Aplicación destacada:soportes impresos en 3D
Los soportes, aunque son piezas bastante simples, son una opción popular para la impresión 3D. Por un lado, la impresión 3D permite la optimización del soporte, lo que ayuda a mejorar el rendimiento de una pieza, así como la estructura en la que se utiliza un soporte.
En Application Spotlight de hoy, exploramos los beneficios clave del uso de la impresión 3D para soportes, así como también nos sumergimos en algunas aplicaciones interesantes en las industrias aeroespacial y automotriz.
Eche un vistazo a las otras aplicaciones cubiertas en esta serie:
Impresión 3D para intercambiadores de calor
Impresión 3D para rodamientos
Impresión 3D para la fabricación de bicicletas
Impresión 3D para odontología digital y fabricación de alineadores transparentes
Impresión 3D para implantes médicos
Cohetes impresos en 3D y el futuro de la fabricación de naves espaciales
Impresión 3D para la fabricación de calzado
Impresión 3D para componentes electrónicos
Impresión 3D en la industria ferroviaria
Gafas impresas en 3D
Impresión 3D para la producción de piezas finales
Impresión 3D para piezas de turbinas
Cómo la impresión 3D permite componentes hidráulicos de mejor rendimiento
Cómo la impresión 3D apoya la innovación en la industria de la energía nuclear
¿Qué es un paréntesis?
Un soporte es un sujetador, diseñado para mantener juntas dos partes perpendiculares en un ensamblaje y fortalecer el ángulo.
Los soportes mantienen unidas las estructuras que nos rodean (piense en edificios, aviones y automóviles), lo que determina en gran medida la fuerza, la resistencia y la integridad de esas estructuras.
¿Por qué utilizar la impresión 3D para corchetes?
Los soportes son componentes bastante simples de fabricar utilizando métodos tradicionales. Sin embargo, con la llegada de la impresión 3D, los ingenieros ahora pueden explorar nuevas formas de optimizar los diseños de soportes.
Esto es en gran medida posible, gracias a la capacidad de la impresión 3D para crear formas geométricas complejas que serían imposibles o prohibitivas en tiempo y costo con los medios de fabricación tradicionales.
Los beneficios clave de los brackets impresos en 3D son:
Producción más rápida
La producción de soportes metálicos complejos generalmente requerirá múltiples configuraciones de la máquina y puede llevar muchas horas completarla. La impresión 3D, por otro lado, puede ofrecer una solución más rápida. Una razón es que es posible anidar varias piezas dentro de una impresora 3D, lo que permite la producción de varios soportes simultáneamente en la misma máquina.
Para un soporte que fue previamente moldeado por inyección, el ahorro de tiempo es aún mayor porque la impresión 3D elimina el tiempo de espera de producir una herramienta de molde.
Montaje eliminado
Algunos soportes están hechos de varias piezas, lo que puede aumentar el tiempo necesario para ensamblar el soporte. La impresión 3D permite diseñar y producir un soporte como una pieza consolidada, por lo que se requiere menos mano de obra y tiempo para armar el soporte. Es probable que la impresión 3D de un soporte como una sola pieza también aumente la resistencia general de una pieza.
En un ejemplo, Philips utilizó la impresión 3D para producir un soporte rediseñado que mantiene las lámparas en su lugar en la línea de producción. La pieza se rompía con frecuencia, con una o dos fallas cada semana, en gran parte debido a la exposición repetida a altas temperaturas, junto con una estructura que presenta líneas de soldadura de un soporte de cuatro piezas.
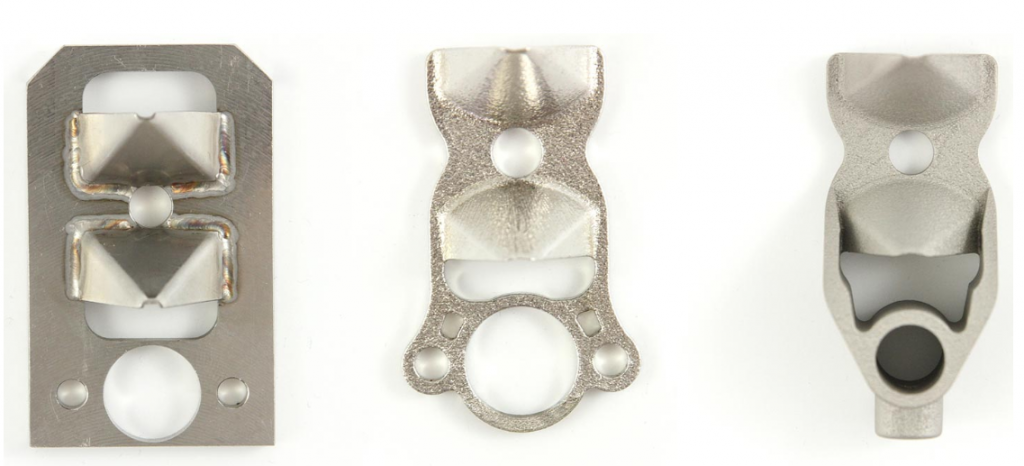
Philips pudo rediseñar una pieza de metal como un soporte de estructura única, lo que redujo el montaje de la pieza, que consumía mucho tiempo, y eliminó por completo los puntos de presión de la línea de soldadura. Durante sus primeros tres meses de uso, el soporte rediseñado no se ha roto ni una vez.
Reducción del desperdicio de material
El proceso de impresión 3D de un soporte como un componente a menudo utiliza menos material, creando así un soporte más ligero.
Ese ahorro de peso se traduce en un uso reducido de material y, en algunos casos, puede mejorar el rendimiento de un sistema en el que se utiliza un soporte.
Tome los motores GEnx de GE como ejemplo. Los motores utilizaban soportes fabricados con métodos tradicionales como el fresado. Significa que las piezas se fresaron a partir de un gran bloque de metal, y más de la mitad terminó como desperdicio.
El equipo que trabajaba en los soportes se dio cuenta de que mediante la impresión 3D de la pieza, podrían reducir hasta un 90 por ciento de los residuos.
El equipo también implementó pequeñas mejoras de diseño que redujeron el peso del soporte en un 10 por ciento. Según el equipo, "cuando se trata de volar, cada onza cuenta". Significa que la reducción del peso del componente puede tener un impacto en la tasa de consumo de combustible del avión, reduciéndolo y, por lo tanto, conduciendo a un avión más eficiente.
En otro ejemplo, los ingenieros de Ford recientemente imprimieron en 3D un soporte de freno de estacionamiento eléctrico de plástico para Ford Mustang Shelby GT500 que es un 60 por ciento más liviano que una versión de acero previamente estampada.
La posibilidad de reemplazar el metal por plástico o composite
Para algunas aplicaciones, la impresión 3D se puede utilizar para producir soportes de plástico en lugar de metal. Los soportes de plástico pueden ser más adecuados para aplicaciones como productos de consumo con una vida útil limitada o productos con componentes electrónicos sensibles donde los soportes metálicos no funcionan.
Un ejemplo proviene de un fabricante de dispositivos de comunicación, Boyce Tecnologías. La empresa utilizó la impresión 3D para fabricar piezas de plástico para los tótems de NYC Transit. Cada uno de estos sistemas cuenta con una tapa de acrílico verde en la parte superior que alberga una tira de LED para iluminación, así como un instrumento de antena sensible.
Para evitar la interrupción de la señal de la antena, no debería haber ninguna material metálico delante de él. Significa que la empresa tuvo que fabricar los soportes para la tira de LED y la carcasa para la antena en plástico. El equipo de Boyce dispuso de poco tiempo para el diseño, la ingeniería y la producción, por lo que la impresión 3D fue una solución adecuada.
Usando el sistema BigRep Studio, Boyce pudo crear prototipos de soportes de montaje curvos para las luces LED para iluminar la tapa y luego pasar directamente a la fabricación de estas piezas en esta misma plataforma.
La impresión 3D de estos soportes permitió que se fabricaran de forma rápida y más rentable que el moldeo por inyección o el mecanizado, al mismo tiempo que cumplía con el requisito de no metal sobre la antena.
Más ejemplos de corchetes impresos en 3D
Aeroespacial
Soportes de titanio impresos en 3D para Boeing 787
Los soportes aeroespaciales impresos en 3D, hechos de aleaciones de titanio, son cada vez más comunes en el diseño de aviones. Un ejemplo es un soporte para un pestillo de puerta de acceso para el Boeing 787, instalado por Spirit AeroSystems.
El accesorio del pestillo de la puerta, que anteriormente se mecanizaba, ahora está impreso en 3D por Norsk Titanium, utilizando su tecnología patentada Rapid Plasma Deposition (RPD). El nombre describe el proceso:un arco de plasma permite la deposición controlada de titanio a velocidades de construcción rápidas. Según se informa, la tecnología es 50-100 veces más rápida que los sistemas basados en polvo y utiliza entre un 25 y un 50 por ciento menos de titanio que los procesos de forjado.
La razón clave para cambiar a la impresión 3D de titanio es la oportunidad de reducir la producción. costo. El titanio es caro y, al mecanizar una pieza a partir de un bloque de titanio, se desperdicia una gran cantidad de este material caro. El segundo problema es una gran cantidad de tiempo de máquina y gastos de herramientas de corte que se dedican al mecanizado del metal, lo que aumenta el costo de producción.
Al imprimir en 3D un soporte, Spirit puede reducir estos costos sustancialmente, mientras acelera el tiempo de comercialización de piezas nuevas en al menos un 60 por ciento.
Liebherr-Aerospace 3D imprime soportes para Airbus
En otro ejemplo en la industria aeroespacial, Liebherr-Aerospace ha comenzado a imprimir en 3D los soportes del tren de aterrizaje de morro para el Airbus A350 XWB.
Estos soportes serán los primeros calificados Piezas de titanio impresas en 3D introducidas en el sistema Airbus.
A diferencia de Spirit AeroSystems, Liebherr pudo rediseñar una pieza para lograr una reducción de peso del 29 por ciento. El uso de la impresión 3D también ayudó a aumentar la rigidez del componente en un 100%.
En 2019, Liebherr-Aerospace alcanzó un hito clave:la Oficina Federal de Aviación de Alemania dio luz verde a la empresa para producir componentes utilizando AM. Desde entonces, Liebherr ha estado imprimiendo en 3D piezas en serie de titanio, incluidos los soportes.
Automotriz
Un soporte de techo, optimizado e impreso en 3D por BMW
En 2018, BMW lanzó su icónico automóvil i8 Roadster, con un galardonado soporte de techo de metal impreso en 3D.
El soporte de techo, un pequeño componente que ayuda a plegar y desplegar la parte superior del automóvil, requirió un nuevo diseño para maximizar el rendimiento del mecanismo de plegado del techo. Para lograr este objetivo, los ingenieros de BMW combinaron la impresión 3D con un software de optimización de topología.
Al usar el software, los ingenieros pudieron ingresar parámetros como el peso, el tamaño del componente y la carga que tomará. Luego, el software generó un diseño que optimizó la distribución del material de la pieza.
El diseño logrado por el equipo de ingeniería fue imposible de fundir. El equipo descubrió que la única forma de hacer posible este diseño era mediante la impresión 3D de metal.
Gracias a la tecnología Selective Laser Melting (SLM), los ingenieros crearon un soporte de techo de metal que es 10 veces más rígido y un 44% más ligero que la alternativa convencional.
Soportes ligeros de Bugatti
Los vehículos de Bugatti también cuentan con varios soportes impresos en 3D. Uno es un soporte de spoiler de titanio fabricado en colaboración con Fraunhofer IAPT. Se dice que este spoiler mejora el diseño aerodinámico de los vehículos Bugatti.
Otro socio en el proyecto del soporte del spoiler fue Siemens, que ayudó a optimizar el soporte para la producción. Al final, la parte final mostró una resistencia a la tracción de 1250 MPa, una densidad de material de más del 99,7 por ciento y una reducción de peso del 53 por ciento.
La impresión 3D también se ha utilizado para reinventar un pequeño Soporte de motor con refrigeración por agua integrada para el superdeportivo Bugatti Chiron. La pieza sirve como un escudo térmico activo, reduciendo significativamente el calor transferido desde el motor. El innovador componente, impreso en AlSi10Mg en una impresora SLM280 Twin 3D de SLM Solutions, se ha instalado en todos los vehículos de la serie desde el lanzamiento del primer Bugatti Chiron.
Brackets impresos en 3D:componentes pequeños con una gran oportunidad
Los soportes son piezas pequeñas y bastante mundanas, que eran difíciles de optimizar en el pasado, cuando los ingenieros estaban limitados por los métodos de fabricación tradicionales. Hoy en día, los ingenieros pueden diseñar soportes optimizados y dar vida a estos diseños con la ayuda de la impresión 3D.
Gracias a la tecnología, los soportes se pueden hacer más ligeros, pero más rígidos y duraderos. Los ejemplos anteriores también demuestran que al aprovechar la impresión 3D, se puede mejorar la vida útil del componente y el rendimiento general.
Claramente, todavía estamos lejos de los brackets impresos en 3D en masa. Dicho esto, las aplicaciones especializadas, como los soportes para aviones y los soportes producidos en pequeños volúmenes, seguirán siendo un buen nicho para la tecnología en el futuro.
Impresión 3d
- Soldadura y encolado de piezas de plástico impresas en 3D
- Exploración de la impresión 3D Polyjet
- ¿Qué es la bioimpresión?
- Aplicación destacada:Impresión 3D para implantes médicos
- Aplicación destacada:Impresión 3D para odontología digital y fabricación de alineadores transparentes
- Aplicación destacada:Impresión 3D para la fabricación de bicicletas
- Aplicación destacada:Impresión 3D para rodamientos
- Aplicación destacada:Impresión 3D para intercambiadores de calor
- Aplicación destacada:Impresión 3D en la industria ferroviaria
- COVID-19 ha impulsado la impresión 3D en el centro de atención
- Aplicación de la impresión 3D en la industria automotriz