Gear Manufacturing 101:Una guía sobre los procesos de producción de engranajes
El concepto de engranajes ha existido por un tiempo, ya que se encuentran entre los componentes mecánicos más antiguos que aún son relevantes en la actualidad. Ya sea la industria del automóvil, el sector aeroespacial, cualquier maquinaria industrial, o algo tan simple como un reloj. Los engranajes son necesarios en todas partes y tal vez le gustaría aprender sobre la fabricación de engranajes.
Entonces, la pregunta es cómo se fabrican los engranajes.
Prefacio:Proceso de fabricación de engranajes
No existe un proceso único para la fabricación de engranajes, ya que requieren procesos diferentes según el tipo y la aplicación.
En general, los engranajes funcionan en condiciones muy exigentes porque la transmisión de potencia (el propósito real del engranaje) tiene varios requisitos. En primer lugar, los engranajes deben estar en perfectas condiciones. Entonces, siempre deben ser confiables, tener tensiones residuales mínimas y poca o ninguna posibilidad de propagación de grietas.
Naturalmente, todos estos requisitos son extremadamente difíciles de cumplir. Sin embargo, nadie puede negar su importancia. Es por eso que la producción de engranajes es un campo altamente especializado con tolerancias limitadas y margen de error.
Este artículo lo llevará de regreso a los conceptos básicos de la fabricación de engranajes relacionados con los materiales comunes para los engranajes industriales, los procesos que los preparan y cómo los engranajes pueden soportar toda esa carga sin fallar.
Tipos comunes de engranajes y sus aplicaciones
Antes de pasar a los detalles sobre el corte de engranajes y los procesos de fabricación, es importante echar un vistazo a los conceptos básicos. Son diferentes tipos de engranajes y su aplicación y ventajas.
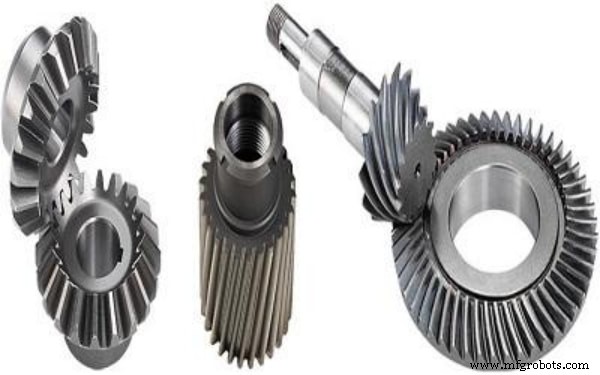
Su aplicación, parámetro de rendimiento y muchos otros factores juegan un papel importante en el tipo de engranajes que utiliza. Hay varias formas de caracterizar el tipo de engranaje, pero la mejor y más relevante desde la perspectiva de la fabricación de engranajes es a través del perfil de sus dientes.
Estos son los 5 tipos de engranajes que encontrarás.
Engranajes rectos
Haz un dibujo aproximado de cómo se ve el equipo en tu mente. Hay muchas posibilidades de que esté pensando en engranajes con dientes rectos. Así es exactamente como se ve un engranaje recto.
El engranaje recto es el tipo de engranaje más común y tiene múltiples aplicaciones en centrales eléctricas, componentes aeroespaciales, máquinas industriales y mucho más. Los dientes rectos son los más simples de fabricar y soportan altas velocidades y cargas. Sin embargo, producen mucho ruido y no son adecuados para aplicaciones en las que también se necesitan operaciones fluidas.
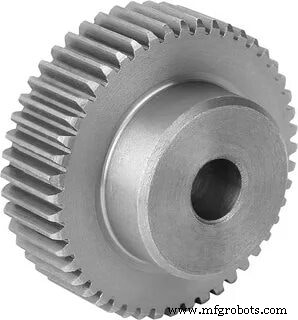
Además, los engranajes rectos pueden acoplarse con otros engranajes del mismo tipo y engranajes internos/externos. Encontrará engranajes rectos en muchos mecanismos de engranajes, como una configuración simple de cremallera/piñón o un sistema de engranajes planetarios.
Su simplicidad significa que es más fácil de hacer para ti. Por lo tanto, le resultará más fácil mantener la precisión durante la producción de engranajes. Los engranajes rectos también tienen poca o ninguna carga axial, por lo que son bastante eficientes para un tren de engranajes en el que desea minimizar las pérdidas mecánicas.
Engranajes helicoidales
Los engranajes helicoidales son bastante similares a los engranajes rectos, pero vienen con dientes que se enroscan alrededor de un cuerpo cilíndrico. Esta cualidad les permite trabajar fácilmente con ejes paralelos y no paralelos. Su acoplamiento, sin embargo, solo funciona con otros engranajes helicoidales del mismo ángulo de hélice (el ángulo de giro del cilindro original).
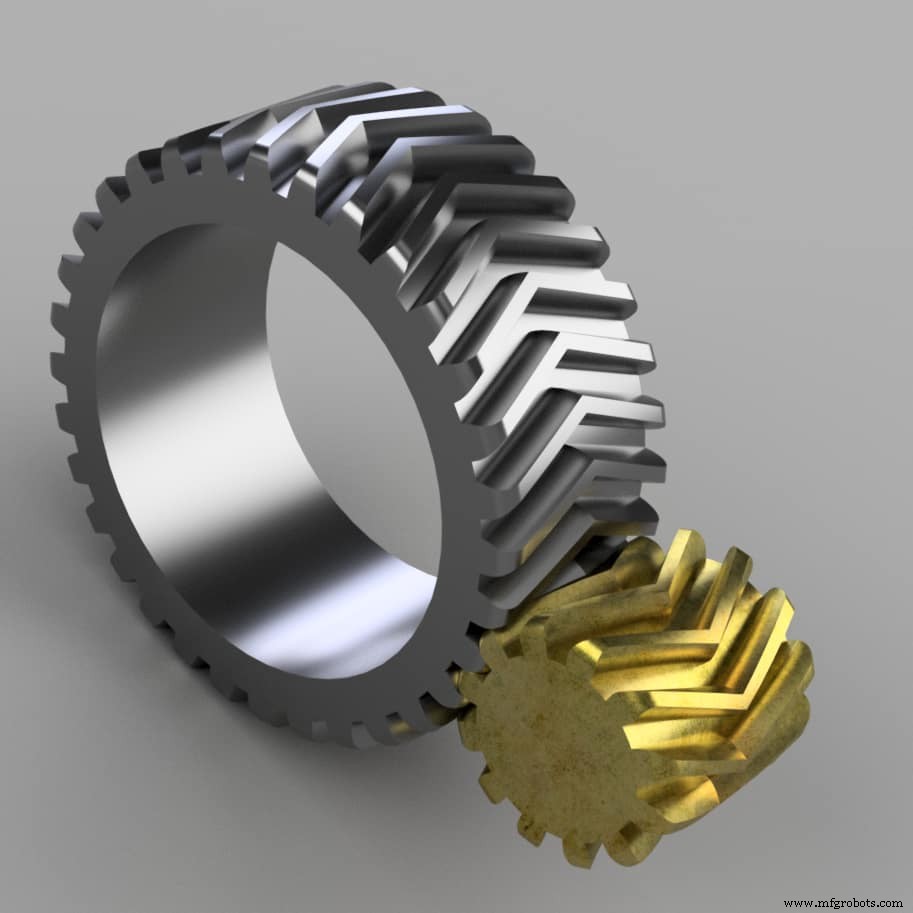
La mayoría de las aplicaciones de los engranajes helicoidales son las mismas que las de los engranajes rectos. Sin embargo, los dientes angulados juegan un papel muy importante en la reducción de la carga de impacto y hacen que las operaciones sean más fluidas. Esto también significa menos ruido, pero a costa de la eficiencia. En relación con los engranajes rectos, un tren de engranajes helicoidales tendrá más pérdidas y también necesitará cojinetes de empuje debido a la forma.
Desde una perspectiva de fabricación, los engranajes helicoidales son más resistentes que los engranajes rectos. Los ángulos de hélice son bastante difíciles de replicar con un rango de tolerancia aceptable bajo. Además, los costos de fabricación y luego la adición de otros elementos axiales los hacen adecuados para operaciones limitadas.
Engranajes cónicos
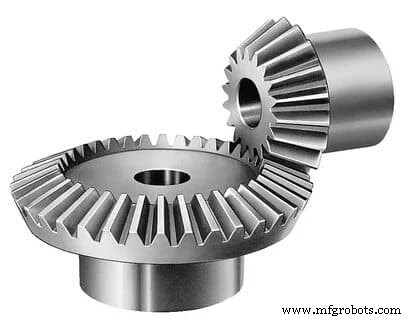
Los engranajes cónicos no son sus engranajes cilíndricos estándar. Vienen en una superficie cónica que le permite cambiar la dirección de la transmisión en ejes que se cruzan. Generalmente, los engranajes cónicos funcionan con 90 0 anglos. Sin embargo, también puede usarlos en otras configuraciones.
Estos son algunos tipos comunes de engranajes cónicos que puede encontrar en una variedad de aplicaciones.
- Engranajes cónicos rectos
- Engranajes cónicos en espiral
- Engranajes de inglete
- Engranajes de corona
- Engranajes hipoides
Engranajes helicoidales
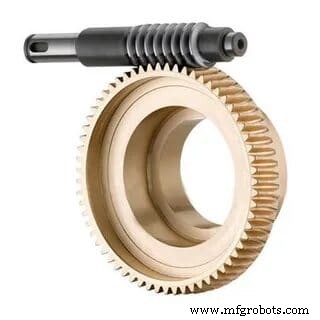
El sistema de engranaje helicoidal es una combinación de dos componentes. Una rueda helicoidal y un engranaje en forma de tornillo. Se utilizan predominantemente en la industria aeroespacial, máquinas industriales, ascensores y dirección de automóviles.
La configuración de la rueda helicoidal no ofrece mucha velocidad o eficiencia. Sin embargo, ofrece una característica única requerida para los mecanismos de autobloqueo. En muchos casos, el tornillo sin fin puede girar la rueda, pero no puede ocurrir lo contrario debido a los ángulos de los engranajes. Además, otra cosa importante a tener en cuenta es que los engranajes de rueda helicoidal tienen mucha fricción y pueden requerir una fricción continua para funcionar correctamente.
Piñón y cremallera
El sistema de piñón y cremallera es otra combinación que funciona principalmente para transferir el movimiento de rotación a lineal y viceversa. Los dientes del engranaje pueden acoplarse tanto con dientes rectos como helicoidales, por lo que puede trabajar tanto en ejes paralelos como en ángulo. Algunas de las aplicaciones más comunes de este sistema se encuentran en sistemas de automóviles, básculas y otros sistemas similares.
Materiales utilizados para producir engranajes
No hay restricción material cuando se trata de engranajes. Los primeros eran de madera, y puedes encontrar engranajes de diferentes materiales en toda la industria. Desde engranajes de acero o hierro a gran escala industrial hasta pequeños engranajes de plástico en juguetes. Las combinaciones de materiales son infinitas.
No obstante, los siguientes elementos son los más utilizados en los procesos de fabricación y formación de engranajes:
- Hierro fundido
- Acero
- Bronce
- Plásticos
Los engranajes tienen criterios muy específicos para la selección de materiales. Dependiendo de la aplicación, cualquier material que elija debe tener la resistencia y la resistencia a la tracción adecuadas.
Además, el coeficiente de fricción es otra consideración porque los engranajes necesitan un contacto constante. Finalmente, también debe seleccionar materiales que sean fáciles de procesar. Será más difícil trabajar con un material resistente con baja capacidad de fabricación porque la fabricación de engranajes requiere una precisión y exactitud extremas.
Los materiales antes mencionados vienen con el equilibrio perfecto de estas propiedades para sus aplicaciones. Es por eso que comúnmente los verás en la mayoría de los engranajes que encuentres.
RapidDirect puede ofrecer todos estos materiales utilizados en el proceso de fabricación de engranajes. Cargue su archivo de diseño para obtener una cotización para su proyecto de equipo.
Procesos comunes de fabricación de engranajes
La producción de engranajes es bastante complicada debido a la precisión que exige. Hoy en día, la fabricación de engranajes es una industria en sí misma que se basa en múltiples procesos, tanto tradicionales como modernos, para garantizar el equilibrio adecuado entre costo, calidad y operaciones.
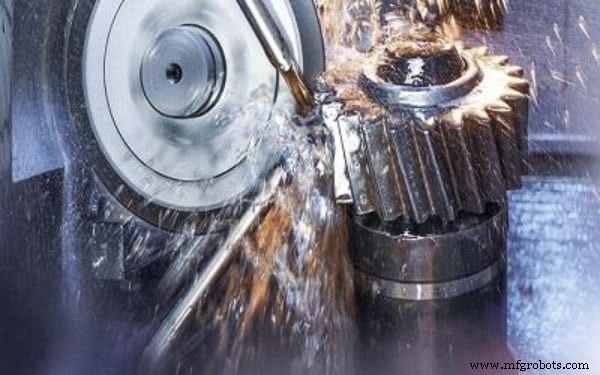
Aquí hay una lista de procesos comunes de corte y fabricación de engranajes junto con sus aparentes ventajas y desventajas.
1 – Reparto
La fundición es un proceso más simple que se utiliza predominantemente para preparar espacios en blanco o cilindros para engranajes, mientras que los dientes se preparan mediante mecanizado. Sin embargo, es un proceso de fabricación de engranajes viable para muchas aplicaciones debido a su capacidad de producción en masa y relativa facilidad.
Sin embargo, existe un área en la que la fundición es el método de fabricación más preferido en la industria. Esa es la producción de engranajes muy grandes. Los métodos de mecanizado y otros métodos de formación de engranajes no son tan viables en casos de grandes diámetros. En general, los engranajes más grandes son casi siempre del tipo de engranajes rectos. Por lo tanto, su relativa simplicidad hace que el casting sea una muy buena opción.
Entre los tipos más comunes de métodos de fundición, la fundición en coraza, la fundición a presión, la fundición en arena y la fundición en molde permanente son las más comunes para la producción de engranajes. Otros métodos tienen un uso limitado en algunas aplicaciones. Sin embargo, los mencionados son los más comunes en la industria.
2 – Forja
Este es otro proceso de formación que puede brindarle piezas en bruto y engranajes preparados según sus requisitos. La forja es bastante viable en los casos en los que tiene engranajes relativamente simples.
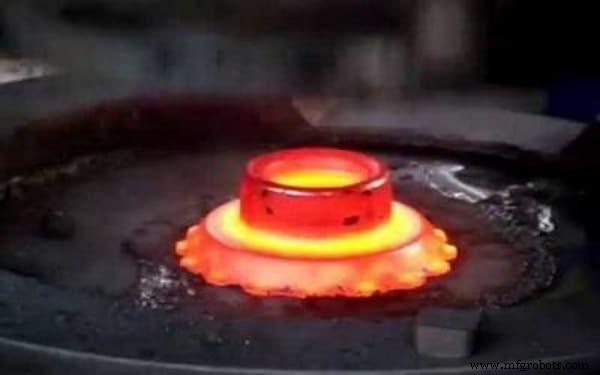
Teóricamente, la forja es un excelente proceso de fabricación de engranajes para aplicaciones de servicio pesado por una sencilla razón. La forja requiere un tratamiento térmico, lo que significa que el engranaje resultante tendría mejores propiedades de fatiga. Sin embargo, la tremenda fuerza requerida para el proceso de forjado limita el tamaño y la delgadez de este proceso.
En general, la forja funciona bien para engranajes de 6 a 10 pies de diámetro. Dependiendo del tipo de forja, por ejemplo, forja de precisión, es posible que necesite o no mecanizar los engranajes al final.
3 – Extrusión y estirado en frío
Este es otro proceso de formación de engranajes que es a la vez versátil y más simple. De hecho, la extrusión tiene un menor gasto de herramientas, pero eso no significa que sea el proceso más económico.
La extrusión, como su nombre indica, es el proceso de pasar un perfil de metal calentado a través de una forma predeterminada más pequeña. Como resultado, obtienes una barra de la forma deseada con una superficie exterior endurecida y lisa.
El proceso de estirado en frío es muy similar a la extrusión. Hay dos diferencias. La extrusión empuja la pieza en bruto a través de un troquel que tira de ella. La otra diferencia es la temperatura. El estirado en frío no calienta la palanquilla. Aumentando así las propiedades mecánicas a expensas del costo.
4 – Pulvimetalurgia
La pulvimetalurgia es un proceso avanzado que logró avances significativos en los últimos años. Hoy en día, se utiliza para múltiples procesos de fabricación, incluida la producción de engranajes.
Entonces, ¿cómo funciona la pulvimetalurgia? Desde el punto de vista, es bastante simple. Sin embargo, hay muchas complejidades involucradas.
Todo comienza con polvo de metal. El primer paso es tomar todo el polvo y darle la forma final que desee. Una vez que haya terminado, el siguiente paso garantiza que toda la configuración sea bastante compacta, ya que dará como resultado mejores propiedades mecánicas. Calienta todo el montaje con cuidado y listo.
La pulvimetalurgia es extremadamente eficiente, simple y viable para grandes cantidades. No tiene que preocuparse por ningún procesamiento posterior y el producto estará listo para usar. Sin embargo, los engranajes resultantes no pueden soportar demasiada carga y también existen limitaciones de tamaño.
Además, el costo inicial de cualquier configuración de pulvimetalurgia es bastante alto, lo que lo hace inviable para cualquier producción de bajo volumen.
5 – Supresión
El corte en blanco es un proceso muy similar a la extrusión, pero tiene capacidades tridimensionales limitadas. Este proceso de formación de engranajes utiliza láminas de metal para crear la forma deseada con la ayuda de múltiples troqueles. Puede producir diferentes tipos de engranajes con el proceso de corte. Sin embargo, los engranajes rectos le brindan los mejores resultados.
Hoy en día, múltiples industrias utilizan el proceso de corte en la producción de engranajes para aplicaciones livianas. Por ejemplo, equipos de oficina, hidráulica, dispositivos médicos pequeños y otras aplicaciones con requisitos de carga bajos.
6 – Mecanizado de engranajes
El mecanizado es uno de los procesos de fabricación de engranajes más comunes debido a su versatilidad. El mecanizado tradicional era bastante común para el corte y la fabricación de engranajes, pero los avances del mecanizado CNC han impulsado su popularidad.
Los siguientes 4 métodos de corte de engranajes son los más comunes en la industria.
Fresado
El tallado utiliza un dispositivo de corte cónico llamado placa. Tanto la encimera como la pieza de trabajo giran cuando la encimera gira alrededor del engranaje en bruto. Hasta ahora, los engranajes helicoidales y rectos externos son los únicos productos que puede crear a partir del tallado.
El proceso es bastante versátil y rápido. También puede aumentar sus tasas de producción procesando varias pilas juntas. Sin embargo, requiere más habilidad y precisión.
Dar forma
El moldeado es un proceso avanzado de corte y fabricación de engranajes que desarrolla engranajes que Hobbing no puede manejar. El cortador puede tener cualquier forma, como un piñón, una cremallera o una sola punta. Se ve bastante similar a los engranajes y funciona cortando el espacio en blanco en la forma requerida. Puede crear engranajes internos o de grupo con el proceso de modelado.
Brochado
El brochado es quizás el método más rápido de corte de engranajes. Se basa en una herramienta de dientes múltiples con cortadores integrados que son más profundos que su predecesor. Esto da como resultado cortes incrementales más pequeños que son más fáciles de realizar y le brindan rápidamente la forma requerida sin comprometer la precisión.
Este proceso de fabricación de engranajes es típico de los engranajes internos, pero también puede usarlo para hacer dientes externos. Para eso, necesitará una herramienta especializada para brochado de ollas que le permita replicar con la misma precisión y eficiencia.
Fresado
Este es un método básico de corte de engranajes en el que produce dientes de engranajes individuales secuencialmente. Sin embargo, es bastante versátil, especialmente cuando se trata de una fresadora CNC. Si bien puede fabricar cualquier tipo de engranaje en una fresadora, la precisión de este método deja mucho que desear. Es por eso que el fresado no es tan común como lo era antes.
Sin embargo, los desarrollos recientes en el dominio CNC y multieje han cambiado las cosas. La fabricación de engranajes en fresadoras es cada vez más común. Entonces, las cosas mejorarán aún más con el tiempo.
Posprocesamiento de fabricación de engranajes
Según el método de fabricación de engranajes que haya utilizado, sus engranajes necesitarán un procesamiento posterior antes de que estén 100 % listos. Ese posprocesamiento puede variar desde el tratamiento térmico para mejorar las características de fatiga hasta la corrección dimensional y el acabado superficial.
Estos son los 5 procesos de acabado de superficies más comunes en la producción de engranajes.
- Molido: Tal como lo sugiere su nombre, el esmerilado es un proceso común de acabado de superficies que le brinda un acabado uniforme en toda la superficie. Puede realizarlo de forma intermitente o continua, y no afectará los resultados.
- Lapeado: Este proceso es para engranajes sensibles donde se necesita una precisión extrema. El lapeado utiliza pequeñas partículas abrasivas para alisar una superficie a velocidades bajas o medias.
- Afilado: Este es otro proceso común que pule la superficie y la suaviza. Además, también puede corregir algunos errores menores en la geometría de sus dientes.
- Afeitado: Este proceso elimina capas extremadamente finas de la superficie para lograr un perfil suave. El afeitado suele ser costoso, por lo que rara vez se usa en la producción de engranajes.
- Bruñido: En esencia, el pulido es el proceso de utilizar la compresión para alisar la superficie.
Acérquese a RapidDirect para obtener los mejores servicios de fabricación de engranajes
La fabricación de engranajes es un campo altamente especializado que requiere extrema precisión y exactitud. Los engranajes son un componente esencial para cualquier sistema mecánico e incluso el defecto de fabricación más pequeño puede tener muchas consecuencias desastrosas. Por lo tanto, debe tener cuidado con el servicio que seleccione.
RapidDirect es un servicio certificado por ISO con el equipo más experimentado que ofrece el mejor rendimiento al precio más competitivo. Ofrecemos servicios de vanguardia que le brindan lo mejor en lo que respecta a la fabricación de engranajes.
Desde engranajes grandes para maquinaria industrial hasta los componentes más pequeños para cualquier aplicación de nicho, RapidDirect ofrece la combinación adecuada de habilidades, experiencia y calidad que necesita. Contáctenos hoy y obtenga una cotización inicial en unas pocas horas.
máquina CNC
- Fabricación vs producción:en qué se diferencian estos procesos
- Unir o formar procesos de fabricación:¿Cuál es la diferencia?
- La robótica y el futuro de la producción y el trabajo
- La importancia del mantenimiento de equipos en la fabricación
- ¿Cuáles son los procesos de fabricación importantes que se siguen en diferentes industrias? – Yo
- ¿Cuáles son los procesos de fabricación importantes que se siguen en diferentes industrias?
- 3 procesos de acabado innovadores utilizados en la fabricación de engranajes
- El uso creciente de la automatización en la fabricación
- El impacto de la fabricación aditiva en la producción industrial
- El auge de la robótica avanzada en la fabricación industrial
- Una descripción general de la importancia de los procesos de mecanizado CNC en la fabricación