Un control de calidad de máquina herramienta de mayor calibre
El control de calidad de las máquinas herramienta está en la cúspide de un cambio profundo. Según Steffen Hailer, gerente de producto e ingeniero de aplicaciones de AfM Technology en Aalen, Alemania, una norma ISO que se publicará próximamente (ISO 230-13) definirá el proceso mediante el cual se puede calibrar una máquina herramienta de modo que su las mediciones de sondeo pueden ser aceptadas por el departamento de calidad.
Esto no significa que la máquina herramienta siempre será tan precisa como una MMC típica. Pero los departamentos de producción y control de calidad hablarán el mismo idioma, y las mediciones de la máquina se podrán utilizar para el control de calidad. Eso, a su vez, ofrece ventajas en un mejor control de procesos y un menor costo de calidad.
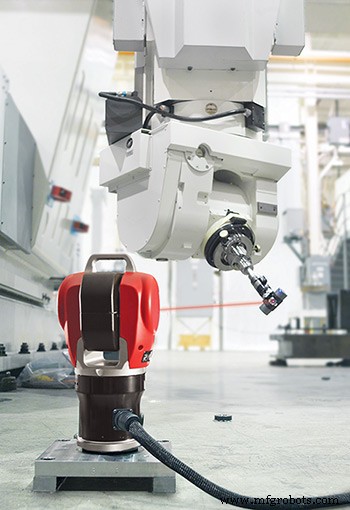
La compensación de errores volumétricos (VEC) es quizás el factor más importante que hace posible que una máquina herramienta realice un control de calidad aceptable. Pero incluso si aún usa equipos fuera de línea para la inspección final (que generalmente será el caso), los últimos métodos en VEC ofrecen la mejor ruta para garantizar una alta precisión en la producción de piezas complejas.
Por ejemplo, Art Kietlinski, gerente de operaciones de Automated Precision Inc. (API) de Rockville, Md., dijo que el paquete de compensación de la compañía hará una mejora de cuatro a cinco veces en la precisión volumétrica de una máquina herramienta de varios ejes, y a veces una mejora aún mayor. “Normalmente, podemos ver una máquina con un error volumétrico máximo en la punta de la herramienta de, por ejemplo, 0,3 a 0,5 milímetros antes de la calibración. Y luego, después de la calibración, podríamos estar alrededor de 0.075. En una máquina de cinco ejes, analizamos y mejoramos los 43 errores posibles”. [Consulte "Mantener máquinas honestas con calibración avanzada, optimización", Ingeniería de fabricación, junio de 2019, para obtener una explicación de las 43 posibles desviaciones de la máquina herramienta.]
API hace esto al combinar un rastreador láser con lo que ellos llaman Active Target, explicó Ron Hicks, vicepresidente de administración y marketing de productos. “Active Target es un pequeño reflector motorizado montado en el eje. Permite que el rastreador láser mida con precisión la posición de la punta de la herramienta de la máquina desde una sola posición del instrumento”. Eso es significativo, señaló Hicks, porque el proceso VEC mueve el husillo en tiempo real a través de todos los ejes de la máquina durante el proceso de medición. Eso no sería posible con un reflector de seguimiento láser estándar, porque el haz se rompería en varios puntos a lo largo del volumen de la máquina. Hicks agregó que “a diferencia de los procesos láser convencionales, nuestro sistema no tiene que estar alineado con los ejes principales de una máquina herramienta. Esto tiene ventajas dramáticas en términos de velocidad y precisión... Hemos podido compensar dos máquinas en un solo día".
El sistema de API mide "todas las posiciones posibles de la máquina", agregó Kietlinski, por lo que en un volumen de máquina grande (por ejemplo, 10 m) podría trazar hasta 250 puntos. A partir de ahí, el software propietario genera coeficientes para los polinomios que calculan las correcciones de error necesarias para cada eje. Como explicó Kietlinski, se trata de matemáticas complejas, porque “los errores no son necesariamente lineales. Podría terminar con un polinomio de segundo o tercer orden que debe resolverse”.
La planta de Northrop Grumman en Palmdale, California, es una de varias historias de éxito, dijo Hicks. La planta utiliza grandes máquinas de pórtico de cinco ejes para realizar todo el recorte y la perforación de orificios para todo el fuselaje del F-35, y API visita cada año para realizar VEC en cada máquina. Mientras tanto, dijo Kietlinski, Lockheed Martin e Israeli Aerospace mecanizan las secciones del ala en horizontales, a las que API también da servicio.
Hay límites. Una visita reciente a una empresa de Michigan que produce herramientas, prototipos y componentes de producción de bajo volumen de alta calidad presenta una nota de advertencia.
Comprender las limitaciones
Kietlinski relató que la empresa de Michigan invitó a API a demostrar su equipo en una máquina de cinco ejes que ya se había sometido a VEC según un mapa de 21 errores, “que es la norma para la mayoría de las máquinas y CMM”. Como explicó Kietlinski, “todas estas calibraciones asumen que la máquina tiene un cuerpo rígido, lo que significa que todos los errores angulares serían los mismos a lo largo del recorrido de ese eje a través del volumen. Entonces, por ejemplo, no importa dónde ejecute el eje X a través del volumen, si tuviera que medir los errores de cabeceo, guiñada y balanceo, obtendría los mismos datos angulares. Pero ese no es siempre el caso en estas máquinas más grandes”. Eso generalmente se debe a que los rieles no son paralelos, dijo. Esto crea estrés en la máquina y su sistema de accionamiento, lo que hace que "las corrientes de carga aumenten y una serie de otros problemas".
Entonces, lo primero que Kietlinski verificó fue la rectitud de los ejes lineales, lo que lleva menos de una hora usando el rastreador láser. Agregó que suele haber una relación directa entre la rectitud y otros errores geométricos, como los errores de cabeceo, guiñada, balanceo y cuadratura, “porque ni siquiera puedes evaluar la cuadratura si no eres recto”. En este caso, encontró errores de hasta 200 a 250 micras (0,010”). API realizó una alineación completa en la máquina, “incluso soltando el puente y cuadrándolo mecánicamente. Luego aplicamos el mapa de corrección de errores 21. En este punto... los errores angulares eran los mismos en toda la máquina y pudimos mejorar la máquina diez veces con respecto a la calibración anterior".
Eso se debe en gran parte a la alineación mecánica mejorada, enfatizó Kietlinski. “Cuanto mejor tenga la máquina mecánicamente alineada, mejores serán los resultados de la calibración”. Por el contrario, "no se puede tomar una máquina que no esté alineada mecánicamente y tratar de arreglar todo con software".
Corrección de errores en proceso
Dentro de los límites que acabamos de discutir, VEC puede mejorar notablemente las imprecisiones geométricas de una máquina. Pero, ¿qué pasa con las "inexactitudes de trabajo", los errores adicionales que ocurren durante el mecanizado, debido a las tensiones operativas, la inestabilidad térmica y otros factores? Bill Malanche, director de operaciones de Mitsui Seiki (EE. UU.), Franklin Lakes, N.J., enumeró las principales causas de imprecisión como “pérdida de movimiento, calor y diseño. El movimiento perdido funciona en muchos aspectos, pero se puede resumir en alineación y ajuste geométricos”. Con VEC abordando los otros factores, la inestabilidad térmica emerge como quizás la principal fuente de errores en el proceso. Y cuanto más grande es la máquina, más variación se puede ver en la posición real de la herramienta frente a la nominal.
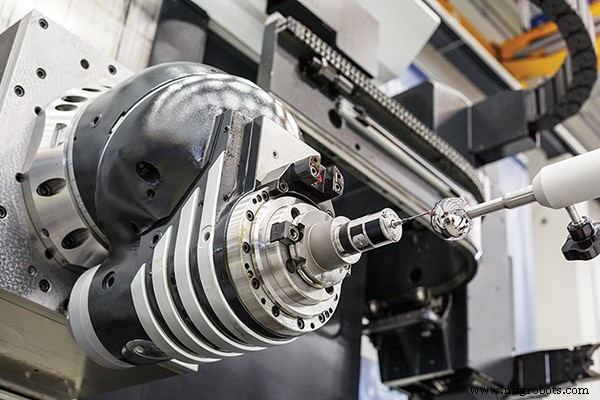
Un enfoque para lidiar con este problema es usar la sonda interna de una máquina para ayudar a calcular esa desviación y luego compensarla. Doug Schulte, gerente de desarrollo comercial de Select Machining Technologies, Windsor, Conn., dijo que sus máquinas Soraluce “sondean una esfera de calificación en varios puntos preestablecidos. Hace esto para muchas posiciones de la cabeza y el eje. Luego, el software compara los puntos medidos con el modelo cinemático de la máquina y realiza las compensaciones necesarias para asegurar el punto central de la herramienta en la geometría de la máquina”. Soraluce llama a esta función Dynamic Head Calibration (DHC), y Schulte dijo que es una característica común en las máquinas de cinco ejes. [Ingeniería de fabricación cubrió la versión de Okuma en el artículo de junio de 2019.]
Las máquinas de Soraluce generalmente están equipadas con múltiples cabezales de dos ejes, y DHC toma de 25 a 30 minutos para todo el ciclo de medición. Está diseñado para la compensación periódica previa al mecanizado, como VEC. Pero Soraluce tiene una función adicional llamada Accura Heads que se enfoca en posibles errores en el proceso y solo toma uno o dos minutos hacerlo. Esta opción utiliza la misma sonda y esfera de medición, pero se ejecuta dentro del programa de mecanizado, explicó Schulte.
“Si va a abordar una función en una pieza que está en un ángulo específico y ese ángulo es muy crítico, puede usar la rutina Accura Heads para verificar el ángulo y la posición del punto de herramienta de esa orientación particular. Luego hará ese desplazamiento para esa herramienta. Haces ese ciclo de sondeo inmediatamente antes de ejecutar esa operación”.
Schulte también indicó que para tolerancias más estrictas en ciertos diseños de máquinas, el usuario debe montar la esfera más cerca del área donde se va a cortar, según el tamaño de la máquina. “Soraluce ha construido máquinas con recorridos longitudinales de más de 60 metros”, añade. Uno puede imaginar fácilmente que las influencias externas podrían causar una desviación entre el posicionamiento real y el nominal tan lejano.
El apretón de manos de mecanizado/control de calidad
Tomando una "máquina compensada" como un hecho, los operadores pueden considerar la posibilidad de utilizar la sonda de una máquina herramienta para realizar funciones de control de calidad. La nueva norma ISO 230-13 definirá los requisitos y lo hará en referencia a la ISO 10360, que es la norma para MMC. La especificación clave con la que se juzgan las CMM es su valor de error máximo permisible (MPE). Una prueba de aceptación mediría siete orientaciones (cuatro diagonales del cuerpo, más una a lo largo de X, Y y Z) con un calibrador de pasos o un láser en combinación con una esfera de medición. Para pasar la prueba, la desviación máxima (E0) no debe ser mayor que el MPE.
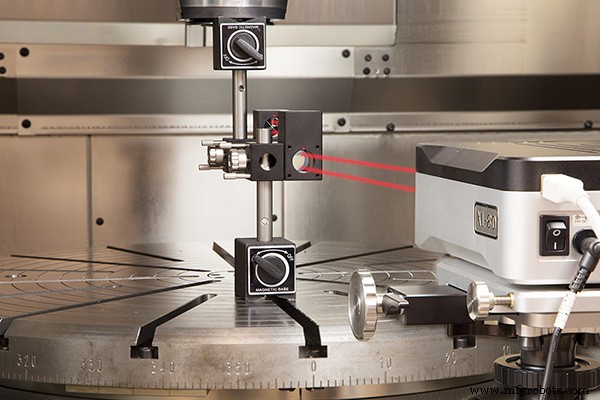
Como explicó Hailer, la nueva norma ISO define el procedimiento de prueba de aceptación y los valores necesarios con la misma claridad para las máquinas herramienta, pero es un nuevo concepto para los fabricantes de máquinas. “Por el momento, ningún fabricante de máquinas herramienta conoce el tamaño de su MPE. Tienen que aprender el procedimiento para determinar dicho valor y luego averiguar cuál es. Este es uno de los servicios que brindamos a los OEM”. Una vez que un constructor ha determinado este valor para una máquina determinada, y se verifica en el sitio, tal como lo haría para una instalación de CMM, un usuario podría realizar una inspección final de la pieza en la máquina, nunca colocarla en una CMM, y entregar la pieza. a un cliente con un informe que documente la precisión de las mediciones.
Si el MPE de una máquina herramienta es aceptable o no para el usuario final es otra cuestión. Pero parece probable que las máquinas de mayor precisión cumplirán un control de calidad satisfactorio al menos para algunas aplicaciones. Eso es particularmente cierto para piezas muy grandes, observó Béat Ries, gerente de productos de molienda de Mitsui Seiki. “Se paga mucho dinero por una CMM grande, especialmente cuando se quiere llegar a una precisión ultraalta. Los números son astronómicos. Parece que nadie es capaz de proporcionar una solución económica.”
Hay más, dijo Ries. Conocer solo el MPE de una CMM o máquina herramienta no es suficiente para satisfacer los estándares aeroespaciales o automotrices. Esto se debe a que también "requieren un valor de incertidumbre junto a cada medición o validación realizada en las piezas". Entonces, si bien muchas personas piensan que el MPE solo es la "precisión" de una máquina, la figura no captura las variaciones de medición, y las imprecisiones adicionales, que ocurren en el mundo real. Por ejemplo, explicó Ries, “las fluctuaciones de temperatura en una tienda producirían mediciones diferentes. Entonces, si una CMM tiene un MPE de 1,9 más L/250 micras, la incertidumbre calculada podría ser de 3 micras por metro. Si mide más de un metro, el valor MPE sugeriría que tiene una precisión de 5,9 micrones. Pero si agrega el valor de incertidumbre, verá que en realidad está midiendo con una precisión de más o menos 8,9 micras".
Dividir el micrón
Un taller que se toma muy en serio la medición es Precision Grinding Solutions (PGS) en Hamden, Conn. El propietario, Curt Reed, considera esencial que tengan una comprensión firme de su control de calidad, para incluir mediciones de incertidumbre, porque rectifican piezas giratorias de motores a reacción. para grandes OEM como Pratt &Whitney, además de proveedores aeroespaciales de nivel 1 y 2. PGS incluso tiene un contrato para calibrar medidores para varias ubicaciones de Pratt.
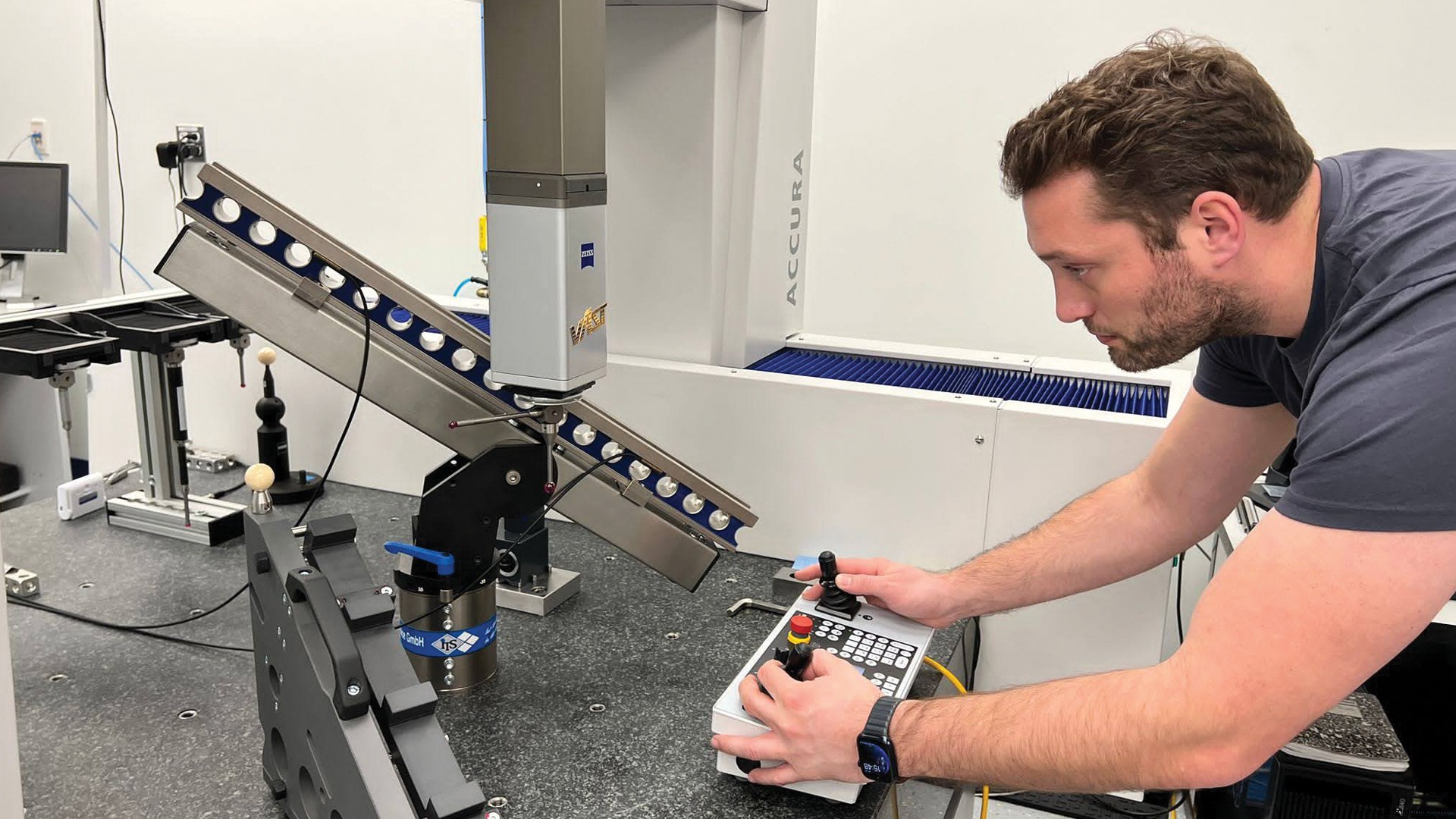
PGS tiene una Zeiss PRISMO ultra CMM, a la que Reed se refiere como una máquina de "clase de referencia". El CMM cuenta con un E0 de 0,5 + L/500 μm, y PGS ha estado determinando el presupuesto de incertidumbre “una de las formas antiguas. Toma un artefacto conocido, digamos uno de los medidores Pratt en los que estamos involucrados en la calibración, y mide una característica crítica 50 veces más o menos. Luego, examina esta distribución de datos, considera factores como los cambios en la temperatura de la habitación, conecta todo eso en una fórmula de larga data y obtiene una cifra de incertidumbre".
Ahora PGS está implementando un nuevo método para manejar aún mejor la incertidumbre de la medición:Virtual CMM (VCMM). Reed explicó que VCMM es un módulo de complemento para el paquete de software ejecutivo Calypso de Zeiss que "le permite insertar otra columna en sus informes que muestra la incertidumbre de cada medida que toma". Más allá de eso, también captura todos los demás errores que la calibración del láser no tiene en cuenta, agregó Reed.
PGS está trabajando con AfM para capturar los datos necesarios para este esfuerzo, que según Reed va más allá del seguimiento de las fluctuaciones y vibraciones de temperatura. “Por ejemplo, tiene en cuenta si estás usando un lápiz óptico largo con un eje delgado o uno corto y rechoncho. ¿Cómo es la firma de doblado de la máquina? Cuando estás midiendo la máquina, ¿cuál es la geometría real, las escalas, las guías... cómo se ve todo eso? AfM determinará todo esto tomando una serie de medidas especiales con un conjunto de artefactos que incorporan varias bolas y pasos. Luego, los archivos de error se ejecutarán en segundo plano para determinar la incertidumbre.
En resumen, dijo Reed, “VCMM es una forma mucho más moderna y completa de examinar la incertidumbre para todo el sistema y el laboratorio. No se basa solo en un artefacto. Es calificar a través de todas las medidas que está tomando AfM, y es calificar todo el volumen de medición de la CMM, no solo un área local donde probó un medidor".
Una vez terminados, comentó Reed, los nuevos informes harán que la imagen de calidad parezca peor, “porque hace un mejor trabajo, característica por característica. Si activa esta función, verá la incertidumbre de cada característica que se ejecuta en cada programa. Entonces, si mide algo que habría sido 'a la micra' y agrega la incertidumbre, tal vez sea 1,15 micras. Pero ofrece un examen real y veraz de la incertidumbre de todo el sistema”.
El sistema de Reed ya es excelente. PGS tiene una CMM de primer nivel y su laboratorio es estable a la temperatura dentro de un tercio de grado F. Pero han realizado otras inversiones para limitar la incertidumbre:"Compramos el software y los artefactos de medición de AfM para obtener un mejor control de la precisión de la máquina". . También compramos un borde escalonado de 700 milímetros idéntico al que utiliza el servicio Zeiss. Nuestra intención es saber dónde está la máquina en todo momento”.
PGS ya no dependerá únicamente de las calibraciones anuales del OEM, ya que solo representan una instantánea en el tiempo. Reed dijo que esas visitas cuestan una cantidad significativa de dinero y aún dejan a uno preguntándose cómo está funcionando la máquina durante todo el año. “Si el OEM regresa en un año y la calibración 'como se encontró' no cumple con las especificaciones, pone en duda todos los productos que ha estado aceptando con la máquina. Ya no estamos dispuestos a correr ese riesgo. Intentamos realizar exámenes semanales, o incluso diarios, de nuestras CMM”.
Mantenimiento y reparación de equipos
- Compromiso de esquina:cómo mecanizar esquinas
- 10 pasos clave para elegir una herramienta de pronóstico de máquinas
- Operaciones de máquinas de torno y herramientas de corte de torno
- Los pedidos de máquinas-herramienta disminuyen en septiembre
- Fuji presenta una máquina multitarea
- Methods Machine Tool para adquirir Koch Machine Tool
- Capacidad de fresado del centro de torneado y fresado
- Centro de torneado y tecnología de máquinas
- 3 métodos de construcción de herramientas CNC de 5 ejes
- Comprender el proceso de mecanizado y la máquina herramienta
- Cómo agregar una nueva herramienta