Fabricación de compuestos futuros:AFP y fabricación aditiva
"Sobreimpresión" en superficies y soportes de CFRP prefabricados (arriba a la izquierda) , procesos de hibridación como la impresión 3D y el devanado de filamentos (arriba a la derecha) , Núcleos de impresión 3D en laminados AFP y máscaras de AFP en núcleos impresos en 3D (abajo a la derecha) e impresión 3D CEAD AM Flexbot a 45 grados (abajo a la izquierda) . Crédito de la foto:TU Munich, presidente de compuestos de carbono
En septiembre asistí al simposio virtual "FUTURA FABRICACIÓN DE COMPUESTOS - AFP &AM", en referencia a la colocación automatizada de fibra (AFP) y la fabricación aditiva (AM). Este simposio fue organizado por el presidente de compuestos de carbono (LCC) en Universidad Técnica de Munich (TUM, Munich, Alemania). El evento también incluyó al socio de investigación de TUM, la Universidad Nacional de Australia (ANU, Canberra). El simposio revisó las capacidades de I + D de compuestos en TUM y ANU, así como los proyectos completados y en curso con socios industriales, incluidos AFPT, Airbus, BMW, CEAD, DLR, Fraunhofer, GKN Aerospace, INOMETA, SGL Carbon y Victrex.
La colaboración de TUM con ANU comenzó en 2010 con el proyecto AutoCRC para desarrollar tanques de almacenamiento de gas natural comprimido (GNC) a partir de compuestos termoplásticos. La I + D conjunta ha continuado desde entonces, incluida la formación del centro del Australian Research Council para la fabricación automatizada de compuestos avanzados (AMAC) y tres áreas de enfoque principales en ANU:
- Mejora de materiales
- Materiales y recubrimientos a nanoescala para mejorar las propiedades funcionales de los compuestos de carbono
- Cintas preimpregnadas mejoradas con grafeno para conductividad térmica y eléctrica
- Laser-AFP
- Proyecto con Ford para desarrollar acero reforzado con compuestos
- Control digital del sesgo de calentamiento, p. ej. estabilidad del proceso para esquinas / geometrías 3D
- Diagnóstico avanzado con tomografía computarizada de rayos X
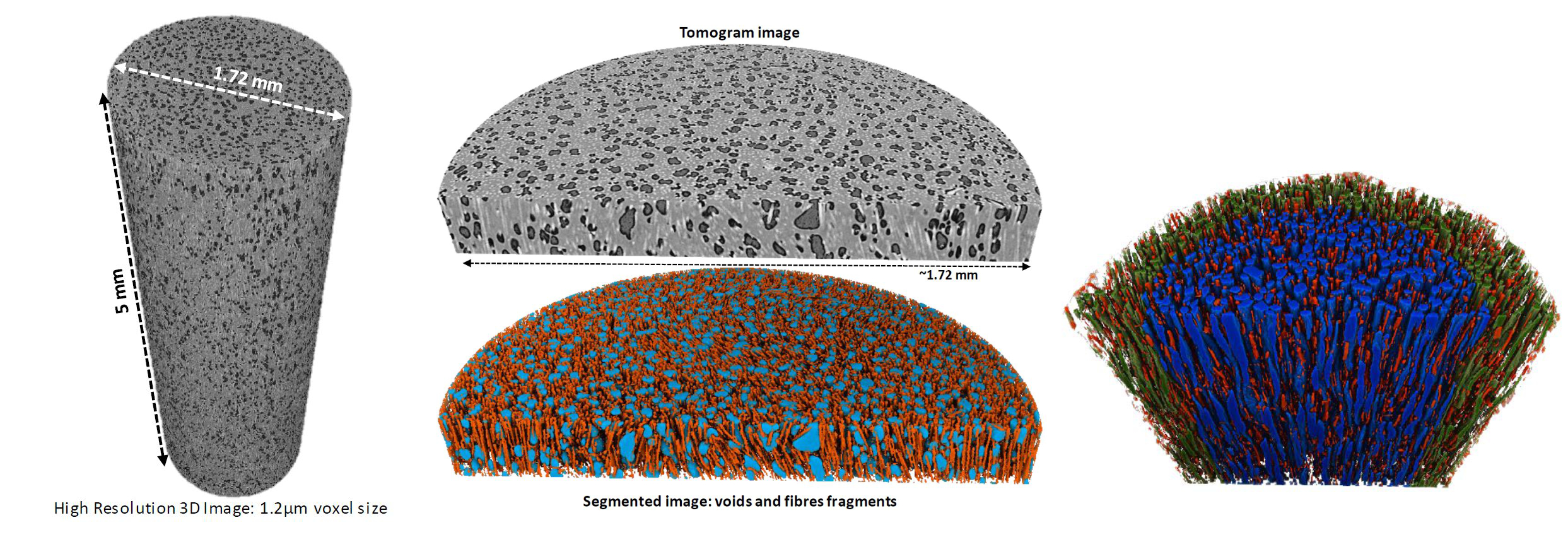
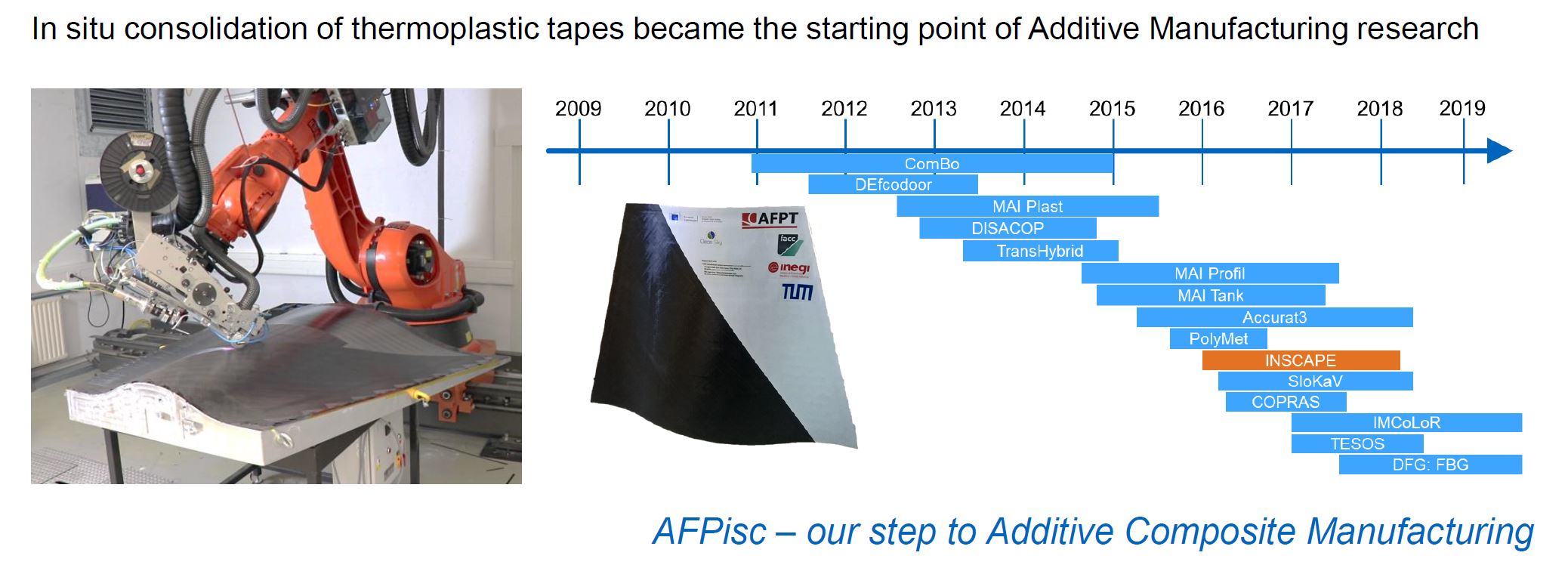
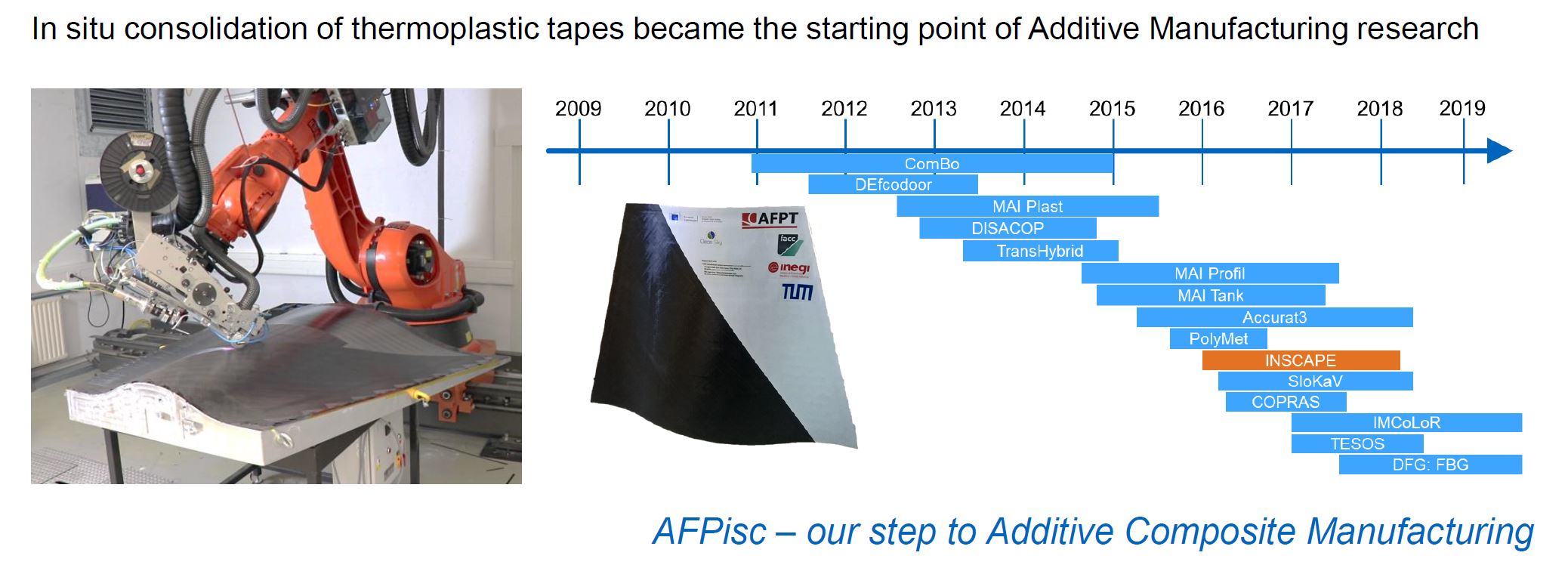
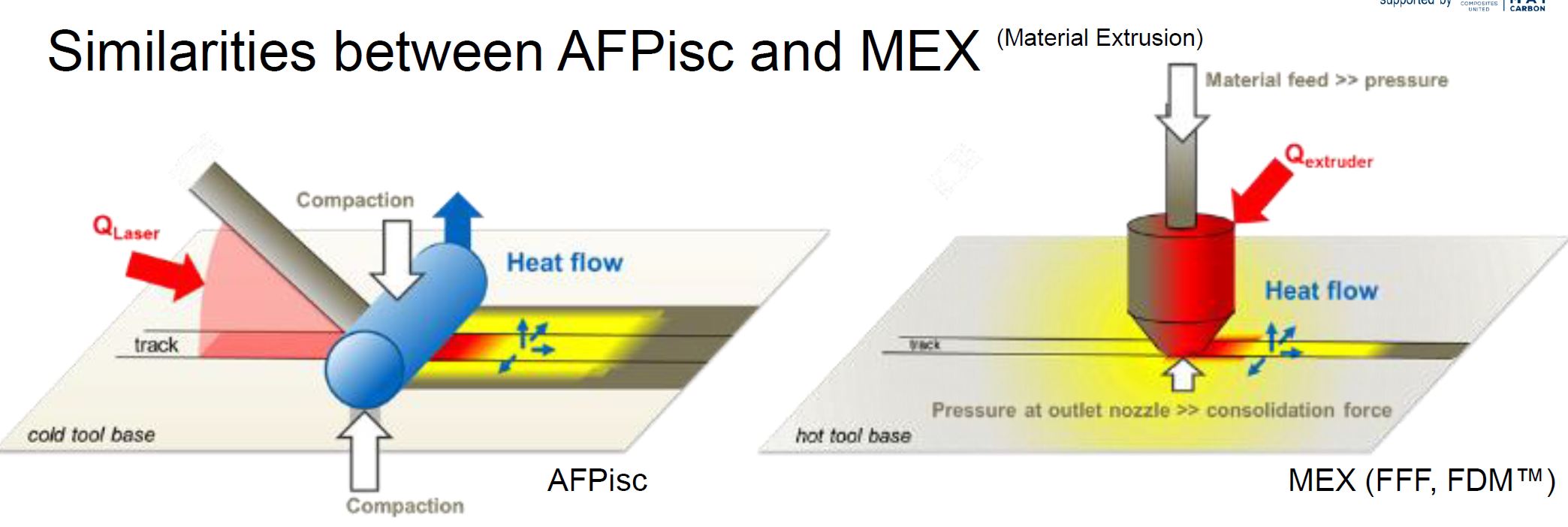
Discutió las similitudes entre la extrusión de material (MEX), el proceso más común utilizado para la impresión 3D de compuestos reforzados con fibra, y AFP ISC:
- Tratamiento térmico local y recurrente
- Diseño basado en capas y propiedades de material ortotrópico
- Colocación del material a lo largo de trayectorias programadas en 2D y 3D y activación térmica entre capas.
Luego, Drechsler discutió las necesidades futuras de compuestos y cómo la combinación de AFP y MEX podría proporcionar soluciones, incluidas a corto plazo en herramientas y a más largo plazo en estructuras livianas de alto rendimiento que sean rentables y ecológicamente sostenibles.
Al describir las capacidades de LCC, Drechsler brindó una descripción general de su equipo MEX, así como de los proyectos de I + D pasados y en curso en la fabricación aditiva.
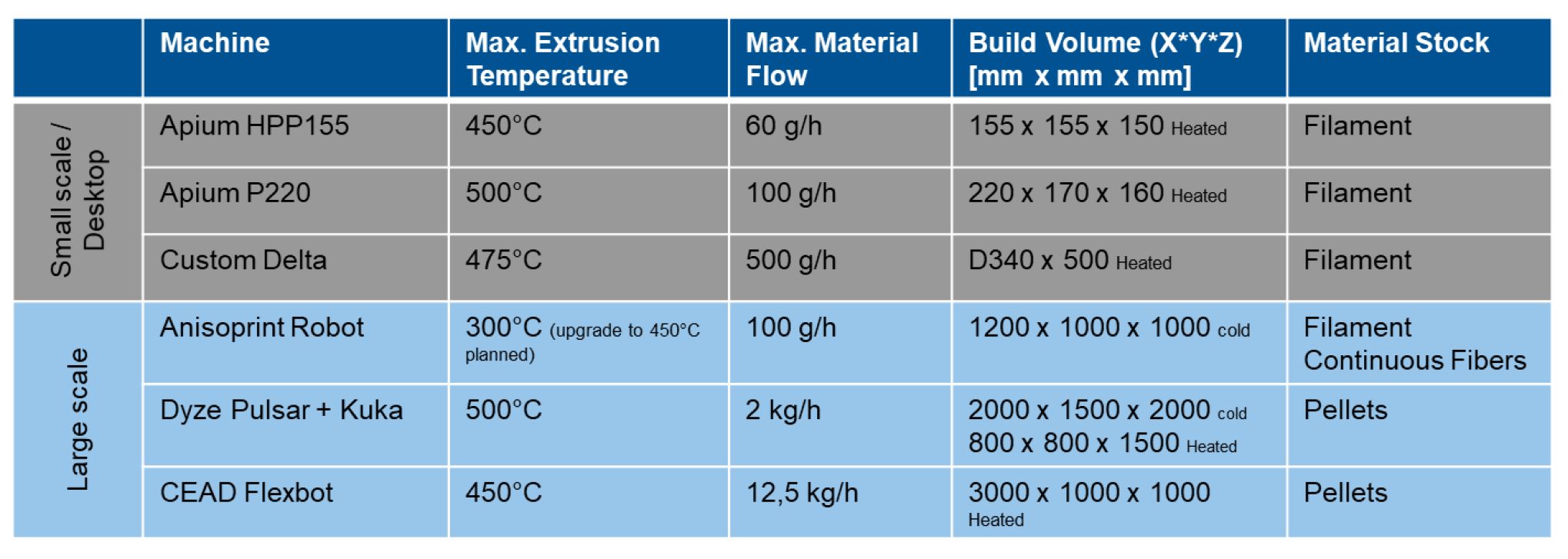
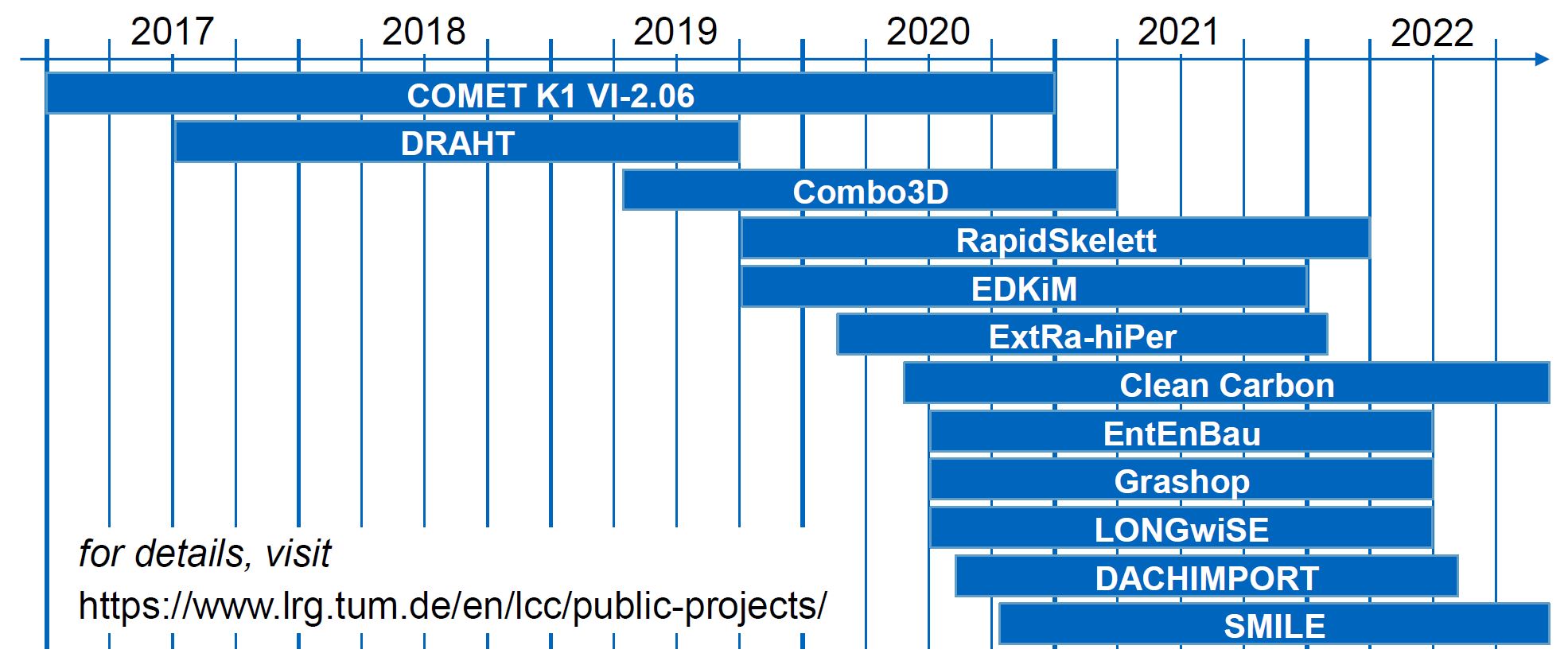
Con respecto a ISC AFP, los desarrollos recientes y en curso en LCC incluyen:
- Un cabezal de bobinado de recipientes para apoyar la industrialización de estructuras como recipientes a presión, incluidos tanques de almacenamiento de hidrógeno
- Control de circuito cerrado del calentamiento del rayo láser
- Usar un rodillo refrigerado por líquido para la consolidación
- Caracterización de cintas para optimizar ISC.
Los desarrollos de LCC en MEX y la impresión 3D se exploraron más a fondo en múltiples presentaciones durante los próximos 2 días.
CEAD e impresión 3D a gran escala
La siguiente presentación después del discurso de apertura de Drechsler estuvo a cargo de Maarten Logtenberg, director ejecutivo de CEAD (Delft, Países Bajos). Fundada en 2014, CEAD ha vendido sistemas comerciales basados en su tecnología Continuous Fiber Additive Manufacturing (CFAM), tanto como una celda cerrada basada en pórtico (CFAM Prime) y un sistema basado en robot (AM Flexbot). LCC es propietaria de este último (consulte la tabla anterior) y trabaja con LCC en varios proyectos (consulte CW artículos sobre CEAD y su trabajo con TUM LCC).
Los aspectos más destacados de la presentación de Logtenberg incluyeron el desarrollo de CEAD de soluciones híbridas que integran fresado CNC, grandes lechos de impresión calentados (1,2 mx 3 my 1,2 mx 2 m) y lechos de impresión rotativos calentados. También busca celdas aún más grandes e impresión de 45 grados, así como la impresión de herramientas reforzadas con fibra para la producción en autoclave en serie de piezas de aviones comerciales.
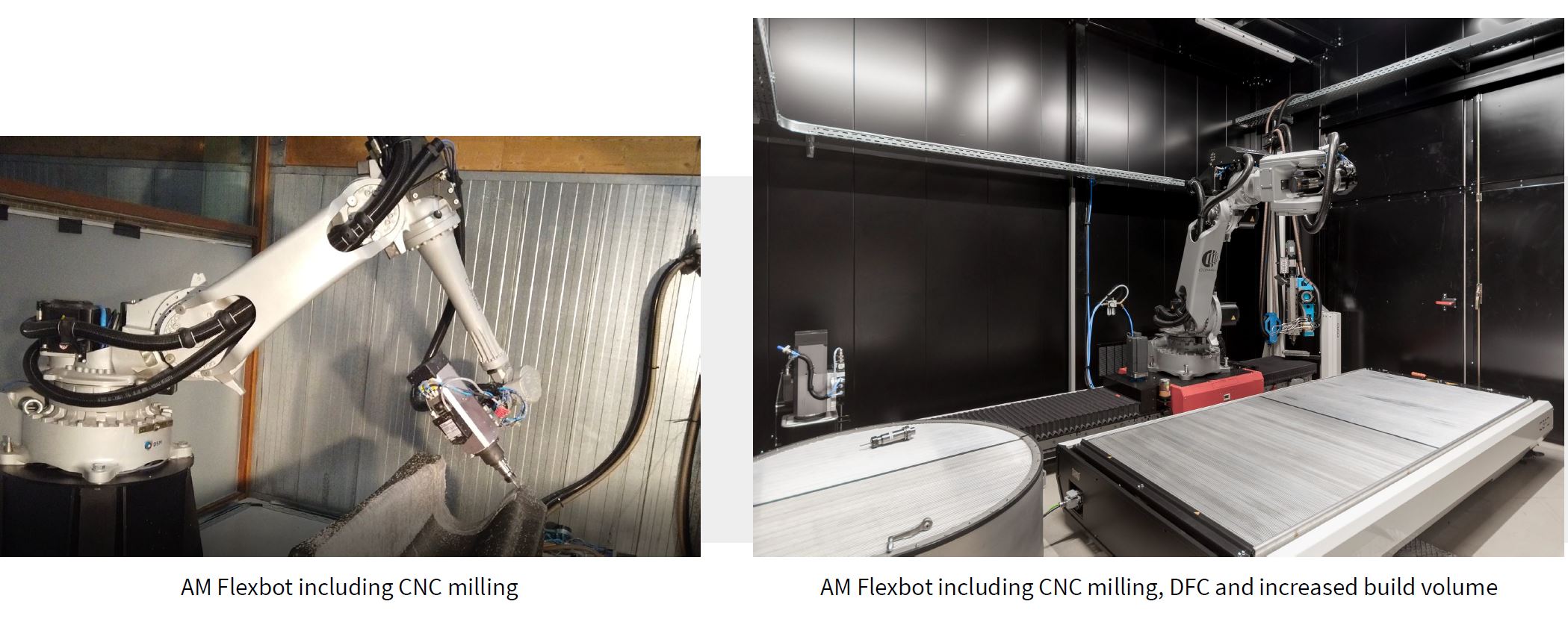
Logtenberg señaló que uno de los principales desafíos para las herramientas de autoclave impresas en 3D es la expansión térmica y las herramientas mucho más grandes de 4 metros tienden a expandirse demasiado (consulte "Herramientas aditivas híbridas de gran formato"), lo que dificulta la compensación suficiente a través del diseño de la herramienta. . La solución que propuso es reemplazar el refuerzo de fibra cortada que se utiliza principalmente hasta la fecha por fibra continua depositada por sistemas como AM Flexbot.
Este camino a seguir se secundó en la presentación “ Introducción de intensificadores de vía impresos en 3D para la producción de aletas compuestas ”Impartido por Thomas Herkner en GKN Aerospace en Munich, Alemania. Estos intensificadores de CFRP impresos en 3D se utilizan como herramientas en la producción de flaps de aterrizaje de CFRP para los Airbus A350 y A330. Aunque este exitoso programa en GKN usó refuerzo de fibra cortada, Herkner mostró una hoja de ruta para un mayor desarrollo que incluía el uso de fibra continua en herramientas impresas en 3D, así como, eventualmente, en las partes de la aeronave.
Este camino a seguir fue bien explicado por la investigación de LCC, Patrick Consul, en un blog reciente de CW:
Consul también hizo una presentación en el simposio de TUM, analizando el diseño de procesos para AM a gran escala basada en extrusión. Discutió cómo las transiciones de vidrio y fase que se muestran a continuación representan el mayor cambio en las propiedades del material de los gránulos reforzados con fibra picada que se funden y extruyen en sistemas de impresión 3D como CFAM y AM Flexbot.
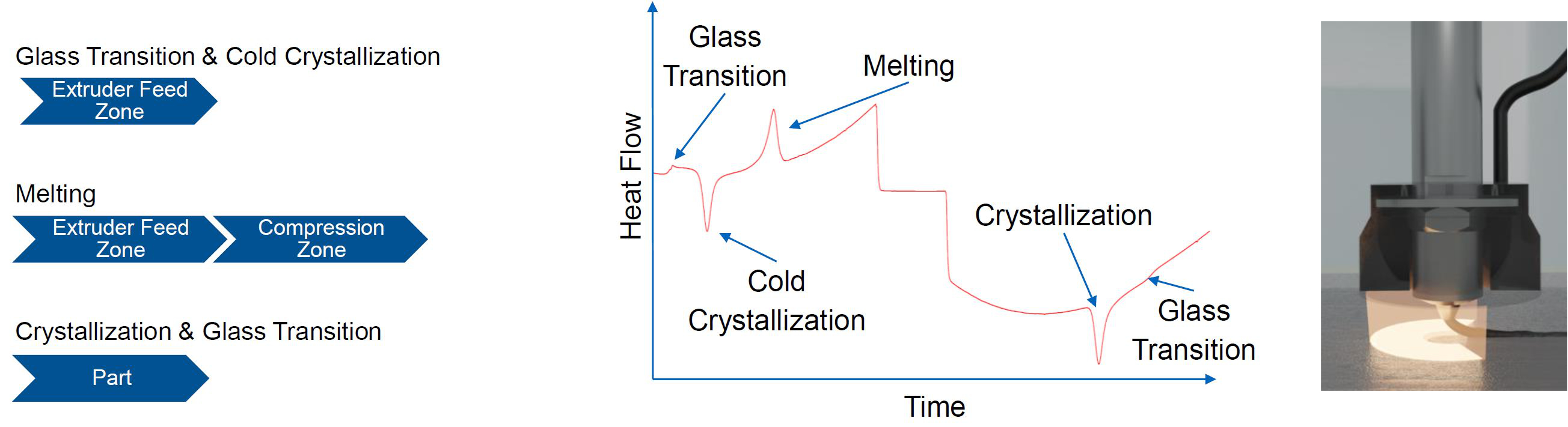
El trabajo de Consul ha analizado cómo los parámetros MEX, como la viscosidad del polímero y la temperatura de extrusión y el par, afectan la cristalinidad en el material compuesto impreso, lo que a su vez influye en la capacidad de soldar capas durante la impresión 3D. Además de esta unión capa a capa, Consul también ha explorado la alineación de las fibras y la tensión residual en las capas impresas. Una solución presentada fue utilizar un láser para precalentar el sustrato durante la impresión, ampliamente utilizado hoy en día en ISC AFP de compuestos termoplásticos, transfiriendo así el conocimiento de AFP a AM. Los experimentos iniciales han utilizado un anillo de diodos láser controlables.
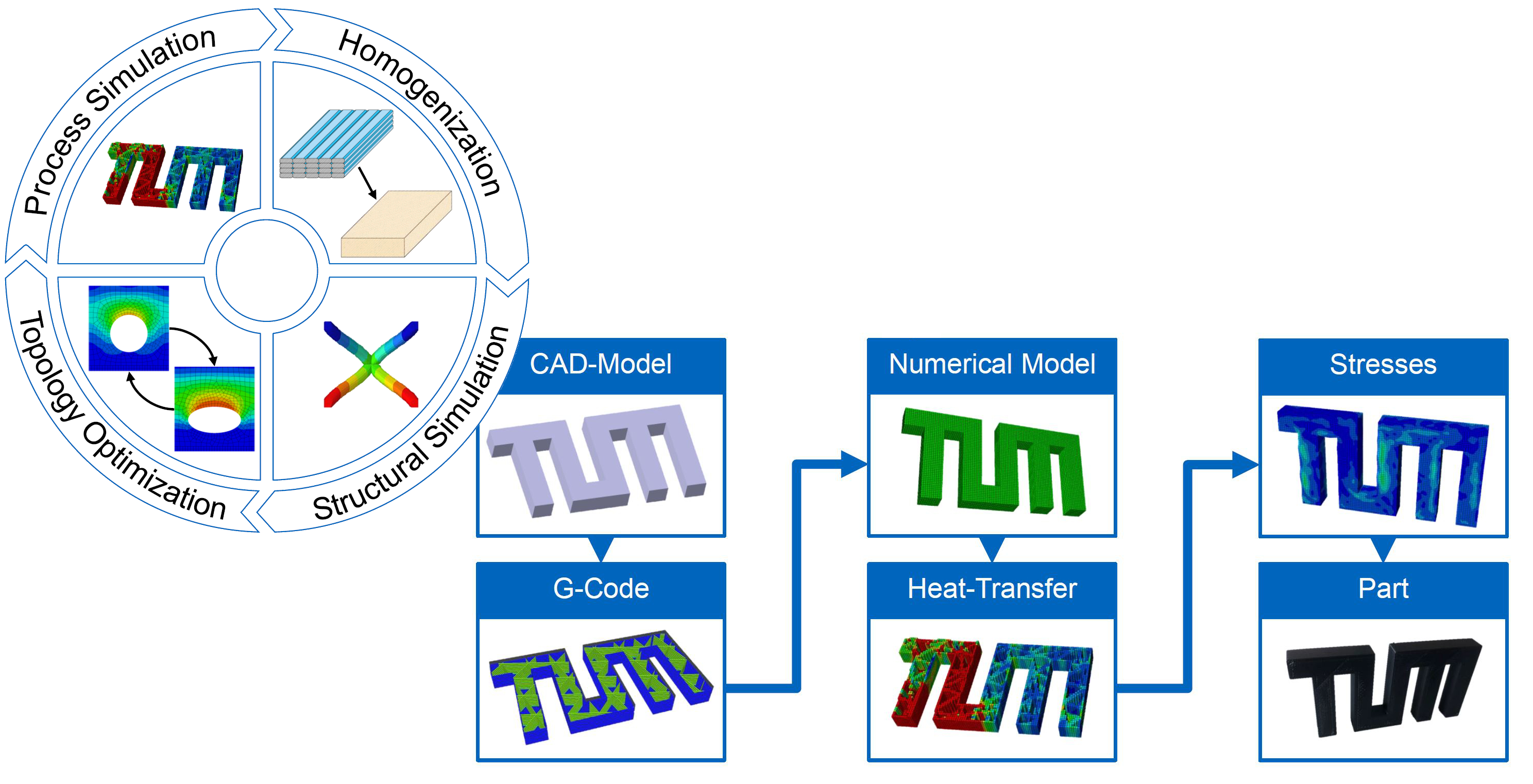
El colega de Consul, Matthias Feuchtgruber, presentó más tarde en el día, avanzando desde el diseño de procesos y caracterización de materiales hasta el desarrollo de una cadena de proceso virtual para composites AM.
Alexander Matschinski luego hizo una presentación sobre la integración de fibras sin fin en compuestos AM, presentando la tabla a continuación, que se convirtió en la base para la tabla modificada que utilicé en CW Artículo complementario de próxima generación sobre impresión 3D de fibra continua. Matschinski también habló sobre el trabajo en el diseño de estructuras AM de fibra continua y el desarrollo futuro de la "sobreimpresión" en piezas y superficies de CFRP prefabricadas.
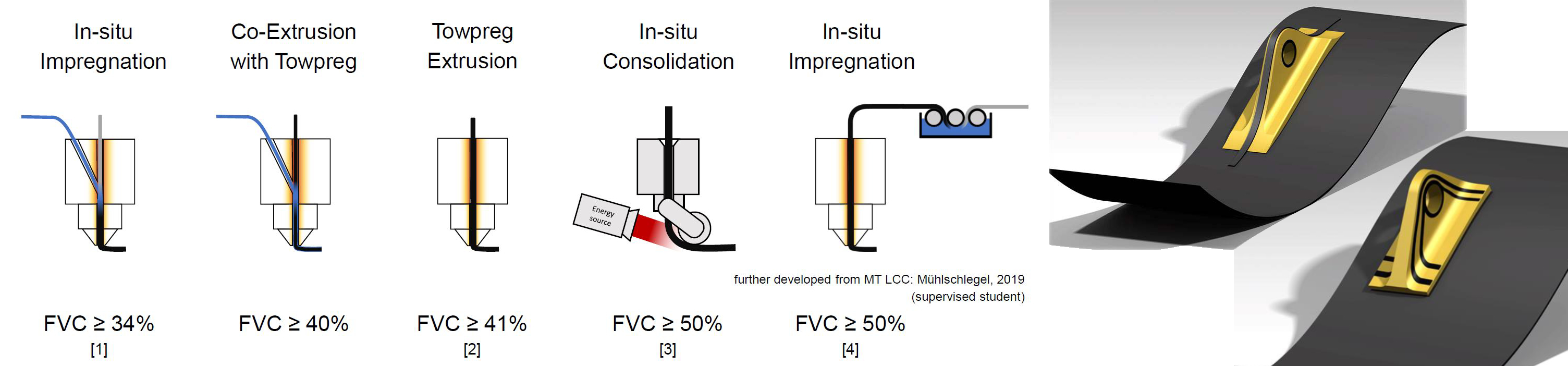
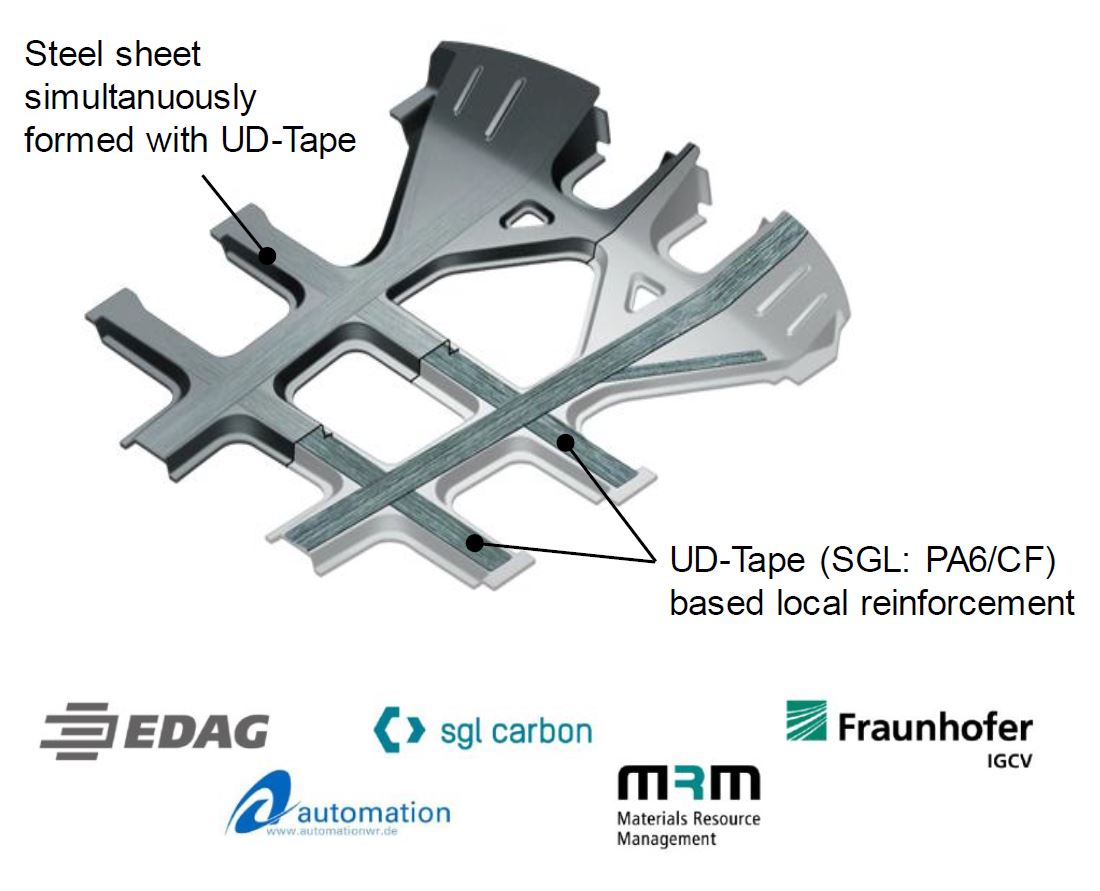
El doctor Christopher Ebel de SGL Carbon mostró otras aplicaciones interesantes de las fibras continuas, que incluyen el refuerzo de estructuras de acero para los bajos de la carrocería para automóviles, reduciendo el número de piezas de 37 a 9 y el peso en un 41%. Otro concepto fue el devanado en 3D utilizando Towpreg impregnado con resina epoxi de curado rápido para estructuras de carga optimizada. Este enfoque impulsado digitalmente comienza con la simplificación de cargas complejas y la optimización de la topología, seguido de la fabricación automatizada. Las piezas resultantes pueden aprovechar el bloqueo de forma de los insertos en las estructuras, lo que permite la introducción de carga sin pérdida de rigidez. Los últimos procesos de impresión de metales en 3D se pueden utilizar para tales insertos, optimizando aún más la eficiencia de manejo de carga y la reducción de costos.
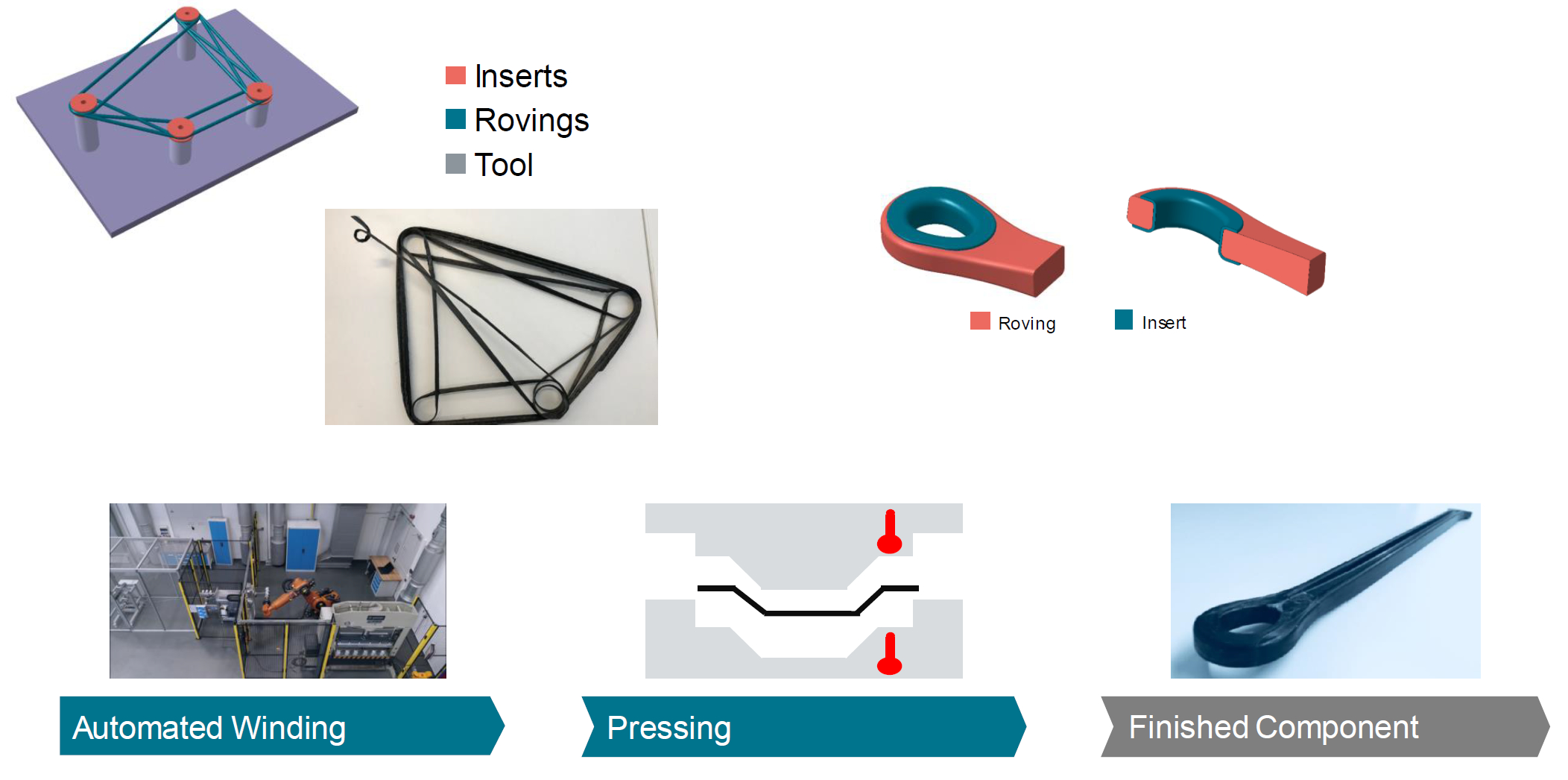
Sebastian Nowotny de DLR habló sobre la combinación de la impresión 3D con ISC AFP de compuestos termoplásticos, incluida la impresión 3D sobre laminados AFP y AFP sobre estructuras parcialmente abiertas impresas en 3D. Los primeros experimentos incluyen la impresión 3D de un núcleo sobre una piel de CFRP prefabricada y luego AFP / cinta colocada sobre el núcleo impreso en 3D. Las muestras se crearon y luego se sometieron a una prueba de cizallamiento por tracción para evaluar la unión entre la piel y el núcleo.
Título de la presentación
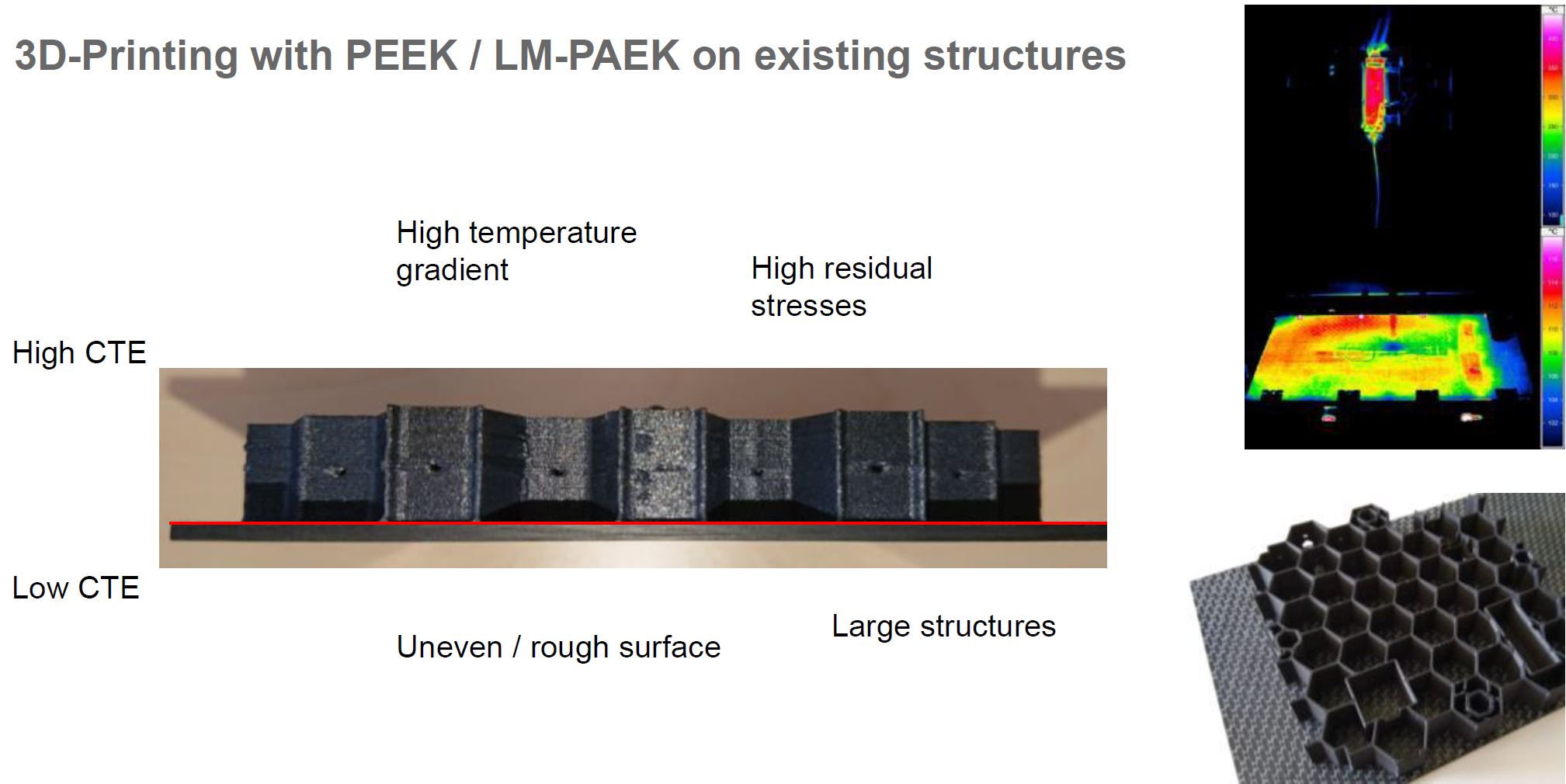
Crédito de la foto:Sebastian Nowotny, DLR, Simposio de TUM, septiembre de 2020
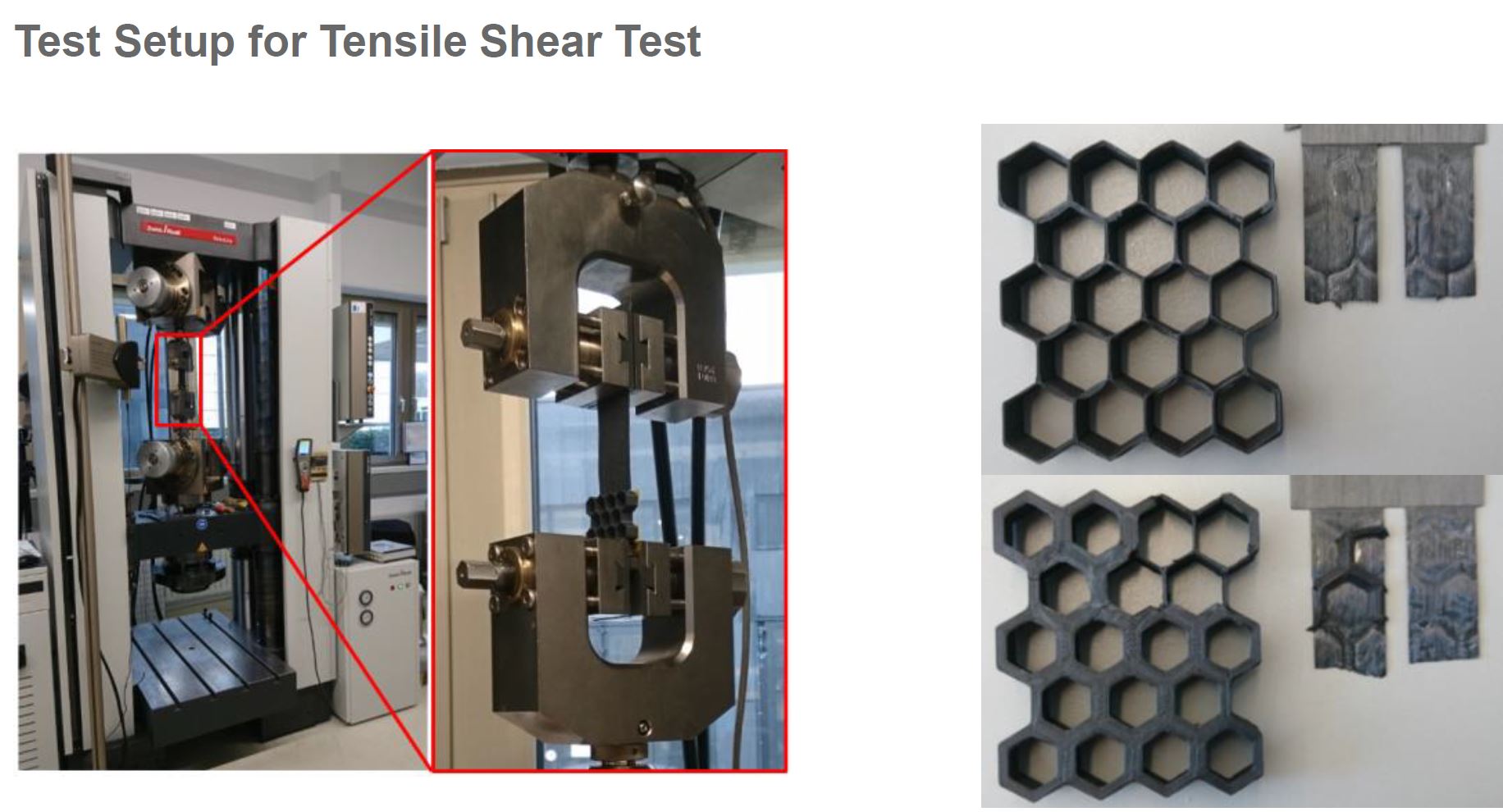
Ensayo de cizallamiento por tracción de cupones realizados mediante impresión 3D híbrida y AFP. Crédito de la foto:Sebastian Nowotny, DLR, Simposio de TUM, septiembre de 2020
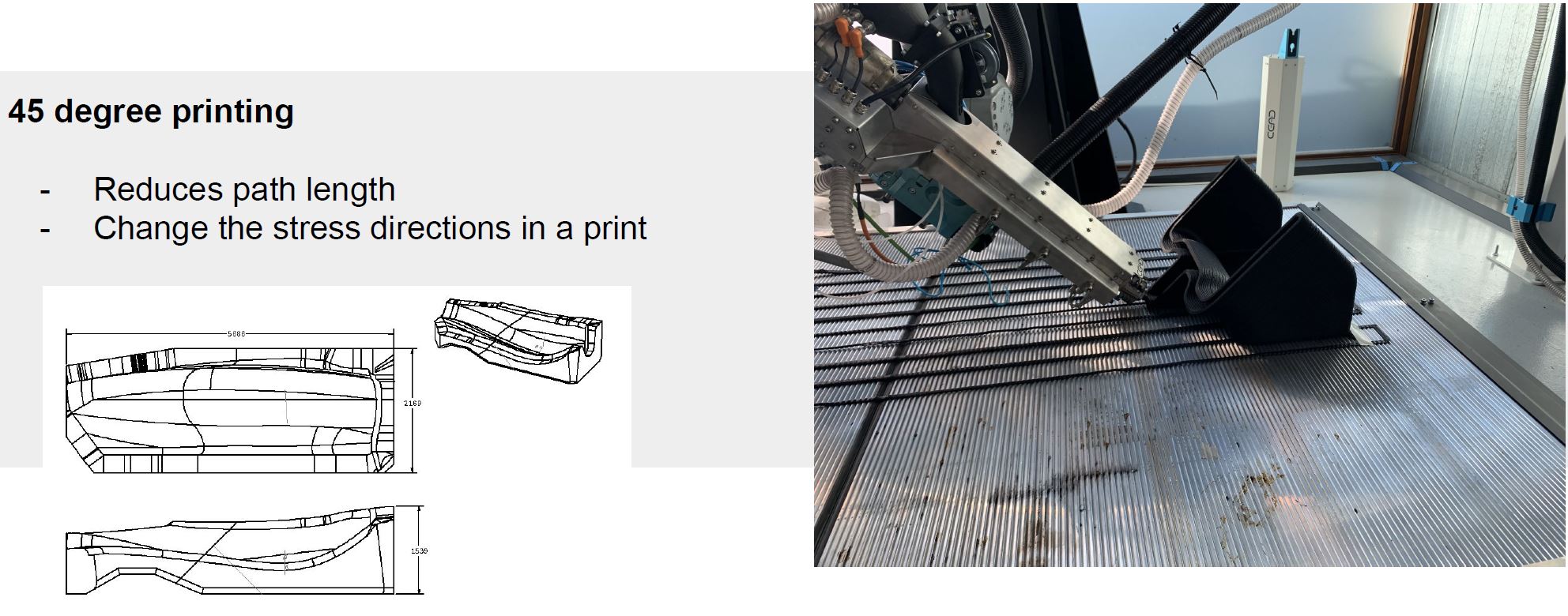
Crédito de la foto:CEAD, Simposio de TUM, septiembre de 2020
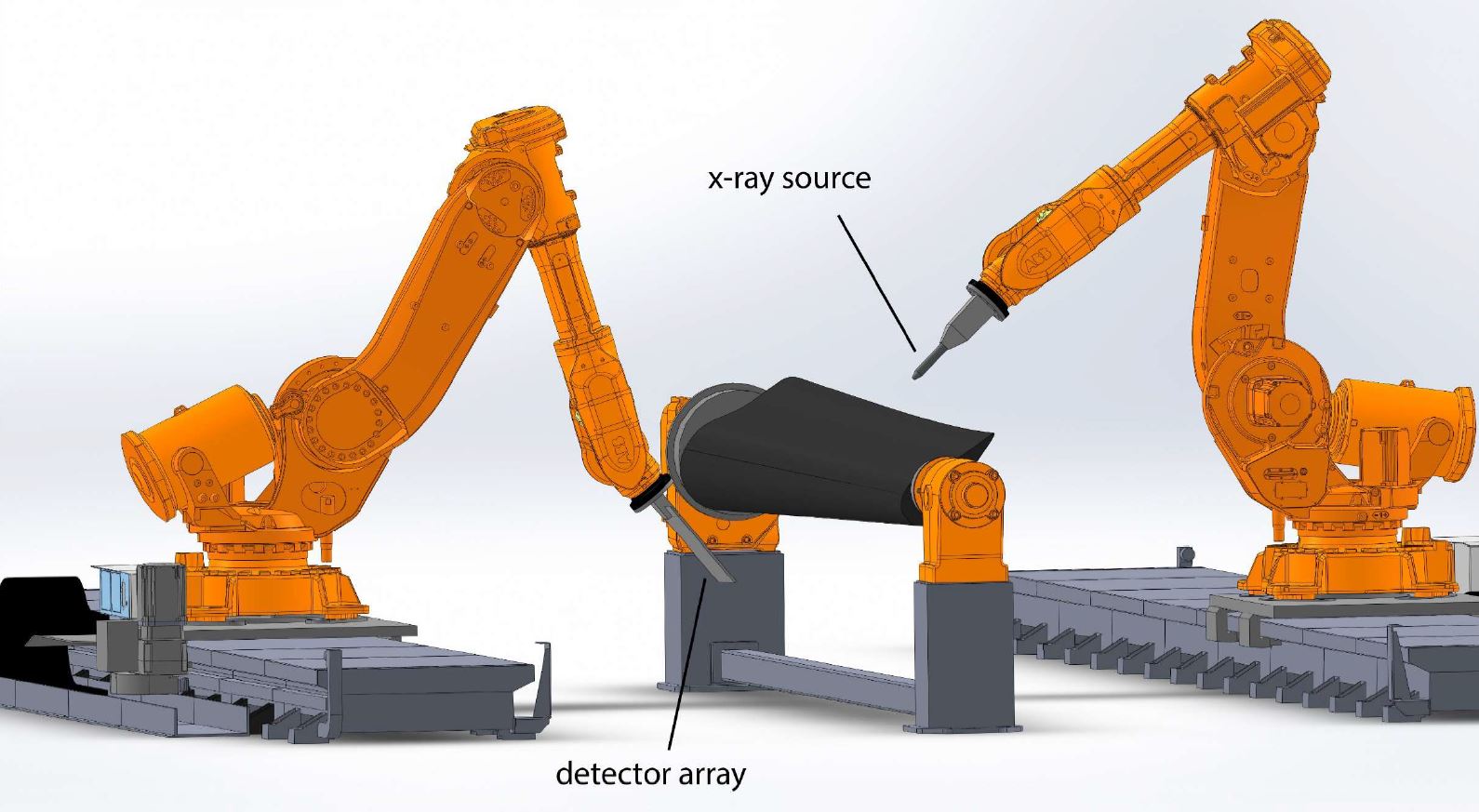
Aplicación futura de la tomografía computarizada durante la producción de composites. Crédito de la foto:Universidad Nacional de Australia, Simposio de TUM, septiembre de 2020
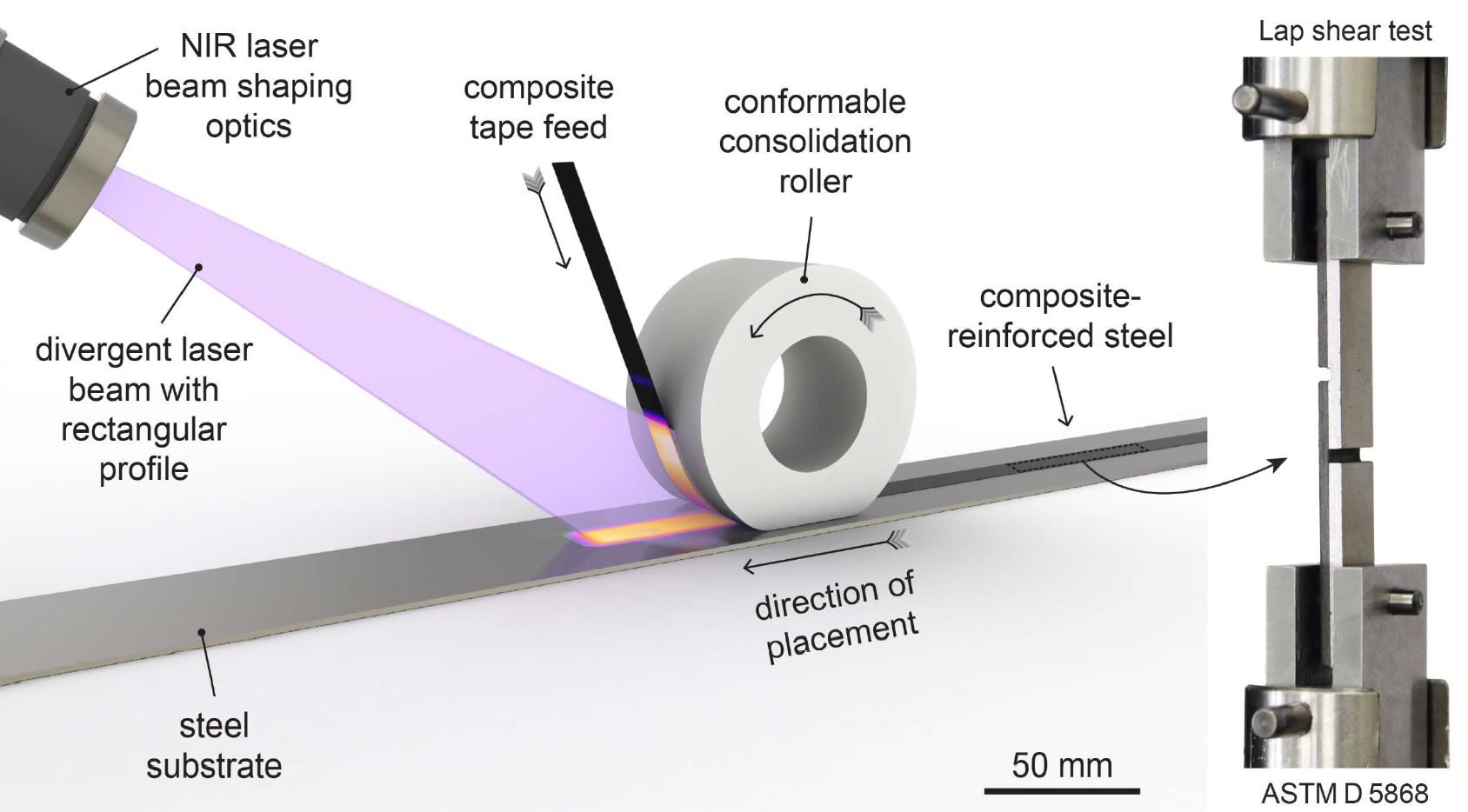
Trabajos de desarrollo utilizando láser AFP para crear estructuras híbridas CFRP-metal. Crédito de la foto:Universidad Nacional de Australia, Simposio de TUM, septiembre de 2020
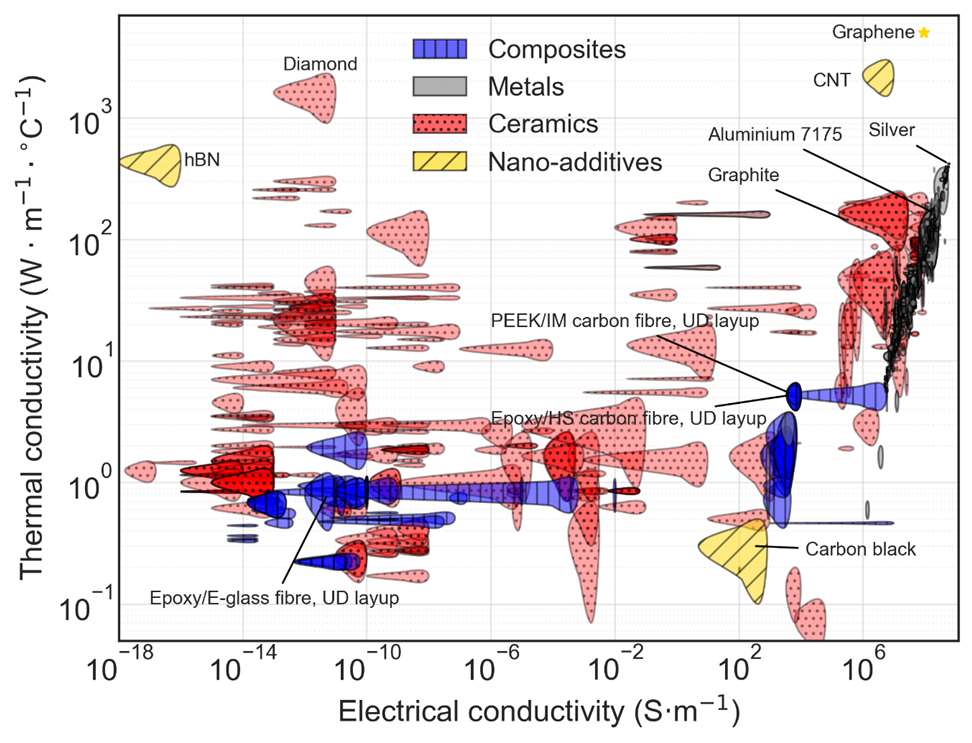
Cintas preimpregnadas mejoradas con grafeno para conductividad térmica y eléctrica. Crédito de la foto:Universidad Nacional de Australia, Simposio de TUM, septiembre de 2020
Anterior SiguienteChristian Weimer, jefe de materiales de Airbus Central Research &Technology, analizó la impresión de fibra continua como parte del panorama tecnológico en evolución, cuyo objetivo es reducir el peso con costos reducidos y una mayor sostenibilidad que se debe lograr para que los compuestos aseguren un lugar en los aviones del futuro. Hizo hincapié en que los compuestos 3D verdaderamente eficientes deben emplear:
- Las materias primas y los productos intermedios adecuados:fibras, semiacabados
- Procesos e interfaces eficientes:termoplásticos AM, moldeo por inyección
- Diseño y dimensionamiento adaptados:integral, totalmente optimizado para carga en 3D)
- Superficie y funcionalidad:ESN (número de serie electrónico), SHM (monitoreo de salud estructural)
También discutió la necesidad de fibras y resinas de origen biológico para cumplir con los objetivos urgentes de sostenibilidad ambiental y climática.
El simposio de TUM incluyó muchas más presentaciones, incluidos resúmenes del trabajo en ANU, y todas fueron muy interesantes para mostrar cómo los compuestos están avanzando y cómo LCC, trabajando con socios en todo el mundo, continúa visualizando lo que los compuestos pueden lograr y hacer avanzar nuestra industria.
Resina
- ¿Es la tecnología de fabricación híbrida el futuro de la fabricación aditiva?
- Presentación de AM Fridays y Additive Podcast
- Fabricación aditiva con composites en la industria aeroespacial y de defensa
- Essentium y Lehvoss se asocian para desarrollar materiales para la fabricación aditiva
- La robótica y el futuro de la producción y el trabajo
- AMRC y socio Prodrive para el avance de la fabricación de componentes compuestos reciclables
- El aditivo PES aumenta la resistencia a la fractura y al micro-agrietamiento en compuestos epoxi
- Se forma una alianza de fabricación aditiva y termoplásticos sostenibles en Colorado
- ¿Qué es la fabricación aditiva? - Tipos y funcionamiento
- ¿Automatización y el futuro de la fabricación digital?
- Fabricación aditiva en medicina y odontología