Personalización de sensores ultrasónicos para la optimización y el control de procesos compuestos
Este blog es una continuación de mi informe sobre el proyecto CosiMo (“compuestos para la movilidad sostenible”). Ese proyecto fue lanzado en 2018 por Faurecia Clean Mobility (Nanterre, Francia) para demostrar la "fabricación inteligente" de una tapa de caja de batería compuesta. La pieza de desafío de 1.100 milímetros de largo y 530 milímetros de ancho presentaba refuerzos de fibra de vidrio no tejida y fibra de carbono unidireccional, así como inserciones de metal y espuma, geometría compleja que incluye varios radios y espesores que varían de 2.5 a 10 milímetros. La pieza se moldeó usando moldeo por transferencia de resina termoplástica (T-RTM), donde se inyectó monómero de caprolactama y luego se polimerizó in situ durante el ciclo de prensado calentado para formar un compuesto de poliamida 6 (PA6). El objetivo principal del proyecto era investigar un proceso completamente automatizado utilizando un control de proceso de circuito cerrado basado en sensores.
Este blog explora con más detalle la red de 74 sensores utilizados en la parte del desafío CosiMo, y en particular los sensores ultrasónicos desarrollados por la Universidad de Augsburg (UNA, Augsburg, Alemania) y cómo se utilizaron los datos de todos los sensores para construir un modelo digital del proceso (gemelo digital).
Basado en el éxito de CosiMo y la necesidad de un centro de desarrollo para el desarrollo de fabricación basado en sensores e inteligencia artificial, UNA ha formado la red de producción de inteligencia artificial de Augsburg, en colaboración con el socio del proyecto CosiMo, el Centro Aeroespacial Alemán (DLR), el Centro de Tecnologías de Producción Ligera ( ZLP, Augsburg) y el Instituto Fraunhofer de Tecnología de Fundición, Composites y Procesamiento (Fraunhofer IGCV). "Estamos estableciendo una nueva instalación de 5.000 metros cuadrados que operaremos en colaboración", dice el Dr. Markus Sause, profesor de UNA y director de la Red de Producción de IA de Augsburg. "Tendremos células de producción automatizadas, muchas de ellas enfocadas en tecnologías de compuestos, que nos permitirán demostrar lo que puede hacer la IA".
Red de sensores CosiMo
Para el proyecto CosiMo, se integraron 74 sensores en las herramientas de acero RTM suministradas por Christian Karl Siebenwurst GmbH &Co. KG (Dietfurt, Alemania) para moldear la tapa de la caja de la batería T-RTM. Utilizada para monitorear los parámetros del proceso durante la inyección de resina, la infiltración (monitoreo del frente de flujo) y la polimerización in situ, esta red incluía:
- 1 sensor de vacío
- 4 sensores de presión / temperatura de Kistler (Winterthur, Suiza)
- 4 sensores de temperatura de Kistler
- 8 sensores de temperatura / análisis dieléctrico (DEA) de Netzsch (Selb, Alemania)
- 57 sensores ultrasónicos desarrollados por la Universidad de Augsburg.
En mi informe inicial sobre CosiMo, hablé de cómo esta red de sensores era para I + D, no para producción estándar:
“Para la producción industrial en serie, nadie instalaría tantos sensores y eso no es lo que esperaríamos”, dice el líder del proyecto de fabricación de CosiMo en DLR ZLP, Jan Faber. “Pero para esta investigación, esta gran red de sensores era muy precisa y nos ayudó a tener visibilidad completa del proceso y comportamiento material . Pudimos ver los efectos locales en el proceso en respuesta a variaciones en el espesor de la pieza o en los materiales integrados, como el núcleo de espuma ”.
Entonces, ¿cómo se diseñó esta red? “La mayoría eran sensores ultrasónicos porque tienen el costo más bajo”, explica Faber. “Los usamos en una cuadrícula a una distancia definida entre sí. En algunas posiciones, sacamos los sensores ultrasónicos y colocamos los sensores de temperatura / presión de Kistler o DEA / temperatura de Netzsch. Y para estos sensores específicos, tanto el DEA como el Kistler, solo intentamos tener uno cerca del bebedero, donde entraba la resina, y luego uno lejos. Así, pudimos monitorear los lugares a donde llega la resina después de haber visto la temperatura del molde durante algún tiempo ”.
¿Por qué utilizar diferentes tipos de sensores? “Una tarea de investigación fue comparar las señales y ver cómo funcionan los diferentes sensores”, dice Faber. Esto es importante porque los diferentes tipos de sensores se basan en diferentes principios de medición. Por ejemplo, los sensores DEA miden la impedancia CA de la resina, que se puede dividir en diferentes fracciones, que a su vez muestran diferentes efectos en el polímero. Mientras tanto, Kistler utiliza sensores piezorresistivos que se basan en un puente Wheatstone a base de silicio, un tipo de circuito utilizado para medir la resistencia eléctrica dinámica, conectado a una membrana que forma el extremo sensor instalado en la pared de la cavidad de la moldura. La membrana se extiende bajo presión, lo que cambia la resistencia eléctrica del puente Wheatstone de silicio, que a su vez emite una señal eléctrica. “También usamos el nuevo sensor 4001a de Kistler que mide tanto la presión como la temperatura”, señala Faber. "Fue muy útil tener ambos valores para puntos locales seleccionados en la herramienta".
Sensores ultrasónicos UNA
La mayoría de los sensores utilizados en la red de piezas de CosiMo eran sensores ultrasónicos desarrollados por UNA. Sause señala que se vieron favorecidos no solo por su bajo costo (<10 euros) sino también porque pueden entregar una amplia gama de información.
Los sensores ultrasónicos se han utilizado durante décadas para inspeccionar piezas compuestas terminadas, pero también tienen una larga trayectoria en el moldeo por inyección. Los sensores ultrasónicos envían una onda de sonido de alta frecuencia a un medio y miden su reflexión (pulso-eco) y / o transmisión. En el proyecto CosiMo, la frecuencia nominal fue de 2000 kilohercios. De los 57 sensores ultrasónicos instalados en el molde, a una distancia de 20 milímetros de la superficie de la cavidad, 10 funcionaron en modo transmisión y el resto en modo pulso-eco. Los sensores ultrasónicos miden la velocidad de la onda y disminuyen su amplitud (atenuación); ambos son sensibles a las propiedades del polímero. Además, la velocidad de la onda se puede calcular en función de la presión y la temperatura, pero los datos de ultrasonido deben calibrarse para el polímero que se está investigando.
“El sensor ultrasónico que hemos desarrollado en realidad no es muy diferente de lo que está disponible comercialmente”, dice Sause. “Se basa en un material piezoeléctrico, que es bastante sensible para convertir un movimiento elástico en una señal eléctrica. Pero donde los sensores típicos pueden operar a temperaturas de hasta 150 ° C, tuvimos que igualar las altas temperaturas del molde termoplástico a más de 200 ° C, lo que fue un poco desafiante para la electrónica del sensor ”.
“También tuvimos que diseñar el sistema mecánico para integrar correctamente el sensor en el molde”, explica, “lo que requería una carga de resorte con un buen sellado para proporcionar un buen acoplamiento. Había una gran cartera de requisitos que el sensor tenía que cumplir; así que tuvimos que diseñarlo prácticamente desde cero. También hicimos un diseño acústico adecuado de todo el sistema ”.
Monitoreo de frente de flujo y polimerización
“La acústica se centra en las propiedades elásticas de los materiales en el molde”, continúa Sause. “Básicamente, la rigidez en un líquido no es la misma que cuando se completa la polimerización. Estamos monitoreando efectivamente esa transición. Observamos la intensidad acústica de la reflexión de la onda en la interfaz entre el molde y el material polimérico en cada ubicación del sensor y, por lo tanto, seguimos continuamente el curado a lo largo del tiempo ”.
La mecánica de esta medición se explica por Sause y Faber, et. al., en el documento de la conferencia SAMPE Europe 2021, “Monitoreo del proceso basado en sensores de polimerización in situ en la fabricación de T-RTM con caprolactama”. La relación de la amplitud del eco de la señal acústica antes y después de la impregnación de la preforma depende del índice de reflexión en la interfaz molde-pieza, R. Esto se acerca a un valor constante a medida que avanza la polimerización. Idealmente, una vez que la polimerización se acerque a su finalización, el cambio en R será cero.
También es posible, a partir de la señal de transmisión acústica, extraer el tiempo de recorrido para que las ondas ultrasónicas atraviesen la preforma impregnada. Esto es útil ya que la velocidad del sonido a través de la preforma está relacionada con el grado de polimerización. Para la experimentación completada en el momento del documento SAMPE Europe 2021, el tiempo entre la humectación completa de la preforma en la ubicación del sensor y la finalización de la polimerización fue de 240 segundos.
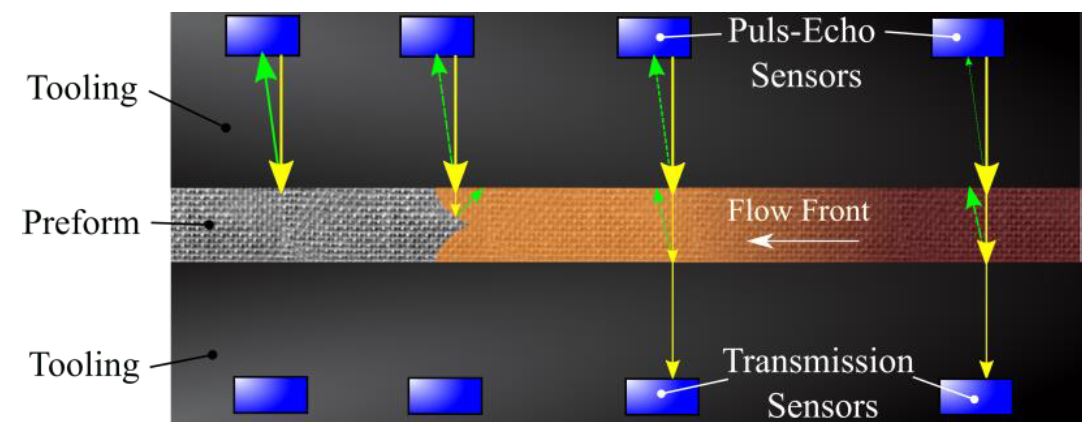
"También podemos monitorear el flujo durante la inyección", explica Sause, "porque la información de la señal acústica cambia cuando el frente de flujo del polímero pasa por el sensor". También verificado en el documento SAMPE Europe 2021, la señal acústica cayó abruptamente desde un valor inicial normalizado de 1 a entre 0,85-0,9 al llegar el frente de flujo de caprolactama para el sensor seleccionado 15 segundos después de que comenzara la inyección.
Desarrollo de un gemelo digital del proceso
Sause dice que desarrollar el sensor ultrasónico fue en realidad una parte muy pequeña de lo que hizo UNA en el proyecto CosiMo, "y ni siquiera la parte más fascinante". El verdadero logro, señala, fue el análisis de datos y el desarrollo de un modelo digital del proceso para permitir el control de circuito cerrado durante la fabricación de piezas.
"Lo que estamos tratando de hacer es proporcionar información sobre lo que realmente está ocurriendo en el molde", agrega. “Hemos establecido rutas para adaptar el proceso con temperatura y presión, más o menos, pero lo que estamos haciendo ahora es explotar la información de la señal acústica haciendo pulsaciones activas en la ubicación de cada sensor. Y esto nos permite determinar varias cosas, como la forma del frente de flujo, el tiempo que tarda en llegar a cada parte de la preforma y el grado de polimerización en la ubicación de cada sensor ”.
“Idealmente, puede establecer configuraciones para habilitar el control de circuito cerrado y ajustar durante el proceso”, dice Sause. “Estos incluirían parámetros como la presión de inyección y la presión y temperatura del molde. También puede utilizar esta información para optimizar sus materiales ”.
El desarrollo del gemelo digital fue un esfuerzo de múltiples etapas y de múltiples socios. Comenzó con uno de los paquetes de trabajo asignados al DLR ZLP. “Establecimos una simulación basada en una placa 2D, donde queríamos simular el llenado y la polimerización utilizando el software de simulación PAM-RTM de ESI Group (Rungis, Francia)”, dice Faber. “Obtuvimos los datos de permeabilidad de las preformas de los socios del proyecto ITA (Instituto de Tecnología Textil, RWTH Aachen, Alemania) y SGL Carbon (Wiesbaden, Alemania) y también un modelo reactivo de la reacción del polímero termoplástico de la Universidad de Augsburg. Luego integramos todo en la simulación e intentamos ver qué tan cerca podíamos llegar a los datos reales del sensor ”.
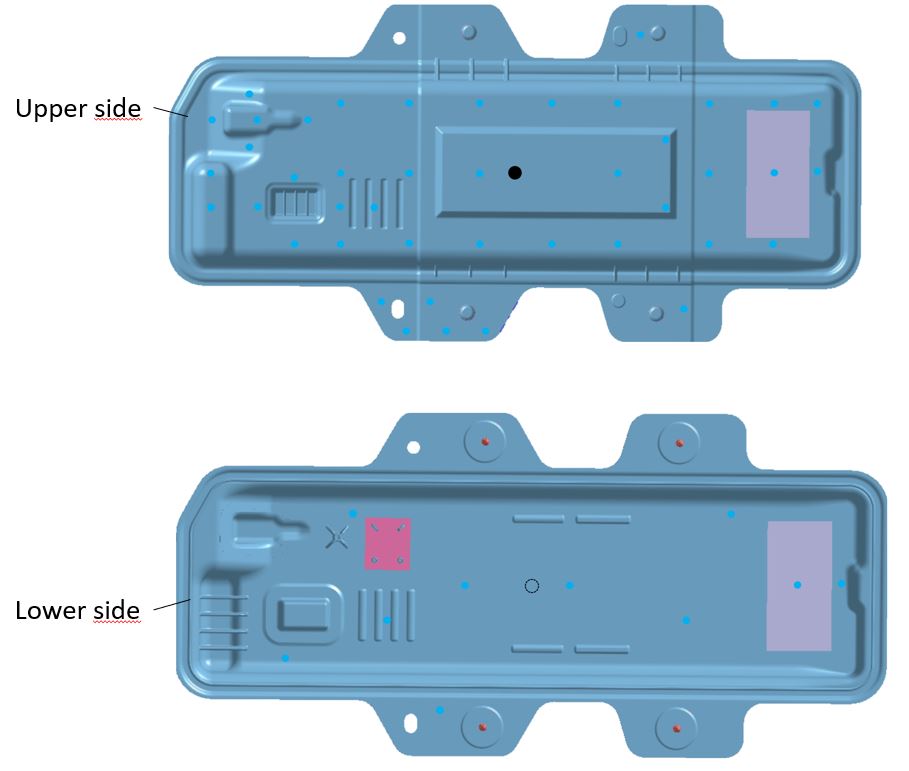
Los puntos azul claro en los moldes superior e inferior de la parte de demostración del proyecto CosiMo proporcionaron datos en puntos específicos durante todo el proceso. Luego, esto se usó en la simulación de gemelo digital para interpolar entre las ubicaciones de los sensores y modelar el proceso a lo largo de la pieza. Crédito de la foto:proyecto CosiMo, DLR ZLP Augsburg, Universidad de Augsburg
“Descubrimos, basándonos en el modelo de placa 2D, que en realidad estamos muy cerca en lo que respecta al relleno”, continúa Faber. “Pero tuvimos algunos efectos de temperatura durante la polimerización que no pudimos describir en la simulación. Por ejemplo, esta reacción de polimerización es exotérmica y se ve un ligero aumento en los sensores de temperatura en los datos reales, pero el aumento en la simulación fue mucho mayor. Entonces, esta es un área en la que continuamos trabajando ”.
Una de las cosas que el equipo quería descubrir de la simulación era el tiempo necesario para que se completara la polimerización. “Lo que realmente queríamos era el tiempo mínimo que necesitábamos en el molde”, señala Faber. Esta información se derivó del modelo de simulación y se basó, como lo hizo toda la simulación, en múltiples tipos de sensores y algoritmos de IA. Por ejemplo, Netzsch proporcionó los sensores dieléctricos utilizados para el análisis dieléctrico, pero también ayudó con partes del gemelo digital del proceso. “Establecieron modelos de IA predictivos para investigar los mecanismos dentro de la inyección y predecir en qué momento debería terminar la polimerización y cuál sería el estado de polimerización”, dice Faber.
(Tenga en cuenta que Netzsch ha combinado sus competencias en caracterización de materiales, simulación cinética y tecnología de sensores para establecer nuevas ofertas en soluciones de inteligencia artificial y en la nube. Este tipo de solución integrada se ha demostrado con éxito en CosiMo para proporcionar una evaluación en tiempo real del grado de polimerización y se comercializará bajo la marca sensXPERT.)
A partir de la red completa de sensores y simulación, se encontró que 96% fue la polimerización máxima alcanzada y que requirió 4.5 minutos. "Así que es mucho más rápido que los procesos de infusión, pero mucho más lento que la inyección de alta velocidad con termoestables, por ejemplo".
“Los datos del sensor encajan en el modelo de gemelo digital”, dice Sause. “La idea era tener un modelo ejecutándose al mismo tiempo que el proceso que se estabiliza numéricamente por la información del sensor. Los puntos azules proporcionan una gruesa cuadrícula de sensores ultrasónicos, y luego pudimos interpolar entre esos puntos. Por ejemplo, pudimos proporcionar un video de cómo se desarrolla el frente de flujo en la parte CosiMo en función del tiempo en función de los datos de medición de nuestros sensores ”.
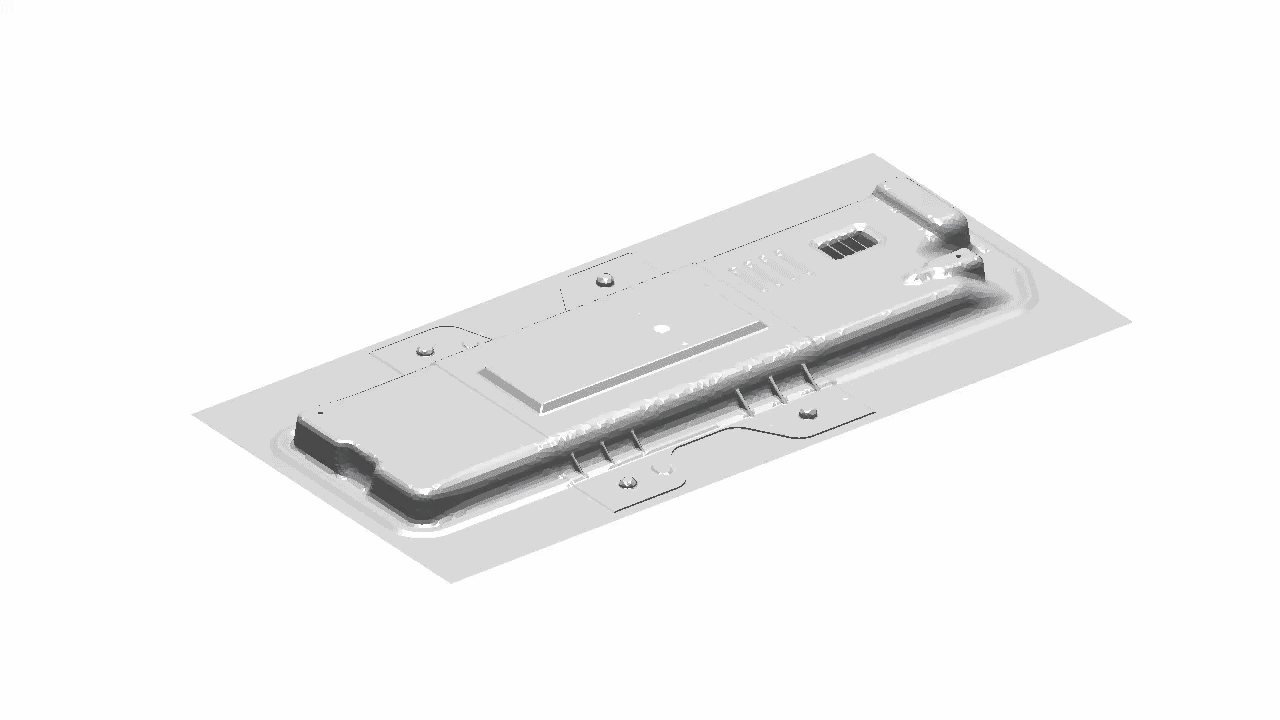
¿Cómo se validaron las predicciones de la tasa de polimerización? “Tuvimos varios enfoques”, dice Sause. “Primero, un estudiante de doctorado aquí en UNA estaba haciendo un conjunto completo de modelos para la cinética de reacción del sistema de material de caprolactama a PA6. Entonces, estaba estudiando simultáneamente espectroscopía infrarroja junto con datos reométricos y datos de los sensores de análisis dieléctrico para proporcionar un modelo de material muy preciso para la cinética curada de ese sistema y para validar ese modelo. Entonces, usamos el mismo modelo para validar nuestros sensores ".
Arquitectura del gemelo digital
La arquitectura de cómo funciona el gemelo digital es descrita por Stieber, et. Alabama. en el documento técnico de 2020, "Hacia la supervisión de procesos en tiempo real y el aprendizaje automático para la fabricación de estructuras compuestas":
Consta de tres partes:la maquinaria T-RTM, los sensores in situ en las herramientas del molde y el gemelo digital. Esta estructura y el gemelo digital, en particular, se han desarrollado con los siguientes objetivos O1 - O4 en mente:
- O1:Supervise el proceso de fabricación de cada pieza compuesta con los sensores in situ de las herramientas.
- O2:Visualice cada proceso de fabricación en tiempo real para obtener más información sobre el proceso.
- O3:Entrene modelos de AA sobre datos reales y simulados para predecir el resultado del proceso de fabricación.
- O4:Utilice modelos de AA capacitados para reducir los rechazos de producción.
Luego, los sensores alimentan datos al análisis de borde del gemelo digital, que luego se puede usar para predecir la dinámica futura del frente de flujo, determinar el contenido de volumen de fibra de cada preforma textil, predecir puntos secos y detectar anomalías que pueden reducir las piezas rechazadas.
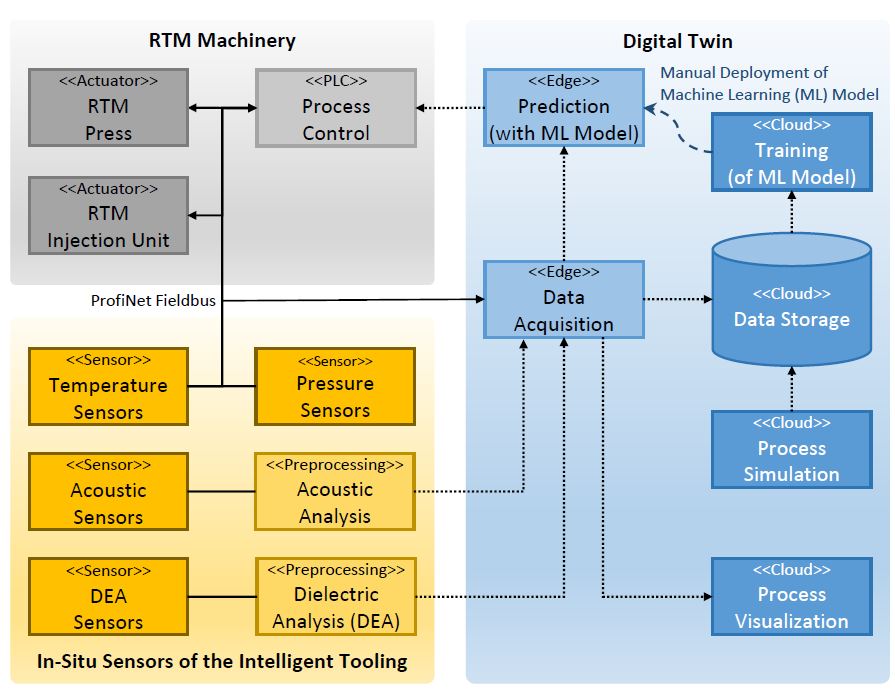
La maquinaria T-RTM consta de dos componentes estándar:una prensa en caliente Wickert (Landau in der Pfalz, Alemania) de 440 kilonewton y una unidad de inyección T-RTM de KrausMaffei (Múnich, Alemania). Ambas máquinas, así como toda la red de sensores, están conectadas a un PLC (controlador lógico programado) que es responsable de controlar todo el proceso de fabricación.
Debido a que los sensores necesitan un procesamiento previo en tiempo real para transformar los datos sin procesar en información de nivel superior sobre el frente de flujo o el curado de la resina, los datos preprocesados se registran directamente en el borde utilizando una unidad de adquisición de datos ibaPDA de iba AG ( Fürth, Alemania). Por lo tanto, los datos del sensor se registran y combinan con un sello de tiempo coherente vinculado a los datos del proceso y la información de la pieza con los datos del sensor según los objetivos O1 y O2.
Para optimizar automáticamente el proceso de fabricación, los datos almacenados se utilizan para entrenar modelos de aprendizaje automático (ML) para abordar el objetivo O3. Estos modelos son responsables, por ejemplo, de reconstruir el frente de flujo de la resina a partir de la red de sensores, de predecir el progreso del frente de flujo e, idealmente, de adaptar los parámetros del proceso para optimizar el resultado, ya sea durante una instancia de proceso o para ejecuciones posteriores. . Debido a que los datos reales generalmente no son suficientes para entrenar modelos confiables, el equipo de gemelos digitales utilizó ejecuciones simuladas PAM-RTM para aumentar los datos medidos. Después del entrenamiento previo con datos simulados, el gemelo digital se ajustó con datos del mundo real. Esta estrategia se conoce como aprendizaje por transferencia y se ha adoptado con éxito en aplicaciones de procesamiento de lenguaje natural y visión por computadora. Los análisis avanzados posibles con ML permiten mayores capacidades de predicción y visualización de procesos, así como un control de circuito cerrado.
Integración de sensores para la producción de compuestos industriales
Entonces, ¿cómo aplican los fabricantes de componentes compuestos esta tecnología para desarrollar el control de circuito cerrado en sus propios procesos de producción? Sause dice que tiene sentido utilizar varios tipos de sensores para validar de forma cruzada el control de flujo y curado / polimerización y para proporcionar información complementaria. Y luego se trata de definir la ubicación del sensor, incluidos los tipos que se colocan en cada ubicación. "Por ejemplo", señala, "no necesita sensores de presión y temperatura en todas partes, sino solo donde necesita esos puntos de datos clave, como la entrada de resina, puntos de geometría compleja, etc."
Cuantos sensores? “Para CosiMo, usamos 74 sensores, pero para una pieza de medio metro usaría menos, quizás 35-40 dependiendo de su geometría y puntos clave de interés”, dice Sause. “También depende del proceso de producción. Hay procesos en la industria aeroespacial, por ejemplo, que se han utilizado durante décadas y están bien establecidos. Para estos, es posible que no necesite muchos sensores y podría ser posible integrarlos sin mucho trabajo de desarrollo al principio. Pero otros procesos son más desconocidos y requerirán más trabajo por adelantado. Para CosiMo, estábamos considerando usar T-RTM con polimerización in situ a PA6, y esto no estaba tan bien documentado como RTM con epoxi, por ejemplo ”.
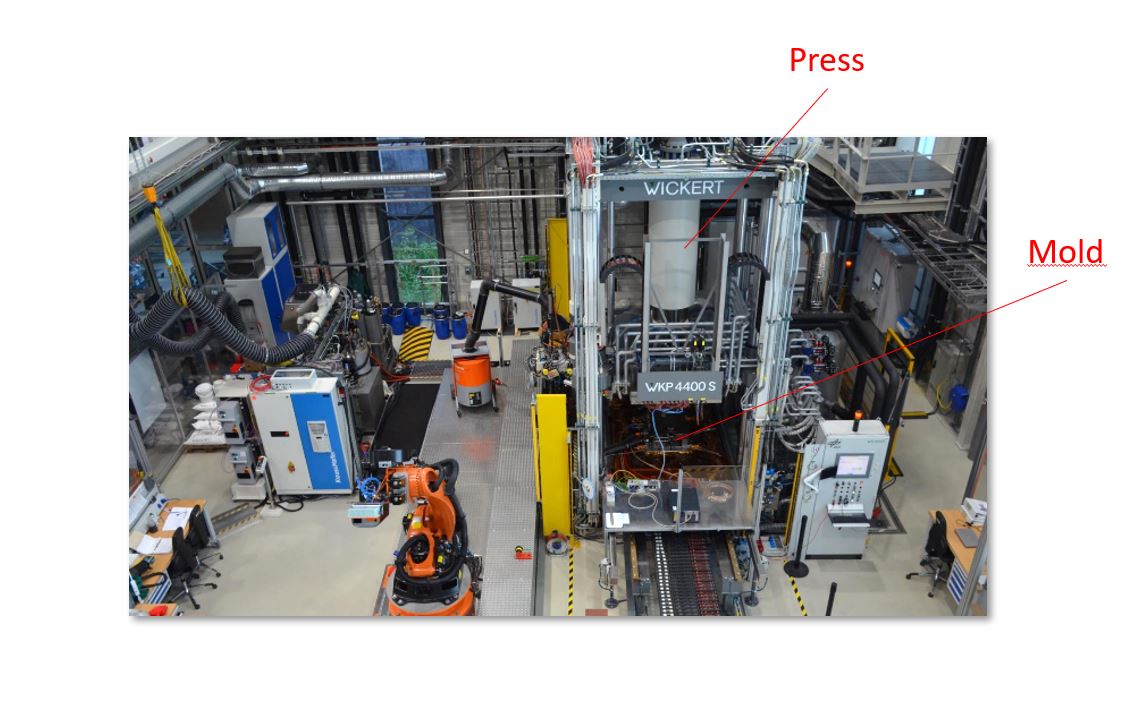
El equipo de fabricación del proyecto CosiMo comprendía una prensa Wickert de 440 kN y una máquina de inyección KraussMaffei. Crédito de la foto de esta serie:proyecto CosiMo, DLR ZLP Augsburg, Universidad de Augsburg
¿Cuánto tiempo requiere la construcción de un modelo digital? ¿Y eso siempre es necesario para lograr un control de bucle cerrado? “Nuevamente, depende de su proceso y del nivel que desee alcanzar”, dice Sause. “En primer lugar, tener la información del sensor integrada le permite visualizar lo que está sucediendo dentro de su caja negra de procesamiento y qué parámetros utilizar.
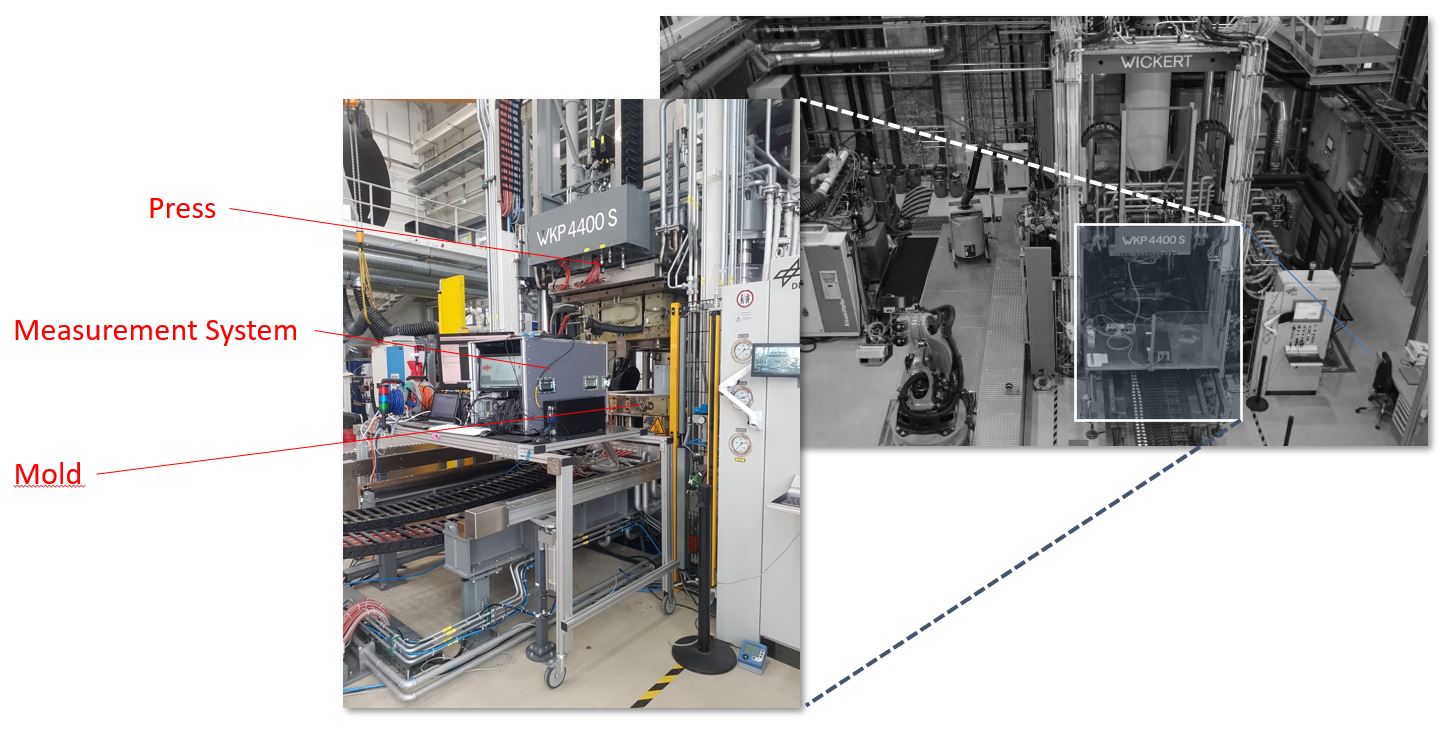
El sistema de control de circuito cerrado desarrollado en CosiMo también integró sensores en el molde y un sistema de adquisición de datos (el sistema de medición se muestra aquí) de iba AG.
Una vez que se alcanza ese primer objetivo, quedan algunos pasos más para lograr el control del proceso de ciclo cerrado. La mitad del camino, quizás, es tener la visualización y puede presionar el botón de parada usted mismo para adaptar el proceso y evitar el rechazo de piezas. Así que eso también es un comienzo. Y luego puede desarrollar el gemelo digital, pero necesita datos de entrenamiento. Por lo tanto, debe proporcionar eso de alguna manera, lo que significa que puede producir un par de partes para usar como datos de entrada. Pero también es necesario producir piezas de baja calidad. Por lo tanto, es una cuestión de su voluntad de invertir en la capacitación de su enfoque de aprendizaje automático ".
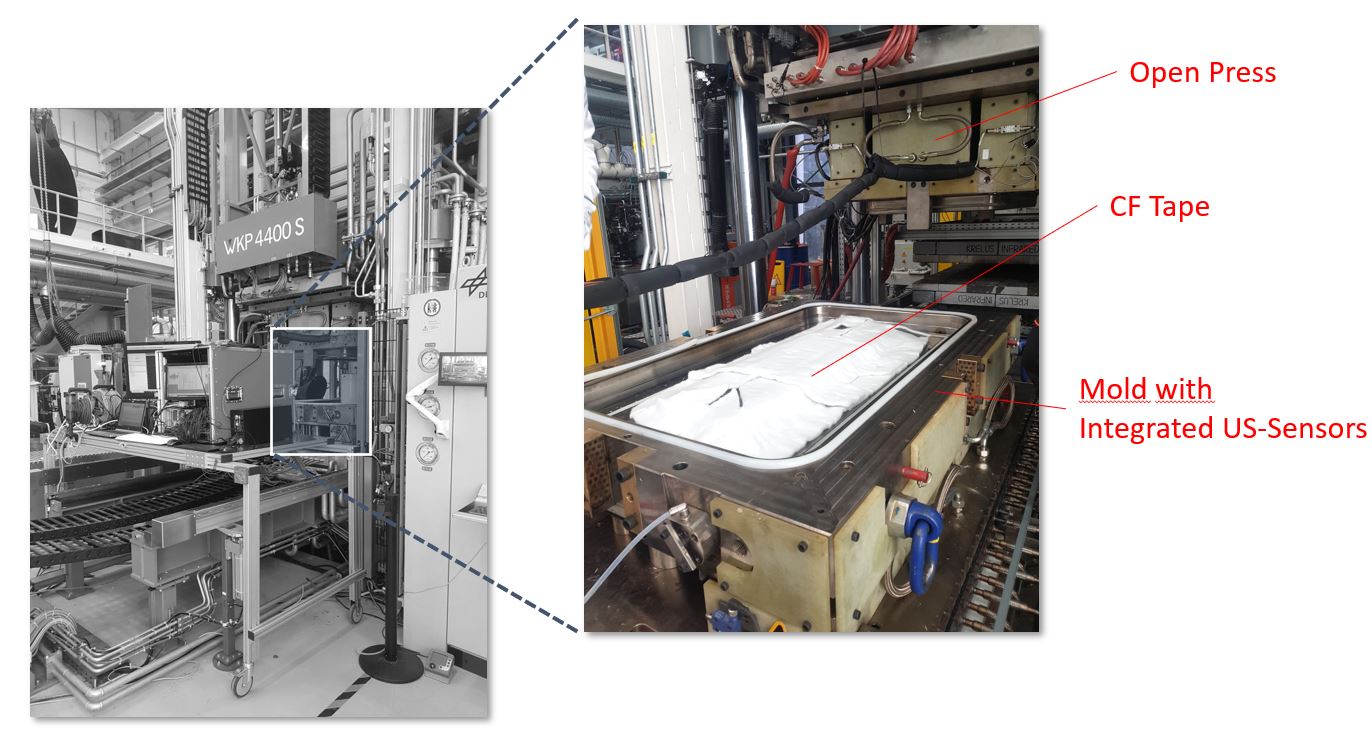
Una vez entrenado, el gemelo digital puede optimizar los parámetros del proceso y proporcionar un control de proceso de circuito cerrado.
Sin embargo, Sause reconoce que el enfoque de aprendizaje por transferencia adoptado en CosiMo, “es transferible hasta cierto punto a geometrías o sistemas de materiales similares y otras variaciones que no cambian completamente la situación. Por lo tanto, puede construir su base de datos de esa manera, con la posibilidad de identificar tendencias de eficiencia utilizando los datos ya adquiridos. Luego puede usar eso para otras preguntas que pueda tener al lado ".
Entonces, la forma de comenzar parece ser:¿comenzar a usar sensores y construir modelos digitales que combinen con los sensores para que pueda comprender su proceso? “Por supuesto”, dice Sause. “Y puedo asegurarles que la mayor parte de la maquinaria que se utiliza en la producción hoy en día sigue siendo muy estúpida. Muchas máquinas no tienen sensores que puedan brindarle las bases de datos para brindar retroalimentación sobre lo que está sucediendo. Entonces, sí, la integración de los sistemas de sensores sería el primer paso. Pero necesita hacer un sistemático adquisición de datos, y también proporcionar una arquitectura de almacenamiento de datos, para poder hacer algo con los datos . De hecho, ves muchas empresas que tienen sensores integrados, pero luego no hacen nada con los datos ".
Red de producción de IA
Para responder a las preguntas anteriores, Sause siguió recurriendo a varios grupos dentro de UNA, así como a empresas derivadas que pueden proporcionar integración de sensores y servicios de gemelos digitales. Con ese fin, UNA, DLR ZLP y Fraunhofer IGCV lanzaron la Red de producción de IA de Augsburgo en enero de 2021. “El marco de colaboración proviene de proyectos que hemos tenido con DLR y Fraunhofer en el pasado”, dice Sause. “Estamos tomando el modelo de desarrollo de producción basado en inteligencia artificial de CosiMo y ahora lo estamos extendiendo a una escala muy amplia. Así, por ejemplo, el presupuesto para nuestro trabajo en CosiMo fue de 10 millones de euros, pero para la Red de producción de IA es de 92 millones de euros como financiación inicial. Esto nos brindará la posibilidad de iniciar muchos proyectos de investigación nuevos como CosiMo en la explotación de la inteligencia artificial en la fabricación. Y no estamos trabajando solo en compuestos, sino que nos enfocamos mucho en ellos ".
El uso de sensores ultrasónicos para mejorar el mecanizado CNC es un proyecto que ya comenzó en 2021. “Hay un proyecto a punto de comenzar sobre el reciclaje de compuestos de matriz cerámica (CMC)”, dice Sause, “y tendremos varios proyectos con un vínculo estrecho entre fabricación aditiva y reutilización de materiales reforzados con fibras específicamente reciclados ”.
En cuanto a los roles que jugará cada organización, Sause explica que no hay competencia, ya que cada institución tiene un presupuesto asignado. “Todos tenemos nuestra parte y, por lo tanto, somos libres de colaborar como lo hemos hecho en el pasado. Además, nos conocemos bastante bien y conocemos nuestras competencias, fortalezas y debilidades. Es divertido trabajar juntos porque sabemos lo que podemos y no podemos hacer. Muchas empresas se han acercado a nosotros que quieren trabajar con nosotros y ahora estamos discutiendo cómo encontrar la combinación ideal de nuestro lado de competencias ”.
En cuanto a la instalación de producción de 5.000 metros cuadrados, “la haremos todos juntos”, dice Sause. “Planeamos abrir a principios de 2023 y comenzar a instalar máquinas. Y proporcionaremos configuraciones de producción automatizadas que unen las celdas individuales. Muchos de ellos se centrarán en tecnologías de producción de compuestos. Y lo haremos para mostrar y demostrar a los socios de la industria lo que la IA puede hacer en un entorno de producción de este tipo. También queremos tener socios de la industria que ingresen y también coloquen máquinas en nuestras instalaciones para que podamos ejecutar proyectos juntos para ver cómo vincular e integrar nuevas soluciones para sus sitios ”.
Resina
- Válvulas para control y cierre difíciles
- Sensores y sistemas para CBM
- Ingeniería del proceso de recubrimiento por inmersión y optimización del rendimiento para dispositivos electrocrómicos de tres estados
- OTOMcomposite desarrolla software para la producción de Composites 4.0 utilizando colocación de cinta asistida por láser y bobinado
- Resinas epoxi reprocesables, reparables y reciclables para composites
- Combinación de medidas dieléctricas de CA y CC para el control del curado de compuestos
- TPAC y TPRC desarrollan un proceso de reciclaje de compuestos termoplásticos
- Sugerencias para la configuración y el cableado de las carcasas del panel de control
- ¿Qué es el mecanizado ultrasónico? - Trabajo y proceso
- Conexiones para Control:Interfaces de Comunicaciones para Sensores de Posición y Movimiento
- Recopilar datos de campo para la optimización de procesos