Cintas termoplásticas multicapa, AFP e infusión de resina para composites más democráticos
Novotech (Nápoles, Italia) comenzó como una empresa derivada de la Universidad de Nápoles "Federico II" en el sur de Italia, fundada por el profesor Leonardo Lecce en 1992. "Hemos apoyado a empresas de aviación general y proporcionado servicios de I + D en toda Italia", dice Lecce. quien ahora es el CEO de Novotech. "Hemos proporcionado análisis estructurales para piezas de aviones y también ayudamos con el desarrollo de aviones".
Ubicada cerca de la fábrica de Leonardo que fabrica las secciones de fuselaje de material compuesto para el Boeing 787, Novotech comenzó a enfocarse en compuestos en 2014. Compró una celda de colocación automática de fibra (AFP) de Coriolis Composites (Queven, Francia) y desarrolló en autoclave ( OOA), incluida la infusión de resina y la fabricación de compuestos termoplásticos, con experiencia especial en consolidación in situ mediante AFP.
Novotech ha participado en numerosos proyectos de investigación de la industria, que incluyen:
- MESEMA (Sistemas de energía magnetoelástica para incluso más aeronaves eléctricas)
- SARISTU (Estructuras de aeronaves inteligentes e inteligentes)
- ASAM (Simulación avanzada de mecanismos de aeronaves)
- LAMITECH (Métodos de prueba innovadores para la estratificación automática de materiales compuestos híbridos)
- PROALATECH (Análisis de soluciones de reparación y caracterización estructural de empenajes de CFRP innovadores)
- CARA (Ambiente de cabina de avión amigable)
- AIRGREEN 2 - CLEAN SKY 2 (Desarrollo de conceptos y metodologías de alas innovadoras para aviones regionales de próxima generación)
- COMPROBACIÓN HERMANA (Investigación e integración de sistema innovador para Inspección No Destructiva AFP)
- TRINITI - CLEAN SKY 2 (Tanques de nitrógeno termoplásticos multimaterial de alta presión para aeronaves)
- NHYTE - H2020 (Nuevas aeroestructuras de compuestos termoplásticos híbridos fabricadas por OOA)
“También tenemos una relación especial con Cytec en el Reino Unido, desarrollando nuevos materiales y procesos compuestos”, dice Lecce. Tenga en cuenta que Cytec fue adquirida por Solvay y la ubicación a la que se hace referencia es Solvay Composite Materials en Heanor, Reino Unido, un sitio con una larga historia de innovación, incluido el proceso de formación de doble diafragma probado recientemente a través del programa RAPM. “Nuestra última actividad de este tipo fue desarrollar un proceso termoplástico OOA que utiliza una prensa nueva e innovadora que combina PEEK (polieteretercetona) y PEI (polieterimida) en un nuevo material compuesto”. Este nuevo material, equipo y proceso ahora se ha demostrado en un larguero de avión de plástico reforzado con fibra de carbono (CFRP), fabricado mediante consolidación y soldadura in situ de AFP a través del proyecto NHYTE.
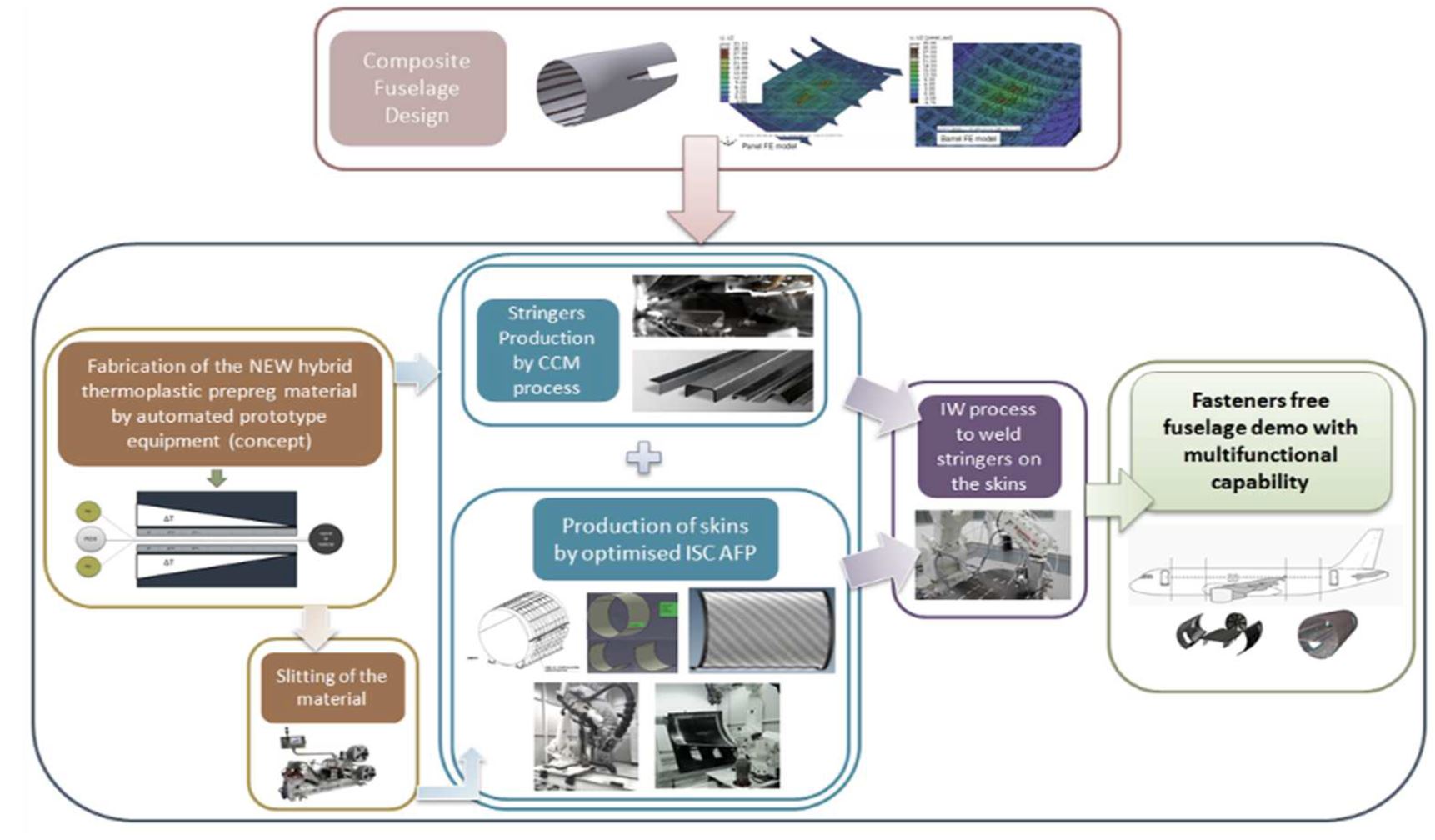
NHYTE
Financiado por el programa Horizonte 2020 de la Comisión Europea, NHYTE es un proyecto de investigación realizado entre mayo de 2017 y octubre de 2020. “NHYTE trata sobre el uso de enlaces amorfos para permitir condiciones sostenibles de temperatura y proceso para compuestos termoplásticos”, explica el Dr. Marco Barile, coordinador del proyecto NHYTE y CTO de Novotech. Esta unión amorfa (ver diagrama a continuación) es un concepto patentado por otro socio de NHYTE, la división de aeroestructuras de Leonardo (Roma, Italia) que tiene múltiples instalaciones de producción en el sur de Italia.
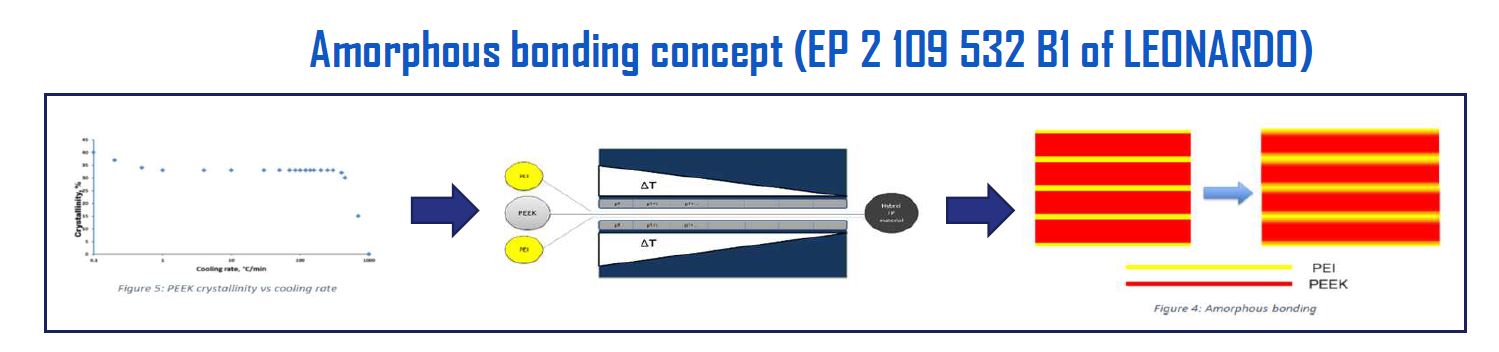
Crédito de la foto:Proyecto NHYTE
“Con el material desarrollado en NHYTE, podemos superar las limitaciones actuales del material con la consolidación in situ (ISC) de AFP de compuestos termoplásticos (TPC). En lugar de procesar a temperaturas poco menos de 400 grados C para los polímeros de PEEK semicristalinos, podemos calentar justo por encima de la temperatura de transición vítrea (Tg) de 215 grados para la capa de PEI amorfa. El derretimiento y enfriamiento del PEI también es más rápido, sin tener que estar tan controlado que el PEEK ". Barile señala que este concepto puede utilizar otros termoplásticos amorfos. Se eligió PEI porque se adhiere bien al PEEK, un material bien probado en múltiples demostradores de aeroestructuras de AFP.
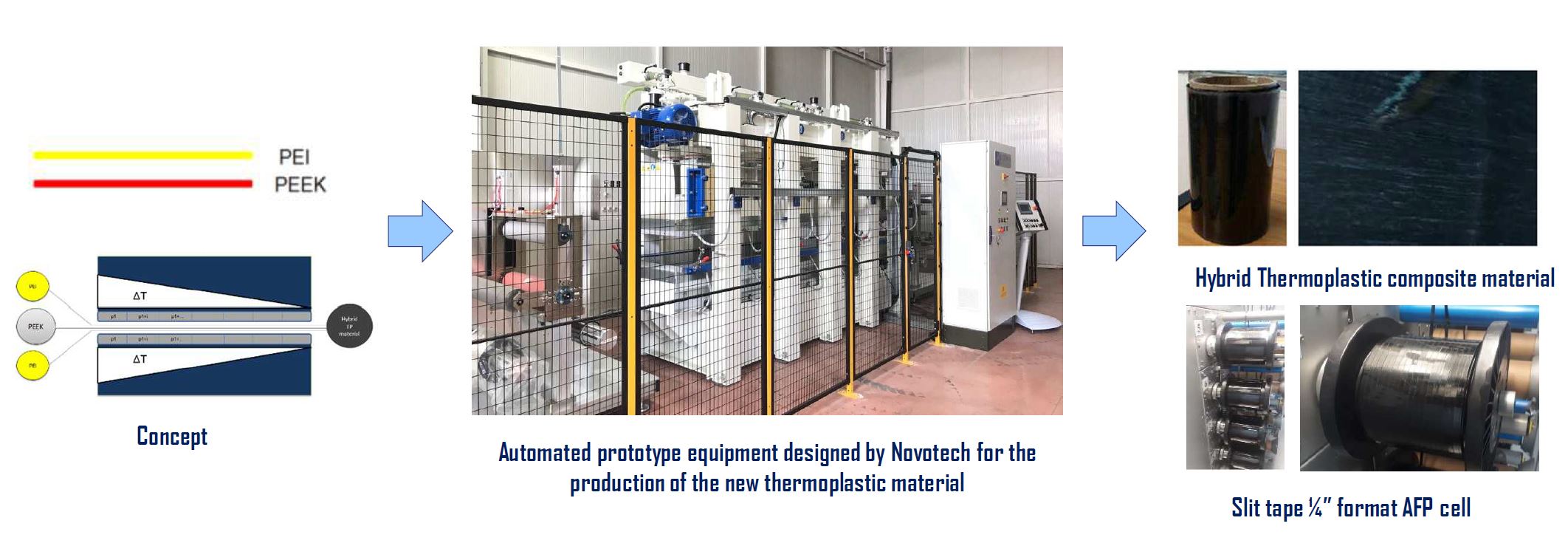
Este nuevo material desarrollado en NHYTE fue producido en una prensa continua diseñada por NOVOTECH. Orma Macchine (Bérgamo, Italia) suministró el cuerpo de la prensa y COMEC Innovative (Chieti, Italia) proporcionó los módulos de enrollado y desenrollado. “Esta prensa puede hacer un rollo continuo de material que luego cortamos en cinta hendida para usar en una máquina AFP”, dice Barile. Tres materiales diferentes ingresan a la prensa por la izquierda, como se ve en la imagen de arriba. "Tenemos PEI arriba y abajo y luego PEEK en el medio", explica Barile.
Como polímero semicristalino, PEEK proporciona las altas propiedades mecánicas necesarias para las estructuras primarias, mientras que las capas de PEI amorfas proporcionan una fusión rápida y sencilla para la unión. “Controlamos la presión y el enfriamiento del material a lo largo de las placas de la prensa, comenzando desde aproximadamente 400 grados C al comienzo de la prensa hasta menos de 200 grados C al final de la prensa. El resultado es un material que es una combinación de las tres capas de entrada ”.
Este nuevo tipo de cinta termoplástica ya está consolidado durante la fabricación, por lo que durante la AFP, solo necesita calentarse para fundir y compactar las capas de PEI para una unión amorfa. El resultado es un laminado que comprende una cinta de PEEK a PEI completamente consolidada y capas de PEI a PEI, como se muestra en la patente de Leonardo. Este proceso de AFP presenta menos obstáculos que el AFP ISC actual que utiliza cintas de PEEK y PEKK (polieteretercetona). Como se explicó en la Parte 2 de mi característica de 2018 sobre consolidación in situ, el AFP ISC actual requiere calentar la cinta y el sustrato a la temperatura de fusión, colocar la cinta sobre el sustrato y luego consolidar con un rodillo para que el proceso de enfriamiento se controle con precisión, lo que permite los polímeros semicristalinos para lograr una cristalinidad suficientemente alta (30-40%) y bajos vacíos (<3-5%) para las propiedades estructurales.
Los críticos de AFP ISC afirman que es demasiado lento:una velocidad de aplicación de 60-100 mm / s frente a 600-700 mm / s para el método de "dos pasos" que comprende una aplicación rápida de AFP seguida de un paso secundario en el horno o autoclave para completar consolidar / recocer tensión térmica en el laminado. “Con nuestro material, puede lograr tasas de aplicación de AFP que no son tan lentas como la consolidación in situ típica y el calentamiento requerido durante AFP también se puede mantener por debajo de 300 grados C”, dice Barile. "Puede cerrar la brecha de rendimiento con los materiales estándar que tenemos ahora". Aquí, Barile está comparando AFP ISC de compuestos termoplásticos con compuestos termoendurecibles utilizados en los aviones Boeing 787 y Airbus A350. “Con componentes grandes como las secciones del fuselaje, el problema es la asequibilidad cuando se usa el curado en autoclave. Los termoplásticos permiten un proceso de producción más asequible, pero tiene altas temperaturas y tasas de AFP lentas con los materiales de grado aeroespacial actualmente disponibles en el mercado. Nuestro enfoque ayuda a resolver estos problemas. Podemos alcanzar aproximadamente un 30 por ciento de cristalinidad en la cinta a través de la prensa continua. Por lo tanto, tiene esa cristalinidad en la pieza y solo está trabajando con la capa amorfa durante la AFP. Aunque todavía es un material experimental, que puede mejorarse, el objetivo del proyecto NHYTE es tener un proceso de fabricación de un solo paso que se pueda utilizar en aplicaciones aeroespaciales estructurales ”.
Optimización de cintas y AFP
“Los primeros materiales de cinta multicapa se fabricaron aquí en Novotech”, dice Barile. Estas cintas utilizaron película de hendidura sin relleno Ultem 1000 de Sabic (Riyadh, Arabia Saudita) para la cinta PEEK reforzada con fibra de carbono PEI y APC-2 / AS4 de Solvay. El espesor total fue ≈0,26 milímetros, que comprendía capas de PEI de 1 o 2 milésimas de pulgada (0,001 o 0,002 pulgadas) de espesor. En la primera fase del proyecto, se probaron múltiples cupones de ambas variaciones para determinar la resistencia al corte interlaminar (ILSS) con el fin de validar el proceso de fabricación de material termoplástico híbrido. Los cupones pequeños también fueron probados por Applus Laboratories (Barcelona, España), socio de NHYTE, para una gama completa de propiedades mecánicas que incluyen resistencia y módulo de tracción y compresión, compresión de pozo abierto (OHC), tensión de pozo lleno, compresión después del impacto (CAI), apenas visible daños por impacto (BVID) y propiedades después del acondicionamiento de fluidos.
“No teníamos la misma experiencia que los proveedores de cintas compuestas termoplásticas, por lo que se puede mejorar la calidad del material. Por ejemplo, el volumen de la fibra varía de bajo a alto a través del grosor, lo que afecta las propiedades de la cinta y el laminado, incluido el ILSS. Pero NHYTE tenía como objetivo demostrar el concepto, lo que hemos hecho ".
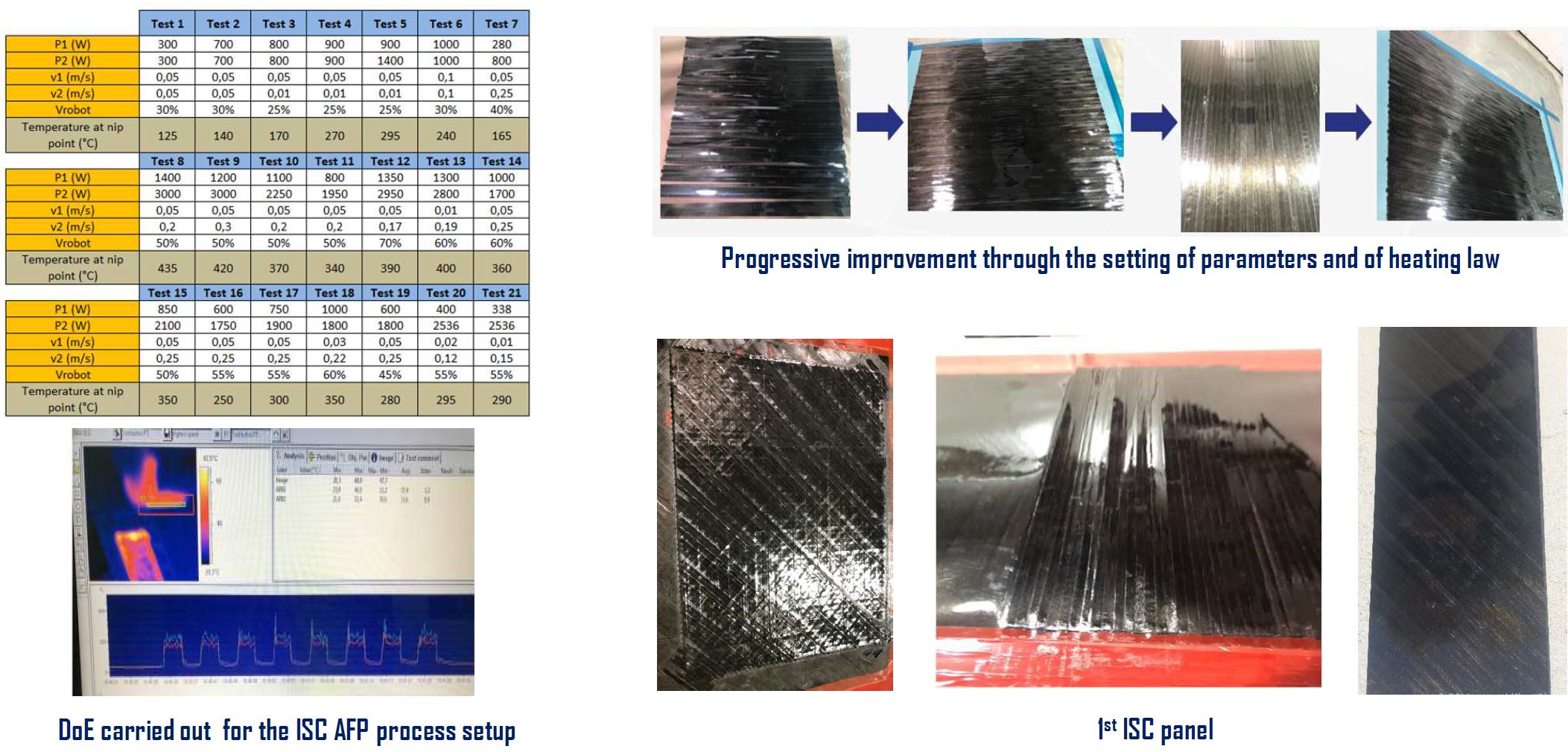
Como se puede ver en las imágenes de arriba, la optimización del proceso de AFP para el nuevo material requirió un trabajo experimental significativo. "También utilizamos un enfoque de diseño de experimentos (DOE) para optimizar los parámetros de AFP y una herramienta fue desarrollada por la Universidad del Sur de Bretaña (USB, Lorient, Francia) asociada de NHYTE para mejorar la carga de calentamiento del láser a través de la simulación numérica predictiva". observa Barile.
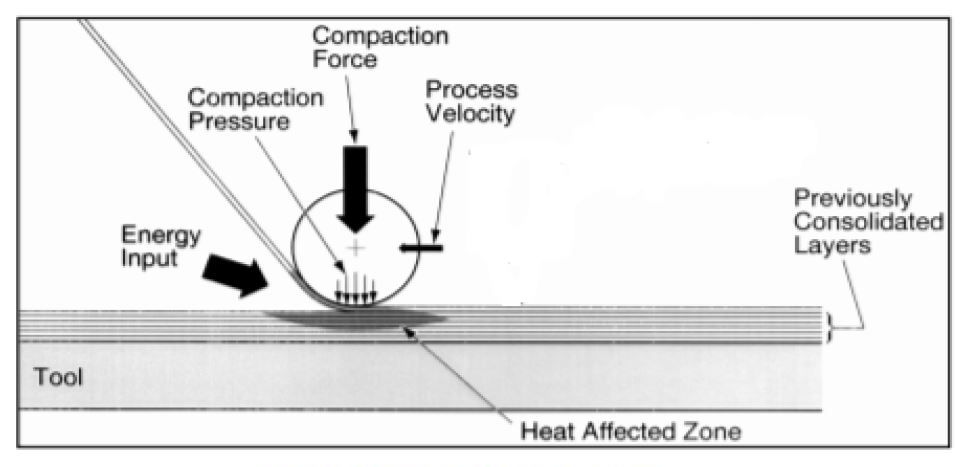
Esta simulación se utilizó por primera vez en la cinta APC-2 para verificar la calidad de la herramienta predictiva y luego se aplicó al nuevo material multicapa. Se ha enviado un artículo sobre este trabajo para su publicación en la revista Composite Structures . "Está modelando las conductividades del calor en el punto de contacto", dice Barile. “Luego verificamos experimentalmente lo que se predijo en la simulación numérica. Esto es necesario para determinar el mejor compromiso entre la velocidad de aplicación, el flujo de fusión de los polímeros y el envejecimiento [cocción] de la lámina compuesta. Es un equilibrio de varias variables durante el proceso de consolidación in situ. Observamos la disminución de temperatura de la cinta entrante sobre la cinta ya colocada en la herramienta. Si puede gestionar este cambio de temperatura, puede reducir la tensión residual en el laminado. Entonces, trabajamos para evaluar la variación de temperatura durante el reposo. Debe personalizar el calentamiento de acuerdo con la forma del camino y la orientación de la lámina.
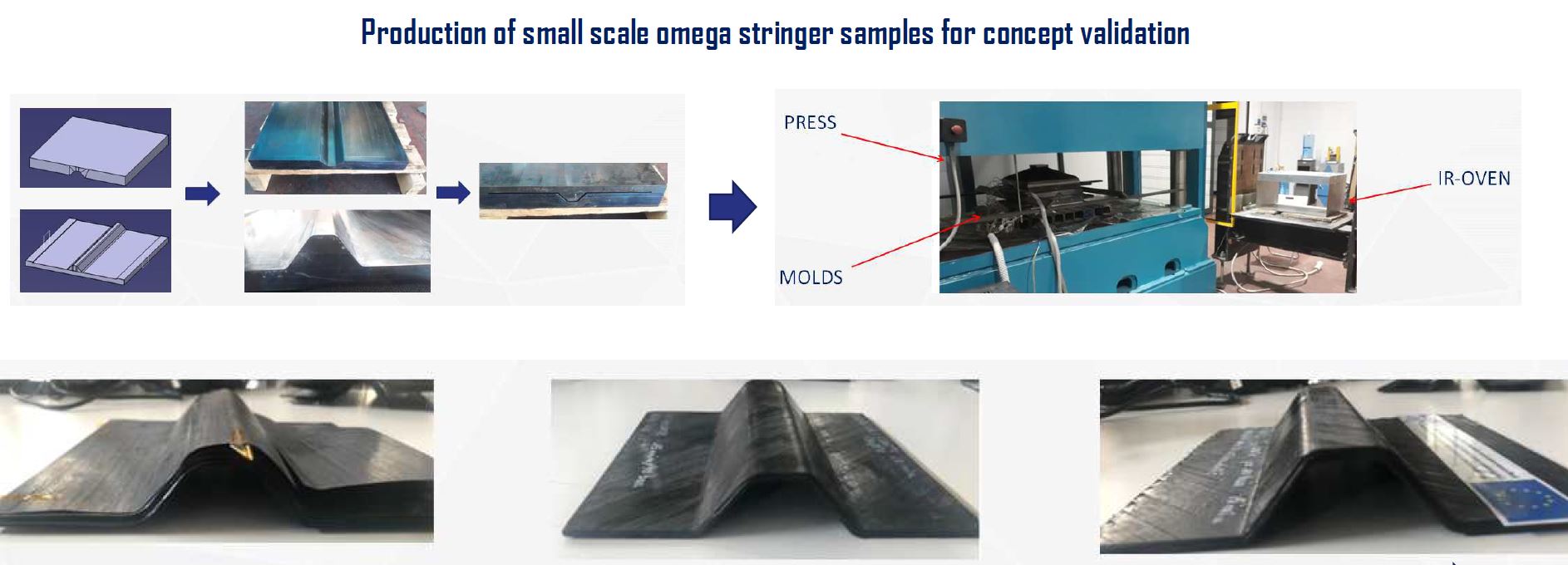
Demostradores de stringer y fuselaje
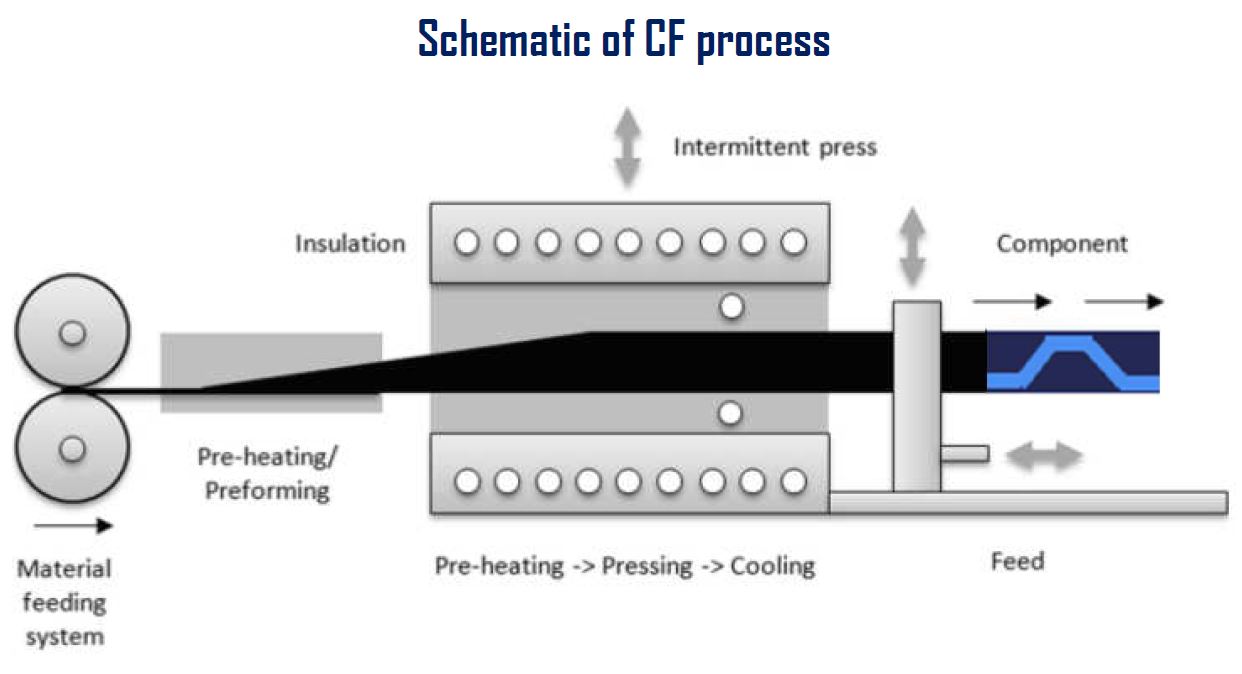
El siguiente paso fue producir demostradores de larguerillos, primero como muestras a pequeña escala hechas con una prensa estacionaria y luego como demostradores de un proceso continuo de formación de larguerillos para verificar lo que se requeriría para la producción de piezas industriales. Estos largueros se unieron luego a un demostrador de panel de revestimiento de fuselaje AFP mediante soldadura por inducción desarrollada por la organización de I + D CETMA (Brindisi, Italia).
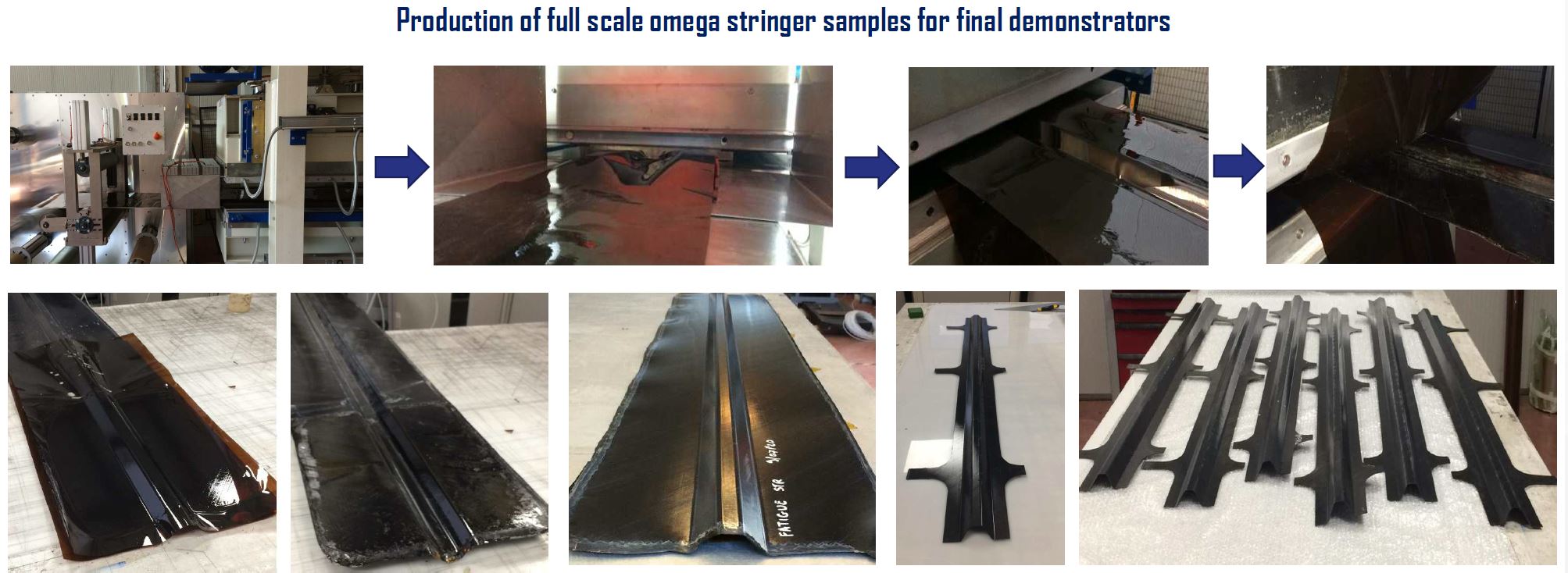
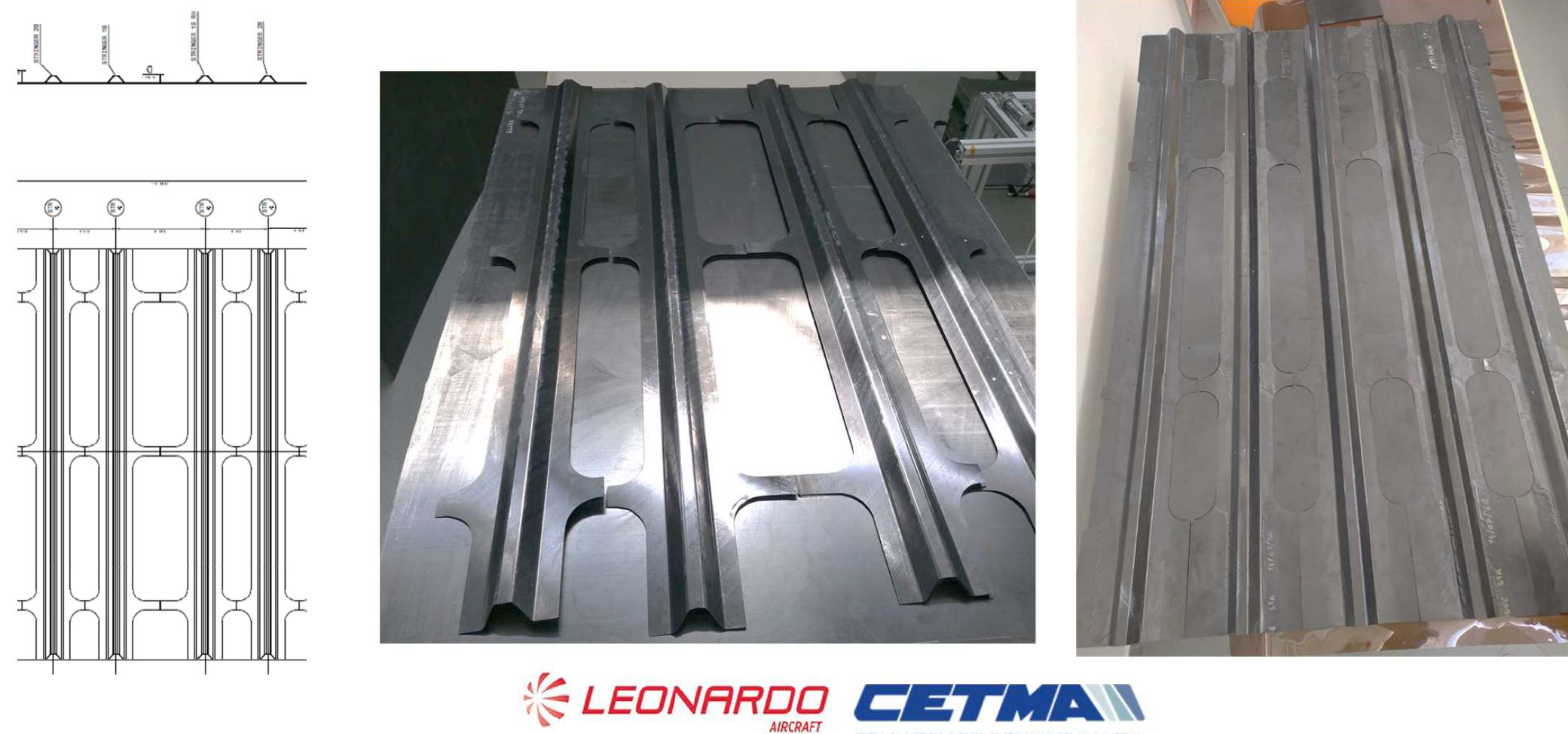
¿El nuevo material multicapa ofreció alguna ventaja para la soldadura por inducción? "Básicamente procesó lo mismo", dice Barile. "Sin embargo, no fue fácil para CETMA definir los parámetros del proceso de soldadura porque nuestro nuevo material tiene una menor cantidad de fibra de carbono en comparación con las cintas estándar". Luego, Applus probó los demostradores de largueros y el demostrador final del panel del fuselaje. Los socios del proyecto NHYTE University of Bath (Bath, Reino Unido) y Leonardo Aircraft también utilizaron NDI para evaluar la calidad de los paneles y largueros.
"Hemos fabricado muchos cupones y piezas pequeñas, así como el gran demostrador", señala Barile. “Los resultados de las pruebas de Applus son muy buenos considerando el menor costo del proceso de fabricación en comparación con lo que es estándar ahora. Tenemos entre un 20 y un 25% menos propiedades de resistencia y rigidez en comparación con los materiales de cinta termoplástica estándar disponibles actualmente, pero hemos identificado mejoras en el proceso que deberían ayudar a mejorar esto ”.
NHYTE finalizó el 30 de octubre de 2020. “Nuestra idea es continuar con un nuevo proyecto para incluir todas las mejoras que tenemos en mente”, dice Barile. “Hemos probado cómo fabricar el material y cómo procesarlo mediante la consolidación in situ de AFP, el conformado continuo y la soldadura por inducción. Ahora necesitamos optimizar aún más para la industrialización ". Novotech busca continuar con el mismo consorcio enriquecido con nuevos socios.
En particular, Leonardo también está trabajando para mejorar la consolidación in situ de AFP utilizando soldadura por inducción y cinta TPC que se puede calentar y enfriar rápidamente. Además, investigadores del Instituto IMDEA Materiales (Madrid, España) y FIDAMC (Madrid, España) acaban de publicar resultados alentadores sobre composites multicapa PEI / PEEK, este último líder en consolidación in situ de AFP desde hace muchos años. Para obtener más artículos técnicos, consulte las publicaciones de NHYTE.
Proyecto SWING
El Smart Wing for New General aviation (SWING) es un proyecto que comenzó con el respaldo de Piaggio Aerospace (Villanova d’Albenga, Italia) y está cofinanciado por el Ministerio de Desarrollo Económico de Italia (MISE). Además de Novotech, el consorcio italiano del proyecto está formado por la empresa de desarrollo tecnológico Protom (Nápoles) como coordinador, Laer Aeronautical Manufacturing (Airola), A. Abete Aerostructures (Nola) y el especialista en diseño aeroespacial ItalSystem (Avellino). Uno de los objetivos de SWING es adaptar los procesos de composites automatizados fuera de autoclave (OOA), incluida la infusión de resina líquida (AFP) y la infusión de resina líquida (LRI), para la producción rentable y sostenible de aviones más pequeños, utilizando el P.180 Avanti ala delantera como plataforma de demostración.
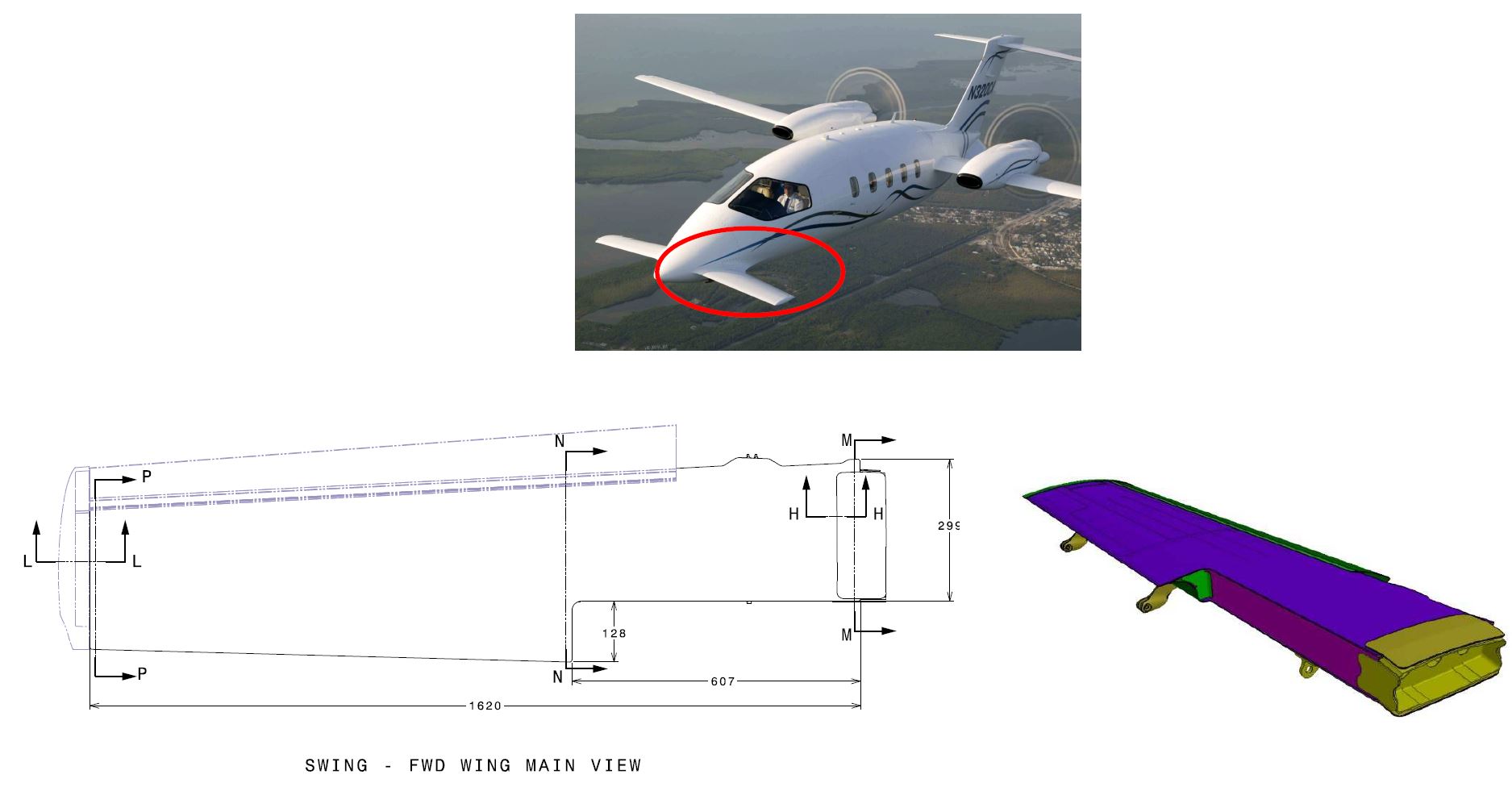
“La idea es producir el ala delantera del P.180 en solo dos partes principales:un panel superior y un panel inferior, ambos moldeados con largueros y largueros integrados”, dice Lecce.
“Para nosotros, esto comenzó con nuestro trabajo como laboratorio calificado para Solvay en el Reino Unido. Hemos cooperado desde 2015 en nuevos materiales y procesos para AFP, LRI y compuestos termoplásticos. Estábamos haciendo preformas secas usando la cinta de fibra seca PRISM TX1100 de Solvay para usar con AFP. A continuación, estas preformas se infundieron con resina epoxi endurecida Solvay PRISM EP 2400 y se curaron en un horno. Estábamos haciendo este trabajo en el marco del proyecto AIRGREEN 2 para el programa Clean Sky 2 Green Regional Aircraft, y luego continuamos con el proyecto SWING ”. Tenga en cuenta que PRISM TX1100 y PRISM EP 2400 fueron calificados por United Aircraft Corporation para la producción del primer ala infundida con resina para un avión comercial:el avión de pasajeros de pasillo único Irkut MS-21 fabricado por AeroComposit.
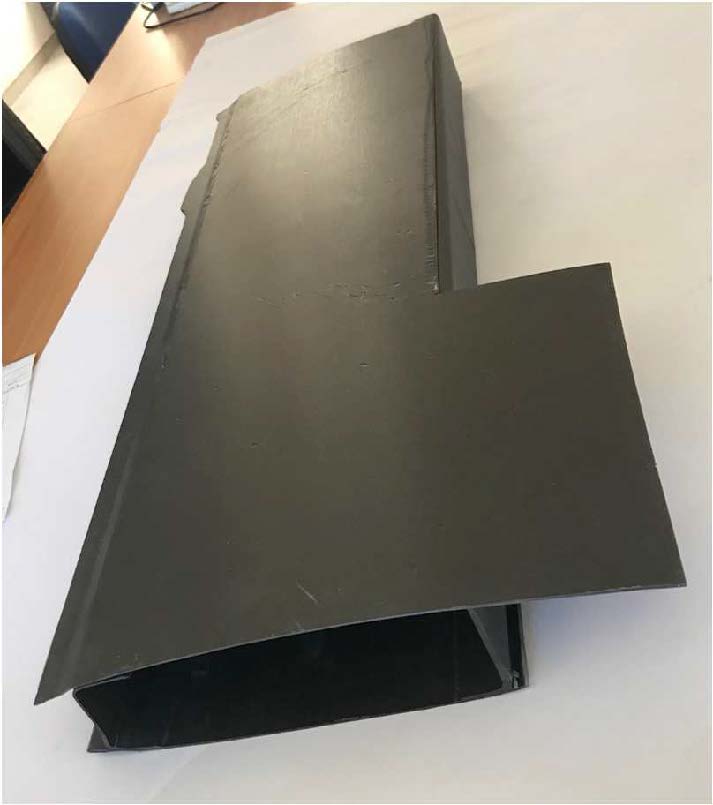
Los paneles moldeados superior e inferior se unirán con adhesivo estructural y luego se probarán estáticamente el próximo año. “Paralelamente, estamos caracterizando otro composite basado en cinta seca TX1100 y una mezcla de resina de Covestro (Leverkusen, Alemania) que puede ser una alternativa válida a las resinas de grado aeroespacial, en particular para los sectores que requieren mayores tasas de producción”, agrega Barile. “Esta resina no es de tan alto rendimiento como esos sistemas, pero funciona bien con la infusión y cumple con los requisitos de la caja del ala. Debe haber algún compromiso si desea reducir los costos. Esperamos que este desarrollo contribuya a introducir la tecnología AFP en la aviación general. También podría utilizarse en el sector de la automoción ”.
TRINITI
Novotech también está trabajando en el proyecto Clean Sky 2 TRINITI - Tanques de nitrógeno de alta presión termoplásticos multimaterial para aviones - que comenzó en 2019 y finalizará en 2021. La entrada de Novotech en este proyecto una vez más evolucionó del desarrollo con una empresa aeroespacial italiana. “Estábamos trabajando para verificar el potencial de AFP utilizando nuestra cinta multicapa en la producción de tanques de combustible criogénico para vehículos de lanzamiento frente a los procesos de bobinado de filamentos que se utilizan actualmente”, explica Barile. "Básicamente, TRINITI desarrollará un concepto de material multicapa similar al NHYTE y luego fabricará un tanque utilizando AFP consolidación in situ".
“La ventaja de AFP con respecto a FW”, prosigue, “es que puedes decidir dónde quieres colocar el material. No está limitado por el filamento enrollado continuamente alrededor de la pieza. Considere un tanque donde tiene mucho material en las tapas de los extremos porque no puede cortar el material durante el bobinado del filamento. Al cortar y reiniciar fibra / cintas donde desee con AFP, el material se usa solo donde se necesita. Por lo tanto, puede administrar los espacios entre las cintas, lo cual es importante para evitar la penetración de gases. Para hacer esto con el devanado de filamentos, hay que aumentar el material aplicado, incluso porque con AFP se usa cinta de hendidura, no estopa impregnada. Y luego, con la consolidación in situ, no hay necesidad de autoclave. Hemos demostrado que las AFP pueden ser una alternativa viable y muy asequible ”.
“Actualmente, CETMA está llevando a cabo pruebas de permeación de gas para evaluar el rendimiento de los materiales multicapa frente a las especificaciones”, dice Barile. El director de temas, Diehl Aviation (Gilching y Dresden, Alemania) ha proporcionado los requisitos para un tanque de nitrógeno de almacenamiento prolongado de alta presión utilizado en los sistemas de extinción de incendios de las aeronaves. Estos tanques deben soportar temperaturas de -55 ° C a 85 ° C en tierra, de -40 ° C a 70 ° C durante el funcionamiento en vuelo y presiones de hasta 1000 bar.
“El objetivo es reducir el peso y los pasos de fabricación”, señala. “Sin embargo, es necesario definir el costo de fabricación con este método. Se ahorra peso al no colocar material innecesario, pero el devanado de filamentos es un proceso más rápido en comparación con AFP ". Otro factor es que este tipo de tanque generalmente tiene un revestimiento de metal o plástico que está envuelto con CFRP. Barile dice que TRINITI está intentando un tanque sin revestimiento (Tipo V). “Evitaremos la permeación de gas mediante el uso de un laminado AFP de bajo vacío. Estamos probando en CETMA ahora con diferentes combinaciones de materiales y preparándonos para reducir la selección. Luego construiremos un tanque prototipo, pero el diseño del tanque depende del material seleccionado y del proceso final. Entonces, esto es en lo que estamos trabajando ahora. La actividad de prueba será realizada por CTL Composites (Galway, Irlanda) ”.
GAVIOTA
El desafiante proyecto SEAGULL se inició hace tres años. “Nuestro objetivo es desarrollar un pequeño hidroavión de nueva generación que incorpore nueva tecnología de fabricación de compuestos, propulsión eléctrica híbrida y un ala plegable automatizada, que desarrollamos y patentamos”, explica Lecce. “La intención era un avión de despegue y aterrizaje corto (STOL) que sea competitivo con los aviones de despegue y aterrizaje vertical (VTOL) pero ofrezca más asequibilidad. Creemos que podría tratarse de una aeronave personal operada desde cualquier superficie y es una posibilidad importante para la aeronáutica y la movilidad futuras ”.
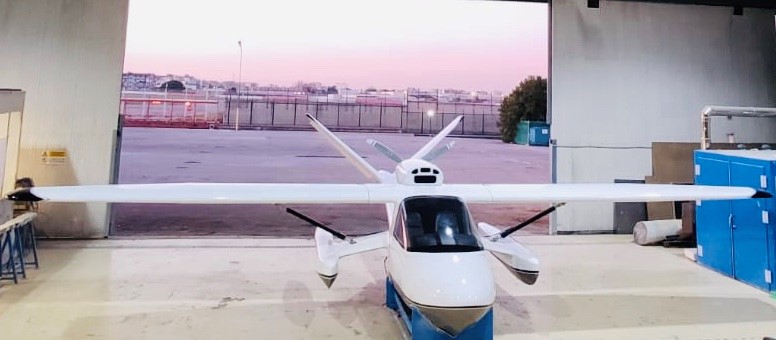
El equipo de SEAGULL ha probado un sistema de propulsión híbrido, construyó un primer prototipo en el agua y comenzó las pruebas en el agua en octubre. "Una vez que se completen estas pruebas, construiremos un prototipo volador dentro de unos meses", dice Lecce. “Este es un equipo con mucha experiencia, compuesto por importantes empresas con más de 50 años de experiencia en la aviación general”.
El prototipo volador SEAGULL contará con un fuselaje, cola y ala compuestos. “Nuevamente, impulsaremos la aplicación de la fabricación automatizada utilizando AFP e infusión de resina”, dice Barile. “Uno de los principales problemas con los compuestos que utilizan estos procesos es el costo de los materiales. De hecho, lo que estamos tratando de hacer es encontrar también una combinación de material y proceso que sea más democrática en términos de costo ”.
Resina
- Fraunhofer IPT desarrolla compuestos termoplásticos en almacenamiento de hidrógeno, álabes de motores y más
- Composites Evolution presenta preimpregnados de alto rendimiento, novedosas cintas termoplásticas UD
- Diseño para la fabricación automatizada de composites de aeroestructuras de bajo volumen
- Las cintas termoplásticas continúan mostrando potencial para aeroestructuras compuestas
- Resinas epoxi reprocesables, reparables y reciclables para composites
- Combinación de medidas dieléctricas de CA y CC para el control del curado de compuestos
- Karl Mayer lanza la línea de producción de cintas termoplásticas UD
- SWM lanza el medio de flujo Naltex para infusión de resina
- Puerta termoplástica por primera vez para compuestos automotrices
- El consorcio de compuestos termoplásticos tiene como objetivo la producción de alto volumen para la industria automotriz y aeroespacial
- Al servicio del mundo de los compuestos en Israel y los EE. UU.