Electrónica de consumo:cubiertas híbridas compuestas
SABIC demostró en un estudio reciente que una cubierta de 1 milímetro de grosor podría cumplir con todas las especificaciones de desempeño relevantes de la industria para computadoras portátiles o tabletas muy delgadas. Fuente, todas las imágenes | SABIC
La electrónica de consumo es un mercado dinámico con tiempos de ciclo bastante cortos entre generaciones de productos. Desde sus teléfonos inteligentes, relojes inteligentes, tabletas y computadoras portátiles / portátiles, los consumidores quieren velocidades de operación más rápidas, baterías de mayor duración, mayor durabilidad y más funciones a menor costo y peso. Para satisfacer la demanda de los consumidores, los fabricantes de equipos originales solicitan a los proveedores materiales con alta estética y libertad de diseño, excelente resistencia al impacto y alta rigidez, que connota calidad en este mercado, de bajo peso y secciones de paredes delgadas. También quieren métodos de procesamiento rentables y altamente repetibles que satisfagan la demanda de producción global en decenas de millones de unidades al año. Estas presiones han empujado al mercado primero a metales livianos para cubiertas / estuches y marcos, y ahora lo están impulsando hacia soluciones de metal / compuestos y totalmente compuestas.
Un estudio de viabilidad realizado por SABIC (Bergen op Zoom, Países Bajos) implicó el uso de dos tipos de compuestos termoplásticos para producir una cubierta de tableta / computadora portátil de 1 milímetro de grosor. El estudio mostró que el diseño del compuesto termoplástico híbrido podría ser una solución viable para el desafiante mercado de la electrónica de consumo.
Caso de prueba
Desde 2012, SABIC ha realizado una serie de inversiones para desarrollar sus propias cintas compuestas termoplásticas reforzadas con fibra unidireccional (UD) (ver “Evolución hacia refuerzos de fibra continua”), que extendieron la competencia central de la empresa en inyección de fibra corta y larga materiales termoplásticos de fibra (LFT) y permitió que SABIC se expandiera a compuestos termoplásticos de mayor rendimiento. En 2015, la compañía compró una participación mayoritaria en el fabricante de cintas Fiber Reinforced Thermoplastics BV (FRT, Lelystad, Países Bajos) y en 2017 se asoció y se convirtió en un inversor minoritario en Airborne (La Haya, Países Bajos), un fabricante de máquinas y desarrollador de procesamiento de compuestos. líneas.
A medida que SABIC y Airborne diseñaron y construyeron tecnología para producir de manera rápida y rentable laminados basados en cinta termoplástica de alta calidad con forma de red para mercados verdaderamente de gran volumen (consulte “Fabricación de compuestos termoplásticos de alta velocidad y alta velocidad”), el equipo comenzó a buscar un caso de prueba. Este demostrador sería una importante herramienta de marketing para probar conceptos de diseño para laminados compuestos termoplásticos producidos a partir de cintas compuestas sobremoldeadas con compuestos reforzados con fibras discontinuas. También sería importante probar las herramientas de ingeniería predictiva que el equipo había desarrollado para ambas tecnologías de materiales y mostrar el proceso de fabricación de alta velocidad que evoluciona en los Países Bajos.
“Decidimos especializarnos en aplicaciones de electrónica de consumo”, explica Gino Francato, líder mundial en compuestos de SABIC. “Ese mercado es muy interesante porque existe una verdadera ambición de pasar a materiales livianos para hacer que nuestros teléfonos móviles y computadoras portátiles sean más livianos y delgados. Y como hacen millones y millones de ellos, decidimos aceptar el desafío que ofrecía este mercado ".
“Decidimos comenzar con algo que fuera razonablemente complejo pero no demasiado complejo ”, explica Scott Davis, científico del personal de SABIC-tecnología de aplicación global. La cubierta superior de una computadora portátil muy delgada o incluso una tableta, que el equipo esperaba que eventualmente se tradujera en componentes de teléfonos inteligentes, parecía un buen lugar para comenzar. “Estábamos trabajando con una geometría general simple, un rectángulo, que aún tenía que mantener una alta estética y ofrecer mucha complejidad en su lado B, incluidas las características de los accesorios”, continúa Davis. “Tuvimos que mantener la cubierta muy delgada, pero aun así cumplir con los desafiantes requisitos de deflexión comunes en la industria. Y, por supuesto, tuvimos que entregar un producto muy consistente a través de un nuevo proceso de fabricación complejo ”.
Como no estaban trabajando con un diseño de cliente real y solo estaban creando la cubierta protectora para una pantalla, usaron geometría genérica. De hecho, señala Davis, cuando comenzaron a cortar herramientas de inyección para el desarrollo interno, ni siquiera estaban seguros de si estarían fabricando una funda para tableta o portátil, por lo que la funda fue diseñada para cualquiera de los dos. “Hubo muchos desafíos para preparar una solución compuesta para la producción de alto volumen”, agrega Davis. “De hecho, sucedían muchas cosas simultáneamente (desarrollo de cintas, desarrollo de laminados y desarrollo de procesos) y no podíamos esperar hasta que todas esas cosas estuvieran finalizadas para comenzar con nuestras herramientas, que es como terminamos con ese diseño”. Con el diseño básico completo, el equipo se centró en otros detalles, como la mejor forma de compuerta, qué tipos de superposiciones se necesitaban entre el inserto laminado y el compuesto de sobremoldeo, cómo manejar la colocación automatizada dentro de la herramienta, cómo lidiar con el coeficiente de ( desajuste de expansión térmica lineal) (CLTE o CTE) entre los dos compuestos y cómo crear una pieza fácilmente repetible.
Cumplir con requisitos desafiantes
El objetivo era desarrollar una cubierta superior de 1 milímetro de espesor que proporcione alta rigidez y supere todos los requisitos estéticos y de rendimiento, especialmente la prueba de deflexión del punto central se aplica regularmente a las cubiertas de los portátiles para evaluar las cargas necesarias para dañar la pantalla subyacente. Los requisitos de carga / deflexión varían según el OEM, el dispositivo y el modelo, pero normalmente no se permiten más de 3-5 milímetros de deflexión bajo 40-120 Newtons de presión, una situación que simula las cargas ejercidas por un dedo o codo presionado en la cubierta como un usuario humano se pone de pie. En muchas industrias, la estrategia para aprobar tales pruebas sería aumentar el grosor de la sección, pero este mercado valora los diseños más delgados que liberan espacio para baterías más grandes y otros componentes sin aumentar el tamaño o el peso del dispositivo. Por lo tanto, el equipo necesitaba usar una estrategia de diseño diferente para evitar daños en la pantalla, es decir, seleccionar materiales más rígidos (a través de un inserto laminado) y usar geometría (por ejemplo, nervaduras mediante sobremoldeo por inyección). Pero, primero, tenían que especificar los materiales.
Uno de estos materiales, el policarbonato (PC), ya es muy utilizado en esta industria para cubiertas y otros componentes, debido a su excelente estética y alta resistencia al impacto. Las mayores debilidades del polímero son la resistencia química y el rayado de la superficie, pero el recubrimiento, la pintura o combinaciones de ambos aplicados a la mayoría de las cubiertas generalmente superan estos problemas potenciales.
“Debido a que las computadoras ultraligeras son tan delgadas, el espacio del paquete en el interior es muy importante, por lo que las desviaciones y la mecánica se vuelven realmente críticas”, señala Francato. "Si bien querría usar vidrio [refuerzo] desde una perspectiva de costos, tuvimos que usar [fibra] de carbono para obtener la rigidez que necesitábamos". Como resultado, todos los laminados basados en cinta evaluados eran variaciones de policarbonato reforzado con fibra de carbono, grados que estaban en desarrollo con la subsidiaria de SABIC, FRT.
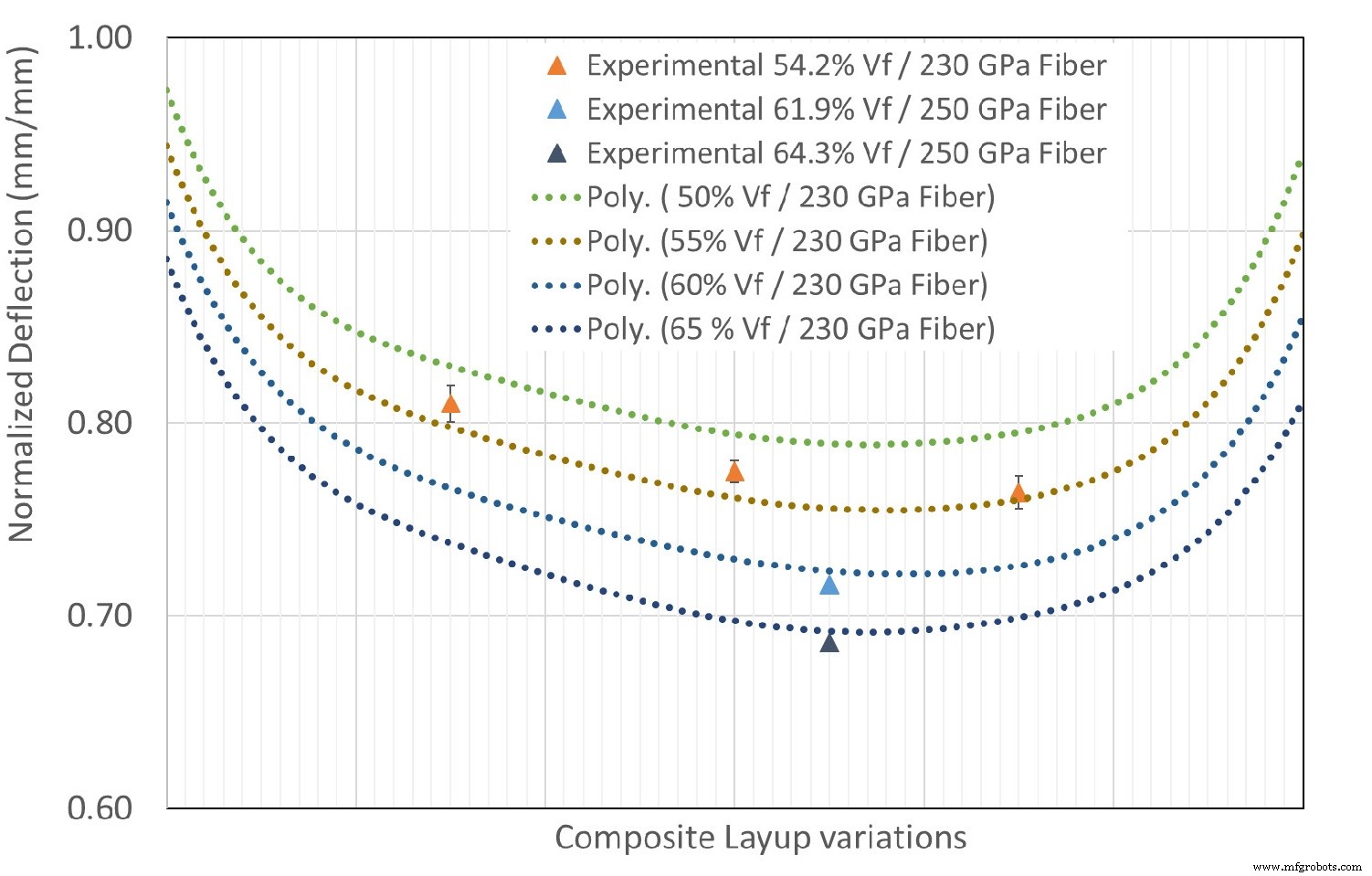
SABIC ha desarrollado modelos predictivos para simular el tipo y la arquitectura de laminado (con y sin compuestos de sobremoldeo) frente al rendimiento de la pieza moldeada e informa que se ha logrado una fuerte correlación entre las predicciones y los resultados experimentales. Se dice que las herramientas de ingeniería predictiva aceleran el desarrollo de materiales.
El compuesto de sobremoldeo requería un enfoque diferente. Inicialmente, la estrategia era utilizar un compuesto LFT de fibra más larga, pero por varias razones, incluidos los altos requisitos estéticos, el tamaño de la pieza y la estrategia de activación, los compuestos de fibra corta cumplían mejor con los requisitos del proyecto. Otro problema fue el tipo de fibra a utilizar. "Es realmente difícil trabajar con compuestos de inyección de carbono corto y aún así obtienen una alta estética", continúa Francato, "por lo que para nuestro material de sobremoldeo, buscamos grados reforzados con vidrio corto". La subsidiaria de SABIC, LNP Engineering Plastics, Inc. (Exton, Pensilvania, EE. UU.) Ofrece muchos grados de fibra de vidrio / PC con buena estética y rigidez que son populares entre los fabricantes de equipos originales (OEM) de dispositivos, por lo que el equipo se centró en ellos.
Si bien la PC completamente amorfa es menos propensa a deformarse que los polímeros semicristalinos, el equipo aún estaba preocupado por las diferencias de CLTE entre las cintas de fibra de carbono UD altamente reforzadas y anisotrópicas y los grados de sobremoldeo de fibra de vidrio corta más isotrópicos y discontinuos con cargas de fibra más bajas. "En paredes tan delgadas, hay muy poco margen de error, por lo que las pequeñas diferencias en CLT fueron cosas que tuvimos que considerar cuidadosamente", explica Davis. “Y eso ni siquiera toca todos los problemas normales que le preocupan al realizar el moldeo por inyección, como la ubicación de las puertas, los patrones de relleno, las presiones de empaque y las líneas de tejido. Todos estos factores fueron simulados y verificados con pruebas físicas ”.
Una vez que se eligieron los materiales, los ingenieros de SABIC llevaron a cabo múltiples iteraciones de llenado de moldes, análisis estructural y simulación de deformación para evaluar la disposición del laminado, la geometría y las combinaciones de materiales para optimizar la rigidez para la prueba de carga / deflexión, además de otros requisitos de rendimiento y costos. La compañía dice que ha desarrollado herramientas de modelado de compuestos completos y precisos (disponibles para los clientes y que se ejecutan en códigos de procesamiento y estructurales comunes) que pueden modelar y simular rápidamente la arquitectura del laminado, la composición del compuesto de sobremoldeo y varias opciones de procesamiento y herramientas en comparación con el rendimiento de la pieza moldeada. Se dice que estas herramientas logran una fuerte correlación entre las predicciones y el rendimiento medido y son ideales para acelerar el desarrollo de materiales personalizados.
Listo para el horario de máxima audiencia
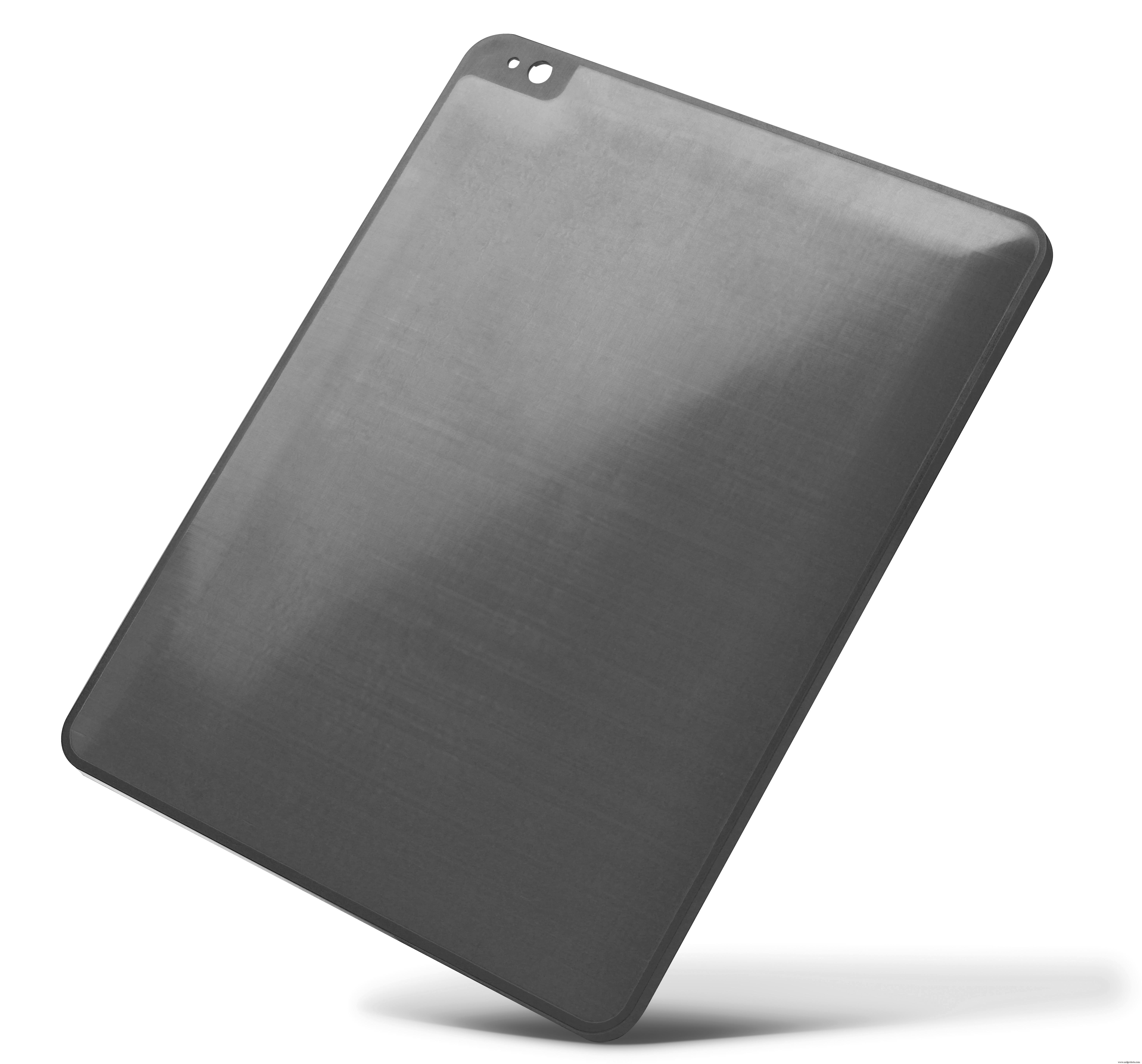
Parte frontal de la cubierta final para computadora portátil / tableta, que se produjo utilizando un inserto laminado a base de cinta de policarbonato reforzado con fibra de carbono sobremoldeado con un compuesto de copolímero de policarbonato / vidrio corto, una combinación que cumplió con todos los requisitos mecánicos y estéticos relevantes en un 1- parte milimétrica de espesor.
El demostrador final presenta un inserto laminado producido a partir de siete capas de cintas de fibra de carbono / PC UDMAX de desarrollo (55% de fracción de volumen de fibra), luego consolidado, recortado, preformado y recortado nuevamente hasta la forma final de red, antes de ser sobremoldeado por inyección con 40% de fibra. fracción de peso THERMOCOMP D452 fibra de vidrio corta / copolímero de PC (un grado optimizado para alto flujo y alta estética y ya ampliamente utilizado en este segmento). La combinación produce una cubierta con alta rigidez y resistencia con poca masa y espesor de sección, al tiempo que incluye numerosos detalles de diseño en 3D, características de fijación y buena estética, aprovechando así lo mejor de cada material. Según se informa, la cubierta pasó todas las pruebas requeridas por la industria y actualmente está siendo evaluada por fabricantes de equipos originales de dispositivos.
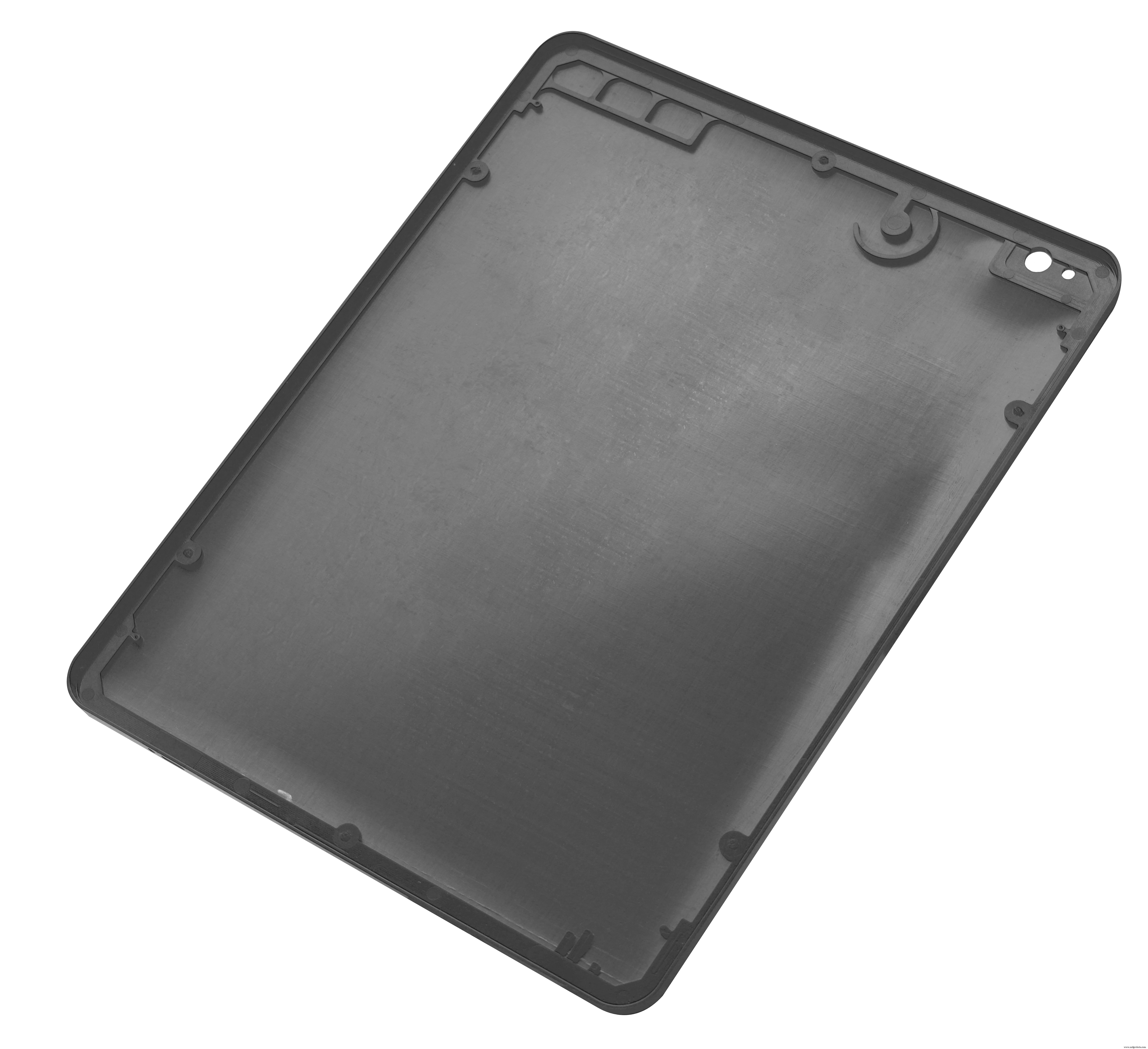
Parte posterior de la cubierta terminada.
El trabajo entre Airborne y SABIC también ha dado frutos para los objetivos del mercado de productos electrónicos de consumo de SABIC. La asociación se anunció en 2018, y este año se han proporcionado más detalles sobre lo que ambas empresas llaman su Línea de fabricación de compuestos digitales, que puede producir cuatro inserciones de laminado consolidado en forma de red a partir de cintas de compuestos termoplásticos por minuto o 1,5 millones de laminados por año de una sola línea de producción. Se dice que el sistema es flexible (en términos de arquitectura y materiales de disposición) y rápido. A partir de 2020, Airborne utilizará la línea para fabricar laminados para uso comercial en electrónica de consumo, convirtiéndose en un recurso que ambas empresas esperan que aumente en gran medida la penetración de los compuestos termoplásticos en este segmento altamente competitivo y acelerado.
fibra
- Materiales:Grafito flexible de una sola capa para electrónica de consumo
- Solvay expande la capacidad de compuestos termoplásticos
- La rueda termoplástica toma el camino difícil
- Fraunhofer encarga células de producción automatizadas de Engel para I + D de compuestos termoplásticos
- Las cintas termoplásticas continúan mostrando potencial para aeroestructuras compuestas
- Avient lanza un compuesto termoplástico de fibra larga de nailon resistente a la humedad
- Costillas Wing of Tomorrow:consolidación OOA, termoplástico, de un solo uso
- INEOS Styrolution para construir un sitio de producción para el compuesto termoplástico StyLight
- Xenia presenta los compuestos termoplásticos CF / PP
- Compuesto termoplástico TenCate calificado para NIARs NCAMP
- Compuesto + metal:Tecnología híbrida de perfil hueco