El proceso a medida produce un pedal de freno compuesto cada minuto
Tier 1 Boge Rubber &Plastics Group (Damme, Alemania) produce lo que dice son los pedales de freno totalmente compuestos más ligeros, menos costosos y más fuertes del mundo, y los primeros en producción comercial. Como se detalla en el FOD de enero (consulte "La estructura compuesta termoplástica reemplaza los metales en los pedales de freno críticos para la seguridad"), el proveedor actualmente produce un cuarto de millón de pedales de freno por año para cuatro plataformas de vehículos producidas por fabricantes de automóviles alemanes y el sistema podría producir hasta 1 millones de pedales al año. Esto es importante porque los pedales son estructurales, deben cumplir con los mismos requisitos rigurosos de rendimiento que el acero y el aluminio existentes, y los diseños cuentan con tres tipos diferentes de compuestos termoplásticos reforzados con vidrio.
Tres materiales aumentan la eficiencia de la fibra
Para mantener los pedales ligeros, delgados, rentables y capaces de cumplir con las exigentes especificaciones de los fabricantes de equipos originales, Boge utiliza una lámina orgánica de fibra de vidrio continua como estructura de carcasa para transportar las cargas principales de la pieza, que pueden llegar a los 3000 newton. Los espacios en blanco de organosheet se suministran precortados a medida, con dos o tres capas totalmente consolidadas por el proveedor Lanxess Deutschland GmbH (Colonia, Alemania). Para reforzar las rutas de carga principales en la hoja orgánica en blanco, Boge agrega tiras de cintas de fibra de vidrio unidireccionales (UD) (suministradas por Celanese Corp., Irving, Texas, EE. UU.) En orientaciones y capas basadas en resultados de simulación de elementos finitos. Para ello, Boge utiliza un software que ha modificado y tarjetas de material que la empresa ha desarrollado con sus proveedores en función de las curvas de tensión / deformación medidas para cada material en las condiciones de temperatura y humedad especificadas por los clientes OEM. Para agregar geometría funcional, Boge utiliza compuestos de fibra de vidrio picada sobremoldeada (de múltiples proveedores) para proporcionar nervaduras estructurales y características de fijación.
Todos los materiales presentan matrices de poliamida 6 (PA6) negra precoloreada, un polímero resistente muy utilizado en la industria automotriz. Si las especificaciones del OEM lo requieren, Boge también tiene la opción de usar una matriz PA6 / 6 menos higroscópica y de mayor temperatura en el compuesto de sobremoldeo, ya que ambos polímeros son lo suficientemente similares para unirse entre sí. Mediante el uso de tres tipos diferentes de compuestos con refuerzo de vidrio en tres formas diferentes, Boge puede colocar la fibra precisamente donde se necesita para cumplir con los requisitos de rendimiento y evitar el exceso de ingeniería. El efecto de arrastre de este enfoque de compuesto híbrido es que reduce el uso de material, el espesor nominal de la pared, el tiempo de ciclo y el costo total de la pieza.
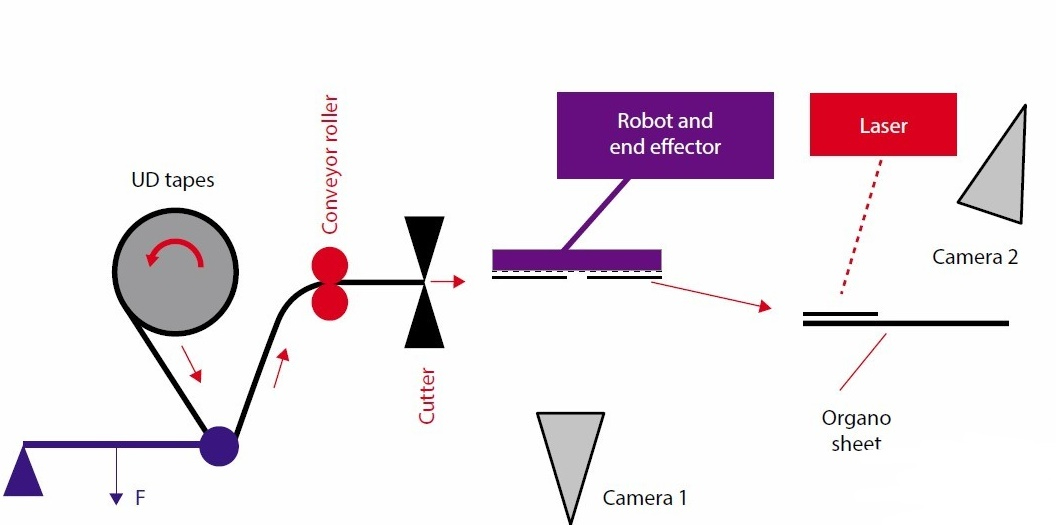
Pasos del proceso y criterios del equipo
Colaboración con el desarrollador de líneas de montaje / automatización M.A.i. GmbH &Co. KG (Kronach, Alemania), Boge ha desarrollado un proceso de producción de tres pasos que es rápido, eficiente y produce piezas de calidad verificada a costos asequibles. Al diseñar el proceso y el equipo, el equipo tenía una serie de requisitos. Primero, para mantener bajos los costos de las piezas, las empresas necesitaban mantener el tiempo de ciclo efectivo total en ~ 1 minuto. Lograr esto requeriría automatización para garantizar que los materiales se muevan sin problemas a través de la celda de fabricación.
En segundo lugar, mientras que los espacios en blanco de la hoja orgánica se suministran preempaquetados, completamente consolidados y precortados a la medida (contorneados), los requisitos de varios diseños de pedales significaban que el equipo necesitaba flexibilidad para cortar, orientar y colocar tiras de cinta de diferentes longitudes en diferentes ubicaciones y direcciones para reforzar el rutas de carga principales de la carcasa de la hoja orgánica. Nuevamente, para mantener bajos los costos, se diseñó un proceso de colocación de cintas a medida para ofrecer un alto nivel de flexibilidad y control, así como también velocidad.
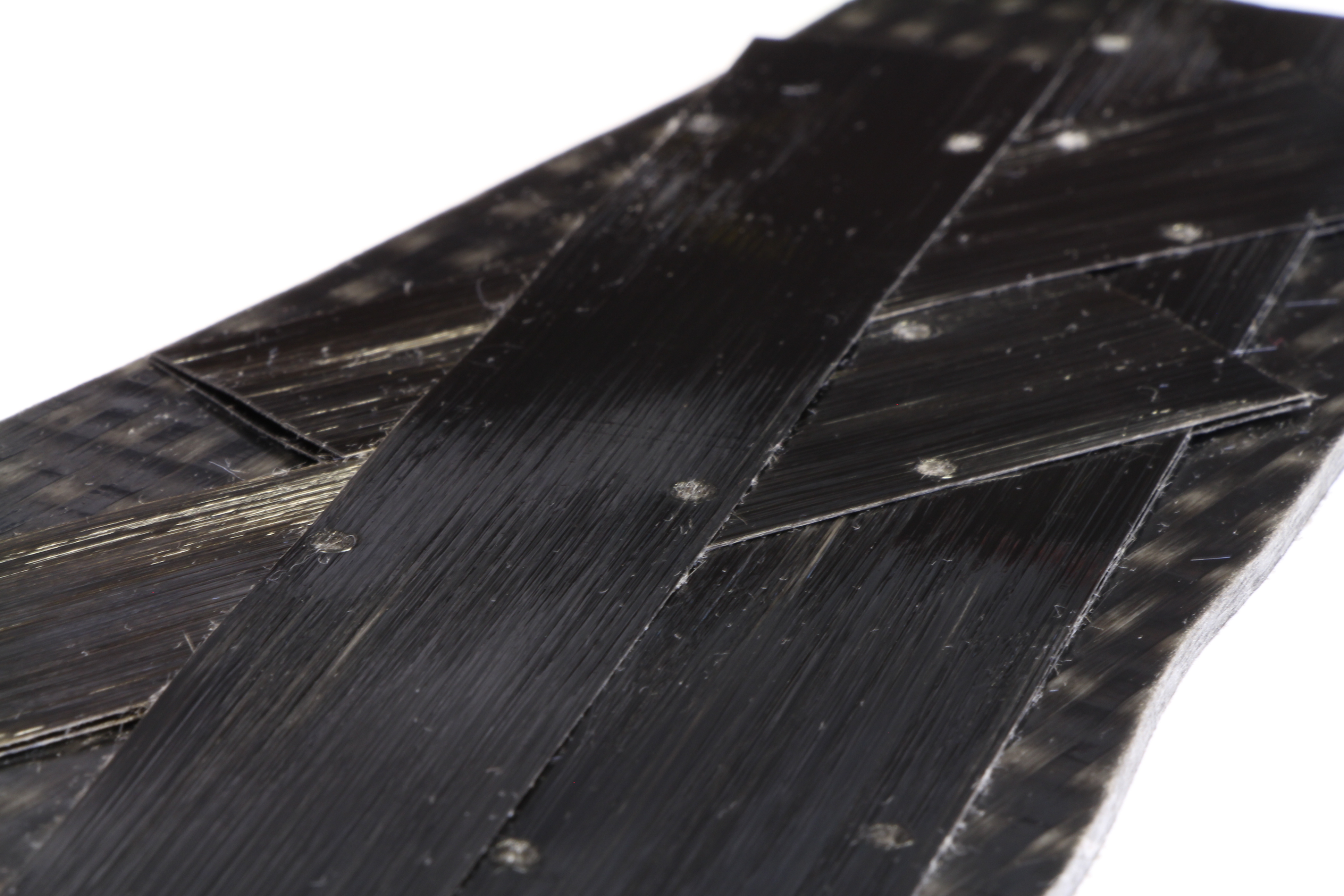
Al inicio del proceso, la celda de fabricación contiene dos pilas de precortadas planchas de organosheet en casetes y cuatro filetes de cintas UD a la vez. Primero, un robot toma una hoja orgánica contorneada y la mueve a la superficie de trabajo. Al mismo tiempo, la cinta UD se extrae y se corta a la longitud requerida. Luego, las tiras se colocan en una cinta de vacío que las mantiene en su lugar a medida que avanza el transportador. A continuación, un robot con una unidad giratoria de recogida y colocación (efector final) extrae una tira a la vez de la correa de vacío y una cámara comprueba la calidad, la dimensión y la posición de cada tira. Cuando se han recogido las cuatro piezas, el robot se mueve al espacio de trabajo y comienza a colocar una tira a la vez en la hoja orgánica en blanco en la ubicación y posición determinadas por la corrección de posición basada en imágenes. A medida que se coloca cada tira, se evita que se mueva mediante múltiples puntos de soldadura creados por un láser. Mientras tanto, se cortan más tiras de cinta y se colocan en la correa de vacío y el proceso se repite hasta que todas las cintas requeridas para un diseño de pedal de freno determinado se apilan y clavan en la posición correcta en la hoja orgánica.
El sistema que produce este blanco de fibra a medida es 100% controlado numéricamente, con todos los aspectos de la operación totalmente programables para una máxima flexibilidad. En cada paso, las cámaras u otros sensores, que están conectados al sistema de control de calidad en línea (QC) del sistema, detectan todos los bordes y posiciones de las tiras de cinta y la carcasa de la hoja orgánica y comparan los datos geométricos de estos materiales con los parámetros conocidos para asegurar que cada material es colocado donde debe estar.
Para mantener altas las velocidades de producción, el blanco de fibra a medida se mueve a continuación a un horno de infrarrojos para calentar ambos materiales justo antes de cubrir / preformar / consolidar las cintas sobre la hoja orgánica. Un paquete antioxidante especial en sistemas de resina de láminas orgánicas y cinta evita el daño térmico. A continuación, la pieza en bruto caliente se mueve rápidamente a la cavidad de drapeado / preformado donde se usa alta presión para formar la pieza en bruto en forma de canal en U, mientras se asegura una superficie de alta calidad. El sistema de control de calidad vuelve a controlar la consolidación y la calidad del preformado mediante el tiempo, la temperatura y la presión.
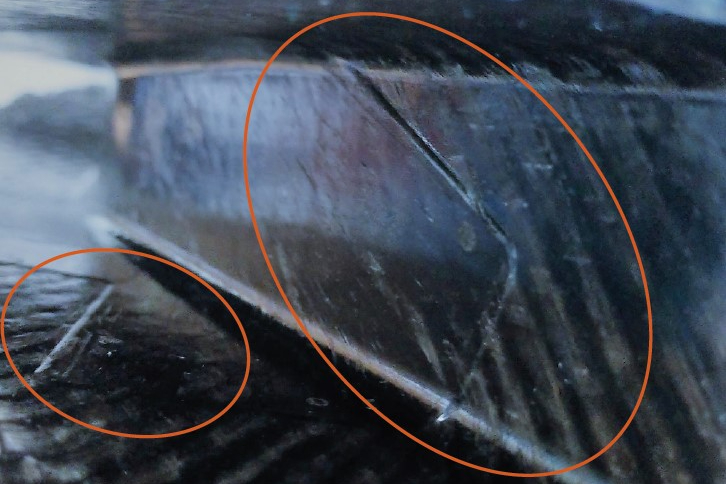
Finalmente, la película aún cálida y cubierta se transporta a un molde de inyección donde se sobremoldea con un compuesto de vidrio corto / PA para crear una geometría adicional, como una estructura de nervadura compleja en la parte inferior. Después del desmoldeo, se realiza un recorte rápido y automatizado y una inspección visual. No se necesita pintura u otro acabado de superficie. El tamaño final del pedal es de aproximadamente 350 x 90 x 60 milímetros. Antes de salir de la celda de fabricación, se coloca un código QR exclusivo en cada pedal para vincularlo con los datos de fabricación y materiales de ese pedal en el sistema de calidad. Después del montaje, se realiza una prueba funcional del pedal dentro de su soporte y una inspección robótica final. Suponiendo que la unidad pasa, se coloca otro código QR en el conjunto del pedal de freno completo para proporcionar una trazabilidad completa de cada pedal y componentes adicionales antes del envío al OEM.
Debido a que los pedales de freno son piezas críticas para la seguridad y deben cumplir con el exigente rendimiento de los fabricantes de equipos originales, así como con los requisitos de calidad, Boge y sus socios han construido múltiples mecanismos a prueba de fallas en el sistema de control de calidad compatible con la Industria 4.0 para verificar de manera rápida y precisa que se cumplieron las especificaciones en cada paso en el proceso. Los datos de control de calidad se almacenan y cada pedal recibe un número de identificación único en forma de código QR para asegurar el 100% de la trazabilidad del material, los cambios y las condiciones del proceso involucradas en la producción de esa pieza.
Los pedales de freno totalmente compuestos que produce Boge pesan aproximadamente la mitad del peso de los pedales de metal. También mejoran la háptica de conducción para los consumidores, son 100% reciclables al final de su vida útil y cumplen o superan el requisito de resistencia del acero tradicional.
Resina
- Los métodos de fabricación de composite más populares
- Desbarbado y desbarbado criogénico
- Primer pedal de freno totalmente de plástico para automóvil deportivo eléctrico a batería
- Solvay expande la capacidad de compuestos termoplásticos
- La rueda termoplástica toma el camino difícil
- Proceso de deposición y propiedades de recubrimientos compuestos de Ni-P-Al2O3 sin electrodos en una aleación de magnesio
- Se presentó el compuesto de revestimiento arquitectónico
- Haciendo mejores bicicletas compuestas en Arkansas
- Cómo funciona el proceso de CMC
- Las 4 cosas críticas que todo operador de prensa plegadora debe saber
- 4 cosas que todo operador de plegadora debe saber mientras duerme