Software, interfaz CNC gana productividad de programación push
Los controles rápidos e inteligentes simplifican las tareas complejas.
Las tecnologías de fabricación y digitalización conectadas están impulsando muchas de las principales innovaciones en los controles de máquinas CNC que ayudan a los talleres de mecanizado a cortar metal y crear piezas de la manera más rápida y eficiente posible. En la mayoría de los casos, el software lidera el camino para ayudar tanto a los programadores CNC como a los operadores en el taller a fabricar fácilmente piezas con la mayor precisión posible.
Los equipos CNC de hoy en día están virtualmente repletos de los últimos avances de hardware, incluidos procesadores más rápidos, más RAM integrada para tareas informáticas intensivas, además de nuevas opciones de unidades de estado sólido que permiten tiempos de arranque casi inmediatos, así como un funcionamiento sin preocupaciones en entornos de taller difíciles.
Sin embargo, los avances de software más recientes, con características que incluyen aplicaciones de fabricación conectadas, simulaciones 3D avanzadas e interfaces de usuario táctiles, continúan brindando a los constructores de CNC las mejores vías para diferenciarse del resto.
“El software de control es realmente el único lugar para que los fabricantes de máquinas herramienta introduzcan innovaciones revolucionarias”, dijo Michael Cope, especialista técnico de productos, Hurco Cos. Inc., Indianápolis. “Dado que las soluciones mecánicas nuevas e innovadoras son pocas y espaciadas, especialmente sin la introducción de alguna nueva tecnología metalúrgica o similar, ofrecer software de vanguardia y cambios en la interfaz gráfica de usuario que hacen que los controles CNC sean más potentes, más versátiles y más fáciles de usar tiene ser el área donde cada constructor se diferencie de la competencia”.
¿Podemos hablar?
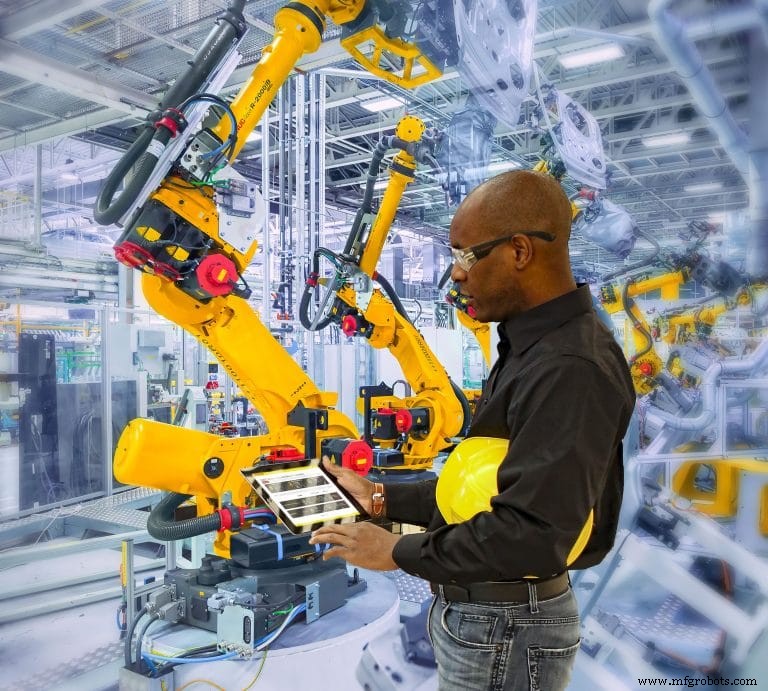
A medida que la industria manufacturera experimenta su transformación de digitalización, los desarrolladores de control CNC y los fabricantes de máquinas herramienta continúan agregando nuevas características y funcionalidades con los últimos sensores, procesadores y software. En IMTS, los desarrolladores de control FANUC y Siemens, en particular, exhibieron nuevos equipos y estrategias para conectar sus controles y automatización para el Internet industrial de las cosas (IIoT) y habilitar la Industria 4.0.
En el stand IMTS de FANUC America Corp., con sede en Rochester Hills, Michigan, la compañía demostró sus últimas tecnologías IIoT, incluido el sistema de monitoreo y recopilación de datos Intelligent Edge Link and Drive (FIELD) de FANUC y su tiempo de inactividad cero en ROBOT-LINKi (ZDT), que utiliza análisis predictivos para ayudar a evitar el tiempo de inactividad debido a fallas inesperadas.
FANUC también mostró nuevas funciones de CNC, que incluyen simulación de mecanizado de modelo 3D de alta resolución mejorada para funciones de mecanizado compuesto y de cinco ejes; su última Serie 0i-Modelo F Plus, la próxima generación de sus controles Serie 0i; y su función Quick and Simple Startup of Robotization (QSSR) para vincular los CNC de FANUC con los robots de la empresa. Además, FANUC ha agregado capacidades de visión integradas directamente en sus CNC.
“Estamos viendo un gran impulso hacia el uso de sistemas de visión incorporados en los CNC”, dijo Paul Webster, gerente de ingeniería de la unidad de CNC con sede en Hoffman Estates, Illinois, de FANUC America. “Esto recién se está lanzando; la tecnología de hardware es la misma que en el lado del robot, pero se implementa de manera diferente”. El sistema, que utiliza un software diferente al de los sistemas de visión utilizados en los robots FANUC, "permite una implementación flexible de la visión a través del CNC", dijo Webster.
La última tendencia de conectar máquinas herramienta CNC entre sí puede ofrecer a los fabricantes una mayor productividad y una calidad más confiable, señaló Tiansu Jing, gerente de productos CNC de Sinumerik para la Unidad de Negocios de Máquinas Herramientas de Siemens con sede en Elk Grove Village, Illinois. “Siemens ofrece innovaciones técnicas variables para todas las áreas de fabricación, incluidas las principales, como la aeroespacial y la automotriz”, dijo. “Las innovaciones no solo se centran en mejorar la velocidad de ingeniería de los fabricantes de máquinas mediante la introducción de un nuevo y potente portal TIA y Safety Integrated Plus, sino también el 'arte' de los productos de digitalización de datos, que ofrecen a los clientes finales formas de conectarse, monitorear, analizar y optimizar sus máquinas.
"Fabricación inteligente/Industria 4.0, que también se denomina 'digitalización', es lo que cambia las reglas del juego en la fabricación", continuó Jing. “Al conectar las máquinas, surgen muchas posibilidades nuevas, así como nuevos modelos comerciales. Para ofrecer un mejor servicio a sus clientes, los fabricantes necesitan aumentar su productividad y calidad para ofrecer mejores productos en plazos de entrega más cortos. Del mismo modo, para fortalecer su posición competitiva en el mercado, las empresas necesitan acortar el tiempo que les lleva diseñar nuevos productos”.
Los maquinistas siempre buscan hacer que las operaciones de corte sean más fáciles y rápidas, agregó Jing. “Para diferentes tipos de máquinas, necesitan diferentes características para lograr este objetivo, p. 'Superficie superior' para moldear y troquelar para una mejor calidad de la superficie en menos tiempo, y 'Administrador de herramientas' para administrar fácilmente todas las herramientas para reducir el tiempo de inactividad de la máquina debido a la rotura de la herramienta, etc.”, dijo.
El software Los elementos de los controles CNC han permitido agregar fácilmente macros y rutinas especializadas que aumentan la productividad tanto en los grandes fabricantes como en las operaciones de talleres más pequeños.
"Los fabricantes buscan una mayor productividad y una mejor calidad todo el tiempo", señaló Jing.
“Limitado por el material de la herramienta y la mecánica de la máquina, es difícil acortar drásticamente la velocidad de corte, por lo que el nuevo potencial para aumentar la productividad es mediante una mejor gestión de la cadena de valor de producción completa, incluida la distribución de tareas a diferentes máquinas, disposición optimizada de herramientas, simulación antes del corte real para verificar el diseño y análisis en línea de los componentes de la máquina, incluidas las herramientas, etc.
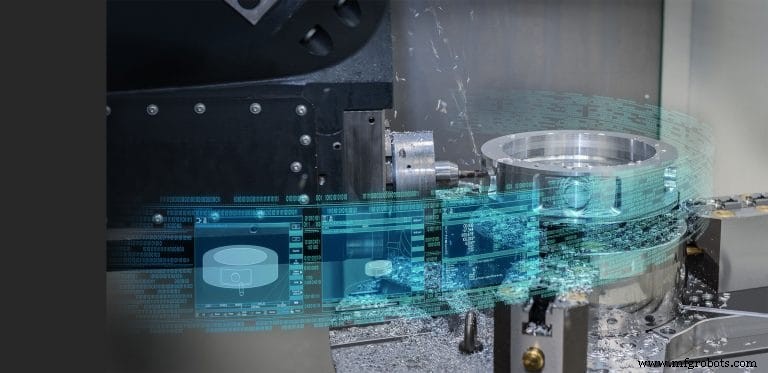
“Siemens ofrece líneas completas de productos para ayudar a los grandes y pequeños fabricantes a configurar su gemelo virtual y analizar su producción para optimizar la producción desde el diseño del producto hasta la entrega”, continuó Jing. El software de Siemens incluye Manage MyMachine, Analyze MyPerformance, Analyze ToolPath y Run MyVNCK para verificar el diseño, optimizar el programa de piezas, simular el corte y mantener las máquinas funcionando a niveles óptimos de rendimiento, agregó.
Al conectar las máquinas con Industry 4.0 y Smart Manufacturing, la industria puede cambiar el juego y cerrar la brecha de habilidades que existe en la fabricación hoy en día, según Cope de Hurco. “Estos nuevos estándares brindan la capacidad de hacer que las máquinas y los controles interactúen entre sí y hacer que las máquinas se conviertan en 'ayudantes' dentro de una gran celda de fabricación, donde un trabajo o programa en particular puede enviarse a la siguiente máquina herramienta disponible y no depender de un disponibilidad de una máquina en particular. También pueden enviar comentarios sobre el trabajo o la máquina a destinatarios específicos de correo electrónico o mensaje de texto.
“Tener el poder y la versatilidad de trabajar con la automatización será cada vez más valioso para los talleres de todos los tamaños en los próximos años”, continuó Cope. "Debido a la menor cantidad de empleados, las tiendas más pequeñas posiblemente se beneficien de esta tecnología incluso más que las tiendas más grandes porque les permite aprovechar más horas del día, incluso sin tener un segundo y tercer turno extendido".
En su stand de IMTS, Hurco presentó la automatización con robots colaborativos, robots seriales multieje y sistemas de tarimas que demostraron la automatización para la producción de piezas de bajo volumen y mezcla alta que se encuentra en muchos talleres, dijo Cope, señalando que la exhibición de automatización fue un esfuerzo colaborativo. entre Hurco y Erowa, Universal Robots, FANUC, Online Resources y Industrial Controls &Automation.
“Hurco ha dedicado amplios recursos de ingeniería para inventar nuestro sistema patentado de control de movimiento impulsado por software, llamado UltiMotion”, dijo Cope. “Con UltiMotion, grandes cantidades de memoria y visualización anticipada de bloques NC (todas las funciones estándar en nuestro control), todas las industrias se benefician, pero será especialmente beneficioso para nuestros fabricantes de moldes y talleres aeroespaciales. La velocidad combinada, el rendimiento y la capacidad de respuesta del eje ayudarán a garantizar que el cliente produzca las mejores piezas posibles, con tiempos de ciclo más cortos y acabados superficiales sobresalientes”.
Configuraciones individuales, simulación premiada
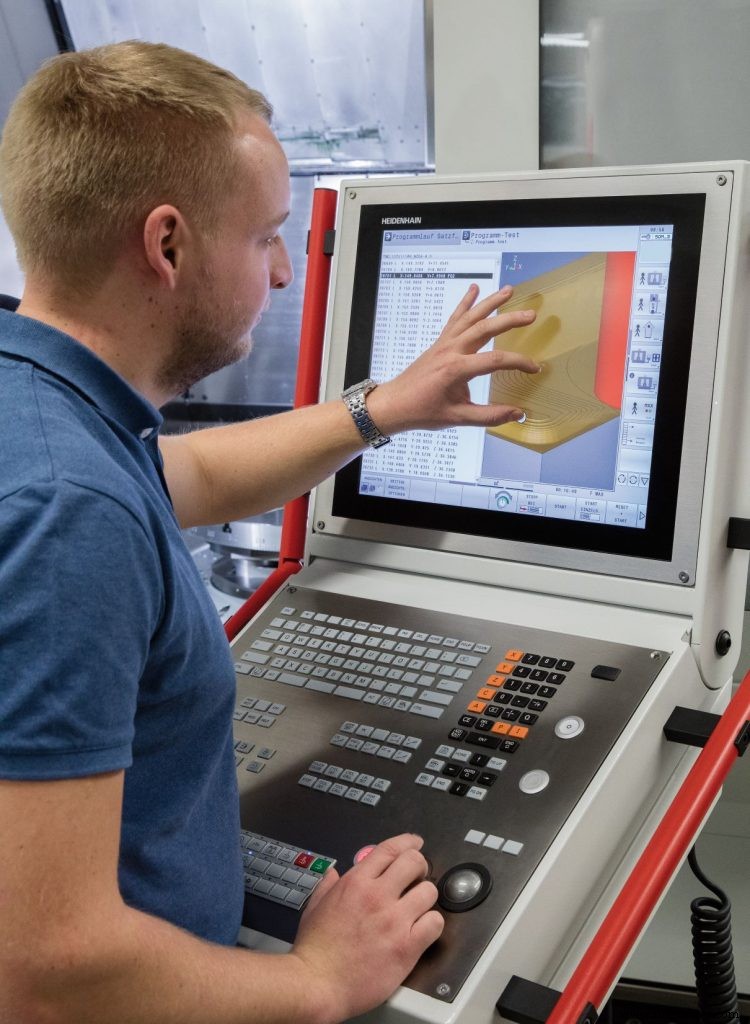
Trabajar de manera más eficiente con configuraciones individuales en máquinas multieje es una tendencia en los CNC hoy en día, señaló Gisbert Ledvon, gerente de desarrollo comercial de TNC, Heidenhain Corp., Schaumburg, Illinois. “La gente quiere hacer más en una máquina si puede, por lo que obviamente cinco ejes han recorrido un largo camino, no solo para cinco ejes completos, sino cada vez más para 3+2 [mecanizado] porque la gente necesita seguir siendo competitiva”, dijo Ledvon. . “Si siguen haciendo lo que están haciendo, no serán competitivos”.
Si bien parte del trabajo de mecanizado está regresando a los EE. UU., el mecanizado más fácil no lo está, agregó.
“Lo complejo está volviendo. Hay una tendencia de personas que quieren hacer más en una máquina herramienta, por lo que son cinco ejes o quieren hacer una aplicación de fresado/torneado en una máquina fresadora. Quieren comenzar con la automatización un poco más, por lo que quieren una funcionalidad fácil en su control para administrar tal vez un simple cambiador de tarimas y establecer prioridades a partir de eso”.
Las operaciones de mecanizado para biselado y corte de engranajes complejos han regresado, con la ayuda de un software más nuevo en el control TNC de Heidenhain, agregó. Las operaciones de mecanizado complejas requieren un modelado 3D de alta precisión en un software de simulación como el que Heidenhain ha añadido recientemente a la caja de herramientas del TNC, incluida su supervisión dinámica de colisiones.
“Aunque puede tener monitoreo de colisiones en el exterior, como con un programa CAM o Vericut, por ejemplo, que verifica su programa para que no tenga colisiones, las personas también quieren hacer eso en la máquina [control], si pueden”, Ledvon dijo. “Si la máquina puede mostrarles visualmente si tienen un problema de colisión, quieren ver el modelo 3D de la cinemática de la máquina y simplemente verificar que si están haciendo la programación, todavía quieren esa verificación en el máquina.”
La simulación de piezas en el control CNC se está volviendo más común, con nuevas simulaciones basadas en CNC introducidas en IMTS por FANUC y otros. La simulación de FANUC ofrece una simulación de piezas en 3D completa, señaló Webster, que muestra el cuerpo sólido de la pieza mientras se somete a operaciones de mecanizado.
El uso de modelos sólidos también está creciendo dentro de las ofertas de los desarrolladores de CNC, señaló Cope de Hurco. “Una tendencia que algunos controles están comenzando a adoptar, y que ciertamente veremos crecer, es la capacidad de importar modelos sólidos directamente al control y crear programas a partir de ellos. Aunque hemos podido importar archivos STL para usarlos como geometría de stock durante varios años, Hurco presentó una nueva característica, Importación 3D con DXF 3D mejorado en IMTS 2018, que fue muy bien recibida por los asistentes a la feria”, agregó Cope. “Dado que muchos usuarios reciben archivos de modelos sólidos de sus clientes, es un beneficio significativo poder simplemente cargar ese archivo en el control y crear un programa de pieza sin necesidad de un sistema CAM”.
Lo que más importa a los maquinistas

La facilidad de uso ocupa un lugar muy alto en las listas de deseos de la mayoría de los maquinistas, y los desarrolladores de CNC están haciendo un progreso constante en esta área, con FANUC renovando su interfaz de usuario en los últimos años y muchos otros desarrolladores incluyen interfaces de pantalla táctil más fáciles de usar.
“Quieren velocidad, no quieren esperar y quieren precisión”, dijo Robin Cave, ingeniero de software de Mazak Corp. con sede en Florence, Ky. “Los gráficos en nuestra máquina con Windows son muy buenos y ayudan a los maquinistas a verificar el código antes de cortar comienza con una simulación bastante buena que
muestra todo”.
La línea Mazatrol Smooth de CNC de Mazak, que incluye SmoothX, SmoothG y SmoothC, fue renovada por Mazak en Japón hace unos tres años utilizando hardware de Mitsubishi e incorporando el sistema operativo integrado Windows 8. Estos CNC ofrecen una operación intuitiva para los usuarios con pantallas táctiles que permiten ajustar el proceso de una pieza, señaló Cave, mediante el uso de barras deslizantes y otras entradas gráficas.
“Es un control increíblemente rápido”, dijo Cave of the Smooth CNCs, señalando que Georgia Tech ha probado los controles. “Procesa más rápido que cualquier cosa que hayamos hecho antes, y las unidades de estado sólido realmente ayudan con la velocidad. No siempre se necesita mucha velocidad, pero cuando se interpola una fresa de punta esférica, se necesita comer mucho código rápidamente”, dijo Cave. “Te encuentras con ese tipo de cosas más en el trabajo aeroespacial y de moldes.
“Otra cosa realmente importante para nuestros clientes es nuestro SMC, nuestra configuración suave de la máquina”, continuó Cave. “Lo que querían los clientes era que nuestras máquinas fueran más flexibles. A veces necesitan ser realmente precisos, a veces no”. El SMC permite a los maquinistas ajustar fácilmente los controles deslizantes para hacer que la máquina sea más o menos precisa según lo requieran las condiciones de mecanizado, señaló, lo que ayuda a facilitar las tareas de programación en la máquina.
Plataforma única para todo
La versatilidad del mecanizado es una tendencia clave para los usuarios de CNC en la actualidad, señaló Todd Drane, gerente de marketing de Fagor Automation-USA, Elk Grove Village, Illinois. “Los fabricantes quieren una única plataforma CNC que pueda abordar cualquier aplicación que tengan en la planta de fabricación”, dijo Drane, señalando que esto permite un mejor intercambio de personal de taller. “Una vez que aprenden una plataforma CNC, la integración a un nuevo proceso para esa persona es mucho más fácil si la plataforma operativa sigue siendo la misma con el nuevo proceso”.
Entre sus últimos desarrollos, la plataforma CNC 8065 de Fagor ha sido diseñada con características avanzadas patentadas necesarias para el mecanizado de alta velocidad, manteniendo el mejor acabado superficial de mecanizado y la máxima precisión, dijo Drane. La función Adaptative Real-Time Feed and Speed (ARFS) de Fagor permite que el CNC analice las condiciones de mecanizado, como la carga del husillo, la potencia del servo y la temperatura de la punta de la herramienta, y adapta tanto la velocidad de avance del eje como la velocidad del husillo para obtener la máxima productividad en el rendimiento del mecanizado, añadió Drane. . “El resultado es una reducción del tiempo de ciclo, junto con un acabado superior de la pieza. También se logra una mayor vida útil del husillo y del servomotor, así como una mejor utilización de la herramienta”.
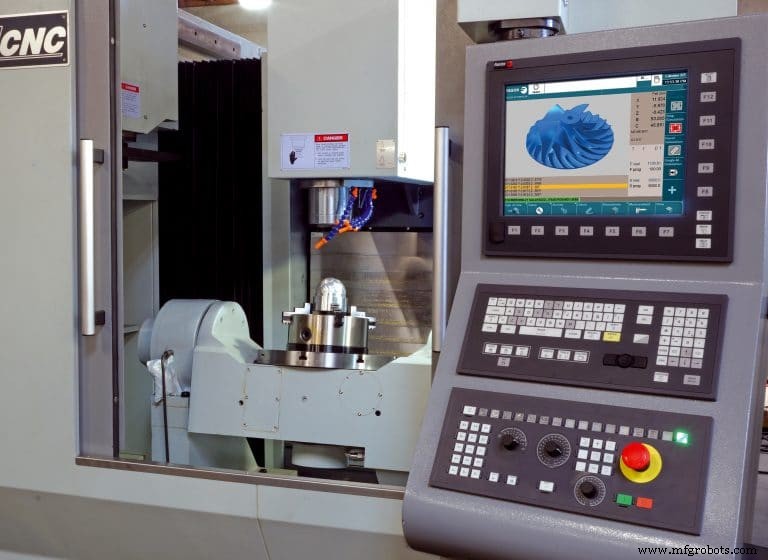
El CNC Fagor 8065 también está equipado con la funcionalidad de mecanizado High Speed Surface Accuracy (HSSA) específica para la industria aeroespacial que ofrece una tensión mecánica reducida en la máquina, lo que aumenta la vida útil de la máquina herramienta. Además, debido a la menor vibración de la máquina, la máquina es capaz de un movimiento más suave y velocidades de avance más altas, dijo Drane. “Además, la herramienta de diagrama de Bode incorporada permite la medición de la respuesta de frecuencia de la máquina, lo que permite filtrar las vibraciones de la máquina producidas por las distintas condiciones y entornos operativos”.
Fagor también cuenta con su aplicación Fagor Machining Calculator (FMC), que está disponible en las plataformas CNC 8060 y 8065. La función consta de una base de datos de materiales a mecanizar y operaciones de mecanizado (fresado y torneado) y una interfaz para elegir las condiciones de corte adecuadas (avance de mecanizado de ejes y velocidad del cabezal para cada operación). Otro avance en los CNC de Fagor es el diseño de hardware compacto de la línea de control, dijo Drane. “En la fabricación actual, como dijo un cliente, el espacio es dinero”, señaló. “Por lo tanto, Fagor ha creado no solo CNC compactos, sino también accionamientos compactos e incluso motores. La idea es proporcionar soluciones ajustadas que se ajusten a la necesidad frente a un enfoque estándar”.
Sistema de control de automatización
- El torno CNC mejora la productividad
- La herramienta de programación de robots reduce los problemas de calibración
- El software de modelado simplifica la programación de robots
- Actualizaciones de software que mejoran la programación y supervisión de cobots
- Funciones de software CNC Programación conversacional
- Ejemplo de programación CNC con ciclo de torneado de desbaste Fanuc G71 y G70
- Programación CNC Sinumerik 840D
- Programación CNC para maquinistas CNC
- Programación de ángulo CNC G01
- Códigos M:prueba de programación CNC
- Códigos G:prueba de programación CNC