Garantía de calidad para la impresión 3D en metal:solución de 3 desafíos comunes
El aseguramiento de la calidad (QA) es posiblemente el paso más importante y, sin embargo, uno de los más desafiantes en la impresión 3D.
Dado que la impresión 3D se utiliza cada vez más en aplicaciones industriales de alto rendimiento, la tecnología debe ofrecer piezas de alta calidad de forma constante y fiable con las propiedades necesarias para satisfacer las aplicaciones más exigentes. Sin embargo, cuando se trata de impresión 3D de metal, este ha sido un desafío continuo para muchos fabricantes que buscan invertir en la tecnología.
El artículo de hoy analizará algunos de los desafíos clave que enfrentan las empresas al intentar para establecer procesos de control de calidad para piezas metálicas impresas en 3D y explorar algunas de las soluciones disponibles.
Desafío 1:garantizar la calidad de sus materiales
Asegurar que una pieza impresa en 3D cumpla con los estándares de aplicaciones altamente exigentes depende en gran medida de la calidad del material utilizado.
Sin embargo, la calificación del material es un desafío continuo para las empresas que producen o manipulan polvos metálicos. Un factor que complica el proceso es la necesidad de mantener la pureza de los polvos metálicos utilizados para la fabricación aditiva.
Este es especialmente el caso de aplicaciones críticas para la seguridad, como piezas de aviones o dispositivos médicos, donde el material utilizado debe estar 100% libre de contaminación. Las impurezas pueden alterar las propiedades de la pieza final lo que, a su vez, podría provocar una impresión fallida.
Sin embargo, hay varias formas en las que los polvos metálicos pueden contaminarse.
Por ejemplo, el riesgo de contaminación puede surgir durante el proceso de impresión en sí o durante el almacenamiento, transporte y manipulación. Tomando el primer ejemplo:podría, por ejemplo, quedar algún residuo de otro polvo en la placa de construcción, lo que provocaría la mezcla de dos polvos diferentes. La limpieza a fondo de la placa de impresión después de cada ciclo de producción es, por lo tanto, un paso preventivo importante.
Otro riesgo proviene de la reutilización del polvo sobrante del proceso de impresión. Si bien la capacidad de reutilizar el material en polvo puede ayudar a reducir el desperdicio, es importante tener en cuenta que la reutilización repetida del polvo de esta manera puede cambiar potencialmente la composición de las partículas, ya que se absorben la humedad, el oxígeno y el nitrógeno.
Inevitablemente, se necesitarán métodos de prueba, adecuados para la fabricación aditiva, para garantizar que no haya contaminación.
Solución:considere la posibilidad de realizar una tomografía computarizada
Una de las formas más precisas de detectar la contaminación en polvos metálicos es mediante la exploración por tomografía computarizada (TC).
Un escáner de TC funciona tomando cientos de imágenes de rayos X desde diferentes ángulos, a partir de las cuales se crea una imagen en 3D. Los escáneres CT modernos pueden capturar detalles de hasta tres micrones, con algunos escáneres microCT de alta resolución, que funcionan en una escala micrométrica mucho más pequeña, alcanzando un tamaño de vóxel de 0,5 micrones.
Los equipos microCT actuales pueden inspeccionar metales que van desde aluminio y titanio hasta aleaciones de metales más pesados como acero inoxidable e Inconel.
Cuando se utilizan para calificar polvos metálicos para impresión 3D, los escáneres CT pueden proporcionar a los ingenieros datos detallados sobre la microestructura del polvo. Estos datos se pueden utilizar para detectar contaminantes de partículas extrañas, así como para medir la distribución del tamaño y la forma de las partículas y detectar la porosidad dentro de las partículas. Obtener esta información es una forma en que los ingenieros pueden confirmar la aplicabilidad del polvo para la producción.
Una empresa que brinda servicios de escaneo CT para la fabricación aditiva es Expanse Microtechnologies.
Hablando en una entrevista con AMFG, James Hinebaugh, presidente y cofundador de la empresa, señala que “Los polvos son el punto clave de interés en toda la cadena de suministro de la fabricación aditiva. Comprender qué hace que un buen polvo se esparza y se imprime bien es una preocupación clave para las empresas.
“Es importante comprender 1) si existe una morfología ideal o un tamaño o distribución morfológica ideal que puede interactuar bien con una amplia variedad de repintadores e impresoras, y 2) cómo podemos reducir los defectos en los polvos como las inclusiones y la porosidad intrapartícula que, según han demostrado los estudios, a menudo queda atrapada en una pieza y no puede escapar de la pieza durante el proceso de impresión ”.
Estas son las dos áreas que Expanse Microtechnologies está abordando con su solución patentada de escaneo MicroCT.
La empresa ha desarrollado métodos avanzados de procesamiento de imágenes, a partir de los cuales es capaz de generar informes detallados sobre la porosidad del material, la morfología de las partículas y los poros, así como la distribución de tamaño y forma de las partículas.
Tener esta información permite a los usuarios de fabricación aditiva identificar cualquier problema de materia prima y comprender los vínculos entre los materiales que utilizan y el nivel de calidad de los componentes impresos.
Si bien probar y calificar la materia prima para la fabricación aditiva puede ser un desafío, es uno de los pasos más importantes para garantizar la calidad de una pieza fabricada aditivamente. Actualmente, la tomografía computarizada ofrece una de las herramientas más robustas y útiles que se puede utilizar para validar materias primas AM.
Desafío 2:establecer el control del proceso
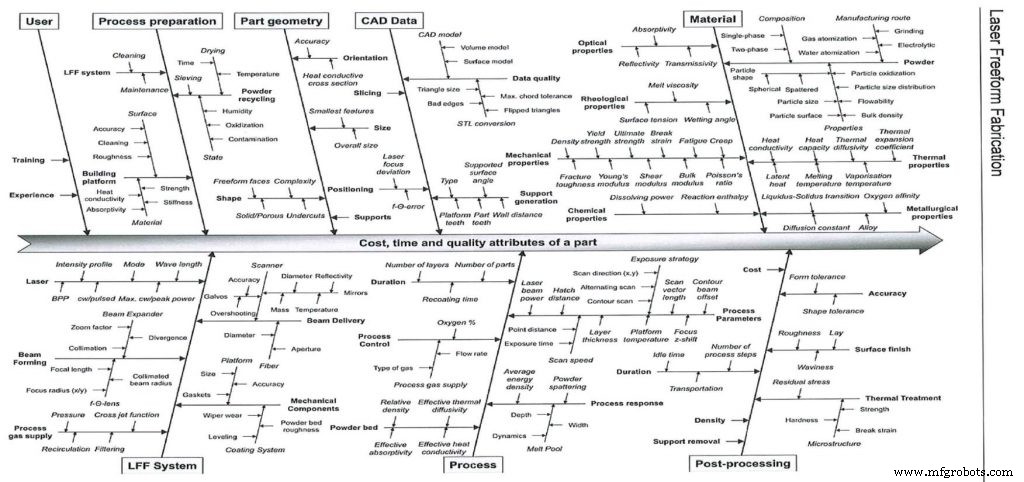
Cuando se trata de impresión 3D de metales, y tecnologías de fusión de lecho de polvo en particular, existe una amplia gama de variables que pueden afectar la forma y estructura de una pieza. Estas variables abarcan todo el flujo de trabajo de AM, desde el diseño hasta la preparación de la construcción y el posprocesamiento.
Tomemos el proceso de impresión como ejemplo. Aquí, solo algunos de los parámetros que determinan el éxito o el fracaso del proceso incluyen la trayectoria y la intensidad del láser y la velocidad de la hoja de recubrimiento de la impresora. Otros factores incluyen el diseño de las estructuras de soporte e incluso sutilezas como la cantidad de veces que se ha reciclado el polvo.
Si bien esta lista ni siquiera es exhaustiva, cada factor tiene un impacto en el resultado. de una construcción y la desviación de alguna manera podría afectar la calidad de la pieza final.
Actualmente, una prueba y error es el enfoque más común para tratar con la amplia gama de variables con el fin de lograr un proceso que produzca repetibles partes. Sin embargo, esto puede implicar la fabricación de la pieza final varias veces, así como pruebas exhaustivas de la pieza en sí.
Por supuesto, adoptar este enfoque es un proceso altamente costoso e ineficiente, y niega uno de los principales beneficios de la tecnología:poder producir pequeños lotes de piezas de manera rentable.
Las empresas, por lo tanto, deben adoptar un enfoque más sostenible y factible para el control de procesos y la calificación de piezas fabricadas aditivamente.
Solución:desarrolle un sistema de control de calidad de circuito cerrado
Es necesario que se unan tres elementos para permitir un proceso de garantía de calidad más rápido, más confiable y sostenible para las piezas impresas en 3D. Esto incluye planificación de construcción, monitoreo de construcción y control de retroalimentación.
- Planificación de la construcción
Una forma de comprender mejor el proceso de impresión es mediante la simulación. Mediante la simulación, los ingenieros pueden probar cómo se comportará una pieza en un entorno digital virtual antes de enviar un diseño a imprimir.
La simulación del proceso de AM permite a los ingenieros analizar los procesos complejos que ocurren durante el proceso de impresión.
Como la impresión 3D de metal es propensa a problemas como deformaciones y distorsiones, la simulación ofrece información clave sobre cómo una pieza se distorsionará durante el proceso de impresión, por ejemplo. Otro ejemplo es el uso de simulación para determinar exactamente cómo se derretirá y solidificará el material.
Los ingenieros pueden usar estos datos para planificar la construcción, seleccionando la orientación de la pieza y las estrategias de soporte más exitosas.
Dicho esto, el software de simulación tiene sus limitaciones. “Todo el software de simulación actual tiene algún nivel de supuestos integrados que limitan la precisión que puede ofrecer. Ese es probablemente el mayor inconveniente en este momento:no pueden ser tan precisos como le gustaría que fueran ", dice el jefe de tecnología de ANSYS, Dave Conover, en una entrevista reciente con AMFG.
Sin embargo, la tecnología de simulación está evolucionando rápidamente y los proveedores de software continúan perfeccionando sus ofertas. En última instancia, la integración del software de simulación en las etapas de diseño y planificación ayudará a eliminar el ensayo y error, al tiempo que reducirá significativamente las posibilidades de fallas de impresión.
- Supervisión de la compilación
Los sistemas de monitoreo en proceso pueden ayudar aún más al proceso de calificación de piezas. Se pueden usar sensores y cámaras para medir múltiples aspectos de la construcción en tiempo real, lo que ayuda a documentar el proceso de construcción y garantizar que se cumplan los requisitos.
Con los procesos AM de lecho de polvo, las cámaras pueden capturar el tamaño y la temperatura del baño de fusión, lo que impacta directamente en la microestructura, las propiedades del material, el acabado de la superficie y el rendimiento general de la pieza.
Ingenieros Luego, puede usar estos datos para predecir la probabilidad de defectos, como deformaciones o grietas, e intervenir en el proceso mucho antes de que ocurran los defectos. A medida que se documentan estos datos, esto puede ayudar a evitar las condiciones del proceso que pueden conducir a estos defectos en el futuro.
Actualmente, existe un número limitado de tecnologías de monitoreo en proceso optimizadas para AM.
Sigma Labs es una empresa que ofrece una solución para el aseguramiento de la calidad de AM en proceso. Su sistema de garantía de calidad PrintRite3D para fabricación aditiva combina multisensores y hardware PrintRite3D SENSORPAK con un módulo de software PrintRite3D INSPECT.
Esta combinación multifacética, registrada como tecnología IPQA, permite optimizar las condiciones del baño de fusión durante el proceso de AM, utilizando datos de sensores y estableciendo métricas de calidad en el proceso. Mediante el análisis estadístico de los datos del proceso, se pueden generar informes sobre la calidad de la pieza y utilizarlos para validar la repetibilidad.
En el futuro, la compañía planea agregar un módulo de software ANALYTICS, enfocado en aprovechar el análisis de Big Data. El módulo podrá extraer información significativa y procesable de los datos recopilados durante los procesos de impresión para simplificar aún más el control de calidad en el proceso.
En cuanto a las impresoras 3D en sí, algunas ya tienen la capacidad de monitoreo en proceso incorporada. Por ejemplo, el fabricante de impresoras 3D EOS ofrece la suite de monitoreo EOSTATE. La solución de hardware y software se basa en cuatro módulos de monitoreo diferentes, incluidos System and Laser, PowderBed, MeltPool y Exposure OT (tomografía óptica), que pueden capturar datos relevantes para la calidad en tiempo real.
Con EOSTATE Exposure OT, EOS afirma ser el único fabricante de sistemas de lecho de polvo metálico que ofrece a sus clientes una herramienta de garantía de calidad que incorpora tomografía óptica.
Este sistema de monitoreo utiliza una cámara que recolecta las emisiones de luz en el espectro del infrarrojo cercano, similar a una cámara termográfica. Puede mapear completamente cada parte a lo largo del proceso de construcción, capa por capa, independientemente de su geometría y tamaño. Con este enfoque, los ingenieros pueden ampliar la gama de fenómenos detectables relevantes para la calidad de las piezas AM.
MTU Aero Engines es una empresa que ya ha comenzado a utilizar esta solución de monitorización en sus líneas de producción en serie para AM. piezas de motores aeronáuticos.
- Cerrando el ciclo
Detectar y documentar los parámetros durante el proceso de impresión es crucial. Pero la capacidad de actuar sobre esta información en tiempo real, un proceso conocido como control de retroalimentación, es lo que hace que este enfoque sea aún más efectivo.
El control de retroalimentación, también conocido como sistema de circuito cerrado, se refiere a la capacidad de detectar desviaciones durante el proceso de impresión y ajustar automáticamente el sistema para compensarlas. Mantener el control sobre el proceso de construcción permite a los fabricantes lograr geometrías, acabados superficiales y propiedades del material consistentes que respaldan la calidad.
Una empresa que ha desarrollado un proceso de AM controlado por retroalimentación es Velo3D. Después de recaudar más de $ 92 millones en fondos, Velo3D surgió el verano pasado con el lanzamiento de su solución de AM de metal de extremo a extremo. Comprende la impresora 3D Velo3D Sapphire, el software de preparación de impresión Flow y lo que la empresa denomina tecnología Intelligent Fusion.
Con estos elementos clave estrechamente integrados entre sí, la tecnología permite la simulación de procesos térmicos, la predicción del rendimiento de impresión y el procesamiento de control de circuito cerrado. Como resultado, el sistema Sapphire puede producir piezas con geometrías desafiantes como voladizos sin prácticamente estructuras de soporte, de manera repetida y consistente.
El software Flow de Velo3D juega un papel integral al permitir estos beneficios. El software ejecuta una simulación y corrección de preimpresión, optimizando el diseño y ajustando la geometría y la orientación de la pieza. Esto ayuda a preparar la lima, equilibrando las deformaciones, para que la pieza salga correctamente. La metrología de procesos in situ acompañada de un control de la piscina de fusión de circuito cerrado funciona en conjunto con el software, lo que finalmente aumenta el éxito de la primera parte a más del 90%.
Desafío 3:Reducir el error humano
El error humano es posiblemente el mayor factor de riesgo para garantizar que una pieza impresa en 3D cumpla con todos los estándares requeridos.
Esto se debe a que la impresión 3D aún requiere más intervención humana de la que cabría esperar, desde el diseño y la eliminación de soportes hasta el posprocesamiento y la verificación manual de que se cumplen los requisitos en cada etapa.
Este nivel de intervención humana aumenta inevitablemente el riesgo de que la parte final se vea comprometida.
Tomemos como ejemplo la etapa de postproducción.
Una vez que se completa una compilación, será necesario desembalarla y las diversas partes que se han impreso en esa compilación deberán identificarse e inspeccionarse antes de enviarlas para su posprocesamiento.
El ingeniero de producción que realiza esta tarea normalmente necesitará consultar una hoja de trabajo impresa, esencialmente haciendo coincidir una imagen 2D con su contraparte física y marcando una lista de requisitos manualmente.
Este enfoque de inspección no solo requiere mucho tiempo, sino que también elimina la visibilidad del flujo de trabajo de la ecuación.
Sin embargo, muchas empresas que adoptan AM encuentran un desafío transformar el manual tareas involucradas en un proceso automatizado más rápido, más preciso.
Dado que reducir la probabilidad de errores humanos es tan importante para garantizar la calidad de las piezas impresas en 3D, una forma de lograrlo es mediante el uso de métodos digitales para automatizar la mayor cantidad posible de pasos de inspección.
Solución:implemente software de flujo de trabajo para la fabricación aditiva
El software de flujo de trabajo ofrece una plataforma digital centralizada para ayudar a los equipos de proyecto y producción a administrar sus procesos de producción de AM.
En el contexto de la garantía de calidad, el software de flujo de trabajo a menudo puede proporcionar el marco completo para ayudar a las empresas a garantizar que se cumplan los requisitos de todas las piezas.
Además, los gerentes de producción pueden usar software de flujo de trabajo para hacer que el proceso de inspección de piezas no requiera papel y sea rastreable. En lugar de inspeccionar manualmente cada pieza, hoja de trabajo en mano, las piezas físicas se pueden comparar con sus homólogos digitales en 3D.
Por ejemplo, la herramienta de gestión de posproducción de AMFG proporciona un visor 3D, que incluye todos los datos de la pieza, lo que permite a los usuarios inspeccionar una pieza y sus propiedades con mayor precisión.
La herramienta permite a los usuarios rastrear la proporción de piezas exitosas y fallidas. Las piezas marcadas como fallidas se devuelven automáticamente a la cola de producción interna de la plataforma para su reproducción. La mayor ventaja de esto es que permite a los usuarios realizar un seguimiento de cada acción realizada en una pieza, lo que agrega trazabilidad y responsabilidad a la necesidad de una gestión de calidad.
¿Existen estándares de control de calidad para AM en toda la industria?
Hasta ahora, hemos visto que comprender cómo calificar procesos, materiales e implementar estrategias digitales es clave para garantizar que las empresas puedan beneficiarse de la impresión 3D para la producción.
Los estándares de toda la industria desempeñarán un papel clave en este proceso. Con la fabricación tradicional, los estándares ya son un lugar común, lo que ayuda a las empresas a garantizar la calidad de sus productos y a encontrar puntos en común. Por supuesto, la fabricación tradicional ha tenido décadas, si no siglos, para desarrollar estándares relevantes.
La impresión 3D, por el contrario, es todavía un proceso relativamente nuevo y muchos estándares y certificaciones aún están en desarrollo. En el futuro, la industria necesitará desarrollar métodos de prueba, protocolos y datos de referencia para reducir el costo y el tiempo para calificar materiales, procesos y piezas de AM.
Afortunadamente, esta es un área que evoluciona rápidamente. Apenas el año pasado, AMST International publicó su estándar F3303, que describe formas de calificar las máquinas y los procesos utilizados para construir piezas utilizando láser o fusión de lecho de polvo por haz de electrones. También se señaló que ya está en curso una norma adicional para respaldar la calificación de las piezas, la garantía de calidad y el posprocesamiento de las piezas de fusión en lecho de polvo.
Junto con ASTM International, el Instituto Nacional de Estándares y Tecnología (NIST) está trabajando hacia el desarrollo de estándares de QA para la industria AM. Por ejemplo, NIST lanzó el proyecto AM Part Qualification, centrado en “las medidas, los métodos y los sistemas metrológicos necesarios para crear medidas robustas después del proceso, desarrollar una sólida comprensión del rendimiento mecánico y calificar las piezas AM”.
Vigilar la calidad
Garantizar la calidad del material y el control del proceso es fundamental para producir piezas metálicas de alta calidad de forma constante con impresión 3D.
Por más complejo que esto pueda parecer al principio, los fabricantes pueden animarse, ya que existen soluciones para respaldar el proceso de garantía de calidad, reforzadas por el desarrollo continuo de estándares para toda la industria.
Tomar estos desafíos e implementar estratégicamente las soluciones adecuadas para su empresa lo ayudará significativamente a capturar los beneficios de la impresión 3D para aplicaciones exigentes de alto valor.
Impresión 3d
- Se espera que los polvos de metal refractario se conviertan en materia prima para la impresión 3D
- Polvos de metal refractario VS tecnología de impresión 3D
- Considerando lo que significa la nueva tecnología de impresión en metal para AM
- Control de calidad en tiempo real:¿Qué sistema es el adecuado para usted?
- Estructuras de soporte para impresión 3D con metal:un enfoque más sencillo
- H.C. AMPERPRINT de Starck:una nueva herramienta para la impresión 3D en metal
- ¿Qué polvos metálicos para impresión 3D se pueden utilizar en 2020? [Guía]
- 6 Consideraciones de diseño importantes para la impresión 3D en metal
- Scalmalloy:el último material de alto rendimiento para impresión 3D en metal
- Consejos de diseño para la impresión 3D de sinterización directa de metal por láser
- Descripción general de la tecnología:cuándo realmente debería optar por la impresión 3D en metal