La evolución de los compuestos aditivos
En octubre de 2020, CW informó sobre la impresión 3D de compuestos con fibra continua y proporcionó un panorama de las tecnologías que se están desarrollando, así como una clasificación de los procesos que se utilizan. Este último fue aportado por Alexander Matschinski, investigador asociado y experto en Fabricación Aditiva en TU Munich y Presidente de Carbon Composites (Lehrstuhl für Carbon Composites, o LCC, Munich, Alemania).
CW nuevamente se está asociando con LCC, pero esta vez para ver el panorama más amplio de fabricación de compuestos aditivos (ACM), especialmente los procesos que se están desarrollando en la interfaz entre los composites convencionales y la fabricación aditiva (AM). “Vemos cada vez más tecnologías que se encuentran fuera de nuestras clasificaciones para la impresión 3D de fibra continua, pero en cambio combinan la fabricación automatizada de compuestos con AM y ofrecen nuevas soluciones que no eran posibles hasta ahora”, señala el investigador de LCC Thomas Wettemann.
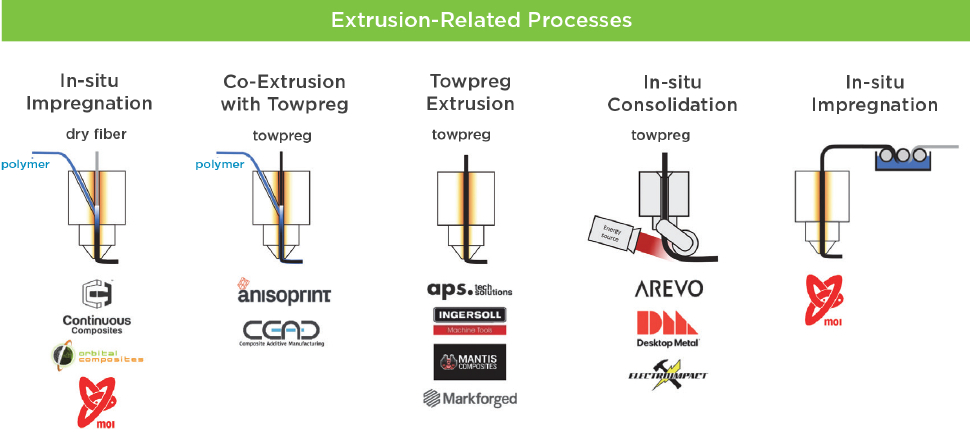
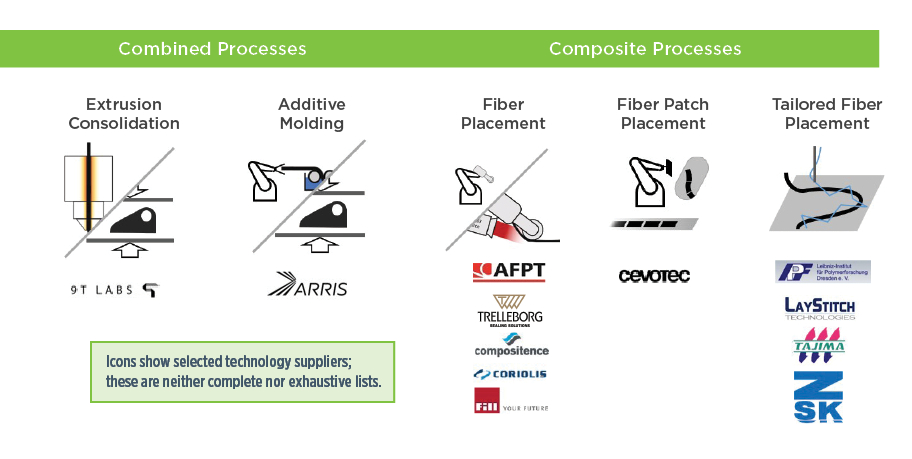
La propia LCC está difuminando las líneas entre los procesos tradicionales y la impresión 3D al combinar la colocación automatizada de fibras (AFP) y el devanado de filamentos (FW) con ACM basado en extrusión (consulte “Fabricación futura de compuestos:AFP y fabricación aditiva”). “También estamos pasando de la extrusión tradicional de termoplásticos a la impresión 3D con termoestables adaptando tecnologías que desarrollamos para el moldeo por transferencia de resina [RTM] y combinándolas con ultrasonidos ”, dice el Dr. Swen Zaremba, subdirector de LCC. Al mismo tiempo, LCC está trabajando para desarrollar estándares para ACM y mejorar sus materiales y procesos.
Tenga en cuenta que existe un panorama de ACM aún más amplio que incluye filamentos rellenos de fibra cortada extruidos mediante modelado de deposición fundida (FDM), materiales de fibra en polvo procesados mediante sinterización selectiva por láser (SLS) y piezas altamente personalizadas que utilizan rellenos con orientación magnética y procesamiento de luz digital. (DLP), este último desarrollado por Fortify (Boston, Mass., EE. UU.). De hecho, estos procesos producen piezas compuestas y abren nuevos mercados y aplicaciones, pero esta discusión se mantendrá dentro del ámbito del refuerzo continuo de fibra.
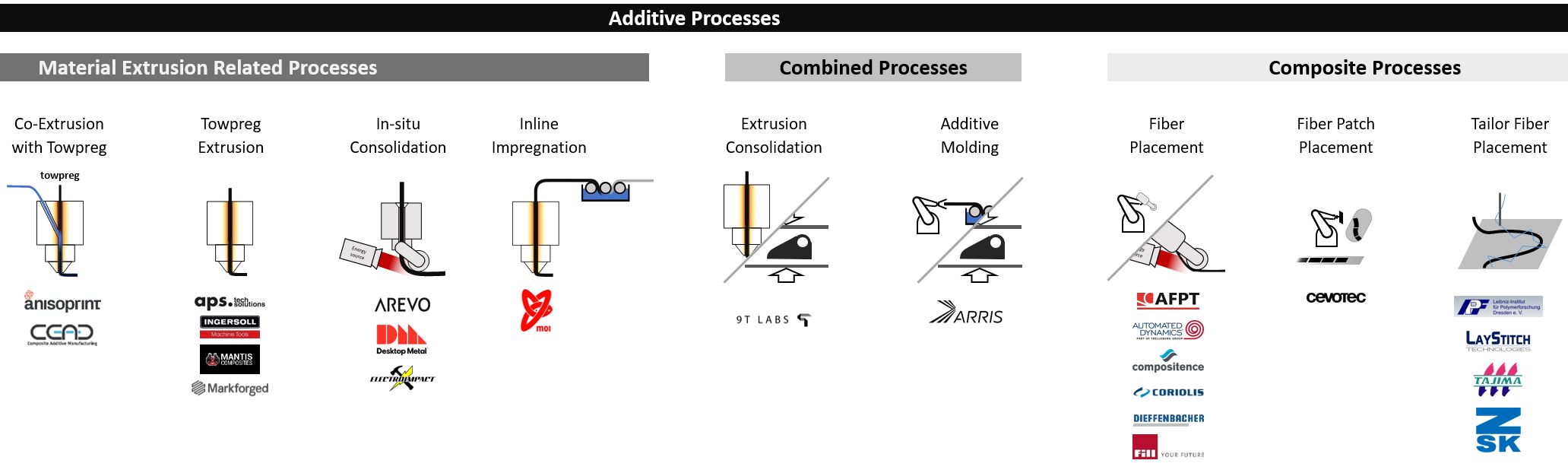
¿Qué es ACM?
“Por lo general, primero tenemos esta discusión, así como la motivación para desarrollar estas nuevas tecnologías”, dice Zaremba. Como explicó Wettemann en una presentación de SAMPE de enero de 2019, la motivación es la producción rentable más allá de la producción en masa, incluido el tamaño de un lote, que también conserva los recursos, minimiza o elimina los desechos y es amigable con el medio ambiente y el clima. “También ofrece una forma de hacer que la cadena de proceso de los compuestos sea completamente digital”, agrega. “Es el primer paso en el camino de décadas de cambio”.
Los componentes clave de la definición de ACM de LCC incluyen:
- Cadenas de proceso largas reducidas a un "procesamiento en una caja" de un solo punto
- Consolidación / polimerización global reemplazada con tratamiento de material local y tratamiento térmico recurrente
- Producción sin herramientas
“ACM concentra lo que antes eran largas cadenas de procesamiento en más o menos un solo punto, una especie de fabricación dentro de una caja”, dice Zaremba. Por lo tanto, agrega Matschinski, "estás procesando los materiales y dando a la pieza su forma dentro de esa caja y sin una herramienta de moldeo". Ambos coinciden en que la "caja" puede ser una celda ACM muy grande, por ejemplo, la celda SCRAM presentada por Electroimpact (Mukilteo, Washington, EE. UU.) En 2020. "ACM también puede usarse fuera de una sola caja", dice Zaremba, "Por ejemplo, nuestro trabajo para agregar refuerzo local y características más pequeñas a piezas AFP más grandes".
Sin embargo, señala Wettemann, "ahora vemos ejemplos de toda la cadena de proceso de compuestos contenidos en una línea o celda automatizada, pero esto no es lo que definiríamos como ACM". La celda SCRAM, por el contrario, tiene la capacidad de procesar material y dar forma sin herramientas al combinar un cabezal AFP termoplástico de consolidación in situ (ISC) con un cabezal de impresión 3D de fabricación de filamentos fundidos [FFF, otro término para FDM]. “Para nosotros, esta consolidación in-situ usando AFP fue de hecho el comienzo de ACM en LCC porque usted crea los composites curados / consolidados a medida que realiza la colocación o la colocación”, dice Zaremba.
Esto nos lleva al segundo punto clave en la definición de ACM de la LCC. “Antes, siempre tenía un paso de consolidación global y, idealmente, el mismo tratamiento de material y el mismo historial en toda la pieza, ya que se moldeó en un autoclave, horno, herramienta calentada o prensa”, explica Zaremba. "Con ACM, estamos realizando este tratamiento térmico y consolidación a nivel local mientras construimos la pieza".
Wettemann señala que ISC ofreció un punto de entrada desde la fabricación automatizada de composites al mundo de la AM, “pero esto también presenta desafíos reales para los materiales y el procesamiento porque este tratamiento local del material es también un tratamiento térmico recurrente. Tenga en cuenta que al principio, solo estábamos adaptando materiales de moldeo por inyección para la impresión 3D. Pero luego nos dimos cuenta de que no está realmente optimizado para la impresión FFF. Entonces, las empresas comenzaron a modificar materiales para sus sistemas de impresión para lidiar con el calentamiento y enfriamiento recurrente de las resinas, y también la velocidad requerida y la necesidad de adherir capas entre sí y evitar deformaciones. Esta última es también la razón por la que cada vez más empresas buscan incluir fibras continuas ”.
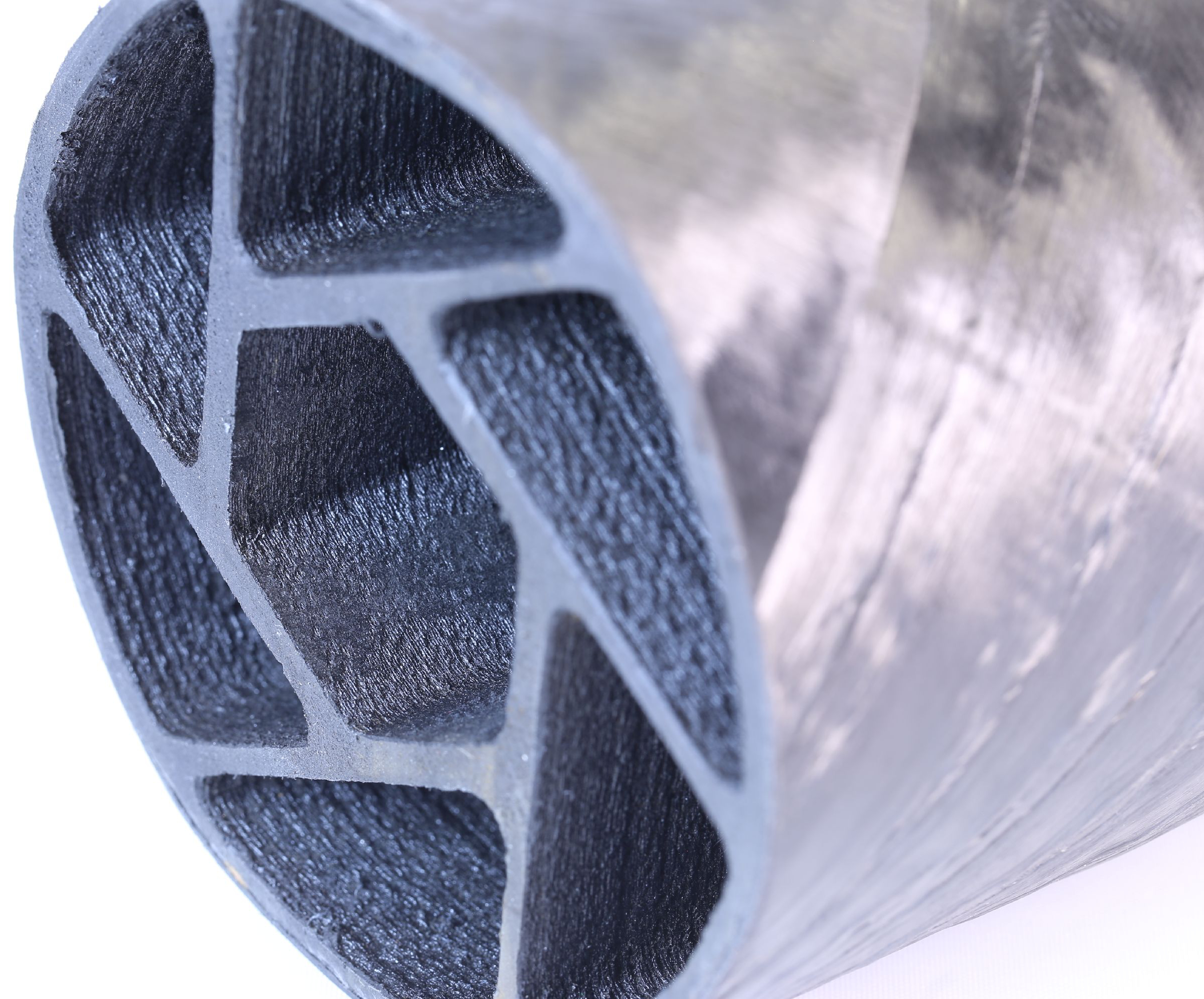
Sin embargo, la integración de fibras continuas también crea problemas. “Esa es una de las razones por las que nos atrajo ACM”, dice Zaremba. “Los procesos de impresión 3D prometieron muchos resultados, pero los resultados no brindaron el tipo de calidad que esperamos para aplicaciones estructurales o aeroespaciales, por ejemplo. Podríamos ver una brecha entre los compuestos avanzados que utilizan fibra continua y lo que pueden ofrecer las tecnologías AM. LCC tiene como objetivo unir estos mundos y realizar el potencial prometido, pero también combinar tecnologías para lograr nuevas soluciones ”.
Fusión de dos mundos
LCC ve muchas de estas nuevas soluciones, por ejemplo, el proceso de moldeo aditivo desarrollado por Arris Composites (Berkeley, California, EE. UU.) Y la celda Fusion Bonding para impresión 3D desarrollada por 9T Labs (Zurich, Suiza), ambos de alto rendimiento. procesos de volumen. “Ninguno de estos procesos da forma a la pieza final dentro del proceso aditivo, pero use un tipo de molde y un segundo paso en ese molde”, dice Matschinski. “Entonces, esto no se ajusta a nuestra definición de ACM. Sin embargo, ambos presentan soluciones interesantes que combinan la fabricación de compuestos tradicionales y las tecnologías AM ”.
“9T Labs definitivamente está usando impresoras 3D”, señala Wettemann, “pero para crear una preforma que luego se procesa en un proceso de conformado digitalizado para crear componentes compuestos termoplásticos livianos que son completamente nuevos y están dirigidos a mercados que antes no podían usar la tecnología de compuestos. " Aquí, se refiere al objetivo de 9T Labs de reemplazar metales en piezas donde el moldeo por inyección no puede ofrecer un rendimiento suficiente. "En LCC también hemos investigado cómo introducir fibras sin fin en el moldeo por inyección, pero es bastante difícil hacer un posicionamiento preciso de las fibras sin fin en el proceso de inyección". Por el contrario, la tecnología de 9T Labs ofrece lo que parece ser un método de fabricación fácil de implementar para piezas de alto rendimiento.
Arris Composites tiene un enfoque diferente, pero logra un objetivo algo similar, aunque apunta a volúmenes de piezas en un orden de magnitud mayor. “No solo permitimos la producción de alto volumen de piezas de fibra continua, sino que también agregamos multifuncionalidad que desbloquea la consolidación dinámica de piezas”, dice Riley Reese, cofundador y director de tecnología de Arris Composites. "Por ejemplo, convertimos un ensamblaje de 17 componentes en una sola pieza mientras aumentamos la resistencia y agregamos propiedades como la transparencia de radio. Somos competitivos en costos con el moldeo por compresión, por ejemplo, SMC [compuesto de moldeo en láminas], pero con el rendimiento de fibras continuas ".
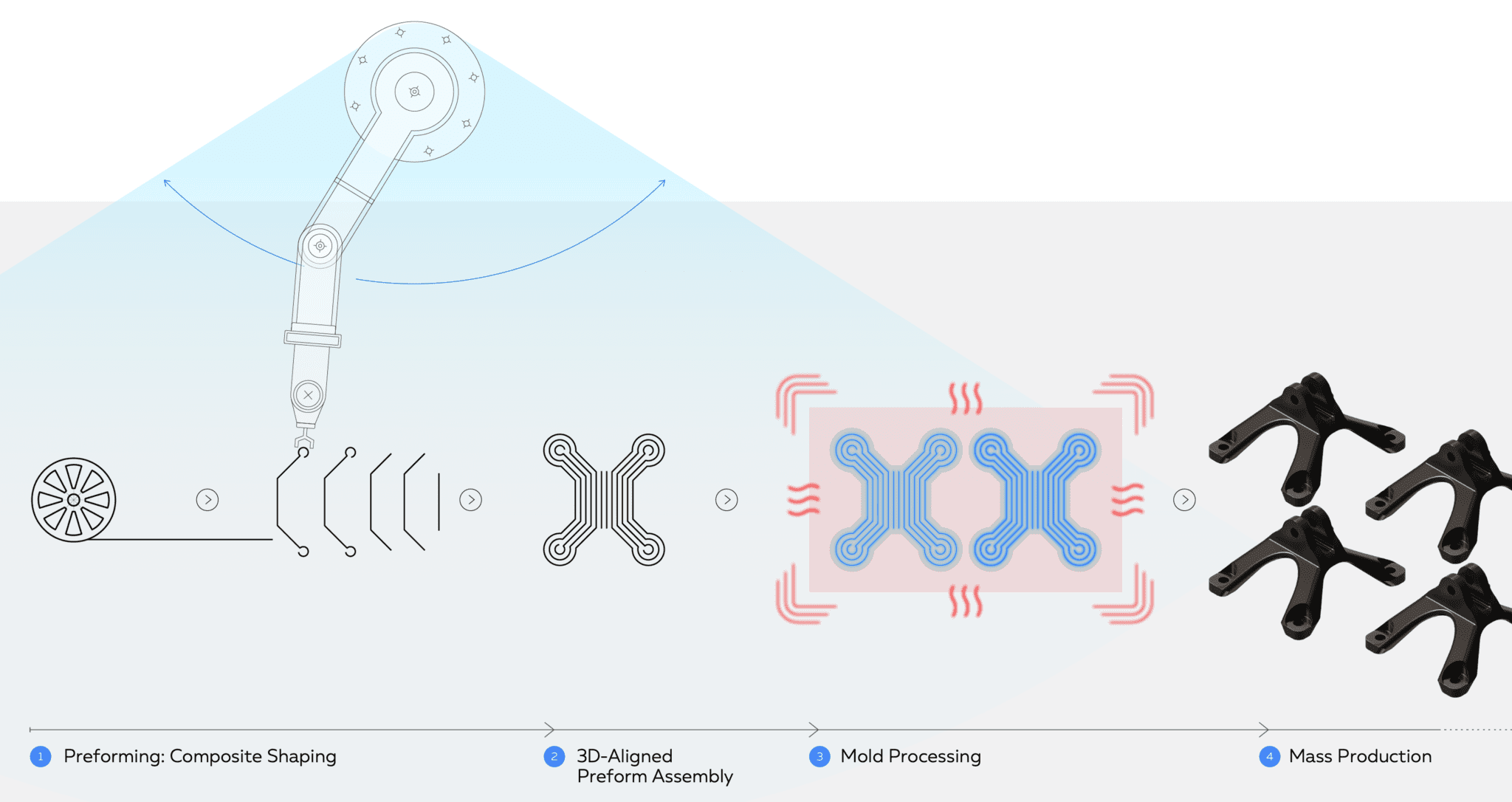
ACM directo frente a indirecto
Volviendo a la definición de ACM de LCC, el tercer componente clave reconoce el debate entre la fabricación con y sin una herramienta de moldeo. " Directo Los enfoques son de donde proviene la forma final de la impresión:nunca tengo una herramienta ”, dice Wettemann. “La ventaja es estar completamente libre de la fabricación de herramientas. Mientras tengamos moldes, hablaremos de indirectos procesos, o estamos hablando de la fabricación de compuestos más convencionales, que luego es asistida por tecnologías AM ”.
Wettemann señala que estos enfoques híbridos están ayudando a abordar factores como la consolidación y las herramientas que aumentan el costo y el tiempo de la fabricación de compuestos tradicionales. “Vimos desarrollos del Centro de Diseño y Fabricación Digital de la Universidad Tecnológica de Singapur y de Mikrosam [Prilep, Macedonia] de 2015 a 2017, donde se desarrollaron robots automatizados para producir piezas compuestas avanzadas en un proceso tipo AFP pero sin herramientas”, dijo explica. “Entonces, esto avanza hacia ACM en el sentido de que ambos enfoques tuvieron éxito en la fabricación digital en el espacio libre sin una herramienta, pero aún se necesita un mayor desarrollo. Reducir la necesidad de herramientas es clave porque eso también nos brinda nuevas posibilidades tanto para fabricar componentes compuestos como para el tipo de componentes que se pueden fabricar ”. Por ejemplo, las rutas de carga muy orgánicas generadas por la optimización de topología y el software de diseño generativo persiguen de hecho la eficiencia de estructuras biológicas como huesos y árboles, pero son muy difíciles de fabricar con fibras continuas.
Desarrollos futuros en LCC
“En la fabricación de piezas directas, vemos lo mismo que está mostrando en su paisaje, que las líneas se están difuminando y nos estamos moviendo hacia un enfoque de fabricación mucho más híbrido”, dice el investigador de LCC Patrick Consul (consulte “Impresión 3D CFRP moldes para flaperones RTM, exoesqueletos y más ”). A principios de este año, su equipo completó las primeras pruebas de un enfoque híbrido que combina extrusión de material y deposición de energía dirigida [DED] utilizando una máquina prototipo basada en láser para imprimir en laminados preconsolidados e impresiones 3D muy grandes sin una cámara calentada. "También estamos trabajando para combinar ACM con fresado y AFP, que son ajustes realmente buenos porque todos se basan en trayectorias de herramientas complicadas", dice. "La transición entre ellos se vuelve bastante simple y no necesita mucha capacitación adicional". Por lo tanto, la cadena de procesos se acorta, digitaliza y simplifica.
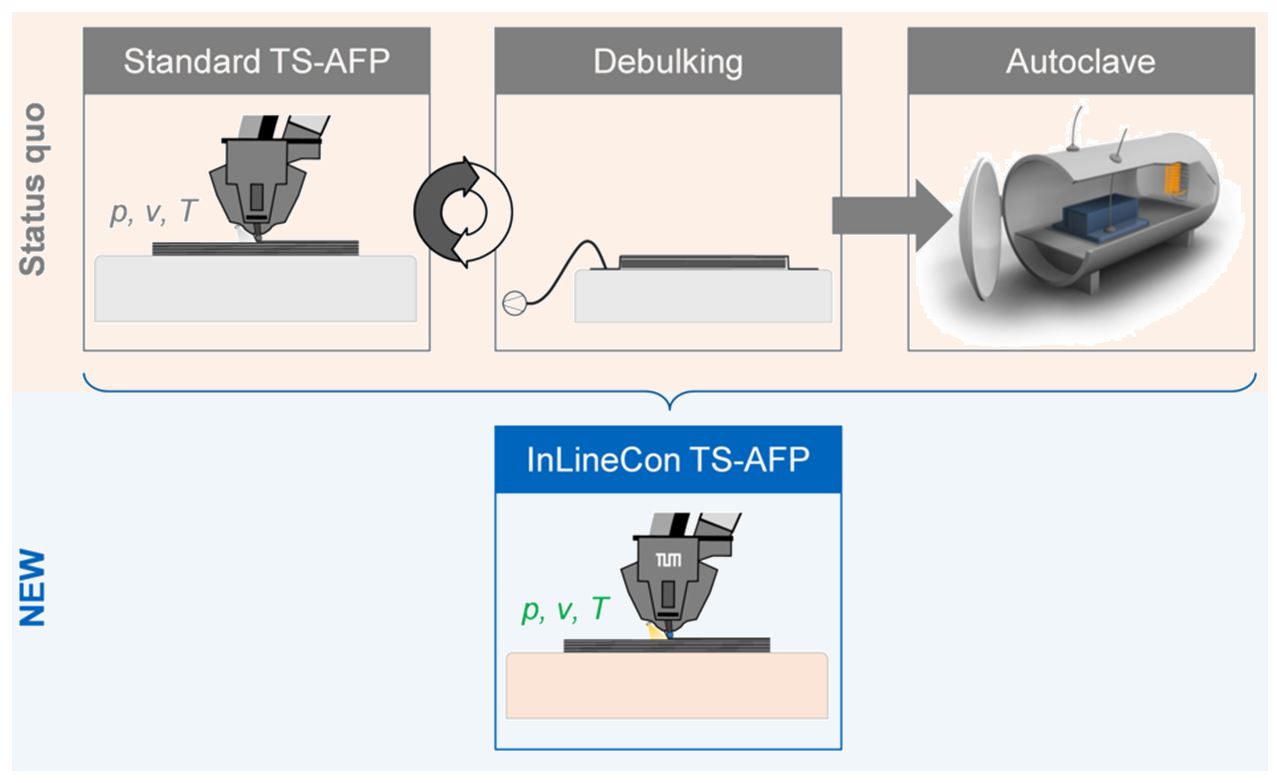
LCC también está impulsando el enfoque híbrido al combinar tecnologías desarrolladas para RTM e impresión 3D. “El resultado es similar al curado sobre la marcha, pero queríamos alejarnos de las resinas de curado UV porque son un poco demasiado caras cuando se desea construir piezas más grandes”, explica Zaremba. “En su lugar, utilizamos una nueva técnica de mezcla ultrasónica que desarrollamos para RTM y ahora la adaptamos para su uso en una extrusora típica con epoxis económicos de curado rápido que se desarrollaron para la industria automotriz”.
Matschinski explica esta tecnología con más detalle:"Estamos utilizando la vibración ultrasónica para mezclar y curar la resina epoxi casi instantáneamente mientras depositamos la fibra impregnada durante la impresión". ¿En qué se diferencia de los ultrasonidos que utiliza el DLR Institute of Composite Structures and Adaptive Systems en Braunschweig, Alemania (consulte “Reducción del costo de los materiales de impresión 3D de fibra continua”)? Matschinski explica:“DLR está utilizando la vibración ultrasónica para mejorar la infiltración de una matriz termoplástica en las fibras extendidas para crear filamentos de impresora 3D continuos reforzados con fibra, que luego se imprimen utilizando extrusión de material convencional. Usamos ultrasonidos para endurecer un filamento termoestable continuo reforzado con fibra ”.
“Organizaciones como Arris Composites, 9T Labs y nuestros equipos aquí en LCC, por ejemplo, son interesantes porque tienen raíces y empleados tanto del mundo de los compuestos como del mundo de AM”, dice Wettemann. “Se unen para crear nuevas tecnologías que pueden ayudarnos ahora a alejarnos de una economía futura que potencialmente está limitada por los recursos y el crecimiento, que lucha contra la crisis climática. Proporcionan un camino hacia las soluciones necesarias ”.
Resina
- Impresión 3D frente a fabricación aditiva:¿cuál es la diferencia?
- El valor de la fabricación aditiva en la industria automotriz
- La evolución del mantenimiento industrial
- La fabricación aditiva entra en la siguiente etapa de su evolución en el AHO
- ¿Es la tecnología de fabricación híbrida el futuro de la fabricación aditiva?
- Creación rápida de prototipos:la evolución de la impresión 3D
- La evolución de la práctica de mantenimiento
- La conferencia magistral de SAMPE 2018 mira hacia el futuro de los compuestos
- La evolución de los materiales médicos
- La evolución de las máquinas médicas
- La evolución de la visión 3D