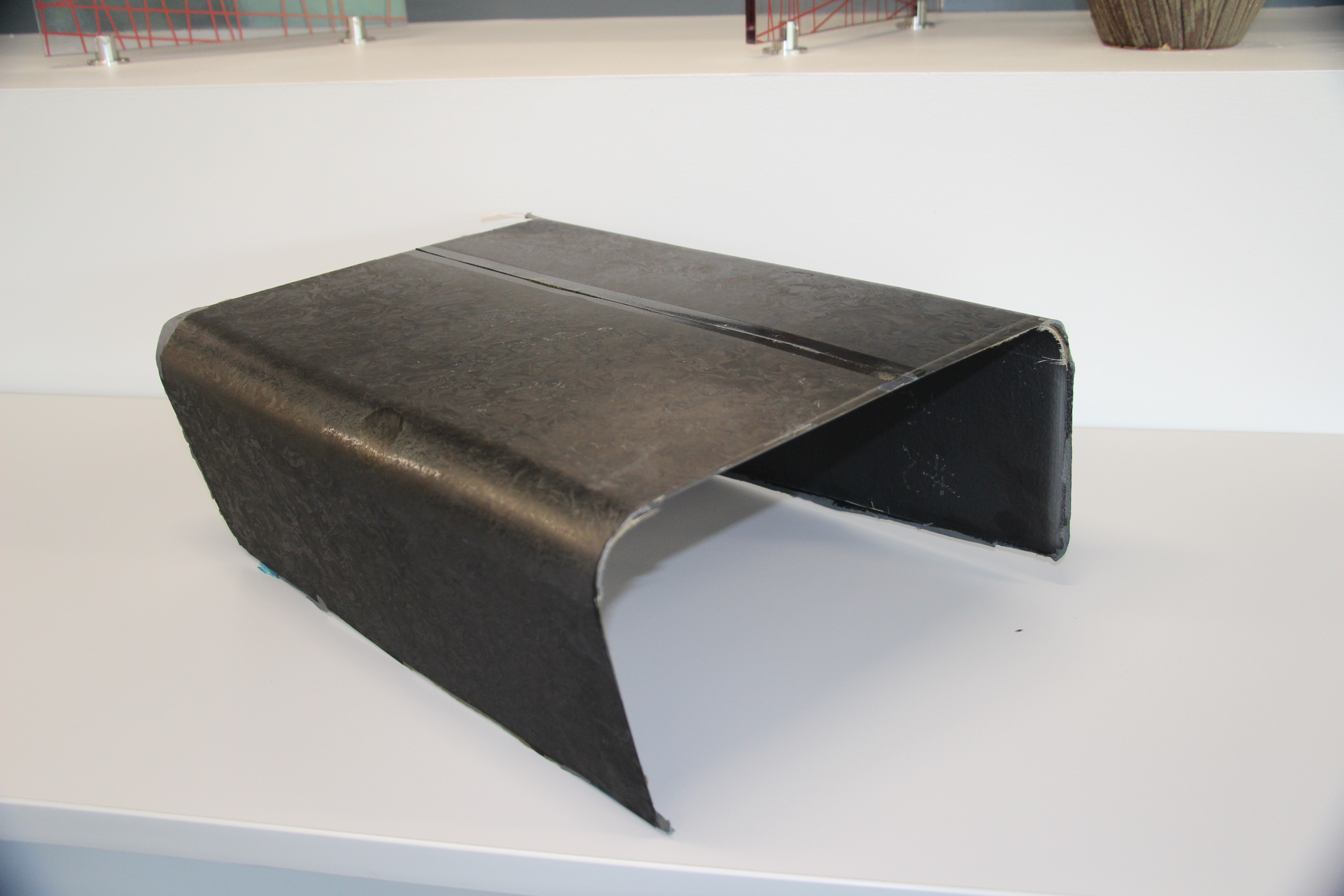
Para aumentar la eficiencia de impresión, las secciones de herramientas se imprimieron una tras otra y luego se cortaron en piezas a derecha e izquierda. Para lograr la longitud de 3.3 metros, las dos secciones de la derecha se unieron seguidas de las dos secciones de la izquierda utilizando el adhesivo epoxi Loctite EA9394 de Henkel Corp. (Rocky Hill, Connecticut, EE. UU.). El equipo dejó el núcleo AM sin mecanizar, sintiendo que era fundamental para lograr bajos costos de herramientas y plazos de entrega cortos, así como para crear un enclavamiento mecánico entre el núcleo AM y las pieles de CFRP en cada lado. La parte posterior de cada mitad de la herramienta se laminó con cinco capas de preimpregnado, mientras que la parte frontal se laminó con nueve capas para proporcionar material adicional que podría eliminarse durante el mecanizado posterior al curado.
Resultados preliminares
Además de controlar el CLTE del núcleo AM, el preimpregnado proporcionó una superficie libre de picaduras que mantuvo la integridad del vacío sin necesidad de sellador / revestimiento. Este enfoque fue tan exitoso que permitió el uso de un diseño de herramienta de varias piezas sellado con una junta, que los investigadores creen que no se había demostrado previamente en herramientas AM utilizadas a altas temperaturas. Además, la masa de la herramienta se redujo significativamente; la herramienta de subescala fue un tercio del peso calculado para un diseño Invar comparable. Las herramientas de CFRP más ligeras no solo son más fáciles de manipular y almacenar en rejillas, sino que también requieren ciclos de calentamiento / enfriamiento de autoclave más cortos. En una herramienta para moldear el mástil en C a gran escala, esa ventaja de peso podría marcar la diferencia entre estar por debajo o por encima de los límites de peso del pórtico / grúa en algunos espacios de fabricación.
Es importante destacar que el costo de la herramienta híbrida de 0,6 metros se calculó durante la fabricación, utilizando las tarifas de mano de obra estándar de la industria, a $ 24,136 USD con una división aproximada de 50/50 entre los costos de mecanizado y los costos de impresión / laminado. Por el contrario, una herramienta Invar idéntica se cotizó en $ 46,775 USD, un ahorro de casi el 50%. Los costos de la herramienta de 3,3 metros no están completos, pero se espera que produzcan aproximadamente un 30% de ahorro en base a costo / unidad de longitud, ya que los costos de material / impresión escalan linealmente, pero los costos de mecanizado disfrutan de una economía de escala que reduce su impacto. El enfoque híbrido produjo herramientas que cumplieron con los requisitos de rendimiento operativo de Airbus y Northrop Grumman y se considera una alternativa viable a Invar para herramientas de prototipo rápido o de bajo uso. La investigación de la vida útil de la herramienta no formó parte de este estudio, pero probablemente se extendería considerablemente más allá de los 12 ciclos que se demostraron.
El programa se extendió de 18 a 30 meses, pero todavía hay áreas en las que se necesitan más estudios, como comprender cómo la geometría del núcleo final tal como se imprime difiere de la predicha en los modelos CAE. El equipo también quiere mejorar la precisión predictiva para que se agreguen suficientes capas en áreas críticas para garantizar que no haya perforaciones durante el mecanizado. Aún así, el equipo consideró que este era un proyecto exitoso con una oportunidad considerable para futuras herramientas de LFAM.
"Northrop Grumman espera construir una pieza de demostración de mástil de 3 metros utilizando la herramienta híbrida de 3,3 metros de largo construida por UDRI y nuestro propio proceso automatizado de conformado de refuerzo (ASF) para evaluar la durabilidad y estabilidad dimensional de la herramienta", agrega Vern Benson, miembro técnico de Northrop Grumman.
Resina
- Evonik, Evolución de soluciones aditivas para desarrollar materiales de impresión 3D para el proceso STEP
- Henkel ofrece una plataforma de materiales para la fabricación aditiva
- Essentium y Lehvoss se asocian para desarrollar materiales para la fabricación aditiva
- Nuevo nailon 6 termoestabilizado para trenes de potencia híbridos y eléctricos
- Trelleborg anuncia nuevo distribuidor para materiales de herramientas
- UAMMI, Impossible Objects construye piezas compuestas para la Fuerza Aérea de EE. UU.
- Victrex y Bond se asocian para la impresión 3D de piezas PAEK
- AeroLas explora una nueva tecnología de hilado para hilo híbrido termoplástico
- Consejos para moldes de impresión 3D
- Reducción al mínimo de los tiempos de respuesta para piezas grandes
- Fabricación y Matricería de Piezas Metálicas para Sistemas de Inyección de Combustible