CosiMo:Proceso inteligente de termoplástico RTM demostrado para el simulador de desafío de la tapa de la caja de la batería
Faurecia Clean Mobility (Nanterre, Francia) lanzó en 2018 el proyecto “compuestos para la movilidad sostenible” (CosiMo) para desarrollar un proceso inteligente de moldeo por transferencia de resina compuesta termoplástica (RTM) utilizando una red de sensores completa que incluye datos de un molde inteligente también como datos de máquina de una máquina de inyección y prensa en caliente. El proyecto se completará a fines de 2021 y los socios de CosiMo han adquirido conocimientos y experiencia con el control de circuito cerrado que combina datos de sensores en tiempo real con parámetros de materiales de datos de laboratorio y datos de simulación. CosiMo está financiado por el Ministerio de Asuntos Económicos, Desarrollo Regional y Energía de Baviera dentro del programa Campus Carbon 4.0.
La parte de demostración, que mide 1.100 milímetros de largo y 530 milímetros de ancho, fue diseñada por el centro de investigación de Faurecia Clean Mobility en Augsburg, Alemania. El objetivo era explorar las limitaciones del material y el proceso, incluido el núcleo de metal y espuma, geometría compleja, varios radios y espesores que varían de 2,5 a 10 milímetros. Las instalaciones del Instituto de Tecnología Textil (ITA) en Augsburgo proporcionaron telas no tejidas de fibra de vidrio de hasta 1.000 gramos / metro cuadrado. También se investigaron las telas de fibra de vidrio que no se arrugan (NCF) y las cintas unidireccionales de fibra de carbono para el refuerzo local. Los materiales de fibra de vidrio permiten el uso de fibras recicladas de piezas compuestas al final de su vida útil (EOL).
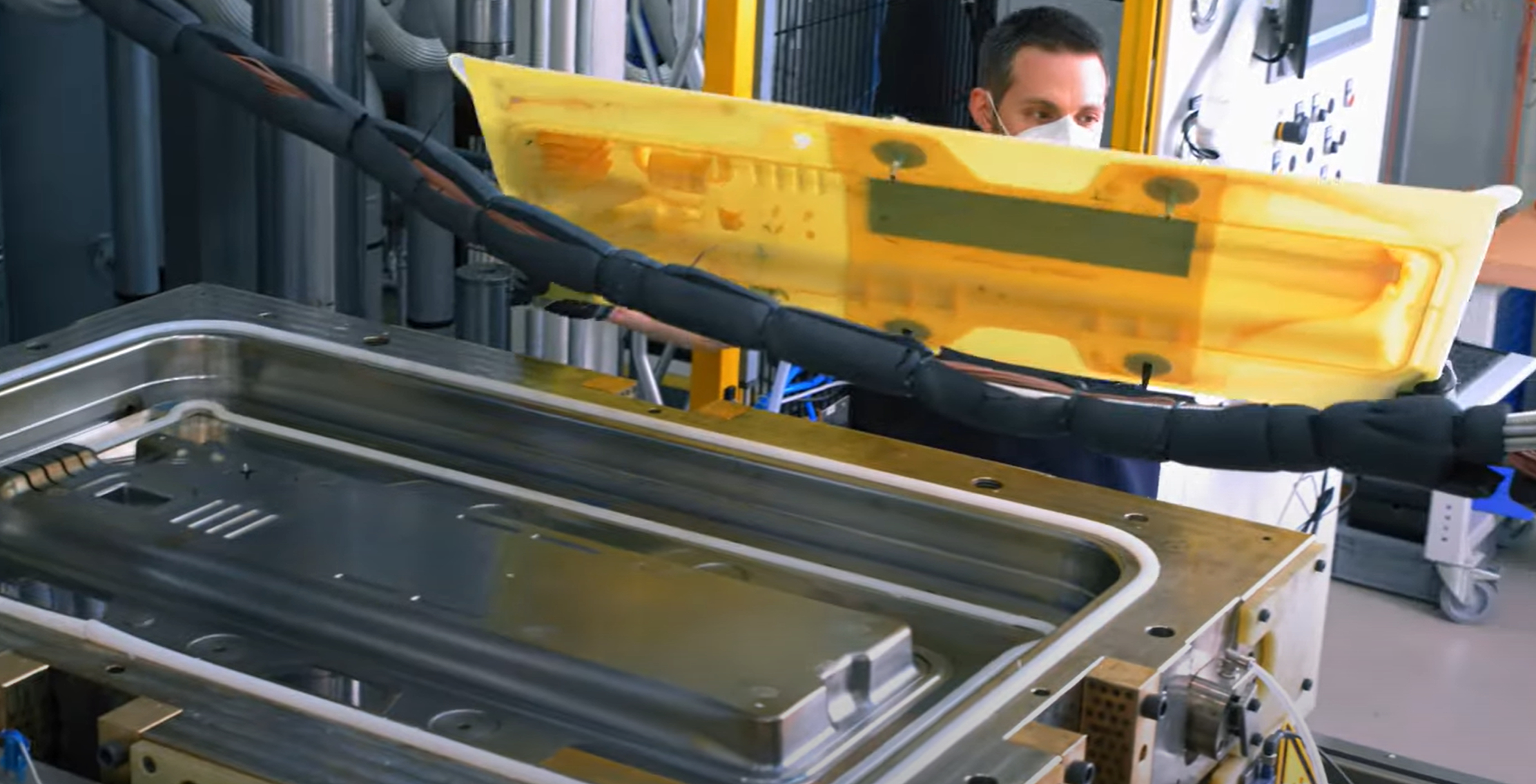
Basado en el diseño de la pieza de Faurecia Clean Mobility y la herramienta de preformado fabricada en Augsburg, el proceso T-RTM en CosiMo utilizó una máquina de inyección KraussMaffei (Munich, Alemania) 3K (tres componentes). El proceso es un derivado de un proceso 2K patentado por Tecnalia (Donostia-San Sebastián, España) que fue demostrado por KraussMaffei en la feria K 2016 en Düsseldorf, Alemania. La máquina de inyección 3K se combinó con una prensa en caliente Wickert (Landau in der Pfalz, Alemania) de 4.400 kilonewton en la que se instaló una herramienta de acero RTM. La herramienta RTM fue fabricada por Siebenwurst en Dietfurt, Alemania.
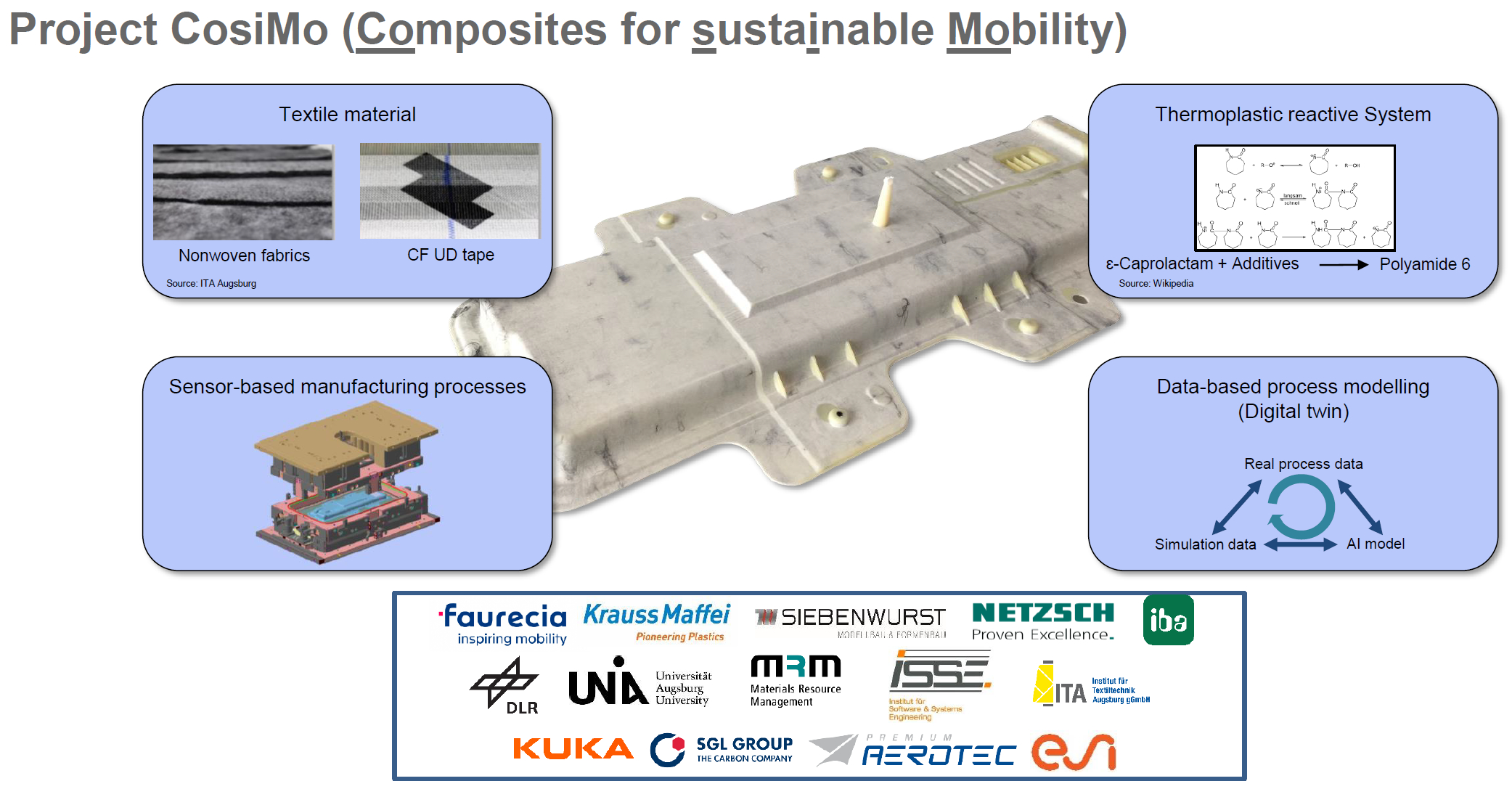
El objetivo principal del proyecto era investigar la automatización completa y el control de procesos basado en sensores para un proceso T-RTM de un solo paso utilizando un molde RTM con sensores y una prensa en caliente. Aproximadamente 100 piezas de demostración fueron fabricadas en este proyecto por el Centro Aeroespacial Alemán (DLR) Centro de Tecnologías de Producción Ligera (ZLP, Augsburg). "Estas piezas, fabricadas con distintos refuerzos, eran de alta calidad y demostraron una alta reproducibilidad", dice Jan Faber, líder del proyecto de fabricación de CosiMo en DLR ZLP.
Como líder del proyecto para el paquete de trabajo “HAP 3 - Herramientas inteligentes”, DLR ZLP también proporcionó la interfaz clave entre las caracterizaciones básicas de materiales en los paquetes de trabajo “HAP 1 - No tejidos a medida” y “HAP 2 - Sistemas reactivos” y el “HAP 4 - Control de procesos basado en datos ”.
Red de sensores
Se integraron más de 70 sensores en las herramientas de acero RTM para monitorear los parámetros del proceso durante la inyección de resina y la polimerización in situ. Esta red comprendía una variedad de sensores que incluían sensores combinados de presión / temperatura de Kistler (Winterthur, Suiza), sensores dieléctricos de Netzsch (Selb, Alemania) y sensores ultrasónicos desarrollados por la Universidad de Augsburg. Estos últimos se basan en conceptos de sensores piezoeléctricos comerciales ampliamente utilizados, pero modificados para las altas temperaturas y los requisitos de integración en el molde del procesamiento de compuestos termoplásticos. Los datos de materiales, procesos y máquinas se recopilaron, procesaron y luego se publicaron en la plataforma de aprendizaje automático mediante un sistema central de adquisición de datos suministrado por iba AG (Fürth, Alemania).
Simulación y optimización de procesos
La red de sensores permitió el seguimiento del flujo de resina y la polimerización, así como el seguimiento de los parámetros de la pieza en la compleja geometría de la herramienta. Se utilizaron parámetros de proceso como la temperatura y la presión para analizar el comportamiento de polimerización y llenado de resina en tiempo real.
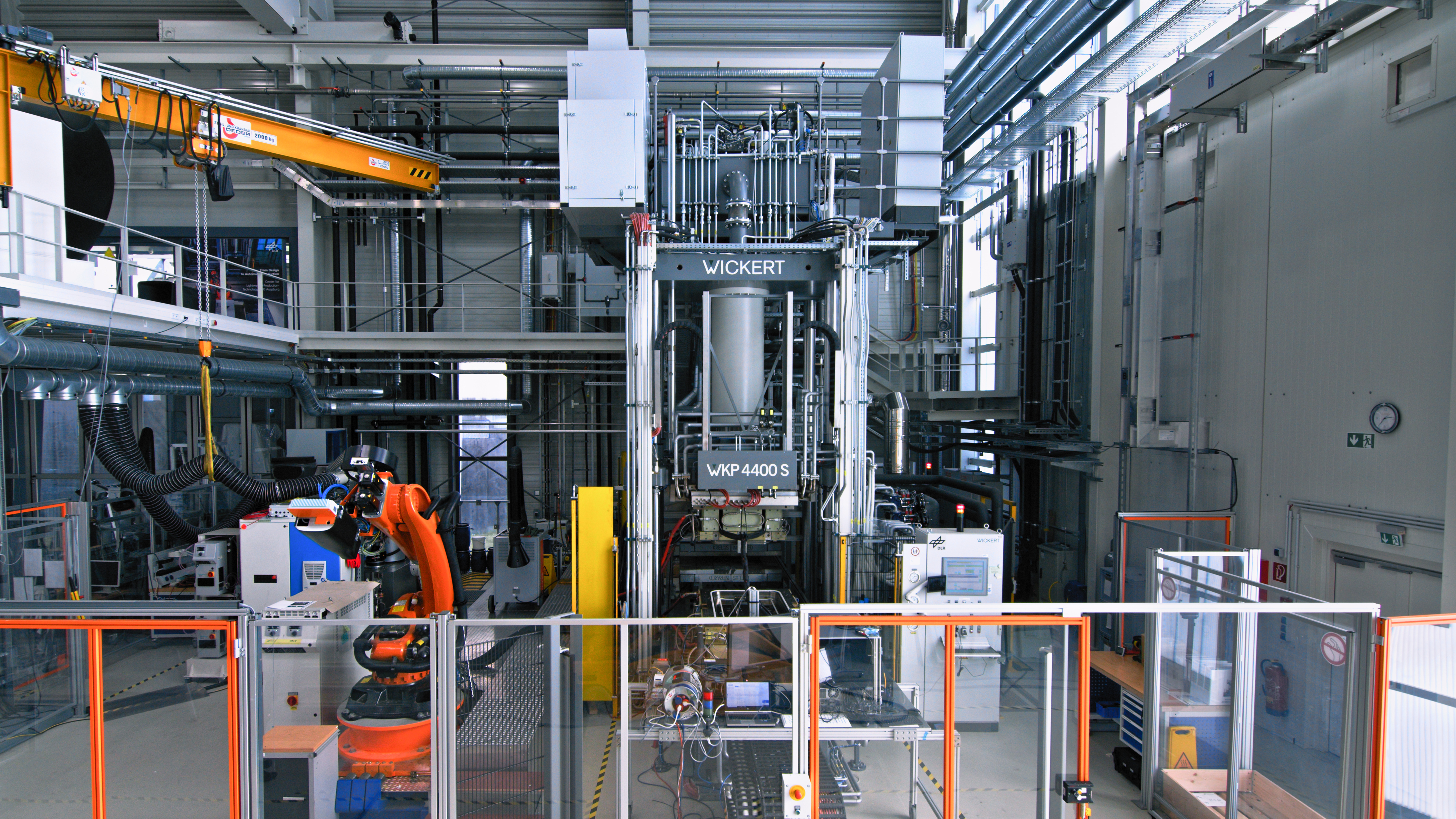
Los datos de los parámetros de proceso de los sensores también se utilizaron para optimizar los modelos de simulación de procesos. Sobre la base de un demostrador de fabricación previamente definido, los subprocesos de fabricación de la pieza (por ejemplo, simulación de llenado de resina) y las características del componente polimerizado (por ejemplo, simulación de distorsión) se modelaron con el software de compuestos ESI PAM (ESI Group, Rungis, Francia). DLR ZLP comparó estos resultados de simulación con datos de proceso reales para optimizar el proceso T-RTM, como parte de las actividades de HP3-Workpackage.
Luego, el proyecto desarrolló un control de procesos automatizado y basado en datos de simulación basado en métodos de aprendizaje automático. El Instituto de Ingeniería de Software y Sistemas (ISSE, prof. Reif) de la Universidad de Augsburg generó datos de capacitación en aprendizaje automático y desarrolló modelos de inteligencia artificial (IA) que predecían el estado de polimerización, así como el tiempo requerido para la polimerización y posibles problemas durante subprocesos de inyección, llenado y polimerización de resinas. Esto se hizo en cooperación con Kuka (Augsburg, Alemania), otro socio clave del proyecto.
El Instituto de Gestión de Recursos de Materiales (MRM) de la Universidad de Augsburg desarrolló un modelo cinético que describe el progreso de la polimerización. Netzsch también fue un colaborador clave, transfiriendo su conocimiento de la monitorización de procesos termoendurecibles a la monitorización de procesos termoplásticos para ayudar a establecer la capacidad de los modelos predictivos de inteligencia artificial para predecir en qué momento debería finalizar la polimerización de PA6 y cuál sería el estado de polimerización.
Fabricación y prueba de piezas
Para la producción de piezas, la herramienta de acero se calentó a 170 ° C y los componentes de resina de caprolactama reactiva se calentaron a 120 ° C. La preforma se colocó en el molde, que luego se cerró. Después de una breve permanencia para permitir que la preforma alcanzara la temperatura del molde, se inyectó el monómero de caprolactama, lo que llevó 20-25 segundos. La simulación del proceso mostró que la polimerización in situ requirió 5,7 minutos después de la inyección para una conversión del 98,5%. Pasado este tiempo, se abrió la prensa y se desmolde la pieza a 170 ° C.
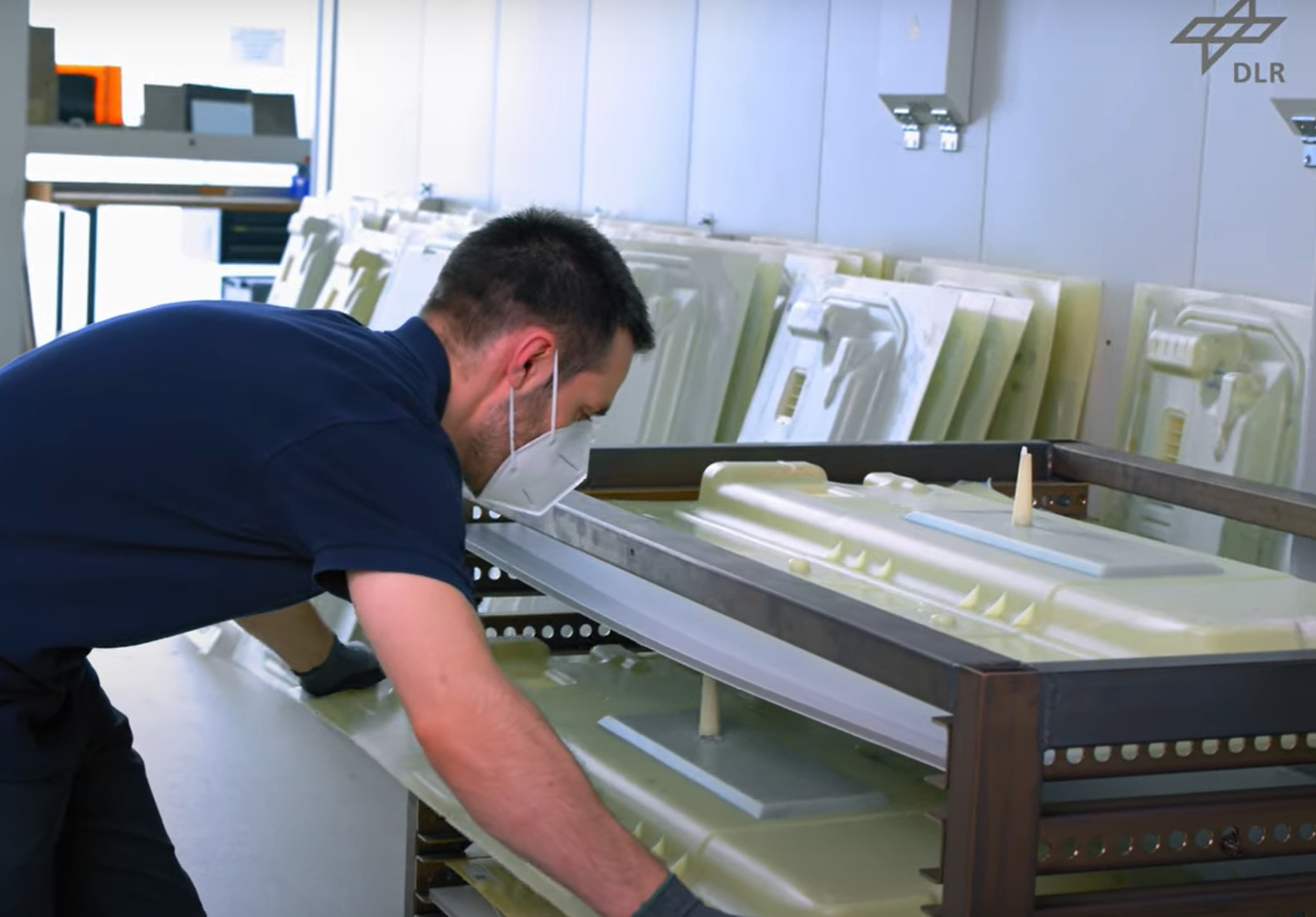
El grado de polimerización se confirmó mediante espectroscopia infrarroja, datos reométricos y análisis de polimerización con sensor DEA. Las piezas terminadas se evaluaron mediante pruebas no destructivas que incluyeron microscopía, termografía y ultrasonido acoplado por aire. La calidad de la pieza se correlacionó con los datos del sensor de proceso y se comparó con piezas similares de fibra de vidrio / termoplásticos en el mercado.
Desarrollo futuro
Para DLR ZLP, dice Faber, este proyecto ha sido un éxito. “Hemos completado nuestra parte y hemos desarrollado mucho conocimiento sobre el uso de sensores para lograr un control de ciclo cerrado completamente digital del procesamiento de compuestos”, dice. “Para la producción industrial en serie, nadie instalaría tantos sensores y eso no es lo que esperaríamos. Pero para esta investigación, esta gran red de sensores fue muy precisa y nos ayudó a tener una visibilidad completa del proceso y el comportamiento del material. Pudimos ver los efectos locales en el proceso en respuesta a variaciones en el espesor de la pieza o en los materiales integrados, como el núcleo de espuma ”.
Señala que este proyecto ha generado mucho conocimiento y ve el potencial futuro para aplicarlo a procesos de infusión y RTM más lentos, donde el riesgo de problemas de calidad de las piezas ha sido históricamente muy alto. Faber también presentará los desarrollos y resultados del proyecto CosiMo en "Monitoreo de procesos basado en sensores de polimerización in situ en la fabricación de T-RTM con caprolactama" el miércoles 29 de septiembre durante el evento en vivo y virtual, conferencia SAMPE Europe 21, en sesión. 1, Sala 1 - Automotriz.
DLR ZLP es también uno de los tres socios clave en la red de producción de IA (inteligencia artificial) de Augsburg, fundada en enero de 2021, que también reúne a la Universidad de Augsburg y al Instituto Fraunhofer de Fundición, Composites y Tecnología de Procesamiento (Fraunhofer IGCV). Como explicó el Dr. Markus Sause, director de AI Production Network y también investigador del proyecto CosiMo que desarrolla sensores ultrasónicos, “vamos a extender este plan de colaboración que se ha destacado en el proyecto CosiMo a una escala mucho mayor, desarrollando Tecnologías de IA para producción con un fuerte enfoque en compuestos. Nuestra nueva instalación de 5.000 metros cuadrados en Augsburgo se abrirá en 2022 y se equipará con una variedad de máquinas durante el próximo año, lo que permitirá a las empresas ver demostraciones de lo que la IA puede hacer por procesos reales en un entorno de producción ”.
Mientras tanto, Faurecia Clean Mobility ampliará internamente el conocimiento adquirido sobre el proyecto CosiMo, que está totalmente alineado con la estrategia de sostenibilidad y transición ecológica de Faurecia. Faurecia también agradece al Ministerio Federal de Economía, Desarrollo Regional y Energía de Baviera, que ha apoyado financieramente este proyecto de investigación.
Resina
- Batería
- Compuesto de TPE utilizado para hisopos de "algodón" sostenibles
- Biomaterial termoplástico "perfeccionado" para aplicaciones médicas
- TPE de grado médico utilizado para la pelota de terapia ganadora de premios
- Personalización de sensores ultrasónicos para la optimización y el control de procesos compuestos
- Las cintas termoplásticas continúan mostrando potencial para aeroestructuras compuestas
- UBQ Materials obtuvo las certificaciones ISO para termoplásticos derivados de residuos
- Polyscope Polymers gana el premio a la innovación JEC por sus rieles guía compuestos termoplásticos
- Puerta termoplástica por primera vez para compuestos automotrices
- Factores importantes a tener en cuenta para subcontratar un proceso de ensamblaje de construcción de cajas
- Cosas a considerar para el proceso de ensamblaje de construcción de cajas