Las grandes cubiertas compuestas protegen mucha agua
El almacenamiento y suministro de agua en Bogotá, Colombia, como en cualquier gran área urbana, es complicado. El desafío no es de abastecimiento, ya que la ciudad de unos 9 millones de habitantes recibe 32 pulgadas (824 milímetros) de lluvia cada año, además del río Bogotá que atraviesa la ciudad. El desafío es capturar esa agua, tratarla y luego almacenarla para que siga siendo potable y esté disponible según lo necesiten los residentes y las empresas. Para ello, la Empresa de Acueductos y Alcantarillados (Empresa de Acueductos y Alcantarillados, EAAB, Bogotá) ha construido a lo largo de los años una serie de 59 tanques en toda la ciudad para almacenar agua tratada y asegurar el suministro a los clientes.
Algunos de estos tanques son tanques reales, completamente cerrados para proteger el agua de los elementos externos. Otros, muchos de ellos más antiguos, son lavabos de hormigón macizo protegidos de los elementos con una serie de tapas extraíbles. Uno de esos tanques, llamado Casablanca y ubicado en el barrio de Ciudad Bolívar en la sección sur de Bogotá, atiende a una población de aproximadamente 3 millones de personas. Casablanca, el tanque de almacenamiento de agua más grande de la red EAAB y el tanque de almacenamiento de agua más grande de Colombia, mide 144 metros (472 pies) de largo x 110 metros (361 pies) de ancho x 9 metros de profundidad y tiene capacidad para almacenar 143.000 metros cúbicos ( 38 millones de galones) de agua. El tanque está dividido en dos por un divisor de concreto que corre por su centro para que el agua se almacene en dos secciones iguales.
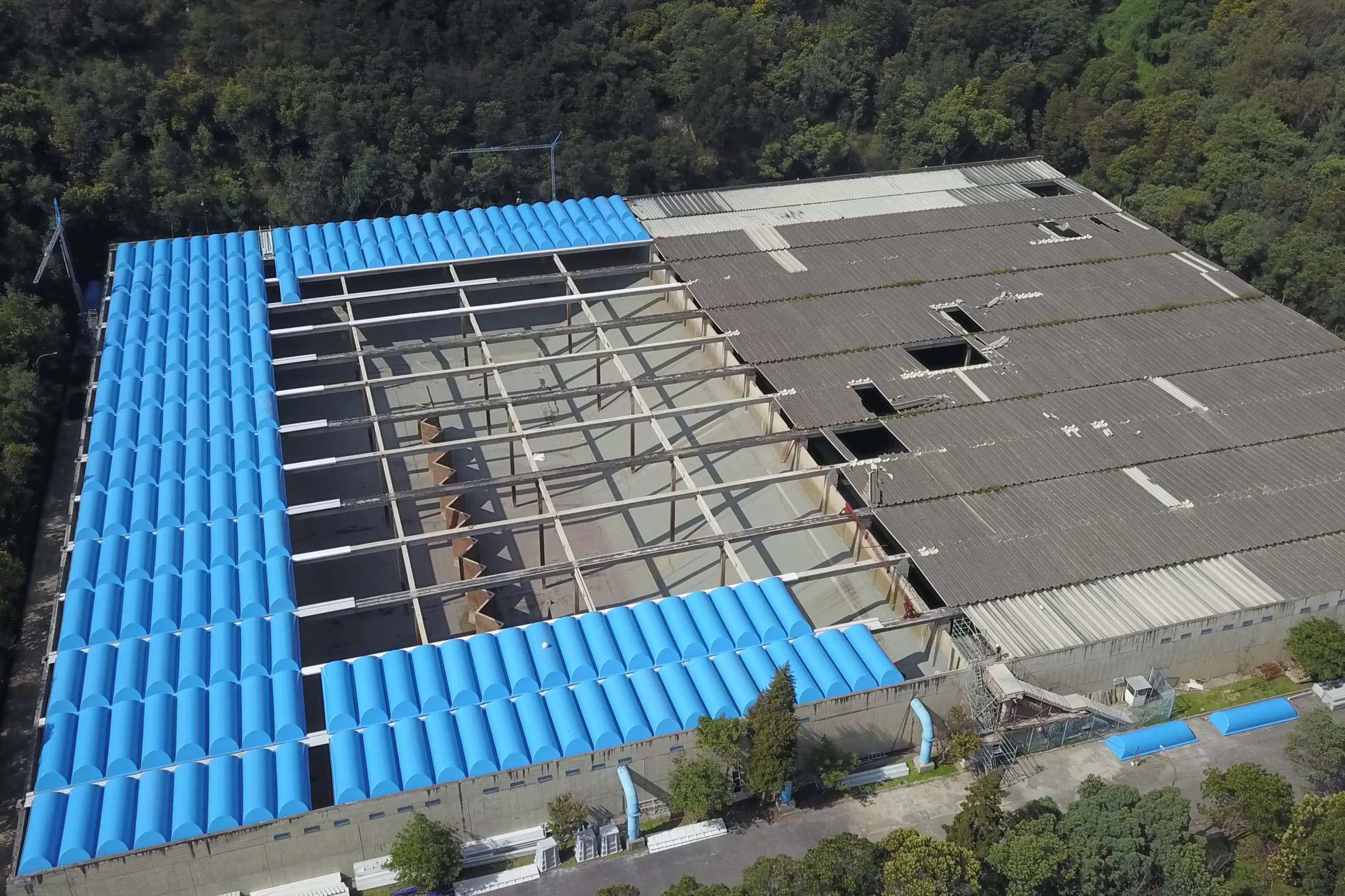
Mantener el Casablanca de 66 años no es tarea fácil. En 2009, se descubrió que las grietas en el piso de concreto del tanque dejaban escapar 360,000 litros (95,000 galones) de agua cada hora . Las reparaciones del hormigón con un revestimiento de poliurea redujeron las fugas a cero. Casablanca, sin embargo, todavía tenía un problema por encima del hormigón. El agua del tanque estaba protegida por una serie de cubiertas que consistían en una mezcla de concreto y asbesto, lo que representaba una amenaza significativa para la calidad del agua y la salud humana. Las cubiertas antiguas también eran propensas a fallar y su mantenimiento era caro. EAAB necesitaba reemplazar las cubiertas viejas por una alternativa más segura, liviana y duradera.
Grandes portadas, y muchas de ellas
EAAB decidió buscar una solución de materiales compuestos para las cubiertas, pero la escala del proyecto lo desafió de inmediato. Casablanca está atravesada por una serie de pilares de hormigón que soportan una red de vigas sobre las que descansan las cubiertas. Estas vigas están espaciadas alrededor de 7.2 metros (23.6 pies), por lo que las nuevas cubiertas tendrían que ser autoportantes y cubrir ese tramo para hacer uso de la infraestructura existente. EAAB propuso que tales cubiertas se fabriquen mediante moldeo por transferencia de resina ligera (LRTM). ¿El reto? Las estructuras compuestas de este tamaño requeridas para esta aplicación nunca se habían fabricado mediante LRTM en Colombia. Muchos fabricantes simplemente no pudieron asumir el proyecto.
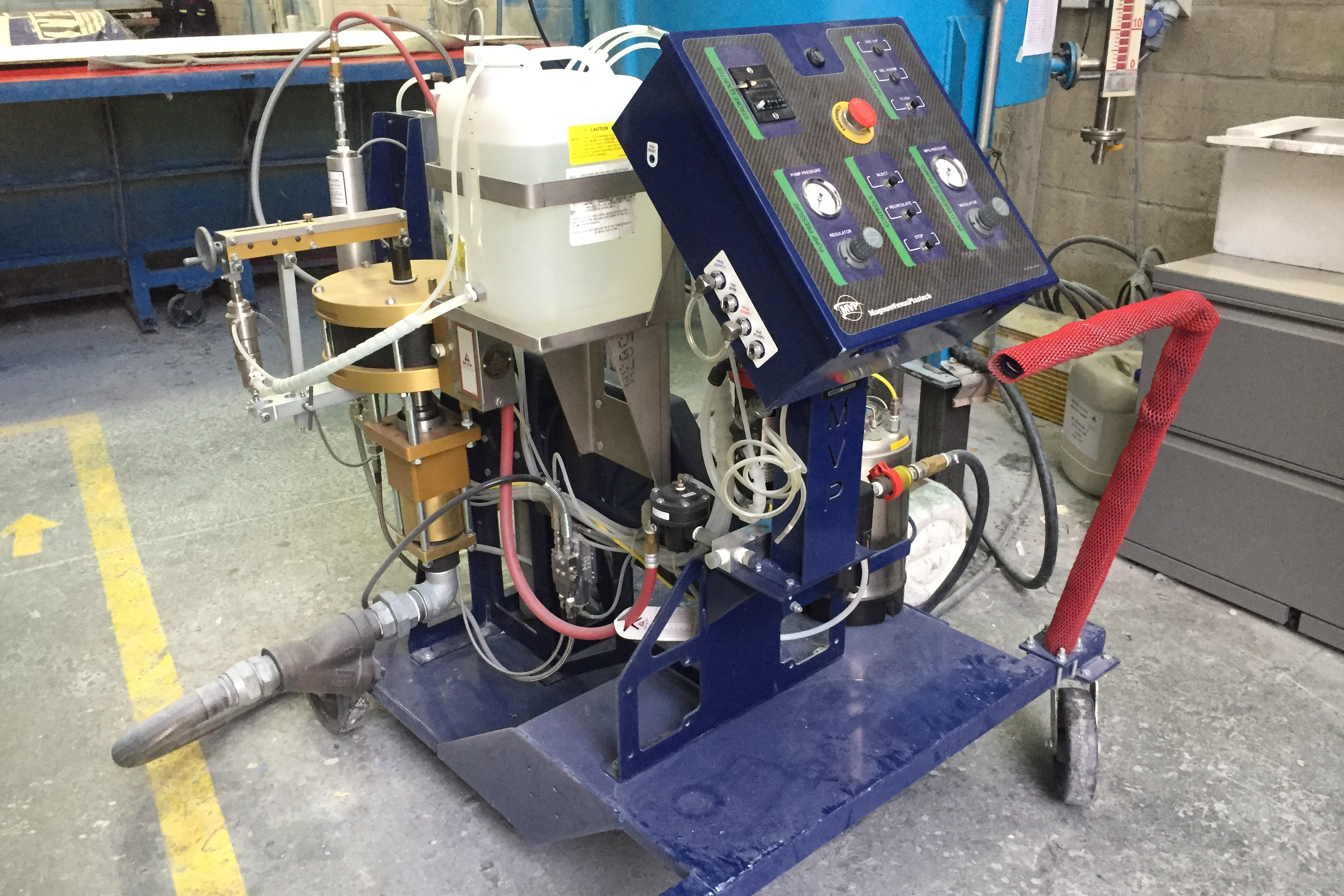
La excepción fue Innovative Engineering Solutions, o Soling, un fabricante de composites ubicado en La Estrella, Antioquia, Colombia, al sur de Medellín. Soling fue fundada en 2014 por Javiar Moreno, quien posee y opera varias empresas de fabricación de compuestos en Colombia y sus alrededores. Rodrigo Vergara, coordinador de ingeniería de Soling, dice que el tamaño de las cubiertas no fue una novedad para muchos fabricantes. “Nadie tenía experiencia con esto en Colombia por el tamaño de la pieza”, señala. “Es la pieza compuesta más grande fabricada en Colombia”. Para Moreno, sin embargo, el tamaño de las portadas fue un desafío interesante. “Para nuestro dueño [Moreno]”, dice Vergara, “fue un sueño hecho realidad. "Imposible" es una palabra que no entiende. Dijo:'¡Haremos esto!' Yo dije, '¡Está bien!' ”
Soling propuso una solución específica para el proyecto Casablanca:una serie de 840 estructuras compuestas rectangulares abovedadas, cada una de las cuales mide 7,6 metros de largo y 2,4 metros de ancho (24,9 x 7,9 pies). Se eligió el diseño de cúpula semicircular, dice Vergara, porque “la forma geométrica que tiene la mayor resistencia mecánica es una circunferencia. Este fue el factor principal para garantizar que las cubiertas fueran autoportantes. Por otro lado, teníamos que encontrar la forma más sencilla de enviarlos desde el sitio de fabricación hasta el punto de instalación, que estaba a 260 millas de distancia ”.
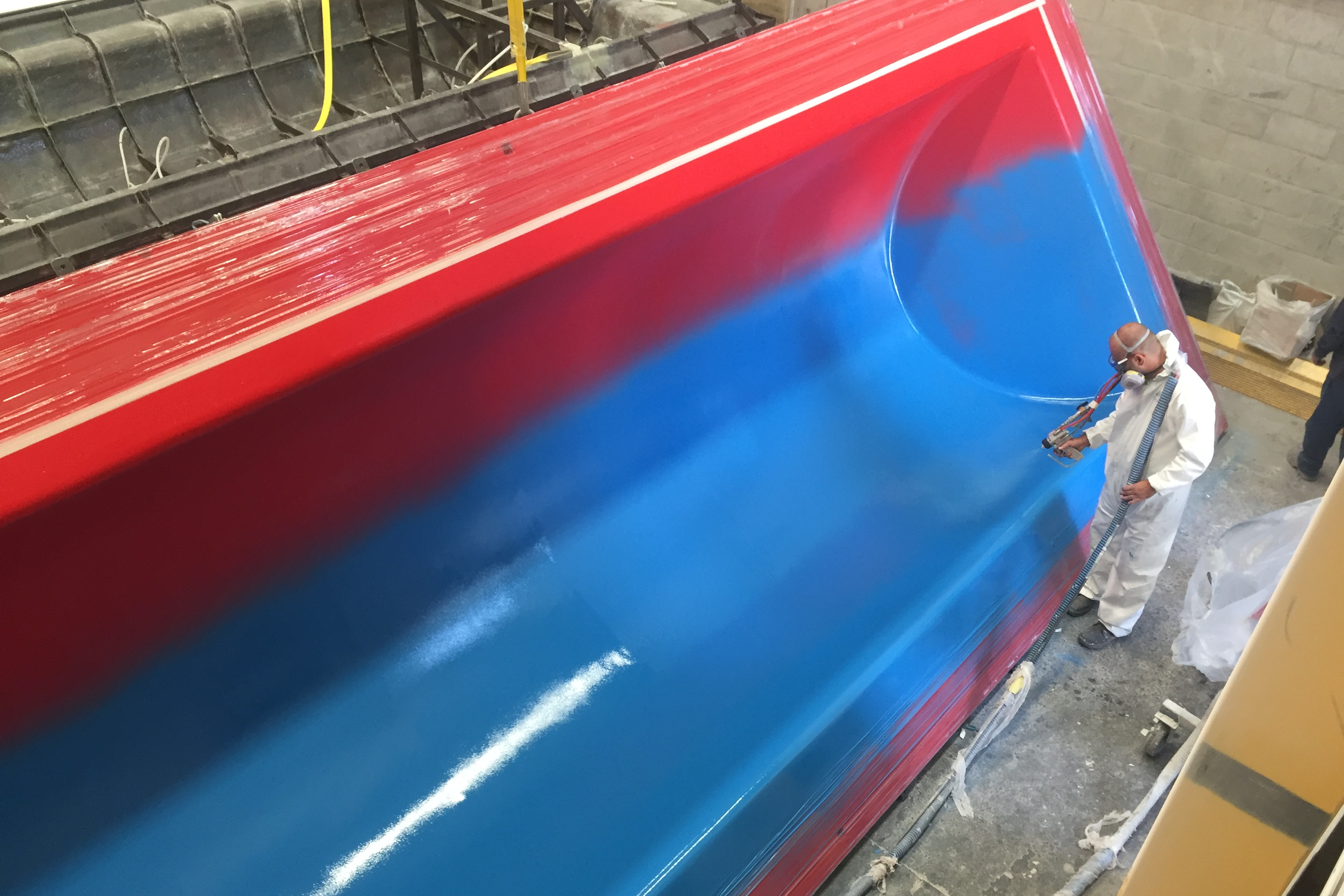
Las cubiertas se fabricarían mediante LRTM con, según la especificación de la EAAB, una capa de gel azul en la superficie exterior y una capa de gel blanca en la superficie interior. Compuesto por tejidos de fibra de vidrio y una resina de poliéster, la cubierta, con una superficie de 28,5 metros cuadrados (207 pies cuadrados), pesaría 320 kilogramos (705 libras), 208 kilogramos de los cuales serían resina. Con un diseño en la mano y el compromiso de entregar las cubiertas, Vergara y Soling se pusieron manos a la obra.
Construyendo la cubierta perfecta
Soling, por supuesto, no asumió el proyecto de Casablanca sin ayuda. Trabajar con la empresa era una red de suministro que incluía un distribuidor, un proveedor de materiales y un proveedor de equipos. El distribuidor, Minepro SAS (Medellín, Colombia), brindó soporte técnico y trabajó con el proveedor de equipos Magnum Venus Products (MVP, Knoxville, Tenn., EE. UU.), Que suministró bombas y equipos auxiliares para el proceso LRTM. Los proveedores de materiales son Andercol (Medellín), que proporcionó la matriz de resina de poliéster, gelcoats y soporte técnico, y Jushi (Ciudad de Tongxiang, China), que proporcionó los tejidos de fibra de vidrio E.
La fabricación, naturalmente, comienza con las herramientas. La pregunta era cuántos moldes requería el proyecto. Para determinar esto, Vergara dice que Soling primero tuvo que establecer el ritmo de fabricación para cumplir con los requisitos de entrega de EAAB. Esto, a su vez, se vio afectado por los requisitos en el lugar de trabajo. Para evitar la contaminación potencial del suministro de agua durante la instalación de las nuevas cubiertas, la EAAB acordó vaciar la mitad de Casablanca sobre la cual se entregaban las cubiertas y colocarlas en su lugar. Reducir la capacidad de almacenamiento de agua de Casablanca a la mitad plantea desafíos, por lo que la EAAB necesitaba que la entrega y la instalación se realizaran lo más rápido posible.
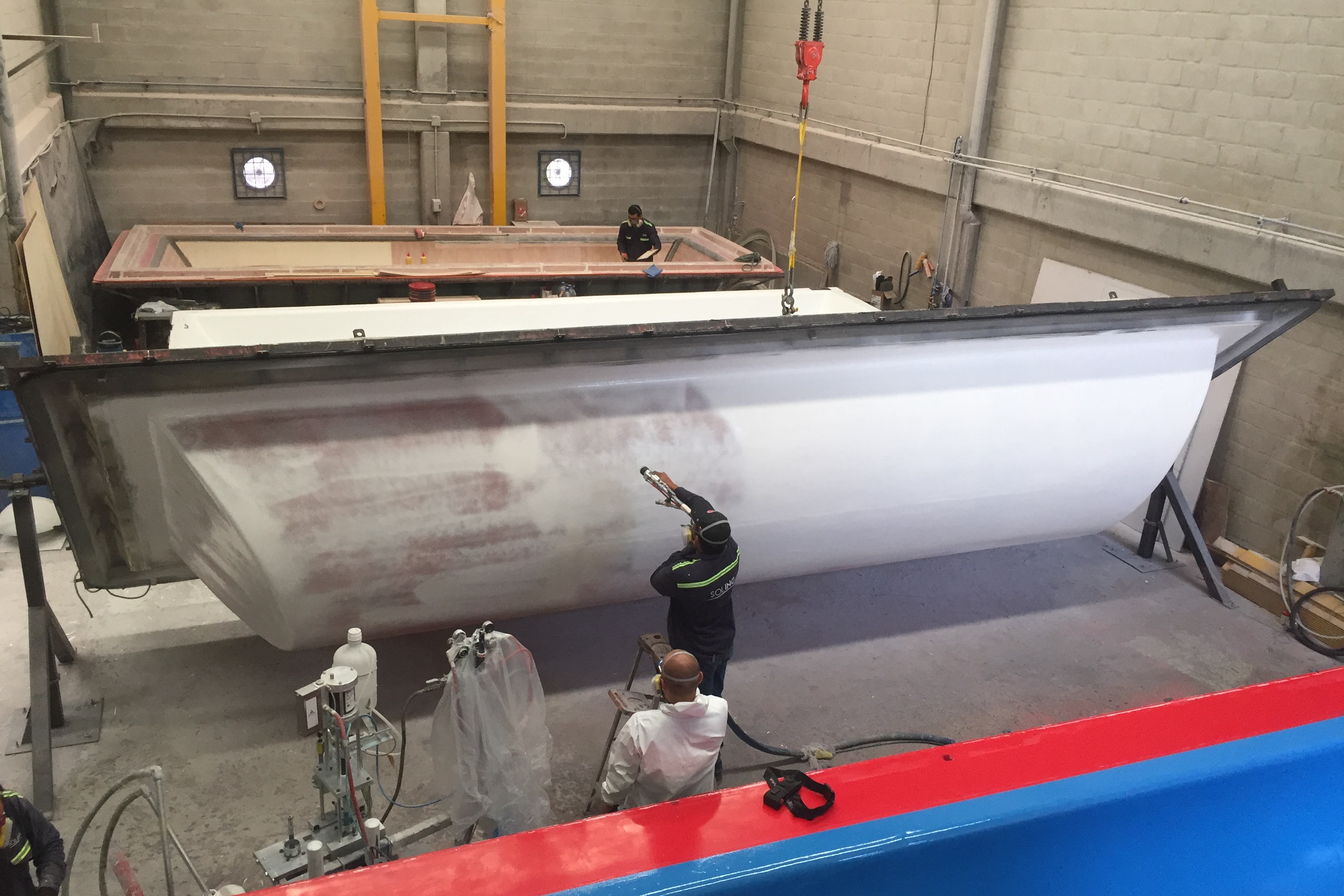
Soling, en colaboración con EAAB, explica Vergara, estableció un programa de producción que entregaría seis cubiertas por día. En una instalación que ejecuta tres turnos de ocho horas por día, eso requería dos moldes, cada uno capaz de fabricar una cubierta por turno. Los moldes, dice, fueron construidos internamente y estaban compuestos por un diseño masculino / femenino compuesto de fibra de vidrio respaldado por una estructura de soporte de acero.
Con los moldes construidos, Soling comenzó el trabajo de establecer cómo, específicamente, se fabricarían las cúpulas. Trabajando con Minepro y MVP, Vergara dice que se decidió que cada molde sería alimentado por dos puertos de inyección de resina, con un puerto de vacío. Para la inyección de resina, MVP recomendó el uso de su unidad de bomba de moldeo por transferencia de resina (RTM) de alto volumen Patriot Innovator, que es capaz de entregar el gran volumen de resina que requiere cada cubierta. MVP también proporcionó sus válvulas Turbo Autosprue, así como acopladores universales, sellos y accesorios para moldes.
Para comenzar la producción de una cubierta, dice Vergara, la mitad hembra del molde se roció con gel coat blanco y la mitad macho del molde se roció con gel coat azul. Como se señaló, ambos gelcoats fueron suministrados por Andercol. A continuación, las esteras y telas de vidrio E suministradas por Jushi se colocaron a mano en la mitad femenina del molde. A continuación, se bajó, mediante una grúa, la mitad macho del molde a la mitad hembra, con las dos mitades unidas. Después de tirar del vacío, comenzó la inyección de resina. Vergara dice que la inyección de cada cubierta se completó en aproximadamente 40 minutos, seguida de un curado a temperatura ambiente. Después de que se demolió cada cubierta, se recortó a las dimensiones finales y se cortaron canales de alimentación para mitigar el agua de lluvia en la superficie del reborde de la cubierta.
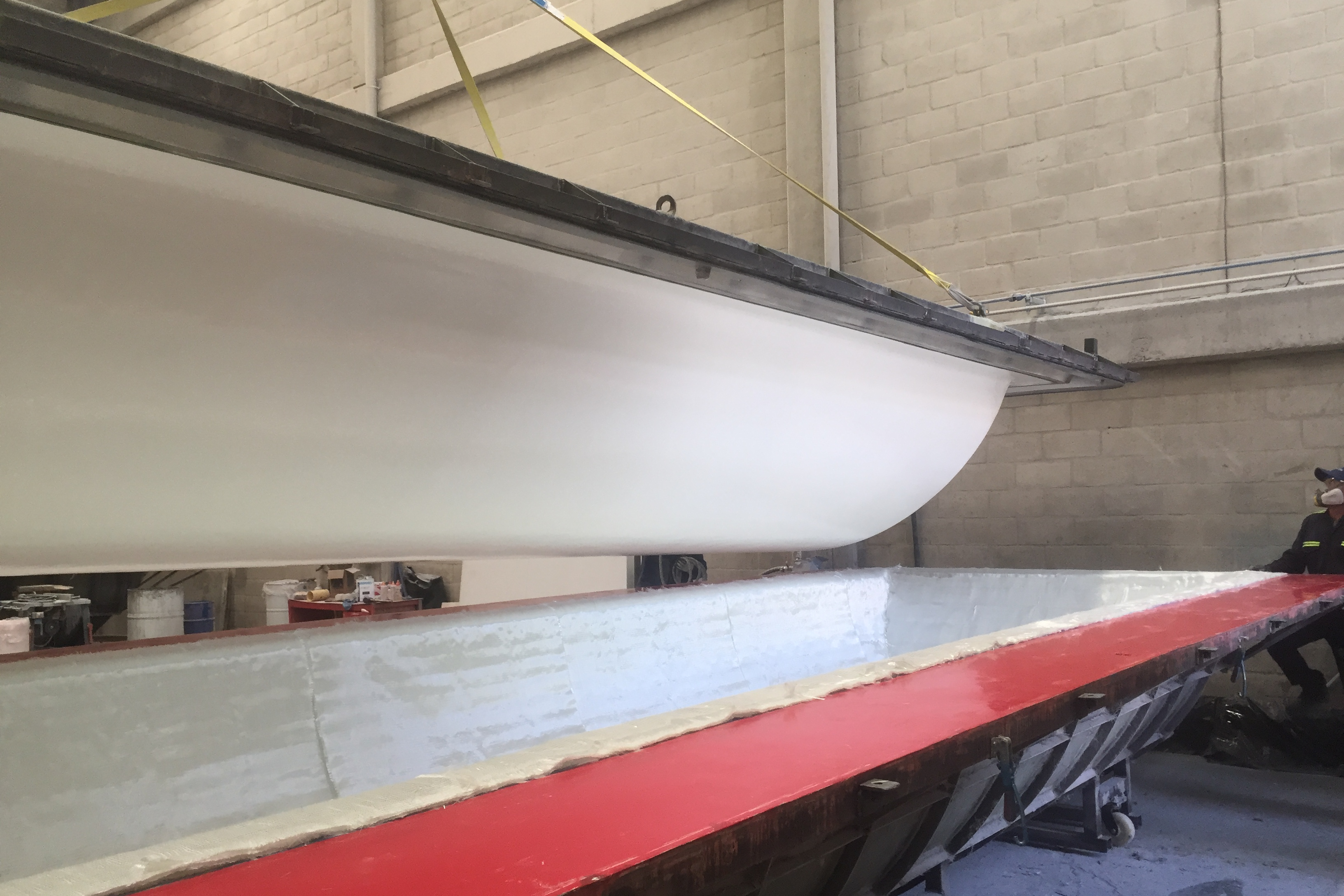
Vergara dice que el gran tamaño de las cubiertas, combinado con los estrictos requisitos de peso y dimensión, planteó el mayor desafío para su fabricación. Determinar la ubicación del puerto de inyección y administrar el tiempo de inyección requirió mucho ensayo y error y consultas con expertos técnicos. Sin embargo, Vergara dice que, finalmente, Soling se decidió por un proceso de fabricación que demostró ser altamente repetible y confiable.
“El mayor desafío fue el peso de los elementos que íbamos a instalar, porque no podíamos exceder la capacidad de carga de la estructura existente”, dice Vergara. “Esto requería que todas las piezas tuvieran las mismas características, tanto en geometría como en peso. La única forma de garantizar estas condiciones era utilizar un proceso que garantizara la repetibilidad ”.
Las cubiertas terminadas se enviaron a los 418 kilómetros (260 millas) desde las instalaciones de Soling cerca de Medellín al sitio de trabajo de Casablanca en Bogotá y luego se instalaron mediante una grúa, se bajaron sobre la estructura de soporte y los trabajadores las colocaron de pie sobre las vigas sobre las que se apoyarían las cubiertas. Aunque las cubiertas no están sujetas mecánicamente a las estructuras de soporte, Vergara dice que tampoco están diseñadas para ser movidas o removidas a menos que “haya ocurrido algo muy serio”.
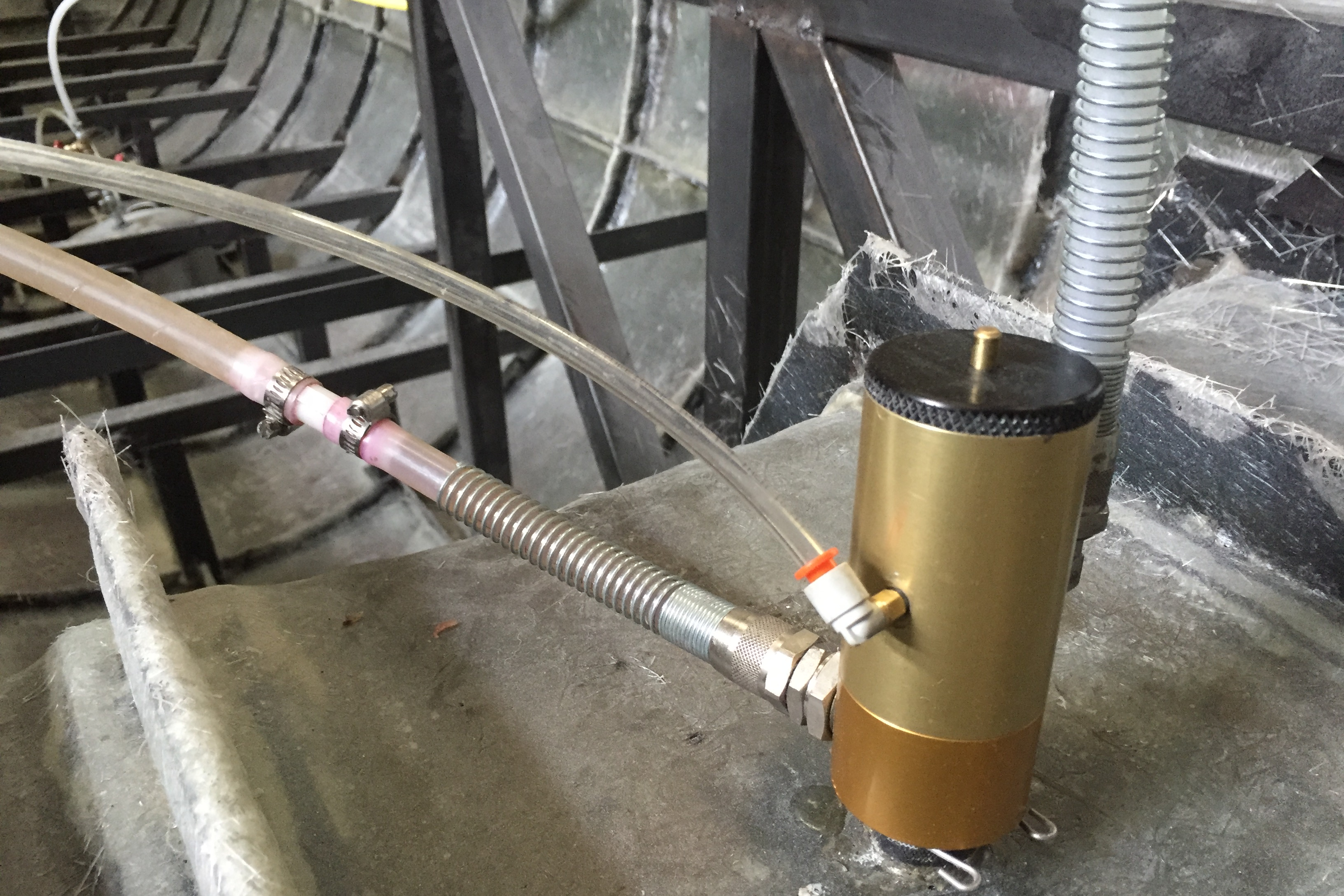
Soling comenzó el trabajo de diseño en las cubiertas a principios de 2019 y comenzó la fabricación de las primeras cubiertas en 2020. La pandemia de coronavirus y los desafíos mecánicos ocasionales hicieron que la fabricación se detuviera y comenzara, pero Vergara dice que Soling completó la producción de las 840 cubiertas en un período de 7 a 7 años. 8 meses, terminando a fines de 2020. Se espera que las nuevas cubiertas duren mucho más y requieran mucho menos mantenimiento que las que reemplazaron.
El proyecto de Casablanca, dice Vergara, ha demostrado las capacidades de Soling como fabricante de grandes estructuras compuestas de alta calidad y alto rendimiento y ha abierto las puertas a otras oportunidades. “Este proyecto fue un desafío en el que tuvimos que romper paradigmas que decían que piezas de esta magnitud no se podían fabricar con este método de fabricación, y aun así lo hicimos”, dice. “Para el futuro de Soling, algo está muy claro:no hay proyecto que no seamos capaces de hacer”.
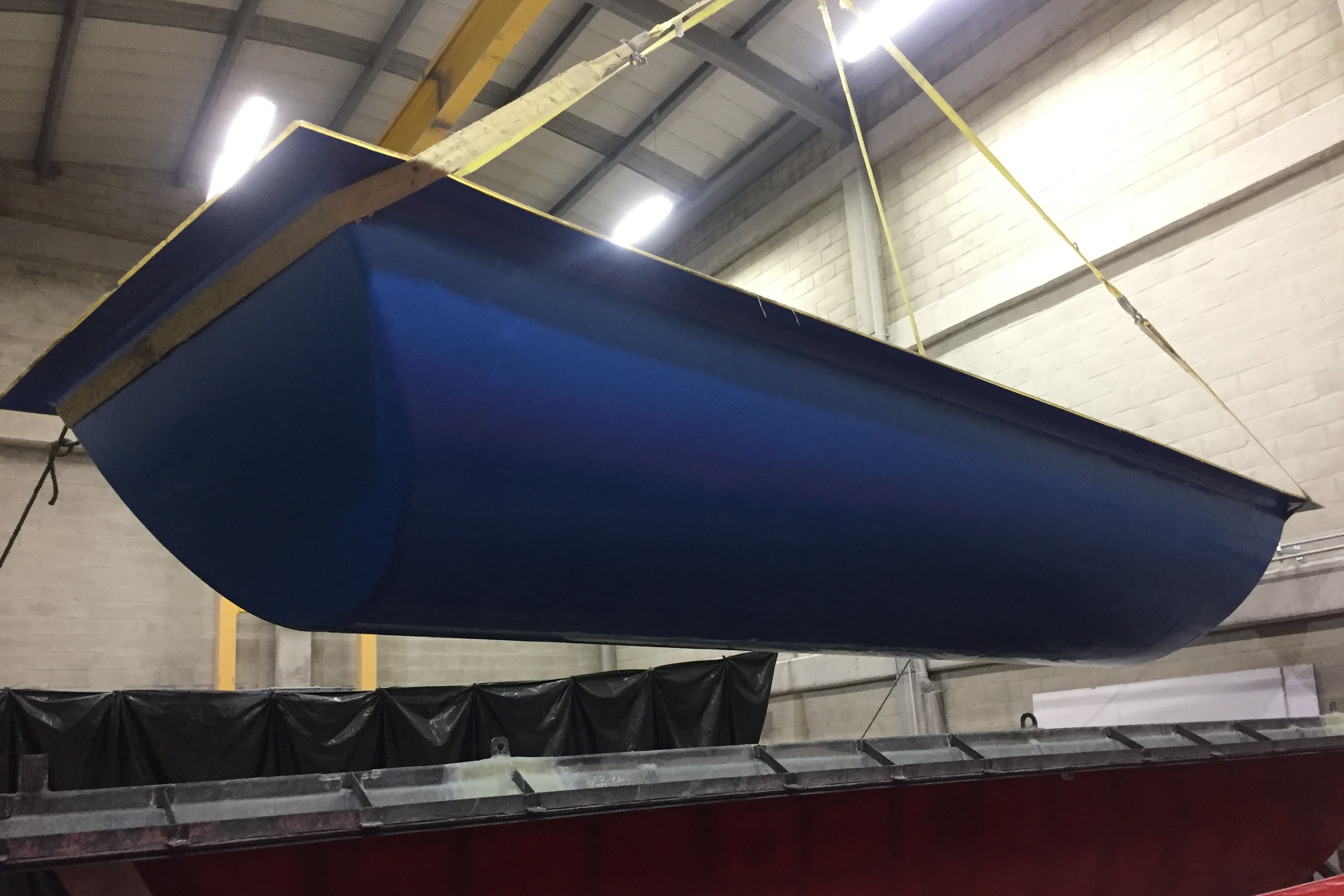
Resina