Los kits fáciles de usar permiten la reparación dentro del campo de estructuras compuestas
Los puentes desplegables modulares son un activo clave en las operaciones tácticas militares y la logística, así como para restaurar la infraestructura de transporte durante desastres naturales. Se está investigando la construcción de materiales compuestos para reducir el peso de dichos puentes, lo que a su vez reduce la carga sobre los vehículos de transporte y los mecanismos de lanzamiento y recuperación. Los materiales compuestos también ofrecen el potencial de aumentar la capacidad de carga y prolongar la vida útil en comparación con los puentes metálicos.
El puente compuesto modular avanzado (AMCB) es un ejemplo, diseñado y construido con laminados epoxi reforzados con fibra de carbono (Fig.1) por Seemann Composites LLC (Gulfport, Miss., EE. UU.) Y Materials Sciences LLC (Horsham, Penn., EE. UU.) ). Sin embargo, la capacidad de reparar tales estructuras en el campo ha sido un problema que dificulta la adopción de materiales compuestos.
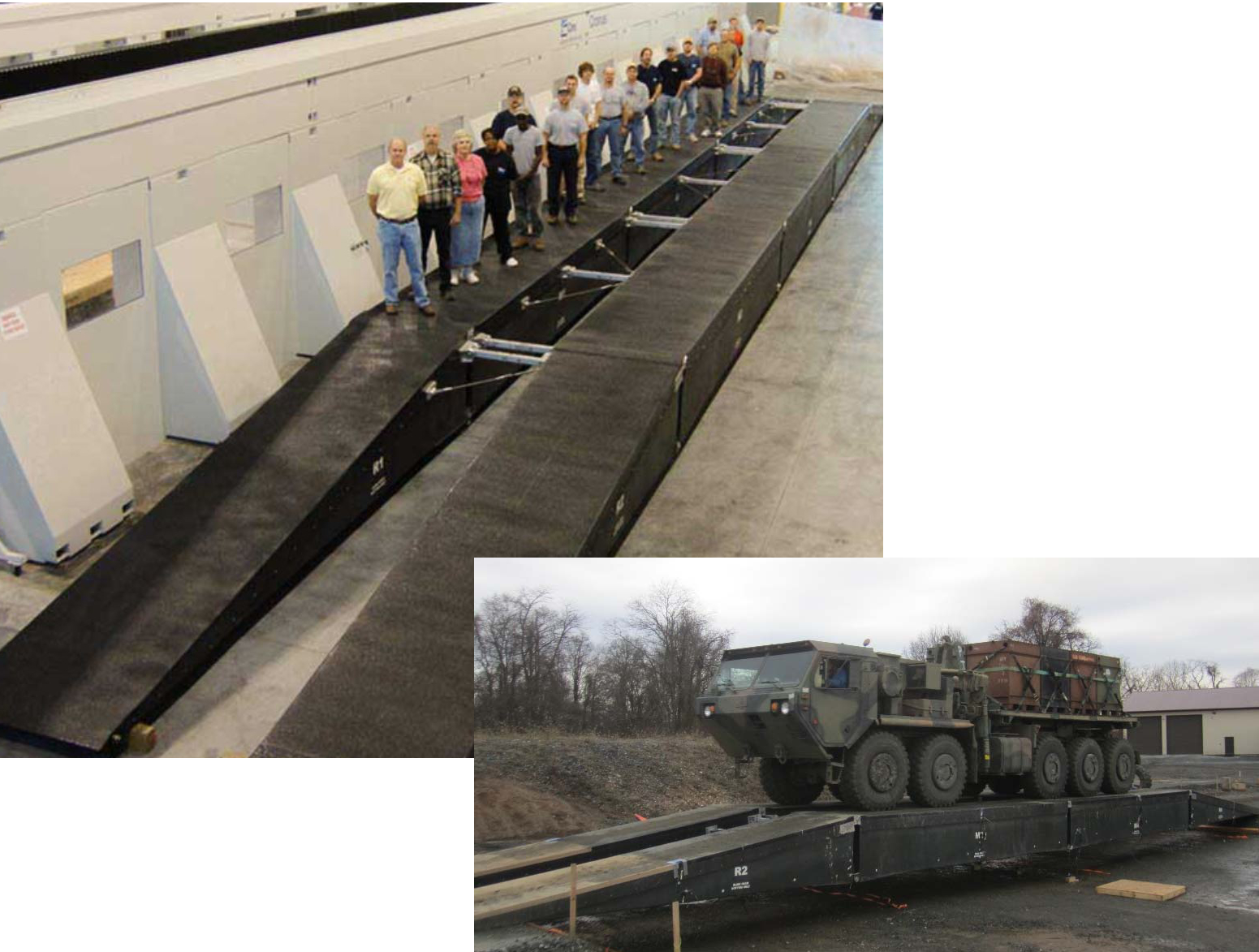
En 2016, Custom Technologies LLC (Millersville, Maryland, EE. UU.) Recibió una subvención de Fase I de Investigación en Innovación para Pequeñas Empresas (SBIR) financiada por el Ejército de EE. UU. Para desarrollar un método de reparación que los soldados puedan realizar con éxito en el campo. Con base en este método, en 2018 se otorgó una subvención SBIR de la Fase II para demostrar nuevos materiales y equipos que funcionan con baterías que podrían restaurar el 90% o más de la resistencia original de la estructura, incluso cuando la reparación del parche la realiza un novato sin capacitación previa. . La viabilidad de la tecnología se estableció mediante la realización de una serie de tareas analíticas, de selección de materiales, fabricación de muestras de prueba y pruebas mecánicas, así como reparaciones a pequeña y gran escala.
Desde cubiertas de barcos agrietadas hasta cubiertas de puentes
El investigador principal de ambas fases SBIR fue Michael Bergen, fundador y presidente de Custom Technologies LLC. Bergen se retiró del Centro de Guerra de Superficie Naval (NSWC) Carderock con una permanencia de 27 años en el Departamento de Estructuras y Materiales, donde dirigió el desarrollo y la aplicación de tecnologías compuestas para la flota de la Armada de los EE. UU. El Dr. Roger Crane se unió a Custom Technologies en 2015 después de retirarse de la Marina de los EE. UU. En 2011 con 32 años de servicio. Su experiencia en compuestos incluye publicaciones técnicas y patentes que cubren temas como nuevos materiales compuestos, fabricación de prototipos, métodos de unión, compuestos multifuncionales, monitoreo de la salud estructural y reparación de compuestos.
Estos dos expertos ya habían desarrollado un proceso único que usaba compuestos para reparar grietas en superestructuras de aluminio 5456 en el crucero de misiles guiados USS Ticonderoga CG-47. “Ese proceso se desarrolló para reducir el crecimiento de grietas y servir como una alternativa asequible al reemplazo de la placa de la plataforma de entre 2 y 4 millones de dólares”, dice Bergen. “Por lo tanto, habíamos demostrado que sabíamos cómo hacer reparaciones fuera del laboratorio y en un entorno de servicio real. Pero el desafío fue que los métodos actuales para los activos militares no tienen mucho éxito. Las opciones son una reparación de duplicador adherido [esencialmente pegando una placa en la parte superior del área dañada] o retirar el activo del servicio para reparaciones de nivel de depósito (nivel D). Hay tantos activos a un lado porque se requiere una reparación de nivel D ".
Lo que se necesita, continúa, “es un método que pueda ser ejecutado por un soldado sin experiencia en composites, utilizando solo un kit y un manual de reparación. Nuestro objetivo era facilitar el proceso:leer el manual, evaluar el daño y realizar la reparación. No queríamos ninguna mezcla de resinas líquidas porque eso requiere una medición precisa para asegurar un curado completo. También necesitábamos un sistema sin residuos HAZMAT que manejar después de que se completara la reparación. Y tenía que estar empaquetado como kits que las redes ya instaladas pudieran implementar ”.
Nuevos materiales de parche adheridos
Una solución que Custom Technologies ha demostrado con éxito es un kit portátil que permite un parche compuesto adherido, adaptado al tamaño del daño, hasta un máximo de 12 pulgadas cuadradas, utilizando un adhesivo epoxi endurecido. Las demostraciones se completaron en materiales compuestos representativos de la plataforma AMCB de 3 pulgadas de espesor, que presenta un núcleo de balsa de 3 pulgadas de espesor (15 libras por pie cúbico de densidad) con caretas que comprenden dos capas de Vectorply Corp. (Phenix City, Ala., EE. UU.) Tejido cosido biaxial de carbono C-LT 1100 0 ° / 90 °, una capa de fibra de carbono C-TLX 1900 triaxial 0 ° / + 45 ° / -45 ° y dos capas más de C-LT 1100 para un total de cinco capas. "Decidimos que el kit usaría parches prefabricados en una disposición cuasi-isotrópica de multiaxiales similares para que la orientación de la tela no fuera un problema", dice Crane.
El siguiente tema fue la matriz de resina para reparaciones de laminado. Para evitar mezclar resinas líquidas, el parche usaría preimpregnados. “Sin embargo, el desafío para estos es el almacenamiento”, explica Bergen. Para desarrollar una solución de parche almacenable, Custom Technologies se asoció con Sunrez Corp. (El Cajon, California, EE. UU.) Para desarrollar un preimpregnado de fibra de vidrio / éster de vinilo que cura en seis minutos usando luz ultravioleta (UV). También trabajó con Gougeon Brothers (Bay City, Michigan, EE. UU.), Que sugirió usar una nueva película de resina epoxi flexible.
Las primeras investigaciones ya habían demostrado que el epoxi era la resina más adecuada para un preimpregnado de fibra de carbono:el éster de vinilo curado con UV funciona muy bien con fibras de vidrio translúcidas, pero no cura debajo de las fibras de carbono que bloquean la luz. Basado en la nueva película de Gougeon Brothers, el preimpregnado epoxi final demostró un curado de una hora a 210 ° F / 99 ° C con una larga vida útil a temperatura ambiente; no se requiere almacenamiento a baja temperatura. La resina también curará a temperaturas más altas, dice Bergen, por ejemplo a 350 ° F / 177 ° C si una temperatura de transición vítrea más alta (T g ) se requiere. Ambos preimpregnados se suministran en el kit de reparación portátil como capas de parches preimpregnados prefabricados sellados en sobres de película plástica.
Debido a que los kits de reparación pueden estar almacenados durante un tiempo prolongado, se solicitó a Custom Technologies que realizara un estudio de vida útil. “Compramos cuatro cajas de plástico duro, típicas del tipo que usan los militares para el envío de equipos, y colocamos muestras de adhesivos epoxi y preimpregnados de éster de vinilo en cada una”, dice Bergen. Luego, las cajas se colocaron en cuatro lugares diferentes para realizar las pruebas:en el techo de las instalaciones de Gougeon Brothers en Michigan, en el techo de un aeropuerto en Maryland, al aire libre en una instalación en Yucca Valley (desierto de California) y en un laboratorio de pruebas de corrosión al aire libre. en el sur de Florida. Todos los casos tenían registradores de datos, señala Bergen, “y extraíamos muestras de datos y materiales cada tres meses para su evaluación. Las cajas de Florida y California registraron una temperatura máxima de 140 ° F, lo cual es un verdadero desafío para la mayoría de las resinas de reparación ”. Además, Gougeon Brothers probó internamente la resina epoxi pura recién desarrollada. “Las muestras mantenidas durante meses en un horno a 120 ° F comenzaron a polimerizar”, dice Bergen. "Sin embargo, para las muestras correspondientes mantenidas a 110 ° F, la química de la resina avanzó solo una pequeña cantidad".
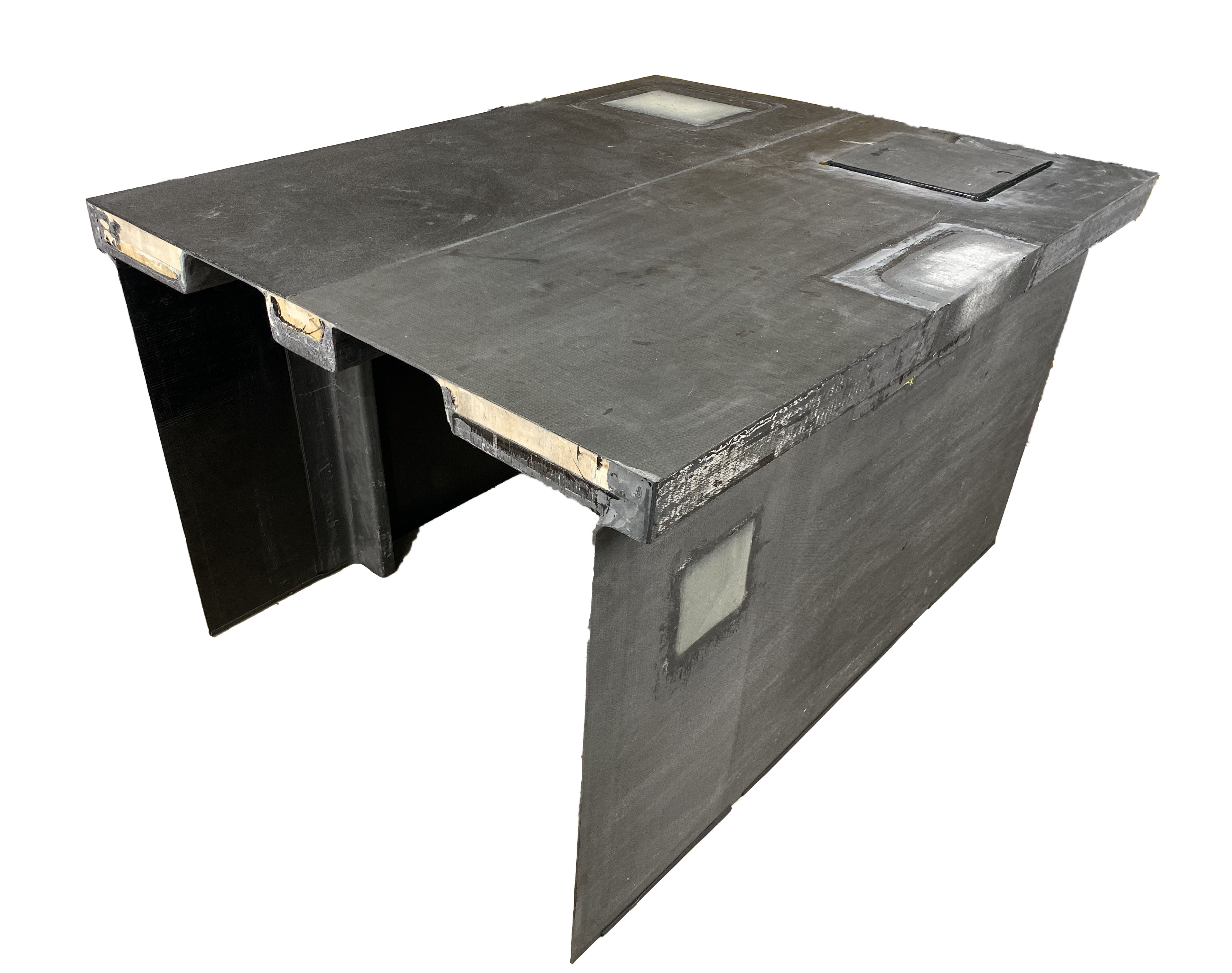
Prueba de reparación
Para demostrar la tecnología de reparación, se tuvieron que fabricar, dañar y luego reparar laminados representativos. “En el proyecto de la Fase I, inicialmente trabajamos con vigas a pequeña escala de 4 x 48 pulgadas y pruebas de flexión de cuatro puntos para evaluar la viabilidad de nuestro proceso de reparación”, dice Crane. “Luego hicimos la transición a paneles de 12 x 48 pulgadas en el proyecto de la Fase II, aplicando carga para crear un estado de tensión biaxial a la falla, y luego evaluamos el desempeño de la reparación. En el proyecto de la Fase II, también completamos las reparaciones de un modelo del AMCB que habíamos construido ”.
Los paneles de prueba utilizados para demostrar el rendimiento de la reparación se fabricaron utilizando el mismo pedigrí en laminado y núcleo que el AMCB construido por Seemann Composites, dice Bergen, “pero reducimos el grosor de la hoja frontal de 0,375 pulgadas a 0,175 pulgadas, según los ejes paralelos teorema. Este enfoque, junto con elementos adicionales de la teoría de vigas y la teoría clásica del laminado [CLT], se utilizó para relacionar el momento de inercia y la rigidez efectiva del AMCB a gran escala con artículos demostrativos de menor tamaño más manejables y rentables. Luego utilizamos modelos de análisis de elementos finitos [FEA] desarrollados por XCraft Inc. (Boston, Mass., EE. UU.) Para refinar el diseño de las reparaciones estructurales ". Las telas de fibra de carbono para los paneles de prueba y el modelo AMCB se compraron a Vectorply y el núcleo de balsa fue suministrado por Core Composites (Bristol, R.I., EE. UU.).
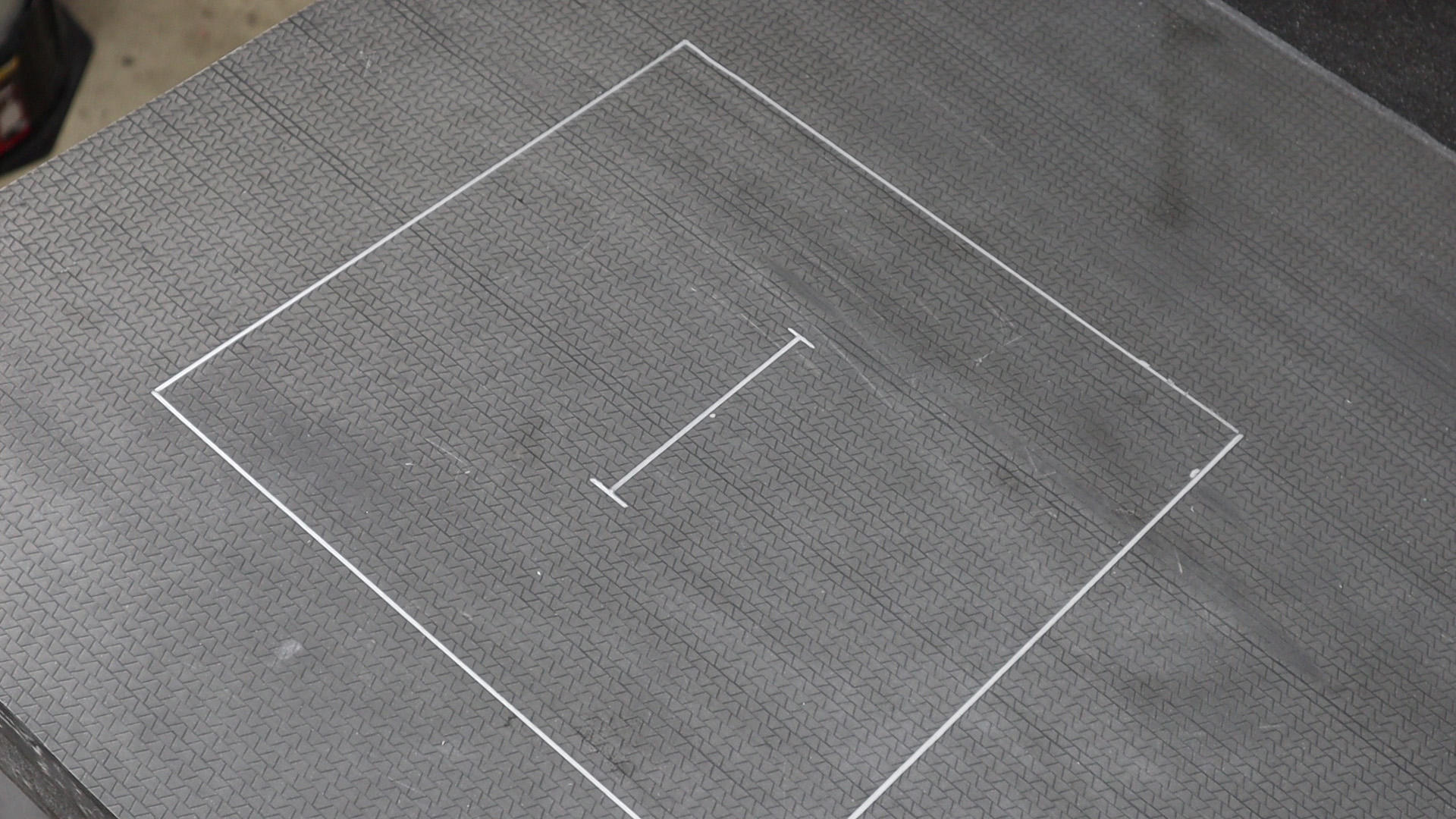
Paso 1. Este panel de prueba muestra el diámetro del orificio de 3 pulgadas para simular el daño marcado en el centro, así como el perímetro de reparación. Crédito de la foto de todos los pasos:Custom Technologies LLC.
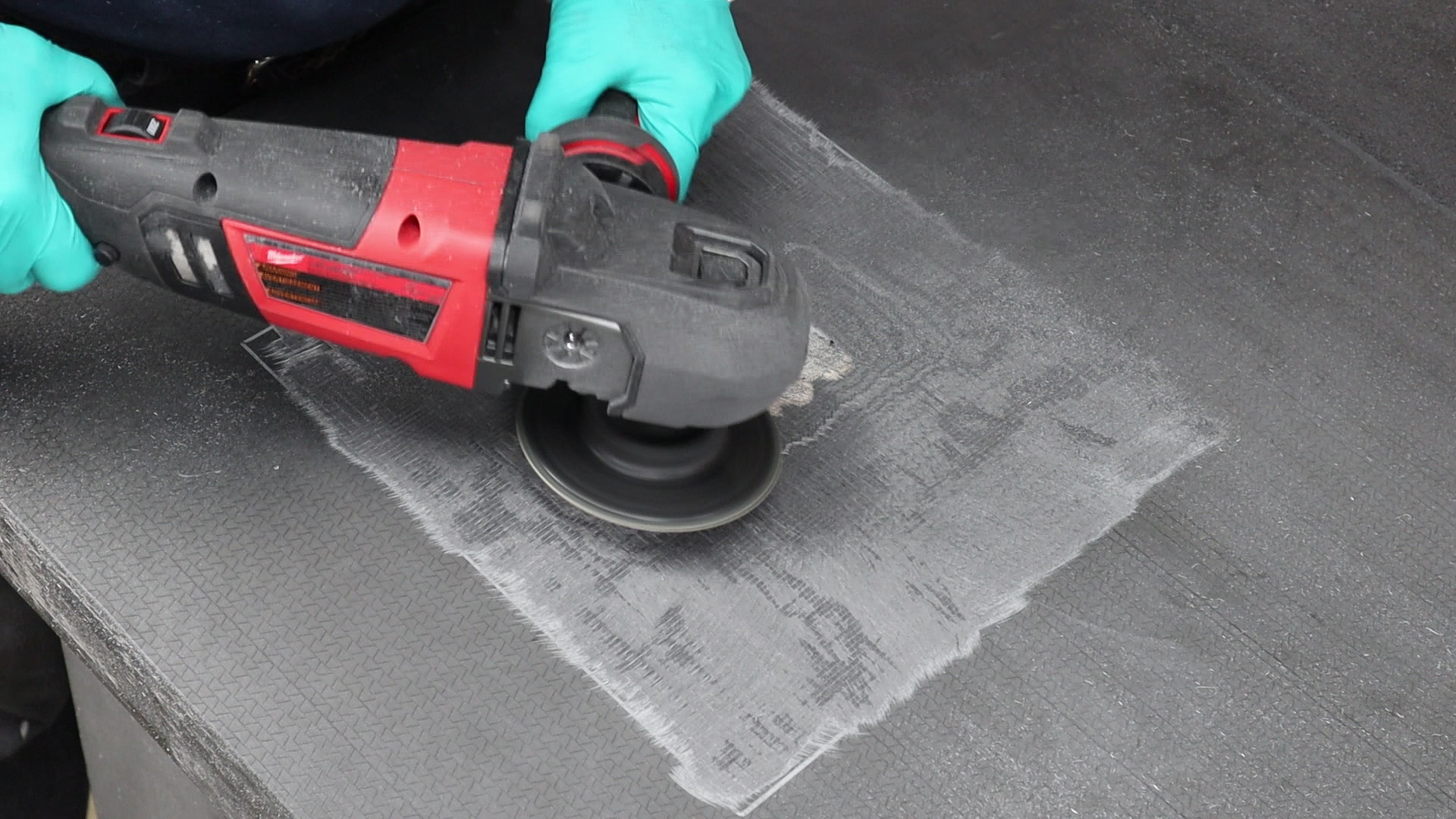
Paso 2. Se usa una amoladora de mano a batería para quitar el material dañado y un bisel de 12:1 para recibir el parche de reparación.
“Queríamos simular un mayor grado de daño en los paneles de prueba de lo que probablemente se vea en las cubiertas de los puentes en el campo”, explica Bergen. “Entonces, nuestro enfoque fue usar una sierra de corona para hacer un agujero de 3 pulgadas de diámetro. Luego sacamos el tapón del material dañado y realizamos una bufanda 12:1 usando una amoladora neumática de mano ”.
Para la reparación de fibra de carbono / epoxi, explica Crane, una vez que se quitó el material de la hoja frontal "dañado" y se aplicó la bufanda adecuada, el preimpregnado se cortó a lo ancho y largo para que coincidiera con la conicidad del área dañada. “Para nuestros paneles de prueba, esto requirió cuatro capas de preimpregnado que hicieron que el material de reparación estuviera nivelado con la parte superior de la hoja frontal de carbono original en buen estado. Después de esto, se centraron tres capas superpuestas del preimpregnado de carbono / epoxi sobre esta sección de reparación. Cada capa sucesiva se extendió 1 pulgada en todos los lados de la capa de abajo, lo que proporcionó una transferencia de carga gradual desde el "buen" material circundante al área reparada ". El tiempo total para realizar esta reparación, incluida la preparación del área de reparación, el corte y la colocación del material de reparación y la aplicación del procedimiento de curado, fue de aproximadamente 2,5 horas.
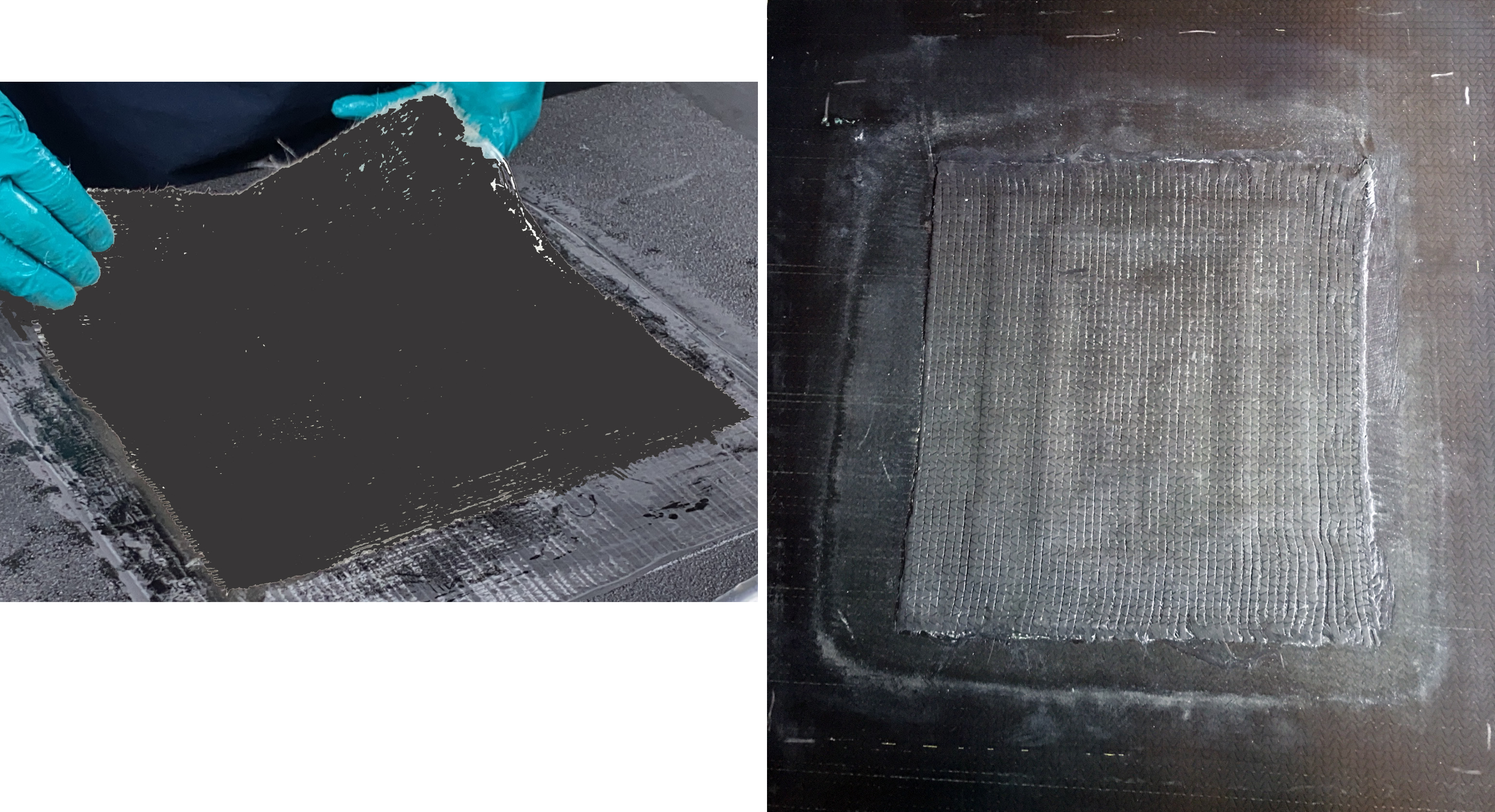
Aunque la reparación de carbono / epoxi es simple y rápida, el equipo reconoció la necesidad de una solución aún más conveniente que pudiera restaurar el rendimiento. Esto llevó a la exploración del preimpregnado curado con ultravioleta (UV). “El interés en la resina de éster de vinilo Sunrez se basó en la experiencia anterior de la Marina con Mark Livesay, quien fundó la empresa”, explica Bergen. “Comenzamos proporcionando a Sunrez un tejido de vidrio cuasi-isotrópico para preimpregnado con su éster de vinilo y evaluamos el perfil de curado en diversas condiciones. Además, sabiendo que la resina de éster de vinilo no proporciona propiedades de unión secundaria tan adecuadas como lo hace el epoxi, hubo un esfuerzo adicional para evaluar varios agentes de acoplamiento de líneas de unión y calificar uno para esta aplicación ”.
Otro problema fue que la fibra de vidrio no proporciona las mismas propiedades mecánicas que la fibra de carbono. “Esto se solucionó mediante el uso de una capa adicional de éster de vidrio / vinilo en comparación con el parche de carbono / epoxi”, dice Crane. "La razón por la que solo se necesitaba una capa adicional era que el material de vidrio era una tela más pesada". Esto dio como resultado un parche adecuado que se podía aplicar y luego curar en seis minutos incluso en temperaturas muy frías / heladas en el interior del campo sin necesidad de proporcionar calor. Crane señala que esta reparación podría completarse en una hora.
Ambos sistemas de parches fueron demostrados y probados. Para cada reparación, se marcó el área a dañar (paso 1), se creó con la sierra de perforación y luego se retiró con una amoladora manual a batería (paso 2). A continuación, el área de reparación se rebajó a un ahusamiento de 12:1. La superficie escarchada se limpió con toallitas con alcohol (paso 3). A continuación, el parche de reparación se cortó a la medida, se colocó sobre la superficie limpia (paso 4) y se consolidó con un rodillo para eliminar las burbujas de aire. Para el preimpregnado de éster de vinilo curado por UV / fibra de vidrio, se colocó luego una capa desprendible sobre el área de reparación y el parche se curó usando una luz ultravioleta inalámbrica durante seis minutos (paso 5). Para el preimpregnado de fibra de carbono / epoxi, el área de reparación se embolsó al vacío y se curó utilizando un adhesivo caliente preprogramado de un botón que funciona con pilas durante una hora a 210 ° F / 99 ° C.
Pasos de reparación
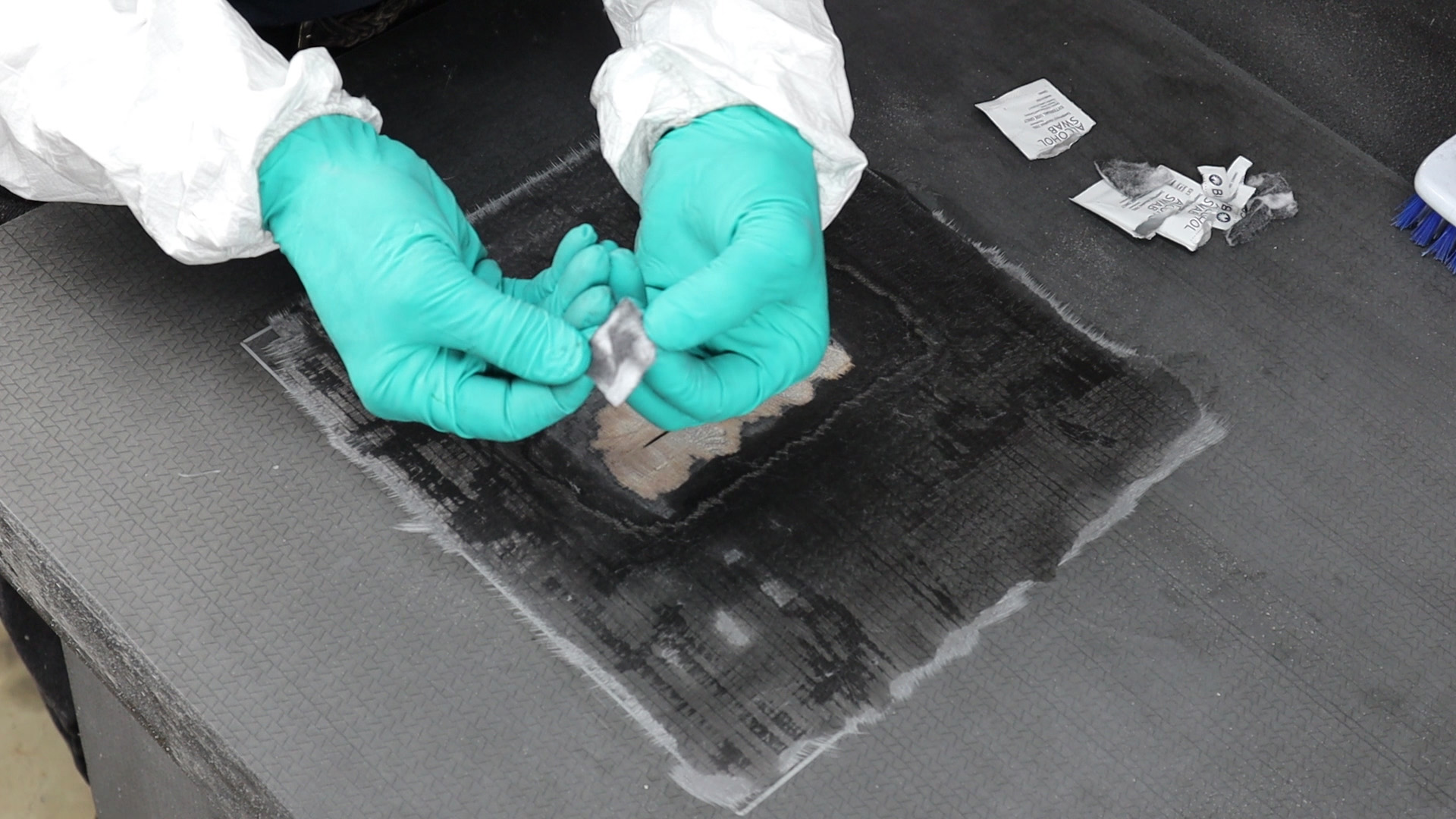
Paso 3. El área de reparación preparada se limpia luego con una toallita con solvente usando toallitas con alcohol desechables.
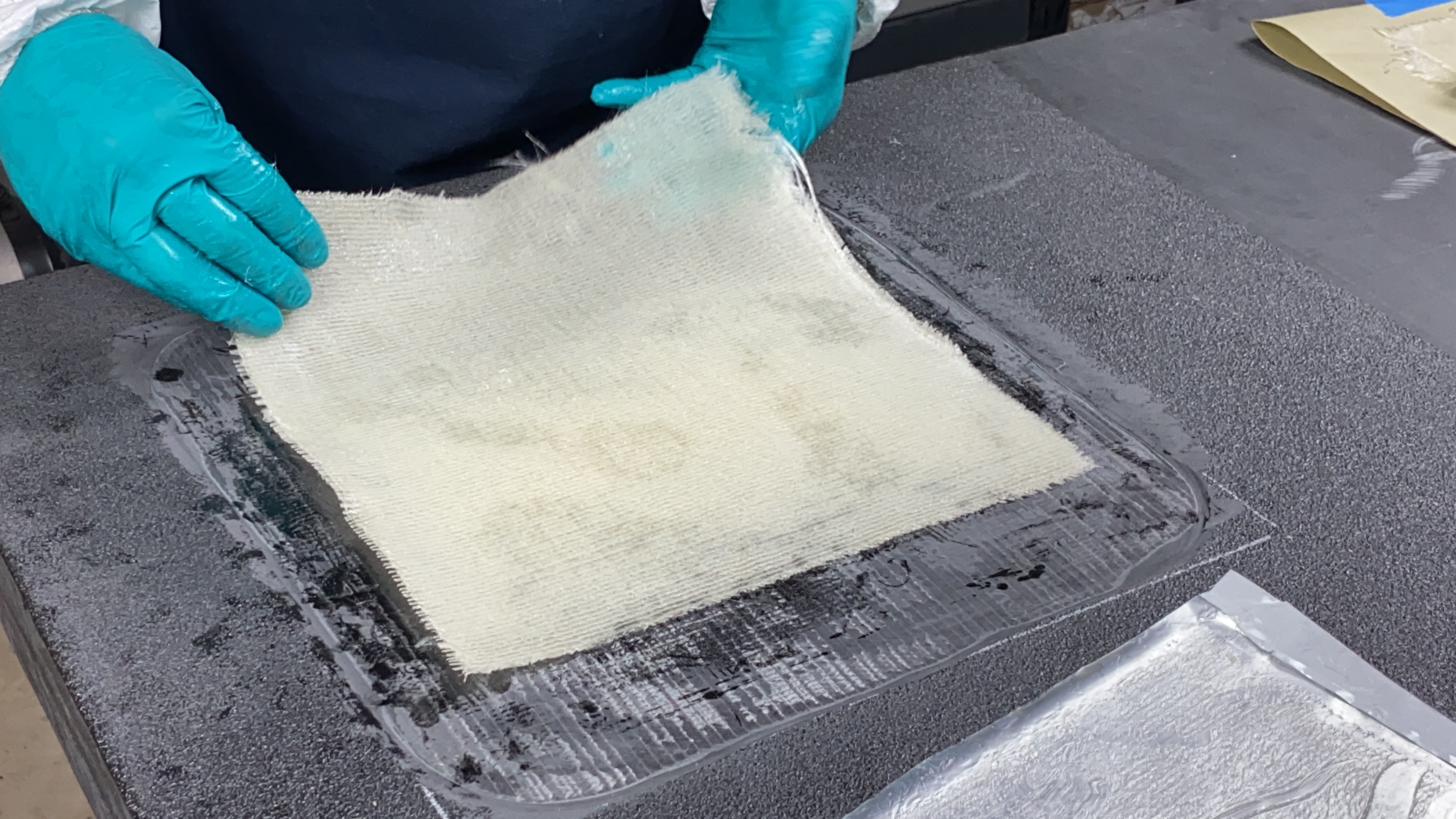
Paso 4. El parche de reparación de fibra de vidrio / éster de vinilo se corta a la medida y se coloca en el área de reparación.
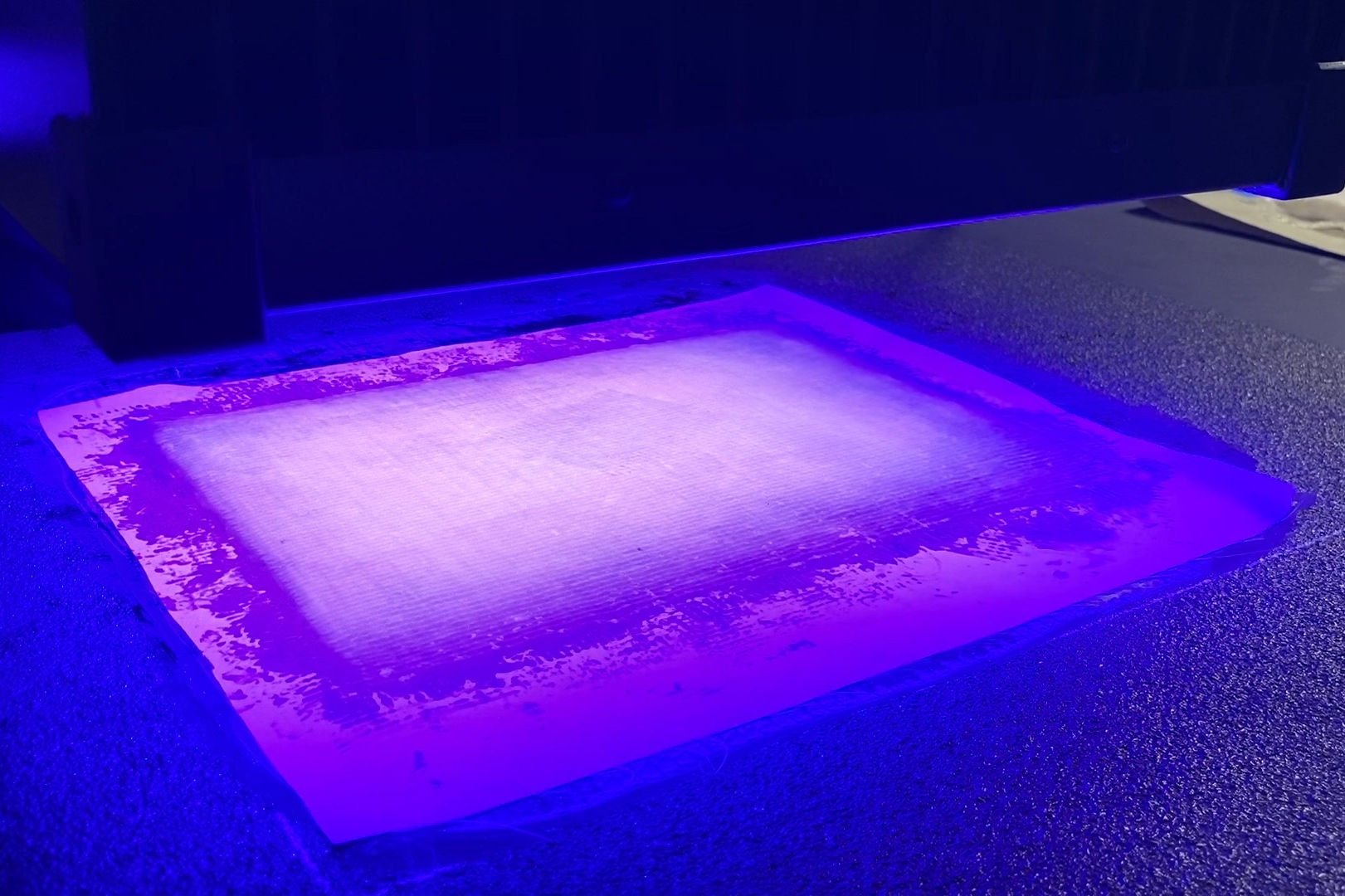
Paso 5. Después de colocar una capa protectora sobre el área de reparación, la reparación del parche se cura con una luz ultravioleta inalámbrica durante seis minutos.
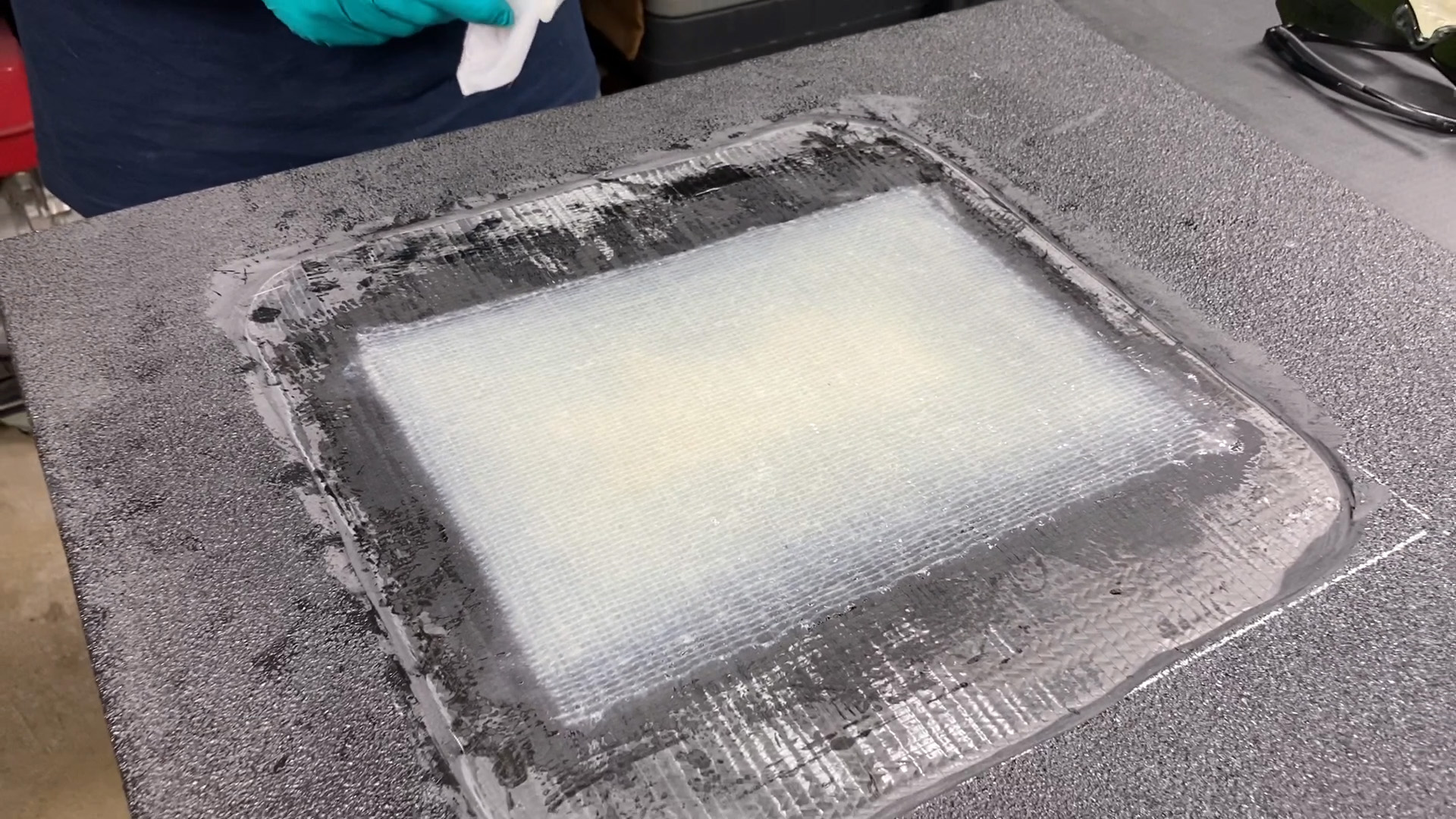
Paso 6. Reparación completa del parche preimpregnado de éster de vinilo / fibra de vidrio curado con UV.
Anterior Siguiente"Luego, realizamos pruebas para evaluar la unión adhesiva del parche y la capacidad de restaurar la capacidad de carga de la estructura", dice Bergen. “En la Fase 1, se nos pidió que demostráramos facilidad de aplicación y capacidad para restaurar al menos el 75% de la resistencia. Esto se logró en las vigas de núcleo de balsa / fibra de carbono / epoxi de 4 x 48 pulgadas en flexión de cuatro puntos después de la reparación del daño simulado. El proyecto de la Fase 2 utilizó paneles de 12 x 48 pulgadas y tenía que mostrar un requisito de resistencia superior al 90% bajo cargas de tensión complejas. Cumplimos con todos estos requisitos y luego filmamos los métodos de reparación en el modelo AMCB para proporcionar una referencia visual de cómo usar las técnicas y el equipo dentro del campo ".
Éxito de principiantes, futuras aplicaciones
Un aspecto clave del proyecto fue demostrar que un novato podría completar fácilmente la reparación. Para ello, Bergen tuvo una idea:“Le había prometido una demostración a nuestros dos puntos técnicos de contacto en el Ejército:el Dr. Bernard Sia y Ashley Genna. En la revisión final del proyecto de la Fase I, le pedí a Ashley, que no tenía experiencia previa en reparaciones, que realizara la reparación. Utilizando los kits y el manual que le proporcionamos, aplicó el parche y completó la reparación sin ningún problema ”.
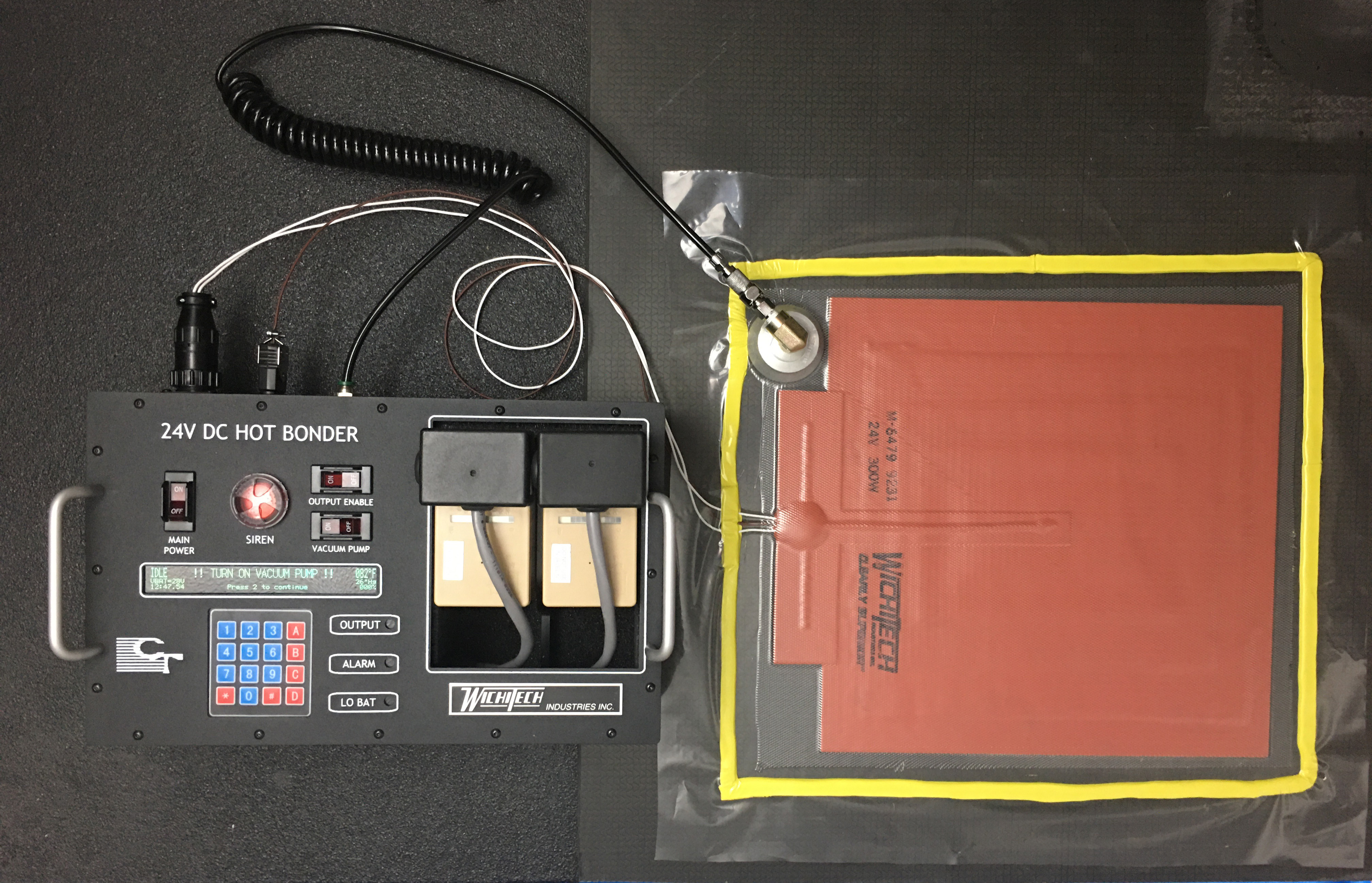
Otro desarrollo clave es el sistema de curado a batería (Fig. 2). “Con la reparación del cuadro, solo tiene energía de la batería”, señala Bergen. "Todo el equipo de proceso en nuestro kit de reparación desarrollado es inalámbrico". Esto incluye el pegador en caliente alimentado por batería que Custom Technologies desarrolló con el proveedor de pegado en caliente WichiTech Industries Inc. (Randallstown, Md., EE. UU.). "Este pegador térmico a batería está preprogramado para completar el curado, por lo que el principiante no necesita programar el ciclo de curado", dice Crane. "Simplemente presionan el botón y completa la rampa adecuada y se sumerge". Las baterías que se utilizan actualmente duran un año antes de que sea necesario recargarlas.
Con el proyecto de la Fase II ya completado, Custom Technologies está preparando una propuesta de mejora de seguimiento y recopilando cartas de interés y apoyo. “Nuestro objetivo es convertir esta tecnología en TRL 8 y llevarla al campo”, dice Bergen. "También vemos potencial para aplicaciones no militares".
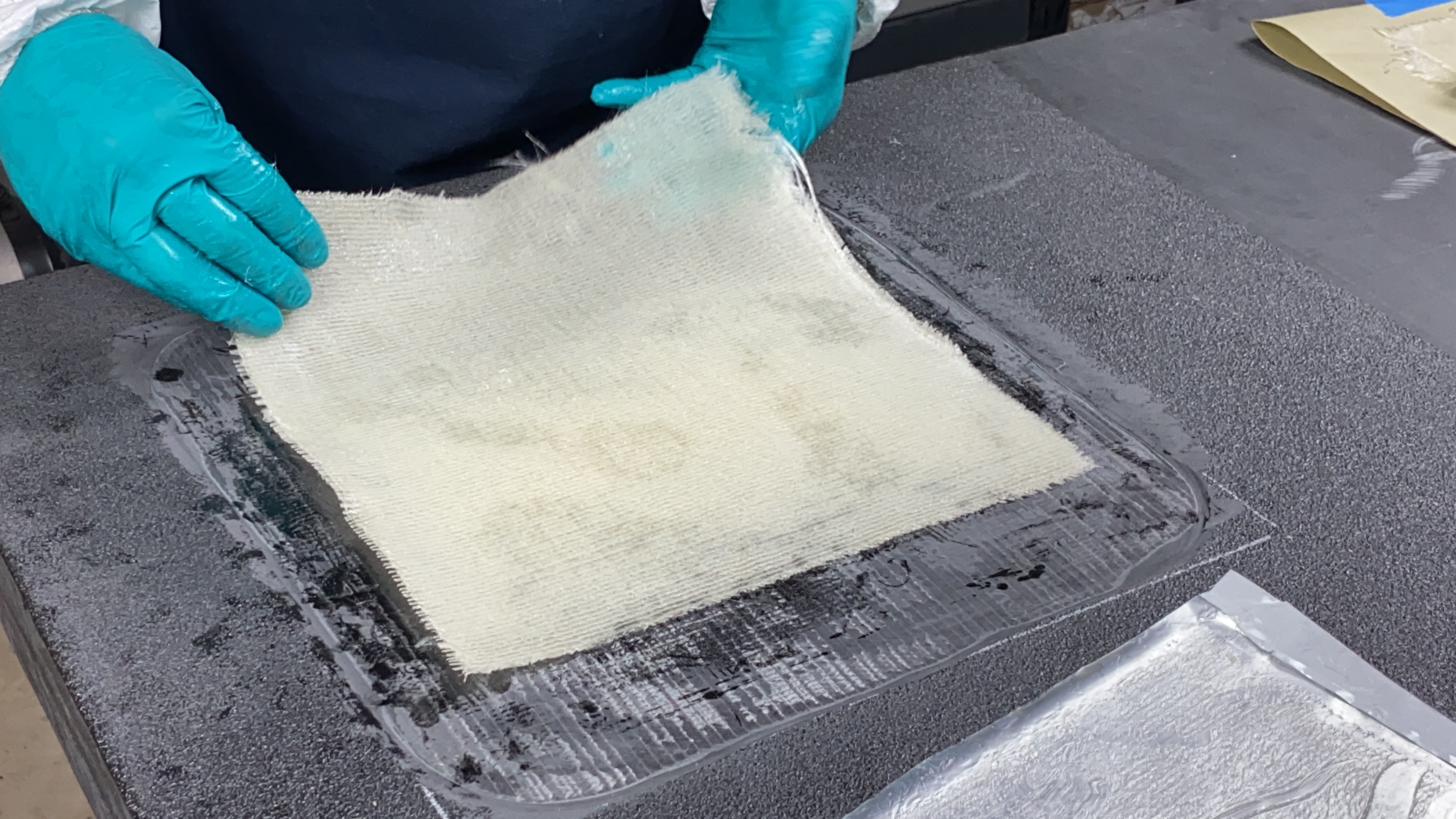
Resina
- Las 3 aplicaciones de ingeniería de compuestos termoestables más comunes
- Fabricación de materiales compuestos:Fabricación de materiales compuestos
- Las estructuras termoplásticas son el foco de la presencia de Engel en China Composites Expo
- Desarrollo de estructuras de isogrid compuestas utilizando tecnología innovadora de deposición
- Alveus comercializará el servicio compuesto de reparación de barcos Compa Repairs
- Herramientas innovadoras, la automatización permite una nueva línea de pozos de ventanas compuestas
- La investigación de AFRL avanza en los compuestos CF / epoxi imprimibles en 3D
- Hexcel se asocia con Lavoisier Composites, Arkema
- AMRC y socio Prodrive para el avance de la fabricación de componentes compuestos reciclables
- TenCate celebra la asamblea del consorcio de compuestos termoplásticos en Brasil
- Materiales compuestos:dónde encontrarlos en NPE2018